Thingiverse
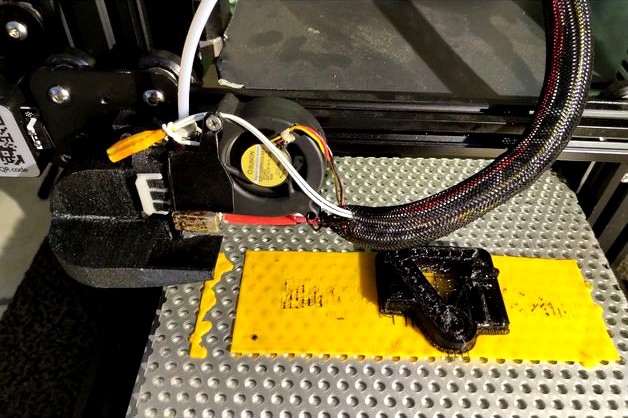
Polycarbonate Recirculation Ender PC mods Stage1 by dhilipp
by Thingiverse
Last crawled date: 3 years, 3 months ago
Print Polycarbonate or other materials with 300°C on a cheap machine like this Ender3.
Recirculate air from the heatsink, to heat an enclosure and prevent warping.
This stage one is fully working, but it can be seen as a bootstrap: You will get a bad print first without these mods of course, but it will enable you to get a better print next time, and to build Stage2, which will be a fully printed toolhead, posted here soon.
Generally speaking, printing PC is really a pain, but it could be usefull for printing functional prototypes.
You still need some kind of housing, or, at least a hood, to keep things warm. Ambient temperature is more important here than usually. I use to set the outlet of the heatsink to 80 till 100 °C, which is still fine with the bowden tube and it gives a minimum of about 50°C on the edges of the buildplate. It also preheats your material a bit, or cools it when you turn up the fan for PLA printing. Consider this to be a very good effect when retracting PLA!
It's a good idea to start printing smaller parts, heating up the room while getting bigger.
layeradhesion often lacks, when printing to cold or when the object needs too much moves in y-direction. but it's really possible to print objects, let's say half the size of the buildplate, with this bulletproof polymer.
suggested settings:
-minimal infill as supports, alligned (in cura infill "lines" put one angle in "infill line directions")
-min 3 perimeters to keep in some warmth
-always lift head while travelling
-cura->print settings(3bars_menu:expert view)->experimental->"SLICINGTOLLERANCE: EXCLUSIVE" is mandatory for good fittings and threads to print in the right dimensions
hardware requirements:
-a good mainboard with 2nd hotend terminals for the radial fan and
-2nd temp sensor (same as hotend)
-use a fuse! you need to print at 299°C (silicone insulations are not rated to this)
-update or compile the Marlin firmware (i use a bigtree SKR1.3 in case you want to copy)
-heatbreak without teflon inlay
-and of course stay in place (heating failures are likely to occure)
here you find my marlin version with a PID for Chamberhttps://github.com/RaabenF/Marlin
the PID is adjustable in the menu config->temp->advanced->PID C
sadly there are some problems in the latest Cura 4.7 with profiles, you might have to install 4.6.x if you want to use my included settings
download: https://github.com/Ultimaker/Cura/releases/tag/4.6.2
finally, one sure advantage, is a way much faster heating of the bed.
please let me know what you think of it
and
happy printing!
Recirculate air from the heatsink, to heat an enclosure and prevent warping.
This stage one is fully working, but it can be seen as a bootstrap: You will get a bad print first without these mods of course, but it will enable you to get a better print next time, and to build Stage2, which will be a fully printed toolhead, posted here soon.
Generally speaking, printing PC is really a pain, but it could be usefull for printing functional prototypes.
You still need some kind of housing, or, at least a hood, to keep things warm. Ambient temperature is more important here than usually. I use to set the outlet of the heatsink to 80 till 100 °C, which is still fine with the bowden tube and it gives a minimum of about 50°C on the edges of the buildplate. It also preheats your material a bit, or cools it when you turn up the fan for PLA printing. Consider this to be a very good effect when retracting PLA!
