Thingiverse
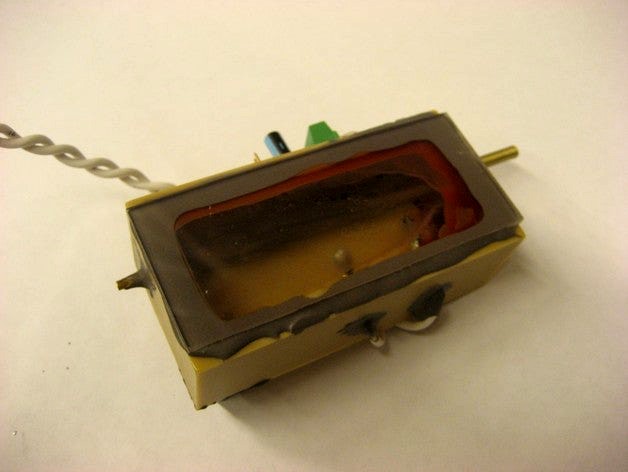
Waxuum Version 1.0 by mattmoses
by Thingiverse
Last crawled date: 3 years ago
The waxuum is sort of a reverse-extruder. The idea is that a heated hollow needle is used to remove material from a block of wax in a controlled manner, analogous to conventional machining using an endmill. A vacuum pump* pulls the molten wax through the needle, after which it is deposited in a reservoir where it can be recycled. The wax part can then be used directly, or more likely it can be used as a pattern for a mold. Below is a basic overview of how the process might work in a well-developed system. See video of a simple test at http://www.youtube.com/watch?v=rnKD9oIzcnM .
A heated basin is filled with wax, which is then allowed to cool. This big block of wax forms the working material for our little setup.
A waxuum mounted where the extruder usually goes on your 3D printer carves a master pattern (including containment walls) out of the wax block.
Elastomer resin is poured directly into negative pattern in the wax block.
When the elastomer cures, it is peeled off the wax master and used as a mold to crank out large numbers of parts.
The wax master is remelted within its heated basin. The removed wax in the reservoir is added back. The basin is cooled, and the wax is ready to use again for a new master pattern.
ADVANTAGES
The wax is melted instead of cut, so high forces are not required at the tool-tip. The low force requirement means that the XYZ positioner can be much more flexible (and cheaper and easier-to-make) than is normally required for conventional machining. Unlike conventional machining, there is no need for chip removal.
In many cases the surface finish on parts is better than that on filament-extruded parts, due to the smoothing effect of the hot needle moving over the wax. There are also fewer warping, delamination, and anisotropy problems.
You get a mold instead of a part: casting from a pattern can produce parts at a much faster rate than printing. You also have a greater choice of materials (plastics, metals, ceramics, and wax can all be cast in silicone molds).
DISADVANTAGES
You get a mold instead of a part: there are several additional steps and materials, including the manual work of pouring resins. Sometimes you really want to just print your parts and go.
Limited geometry: unless you make multi-part molds with cores and such, you are limited to relatively simple geometry. Hollow and concave parts are difficult.
The waxuum is relatively unproven compared to the many filament extruder designs currently in use.
RESULTS
The test showed it was feasible to use a tool of this design to make wax patterns. The most important thing to consider seems to be optimizing heat transfer from the needle to the wax, while minimizing heat loss due to movement of cool air through the needle. The thin-walled brass tubing is just barely acceptable for this purpose. The next version will use a material with higher thermal conductivity, such as thick-walled copper tubing. The heater should probably be located outside of the case. Possibly two heaters should be used - one for the needle and one to keep the wax molten inside the case.
*Update March 6 2010: See this cool article on converting an aquarium pump to a vacuum pump http://garage-shoppe.com/wordpress/?p=109
A heated basin is filled with wax, which is then allowed to cool. This big block of wax forms the working material for our little setup.
A waxuum mounted where the extruder usually goes on your 3D printer carves a master pattern (including containment walls) out of the wax block.
Elastomer resin is poured directly into negative pattern in the wax block.
When the elastomer cures, it is peeled off the wax master and used as a mold to crank out large numbers of parts.
The wax master is remelted within its heated basin. The removed wax in the reservoir is added back. The basin is cooled, and the wax is ready to use again for a new master pattern.
ADVANTAGES
The wax is melted instead of cut, so high forces are not required at the tool-tip. The low force requirement means that the XYZ positioner can be much more flexible (and cheaper and easier-to-make) than is normally required for conventional machining. Unlike conventional machining, there is no need for chip removal.
In many cases the surface finish on parts is better than that on filament-extruded parts, due to the smoothing effect of the hot needle moving over the wax. There are also fewer warping, delamination, and anisotropy problems.
You get a mold instead of a part: casting from a pattern can produce parts at a much faster rate than printing. You also have a greater choice of materials (plastics, metals, ceramics, and wax can all be cast in silicone molds).
DISADVANTAGES
You get a mold instead of a part: there are several additional steps and materials, including the manual work of pouring resins. Sometimes you really want to just print your parts and go.
Limited geometry: unless you make multi-part molds with cores and such, you are limited to relatively simple geometry. Hollow and concave parts are difficult.
The waxuum is relatively unproven compared to the many filament extruder designs currently in use.
RESULTS
The test showed it was feasible to use a tool of this design to make wax patterns. The most important thing to consider seems to be optimizing heat transfer from the needle to the wax, while minimizing heat loss due to movement of cool air through the needle. The thin-walled brass tubing is just barely acceptable for this purpose. The next version will use a material with higher thermal conductivity, such as thick-walled copper tubing. The heater should probably be located outside of the case. Possibly two heaters should be used - one for the needle and one to keep the wax molten inside the case.
*Update March 6 2010: See this cool article on converting an aquarium pump to a vacuum pump http://garage-shoppe.com/wordpress/?p=109
Similar models
thingiverse
free
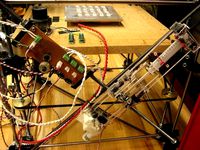
Metal Extruder and Syringe Pump by mattmoses
... heated plate seems to help avoid warping, but the downside is that the bottom of the part starts to ooze outwards after a while.
grabcad
free

