Thingiverse
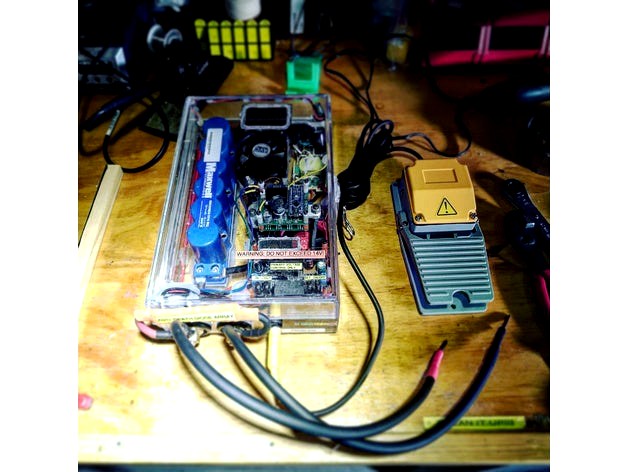
Ultracapacitor Driven, Dual Pulse Spot Welder, a Novel Iteration by wubwub89
by Thingiverse
Last crawled date: 3 years ago
UPDATE (consolidated): Hi everyone. I have yet to find time for a video, mostly due to life pressures, etc, I have zero free time for anything that isn't paying. Please, as I stated in multiple places of this post, you must pay close attention to your primary resistances! Very small bits of resistance accumulating will negatively affect the operation of your welder. I have had more people write me saying the design doesn't work, and they include a picture of a total rats nest using 12 gauge wire. It will never, aside from elevated voltages, work right without really low sub-ohm resistances across the machine's primary circuits. If you have any questions, please read through the guide again before you write me. If you send me a message asking about something that is clearly specified in the guide, I may not be polite. If you have questions about something that is NOT specified in the guide, by all means feel free to write me or comment.
I do not plan to change this design at this time, however, in the near future I MIGHT switch the unit over to a toroid transformer on a 2x15v secondary in parallel and down-regulated for a big boost in charging current. At this time though, I am happy with the conversion efficiency of the large switched supply (it's really just a lightly modded laptop charger), and I am happy with the dwell time between firing, usually around 1-1.5 seconds depending on voltage used.
I have been using the welder consistently in building my own cell packs of all shapes and sizes, along with some other weird spot welding, like ground strapping on projects with metal cases. Everything is working great and consistently without any failures (exception being one full blow-out on an aluminum case cell, my fault for even trying a resistive weld on that!) at about 7500+ individual welds (I don't remember what the actual counter reads exactly).
I have had a few cell packs with mild issues, but not due to the welder. Apparently I picked up a batch of "pure nickel" tabs that were just nickel alloy coated really high iron content steel, and tons of them corroded to hell. I checked, and sure enough, tons of sparks coming from that batch of the grinder wheel. Some of the China direct sellers on various sites will sub in crap parts because they either don't know because they're just a salesman pushing widgets, or don't care. It's probably both, but regardless of all that make sure you check your source for nickel tabs.
UPDATE 2/2/18: I am having some hardware trouble with my camera recording in HD that will hopefully be solved in the next 30 days. I have gotten a few messages about my design not working, well, then you built it incorrectly or your components are out of spec! It's critical to minimize the primary circuit resistance properly! Please note, this is a critical engineering spec design with very little room for error or changes. Just using crimped lugs over soldered lugs may create too much resistance, circumstantially, and you MUST BE USING 4/0 GAUGE PRIMARIES OR LARGER, PERIOD [Edit: To clarify, I am saying this just to make sure anyone who builds the unit with a long primary circuit run doesn't encounter resistance issues]. I have NO trouble creating strong, deep coalescence through multiple boundary layers at low duty. IF you are getting blowouts, turn your primary pulse time and/or voltage down! Once again, this design does not allow for much error, including capacitor/bank quality from previous use and abuse.
UPDATE: After some more testing and production applications, it's working great for certain. However, I am struggling with some certain metals due to their resistance, notably copper and aluminum. I actually blew a hole through the casing of an aluminum LFP battery! (Oops, tossed it in a bag, then an empty paint can, and in the backyard to be safe, it's not reacting, if it was Li-Ion or it would have started thermal runaway and out-gassing potentially). That being said, it's demonstrably safe to use on steel casings as long as you don't lose the reigns on the pulse width and voltage. After investigating later on (when ambient temps were below 40 deg F), approximately a 0.5mm hole was found in the casing.
Hey everyone!
Firstly, This post is a work in progress! While the device is constructed, thoroughly tested, and working great, I will update and expand upon this post over the next month when I have time. Please like and collect to follow! I will be providing a very clear and advanced schematic for the electronics in this configuration. How you choose to build your enclosure and power supplies is totally up to you, but I will show you how to build and operate this type of unit safely. Again, this post will be reformatted, edited, and expanded over the next month. There will also be a detailed YouTube video regarding this methodology. Thank you!
This unit was designed and built by myself, for the purpose of spot welding battery tabs, spot welding small metallic projects, and generally, for providing very large amounts of current in a short period of time when needed.
This product's design is protected under Creative Commons Attribution, please give credit where credit is due!
DISCLAIMER and WARNING
This device utilizes both line AC voltage and extremely dense energy storage through the capacitor bank. AC 85v+ (probably less under the right conditions) with a big current supply is LETHAL when a human being acts as a ground path for the current available. Do not EVER, EVER touch, dismantle, assemble, test, look funny at it, or otherwise work with line voltage unless you know what you are doing! Seriously! The capacitor bank presents a very real, but different threat. The capacitor bank builds a reasonably safe DC voltage current source, which DC voltages below 24 volts can be considered safe, there are still some serious consequences to mishandling. DEAD SHORTS ACROSS HIGH-DENSITY ELDC UNITS WILL CAUSE A FIRE, EXPLOSION, SEVERE PERSONAL INJURY AND PROPERTY LOSS! Seriously, you do not want to dead short one of these units! ELDC shorts will vaporize box wrenches, destroy low impedance circuits, raise your car payment, and make your wife leave you! All kidding aside, please be careful when handing high-current devices, make sure you understand how to prevent traces from forming where they shouldn't, and avoid improperly constructed conductive parts, including wiring, IC's, anything that has a low electrical resistance is potentially an exploding fireball with shrapnel when working with super-high current devices.
So, now that my readers know they can accidentally kill themselves or lose everything in the process of building this device, let's get on with it!
ABSTRACT
The purpose of this article is to define the systems and subsystems of the aforementioned device and their working principles in detail, along with providing a clear, informative, and confusion-free schematic of the system and its subsystems. We will also be discussing material science involving spot-welding with this type of device. This document was written by an engineer, from the perspective of a DIY need to weld battery tabs and small metallic objects that are sensitive to heat. The author is not a professional welder. The writer was simply frustrated with the poor write-ups found on the web about these devices and did not approve of their safety or design effectiveness.
