Thingiverse
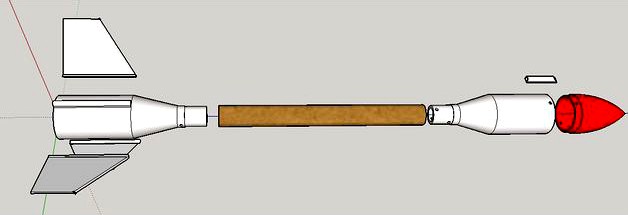
REKSUS - Rocket for D sized motors with large payload bay by hacos
by Thingiverse
Last crawled date: 4 years, 2 months ago
This is a model rocket I built and successfully flew.
The goal of this project was to built a stable rocket with a lage payload bay for electronic experiments. Long flight times and high speed were not the main goal. But I will continue developing it and want to reduce the weight to get longer and faster flights in the future.
It is designed to work with D-sized model rocket motors (18mm diameter). I added another motor holder part for 24 mm motors (base_28mm.stl)
Non-3D-printed things you need:
Strong string. I used kite strings
Several pieces of some kind of 4mm rod. I used parts of an old broken carbon fiber rod
A cardbord tube, 300 mm long, 30 mm outer diameter, 28 mm inner diameter. My cardboard tube came from a roll of cling film. If you dont find a fitting tube, you can just print a cylinder. The printed part will be less durable and heavier.
A parachute. I used a 700 mm diameter nylon parachute
A small key ring. less than 28 mm diameter.
Model rocketmotors. I used D9-7 and D9-5 motors from http://www.raketenmodellbau-klima.de (german shop)
Tools:
Sandpaper
Small file
4 mm drill or round file
Knife and hammer (always helps)
CA glue (or epoxy, if you are patient)
The cardboard tube forms the center piece of the rocket.
The main design feature of this rocket is the large payload bay, that is meant to house some elektronics experiments. It can fit a cylindrical payload 80 mm long and 55 mm in diameter. That should theoretically be enough to hold a raspberry pi zero with some batteries and other stuff. There is additional space for payload in a cone below the payload bay and in the hollow nosecone. The payload bay is closed through the whole flight and does not get ejected with the parachute.
The parachute has its own space in the cardboard tube between the Payload bay and the motor section. The central cardboard tube is glued (and/or pinned) to the payloadbay. The payloadbay and the motor section are connected by 500 mm of strong kite string. When the ejection charge of the motor fires, the cardboard tube seperates from the motor section and pulls the parachute out of the tube. The payload bay comes to hang below the motor section under the parachute.
The base of ther rocket holds the model rocket engine. The three fins are glued around the base. There is also a guiding tube on the outside of the base to guide the rocket during launch. Above the motor holder inside the base there is a baffle that slows down the hot gasses from the seperation charge and stops sparks from damaging the parachute. The fins are slightly slanted to give the rocket a slow rotation during the flight to balance out asymetries in the motor burn (not fas enough for real spin stabilisaton). The fins ara also quite large and and the center of mass of the whole rocket is far foreward because of its length and the paylod at the front. This should ensure a very stable flight.
The rocket has an overall lenght of 710 mm and weights about 260 g (with motor, without payload).
I already flew this rocket twice with a dummy payload. (Video will follow soon. Edit: Scratch that. I lost the video)
It flew well, but (as expected) not terribly high or fast. But all in all the test flights were sucessfull. Now a friend of mine is building a payload for the first real flight.
Room for future improvement:
Reduce the diameter of the rocket base to 30 mm (outer diameter of cardboard tube). This greatly reduces the weight, but makes it impossible to add the lower guiding tube. But one guiding tube at the top should be enough.
Make a smaller baffle. A baffle with 2 walls instead of 4 should be enough to protect the parachute and save weight by making the base section shorter.
Cardboard tube could be shortened because the parachute does not use the whole space inside.
Special nosecone and / or payloadbay to allow a Pi-camera to film the flight.
Some kind of motor retainer. Always lost the motors on seperation because they were blown out the back of the rocket. The seperation charge was still strong enough to pull out the parachute. Maybe the back preasure from the baffle is too large and a smaller baffle will solve this problem.
Better fastening system for the nosecone. Getting the rod through the holes on both sides is quite difficult.
Things I thought about, but did not include:
Rubber band between parachute and rocket to dampen shock on parachute opening. Worked well without this.
Stronger slanted fins for more rotation. The payload will include gyros and accelerometers. Too much rotation might saturate them. Future versions might have completly straight fins.
Printing the fins and rocket base as one part. I decided to have them in seperate parts, because the fins are the parts most likely to break in a "hard landing". If this happens you can cut of the remains of the broken fin and glue a new one on.