It's a good idea to start printing smaller parts, heating up the room while getting bigger.
layeradhesion often lacks, when printing to cold or when the object needs too much moves in y-direction. but it's really possible to print objects, let's say half the size of the buildplate, with this bulletproof polymer.
suggested settings:
-minimal infill as supports, alligned (in cura infill "lines" put one angle in "infill line directions")
-min 3 perimeters to keep in some warmth
-always lift head while travelling
-cura->print settings(3bars_menu:expert view)->experimental->"SLICINGTOLLERANCE: EXCLUSIVE" is mandatory for good fittings and threads to print in the right dimensions
hardware requirements:
-a good mainboard with 2nd hotend terminals for the radial fan and
-2nd temp sensor (same as hotend)
-use a fuse! you need to print at 299°C (silicone insulations are not rated to this)
-update or compile the Marlin firmware (i use a bigtree SKR1.3 in case you want to copy)
-heatbreak without teflon inlay
-and of course stay in place (heating failures are likely to occure)
here you find my marlin version with a PID for Chamberhttps://github.com/RaabenF/Marlin
the PID is adjustable in the menu config->temp->advanced->PID C
sadly there are some problems in the latest Cura 4.7 with profiles, you might have to install 4.6.x if you want to use my included settings
download: https://github.com/Ultimaker/Cura/releases/tag/4.6.2
finally, one sure advantage, is a way much faster heating of the bed.
please let me know what you think of it
and
happy printing!
Similar models
thingiverse
free
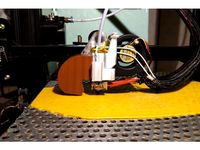
Polycarbonate Recirculation Ender PC mods Stage2 by dhilipp
...iginal screws. further i'm trying to use only "one fan" for part-cooling and heating (brown outlet in the pictures)
thingiverse
free
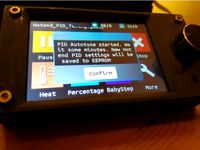
Hotend and Heatbed PID Tuning - Gcode programs
...et heatbed temp to 0c
m117 hotend pid tuning done
g4 p4000
m117 by dareknorway https://www.thingiverse.com/thing:4226437
g4 p4000
thingiverse
free
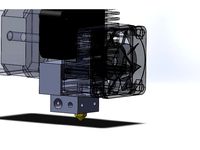
Hotend Heatsink/Mount by Bois3D
...at the 6mm threaded heat break rod threads into. this allowed me to run cooler hotend temps and eliminate skipping and clogging.
thingiverse
free
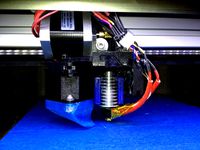
Tygr MOD E3D V5 Felix extruder by tygrik
...nt for clamp nut and smaller hole for the filament with conus. clamp with smaller hole for the filament with conus on both sides.
thingiverse
free
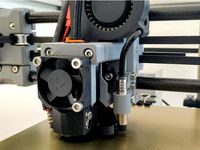
PINDA for HyperCube + Marlin config
...arian blog post:https://zen3d.hu/p-i-n-d-a-marlin-konfiguracio/
mosquito hotend adapter:https://www.thingiverse.com/thing:4032460
thingiverse
free

CraftBot Platform by 3DForms
... up proper print settings like hotend temp, bed temp, fan, layer height, print speed, retract settings, etc... for your filament.
thingiverse
free
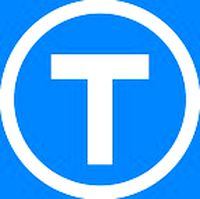
shotgun to M4 mag adaptor by southpaw87
...e same.
printed with tree support, on buildplate only, upside down in cura, 15% infill with pla.
nozzle temp 200c, bed temp 55c.
