Thingiverse
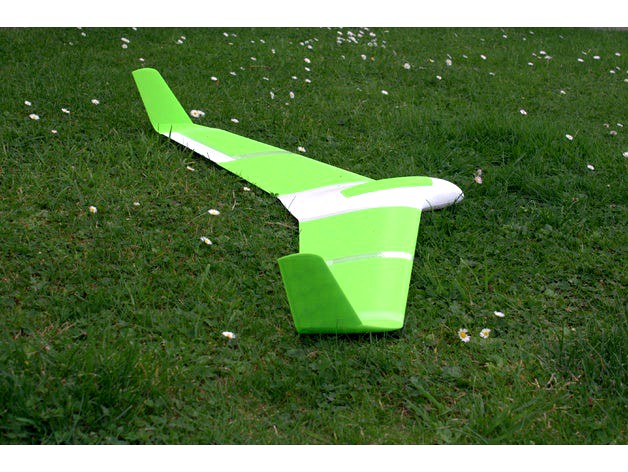
Proteus - an OpenSCAD slope soarer design by spinorkit
by Thingiverse
Last crawled date: 3 years ago
This is a fast, efficient slope soarer, NOT suitable for beginners.https://youtu.be/aQ_SdMxxsIY
Update as of 19 January 2019: the Proteusv2https://www.thingiverse.com/thing:3366296
has more forgiving flying characteristics.
Update as of 9 December 2019: Proteus Plus with 1.8 m span, PW51 airfoil and flaps:https://www.thingiverse.com/thing:3967057
Note: this Openscad design has a large number of parameters such as sweep, washout, dihedral and many many more. Adjusting these parameters will result in a corresponding outer shell being generated, but may result in some internal structures not being correctly positioned, or possibly puncturing the shell, e.g. increasing the dihedral will cause the ends of the main carbon fiber tube spar to be exposed underneath the wing. These issues are fixable but overall it is a lot of work to get that right for all possible parameters.
Requires OpenSCAD version 2017.01.20 or later.
Update 4 November 2017: Added ProteusFlyingWing.scad. This source file replaces CustomizableFlyingWing.scad and fixes an issue where increasing the noseLen parameter above 90 would cause the hatch to fail to fit properly. Note that fuselages generated with this new scad file will not fit the original hatch and vice versa.
Default specs:
Wing profile: MH-45
Fin profile: NACA symmetrical, 8% thickness
Wingspan: depends on printer max z, 1040 mm for 200 mm, 1160 for 230 mm max z
Root chord: 200 mm
Tip chord: 130 mm
Sweep angle (leading edge): 22 degrees
Washout: 3.5 degrees
Dihedral: 1 degree under each wing (2 degrees total)
Flying weight: 560 g for 1160 mm span version (including 28 g of lead nose weight)
Each wing is printed in 3 pieces, root, tip and fin. I have only uploaded the left-hand wing parts. Create the right-hand parts by reflecting them in the slicer. E.g. for Simplify3D, choose Mesh | Mirror Mesh | Mirror X (or Mirror y).
The length of the root and tip pieces is set by the printerMaxZ parameter. I have only printed and flown versions where printerMaxZ is set to 230 mm. I have added stls for the case where printerMaxZ is set to 200 mm, for the convenience of people with printers limited to 200 in height, but I have not printed them.
The hatch does not depend on the printerMaxZ parameter, all the other parts do, to some degree.
The total span (including fins) of the Z200 version is 1040 mm.
The only pieces I glue together are the nose to the rear fuselage and the servo guards to the wing (both with thick cyanoacrylate). The wing joints are taped, with fiberglass reinforced tape being used for the most important join between the root wing section and the tip wing section.
The OpenScad code calculates the estimated CG position using code from rcwingcog@gmail.com:http://rcwingcog.a0001.net/V3_testing/?i=1
This CG position is used to place 2 small dimples at the correct balance position under the fuselage.