Legal Stuff:
Be carefull when flying model rockets and follow your local laws. Make sure you do not cause a fire!
Warning:
Do not leave this Rocket laying around in a car in summer. The PLA got soft and it deformed quite a bit. It still probably flies, but is a bit wonky now.
The goal of this project was to built a stable rocket with a lage payload bay for electronic experiments. Long flight times and high speed were not the main goal. But I will continue developing it and want to reduce the weight to get longer and faster flights in the future.
It is designed to work with D-sized model rocket motors (18mm diameter). I added another motor holder part for 24 mm motors (base_28mm.stl)
Non-3D-printed things you need:
Strong string. I used kite strings
Several pieces of some kind of 4mm rod. I used parts of an old broken carbon fiber rod
A cardbord tube, 300 mm long, 30 mm outer diameter, 28 mm inner diameter. My cardboard tube came from a roll of cling film. If you dont find a fitting tube, you can just print a cylinder. The printed part will be less durable and heavier.
A parachute. I used a 700 mm diameter nylon parachute
A small key ring. less than 28 mm diameter.
Model rocketmotors. I used D9-7 and D9-5 motors from http://www.raketenmodellbau-klima.de (german shop)
Tools:
Sandpaper
Small file
4 mm drill or round file
Knife and hammer (always helps)
CA glue (or epoxy, if you are patient)
The cardboard tube forms the center piece of the rocket.
The main design feature of this rocket is the large payload bay, that is meant to house some elektronics experiments. It can fit a cylindrical payload 80 mm long and 55 mm in diameter. That should theoretically be enough to hold a raspberry pi zero with some batteries and other stuff. There is additional space for payload in a cone below the payload bay and in the hollow nosecone. The payload bay is closed through the whole flight and does not get ejected with the parachute.
The parachute has its own space in the cardboard tube between the Payload bay and the motor section. The central cardboard tube is glued (and/or pinned) to the payloadbay. The payloadbay and the motor section are connected by 500 mm of strong kite string. When the ejection charge of the motor fires, the cardboard tube seperates from the motor section and pulls the parachute out of the tube. The payload bay comes to hang below the motor section under the parachute.
The base of ther rocket holds the model rocket engine. The three fins are glued around the base. There is also a guiding tube on the outside of the base to guide the rocket during launch. Above the motor holder inside the base there is a baffle that slows down the hot gasses from the seperation charge and stops sparks from damaging the parachute. The fins are slightly slanted to give the rocket a slow rotation during the flight to balance out asymetries in the motor burn (not fas enough for real spin stabilisaton). The fins ara also quite large and and the center of mass of the whole rocket is far foreward because of its length and the paylod at the front. This should ensure a very stable flight.
The rocket has an overall lenght of 710 mm and weights about 260 g (with motor, without payload).
I already flew this rocket twice with a dummy payload. (Video will follow soon. Edit: Scratch that. I lost the video)
It flew well, but (as expected) not terribly high or fast. But all in all the test flights were sucessfull. Now a friend of mine is building a payload for the first real flight.
Room for future improvement:
Reduce the diameter of the rocket base to 30 mm (outer diameter of cardboard tube). This greatly reduces the weight, but makes it impossible to add the lower guiding tube. But one guiding tube at the top should be enough.
Make a smaller baffle. A baffle with 2 walls instead of 4 should be enough to protect the parachute and save weight by making the base section shorter.
Cardboard tube could be shortened because the parachute does not use the whole space inside.
Special nosecone and / or payloadbay to allow a Pi-camera to film the flight.
Some kind of motor retainer. Always lost the motors on seperation because they were blown out the back of the rocket. The seperation charge was still strong enough to pull out the parachute. Maybe the back preasure from the baffle is too large and a smaller baffle will solve this problem.
Better fastening system for the nosecone. Getting the rod through the holes on both sides is quite difficult.
Things I thought about, but did not include:
Rubber band between parachute and rocket to dampen shock on parachute opening. Worked well without this.
Stronger slanted fins for more rotation. The payload will include gyros and accelerometers. Too much rotation might saturate them. Future versions might have completly straight fins.
Printing the fins and rocket base as one part. I decided to have them in seperate parts, because the fins are the parts most likely to break in a "hard landing". If this happens you can cut of the remains of the broken fin and glue a new one on.
Legal Stuff:
Be carefull when flying model rockets and follow your local laws. Make sure you do not cause a fire!
Warning:
Do not leave this Rocket laying around in a car in summer. The PLA got soft and it deformed quite a bit. It still probably flies, but is a bit wonky now.