GrabCAD
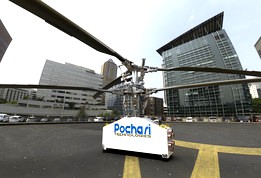
Unmanned aerial heavy lift crane
by GrabCAD
Last crawled date: 1 year, 10 months ago
There exists considerable demand for an affordable, unmanned, non-aviation certified heavy lift rotorcraft which is designed solely for lifting. Lifting applications that require significantly greater operating radius, unlimited mobility, greater operating flexibility, quick setup and turn around time, and where ground-based cranes simply cannot perform. Unlevel, rugged, rocky and unstable, where road access is poor, or situations that require transportation over rivers, lakes, or even over the ocean require an aerial solution. Prime applications include pre-fabricated modular construction, installing offshore wind turbines, installing wind turbines in mountainous terrain, moving air conditioning units atop a building, pouring concrete in mountainous regions, transporting an excavator atop a high rise building for demolition, transporting shipping containers from ports, installing solar farms, bridge construction, moving large stones from a quarry, mining operations, offshore oil and gas rig construction, or moving large stationary power generators or transformers from rural areas. The aerial crane shines in virtually any situation where heavy objects, building materials, or construction equipment need to moved fast, and most importantly anywhere regardless of terrain conditions. Currently, conventional helicopters are prohibitively expensive to purchase and operate: Enter the Aerial crane. Designed solely as a heavy lift craft, not as a manned helicopter, we bypass all of the costly requirements that make helicopters so expensive. By eliminating the pilot, we can remove the entire cockpit section, and the risk of loss of life. In addition, all of the necessary instruments and flight control systems are replaced with a simple remote-control system. The elimination of a crash worthy fuselage and cabin section save considerable weight, adding to the lift capacity. By designing the aerial crane to be moved and transported by truck, instead of ferrying over by flying, we can avoid operating over populated areas, eliminating the need for certification. Once again, the aerial-crane is not an aircraft that is certified by government aviation agencies, rather it’s designed as a highly-mobile job site crane. Its operation is strictly limited to construction and work sites, or any job site for that matter which is only occupied by trained personnel, if any time the aerial-crane is going operate over populated areas, all occupants must be evacuated. No ferrying or flying in the airspace is allowed. By eliminating the need for aviation certification, the cost is reduced by an enormous margin. Certifying a helicopter can cost $200,000,000, a huge investment that needs to be recuperated, by charging a large markup on each aircraft above and beyond the bare manufacturing cost. Only certified suppliers can manufacture parts for a certified aircraft. The aerial crane on the hand has none of these requirements, therefore any machine shop in the world can produce parts, allowing very affordable manufacturing of dynamic components, including the main rotor gearbox, turbomachinery, rotor head, and rotor blades. These components are all very simple, manufacturing can be easily performed by non aerospace specialized companies. Any CNC machine shop in the world can machine a rotor grip or epicyclic gear set, relatively easy to machine components. In addition, certified aircraft of course also have to use certified powerplants. An Arriel 1D1, a commonly used helicopter engine, costs $650,000, over $1000/hp. An equivalent non-certified ground-based turbine generator costs only a fraction of this. To manufacture the equivalent turbine in-house using CNC machined centrifugal impellers, and blisk power turbines, can be performed for less than $50,000 for a 700 hp turboshaft. This price difference may at first glance seem to be hard to believe, but upon closer examination it becomes understandable, by eliminating the extremely high safety and performance standards required for passenger-carrying aircraft, manufacturing costs are dramatically reduced. The aerial crane will be sold for only $1,000,000, only twice the cost of the equivalent capacity tower crane. The capacity of the aerial-crane is 10 tons, or 20,000 lbs, 9000 kg. The range without aerial refueling is 50 miles or one hour of operation. That means our aerial crane can carry 10 tons, over 50 miles! The crane can operate for up to 24 hours at a time with aerial refueling provides by an unmanned ducted fan drone. Conventional cranes are nearly made obsolete in the of the aerial crane.