Vitamins:
500 mm x 5 mm OD Carbon fiber tube spar:https://www.aliexpress.com/item/5pcs-5MM-OD-X-3MM-ID-X-600MM-Carbon-fiber-wing-tube-for-airplane-5-3/32242824992.html?spm=2114.13010608.0.0.dDXTx3
2 mm OD and 3 mm OD carbon fiber rod joiners:https://www.aliexpress.com/item/1pcs-Carbon-Fiber-Rods-Dia-1mm-2mm-3mm-4mm-5mm-6mm-7mm-8mm-10mm-11mm-12mm/32573564619.html?spm=2114.13010608.0.0.dDXTx3
Servos:https://hobbyking.com/en_us/hxt900-micro-servo-1-6kg-0-12sec-9g.html
Servo extension leads:https://hobbyking.com/en_us/10cm-servo-lead-extention-jr-26awg-10pcs-bag.html
Elevon linkages (these are too short for mechanical elevon differential - so use electronic differential, 2 pcs required):https://hobbyking.com/en_us/extreme-3d-1100mm-replacement-control-rod-1-pc.html
Joining root wing section to tip wing section and holding servos in place:https://hobbyking.com/en_us/high-stength-fiber-tape-24mm-x-50m.html
Elevon hinging (both top and bottom surfaces) and joining fins to wing tips:https://hobbyking.com/en_us/1-x-4m-roll-3m-blenderm-tape-hinging-tape-twin-pack.html
Hatch latch:
3M™ Dual Lock™ Reclosable Fasteners (clear not black)
Battery holder bracket mounting:
3M™ Dual Lock™ Reclosable Fasteners (clear not black)
Joining wings to fuselage:
PVC Tape (12mm)
Nose weight:
Lead fishing sinkers (1x 0.5 oz, 2x0.25 oz for the Z230 version)
Weights:
Root wing section (Z230 version): 81g
Tip wing section (Z230 version): 44g
Fin: 18g
Elevon: 11g
Fuselage (nose + rear): 105g
Hatch:17g
Total printed weight (less battery, servos, spar, joiners, tape, etc): 429g
Control throws
These are what I use for the glider version. They are likely to be too large for beginners and for the motorized version.
All measurements relative to the trailing edge at the inner end of the elevons.
Neutral: 1.6 mm of up elevon
Elevator: -4.7 mm to +8 mm
Aileron: - 10.8 to +16.5 mm
In the tx mixer I set the elevator throws to be 45 % and the aileron throws to 100 %.
I set the elevator to 20% exponential and aileron to 45% exponential.
These throws are sufficient to allow a very fast roll, which is why either exponential or dual-rates are needed.
Note, using too much up elevator in a loop will cause the glider to stall at the top of the loop and spin out, so be careful to fly it all the way around the loop to maintain speed (or reduce the maximum elevator throw).
Update as of 19 January 2019: the Proteusv2https://www.thingiverse.com/thing:3366296
has more forgiving flying characteristics.
Update as of 9 December 2019: Proteus Plus with 1.8 m span, PW51 airfoil and flaps:https://www.thingiverse.com/thing:3967057
Note: this Openscad design has a large number of parameters such as sweep, washout, dihedral and many many more. Adjusting these parameters will result in a corresponding outer shell being generated, but may result in some internal structures not being correctly positioned, or possibly puncturing the shell, e.g. increasing the dihedral will cause the ends of the main carbon fiber tube spar to be exposed underneath the wing. These issues are fixable but overall it is a lot of work to get that right for all possible parameters.
Requires OpenSCAD version 2017.01.20 or later.
Update 4 November 2017: Added ProteusFlyingWing.scad. This source file replaces CustomizableFlyingWing.scad and fixes an issue where increasing the noseLen parameter above 90 would cause the hatch to fail to fit properly. Note that fuselages generated with this new scad file will not fit the original hatch and vice versa.
Default specs:
Wing profile: MH-45
Fin profile: NACA symmetrical, 8% thickness
Wingspan: depends on printer max z, 1040 mm for 200 mm, 1160 for 230 mm max z
Root chord: 200 mm
Tip chord: 130 mm
Sweep angle (leading edge): 22 degrees
Washout: 3.5 degrees
Dihedral: 1 degree under each wing (2 degrees total)
Flying weight: 560 g for 1160 mm span version (including 28 g of lead nose weight)
Each wing is printed in 3 pieces, root, tip and fin. I have only uploaded the left-hand wing parts. Create the right-hand parts by reflecting them in the slicer. E.g. for Simplify3D, choose Mesh | Mirror Mesh | Mirror X (or Mirror y).
The length of the root and tip pieces is set by the printerMaxZ parameter. I have only printed and flown versions where printerMaxZ is set to 230 mm. I have added stls for the case where printerMaxZ is set to 200 mm, for the convenience of people with printers limited to 200 in height, but I have not printed them.
