GrabCAD
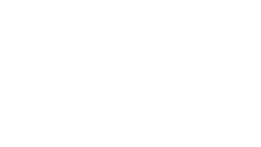
Lunar Torch
by GrabCAD
Last crawled date: 2 years, 7 months ago
This mobile heliostat uses a polished spring-tempered stainless-steel sheet for its mirror.
The deployment of the mirror is a slow and controlled “un-furling” towards the springs free state. Cables let out by brake motors provide this controlled motion.
The cable system also doubles as a control mechanism for the mirrors "shape". The mirror can be made perfectly flat using the motors, which allows compensation for tolerances associated with fabrication, stress relaxation, or thermal expansion. As an additional “bonus” feature, the mirror can be controlled to be slightly convex, or slightly concave, which allows adjustment of the intensity of light hitting the target.
The structural support for the mirror is provided by side bends (for vertical beam strength), tubes across the top and bottom (for horizontal stiffness and flatness), and by the internal stress of the material in balance with the tension in the cables (the free state of the mirror is slightly concave to ensure cables are always in tension). If needed, additional horizontal support can be added in the form of battens tack welded across the back of the mirror. Similarly, vertical stiffness can be increased by adding "tape springs" to the back of the mirror, i.e. thin strips of sheet metal with transverse curvature. During the design phase, FEA can be used to optimize the exact material thickness and support structure of the mirror to ensure flatness.
In the stored state, the mirror is rolled into a large diameter coil. The large curvature allows thicker material to be rolled while remaining above the material yield point. i.e. the "spring" free state of the mirror is maintained.
Pitch and yaw tracking motion is produced by a two axis slew drive, which is connected to control system including a sun sensor.
The overall system has low mass and a low rotational inertia with respect to the rover, due to the mirror in large part “supporting itself”. This makes for reduced rocket fuel required for the trip to the moon, and, allows for transport to different locations on the lunar surface while deployed.
The heliostat includes solar panels below the mirror, and battery energy storage. This provides the power to the motors, controls, and heat management systems.
Supplemental benefits of this design:
- The energy of the springs, which is released as the mirror unfurls, can be used to deploy leg support mechanisms. This would be useful for stand-alone heliostats not mounted to rovers.
- The ability to increase or decrease the reflected light intensity by changing the shape of the mirror. (as mentioned above)
- The tape spring features can produce a controlled "popping action" of the mirror spring by intentionally pulling them past the buckling point with the cables. This can be used to "shake" lunar dust off the mirror if it accumulates over time.
See the attached PDF files for more engineering details of this concept.
The deployment of the mirror is a slow and controlled “un-furling” towards the springs free state. Cables let out by brake motors provide this controlled motion.
The cable system also doubles as a control mechanism for the mirrors "shape". The mirror can be made perfectly flat using the motors, which allows compensation for tolerances associated with fabrication, stress relaxation, or thermal expansion. As an additional “bonus” feature, the mirror can be controlled to be slightly convex, or slightly concave, which allows adjustment of the intensity of light hitting the target.
The structural support for the mirror is provided by side bends (for vertical beam strength), tubes across the top and bottom (for horizontal stiffness and flatness), and by the internal stress of the material in balance with the tension in the cables (the free state of the mirror is slightly concave to ensure cables are always in tension). If needed, additional horizontal support can be added in the form of battens tack welded across the back of the mirror. Similarly, vertical stiffness can be increased by adding "tape springs" to the back of the mirror, i.e. thin strips of sheet metal with transverse curvature. During the design phase, FEA can be used to optimize the exact material thickness and support structure of the mirror to ensure flatness.
In the stored state, the mirror is rolled into a large diameter coil. The large curvature allows thicker material to be rolled while remaining above the material yield point. i.e. the "spring" free state of the mirror is maintained.
Pitch and yaw tracking motion is produced by a two axis slew drive, which is connected to control system including a sun sensor.
The overall system has low mass and a low rotational inertia with respect to the rover, due to the mirror in large part “supporting itself”. This makes for reduced rocket fuel required for the trip to the moon, and, allows for transport to different locations on the lunar surface while deployed.
The heliostat includes solar panels below the mirror, and battery energy storage. This provides the power to the motors, controls, and heat management systems.
Supplemental benefits of this design:
- The energy of the springs, which is released as the mirror unfurls, can be used to deploy leg support mechanisms. This would be useful for stand-alone heliostats not mounted to rovers.
- The ability to increase or decrease the reflected light intensity by changing the shape of the mirror. (as mentioned above)
- The tape spring features can produce a controlled "popping action" of the mirror spring by intentionally pulling them past the buckling point with the cables. This can be used to "shake" lunar dust off the mirror if it accumulates over time.
See the attached PDF files for more engineering details of this concept.
Similar models
grabcad
free

Heliostat with Adjustable Flatness Control
...panels would not be perfectly flat to each other. similary, inflatable designs risk losing gas pressure due to permeation...
grabcad
free

Lunar Sailor (NCKU ISP)
...xsq6wb5ro
https://youtu.be/28gxmpzqx2y
designed by team ncku isp (national cheng kung university, institute of space propulsion)
grabcad
free

NASA Lunar TORCH Heliostat
...e, yet robust design of the heliostat also allows for low-cost production.
for more details on the design, kindly check the pdf.
grabcad
free

Lunar Torch
...that provides power for onboard electronics. heliostat is folded similar to simple hand fan and deployed using spring loaded...
grabcad
free

Design of lunar torch with helio static mirror
...design of lunar torch with helio static mirror
grabcad
using heliostat mirrors we can use to transmit light to darker region
grabcad
free

