Thingiverse
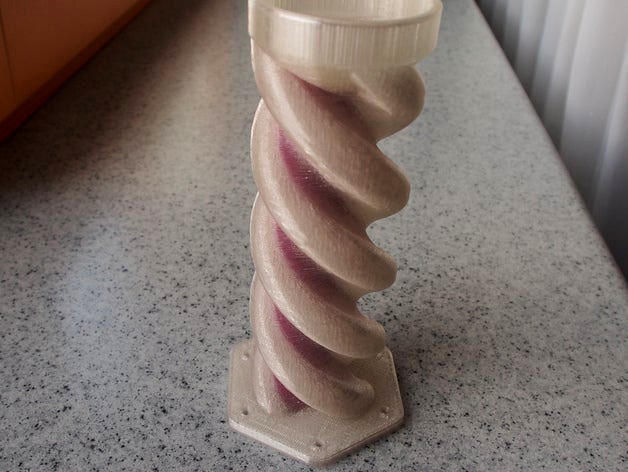
Progressing Cavity Pump (cycloidical) by mechadense
by Thingiverse
Last crawled date: 3 years, 1 month ago
Note: Use of this code is DEPRECATED
Generating this progressing cavity pump thing that is presented here can
now be done with just a few lines of code by using the new library:http://www.thingiverse.com/thing:777936https://github.com/lsuess/scad-lib-cyclogearprofiles
Here is a similar (followup next version) progressing cavity pump thing where that new library is used.http://www.thingiverse.com/thing:867401
DESCRIPTION:
This is the center part of a progressing-cavity-pump (PCP-pump or moineau-pump)
It implements the design approach with alternating epi- and hypocycloids which avoids cusps/kinks (the curve is C1 but not C2 continous)
Right now it uses two and threefold symmetry for rotor and stator respectively, but it shouldn't be hard to change it to any N and (N+1) symmetry (it's prepared) like three and four for more sturdiness or one and two for more throughput.
It is a positive displacement pump and thus provides (if the clearance would be zero) constant flow with arbitrary pressure. At no time the input and output section is directly connected. It is suitable to pump high viscous liquids possibly mixed with solid particles. You can find more info on wikipedia.
IMPORTANT NOTES:
Major tweaking points are marked with arrows.
Currently wall thicknesses are faked by scaling correctly for the radial component and rotating incorrectly (by eye) for tangential component. An offset in the epi and hypocycloid functions would be better.
For the initial print I used a very high clearance of 0.6mm to make sure it will fit.
If your printer is tuned well I recommend to reduce it a lot and make a new stator *.stl.
sidenote:
There are also conical PCPs which by nature cant be completely tight if made out of noncompliable material.
MOTIVATION:
I am thinking about a steel printed version for re extrusion of PLA and PET plastics. Judging from the PLA melt artworks PLA should flow in by gravity. Sadly I had no success trying to "gravity melt" PET in a steel-can at 230ð in 15min. Melting it with an soldering iron at that temperature works like a charm ... why the difference?
For now this is a huge one just for fun and maybe for (off printhead?) paste extrusion.
SOURCES:
http://siag.project.ifi.uio.no/problems/gravesen/http://www2.mat.dtu.dk/people/J.Gravesen/MoineauPump/
Generating this progressing cavity pump thing that is presented here can
now be done with just a few lines of code by using the new library:http://www.thingiverse.com/thing:777936https://github.com/lsuess/scad-lib-cyclogearprofiles
Here is a similar (followup next version) progressing cavity pump thing where that new library is used.http://www.thingiverse.com/thing:867401
DESCRIPTION:
This is the center part of a progressing-cavity-pump (PCP-pump or moineau-pump)
It implements the design approach with alternating epi- and hypocycloids which avoids cusps/kinks (the curve is C1 but not C2 continous)
Right now it uses two and threefold symmetry for rotor and stator respectively, but it shouldn't be hard to change it to any N and (N+1) symmetry (it's prepared) like three and four for more sturdiness or one and two for more throughput.
It is a positive displacement pump and thus provides (if the clearance would be zero) constant flow with arbitrary pressure. At no time the input and output section is directly connected. It is suitable to pump high viscous liquids possibly mixed with solid particles. You can find more info on wikipedia.
IMPORTANT NOTES:
Major tweaking points are marked with arrows.
Currently wall thicknesses are faked by scaling correctly for the radial component and rotating incorrectly (by eye) for tangential component. An offset in the epi and hypocycloid functions would be better.
For the initial print I used a very high clearance of 0.6mm to make sure it will fit.
If your printer is tuned well I recommend to reduce it a lot and make a new stator *.stl.
sidenote:
There are also conical PCPs which by nature cant be completely tight if made out of noncompliable material.
MOTIVATION:
I am thinking about a steel printed version for re extrusion of PLA and PET plastics. Judging from the PLA melt artworks PLA should flow in by gravity. Sadly I had no success trying to "gravity melt" PET in a steel-can at 230ð in 15min. Melting it with an soldering iron at that temperature works like a charm ... why the difference?
For now this is a huge one just for fun and maybe for (off printhead?) paste extrusion.
SOURCES:
http://siag.project.ifi.uio.no/problems/gravesen/http://www2.mat.dtu.dk/people/J.Gravesen/MoineauPump/
Similar models
grabcad
free