INJECTION MOULDING MACHINE
... materials mainly including metals, glasses, elastomers, confections, and most commonly thermoplastic and thermosetting polymers.
thingiverse
free
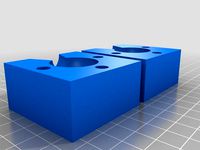
Mold For 1 inch Balls by DrDreidel
...ll need:
3 x 1/4-20 machine screws
3 x 1/4-20 wingnuts
non stick material (vaseline, litium grease, silicone grease, water, etc.)
grabcad
free

Hot Press 100Ton
...eater plate can be use oil heat by heater then circulate or use element on plate.
function is to press sawdust making solid block
thingiverse
free
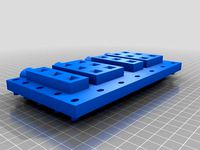
Lego Candle Mold Pattern by sandbot
...lego-like building block candles that can be stacked on each other. this pattern creates a two part mold for casting wax candles.
grabcad
free

mica heat band
...type of heater is specially used in plastic injection molding machines. it can be also used for so many other heating operations.
thingiverse
free
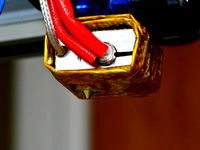
E3D Heater block jacket by thehungarian
... to keep the heat in.
do not try this at home, but, at 200 oc you can touch the outside for a few seconds without getting burned.
grabcad
free

Peltier Module
...although in practice the main application is cooling. it can also be used as a temperature controller that either heats or cools.
grabcad
free

INJECTION MOULDING
... materials mainly including metals, glasses, elastomers, confections, and most commonly thermoplastic and thermosetting polymers.
thingiverse
free
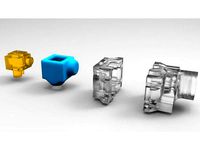
Heater Block Thermal Jacket Mold by karnhack
...rying times are shown on the type of silicone used. (g-translate)
more info: http://www.karnhack.com/heater-block-thermal-jacket/
Mattmoses
thingiverse
free
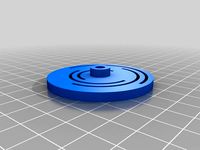
Slotted Disk by mattmoses
...slotted disk by mattmoses
thingiverse
a disk with slots, for controlling timing of solenoid motors (or other things).
thingiverse
free
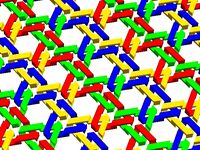
TriMail by mattmoses
... this will make it easier to print. new stls and openscad have been uploaded; the new files have "v2" in the filename.
thingiverse
free
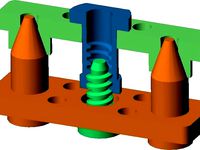
Modular Connectors by mattmoses
...nents for a reconfigurable modular robotic system
which can be found herehttps://rpk.lcsr.jhu.edu/publications#metamorphic_robots
thingiverse
free
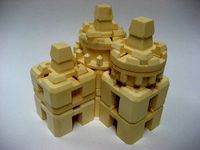
Modular Snap Blocks by mattmoses
...e info on the strengths and weaknesses of the actual physical plastic blocks here http://www.molecularassembler.com/ksrm/3.18.htm
thingiverse
free
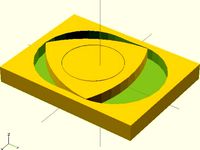
Wankel Engine Model by mattmoses
...code appropriated from
leemon baird's publicdomaingearv1.1.scad
which can be found here:http://www.thingiverse.com/thing:5505
thingiverse
free
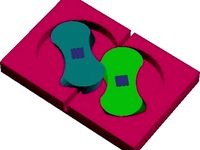
Roots Blower by mattmoses
...code appropriated from
leemon baird's publicdomaingearv1.1.scad
which can be found here:http://www.thingiverse.com/thing:5505
thingiverse
free
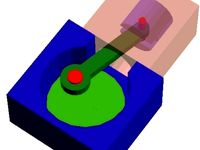
Piston Engine by mattmoses
...moving parts can be changed parametrically.
does anyone want to add some valves and make a real one that runs off compressed air?
thingiverse
free
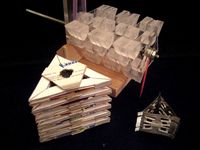
Compliant Mechanism 1 by mattmoses
...ttp://www.youtube.com/watch?v=y6y6ikvtpic
the main article is here:http://www.reprap.org/wiki/compliant_linear_motion_mechanism_1
thingiverse
free