HOW IT WORKS
In principle, this device will adjoin two metallic objects together without the introduction of material (such as a welding rod etc), and generally, without the use of flux. In the case of welding battery tabs, the current can be passed through the tab, into the substrate, back out through the substrate, and back into the tab, in a closed loop, or it can be passed through the tab, and into the substrate. Of course, the polarity can be reversed by changing the probe location and orientation. The results of either method in either polarity configuration will vary greatly based on the resistance of the tab used, the resistance of the target substrate, in addition to overall performance attributable to the overall resistance of the devices current path, along with the ESR of the capacitor. Tab material types and construction will greatly affect the welding procedure, as the current path will differ between different types and methods employed. It's important to familiarize yourself with the type of materials you will be welding together, generally, nickel and steel are my primary targets. Other metals will require more voltage and a longer pulse time in many cases, but this requires further investigation on my part.
WHAT'S IT MADE OF?
This device has a 5.1A digitally controlled and selectable constant voltage/current supply that controls the UC(Ultracapacitor) bank primary voltage, a microcontroller that controls the ON/OFF pulse time for both a small pulse to 'preheat' the materials and build an (ideally) gapless current path, then a larger pulse to complete the weld. Current paths with gaps will cause material breakdown and substrate erosion, which usually occurs when there is a loud pop, and very small pieces of molten metal go flying. In parallel with the primary welding circuit, there is a switchable 5-ohm resistor array (two 100w, 10-ohm resistors in parallel) with thermal insulation active cooling. The entire device is powered by a salvaged and reconfigured 19.5v+ laptop power supply, with each component individually voltage regulated and monitored as follows: the microcontroller and MOSFET array controller is powered by a dedicated L7812cv (12v+) regulator circuit, and the case cooling fan is regulated down to 9.5v+ with a variable CV regulator. Also, on the front-right of the device, you may notice a LED cluster, along with a LED light bar labeled 'Problem', both of these operate in parallel with the primary circuit, but they vary in how they are hooked up, we'll go over the data acquisition later on.
All of the wires in this unit is stranded 20, 18, 16, 12, 8, 6, or 4/0 AWG wire, with PVC or Silicone insulation. All of the high-current lugs are soldered instead of crimped. This is a personal preference, and since the device is to regarded as immobile and we're not expecting to experience multiple G's of vibrations, also, our high current flow will be well below the time needed to get the joints flowing again. This comes from professional knowledge and experience, where as long as the thermal loss from resistance remains lower than the thermal dissipation, to keep it simple, this device will not heat up terminals fast or high enough. Also, we don't want to worry about moisture oxidizing our copper wire, and potentially causing a complete or partial break down the line, as a free-swinging wire ready to carry up to 1400 amps is a terrible situation (See the section about exploding fireballs). We want to build a device that will, optimistically, have properly designed subsystem failure points that will prevent a catastrophic failure. Just about everything besides the primary circuit is fused, just in case of a short. The dissipation of the UC bank through a small gauge wire will almost instantly start a fire. ( I don't take this type of energy storage lightly, and neither should you!)
In my application, the Maxwell 58F UC(lovingly nicknamed, FireBoom9000) was chosen due to its low ESR (approximately 0.22mΩ), consisting of six 2.7v 500F supercapacitors placed in series on a protection board (which prevents overcharging, promotes voltage potential balance, and hopefully, reverse voltage spikes) and allows for a peak storage voltage of 16.2v, which we will never reach due to both energy requirements, and the 14v limitation of the TVS diode on the MOSFET array (more on that later). Also, the Maxwell 58F unit comes in this nicely packaged blue/gray ABS case for safety. Other types of storage could have been chosen, but I preferred this unit for its size and electrical characteristics. It's entirely unnecessary to use 6 3000F BoostCaps or something equally ridiculous in size. At about 12v, with a 25ms primary pulse, and a 15% short pulse (15% of 25ms, variable on the controller), we get a voltage drop of around 0.43v per firing. With the 5.1A supply set to 4A @ 12v, it takes about 1.5-2 seconds to get back to 12v in the UC bank. I finished my first 18650 Li-Ion 4s1p pack in about 20 minutes, WITH a BMS, without any bad welds.
Now, let's talk about the pulse control unit. When I started this endeavor, I wanted to build my own, write my own board files in Eagle CAD, send them out to one of the manufacturers, wait 30-60 days for my professional 4 layer boards to come back to me, write the software for an ATMEL 348p, prototype, break it, rinse and repeat. Then I found a wonderful source for a unit that was already produced, one with almost the exact specification I came up with (in my head) for this device. I decided that it was in my best interests and time conservation to purchase a manufactured unit from http://malectrics.eu , sold by Marc Shoenfleiesh for around $105USD (Shipped to Chicago). After talking with Marc through a few emails, we both were in agreeance to the function of this unit utilizing a UC bank in place of a lead-acid battery without trouble (He is a nice guy, very polite and helpful, I recommend his products). I also purchased his preassembled welding probes since they were around the same price to build them here, they're very nice. The control unit is powered by an external L7812cv without a common line attached, utilizing the module primary common for that circuit. This unit utilizes eight IRFB7430 MOSFET IC's in parallel to manage the current pulses. (Datasheet here: https://www.infineon.com/dgdl/irfb7430pbf.pdf?fileId=5546d462533600a4015356169bcd1e53) for current switching. This array, when closed, provides around 150 ohms resistance, allowing a handful of my subsystems to function in their own unique ways depending on their placement on the common bus. In my design, there are two common busses, one is not switched, the other is 150 ohm to the primary circuit when MOSFET array is in an 'open' state. The unit also includes a small OLED screen and a rotary encoder for control selection. There is also an 'Auto-pulse' function, but I will not use it with this device, ever. I utilize a (very obnoxious and unnecessarily large, thanks, Amazon Prime) footswitch as a trigger for this device. It's removable and uses a TS 1/4" bulkhead on the front of the case.
The outboard assembly includes the welding probes themselves, which are 6 gauge wire, terminated to thick copper electrodes cut to points. They work great, you can even see them dance from the current flow!
This one is important, to protect EVERYTHING from flyback current, I built a rather beefy TVS diode array. That's the orange shrink-wrapped guy labeled "Anti-Death Diode Array" on the two current bulkheads. This is a reverse facing diode that will allow inductive current to pass backward at the head of the circuit after the MOSFET array closes, causing an extreme reversal of current. Think of it as analogous to "water hammer" in the plumbing of your home; when you turn off the water flow rapidly, you hear a bang in the wall. This is the tendency of the water to try to keep flowing, attempt to compress, and immediately flow backward, causing cavitation in the pipes. When that vacuum bubble collapses, we hear that bang, at risk of gross oversimplification. By placing our very large diode array in this position, we are protecting all of our circuitry from flyback current by allowing this very strong inductive pressure to "flyback" from one probe to the other. The specifications of this unit will be listed later on.
On to the boring stuff. However, it's still fairly important.
The case is made from two acrylic drawer organizers that can be found on Amazon Prime, I cemented a 12" acrylic hinge, and an acrylic latch onto these, and made a decent, non-conductive case for pretty cheap. Both the primary cc/cv unit and the pulse control unit are on custom cut nylon standoffs from the top of the case. These are secured with vanadium steel M3 cap-heads of varying length, which long enough to provide a secure hold to the case.