Progressive Cavity Pump
...ion of the form in the original patents. i think i got it right as witnessed by the single contact line between rotor and stator.
grabcad
free

Rotor and Stator for progressive cavity pump
...rotor and stator for progressive cavity pump
grabcad
6 bar head and 2 m3/h capasity
thingiverse
free

A Simpler Construction of Moineau Pump Stator via CNC Milling by encan
... simpler stator within a 2:1 moineau's progressing cavity pump (*) as in:
https://www.youtube.com/watch?v=eutr9iwuhsu
grabcad
free

PROGRESSIVE CAVITY PUMP
...progressive cavity pump
grabcad
progressive cavity pump
grabcad
free

Screw pump
...onents for leading progressive cavity pump manufacturer from india - visflow helical pumps: http://www.helicalpumps.in/about.html
grabcad
free

Progressive Cavity Pump Set
...progressive cavity pump set
grabcad
progressive cavity pump set
grabcad
free

Progressive Cavity Pump Inoxpa 2KSF20
... spiral and stator internal shape estimated.
inlet and outlet size dn40 tri clover clamp type flanges.
output 25ml per revolution
thingiverse
free

PCP pump - improved code by mechadense
... benefit (except slightly better sealing maybe for pumps that are printed with high clearance and that pump low viscosity fluids)
grabcad
free

pc pump
... fluid by means of the progress, through the pump, of a sequence of small, fixed shape, discrete cavities, as its rotor is turned
grabcad
free

Progressive Cavity Pump Seepex BN 5-6L
...riven by a 1.1 kw teco maxe3 motor and
mounted onto a fabricated base frame
n1 : 2 inch flange
n2 : 2 1/2" flange
sat file
Mechadense
thingiverse
free
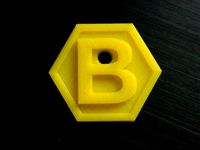
Bee ... by mechadense
...bee ... by mechadense
thingiverse
print request at
linuxwochen 2015 vienna austriahttp://www.linuxwochen.at/wien/
thingiverse
free
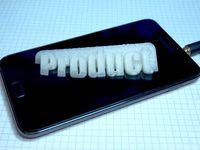
Product by mechadense
...product by mechadense
thingiverse
just a prop. convert your phone to a fake atomically precise personal fabricator.
thingiverse
free
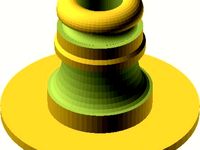
Water Hose Connector by mechadense
...water hose connector by mechadense
thingiverse
compatible with the gardener(tm) system.
thingiverse
free
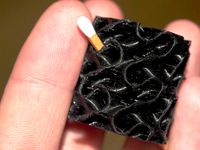
Gyroid Cylinder by mechadense
...iverse
made with minisagecadashttp://www.thingiverse.com/thing:40210
command: intersection2(cylinderc(30,60),gyroid_left(3,25))
thingiverse
free

