Thingiverse
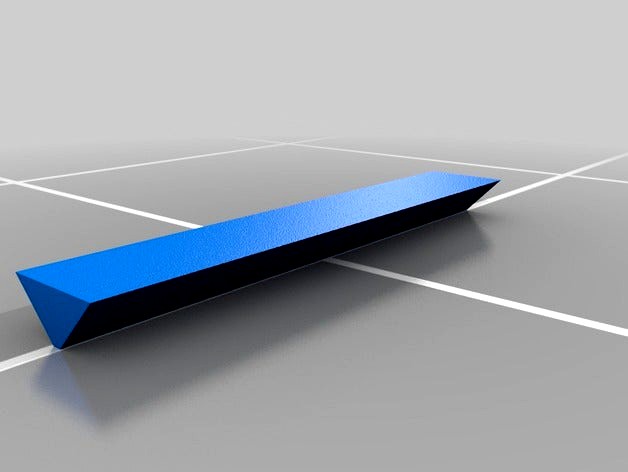
Warp Test for Print Bed Adhesion by TechShopJim
by Thingiverse
Last crawled date: 3 years ago
This model (actually set of three models) is a torture test to see if you can print it without any warping or lifting of the ends. I'll bet you can't.
I have not found a single FDM 3D printer that can print this model in ABS without warping and still allow a clean release of the finished print, unless my new printing surface is installed.
The thing that makes this model such a bear to print is the fact that it has only a 1/8" wide contact patch at the bottom of the V-shaped body. This tiny contact patch does not allow very much adhesion, so the forces of the contracting cooling plastic from each successive layer wants to pull the ends up off the print bed, causing warping.
There are three versions of this model as follows: 1.) Completely solid, 2.) A hollow shell, and 3.) A hollow shell with a vertical partition in the center to impart even more warping force on the ends.
This is the hardest thing that I have ever tried to print without having the ends lift up and warp off the print bed.
Many of you know that I have been working on a novel printing bed with a special surface specifically designed for printing in ABS. I have been trying to solve the ABS adhesion problem for many years, and I was the first one to publish the method now known as ABS juice or ABS slurry. The new print surface is the perfect combination with ABS slurry.
I built this model as a torture test for that new print surface.
I am recording GoPro videos of the build on my new surface material today (4/19/2016), and will update this post as soon as the video is done.
My new build surface is designed to still use ABS slurry, but the great thing is that this surface has tremendous adhesion when it is hot, but no adhesion when it is cool. It is also completely resistant to acetone and solvents, and can be heated to 1150 degrees F without damage (your printer will be damaged at that temperature, but not the print surface). This new print surface is also not made from any kind of glass (all types of glass including borosilicate and tempered glass are prone to thermal shock and can chip or crack or even shatter if the temperature of the glass changes too rapidly). Instead of glass, this new surface is made from a very thin sheet of a very special form of ceramic metallic oxide, which is extremely rigid. It is then coated with a special compound and fused to the rigid material in order to produce a bed that has nearly identical thermal expansion characteristics to ABS when it is hot, but radically different thermal expansion characteristics than ABS plastics when it is cold. This causes the finished part to be easily lifted off the build surface when it has cooled.
As you probably know all too well, the problem with ABS slurry is that it makes your printed parts stick too well to the build surface. The most common solution is to stick Kapton tape on the print bed, and then apply ABS slurry to the Kapton tape. ABS slurry helps the part stick to the Kapton tape on the print bed, but the warping forces will often cause the adhesive of the Kapton tape to actually separate from the bed. We are talking about some major contraction forces here! If the 3D printed sticks OK to a particular surface like Kapton or glass with ABS slurry without warping, usually when you try to remove the model, it won't budge. The only solution in this case is to use a scraper, knife blade, or screwdriver, but you risk scratching the print bed or damaging your finished part.