Now, we're going to talk about an extremely sensitive subject for myself; glue. I don't like glue. Glue doesn't like me. It's a necessary evil in budget assemblies and time constraints. There are only two types of adhesives used in this entire project; methyl ethyl ketone (MEK) cement, and high-temperature hot glue. Both are entirely non-conductive and cheap. MEK cement is a solvent cement designed for plastics, it works extremely well at binding acrylic, among a few other things. It is very tough and almost entirely rigid after curing, too. This was utilized for all of the plastic to plastic bonds in this project. Hot glue was used for all of the wiring positionings at the edges on the case, some added protection in certain areas against catastrophic shorts, and for a few of the more temporary mountings of components. I don't want to permanently cement a power supply in place to have it fail and need replacing. You may also note that I stayed away from silicone based products. I do not always approve of room temperature vulcanizing rubber for use in electrical projects, due to the insulative variance that seems to occur with air bubbles within the RTV bead. Unless it needs to be permanent for certain, and you're pressing the parts together firmly (e.g., hand-tightening a water pump while the RTV starts to vulcanize) I do not recommend a silicone, and for this project, absolutely no silicone (that does not include silicone wiring insulation, different process).
That's all for now, I will update with a complete electrical schematic and a detailed video mirroring this insight when I get around to it.
Thanks for reading!
-Alex
I do not plan to change this design at this time, however, in the near future I MIGHT switch the unit over to a toroid transformer on a 2x15v secondary in parallel and down-regulated for a big boost in charging current. At this time though, I am happy with the conversion efficiency of the large switched supply (it's really just a lightly modded laptop charger), and I am happy with the dwell time between firing, usually around 1-1.5 seconds depending on voltage used.
I have been using the welder consistently in building my own cell packs of all shapes and sizes, along with some other weird spot welding, like ground strapping on projects with metal cases. Everything is working great and consistently without any failures (exception being one full blow-out on an aluminum case cell, my fault for even trying a resistive weld on that!) at about 7500+ individual welds (I don't remember what the actual counter reads exactly).
I have had a few cell packs with mild issues, but not due to the welder. Apparently I picked up a batch of "pure nickel" tabs that were just nickel alloy coated really high iron content steel, and tons of them corroded to hell. I checked, and sure enough, tons of sparks coming from that batch of the grinder wheel. Some of the China direct sellers on various sites will sub in crap parts because they either don't know because they're just a salesman pushing widgets, or don't care. It's probably both, but regardless of all that make sure you check your source for nickel tabs.
UPDATE 2/2/18: I am having some hardware trouble with my camera recording in HD that will hopefully be solved in the next 30 days. I have gotten a few messages about my design not working, well, then you built it incorrectly or your components are out of spec! It's critical to minimize the primary circuit resistance properly! Please note, this is a critical engineering spec design with very little room for error or changes. Just using crimped lugs over soldered lugs may create too much resistance, circumstantially, and you MUST BE USING 4/0 GAUGE PRIMARIES OR LARGER, PERIOD [Edit: To clarify, I am saying this just to make sure anyone who builds the unit with a long primary circuit run doesn't encounter resistance issues]. I have NO trouble creating strong, deep coalescence through multiple boundary layers at low duty. IF you are getting blowouts, turn your primary pulse time and/or voltage down! Once again, this design does not allow for much error, including capacitor/bank quality from previous use and abuse.
UPDATE: After some more testing and production applications, it's working great for certain. However, I am struggling with some certain metals due to their resistance, notably copper and aluminum. I actually blew a hole through the casing of an aluminum LFP battery! (Oops, tossed it in a bag, then an empty paint can, and in the backyard to be safe, it's not reacting, if it was Li-Ion or it would have started thermal runaway and out-gassing potentially). That being said, it's demonstrably safe to use on steel casings as long as you don't lose the reigns on the pulse width and voltage. After investigating later on (when ambient temps were below 40 deg F), approximately a 0.5mm hole was found in the casing.
Hey everyone!
Firstly, This post is a work in progress! While the device is constructed, thoroughly tested, and working great, I will update and expand upon this post over the next month when I have time. Please like and collect to follow! I will be providing a very clear and advanced schematic for the electronics in this configuration. How you choose to build your enclosure and power supplies is totally up to you, but I will show you how to build and operate this type of unit safely. Again, this post will be reformatted, edited, and expanded over the next month. There will also be a detailed YouTube video regarding this methodology. Thank you!
This unit was designed and built by myself, for the purpose of spot welding battery tabs, spot welding small metallic projects, and generally, for providing very large amounts of current in a short period of time when needed.
This product's design is protected under Creative Commons Attribution, please give credit where credit is due!
DISCLAIMER and WARNING
This device utilizes both line AC voltage and extremely dense energy storage through the capacitor bank. AC 85v+ (probably less under the right conditions) with a big current supply is LETHAL when a human being acts as a ground path for the current available. Do not EVER, EVER touch, dismantle, assemble, test, look funny at it, or otherwise work with line voltage unless you know what you are doing! Seriously! The capacitor bank presents a very real, but different threat. The capacitor bank builds a reasonably safe DC voltage current source, which DC voltages below 24 volts can be considered safe, there are still some serious consequences to mishandling. DEAD SHORTS ACROSS HIGH-DENSITY ELDC UNITS WILL CAUSE A FIRE, EXPLOSION, SEVERE PERSONAL INJURY AND PROPERTY LOSS! Seriously, you do not want to dead short one of these units! ELDC shorts will vaporize box wrenches, destroy low impedance circuits, raise your car payment, and make your wife leave you! All kidding aside, please be careful when handing high-current devices, make sure you understand how to prevent traces from forming where they shouldn't, and avoid improperly constructed conductive parts, including wiring, IC's, anything that has a low electrical resistance is potentially an exploding fireball with shrapnel when working with super-high current devices.
So, now that my readers know they can accidentally kill themselves or lose everything in the process of building this device, let's get on with it!
ABSTRACT
The purpose of this article is to define the systems and subsystems of the aforementioned device and their working principles in detail, along with providing a clear, informative, and confusion-free schematic of the system and its subsystems. We will also be discussing material science involving spot-welding with this type of device. This document was written by an engineer, from the perspective of a DIY need to weld battery tabs and small metallic objects that are sensitive to heat. The author is not a professional welder. The writer was simply frustrated with the poor write-ups found on the web about these devices and did not approve of their safety or design effectiveness.
HOW IT WORKS
In principle, this device will adjoin two metallic objects together without the introduction of material (such as a welding rod etc), and generally, without the use of flux. In the case of welding battery tabs, the current can be passed through the tab, into the substrate, back out through the substrate, and back into the tab, in a closed loop, or it can be passed through the tab, and into the substrate. Of course, the polarity can be reversed by changing the probe location and orientation. The results of either method in either polarity configuration will vary greatly based on the resistance of the tab used, the resistance of the target substrate, in addition to overall performance attributable to the overall resistance of the devices current path, along with the ESR of the capacitor. Tab material types and construction will greatly affect the welding procedure, as the current path will differ between different types and methods employed. It's important to familiarize yourself with the type of materials you will be welding together, generally, nickel and steel are my primary targets. Other metals will require more voltage and a longer pulse time in many cases, but this requires further investigation on my part.
WHAT'S IT MADE OF?