The aerial crane is transported to the jobsite by a specialized truck which serves as a landing platform. If a road is not located nearby, the crane is set up and flown over a non-populated route to the jobsite. The crane itself cannot land on terrain, the reason is landing gear adds a significant amount of weight, therefore we decided to eliminate all on-board landing gear. The crane is required to land directly on the truck-based platform. Once landed on the truck-based platform, the rotor blades can be removed, allowing the main module (power module), consisting of the powerplant, gearbox, driveshaft and flight control system, to be placed flat down and carried on a flatbed truck. Set-up time is less than an hour.
The powerplant consists of 6x in-house developed turboshafts. The compressor is all centrifugal, to reduce cost, as centrifugal compressors are easily machined by any machine shop with a 5 axis CNC. A centrifugal compressor design is much simpler, eliminating stators. The power turbine is a “Blisk” design cast or machined out of Haynes Hastelloy X. A Blisk design reduces cost and complexity by machining or casting the entire unit in one single component, both blades and disc, eliminating the need to machine individual blades and “firtree” in the disk. The mass flow rate is 3.5 kg/sec. Bearings are standard high-speed oil lubricated roller bearings. The turboshaft is rated for 1000 takeoff-horsepower, and 850 continuous. The turboshaft is multi-fuel capable, with both gaseous and liquid fuel combustors available. In regions where liquid natural gas is readily available for low cost, a gaseous version is available. In regions where liquid fuels are inexpensive, diesel fuel is used since no high-altitude gelling requirements are present. Liquid hydrogen is also an available fuel option. The main rotor gearbox includes a bevel gear for the co-axial rotor drive, and epicyclic gears for reduction. The turboshafts are placed around a 4 stage large epicyclic gearbox, providing 250x reduction from 50,000 rpm down to 200 rpm for the main rotor. The rotor system incorporates Pochari Hydrogen’s innovative independent rotor control, where hydraulic pitch-link actuators provide rotor pitch actuation without a swashplate. Hydraulic fluid is transmitted via slip-ring for the lower rotor, and via an on-board hydraulic pump for the upper rotor. All flight controls are fly-by-wire. Each actuator is independently activated electronically via remote control. The second option, which the design team is considering as a simpler solution, is a conventional swashplate rotor pitch actuator system. The main rotor hub is manufactured from lay-up sheets of 300,000 psi T800 Toray aerospace-grade carbon fiber. The main rotor grips are titanium, as well as main rotor shaft. The gearbox housing is Aluminum 7075. The bevel gear and epicyclic gears are made of 4340 steel. The rotor system is semi-articulating, with elastomeric bearings providing lead-lag and flap. The main rotor blades are made of Toray T800 carbon fiber and Nomex honeycomb, with a stainless steel leading edge and straight non-swept tips to reduce manufacturing cost, the blade root is also a basic straight end instead of a narrower root design typically found in modern helicopter rotor blades. with a weight of 250 lbs each. Assembly and prototype testing is performed in Chennai, India, with certain components coming from all over China. Turbomachinery is manufactured in China by Shandong Yili Power Technology Co Ltd. and Zhenjiang Supersoar Machinery Co Ltd.
Cranes will be available for purchase in early 2022. The purchase price is $990,000 for the turbine version, and $800,000 for the electric version. The hourly operating cost is $720/hr for the turbine version, and $330/hr for the electric version.
Specifications: Unmanned heavy lift mobile aerial crane (non-certified experimental) Use over populated areas is strictly prohibited