I think you will be impressed by my new build surface for printing in ABS. Here are the main features (this is not a commercial!):
o Thin and extremely rigid and stiff
o Very strong, unlike fragile glass
o No issues with thermal shock causing cracks, warping, shattering, or chipping
o Hot-swappable so you can start a new print as soon as the first one is finished
o Have multiple beds prepped and ready to go
o Literally pick up the finished printed part from the bed when it is done
o No modifications to your printer
o No fastening hardware or clips
o Not affected by heat, solvents, and resistant to abrasion
We will be testing the surface with a number of selected beta testers, as well as at all our 11 TechShop locations worldwide and all our TechShop Inside maker trailers.
If you are interested in being a beta tester (at a 50% discounted price) and you normally print in ABS with your heated-bed ABS printer, please PM me with your information and the type of printer you have, along with the dimensions of the print bed, and I'll put you on the consideration list. I'm hoping to get beta testers all set up starting in May 2016.
Anyway, try printing these models on your printer in ABS (or PLA if that's all you have) and post a photo here showing how much you can avoid warping, and print a finished part with a perfectly flat bottom.
Good luck!
--
Jim Newton
Founder, TechShop
I have not found a single FDM 3D printer that can print this model in ABS without warping and still allow a clean release of the finished print, unless my new printing surface is installed.
The thing that makes this model such a bear to print is the fact that it has only a 1/8" wide contact patch at the bottom of the V-shaped body. This tiny contact patch does not allow very much adhesion, so the forces of the contracting cooling plastic from each successive layer wants to pull the ends up off the print bed, causing warping.
There are three versions of this model as follows: 1.) Completely solid, 2.) A hollow shell, and 3.) A hollow shell with a vertical partition in the center to impart even more warping force on the ends.
This is the hardest thing that I have ever tried to print without having the ends lift up and warp off the print bed.
Many of you know that I have been working on a novel printing bed with a special surface specifically designed for printing in ABS. I have been trying to solve the ABS adhesion problem for many years, and I was the first one to publish the method now known as ABS juice or ABS slurry. The new print surface is the perfect combination with ABS slurry.
I built this model as a torture test for that new print surface.
I am recording GoPro videos of the build on my new surface material today (4/19/2016), and will update this post as soon as the video is done.
My new build surface is designed to still use ABS slurry, but the great thing is that this surface has tremendous adhesion when it is hot, but no adhesion when it is cool. It is also completely resistant to acetone and solvents, and can be heated to 1150 degrees F without damage (your printer will be damaged at that temperature, but not the print surface). This new print surface is also not made from any kind of glass (all types of glass including borosilicate and tempered glass are prone to thermal shock and can chip or crack or even shatter if the temperature of the glass changes too rapidly). Instead of glass, this new surface is made from a very thin sheet of a very special form of ceramic metallic oxide, which is extremely rigid. It is then coated with a special compound and fused to the rigid material in order to produce a bed that has nearly identical thermal expansion characteristics to ABS when it is hot, but radically different thermal expansion characteristics than ABS plastics when it is cold. This causes the finished part to be easily lifted off the build surface when it has cooled.
As you probably know all too well, the problem with ABS slurry is that it makes your printed parts stick too well to the build surface. The most common solution is to stick Kapton tape on the print bed, and then apply ABS slurry to the Kapton tape. ABS slurry helps the part stick to the Kapton tape on the print bed, but the warping forces will often cause the adhesive of the Kapton tape to actually separate from the bed. We are talking about some major contraction forces here! If the 3D printed sticks OK to a particular surface like Kapton or glass with ABS slurry without warping, usually when you try to remove the model, it won't budge. The only solution in this case is to use a scraper, knife blade, or screwdriver, but you risk scratching the print bed or damaging your finished part.
I think you will be impressed by my new build surface for printing in ABS. Here are the main features (this is not a commercial!):
o Thin and extremely rigid and stiff
o Very strong, unlike fragile glass
o No issues with thermal shock causing cracks, warping, shattering, or chipping
o Hot-swappable so you can start a new print as soon as the first one is finished
o Have multiple beds prepped and ready to go
o Literally pick up the finished printed part from the bed when it is done
o No modifications to your printer
o No fastening hardware or clips
o Not affected by heat, solvents, and resistant to abrasion
We will be testing the surface with a number of selected beta testers, as well as at all our 11 TechShop locations worldwide and all our TechShop Inside maker trailers.