This device has a 5.1A digitally controlled and selectable constant voltage/current supply that controls the UC(Ultracapacitor) bank primary voltage, a microcontroller that controls the ON/OFF pulse time for both a small pulse to 'preheat' the materials and build an (ideally) gapless current path, then a larger pulse to complete the weld. Current paths with gaps will cause material breakdown and substrate erosion, which usually occurs when there is a loud pop, and very small pieces of molten metal go flying. In parallel with the primary welding circuit, there is a switchable 5-ohm resistor array (two 100w, 10-ohm resistors in parallel) with thermal insulation active cooling. The entire device is powered by a salvaged and reconfigured 19.5v+ laptop power supply, with each component individually voltage regulated and monitored as follows: the microcontroller and MOSFET array controller is powered by a dedicated L7812cv (12v+) regulator circuit, and the case cooling fan is regulated down to 9.5v+ with a variable CV regulator. Also, on the front-right of the device, you may notice a LED cluster, along with a LED light bar labeled 'Problem', both of these operate in parallel with the primary circuit, but they vary in how they are hooked up, we'll go over the data acquisition later on.
All of the wires in this unit is stranded 20, 18, 16, 12, 8, 6, or 4/0 AWG wire, with PVC or Silicone insulation. All of the high-current lugs are soldered instead of crimped. This is a personal preference, and since the device is to regarded as immobile and we're not expecting to experience multiple G's of vibrations, also, our high current flow will be well below the time needed to get the joints flowing again. This comes from professional knowledge and experience, where as long as the thermal loss from resistance remains lower than the thermal dissipation, to keep it simple, this device will not heat up terminals fast or high enough. Also, we don't want to worry about moisture oxidizing our copper wire, and potentially causing a complete or partial break down the line, as a free-swinging wire ready to carry up to 1400 amps is a terrible situation (See the section about exploding fireballs). We want to build a device that will, optimistically, have properly designed subsystem failure points that will prevent a catastrophic failure. Just about everything besides the primary circuit is fused, just in case of a short. The dissipation of the UC bank through a small gauge wire will almost instantly start a fire. ( I don't take this type of energy storage lightly, and neither should you!)
In my application, the Maxwell 58F UC(lovingly nicknamed, FireBoom9000) was chosen due to its low ESR (approximately 0.22mΩ), consisting of six 2.7v 500F supercapacitors placed in series on a protection board (which prevents overcharging, promotes voltage potential balance, and hopefully, reverse voltage spikes) and allows for a peak storage voltage of 16.2v, which we will never reach due to both energy requirements, and the 14v limitation of the TVS diode on the MOSFET array (more on that later). Also, the Maxwell 58F unit comes in this nicely packaged blue/gray ABS case for safety. Other types of storage could have been chosen, but I preferred this unit for its size and electrical characteristics. It's entirely unnecessary to use 6 3000F BoostCaps or something equally ridiculous in size. At about 12v, with a 25ms primary pulse, and a 15% short pulse (15% of 25ms, variable on the controller), we get a voltage drop of around 0.43v per firing. With the 5.1A supply set to 4A @ 12v, it takes about 1.5-2 seconds to get back to 12v in the UC bank. I finished my first 18650 Li-Ion 4s1p pack in about 20 minutes, WITH a BMS, without any bad welds.
Now, let's talk about the pulse control unit. When I started this endeavor, I wanted to build my own, write my own board files in Eagle CAD, send them out to one of the manufacturers, wait 30-60 days for my professional 4 layer boards to come back to me, write the software for an ATMEL 348p, prototype, break it, rinse and repeat. Then I found a wonderful source for a unit that was already produced, one with almost the exact specification I came up with (in my head) for this device. I decided that it was in my best interests and time conservation to purchase a manufactured unit from http://malectrics.eu , sold by Marc Shoenfleiesh for around $105USD (Shipped to Chicago). After talking with Marc through a few emails, we both were in agreeance to the function of this unit utilizing a UC bank in place of a lead-acid battery without trouble (He is a nice guy, very polite and helpful, I recommend his products). I also purchased his preassembled welding probes since they were around the same price to build them here, they're very nice. The control unit is powered by an external L7812cv without a common line attached, utilizing the module primary common for that circuit. This unit utilizes eight IRFB7430 MOSFET IC's in parallel to manage the current pulses. (Datasheet here: https://www.infineon.com/dgdl/irfb7430pbf.pdf?fileId=5546d462533600a4015356169bcd1e53) for current switching. This array, when closed, provides around 150 ohms resistance, allowing a handful of my subsystems to function in their own unique ways depending on their placement on the common bus. In my design, there are two common busses, one is not switched, the other is 150 ohm to the primary circuit when MOSFET array is in an 'open' state. The unit also includes a small OLED screen and a rotary encoder for control selection. There is also an 'Auto-pulse' function, but I will not use it with this device, ever. I utilize a (very obnoxious and unnecessarily large, thanks, Amazon Prime) footswitch as a trigger for this device. It's removable and uses a TS 1/4" bulkhead on the front of the case.
The outboard assembly includes the welding probes themselves, which are 6 gauge wire, terminated to thick copper electrodes cut to points. They work great, you can even see them dance from the current flow!
This one is important, to protect EVERYTHING from flyback current, I built a rather beefy TVS diode array. That's the orange shrink-wrapped guy labeled "Anti-Death Diode Array" on the two current bulkheads. This is a reverse facing diode that will allow inductive current to pass backward at the head of the circuit after the MOSFET array closes, causing an extreme reversal of current. Think of it as analogous to "water hammer" in the plumbing of your home; when you turn off the water flow rapidly, you hear a bang in the wall. This is the tendency of the water to try to keep flowing, attempt to compress, and immediately flow backward, causing cavitation in the pipes. When that vacuum bubble collapses, we hear that bang, at risk of gross oversimplification. By placing our very large diode array in this position, we are protecting all of our circuitry from flyback current by allowing this very strong inductive pressure to "flyback" from one probe to the other. The specifications of this unit will be listed later on.
On to the boring stuff. However, it's still fairly important.
The case is made from two acrylic drawer organizers that can be found on Amazon Prime, I cemented a 12" acrylic hinge, and an acrylic latch onto these, and made a decent, non-conductive case for pretty cheap. Both the primary cc/cv unit and the pulse control unit are on custom cut nylon standoffs from the top of the case. These are secured with vanadium steel M3 cap-heads of varying length, which long enough to provide a secure hold to the case.
Now, we're going to talk about an extremely sensitive subject for myself; glue. I don't like glue. Glue doesn't like me. It's a necessary evil in budget assemblies and time constraints. There are only two types of adhesives used in this entire project; methyl ethyl ketone (MEK) cement, and high-temperature hot glue. Both are entirely non-conductive and cheap. MEK cement is a solvent cement designed for plastics, it works extremely well at binding acrylic, among a few other things. It is very tough and almost entirely rigid after curing, too. This was utilized for all of the plastic to plastic bonds in this project. Hot glue was used for all of the wiring positionings at the edges on the case, some added protection in certain areas against catastrophic shorts, and for a few of the more temporary mountings of components. I don't want to permanently cement a power supply in place to have it fail and need replacing. You may also note that I stayed away from silicone based products. I do not always approve of room temperature vulcanizing rubber for use in electrical projects, due to the insulative variance that seems to occur with air bubbles within the RTV bead. Unless it needs to be permanent for certain, and you're pressing the parts together firmly (e.g., hand-tightening a water pump while the RTV starts to vulcanize) I do not recommend a silicone, and for this project, absolutely no silicone (that does not include silicone wiring insulation, different process).