thingiverse
free
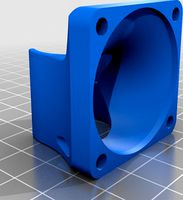
E3D v6 Hotend Heatsink 40mm Fan Duct by Zep_To_3D_Druck
...nt it.
here is the fusion 360 tutorial.https://youtu.be/nly3pzdyfxo
here my youtube channelhttps://www.youtube.com/c/zepto3ddruck
thingiverse
free
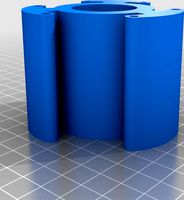
Spool Filament Holder by Mandrk
... to top and bottom and 3 or 4 walls
5h to print,
settings:
material: pla
hotend temp 205°,
bed temp 60°
printing speed 60mm
thingiverse
free
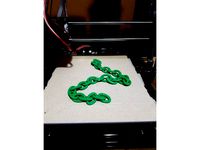
16" Chain by Darknyte
...ted using pla on a heated bed at 55°c and 210°c nozzle temp. the footprint for this print is about 8" x 3" x 3/4".
Dhilipp
thingiverse
free
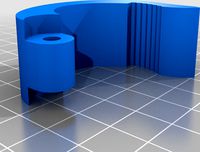
snappy light by dhilipp
...snappy light by dhilipp
thingiverse
a m4 screw is required.
print with exclusive sclicing in cura!
thingiverse
free

HDD 5,25 to 3,5 in drive bay with f3d file by dhilipp
...r what is the better way in the end.
though i think the 3,5" frame looks quite good and places the hdd inside your computer.
thingiverse
free
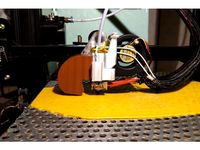
Polycarbonate Recirculation Ender PC mods Stage2 by dhilipp
...iginal screws. further i'm trying to use only "one fan" for part-cooling and heating (brown outlet in the pictures)
Stage1
thingiverse
free
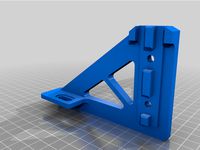
Sidewinder X1 - 3DChanh's Z-Axis Right minimal brace by Daali
...3dchanh where the bracket is raised to accommodate his stage1 back brace. i finally put on stage 1 and...
thingiverse
free
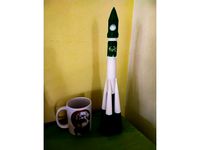
Soviet rocket R-7 Vostok Modular Stages 1/85 - Yuri Gagarin by titanboreal
...upsidedown) vostok-1-stage2-4-white vostok-1-stage3-1-green (print upsidedown) vostok-1-stage3-2-white x4-vostok-1-stage1-1-green (print upsidedown) x4-vostok-1-stage12-white x9-vostok-1-conector-white (print flatsidedown) x4-vostok-1-conector-green (stage 1 vs stage 2)...
thingiverse
free
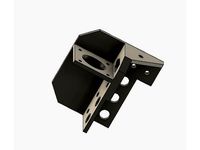
D-bot modifications by gzcwnk
...sep 6, 2015. http://www.thingiverse.com/thing:1001065 the modifications will consist of, stage1 a) replacement lhs stepper motor mount for t-bar nuts...
grabcad
free

cswp sample exam stage1
...cswp sample exam stage1
grabcad
solidworks 2022
cswp stage1
cg_trader
$4
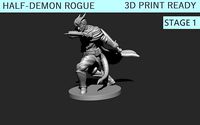
Half Demon Rogue Miniature Stage1 | 3D
...half demon rogue miniature stage1 | 3d
cg trader
this miniature of a tiefling rogue is perfect for tabletop rpg games.
grabcad
free

Reducer(Bevel&Helical Gear)
...gear) grabcad two stage reducer, using bevel gear as stage1 and helical as...
grabcad
free

Fastener with wings
...the bolt through the holes of the two plates. (stage1 then put a hexagon key into the hexagon slot...
