Thingiverse
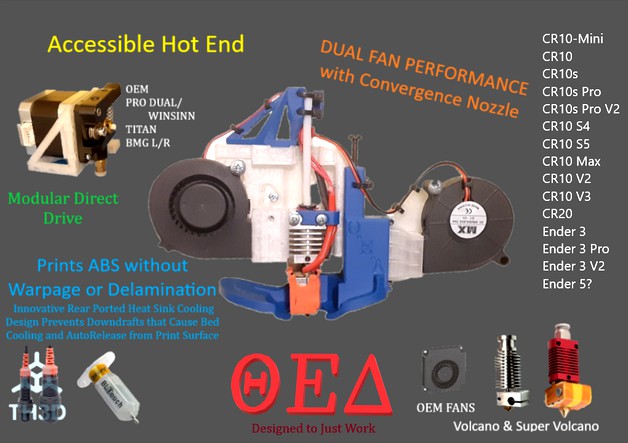
QED Hot End Cooling System with Convergence Part Cooling Nozzle for: Creality CR10 CR10S Pro V2 Ender3 Ender5 MicroSwiss E3DV6 Volcano Hotend 4010 5015 Direct Drive by magnokneeto
by Thingiverse
Last crawled date: 4 years, 5 months ago
I designed a new cooling system to be easy to use.
I wanted to upgrade my machine to allow for access to the hot end without taking anything off. I wanted to be able to adjust my part cooling duct wherever I wanted not just where somebody else thinks it should go and I wanted to be able to upgrade to direct drive if I ever find myself printing flexibles.
It is super easy to service the hot end, it is easy to see the part printing. I can adjust the part cooling while it prints and it is capable of adjusting from a standard 10mm heater block all the way up to a 50mm super volcano. I set mine with a 2mm allen wrench under the nozzle.
I put a large effort into equally distributing and focusing the part cooling duct/nozzle but even with all my design intent I was surprised that with a 4010 blower it performed almost as well as my benchmark tests with 5015 dual fan cooling systems. When I upgraded to a 5015 fan, it exceeded them.
I decided to give ABS a second try, it never worked with my old setups, even with an enclosure...and it was REALLY REALLY easy to print. So easy that I now prefer to print ABS because it is more predictable then PLA. The ABS parts stuck to the glass bed way easier than PLA parts ever did and they didn't pull up in the corners, or split, or anything. (I spray hair gel on the glass). What I have been able to deduce is that my design eliminates the possibility of drafts generated by the heat sink cooling fan ever reaching the bed. Further testing showed that only a sllght amount of air deflected from the heat sink fan onto the bed would curl prints away from the glass.
With all my free time I decided to make it universal so others could use it too. I tracked down a bunch of layouts and bolt patterns and combined them.
The items and machines with ☆ are ones that should be compatible but I haven't been able to test them. I included the heat sink retainer type that should work with each machine. There are three interfaces. The first two are for the traditional post mounted carriages with a zero offset and an 8mm offset. The 8mm is needed for the belt ends that stick out on the Ender 5. The third is for the flat carriage that is based on the CR10 V2.
I included designs for the rectangular Mk8 and Micro Swiss Hot ends and the E3dV6 hot end. The MK8 and MS are much easier to use and perform excellently in heat sink temperature dissipation and the E3D-V6 design performs almost as well in preliminary testing. The Creality Hybrid hotend is in the works but there is not currently a Heat Sink Retainer for the CRX or the OEM hot end on a couple of the Pro models.
Hot end compatibility with each interface type.
CRZed》mk8, MS (CR10 model), E3d-V6
CR8》mk8, MS (CR10 model), E3d-V6
CRV2》 E3d-V6
For the traditional 2 post Creality carriage layouts I made a template for checking the bolt pattern against yours. It is only a few layers thick so it is a quick print and will tell you if the holes line up. You don't even need those extra bolts with the zero offset if you are using a post mounted hot end without DD.
CR10-Mini 》 CRZed ,CR8
☆ CR10 》 CRZed, CR8
☆ CR10s 》 CRZed, CR8
☆ CR10s Pro 》 CRZed, CR8
☆ CR10s Pro V2 》CRZed, CR8
☆ CR10S4 》 CRZed, CR8
☆ CR10S5 》 CRZed, CR8
☆ CR10Max 》 CRZed, CR8
☆ CR20 》 CRZed, CR8
☆ CR10 V2 》 CRV2
☆ CR10 V3 》 CRV2
☆ Ender 3 》 CRZed, CR8
☆ Ender 3 Pro 》 CRZed, CR8
☆ Ender 3 V2 》 CRZed, CR8
☆ Ender 5 》 CR8
There is a possibility that the cooling fans could hit the horizontal frame members. It looks like it should work at least with a 10mm heater block but I can't be sure without more intimate knowledge of the Ender 5.