That's all for now, I will update with a complete electrical schematic and a detailed video mirroring this insight when I get around to it.
Thanks for reading!
-Alex
Similar models
thingiverse
free
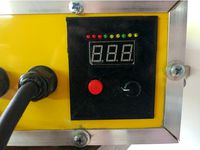
Front panel for spot welder NY-D02X, control panel by ac3as
...tps://a.aliexpress.com/_budbet
you need to make a box, cut a sqare for controller, screw it and glue printed front panel to case.
thingiverse
free
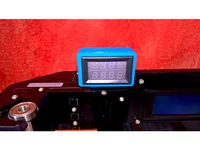
Voltage / Current display-case - for GearBest device (china) by felge4fingers
...oltage/current display from gearbest.
it's possible to mount it with two or three screws anywhere you find a possible place..
thingiverse
free
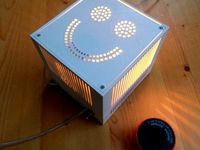
Bob Beck magnet pulser by LeonKnook
...e device from the mains. the capacitors are discharged this way. i'm not responsible for any injuries using this publication.
thingiverse
free
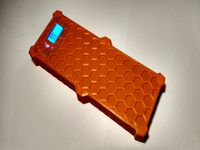
Power bank hexagon case
...verything glue frontplate or mount it in some different way ( magnets or screws, i have been very lazy so i just glued it up ;) )
thingiverse
free
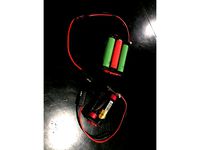
18650 Battery Holder/Sled x1,2,3,4 by ScottieD369
...gative(-) side of battery and spring get hot. if case then go back to tab,tab system. (i will make a set of those in future post)
thingiverse
free
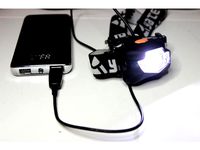
3xAAA battery adapter (for headlamp) by parek
... screws. presolder the screws before screwing it into the adapter.
additionaly you can glue the contacts and cables with gluegun.
grabcad
free

LT-300-S-SP2
...s, control circuits, breakers, robots, and measurement systems, industrial motor installations, electrical transport, substations
thingiverse
free
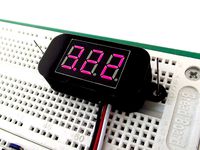
Mini Digital Volt Meter Case by TikiLuke
...marked v20d-3p-11 on the back and hopefully it fits similar ...
cg_trader
$4
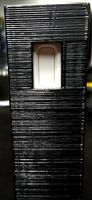
Xiaomi 20000 mAh Power Bank Case With Cap | 3D
...devices. also the cap is made so you can see the battery indicator so you never have to guess about the charge of the power bank.
thingiverse
free
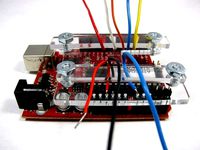
Wire Harness Shield by builttospec
...lled. there's also plenty of space to access the reset button and the isp header on my duemilanove board should i need them.
Ultracapacitor
thingiverse
free
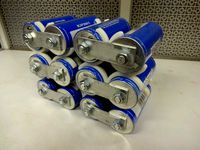
Ultracapacitor Racking by jpearce
...ability technology research group.
for similar see the open-source lab how to build your own hardware and reduce research costs
thingiverse
free
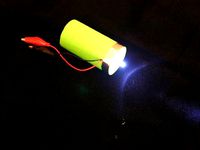
Ultracapacitor Flashlight/Night Light by mrigsby
...mrigsby
thingiverse
this is a flashlight powered by an ultra capacitor. full instructions will be available on instructables.com
thingiverse
free
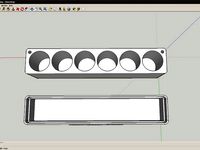
350 Farad 16.2 Volt Ultracapacitor Pack by firepinto
...tube user lasersaber's work.
part number and info for ultracaps:
maxwell
dcell
350 farad 2.7 vdc
m/n: bcap0350 e270 t11 10
thingiverse
free
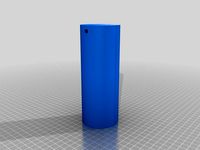
Artificial Muscle Building Tools and Parts by LupusMechanicus
...for building the muscles i am working on at https://hackaday.io/project/4726-artificial-muscles-and-li-s-si-ultracapacitor ...
thingiverse
free
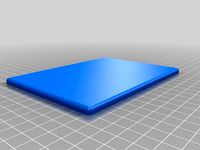
super capacitor battery housing by TThompson
...capacitor battery housing by tthompson thingiverse housing for this http://www.ebay.com/itm/ultracapacitormodule-kit-battery-eliminator-car-audio-starting-remote-solar/301381327649?_trksid=p2047675.c100009.m1982&_trkparms=aid%3d777000%26algo%3daba.mbe%26ao%3d1%26asc%3d34575%26meid%3df88811c26de94f7c98d91434f617c5e2%26pid%3d100009%26rk%3d1%26rkt%3d1%26mehot%3dag%26sd%3d300945126145 ...
thingiverse
free
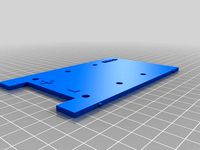
Super Capacitor Bank Enclosure by N3RDPWR
...this is an enclosure for this super capacitor bank: https://www.ebay.com/itm/ultracapacitormodule-kit-battery-eliminator-car-audio-starting-remote-solar/371669580302?sspagename=strk%3amebidx%3ait&_trksid=p2060353.m1438.l2649 the cell and box part needs to be glued...
thingiverse
free
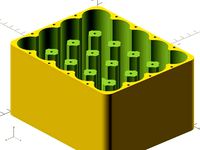
Customizable Supercapacitor Enclosure by RTF671
...rtf671 thingiverse this is an enclosure for supercapacitor (aka ultracapacitor) or similar battery cell shaped objects. it was made...
grabcad
free

ULTRACAPACITOR
...ultracapacitor
grabcad
ultracapacitor 350f / 2,5v / l 64,9mm x dia 33,3mm
grabcad
free

3V, 450F Ultracapacitor, TPLH-3R0-450SS35X71
...ta_sheet.php?i=tplh-3r0/450ss35x71
buy link:
https://www.digikey.com/en/products/detail/tecate-group/tplh-3r0-450ss35x71/9930287
Wubwub89
thingiverse
free
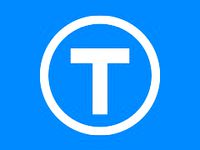
608 Bearing(8mm) to 3mm stabilizer by wubwub89
...
a simple straight through adapter for 608 sized bearings, will fit others. the width of the insert is approximately 13 mm total.
thingiverse
free
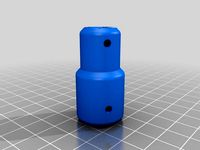
5mm to 8mm heavy duty coupler by wubwub89
...nt adapter/coupler for a 5mm shaft to 8mm leadscrew.
the design utilizes six m3 cap-heads and nuts to bind and locate the shafts.