Sheet Pin by mechadense
...nse
thingiverse
a pin & clamping ring combo to clamp thin plates together.
e.g. usable as connectors for scissor mechanisms.
thingiverse
free
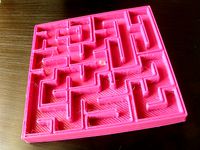
Maze 10x10 - simple by mechadense
...maze 10x10 - simple by mechadense
thingiverse
singly connected. every pair of points can be used as start and goal.
thingiverse
free
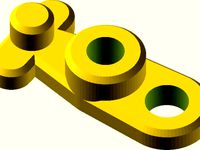
Nail-to-Tentpeg Converter by mechadense
...nail-to-tentpeg converter by mechadense
thingiverse
make tentpegs from nails with this little heads.
customize to your needs.
thingiverse
free
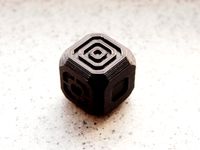
Simplistic Symmetric Die by mechadense
...simplistic symmetric die by mechadense
thingiverse
for gaming afk.
you can support me by ordering there:shapeways entry
thingiverse
free
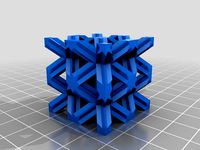
111 spaceframe demo by mechadense
...111 spaceframe demo by mechadense
thingiverse
if you want to know how a 111 space-frame looks like here it is.
thingiverse
free
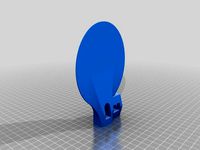
Toy Propeller Fin by mechadense
...toy propeller fin by mechadense
thingiverse
fin for my old two blade propeller thing:http://www.thingiverse.com/thing:8178
Cycloidical
3d_export
$10
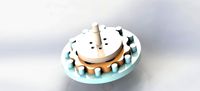
cycloidal drive
...cycloidal drive
3dexport
cycloidal drive
thingiverse
free
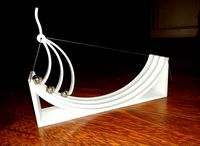
Cycloid art by papp328
...cloid art by papp328
thingiverse
an artistic physic experiment. the curve is a cycloid which has famous features. look after it.
thingiverse
free
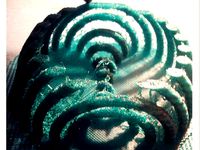
Half Cycloid Spiral Spacecurve by espen
...half cycloid spiral spacecurve by espen
thingiverse
half cycloid spiral spacecurve.
thingiverse
free
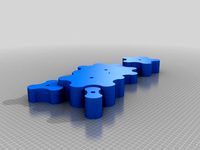
cycloid gear script by ekaggrat
...... it is based on a alternating epicycloid and hypocycloid tooth profile,...
http://demonstrations.wolfram.com/cycloidalgears/
thingiverse
free
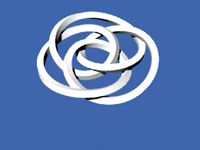
Cycloidal Knot by mm1440
...cycloidal knot by mm1440
thingiverse
square tube rotating around space curve.
thingiverse
free
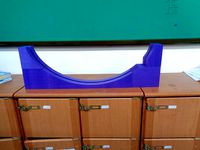
Cycloid Period Experiment Cit with Arduino by CNSHmath
...cycloid period experiment cit with arduino by cnshmath
thingiverse
cycloid model to sound its period using arduino
thingiverse
free
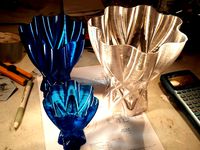
Cycloidic Vase (t-glase) by scottvader
...hingiverse
a simple vase created using solidworks lofts to connect two cycloidic gear like ends. looks great in taulman t-glase.
thingiverse
free
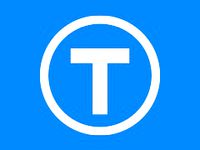
Cycloid Penny Slide by guido666
...e curve problem, which is the curve of fastest descent due to gravity. you can store some pennies in the slots in the base, too.
thingiverse
free
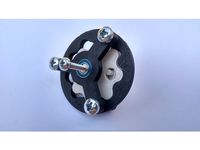
Cycloidal Drive by Meia
...m5 bolt, 1 m3 bolt and a small 5mm washer.
if you put it together carefully and maybe sand it a little it will run very smoothly.
thingiverse
free
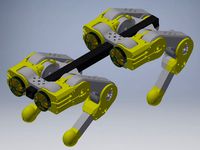
Quadruped with 3D cycloidal Gearboxes
...th modified shaft)
absolute magnetic encoder as5147 (custom board)
https://hackaday.io/project/167855-simple-cycloidal-robot-knee
Cavity
turbosquid
$10