If you are interested in being a beta tester (at a 50% discounted price) and you normally print in ABS with your heated-bed ABS printer, please PM me with your information and the type of printer you have, along with the dimensions of the print bed, and I'll put you on the consideration list. I'm hoping to get beta testers all set up starting in May 2016.
Anyway, try printing these models on your printer in ABS (or PLA if that's all you have) and post a photo here showing how much you can avoid warping, and print a finished part with a perfectly flat bottom.
Good luck!
--
Jim Newton
Founder, TechShop
Similar models
thingiverse
free
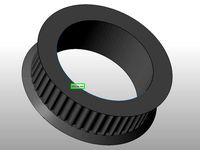
2mm GT2 idler for 608zz bearing 22mm by ylvov
...stant to thermal shock / temperature cycling far in excess of intended use
cut for heated bed platforms
http://www.unique-3d.com/
thingiverse
free
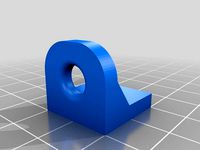
Print Surface Adhesion Test by Enginwiz
...e
to compare the adhesion forces of different tapes, hair sprays, slurries and build plate materials i designed this test print.
thingiverse
free

ABS Acetone Slurry Spreader Puck by gregrjohnson
...r kapton tape in order to help abs parts stick. the puck melts away as you use it. if you want it to last longer use 100% infill.
thingiverse
free
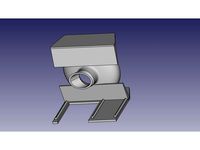
Stock CR10S Hot end additions to print ABS by Boffin48
...to bend up from bed, warping and breaking free.
these add-ons require no modification of stock item, they can be fitted directly.
thingiverse
free
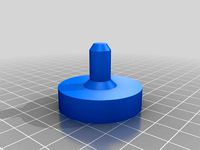
ABS slurry glass coater by wingmaster
... not visible in the later print. so use either transparent abs or use abs in the same color as the where you going to print with.
thingiverse
free
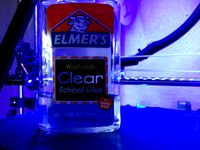
Stops warping of ABS & Nylon prints, Enjoy it! by Chris918
...y it faster by heating print bed to 45 degrees.
*stl download is a dummy file, unless you want a printable set of instructions :p
thingiverse
free
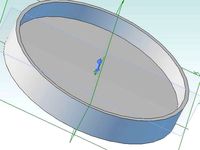
ABS Slurry Dish by i3DGear
...r months.
i don't know if you'll find this useful or not, but i sure did. no more curled up edges on large abs prints.
thingiverse
free
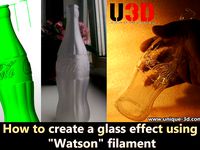
Coca Cola Bottle by ylvov
...stant to thermal shock / temperature cycling far in excess of intended use
cut for heated bed platforms
http://www.unique-3d.com/
thingiverse
free
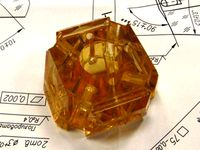
Miracle Adhesion Sitall glass U3D by ylvov
...
flex printinghttp://youtu.be/4zbjub7wq-k
wood printinghttp://youtu.be/1g14g0wlm0w
http://forums.reprap.org/read.php?1,453957
thingiverse
free
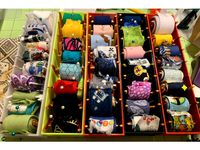
Bias tape(or ribbon) holder and tray by NoNoCovid
...with pla unless you have great bed adhesion. what helped a lot on a glass bed is using a glue stick just on the two short edges.