The hatch does not depend on the printerMaxZ parameter, all the other parts do, to some degree.
The total span (including fins) of the Z200 version is 1040 mm.
The only pieces I glue together are the nose to the rear fuselage and the servo guards to the wing (both with thick cyanoacrylate). The wing joints are taped, with fiberglass reinforced tape being used for the most important join between the root wing section and the tip wing section.
The OpenScad code calculates the estimated CG position using code from rcwingcog@gmail.com:http://rcwingcog.a0001.net/V3_testing/?i=1
This CG position is used to place 2 small dimples at the correct balance position under the fuselage.
Vitamins:
500 mm x 5 mm OD Carbon fiber tube spar:https://www.aliexpress.com/item/5pcs-5MM-OD-X-3MM-ID-X-600MM-Carbon-fiber-wing-tube-for-airplane-5-3/32242824992.html?spm=2114.13010608.0.0.dDXTx3
2 mm OD and 3 mm OD carbon fiber rod joiners:https://www.aliexpress.com/item/1pcs-Carbon-Fiber-Rods-Dia-1mm-2mm-3mm-4mm-5mm-6mm-7mm-8mm-10mm-11mm-12mm/32573564619.html?spm=2114.13010608.0.0.dDXTx3
Servos:https://hobbyking.com/en_us/hxt900-micro-servo-1-6kg-0-12sec-9g.html
Servo extension leads:https://hobbyking.com/en_us/10cm-servo-lead-extention-jr-26awg-10pcs-bag.html
Elevon linkages (these are too short for mechanical elevon differential - so use electronic differential, 2 pcs required):https://hobbyking.com/en_us/extreme-3d-1100mm-replacement-control-rod-1-pc.html
Joining root wing section to tip wing section and holding servos in place:https://hobbyking.com/en_us/high-stength-fiber-tape-24mm-x-50m.html
Elevon hinging (both top and bottom surfaces) and joining fins to wing tips:https://hobbyking.com/en_us/1-x-4m-roll-3m-blenderm-tape-hinging-tape-twin-pack.html
Hatch latch:
3M™ Dual Lock™ Reclosable Fasteners (clear not black)
Battery holder bracket mounting:
3M™ Dual Lock™ Reclosable Fasteners (clear not black)
Joining wings to fuselage:
PVC Tape (12mm)
Nose weight:
Lead fishing sinkers (1x 0.5 oz, 2x0.25 oz for the Z230 version)
Weights:
Root wing section (Z230 version): 81g
Tip wing section (Z230 version): 44g
Fin: 18g
Elevon: 11g
Fuselage (nose + rear): 105g
Hatch:17g
Total printed weight (less battery, servos, spar, joiners, tape, etc): 429g
Control throws
These are what I use for the glider version. They are likely to be too large for beginners and for the motorized version.
All measurements relative to the trailing edge at the inner end of the elevons.
Neutral: 1.6 mm of up elevon
Elevator: -4.7 mm to +8 mm
Aileron: - 10.8 to +16.5 mm
In the tx mixer I set the elevator throws to be 45 % and the aileron throws to 100 %.
I set the elevator to 20% exponential and aileron to 45% exponential.
These throws are sufficient to allow a very fast roll, which is why either exponential or dual-rates are needed.
Note, using too much up elevator in a loop will cause the glider to stall at the top of the loop and spin out, so be careful to fly it all the way around the loop to maintain speed (or reduce the maximum elevator throw).
Similar models
thingiverse
free
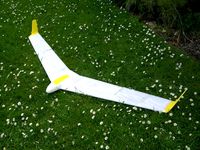
Proteus Plus PW51
...during a crash or bad landing. printing instructions are similar to the original proteus: https://www.thingiverse.com/thing:2086413 note: the hatch is...
grabcad
free

Glider Template for Fat Men.
...: wortmann fx 71l15-20
wing root: wortmann fx 67k17 (1.2 degrees)
wing tip: wortmann fx 67k15 (1.2 degrees)
dihedral: 2.4 degrees
thingiverse
free
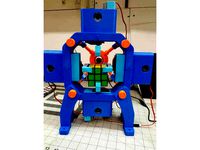
Remix - Fully 3D-Printed Rubik's Cube Solving Robot by jackheli
...___store=en_us
note that in my experience, servos with standard angular throw work fine, no need to use 160 or 180 degree servos.
thingiverse
free
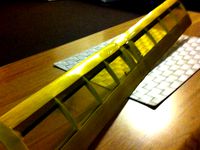
Wing spar, tips and joiner set - high and moderate lift versions included by northshore
... less agressive lift profile, is matched to the version 5 centre spar for the centre join, wing tips and angled joiners included.
thingiverse
free
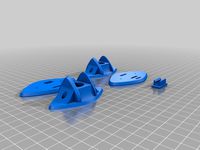
Wing Wing Z-84 EPO 845mm FPV camera mount.