oral cavity
...osquid
royalty free 3d model oral cavity for download as fbx on turbosquid: 3d models for games, architecture, videos. (1512365)
turbosquid
$20
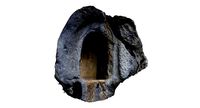
Cavity Rock
...y free 3d model cavity rock for download as max, obj, and fbx on turbosquid: 3d models for games, architecture, videos. (1397880)
turbosquid
$29
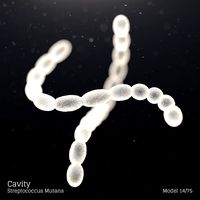
Cavity - Streptococcus Mutans
...vity - streptococcus mutans for download as max, fbx, and obj on turbosquid: 3d models for games, architecture, videos. (1626152)
turbosquid
$24
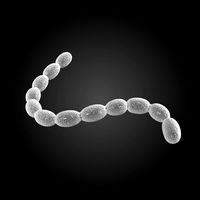
cavity - streptococcus mutans
... available on turbo squid, the world's leading provider of digital 3d models for visualization, films, television, and games.
turbosquid
$7
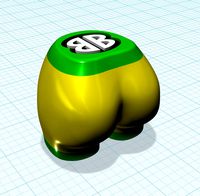
Bootie Music Shaker - Dual Cavity
...d model bootie music shaker - dual cavity for download as stl on turbosquid: 3d models for games, architecture, videos. (1338127)
turbosquid
$7
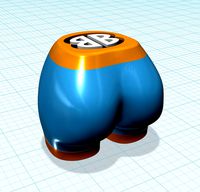
Bootie Spice Shaker - Double Cavity
...model bootie spice shaker - double cavity for download as stl on turbosquid: 3d models for games, architecture, videos. (1338377)
turbosquid
$5
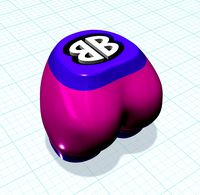
Bootie Spice Shaker - Single Cavity
...model bootie spice shaker - single cavity for download as stl on turbosquid: 3d models for games, architecture, videos. (1338123)
turbosquid
$5
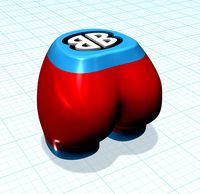
Bootie Music Shaker - Single Cavity
...model bootie music shaker - single cavity for download as stl on turbosquid: 3d models for games, architecture, videos. (1338116)
turbosquid
$14
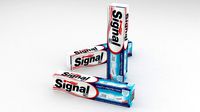
Signal Cavity Protection Toothpaste 100ml 2019
...l cavity protection toothpaste 100ml 2019 for download as max on turbosquid: 3d models for games, architecture, videos. (1417738)
3d_export
free
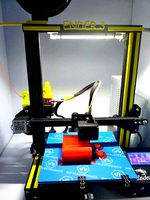
ender 3 frame cavity covers
... of the creality ender 3 - makes it look a bit more attractive it just slides into the open channels of the aluminium framework
Pump
3d_export
$5
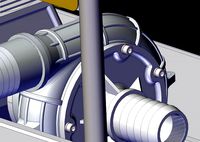
pump
...pump
3dexport
pump
archibase_planet
free
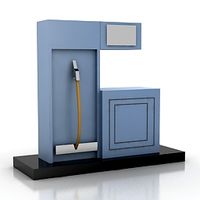
Pump
...pump
archibase planet
petrol pump petrol station gas station
pump - 3d model (*.gsm+*.3ds) for interior 3d visualization.
3d_ocean
$8
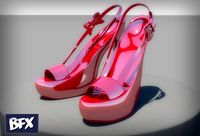
Pumps
...ps
3docean
girls heels high kicks pumps shoes stilettos womens
womens high heels, pumps or stilettos. polygon model – no textures
3ddd
free
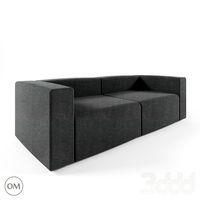
Pump
...ump
3ddd
pump , versus
производитель: versus
модель: pumphttp://www.versus.as/
turbosquid
$3
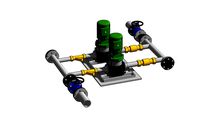
Pumps
...s
turbosquid
royalty free 3d model pumps for download as skp on turbosquid: 3d models for games, architecture, videos. (1275250)
3d_export
$5
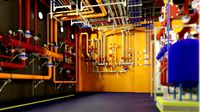
pump
...pump
3dexport
turbosquid
$39
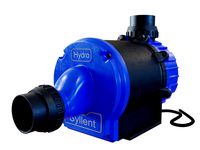
Realistic Water pump SYLLENT PUMP
...realistic water pump syllent pump for download as max and obj on turbosquid: 3d models for games, architecture, videos. (1312864)
turbosquid
$150