Crane is designed solely as a heavy lift machine for construction sites and worksites with only trained personnel present.
Powerplant: Gas turbine or fully electric.
Fully Electric corded version for short radius: 500 feet. The electric powerplant consists of 16x 300 hp axial flux electric motors arranged in a stack of four arranged around an epicyclic gearbox horizontally. Three Aluminum alloy 1350 2000 MCM power cables (weighing 3100 lbs, only half the weight carried by the aerial crane) are carried by an intermediate lifter craft 100 ft above the ground-based power unit, the cable then spans from the lifter craft to the aerial crane up to 500 feet. When more radius is needed, the ground power unit can be moved closer, think of the aerial electric crane as a tower crane on wheels.
A gas turbine-powered version for long working radius, 50 miles, 80 km.
Powerplant specifications for turbine version: 6x 800 shp dual centrifugal compressor dual power turbine reverse flow turboshaft. Turbine inlet temperature: 1560 °F
Combustor: Dual-fuel gaseous-liquid reverse flow
Compression ratio: 14:1
Compressor: Three centrifugal 304 stainless steel
Power turbine: 1x HP, 1x LP Dual 40 blade Blisk Hastelloy X
Specific fuel consumption: 0.55 lbs/shp-hr
Weight: 250 lbs
Shaft ouput speed: 55,000 rpm
Power output: 1000 shp take off, 850 continuous
Fuel consumption at 70% torque: 280 gallons/hr
Fuel consumption at 130% torque: 402 gallons/hr
Rotor system:
6x 23″ x 265″ 250 lbs/ea
Gearbox: 250x reduction helical gear epicyclic, helical bevel gear for coaxial.
System weight and capacity:
Gross take-off weight: 33,000 lbs
Unit empty weight with 1-hour fuel: 10,500 lbs
Net lift capacity: 22,500 lbs
Maximum operating altitude without airspace permission: 400 ft
Maximum non-stop endurance: 24 hours.
Maximum travel distance over ocean or non-populated area: 480 miles, 770 km.
Unit dimensions:
Overall unit width and length: 51′
Overall unit height: 190″
Power module dimensions: 35″ width by 68″ height
Power module weight without rotors: 6700 lbs
Rotor drive module dimensions: 88″ width, 130″ length
Power module with drive module separated can be easily transported in a box truck.
Purchase price: $990,000
Hourly operating cost: $750/hr
https://pocharitechnologies.com/2019/03/06/electric-aerial-crane-system/
The aerial crane is transported to the jobsite by a specialized truck which serves as a landing platform. If a road is not located nearby, the crane is set up and flown over a non-populated route to the jobsite. The crane itself cannot land on terrain, the reason is landing gear adds a significant amount of weight, therefore we decided to eliminate all on-board landing gear. The crane is required to land directly on the truck-based platform. Once landed on the truck-based platform, the rotor blades can be removed, allowing the main module (power module), consisting of the powerplant, gearbox, driveshaft and flight control system, to be placed flat down and carried on a flatbed truck. Set-up time is less than an hour.
The powerplant consists of 6x in-house developed turboshafts. The compressor is all centrifugal, to reduce cost, as centrifugal compressors are easily machined by any machine shop with a 5 axis CNC. A centrifugal compressor design is much simpler, eliminating stators. The power turbine is a “Blisk” design cast or machined out of Haynes Hastelloy X. A Blisk design reduces cost and complexity by machining or casting the entire unit in one single component, both blades and disc, eliminating the need to machine individual blades and “firtree” in the disk. The mass flow rate is 3.5 kg/sec. Bearings are standard high-speed oil lubricated roller bearings. The turboshaft is rated for 1000 takeoff-horsepower, and 850 continuous. The turboshaft is multi-fuel capable, with both gaseous and liquid fuel combustors available. In regions where liquid natural gas is readily available for low cost, a gaseous version is available. In regions where liquid fuels are inexpensive, diesel fuel is used since no high-altitude gelling requirements are present. Liquid hydrogen is also an available fuel option. The main rotor gearbox includes a bevel gear for the co-axial rotor drive, and epicyclic gears for reduction. The turboshafts are placed around a 