I made mounts for ABL, BL touch and all the proximity sensors including EZABL. The size ranges roughly correlate to the height of the heater block. The offsets are absolute and on the physical parts.
I made modular direct drive mounts that replace the strain relief for common extruders. I verified the OEM but have not mounted them with the others. Based on center of mass considerations direct drive exruders that pass the filament to the left of the stepper motor shaft when viewed looking down the shaft will balance better and impart fewer cantilevered loads into the system. The exception being the V2 design which specifically preserves the OEM configuration to mount a stepper motor in front of the carriage and is only compatible with paths on the right of the shaft.
OEM
☆ Titan
☆ Pro dual / Winsinn
☆ Bondtech BMG left and right
I also made provisions for a bed light. It mounts onto the part cooling duct or the optional mount. It is super simple, made up of the arm and the light bar. There are extra components in case you want to get creative with where you put the light.
Oh, I almost forgot. There is a fan adapter for use with most popular fans. The first # is the one you want to use, the second is the fan that it is replacing. The heat sink is designed for a 5015(R) and the part cooling duct has a 4010(R) interface.
4010 R
☆ 4020 R
5015 R
☆ 5020 R
I even included adapters for axial fans even though they are ill suited for this application. Axial fans are high turbulence, low pressure, low speed fans that are good for distributing air about a larger volume, not compressing it through small cavities. Not really sure why they are even used on 3D printers outside of the electronics case. Radial blower fans, while typically requiring a slightly larger size to move the same volume of air, move it faster, with higher pressure and less turbulence allowing for more CFM to be forced through the diminutive cross sections of both part cooling nozzle and heat sink radiator fins.
4010 A
4020 A
☆ 3010 A
Misc:
Printermods MDD V1.3
It appears that since the Printermods MDD v1.3 is compatible with the OEM fan shroud of the ender 3 and CR10 that it should also be compatible with the CRzed or CR8 HSR designs. The points of consideration are the top wheel hole positions and the thickness of the bottom wheel flange. If it is too thick to allow the PCD to pass over it the CR8 version will be required. The test fit template contains a feature to guage this thickness. When installing with direct drive the QED modular DD mounts will be required. Utilizing mounting holes on the back face similar to the MDD design were considered for the QED interface but because every diameter variation for filament drive wheel would necessitate a unique bolt pattern it was deemed too limiting. If you attempt an install please leave a comment to let me know if it works.
REVISIONS2020.12.17: Added Prototype HSR for CR10V2/V3 with an E3d-V6 style hotend. Due to the compact height of this HSR, DD configurations that pass the filament to the left of the steppper motor shaft are not compatible.
I wanted to upgrade my machine to allow for access to the hot end without taking anything off. I wanted to be able to adjust my part cooling duct wherever I wanted not just where somebody else thinks it should go and I wanted to be able to upgrade to direct drive if I ever find myself printing flexibles.
It is super easy to service the hot end, it is easy to see the part printing. I can adjust the part cooling while it prints and it is capable of adjusting from a standard 10mm heater block all the way up to a 50mm super volcano. I set mine with a 2mm allen wrench under the nozzle.
I put a large effort into equally distributing and focusing the part cooling duct/nozzle but even with all my design intent I was surprised that with a 4010 blower it performed almost as well as my benchmark tests with 5015 dual fan cooling systems. When I upgraded to a 5015 fan, it exceeded them.
I decided to give ABS a second try, it never worked with my old setups, even with an enclosure...and it was REALLY REALLY easy to print. So easy that I now prefer to print ABS because it is more predictable then PLA. The ABS parts stuck to the glass bed way easier than PLA parts ever did and they didn't pull up in the corners, or split, or anything. (I spray hair gel on the glass). What I have been able to deduce is that my design eliminates the possibility of drafts generated by the heat sink cooling fan ever reaching the bed. Further testing showed that only a sllght amount of air deflected from the heat sink fan onto the bed would curl prints away from the glass.
With all my free time I decided to make it universal so others could use it too. I tracked down a bunch of layouts and bolt patterns and combined them.
The items and machines with ☆ are ones that should be compatible but I haven't been able to test them. I included the heat sink retainer type that should work with each machine. There are three interfaces. The first two are for the traditional post mounted carriages with a zero offset and an 8mm offset. The 8mm is needed for the belt ends that stick out on the Ender 5. The third is for the flat carriage that is based on the CR10 V2.