Pumpe
...yalty free 3d model pumpe for download as ige, blend, and stl on turbosquid: 3d models for games, architecture, videos. (1284318)
3d_export
$10
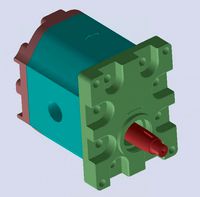
gear pump
...gear pump
3dexport
it is a gear pump in iges format
turbosquid
$19
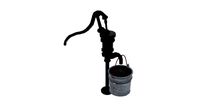
Old Water Pumps Gas Pumps
...pumps gas pumps for download as 3ds, obj, fbx, blend, and dae on turbosquid: 3d models for games, architecture, videos. (1207997)
Progressing
3ddd
free
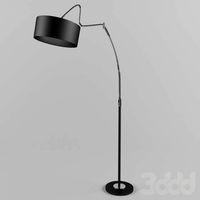
Baga / Progress
...baga / progress
3ddd
baga
progress baga
3ddd
$1
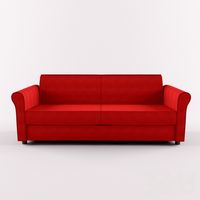
Futura / Progress
...futura / progress
3ddd
futura
фабрика futura модель progress
3ddd
$1
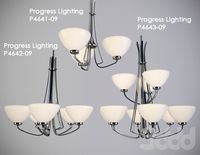
светильник Progress Lighting
...9):
d -50,8 см.
светильник progress lighting (art.p4642-09):
d -62 см.
светильник progress lighting (art.p4643-09):
d -68,6 см.
turbosquid
$5
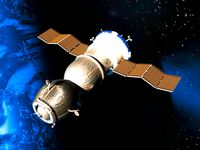
spaceship progress
...
royalty free 3d model spaceship progress for download as max on turbosquid: 3d models for games, architecture, videos. (1589494)
turbosquid
$5

Progressive Knife
... available on turbo squid, the world's leading provider of digital 3d models for visualization, films, television, and games.
turbosquid
$39
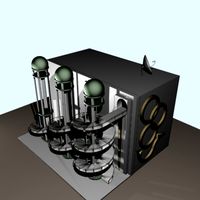
Progressive Arts building
... available on turbo squid, the world's leading provider of digital 3d models for visualization, films, television, and games.
3ddd
$1

Baga Progress - 3291
...baga progress - 3291
3ddd
baga
baga art.3291
3ddd
$1
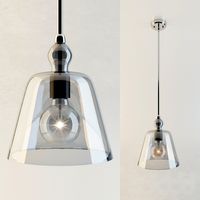
Progress Lighting P5184-104 1
...progress lighting p5184-104 1
3ddd
progress lighting
kitchen lighting
bar lighting
3ddd
free
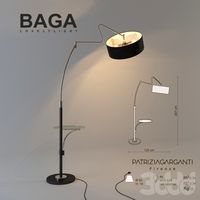
Baga Progress 3434
...a garganti
art. 3434
4 lights floor lamp
finish: leaden and nickel
lampshades: black leather
cm l. 135 - h. 207
d: 50
4x40w e14
turbosquid
$50
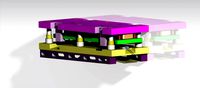
Progressive Sheet Metal Mold
...ree 3d model progressive sheet metal mold for download as ige on turbosquid: 3d models for games, architecture, videos. (1439355)