Techshopjim
thingiverse
free
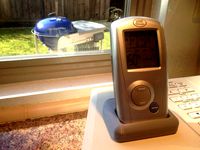
Weber Style BBQ Wireless Thermometer Receiver Stand by TechShopJim
...over the place, and the are really great because you can monitor the temperature of the meat from in the comfort of your kitchen.
thingiverse
free
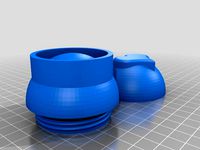
Screwball Heart Threaded Lid Pill Box Container by TechShopJim
... add a heart motif on the lid.
i made this to hold bulk pills for my loving wife so she can keep it on her nightstand.
enjoy!
thingiverse
free
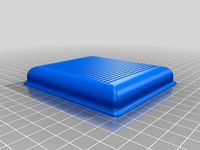
FasTrak Pass Enclosure Case (San Francisco Bay Area) by TechShopJim
...r this enclosure because it really isn't needed. this enclosure is really just a cover for the fastrak circuit board.
enjoy!
thingiverse
free
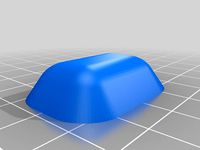
Ford Daylight Sensor Cover by TechShopJim
...c at techshop, and also on my replicator, and it seems to print pretty well at just about any settings that work for other items.
thingiverse
free
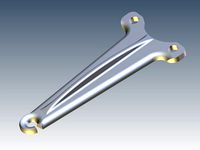
Official TechShop Filament Guide by TechShopJim
...ide was designed jim newton, the founder of techshop, using autodesk inventor 2012 running on a macbook pro 17 through parallels.
thingiverse
free
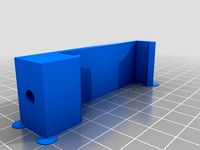
iPhone 4 4s Horizontal Tripod Mount by TechShopJim
... thread the hole with a 1/4-20 tap or a bolt if you don't have a tap. then it screws right on to a standard tripod.
enjoy!
thingiverse
free
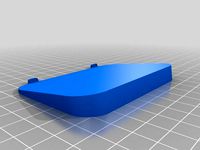
Elevation Dock Wedge for iPhone by TechShopJim
...meant raising the front edge of the elevation dock about 0.4".
please let me know if you like this "thing".
enjoy!
thingiverse
free
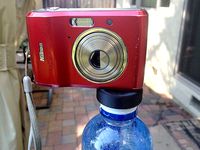
Water Bottle Camera Stand, with Centered Lug by TechShopJim
...on top of the soda or water bottle. be careful that the wind doesn't blow the whole thing over and break your camera!
enjoy!
thingiverse
free
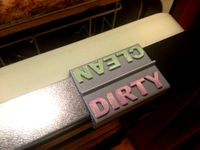
Dishwasher Dirty/Clean Indicator (Kenmore Ultra Wash) by TechShopJim
...licator 1. then i used sharpie pens to color the letters red (for "dirty") and green (for "clean").
enjoy!
thingiverse
free
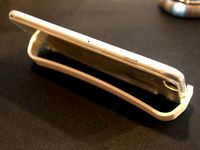
Revised iPhone 6/6s Plus Horiz Stand by TechShopJim
... and it seems to work really well.
you can print this in pla or abs and it will work very well for you with the default 50% fill.
Warp
3d_export
$26
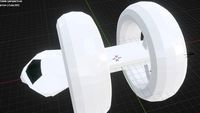
Warp
...warp
3dexport
a minimalist model of a warp ship
turbosquid
$22
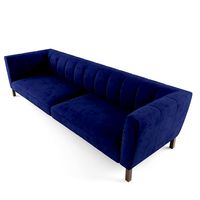
Lema Warp
...
royalty free 3d model lema warp for download as max and fbx on turbosquid: 3d models for games, architecture, videos. (1335291)
turbosquid
free

Warp Hole
... available on turbo squid, the world's leading provider of digital 3d models for visualization, films, television, and games.
turbosquid
$5
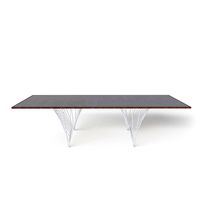
Warp Dining Table
...