...en_us/wing-wing-z-84-epo-845mm-kit.html
https://hobbyking.com/en_us/caddx-turbo-micro-sdr2-plus-fpv-camera-freestyle-version.html
grabcad
free

Carbon fiber tape
...carbon fiber tape
grabcad
carbon fiber tape
thingiverse
free
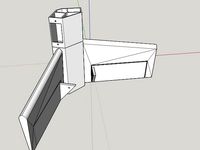
Flying Fox - Tail section w/ servo slots by OmniFox
...ith 9g servo slots, elevons and servo horns.
this is a work in progress, part of the modular "flying fox" rc airplane.
grabcad
free

Curare_40_MK_oz6141
...curare_40_mk_oz6141
grabcad
wing span: 1450mm
dihedral: 4 degree
center rib: 317mm
tip rib: 211mm
l.e. sweep: 78mm
3dwarehouse
free
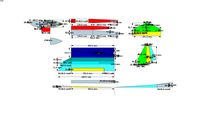
Mini Trainer Glider w/o motor on
...(for each wing) must be 5 degrees. less than 230gr without battery but with servos, receiver and bec. #ft_tini_trainer_mod_glider
thingiverse
free
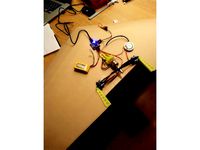
Elevon Direct Servo Actuator for Versa Wing by Dudsr
...d right elevons. you should also use the screw that comes with your servo to lock the the direct actuators onto the servo spline.
Spinorkit
thingiverse
free
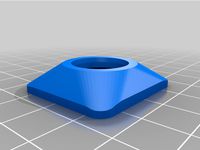
Naked Gopro lens filter holder by spinorkit
... filters/lens protectors, e.g.:https://camerabutter.com/products/gopro-hero-5-6-7-nd-filters
print in black tpu (e.g. ninjaflex).
thingiverse
free
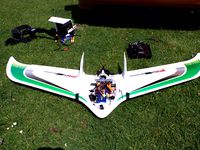
FX-61 Accessories by spinorkit
...r mounting the push button switch for the pixhawk flight computer so that the button protrudes through a small hole in the cover.
thingiverse
free
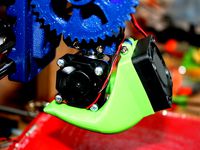
Fan duct for active cooling, supportless, parametized OpenSCAD by spinorkit
...fanductovale3dv6prusareworkv4.stl and fanductovale3dv6.scad for the e3d v6 . this stl should be printed with 0.2 mm layer height.
thingiverse
free
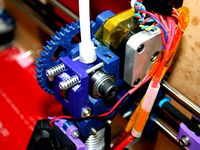
Greg's Wade extruder idler for 40mm M3 bolts by spinorkit
...l over the tension.
i printed it on it's side for extra strength, with (kisslicer medium) support, 3 loops and 100% infill.
thingiverse
free

Crux3 Naked Gopro Mount shifted backwards by spinorkit
...10
resource motor 2 b07
resource motor 3 b06
resource motor 4 b08
it also requires reversing all 4 motors in blheli configurator.
thingiverse
free
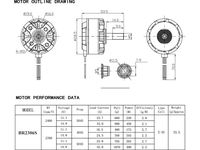
Proteusv2 fuselage rear with motor mount for RaceStar 2306S by Jussimus
...2306s by jussimus thingiverse this is a remix from spinorkit proteusv2 slope soarer. i loved the design. it was...
thingiverse
free
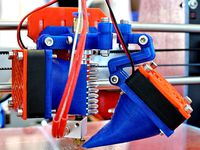
Configurable 40mm fan duct / mount for Wade's extruder by AndrewBCN
...the awesome e3d v6 layer fan duct designed by spinorkit (thing # 217253) and made it compatible with my...