Electroformed Nozzle by mattmoses
... as nickel). the electroforming method may serve to be a useful technique for converting other 3d printed forms into metal parts.
thingiverse
free
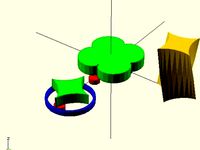
Epitrochoids and Hypotrochoids by mattmoses
...cycloid is an hypotrochoid with d = r.
see http://en.wikipedia.org/wiki/epitrochoid
and http://en.wikipedia.org/wiki/hypotrochoid
0
turbosquid
$12
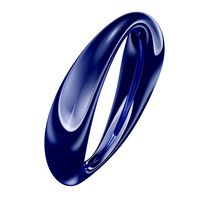
Calligraphic Digit 0 Number 0
...hic digit 0 number 0 for download as max, obj, fbx, and blend on turbosquid: 3d models for games, architecture, videos. (1389318)
3d_export
$6
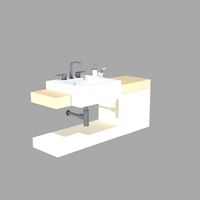
set-0
...set-0
3dexport
turbosquid
$6
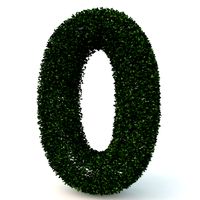
hedge 0
...yalty free 3d model hedge 0 for download as max, obj, and fbx on turbosquid: 3d models for games, architecture, videos. (1450353)
turbosquid
$5
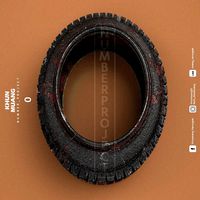
Nuber 0
...oyalty free 3d model nuber 0 for download as ma, obj, and fbx on turbosquid: 3d models for games, architecture, videos. (1564674)
turbosquid
$22
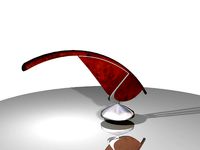
0.jpg
... available on turbo squid, the world's leading provider of digital 3d models for visualization, films, television, and games.
turbosquid
free
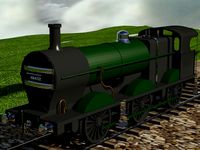
Steam Locomotive Fowler 4F 0-6-0
... available on turbo squid, the world's leading provider of digital 3d models for visualization, films, television, and games.
turbosquid
$10
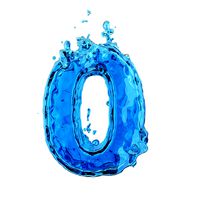
Liquid Number 0
... model liquid number 0 for download as c4d, 3ds, fbx, and obj on turbosquid: 3d models for games, architecture, videos. (1689919)
turbosquid
$45
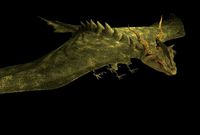
Dragon360_perspShape_tmp.0.jpg
... available on turbo squid, the world's leading provider of digital 3d models for visualization, films, television, and games.
turbosquid
$8
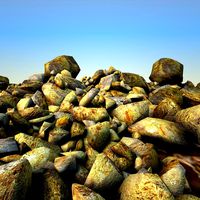
Rocks Debris 0
... available on turbo squid, the world's leading provider of digital 3d models for visualization, films, television, and games.
3d_export
$18
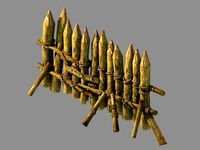
wood-guardrail-fence 0
...wood-guardrail-fence 0
3dexport
wood-guardrail-fence 0<br>3ds max 2015
Version
3ddd
$1
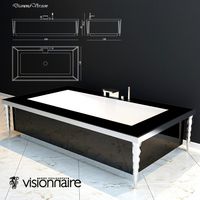
Diamond version
...nd , version , ванна
visionnaire - diamond bath
turbosquid
$50
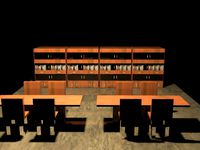
LibraryMini Version
...free 3d model librarymini version for download as max and jpg on turbosquid: 3d models for games, architecture, videos. (1617724)
design_connected
$34
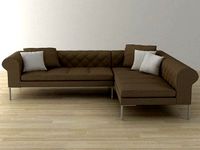
Barocco Version 01
...barocco version 01
designconnected
zanotta barocco version 01 computer generated 3d model. designed by progetti, emaf.
design_connected
$27
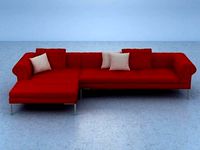
Barocco Version 02
...barocco version 02
designconnected
zanotta barocco version 02 computer generated 3d model. designed by progetti, emaf.
turbosquid
free
![Door [2 versions]](/t/13243146.jpg)
Door [2 versions]
...rbosquid
free 3d model door [2 versions] for download as fbx on turbosquid: 3d models for games, architecture, videos. (1223985)
turbosquid
$2
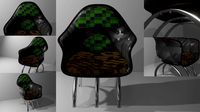
seat version 0.1
...
royalty free 3d model seat version 0.1 for download as blend on turbosquid: 3d models for games, architecture, videos. (1432653)
turbosquid
$12
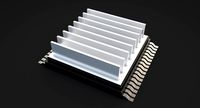
Chip Version 03
...lty free 3d model chip version 03 for download as c4d and fbx on turbosquid: 3d models for games, architecture, videos. (1241145)
3d_export
$10