4 stage large epicyclic gearbox, providing 250x reduction from 50,000 rpm down to 200 rpm for the main rotor. The rotor system incorporates Pochari Hydrogen’s innovative independent rotor control, where hydraulic pitch-link actuators provide rotor pitch actuation without a swashplate. Hydraulic fluid is transmitted via slip-ring for the lower rotor, and via an on-board hydraulic pump for the upper rotor. All flight controls are fly-by-wire. Each actuator is independently activated electronically via remote control. The second option, which the design team is considering as a simpler solution, is a conventional swashplate rotor pitch actuator system. The main rotor hub is manufactured from lay-up sheets of 300,000 psi T800 Toray aerospace-grade carbon fiber. The main rotor grips are titanium, as well as main rotor shaft. The gearbox housing is Aluminum 7075. The bevel gear and epicyclic gears are made of 4340 steel. The rotor system is semi-articulating, with elastomeric bearings providing lead-lag and flap. The main rotor blades are made of Toray T800 carbon fiber and Nomex honeycomb, with a stainless steel leading edge and straight non-swept tips to reduce manufacturing cost, the blade root is also a basic straight end instead of a narrower root design typically found in modern helicopter rotor blades. with a weight of 250 lbs each. Assembly and prototype testing is performed in Chennai, India, with certain components coming from all over China. Turbomachinery is manufactured in China by Shandong Yili Power Technology Co Ltd. and Zhenjiang Supersoar Machinery Co Ltd.
Cranes will be available for purchase in early 2022. The purchase price is $990,000 for the turbine version, and $800,000 for the electric version. The hourly operating cost is $720/hr for the turbine version, and $330/hr for the electric version.
Specifications: Unmanned heavy lift mobile aerial crane (non-certified experimental) Use over populated areas is strictly prohibited
Crane is designed solely as a heavy lift machine for construction sites and worksites with only trained personnel present.
Powerplant: Gas turbine or fully electric.
Fully Electric corded version for short radius: 500 feet. The electric powerplant consists of 16x 300 hp axial flux electric motors arranged in a stack of four arranged around an epicyclic gearbox horizontally. Three Aluminum alloy 1350 2000 MCM power cables (weighing 3100 lbs, only half the weight carried by the aerial crane) are carried by an intermediate lifter craft 100 ft above the ground-based power unit, the cable then spans from the lifter craft to the aerial crane up to 500 feet. When more radius is needed, the ground power unit can be moved closer, think of the aerial electric crane as a tower crane on wheels.
A gas turbine-powered version for long working radius, 50 miles, 80 km.
Powerplant specifications for turbine version: 6x 800 shp dual centrifugal compressor dual power turbine reverse flow turboshaft. Turbine inlet temperature: 1560 °F
Combustor: Dual-fuel gaseous-liquid reverse flow
Compression ratio: 14:1
Compressor: Three centrifugal 304 stainless steel
Power turbine: 1x HP, 1x LP Dual 40 blade Blisk Hastelloy X
Specific fuel consumption: 0.55 lbs/shp-hr
Weight: 250 lbs
Shaft ouput speed: 55,000 rpm
Power output: 1000 shp take off, 850 continuous
Fuel consumption at 70% torque: 280 gallons/hr
Fuel consumption at 130% torque: 402 gallons/hr
Rotor system:
6x 23″ x 265″ 250 lbs/ea
Gearbox: 250x reduction helical gear epicyclic, helical bevel gear for coaxial.
System weight and capacity:
Gross take-off weight: 33,000 lbs
Unit empty weight with 1-hour fuel: 10,500 lbs
Net lift capacity: 22,500 lbs
Maximum operating altitude without airspace permission: 400 ft
Maximum non-stop endurance: 24 hours.
Maximum travel distance over ocean or non-populated area: 480 miles, 770 km.
Unit dimensions:
Overall unit width and length: 51′
Overall unit height: 190″
Power module dimensions: 35″ width by 68″ height
Power module weight without rotors: 6700 lbs
Rotor drive module dimensions: 88″ width, 130″ length
Power module with drive module separated can be easily transported in a box truck.
Purchase price: $990,000
Hourly operating cost: $750/hr
https://pocharitechnologies.com/2019/03/06/electric-aerial-crane-system/
Similar models
grabcad
free