Soarer
turbosquid
free
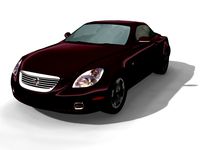
Soarer
... available on turbo squid, the world's leading provider of digital 3d models for visualization, films, television, and games.
3d_export
$15
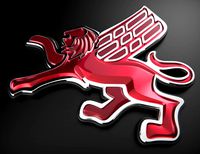
Emblem Toyota Soarer for 3D printing
...emblem toyota soarer for 3d printing
3dexport
emblem toyota soarer
3d_export
$20
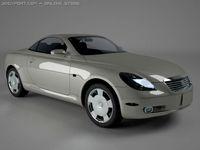
maxwell toyota soarer 3D Model
...maxwell toyota soarer 3d model
3dexport
maxwell
maxwell toyota soarer 3d model maxwell-models 958 3dexport
3d_export
$20
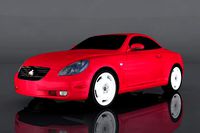
toyota soarer 430scv
...s.<br>car textures:png - 2k resolution other available formats: obj, 3ds, fbx, stl, max. polycount: 34428 poly / 30993 tris
3d_export
$20
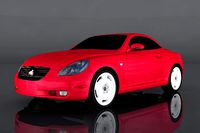
toyota soarer 430scv
...s.<br>car textures:png - 2k resolution other available formats: obj, 3ds, fbx, stl, max. polycount: 34428 poly / 30993 tris
3d_export
$30
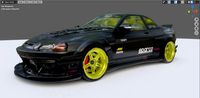
toyota soarer 1991 with 1lr-gue engine
... engin 1lr-gue object : 658 vertices : 714,093 edges : 1333940 faces : 626353 hope you like it guys and thank you for downloading
cg_studio
$36

maxwell toyota soarer3d model
... soarer3d model
cgstudio
.3ds - maxwell toyota soarer 3d model, royalty free license available, instant download after purchase.
thingiverse
free
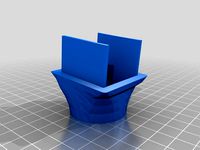
FT Simple Soarer Custom Motor Mount by jason51873
...ic front end.
important note:
this has a 5 degree down tilt built in so make sure you put it with the motor wire hole on the top.
3dcadbrowser
free
![Toyota Soarer [Tuned]](/t/2209776.jpg)
Toyota Soarer [Tuned]
...software.this 3d object can be downloaded in .max, .obj, .3ds, .fbx, .dxf, .lwo, .stl, .wrl, .ma, .dae, .x and .asc file formats.
thingiverse
free
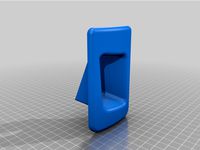
Toyota Soarer SC300 SC400 Rear seat belt buckle surround by WIPName
...the buckles installed in my soarer. i don't know if they will match up to the oem buckles. i mirrored the part in the slicer.
Proteus
3d_export
$199
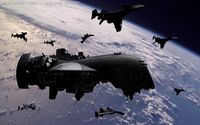
Proteus 3D Model
...proteus 3d model
3dexport
sci-fi spaceship warship cruiser destroyer
proteus 3d model psicore 4922 3dexport
turbosquid
$25
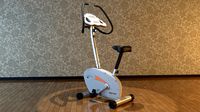
Proteus PEC 2025
...d
royalty free 3d model proteus pec 2025 for download as c4d on turbosquid: 3d models for games, architecture, videos. (1275757)
thingiverse
free
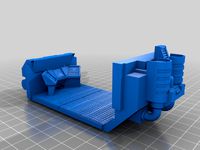
Proteus Proxy Detailed
...proteus proxy detailed
thingiverse
this is a version of the proteus proxy with a detailed interior.
unity_asset_store
$36

PROTEUS Frigate
...te your workflow with the proteus frigate asset from cgpitbull. find this & other space options on the unity asset store.