royalty free 3d model warp dining table for download as max on turbosquid: 3d models for games, architecture, videos. (1603926)
turbosquid
$3
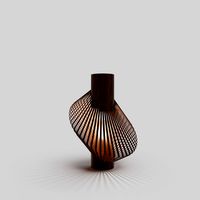
Warp wooden lamp
...d
royalty free 3d model warp wooden lamp for download as max on turbosquid: 3d models for games, architecture, videos. (1593363)
turbosquid
$20
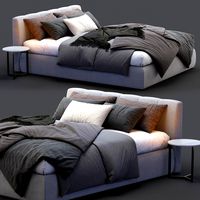
Lema Bed WARP
...yalty free 3d model lema bed warp for download as max and obj on turbosquid: 3d models for games, architecture, videos. (1566989)
3d_export
$10
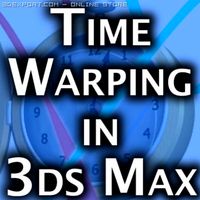
Time Warping In 3ds Max Complete Guide 3D Model
...ecelerate accelerate acceleration backward
time warping in 3ds max complete guide 3d model mental reality studios 21865 3dexport
3d_export
$12
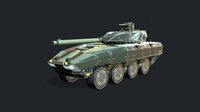
warp a2 predator tank assault gim
...ed diffuse, emissive, metallic, normal, roughness and ao maps. if you need 3d game assets or stl files i can do commission works.
turbosquid
free
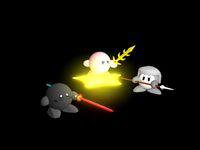
Kirby (Warp Star+Galaxia),ShadowKirby(Dual Sword), WaddleDee(Spear)
... available on turbo squid, the world's leading provider of digital 3d models for visualization, films, television, and games.
3d_export
$10
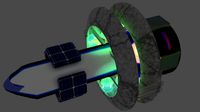
The concept of the spaceship of the future
...of a spaceship of the future for intergalactic travel warp space and...
Adhesion
turbosquid
$1
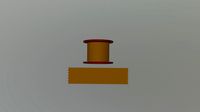
Adhesive tape
...quid
royalty free 3d model adhesive tape for download as obj on turbosquid: 3d models for games, architecture, videos. (1352737)
3d_export
$5
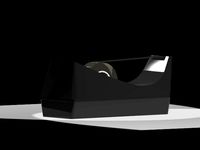
adhesive tape carrier
...adhesive tape carrier
3dexport
adhesive tape carrier
turbosquid
$18
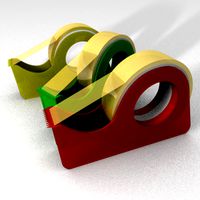
adhesive tape
... available on turbo squid, the world's leading provider of digital 3d models for visualization, films, television, and games.
turbosquid
$20
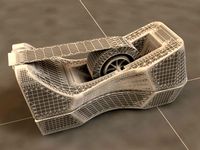
NORDSK STYLISH ADHESIVE TAPE DISPENSER IGES
... available on turbo squid, the world's leading provider of digital 3d models for visualization, films, television, and games.
3d_export
$20
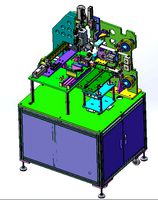
power cord adhesive tape machine
...anipulator: 0.005 mm, repeated positioning accuracy of manipulator: ≤ ± 0.01 mm, and material change mode: manual material change
3d_export
$1000
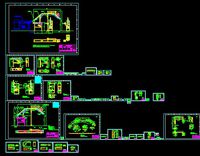
bead triangle adhesive laminating machine
...m onto the steel ring (3) the outlet of the rubber conveying device is connected with the inlet of the winding laminating device.