Blisk with 36 blades for model plane
...t only lower the stiffness and performance of the turbine, but difficult to finish as well. as a result, blisk comes in to being.
grabcad
free

Turbine Blisk
...turbine blisk
grabcad
aircraft powerplant
grabcad
free

Turbine Blisk (Bladed Disk)
...turbine blisk (bladed disk)
grabcad
just a simple model to help show how to make gas turbine or jet engine rotors.
grabcad
free

Turbo Rotor, turbine - compressor, wheel - blisk - fan, impeller, Turbocharger
...eel - blisk - fan, impeller, turbocharger
grabcad
turbo rotor, turbine - compressor, wheel - blisk - fan, impeller, turbocharger
cg_trader
free

Blisk
... of blade and disk, the two components it replaces in turbomachinery. blisks may also be known as integrally bladed rotors (ibr).
grabcad
free

Centrifugal blades
...centrifugal blades
grabcad
turboshaft engine centrifugal compressor
grabcad
free

Blisk
...be machined from a solid peace of material. this blade is only for show of cam processes needed for machining this kind of model.
cg_trader
free
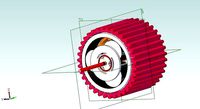
Reducing 101 Turbine Gear Case
...l power. this mechanical is used to drive pumps (both air and fuel). turbine gearbox planetary gear box vehicle part vehicle part
grabcad
free

compressor rotor design
...compressor rotor design
grabcad
this model helps us to compare conventional type of rotor blades and blisk type of rotor blades
grabcad
free

Turbine Rotor
...turbine rotor
grabcad
turbine rotor... centrifugal
Unmanned
3d_export
$12
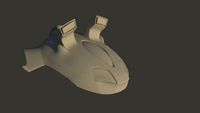
Unmanned Plane 3D Model
...manned plane 3d model
3dexport
space plane unmanned simple wing wings two cheap
unmanned plane 3d model majedworks 99975 3dexport
3d_export
free
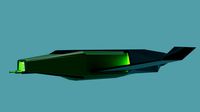
unmanned space plane
...unmanned space plane
3dexport
3d_export
free
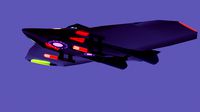
unmanned space plane
...unmanned space plane
3dexport
turbosquid
$50
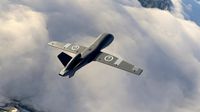
Unmanned Aerial Vehicle
...odel unmanned aerial vehicle for download as ma, fbx, and obj on turbosquid: 3d models for games, architecture, videos. (1544032)
turbosquid
$2
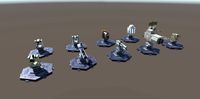
Modern Unmanned Turrets
...unmanned turrets for download as fbx, blend, and unitypackage on turbosquid: 3d models for games, architecture, videos. (1345077)
cg_studio
$119