3dcadbrowser
free
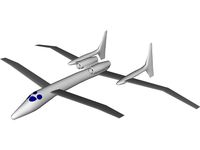
Proteus
...software.this 3d object can be downloaded in .max, .obj, .3ds, .fbx, .dxf, .lwo, .stl, .wrl, .ma, .dae, .x and .asc file formats.
unity_asset_store
$7
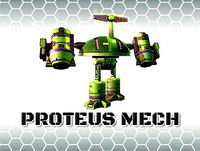
Proteus Mech Robot
...r workflow with the proteus mech robot asset from polyanarchy. find this & other robots options on the unity asset store.
thingiverse
free
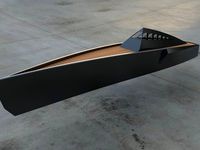
Proteus Concept Boat by omega
...is is my grabcad entry for the
makerbot replicator 2 desktop 3d printer challenge
http://grabcad.com/library/proteus-boat-concept
thingiverse
free
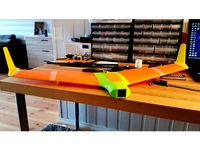
Proteus with Fuse Rear Motor mount by MADRobotNO
...tor cables.
this is 200 version of proteus: https://www.thingiverse.com/thing:2086413
2 last parts er designet for gopro session.
thingiverse
free
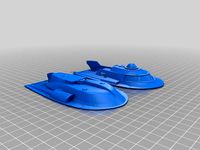
Proteus (halved) by guydebored
...e made a few changes on this version. the rear fins should be better conected now and you won't need rafts or support.
enjoy!
thingiverse
free
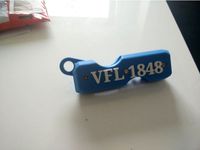
VFL Bochum 1848 - Proteus Key Holder by MacNite
...e
i made this quick mod of the proteus key holder by proteanman for my grand-father-in-law.
i hope, it may help someone as well.
Slope
design_connected
$11
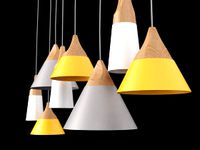
Slope
...slope
designconnected
miniforms slope computer generated 3d model. designed by skrivo.
3ddd
$1
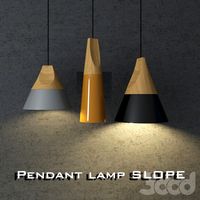
Pendant lamp SLOPE
...pendant lamp slope
3ddd
slope
pendant lamp slope
3ddd
$1
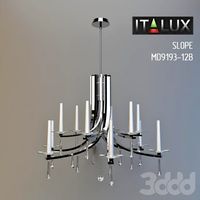
Italux slope md9193
...italux slope md9193
3ddd
italux
italux slope md9193
turbosquid
$15
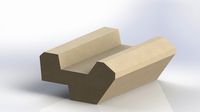
slope stone
...osquid
royalty free 3d model slope stone for download as stl on turbosquid: 3d models for games, architecture, videos. (1666168)
3d_export
$9
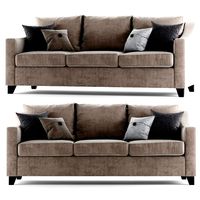
cameron slope
...cameron slope
3dexport
turbosquid
$12
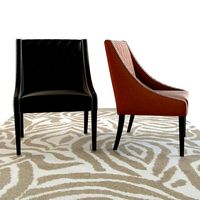
Sloping armchair
... available on turbo squid, the world's leading provider of digital 3d models for visualization, films, television, and games.
3ddd
free
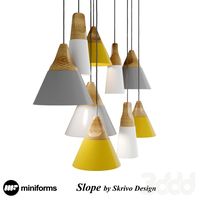
Slope Lamp by Skrivo Design
... miniforms , skrivo design
потолочные подвесные светильники "slope"
3d_export
$30
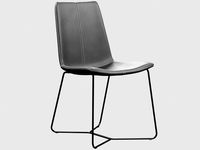
slope chair west elm
...slope chair west elm
3dexport
slope chair west elm max fbx obj
turbosquid
$20
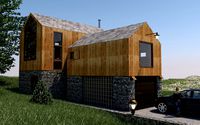
House 2x2 slope
...lty free 3d model house 2x2 slope for download as obj and fbx on turbosquid: 3d models for games, architecture, videos. (1278517)
3d_export
$5
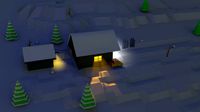
snow slope lowpoly
...snow slope lowpoly
3dexport
Openscad
thingiverse
free
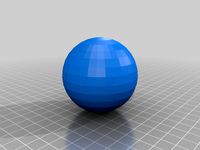
OpenSCAD sphere
...openscad sphere
thingiverse
basic project for openscad.