thingiverse
free
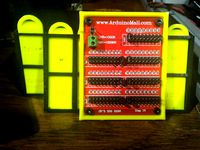
Decade resistor half-case by wubwub89
...e unit. the unit is from arduinomall.com, zero to 999,999 ohms. i have left enough room to remove jumpers, will add a photo soon.
thingiverse
free
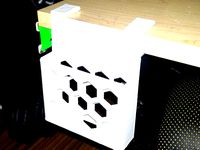
Universal Phone holder for Desk (90deg, 15mm) by wubwub89
...ere is a provision for a charger in the bottom center. accepts phones up to 80mm+ by 15mm+, scale before slicing for other sizes.
thingiverse
free
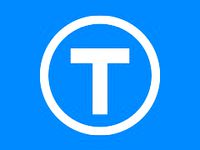
Single switch mount universal, for US switches by wubwub89
...for line voltage ac! only acceptable for low voltage ac/dc projects that can use a standard 120 vac switch!
update: fixed bad stl
thingiverse
free
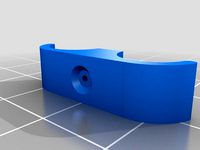
Simple cable anchor by wubwub89
...stener, ream appropriately. if you would like an additional change, post it in the comments, i will add more versions by request.
thingiverse
free
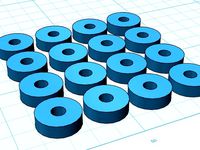
Wide M3 x 3mm spacers by wubwub89
...ed for use on a drone build, i will be printing these with tpu, other materials should work just as well.
id 3.2mm
od 10mm
h 3mm
thingiverse
free

Generic laptop stand (12"+ printers only) by wubwub89
...rinting, you may wish to add some non-skid materials to the top and bottom. as this is universal, it is designed without notches.
thingiverse
free
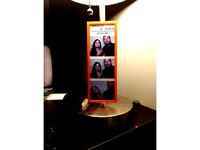
Clip on photo-booth style photo frame by wubwub89
...uture, feel free to request in the comments section, i will get to it when i have free time. tips help for prioritizing requests!
thingiverse
free
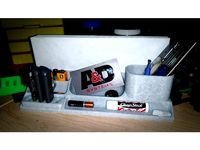
Basic Desk Organizer (Fits 8.5x11" envelope) by wubwub89
... print the first unit!
thanks! please note, these are not for commercial use, personal use only with the cc license of this file!
Welder
3d_export
$5
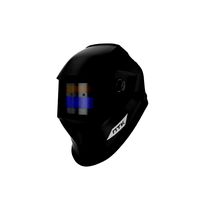
welder mask
...welder mask
3dexport
welder mask for your project
turbosquid
$15
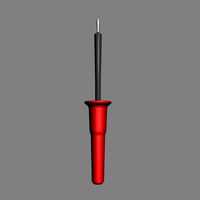
Tin welder
... available on turbo squid, the world's leading provider of digital 3d models for visualization, films, television, and games.
turbosquid
$12
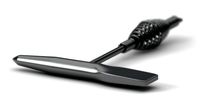
Welder Hammer
... available on turbo squid, the world's leading provider of digital 3d models for visualization, films, television, and games.
turbosquid
$3
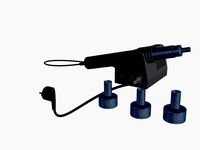
hot air welder
...ty free 3d model hot air welder for download as blend and fbx on turbosquid: 3d models for games, architecture, videos. (1691598)
3ddd
free
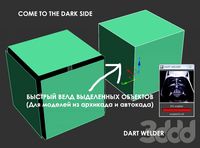
DART WELDER
...dart welder
3ddd
weld'ит вертексы выделенных объектов. бывает полезно для моделей из автокада и архикада.
3d_export
$23
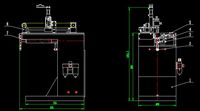
300 straight seam welder full set of CAD drawings
...300 straight seam welder full set of cad drawings
3dexport
300 straight seam welder full set of cad drawings
3d_ocean
$16
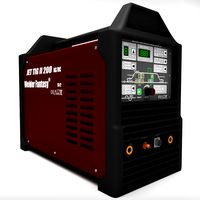
MIG Welder Fantasy
...ith all applied materials: - textures formats: tif (x8), psd (x7) - textures size: x512 (x4), x1024 (x2), x2048 (x1), x4096 (1...
3d_export
$20
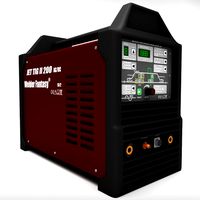
MIG Welder Fantasy 3D Model
...rode wire coated repair mig tig mag mma machine device garage industrial tool
mig welder fantasy 3d model kreatura 92383 3dexport
cg_studio
$19
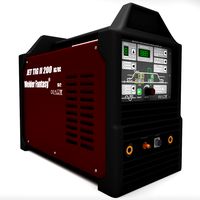
MIG Welder Fantasy3d model
...at gas oxygen
.obj .max .fbx .3ds - mig welder fantasy 3d model, royalty free license available, instant download after purchase.
3d_export
$25
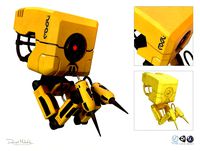
robot welder pbr
... support .fbx format, please use 3ds format; .obj, format was exported from 3ds max. the geometry for .obj format is set to tris.
Novel
3d_export
$10
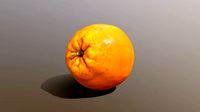
Novel Orange
...novel orange
3dexport
3ddd
$1
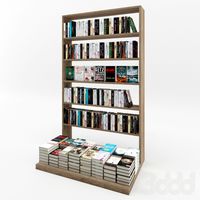
book, novels, thrillers
...book, novels, thrillers
3ddd
книга , стеллаж
book, novels, thrillers
turbosquid
$6
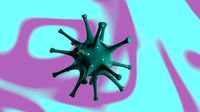
Novel Coronavirus
...d model novel coronavirus for download as obj, blend, and dae on turbosquid: 3d models for games, architecture, videos. (1505188)
3ddd
free
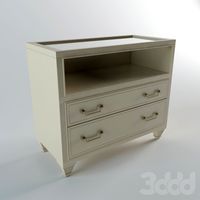
Novel Idea Caracole
...novel idea caracole
3ddd
novel idea , тумба
размеры 38w x 20d x 29.5h
cg_studio
$20
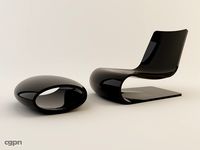
Novelle Vague3d model
...elle vague3d model
cgstudio
.3ds .max - novelle vague 3d model, royalty free license available, instant download after purchase.
3d_ocean
$9
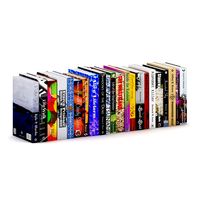
Novel Books 3
...eparately and each have unique texture map on front and back cover. also to make your work easier this model comes in three va...
3d_ocean
$9
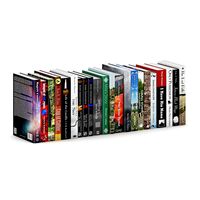
Novel Books 2
...eparately and each have unique texture map on front and back cover. also to make your work easier this model comes in three va...
