Thingiverse
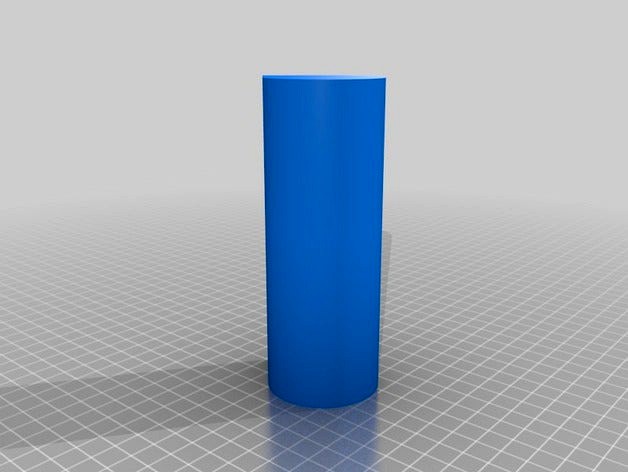
TearDrop Descriptive Geometry Lesson by bathrobotics
by Thingiverse
Last crawled date: 4 years, 2 months ago
A Bit of Descriptive Geometry:
The Tear Drop.
IMAGES IN THE PDF VERSION.
If you know the Top Path for the hole, and the bottom path of the hole, how do you scale the hole to be as large as possible, but still with the Self-supporting style of a Home Printer / RepRap Tear Drop” shape?
The Holes on items designed for home 3D printing are often shaped like Tear Drops as it gives a 45° edge which can be printed with minimal problems on a cheap printer with no support structure.
Some designs assume “ideal” situations and are designed with perfectly circular cross section holes.
Others assume the printer can print with unsupported spans of the hole, so have a flat top section, which is not invasive on the “ideal circle”. These designs are intended for Home Print on cheap 3D Printers but rely on the printer having a faster travel speed for “Bridges” – many softwares like Slic3r have independent settings for the “Bridges” Speed.
In both situations described above, the “Ideal Hole” and the “Bridged Hole” it is easy to determine the diameter of the hole given the top most path and the lower most path. The centre point of the circle will be at the midpoint of a straight line connecting the Upper and lower path.
In other occasions the position of the circular section of the hole is more important than anything else (for mating parts and bolts etc). But sometimes, the top and bottom of the Teardrop holes are the important things (like not wanting a self-supporting channel to break through a wall).
Finding the Centre Point of the Circle for a Tear Drop Hole.
First, draw a plane at 90° to the path, and connect the lines with a mutually perpendicular line. This will be the centreline.
The top will be where the point of the Tear Drop is to be drawn, at 45°.
This is one of the few measured angles we need to produce here.
If we wanted to be fancy, we could do this with bisection of circles (Produce 1 x 60°, bisect another 60° to give 60° + 30° = 90°, then bisect that to give 45°….)
Produce the 2nd tear drop line at a right angle to the first 45° line.
Now project a line perpendicular with the centreline from the base point. This shows as “Horizontal” on my cad system:
Project that line to corner points where it meets the 45° lines. We only need one of these corner points. It will be the centre point of a circle. Here I use a Ø80 circle, but pick one to suit your own dimensions. The important part is the circle must cross both the 45° line and the base construction line.
Next draw two circles of the same diameter (to each other) centred where the circle crosses the base construction line. These circles will cross at two points. These two crossing points will describe a line.
As I used the same diameter circles as the first circle, the first point is the lower corner of the triangle. Draw a line between the two points.
Where this bisecting line crosses the Centreline is the centre point of the teardrop’s Circle.
Now it’s a matter of drawing a circle that touches the two 45° sides and the base construction line. This will show as a tangential relation on most sketch packages.
Trim and make unnecessary lines to construction lines.
This can now be extruded (in this case as a solid, but when you do it as a cut operation to form a hole).
I used this method to maximise the hole size on the self-syphoning cup. That was then projected on an angle to make the cut, so it came out as a little squat, but still cut perfectly self-supporting hole in the Challace.
I’ve included the native files so you can see the construction used here.
Enjoy, Leave notes if this has been useful.
I’m not the best at writing instructions due to my Dyslexia, but I hope this helps.
EUR ING Andy Southern,
Aka Bath Robotics.
The Tear Drop.
IMAGES IN THE PDF VERSION.
If you know the Top Path for the hole, and the bottom path of the hole, how do you scale the hole to be as large as possible, but still with the Self-supporting style of a Home Printer / RepRap Tear Drop” shape?
The Holes on items designed for home 3D printing are often shaped like Tear Drops as it gives a 45° edge which can be printed with minimal problems on a cheap printer with no support structure.
Some designs assume “ideal” situations and are designed with perfectly circular cross section holes.
Others assume the printer can print with unsupported spans of the hole, so have a flat top section, which is not invasive on the “ideal circle”. These designs are intended for Home Print on cheap 3D Printers but rely on the printer having a faster travel speed for “Bridges” – many softwares like Slic3r have independent settings for the “Bridges” Speed.
In both situations described above, the “Ideal Hole” and the “Bridged Hole” it is easy to determine the diameter of the hole given the top most path and the lower most path. The centre point of the circle will be at the midpoint of a straight line connecting the Upper and lower path.
In other occasions the position of the circular section of the hole is more important than anything else (for mating parts and bolts etc). But sometimes, the top and bottom of the Teardrop holes are the important things (like not wanting a self-supporting channel to break through a wall).
Finding the Centre Point of the Circle for a Tear Drop Hole.
First, draw a plane at 90° to the path, and connect the lines with a mutually perpendicular line. This will be the centreline.
The top will be where the point of the Tear Drop is to be drawn, at 45°.
This is one of the few measured angles we need to produce here.
If we wanted to be fancy, we could do this with bisection of circles (Produce 1 x 60°, bisect another 60° to give 60° + 30° = 90°, then bisect that to give 45°….)
Produce the 2nd tear drop line at a right angle to the first 45° line.
Now project a line perpendicular with the centreline from the base point. This shows as “Horizontal” on my cad system:
Project that line to corner points where it meets the 45° lines. We only need one of these corner points. It will be the centre point of a circle. Here I use a Ø80 circle, but pick one to suit your own dimensions. The important part is the circle must cross both the 45° line and the base construction line.
Next draw two circles of the same diameter (to each other) centred where the circle crosses the base construction line. These circles will cross at two points. These two crossing points will describe a line.
As I used the same diameter circles as the first circle, the first point is the lower corner of the triangle. Draw a line between the two points.
Where this bisecting line crosses the Centreline is the centre point of the teardrop’s Circle.
Now it’s a matter of drawing a circle that touches the two 45° sides and the base construction line. This will show as a tangential relation on most sketch packages.
Trim and make unnecessary lines to construction lines.
This can now be extruded (in this case as a solid, but when you do it as a cut operation to form a hole).
I used this method to maximise the hole size on the self-syphoning cup. That was then projected on an angle to make the cut, so it came out as a little squat, but still cut perfectly self-supporting hole in the Challace.
I’ve included the native files so you can see the construction used here.
Enjoy, Leave notes if this has been useful.
I’m not the best at writing instructions due to my Dyslexia, but I hope this helps.
EUR ING Andy Southern,
Aka Bath Robotics.