Unmanned Missions to Mars3d model
...ars3d model
cgstudio
.xsi - unmanned missions to mars 3d model, royalty free license available, instant download after purchase.
cg_studio
$49
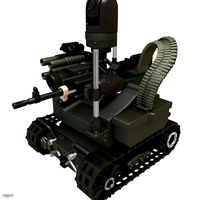
MAARS Unmaned Vehicle3d model
...vehicle3d model
cgstudio
.max - maars unmaned vehicle 3d model, royalty free license available, instant download after purchase.
turbosquid
$300
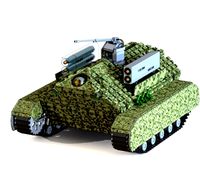
Unmanned Autonomous Land Vehicle
...l unmanned autonomous land vehicle for download as and sldas on turbosquid: 3d models for games, architecture, videos. (1437737)
3d_ocean
$12
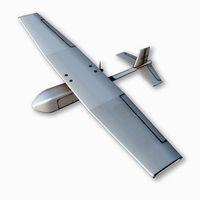
Unmanned Air Vehicle
...t may be man-portable. suavs monoplanes are typically launched by throwing or slingshot, and continue flying on their own. sua...
turbosquid
$199
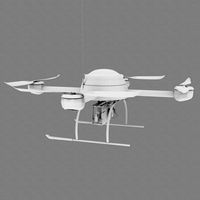
UAV - Unmanned Aerial Vehicle
... available on turbo squid, the world's leading provider of digital 3d models for visualization, films, television, and games.
Aerial
archive3d
free
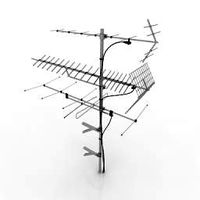
Aerial 3D Model
...n aerial rooftop antenna
aerial n061008 - 3d model (*.gsm+*.3ds) for interior 3d visualization.
3d_export
$5
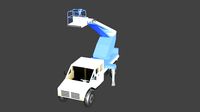
aerial platform
...aerial platform
3dexport
truck for work purposes.
turbosquid
$15

Aerial bomb
... available on turbo squid, the world's leading provider of digital 3d models for visualization, films, television, and games.
3d_export
$60

Aerial 3D Model
...aerial 3d model
3dexport
architecture modelexterior landscape max
aerial 3d model chen3d 14457 3dexport
3d_ocean
$5
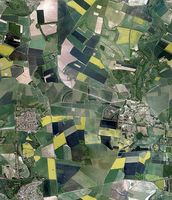
Aerial Fields Texture
... original file is 13000×15111 for close up renders and a lower 4k resolution is also provided. the texture is in tif format an...
3d_export
$5
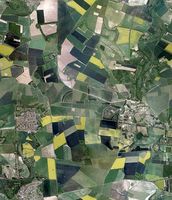
Aerial Fields Texture 3D Model
...aerial fields texture 3d model
3dexport
aerial fields tileable
aerial fields texture 3d model the96th 88019 3dexport
turbosquid
$50
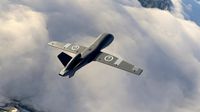
Unmanned Aerial Vehicle
...odel unmanned aerial vehicle for download as ma, fbx, and obj on turbosquid: 3d models for games, architecture, videos. (1544032)
turbosquid
$30
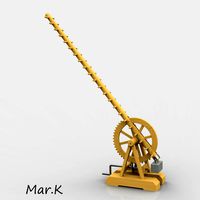
Wood aerial ladder
... available on turbo squid, the world's leading provider of digital 3d models for visualization, films, television, and games.
turbosquid
$19
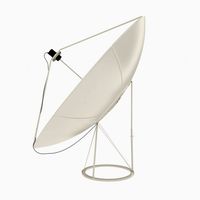
Satellite aerial V4
... available on turbo squid, the world's leading provider of digital 3d models for visualization, films, television, and games.
3d_export
$65
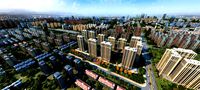
city aerial view
...city aerial view
3dexport
simple rendering of the scene file
Crane
archibase_planet
free
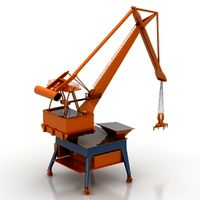
Crane
...rane
archibase planet
crane harbor crane lifting crane port crane
crane 1 - 3d model (*.gsm+*.3ds) for exterior 3d visualization.
archibase_planet
free
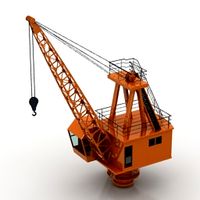
Crane
...rane
archibase planet
crane port crane lifting crane harbor crane
crane 4 - 3d model (*.gsm+*.3ds) for exterior 3d visualization.
archibase_planet
free