3d_export
$16
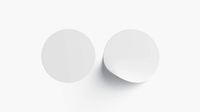
Two White Round Stickers - smooth and bended adhesive labels
...rt editable mesh object to editable poly and load *stickers_uvw.uvw* in unwrap uvw modifier; -studio environment is not included;
3d_export
$20
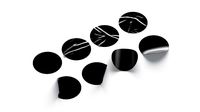
Black Stickers set - 8 adhesive sticky labels
...bject to editable poly and load<br>*stickers_uvw.uvw* in unwrap uvw modifier;<br>-studio environment is not included;
3d_export
$20
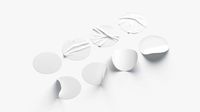
White Stickers set - 8 adhesive sticky labels
...bject to editable poly and load<br>*stickers_uvw.uvw* in unwrap uvw modifier;<br>-studio environment is not included;
3d_export
$20
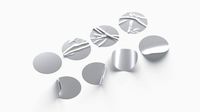
8 Stickers set - silver adhesive sticky labels
...bject to editable poly and load<br>*stickers_uvw.uvw* in unwrap uvw modifier;<br>-studio environment is not included;
Bed
3ddd
$1
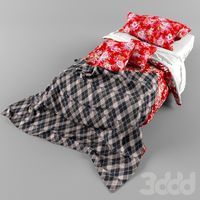
bed
...bed
3ddd
bed , постельное белье
bed
3ddd
$1
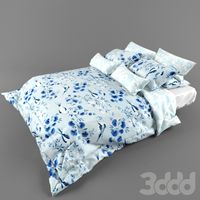
bed
...bed
3ddd
bed , постельное белье
bed
3ddd
$1
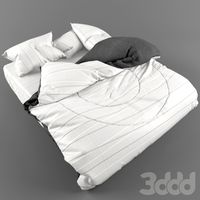
bed
...bed
3ddd
bed , постельное белье
bed
3ddd
$1
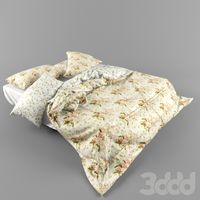
bed
...bed
3ddd
bed , постельное белье
bed
3ddd
$1
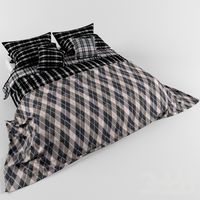
bed
...bed
3ddd
bed , постельное белье
bed
3ddd
$1
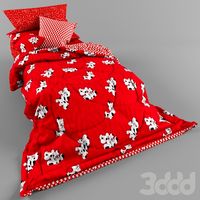
bed
...bed
3ddd
bed , постельное белье
bed
3ddd
free
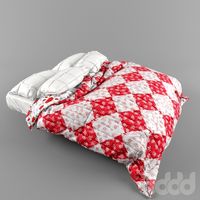
bed
...bed
3ddd
bed , постельное белье
bed
3ddd
free
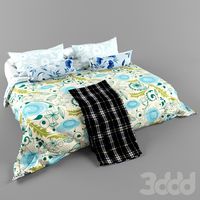
bed
...bed
3ddd
bed , постельное белье
bed
3ddd
$1
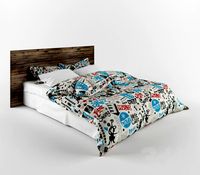
Bed
...bed
3ddd
bed , постельное белье , постель
bed
3d_export
$7
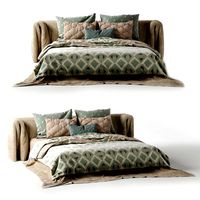
bed adairs bed
...rs bed
3dexport
bed adairs bed in modern style. if you want a smoother surface, please turn on turbosmooth in the modifier list.
Test
turbosquid
$99
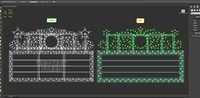
test
...st
turbosquid
royalty free 3d model test for download as max on turbosquid: 3d models for games, architecture, videos. (1251637)
turbosquid
$63
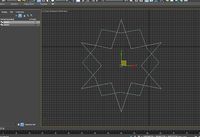
TEST
...st
turbosquid
royalty free 3d model test for download as max on turbosquid: 3d models for games, architecture, videos. (1446233)
turbosquid
$1
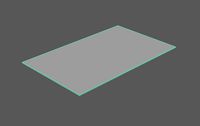
test
...st
turbosquid
royalty free 3d model test for download as fbx on turbosquid: 3d models for games, architecture, videos. (1360941)
3d_export
free

johnny test
...johnny test
3dexport
johnny test 3d
turbosquid
$15
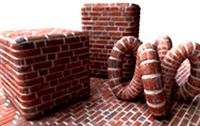
Test
... available on turbo squid, the world's leading provider of digital 3d models for visualization, films, television, and games.