3d_ocean
$9
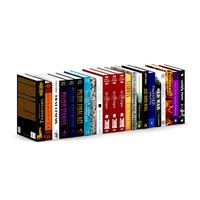
Novel Books 4
...eparately and each have unique texture map on front and back cover. also to make your work easier this model comes in three va...
3d_ocean
$9
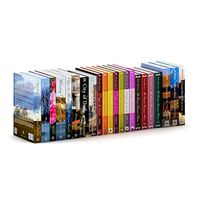
Novel Books 1
...eparately and each have unique texture map on front and back cover. also to make your work easier this model comes in three va...
turbosquid
$9
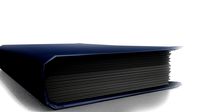
Low Poly Novel Book
... available on turbo squid, the world's leading provider of digital 3d models for visualization, films, television, and games.
Pulse
turbosquid
$7
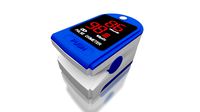
pulse oximeter
...uid
royalty free 3d model pulse oximeter for download as max on turbosquid: 3d models for games, architecture, videos. (1668242)
3d_export
$6
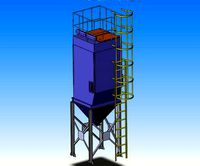
of pulse bag filter
...of pulse bag filter
3dexport
3d model of pulse bag filter
turbosquid
$25

Pulse Cannon
... free 3d model pulse cannon for download as max, fbx, and obj on turbosquid: 3d models for games, architecture, videos. (1559556)
turbosquid
free
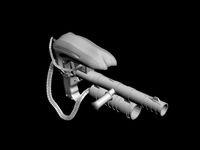
pulse canon
... available on turbo squid, the world's leading provider of digital 3d models for visualization, films, television, and games.
3d_ocean
$15
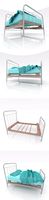
Unmade BED with pulsings
...tal body ,wood base,pulsing elements ,pellows ,unmade bed and all components, all used materials are included sketchup file in...
3d_export
$16
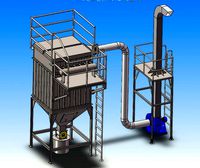
of bag pulse bag filter
...of bag pulse bag filter
3dexport
3d model of bag pulse bag filter
turbosquid
$5
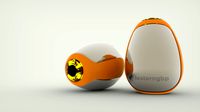
eggy pulse detector
...yalty free 3d model eggy pulse detector for download as sldas on turbosquid: 3d models for games, architecture, videos. (1405234)
3d_export
$10
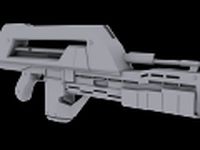
M4A1-Pulse rifle 3D Model
...m4a1-pulse rifle 3d model
3dexport
alien m4a1 pulse pulserifle rifle
m4a1-pulse rifle 3d model slottet 100562 3dexport
turbosquid
$15

M4 Pulse Rifle
... available on turbo squid, the world's leading provider of digital 3d models for visualization, films, television, and games.
turbosquid
$10
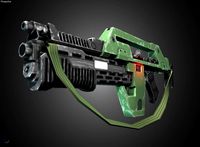
m41a pulse rifle
... available on turbo squid, the world's leading provider of digital 3d models for visualization, films, television, and games.
Driven
turbosquid
$50
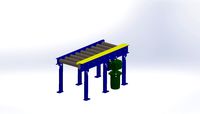
CHAIN DRIVEN CONVEYOR
... available on turbo squid, the world's leading provider of digital 3d models for visualization, films, television, and games.
3d_export
free
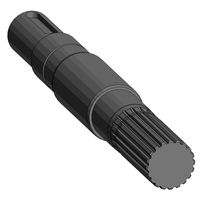
driven shaft of the lump crusher
...driven shaft of the lump crusher
3dexport
3d_export
$27
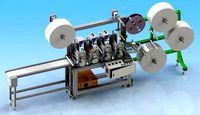
n95 full servo driven mask printer
...n95 full servo driven mask printer
3dexport
n95 full servo driven mask printer
turbosquid
$16
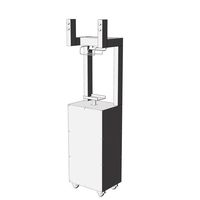
(Project) Food packing helper machine with holding clamp and press table driven by an actuator
... available on turbo squid, the world's leading provider of digital 3d models for visualization, films, television, and games.
3d_export
$47
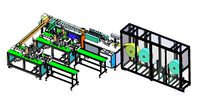
the fifth generation of one driven two new mask machine
...ing, lamination, pressing, ear band tapping, ultrasonic, etc. the structure of the model is detailed, including model parameters.
3d_export
$15
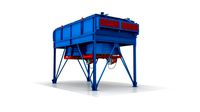
industrial belt-driven air cooler
...leaning up necessary, just drop your models into the scene and start rendering/texturing. no special plugin needed to open scene.
3d_export
free
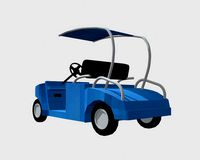
golf cart
...golf cart 3dexport golf cart for golfers to be driven in...
3d_export
$10
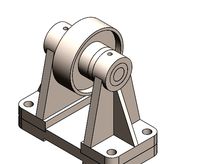
design and assembly of pulley
...pulley 3d model which is used for drive and driven ...
archive3d
free
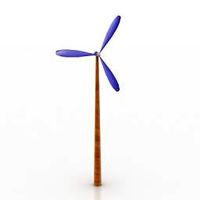
Windmill 3D Model
...windmill 3d model archive3d wind turbine wind-driven powerplant wind-electric set windmill n181208 - 3d model (*.gsm+*.3ds)...
3d_export
$30
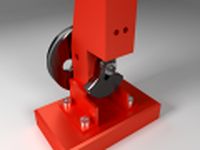
Compressed Air Engine 3D Model
...motor flywheel shaft camshaft piston valve block engineering compressed-air driven compressed air engine 3d model zenmunster 92451...
Spot
archibase_planet
free
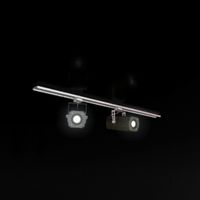
Spot
...spot
archibase planet
luminaire spot candlelight
spot n070308 - 3d model (*.gsm+*.3ds) for interior 3d visualization.
archibase_planet
free
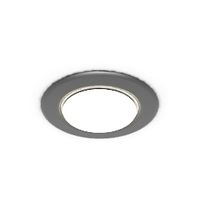
Spot
...spot
archibase planet
lighting luminaire candlelight
spot - 3d model (*.gsm+*.3ds) for interior 3d visualization.
3d_export
$5
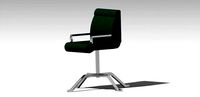
spot chair
...spot chair
3dexport
modern spot chair
3ddd
$1
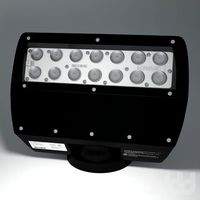
light Spot
...light spot
3ddd
ecosense spot light
3ddd
$1
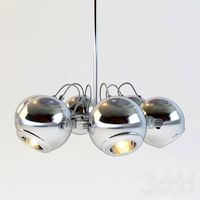
Bebop spots
... light , cosmo
подвесной светильник bebop spots. диаметр 450мм.