Crane
...rane
archibase planet
crane port crane lifting crane harbor crane
crane 2 - 3d model (*.gsm+*.3ds) for exterior 3d visualization.
archibase_planet
free

Crane
...rane
archibase planet
crane harbor crane lifting crane port crane
crane 3 - 3d model (*.gsm+*.3ds) for exterior 3d visualization.
archibase_planet
free
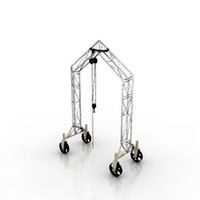
Crane
...crane
archibase planet
crane lifting crane hoisting crane
crane mob n080708 - 3d model for interior 3d visualization.
archibase_planet
free
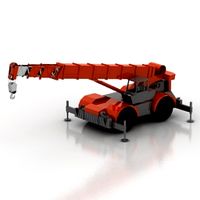
Crane
...e
archibase planet
crane lifting crane hoisting crane
crane n110314 - 3d model (*.gsm+*.3ds+*.max) for exterior 3d visualization.
archibase_planet
free
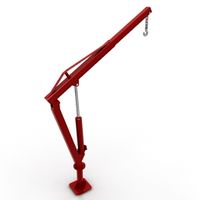
Crane
...base planet
crane lifting crane hoisting crane gibbet
crane n100713 - 3d model (*.gsm+*.3ds+*.max) for exterior 3d visualization.
3d_export
$29
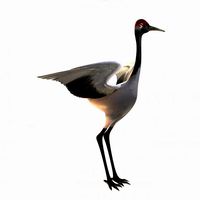
Crane
...crane
3dexport
a cute crane
3d_ocean
$18
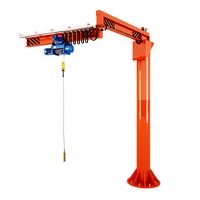
Crane
...crane
3docean
crane lift loader machine work
this is a high poly 3d model crane
archibase_planet
free

Crane
...crane
archibase planet
crane
saddle jib crane cel - 3d model. free download.
Lift
archibase_planet
free
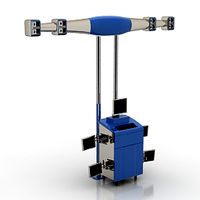
Lift
...lift
archibase planet
lift hoist car lift
lift 1 - 3d model (*.3ds) for interior 3d visualization.
archibase_planet
free
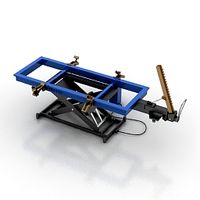
Lift
...lift
archibase planet
lift lifting jack autohoist
lift 2 - 3d model (*.gsm+*.3ds) for interior 3d visualization.
archibase_planet
free