turbosquid
$2
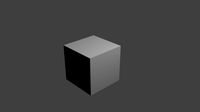
test
... available on turbo squid, the world's leading provider of digital 3d models for visualization, films, television, and games.
turbosquid
free
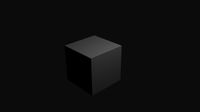
Test
... available on turbo squid, the world's leading provider of digital 3d models for visualization, films, television, and games.
turbosquid
free
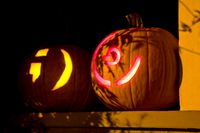
test
... available on turbo squid, the world's leading provider of digital 3d models for visualization, films, television, and games.
turbosquid
free
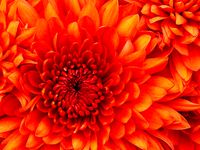
Test
... available on turbo squid, the world's leading provider of digital 3d models for visualization, films, television, and games.
3d_export
$5
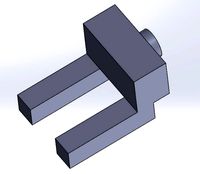
gripper test
...gripper test
3dexport
robot gripper test model
design_connected
$27
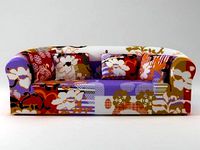
...print
designconnected
moroso print computer generated 3d model. designed by wanders, marcel.
3ddd
free
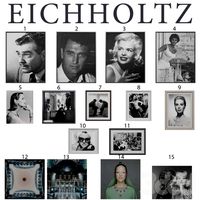
Eichholtz Prints
...- eichholtz print central station i
13 - eichholtz print central station ii
14 - eichholtz print marisa
15 - eichholtz print tish
3ddd
$1
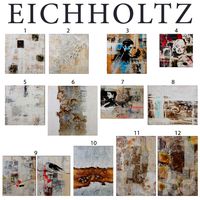
Eichholtz Prints
...print abstract - set of 2
10 - eichholtz print orange abstract
11 - eichholtz print buddha right
12 - eichholtz print buddha left
turbosquid
$1
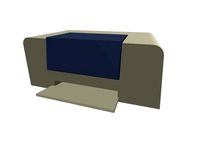
... available on turbo squid, the world's leading provider of digital 3d models for visualization, films, television, and games.
3ddd
free
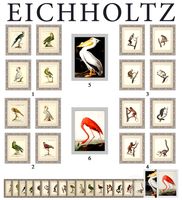
Eichholtz Prints
...of 4
2 - print dunbar 2 set of 4
3 - print guadeloupe 1 set of 4
4 - print guadeloupe 2 set of 4
5 - print giles
6 - print trett
3ddd
$1
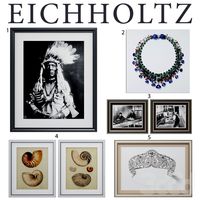
Eichholtz Prints
...nt tutti frutti
3 - eichholtz prints watson - set of 2
4 - eichholtz prints antique nautilus - set of 2
5 - eichholtz print tiara
3d_export
$5
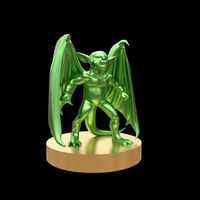
Monster for printing
...monster for printing
3dexport
monster 3d model printing
3ddd
free
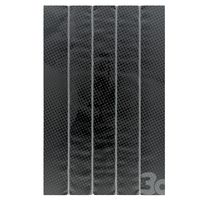
printed rug
...printed rug
3ddd
ковер
very creative printed rug
3ddd
free
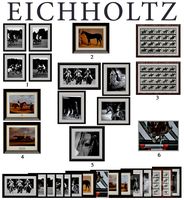
Eichholtz Prints
...иал: бумага
габариты (вхш): 72 x 62 см
описание: print sweetmeat - постер в деревянной раме.
3 - prints varsity set of 2
арти
3ddd
free
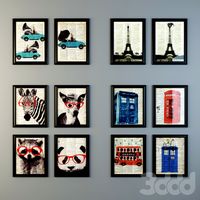
Art Print Posters
...art print posters
3ddd
прованс
art print posters by patrician prints