Lunar TORCH Design
...nshots of some of the phases of the heliostat, an stl file of the dormant heliostat, and a video of the heliostat being deployed.
grabcad
free

L.A.S.E.R. - Lunar Automotive Sun Energy Redirector
...etc.). thus, all the operating methods used are exclusively rotational axes (which allows a better sealing against external dust)
grabcad
free

Lunar Torch with inflatable structure
...in opposition at the mirror film there is a similar system of tie rods. with the inflatable chambers deflated...
grabcad
free

Lunar Torch with inflatable structure
...in opposition at the mirror film there is a similar system of tie rods. with the inflatable chambers deflated...
grabcad
free

Lunar Heliostat
...sing lens. the torch can be rotated through x ,y and z axis, which helps the rover to redirect the solar energy wherever needed.
Lunar
3ddd
free
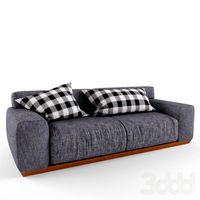
erba lunare
...erba lunare
3ddd
erba
erba lunare
turbosquid
$10
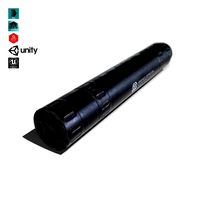
Suppressor Lunar
...quid
royalty free 3d model suppressor lunar for download as on turbosquid: 3d models for games, architecture, videos. (1380407)
3ddd
$1

Lunar lounge
...ounge
3ddd
stellarworks
модель кресла lunar lounge от производителя stellar works. габаритные размеры 850x710x800. 23k полигонов.
turbosquid
$62

Lunar Lander
... free 3d model lunar lander for download as obj, fbx, and lxo on turbosquid: 3d models for games, architecture, videos. (1185844)
turbosquid
$10
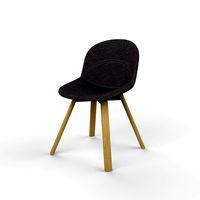
Lunar Chair
...y free 3d model lunar chair for download as 3ds, obj, and dae on turbosquid: 3d models for games, architecture, videos. (1219708)
3ddd
free
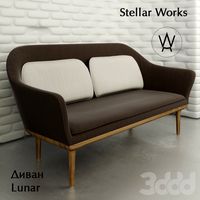
Диван Lunar
...d710xh800mm. в архиве есть текстуры, файлы в 2011 и 2014 версиях и obj-файл. 8,5k полигонов. turbo-/meshsmooth при необходимости.
turbosquid
$39

Lunar Sword
...e 3d model lunar sword for download as max, obj, fbx, and dae on turbosquid: 3d models for games, architecture, videos. (1440758)
turbosquid
$10
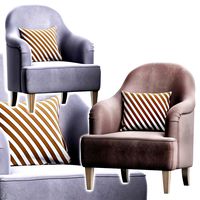
Lunar Armchair
...del lunar armchair by jamni for download as max, fbx, and obj on turbosquid: 3d models for games, architecture, videos. (1566066)
turbosquid
$1

Lunar car
...e 3d model lunar car for download as 3ds, obj, md3, and blend on turbosquid: 3d models for games, architecture, videos. (1209060)
turbosquid
$99

Lunar Plow
... available on turbo squid, the world's leading provider of digital 3d models for visualization, films, television, and games.
Torch
3d_ocean
$16
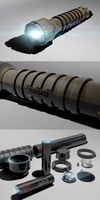
Torch
...flashlight high poly model. day high poly torch light mag lite night lamp rays shine new torch torch
high detailed 3d torch model
design_connected
$13
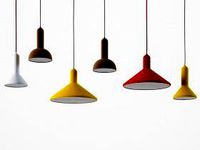
Torch
...torch
designconnected
established & sons torch computer generated 3d model. designed by willenz, sylvain .
3ddd
$1
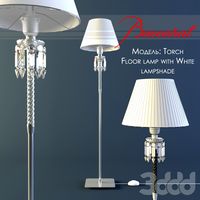
Baccarat - Torch
...- torch
3ddd
baccarat , torch
торшер фирмы baccarat, модель torch, текстуры прилагаются.
turbosquid
$10
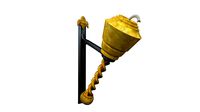
Torch
...h
turbosquid
royalty free 3d model torch for download as max on turbosquid: 3d models for games, architecture, videos. (1364794)
turbosquid
$4
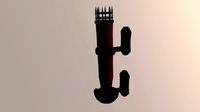
Torch
...h
turbosquid
royalty free 3d model torch for download as c4d on turbosquid: 3d models for games, architecture, videos. (1264168)
turbosquid
free

Torch
...urbosquid
free 3d model torch for download as , fbx, and obj on turbosquid: 3d models for games, architecture, videos. (1598202)
turbosquid
$5

torch
...quid
royalty free 3d model torch for download as max and stl on turbosquid: 3d models for games, architecture, videos. (1531004)
turbosquid
$1
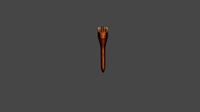
Torch
...d
royalty free 3d model torch for download as , fbx, and obj on turbosquid: 3d models for games, architecture, videos. (1622961)
3d_export
free
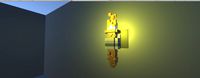
torch
...torch
3dexport
turbosquid
$10
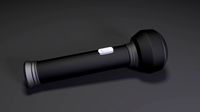
Torch
...
royalty free 3d model torch for download as ma, obj, and fbx on turbosquid: 3d models for games, architecture, videos. (1194449)