3ddd
$1
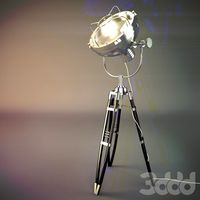
Jumbo Spot
...jumbo spot
3ddd
kare , тренога
jumbo spot
3ddd
$1
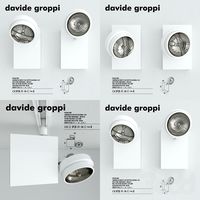
davide groppi spot sistema, spot 1
...davide groppi spot sistema, spot 1
3ddd
davide groppi
davide groppi spot sistema, spot 1
corona+vray
turbosquid
$9
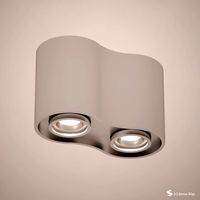
Spot
... available on turbo squid, the world's leading provider of digital 3d models for visualization, films, television, and games.
turbosquid
$8
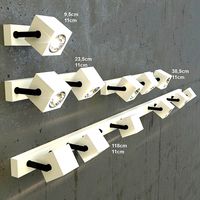
spots
... available on turbo squid, the world's leading provider of digital 3d models for visualization, films, television, and games.
design_connected
$16

Spot Light
...spot light
designconnected
spot light computer generated 3d model.
Iteration
3ddd
$1
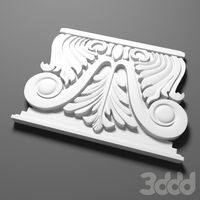
лепнина
...лепнина 3ddd капитель iteration=0 => polygons = 7860 iteration2 => polygons =...
3ddd
$1
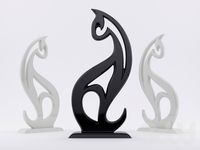
Decorative figurine cat
...decorative figurine cat 3ddd статуэтка iteration: 1.13344...
3ddd
$1
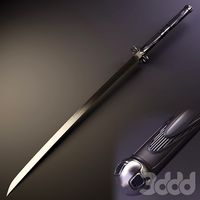
Футуристическая Дай-Катана
...не свёрнут. модель во вьюпорте не сглажена (mesh smooth iteration = 0), но на рендере будет сглаженной (mesh smooth...
3ddd
$1
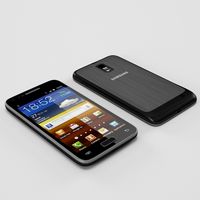
Samsung Galaxy II
...к текстурам чистые. количество полигонов 3500, при применении turbosmooth: iteration 1 - 28000 polys, iterations 2 - 112300 polys....
3ddd
$1
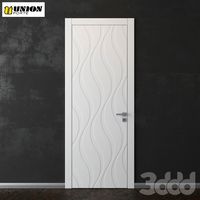
Union Trend TR11
...мм (hmax=2400) в папке max 2012+fbx. polys: 0-iterations=9763 1-iterations=78104 2-iteration=211688 (наличник и...
3ddd
free
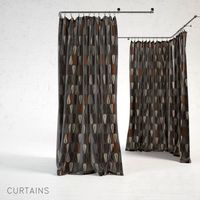
Corner curtains
...curtain (quad polygons) - 126878 + turbosmooth with 2 iteration ...
3d_export
$5
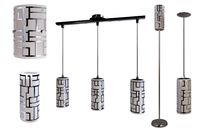
collection of eglo bayman lamps
...max 2021 software. number of polygons: 8952 (without smoothing iteration) number of vertices: 9665 (without smoothing iterations) material: glass,...
3d_export
$129
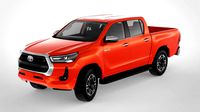
toyota hilux double cab 4wd 2020
...polycount of the model is vary, depends on smoothing iteration and file format. 424k original mech 996k with one...
3ddd
free
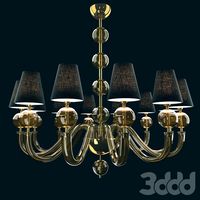
Vermont 12
...www.barovier.com/
высота: 1170 мм.
диаметр: 1180 мм.
текстуры в архиве.
на моделе turbosmooth(iters=0, render iters=2)
3ddd
$1
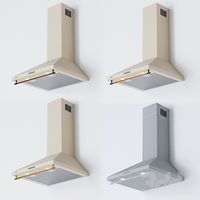
ELEYUS Allegro BG
...iterations=0 polys: 9346 verts: 8849 (1 модель ) turbosmooth iteration=1 polys: 36399 verts: 70774 (1 модель...
Dual
turbosquid
free
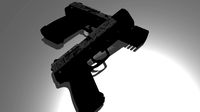
Dual Pistols
...ls
turbosquid
free 3d model dual pistols for download as fbx on turbosquid: 3d models for games, architecture, videos. (1320360)
turbosquid
$2

Dual Axe
...urbosquid
royalty free 3d model dual axe for download as fbx on turbosquid: 3d models for games, architecture, videos. (1332372)
turbosquid
$10
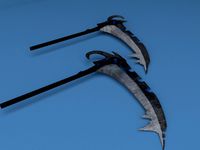
Dual Lesaths
... available on turbo squid, the world's leading provider of digital 3d models for visualization, films, television, and games.
3ddd
$1
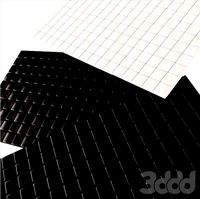
плитка Dual Bianco (Испания)
...й плитки venis dual (испания). технические качества: устойчивость к стирания, отличная геометрия, отсутствие проблем при укладке.
turbosquid
$35
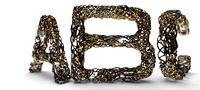
Dual Mesh Fonts
...ree 3d model dual mesh fonts for download as ma, obj, and fbx on turbosquid: 3d models for games, architecture, videos. (1352989)
turbosquid
$29
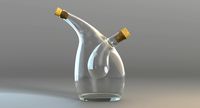
Dual Flask with Bungs
...del dual flask with bungs for download as obj, fbx, and blend on turbosquid: 3d models for games, architecture, videos. (1210512)
turbosquid
$19
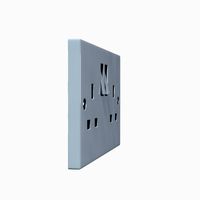
Dual Socket Plug
...3d model dual socket plug for download as obj, fbx, and blend on turbosquid: 3d models for games, architecture, videos. (1303912)
turbosquid
$13
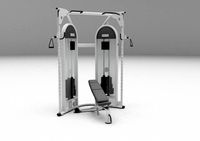
Dual Adjustable Pulley
... available on turbo squid, the world's leading provider of digital 3d models for visualization, films, television, and games.
turbosquid
$10
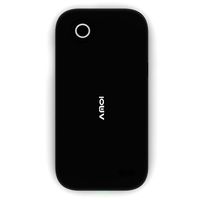
Amoi N809 Dual
... available on turbo squid, the world's leading provider of digital 3d models for visualization, films, television, and games.
turbosquid
$5

Dual Turret Tank
... available on turbo squid, the world's leading provider of digital 3d models for visualization, films, television, and games.