thingiverse
free
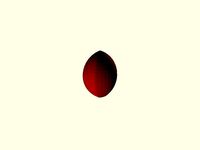
Openscad Football by KySyth
...openscad football by kysyth
thingiverse
openscad not tested
thingiverse
free
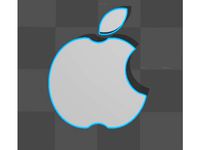
Openscad Apple by KySyth
...openscad apple by kysyth
thingiverse
openscad apple = not tested
thingiverse
free
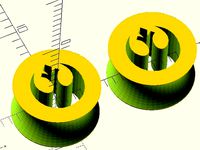
Plugs with openscad by benengel
...plugs with openscad by benengel
thingiverse
plugs with openscad and fontawesome
thingiverse
free
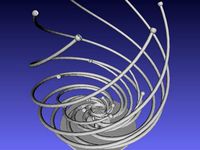
Openscad spirals by mafmuf
...openscad spirals by mafmuf
thingiverse
just fooling around with openscad.
thingiverse
free

Practice on OpenScad by ajensen906
...practice on openscad by ajensen906
thingiverse
a very crude practice on openscad
thingiverse
free
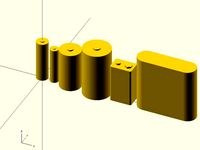
Batteries in OpenSCAD by roman_hegglin
...batteries in openscad by roman_hegglin
thingiverse
common batteries as modules for openscad.
thingiverse
free
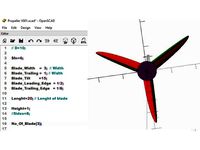
OpenScad Propeller by KySyth
...se
trying to make a propeller with openscad = not tested
this is some of the results
added the openscad file but still need work
thingiverse
free
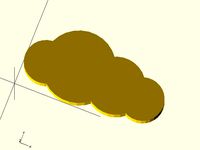
Openscad Cloud by Twanne
...openscad cloud by twanne
thingiverse
openscad cloud.
size can be adjusted
thingiverse
free
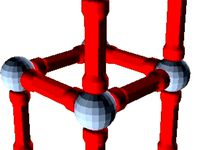
Geomag for OpenScad by vicnet
...geomag for openscad by vicnet
thingiverse
openscad file to design geomag things.
Design
3ddd
$1
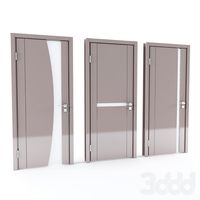
LINE DESIGN (Doors Design)
...line design (doors design)
3ddd
дверь
modern doors design - line design concept
3ddd
$1
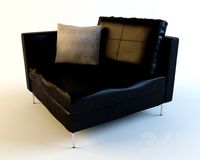
VER DESIGN
...ver design
3ddd
ver design
кресло ver design
3ddd
$1
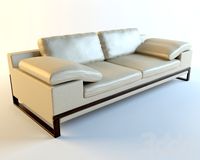
VER DESIGN
...ver design
3ddd
ver design
диван ver design
3ddd
$1
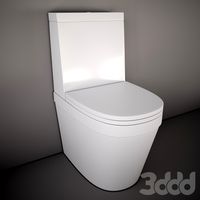
Bagno design
...bagno design
3ddd
bagno design , унитаз
санитария bagno design
3ddd
free
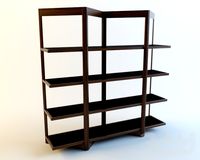
VER DESIGN
...ver design
3ddd
ver design , стеллаж
полка ver design
3ddd
$1
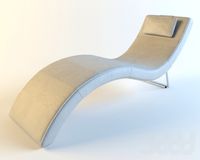
VER DESIGN
...ver design , лежак , шезлонг
шезлонг ver design
3d_export
free
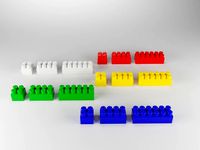
designer
..., trees and much more. the model has 3 types of parts: - 4 cells - 6 cells - 8 cells the *.max file contains 5 colored materials.
3d_export
$19
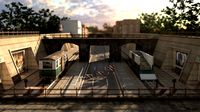
level design
...level design
3dexport
you can use this design (level design) in your own game.
3d_export
$7
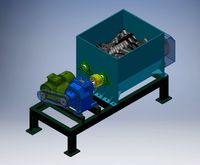
Crusher design
...crusher design
3dexport
crusher design
3d_export
$4
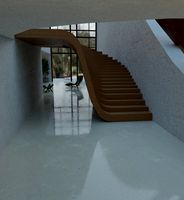
interior design
...interior design
3dexport
interior design