I included designs for the rectangular Mk8 and Micro Swiss Hot ends and the E3dV6 hot end. The MK8 and MS are much easier to use and perform excellently in heat sink temperature dissipation and the E3D-V6 design performs almost as well in preliminary testing. The Creality Hybrid hotend is in the works but there is not currently a Heat Sink Retainer for the CRX or the OEM hot end on a couple of the Pro models.
Hot end compatibility with each interface type.
CRZed》mk8, MS (CR10 model), E3d-V6
CR8》mk8, MS (CR10 model), E3d-V6
CRV2》 E3d-V6
For the traditional 2 post Creality carriage layouts I made a template for checking the bolt pattern against yours. It is only a few layers thick so it is a quick print and will tell you if the holes line up. You don't even need those extra bolts with the zero offset if you are using a post mounted hot end without DD.
CR10-Mini 》 CRZed ,CR8
☆ CR10 》 CRZed, CR8
☆ CR10s 》 CRZed, CR8
☆ CR10s Pro 》 CRZed, CR8
☆ CR10s Pro V2 》CRZed, CR8
☆ CR10S4 》 CRZed, CR8
☆ CR10S5 》 CRZed, CR8
☆ CR10Max 》 CRZed, CR8
☆ CR20 》 CRZed, CR8
☆ CR10 V2 》 CRV2
☆ CR10 V3 》 CRV2
☆ Ender 3 》 CRZed, CR8
☆ Ender 3 Pro 》 CRZed, CR8
☆ Ender 3 V2 》 CRZed, CR8
☆ Ender 5 》 CR8
There is a possibility that the cooling fans could hit the horizontal frame members. It looks like it should work at least with a 10mm heater block but I can't be sure without more intimate knowledge of the Ender 5.
I made mounts for ABL, BL touch and all the proximity sensors including EZABL. The size ranges roughly correlate to the height of the heater block. The offsets are absolute and on the physical parts.
I made modular direct drive mounts that replace the strain relief for common extruders. I verified the OEM but have not mounted them with the others. Based on center of mass considerations direct drive exruders that pass the filament to the left of the stepper motor shaft when viewed looking down the shaft will balance better and impart fewer cantilevered loads into the system. The exception being the V2 design which specifically preserves the OEM configuration to mount a stepper motor in front of the carriage and is only compatible with paths on the right of the shaft.
OEM
☆ Titan
☆ Pro dual / Winsinn
☆ Bondtech BMG left and right
I also made provisions for a bed light. It mounts onto the part cooling duct or the optional mount. It is super simple, made up of the arm and the light bar. There are extra components in case you want to get creative with where you put the light.
Oh, I almost forgot. There is a fan adapter for use with most popular fans. The first # is the one you want to use, the second is the fan that it is replacing. The heat sink is designed for a 5015(R) and the part cooling duct has a 4010(R) interface.
4010 R
☆ 4020 R
5015 R
☆ 5020 R
I even included adapters for axial fans even though they are ill suited for this application. Axial fans are high turbulence, low pressure, low speed fans that are good for distributing air about a larger volume, not compressing it through small cavities. Not really sure why they are even used on 3D printers outside of the electronics case. Radial blower fans, while typically requiring a slightly larger size to move the same volume of air, move it faster, with higher pressure and less turbulence allowing for more CFM to be forced through the diminutive cross sections of both part cooling nozzle and heat sink radiator fins.
4010 A
4020 A
☆ 3010 A
Misc:
Printermods MDD V1.3
It appears that since the Printermods MDD v1.3 is compatible with the OEM fan shroud of the ender 3 and CR10 that it should also be compatible with the CRzed or CR8 HSR designs. The points of consideration are the top wheel hole positions and the thickness of the bottom wheel flange. If it is too thick to allow the PCD to pass over it the CR8 version will be required. The test fit template contains a feature to guage this thickness. When installing with direct drive the QED modular DD mounts will be required. Utilizing mounting holes on the back face similar to the MDD design were considered for the QED interface but because every diameter variation for filament drive wheel would necessitate a unique bolt pattern it was deemed too limiting. If you attempt an install please leave a comment to let me know if it works.
REVISIONS2020.12.17: Added Prototype HSR for CR10V2/V3 with an E3d-V6 style hotend. Due to the compact height of this HSR, DD configurations that pass the filament to the left of the steppper motor shaft are not compatible.