Lift
...lift
archibase planet
lift autohoist car lift hoist
lift 3 - 3d model (*.gsm+*.3ds) for interior 3d visualization.
3d_ocean
$21
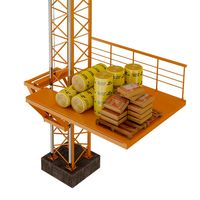
Lift
...lift
3docean
crane industrial lift loader machine outdoor work
lifts with building materials
archibase_planet
free
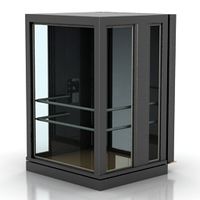
Lift
...lift
archibase planet
lift elevator
lift n050713 - 3d model (*.gsm+*.3ds) for interior 3d visualization.
archibase_planet
free
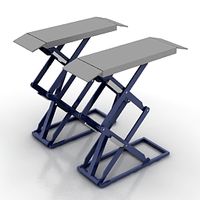
Lift
...lift
archibase planet
lift autohoist hoist
lift for car n240611 - 3d model (*.3ds) for interior 3d visualization.
archibase_planet
free
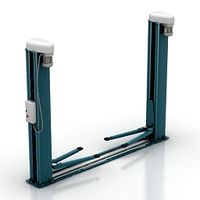
Lift
...lift
archibase planet
lift autohoist hoist
lift for car n020711 - 3d model (*.gsm+*.3ds) for interior 3d visualization.
archibase_planet
free
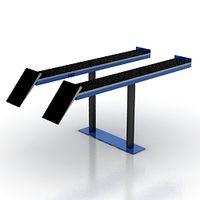
Lift
...lift
archibase planet
autohoist lift hoist
lift car 2 n150111 - 3d model (*.gsm+*.3ds) for interior 3d visualization.
archibase_planet
free
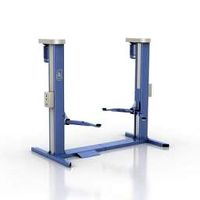
Lift
...lift
archibase planet
car lift car elevator hoist
lift n090709 - 3d model (*.gsm+*.3ds) for interior 3d visualization.
archibase_planet
free
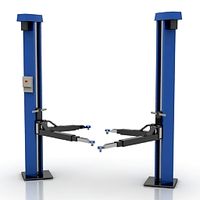
Lift
...lift
archibase planet
lift hoist elevator
lift car 1 n150111 - 3d model (*.gsm+*.3ds) for interior 3d visualization.
Heavy
design_connected
$16
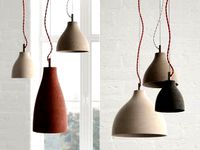
Heavy
...heavy
designconnected
decode heavy computer generated 3d model. designed by hubert, benjamin.
turbosquid
$12
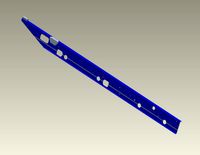
Spar TRAIN-Heavy HEAVY-DUTY
... available on turbo squid, the world's leading provider of digital 3d models for visualization, films, television, and games.
3ddd
$1
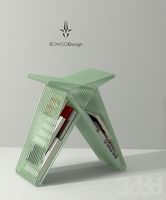
The Heavy Rabbit
...the heavy rabbit
3ddd
табурет
project: heavy rabbit
designed by bongo design
3d_ocean
$40
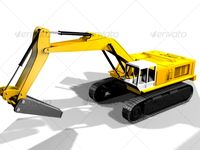
Heavy vehicles
...el this model is created with 3ds max 2009 and content .max (3ds max), size: 7,65 mb this model can be used in any scene. enjoy !
3d_export
$8
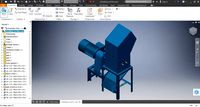
heavy plastic crusher
...heavy plastic crusher
3dexport
heavy plastic crusher
3d_export
$5
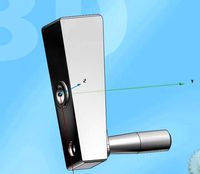
heavy rotation handle
...heavy rotation handle
3dexport
heavy rotation handle
turbosquid
free
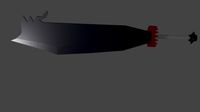
heavy sword
...ord
turbosquid
free 3d model heavy sword for download as fbx on turbosquid: 3d models for games, architecture, videos. (1223423)
turbosquid
free
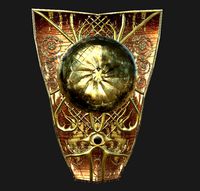
Heavy Shield
...squid
royalty free 3d model heavy shield for download as fbx on turbosquid: 3d models for games, architecture, videos. (1382280)
turbosquid
$42

Heavy Tank
...
royalty free 3d model heavy tank for download as max and fbx on turbosquid: 3d models for games, architecture, videos. (1311230)
turbosquid
$3
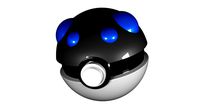
Heavy Ball
...
royalty free 3d model heavy ball for download as ma and obj on turbosquid: 3d models for games, architecture, videos. (1515557)