magnolia grandiflora mature version
...magnolia grandiflora mature version
3dexport
magnolia grandiflora mature version
3d_export
$8
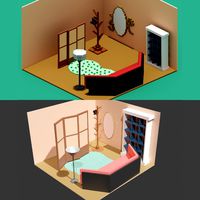
room assets and voxel version
...room assets and voxel version
3dexport
room assets and voxel version
turbosquid
$35
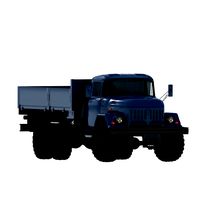
Zil Civilian version
... model zil civilian version for download as cgf, fbx, and obj on turbosquid: 3d models for games, architecture, videos. (1639420)
1
turbosquid
$69
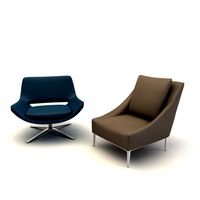
armchairs(1)(1)
... available on turbo squid, the world's leading provider of digital 3d models for visualization, films, television, and games.
turbosquid
$15
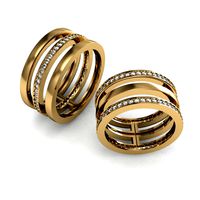
ring 1+1
... available on turbo squid, the world's leading provider of digital 3d models for visualization, films, television, and games.
turbosquid
$10

chair(1)(1)
... available on turbo squid, the world's leading provider of digital 3d models for visualization, films, television, and games.
turbosquid
$8

Chair(1)(1)
... available on turbo squid, the world's leading provider of digital 3d models for visualization, films, television, and games.
turbosquid
$2
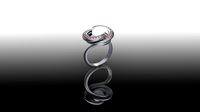
RING 1(1)
... available on turbo squid, the world's leading provider of digital 3d models for visualization, films, television, and games.
turbosquid
$1
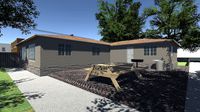
house 1(1)
... available on turbo squid, the world's leading provider of digital 3d models for visualization, films, television, and games.
turbosquid
$1
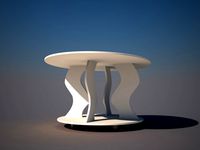
Table 1(1)
... available on turbo squid, the world's leading provider of digital 3d models for visualization, films, television, and games.
turbosquid
$59
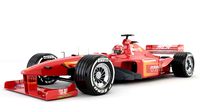
Formula 1(1)
...lty free 3d model formula 1 for download as max, fbx, and obj on turbosquid: 3d models for games, architecture, videos. (1567088)
design_connected
$11
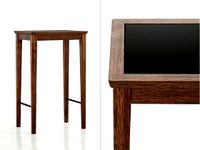
No 1
...no 1
designconnected
sibast no 1 computer generated 3d model. designed by sibast, helge.
turbosquid
$2
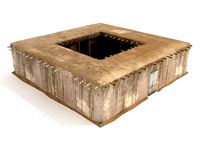
desert house(1)(1)
...3d model desert house(1)(1) for download as 3ds, max, and obj on turbosquid: 3d models for games, architecture, videos. (1055095)