clara_io
free
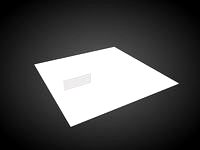
stage1
...stage1
clara.io
clara_io
free
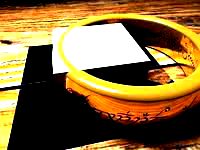
Stage1
...stage1
clara.io
Recirculation
3d_export
$5
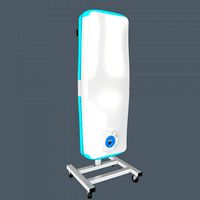
recirculator
...recirculator
3dexport
medical recirculator. under subdi.
turbosquid
$10
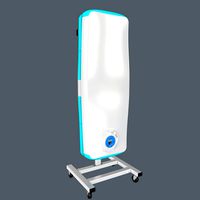
recirculator
...odel recirculator for download as c4d, c4d, fbx, obj, and stl on turbosquid: 3d models for games, architecture, videos. (1681233)
cg_studio
$99

EGR engine3d model
...chevrolet v8 vehicle race hot rod street exhaust gas recirculation gasturbine turbine .obj .fbx .max - egr engine 3d...
thingiverse
free
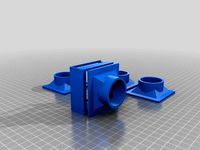
Recirculating air filter by Manxian
...inatly safe its best not to take chances with you or your families health this is designed to help maintain heat in the enclosure
thingiverse
free
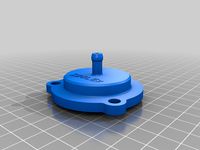
Opel Vauxhall internal recirculation Valve BOV 2.0 Turbo
...nal recirculation valve bov 2.0 turbo
thingiverse
opel/vauxhall 2.0 turbo internal recirculation valve (bov) for
z20lex engines.
thingiverse
free
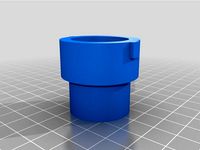
HKS SSQV Recirculating Adapter by notarikon
...ted, and currently resides in my vehicle. underbonnet temps have shown no issue (printed in pla), with no deformation or warping.
thingiverse
free
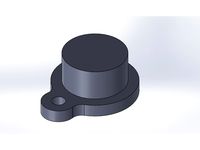
Saab T7 recirculation block off by hardov
...ecirculation path if you use td04 or gt17 turbo and cobra pipe. it is necessary if you want to install blow off valve to the car.
thingiverse
free
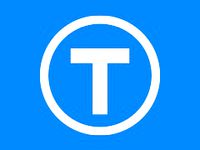
HKS SSQV Recirculation fitting with Whistle/Chirp by Skuce
...hks ssqv recirculation fitting with whistle/chirp by skuce
thingiverse
sketchup 2017
thingiverse
free
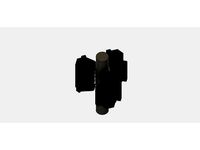
Recirculating linear bearing (modular) by GreyHunter147
...nd screw them together with simple m3 screws. it's small and cheap to print. next, i also add the 20x20 square frame version.
thingiverse
free
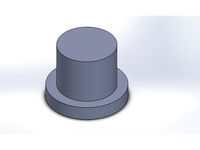
Saab T5 recirculation block off by hardov
...necessary if you want to install blow off valve to the car. works good with pla. i have used it a year on my car and no problems.
Polycarbonate
design_connected
$16
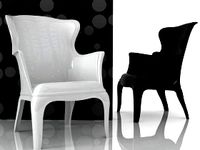
Polycarbonate armchair
...polycarbonate armchair
designconnected
polycarbonate armchair computer generated 3d model.
archive3d
free
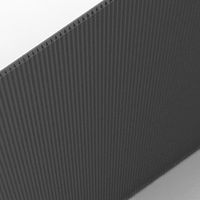
Polycarbonate 3D Model
...ve3d
polycarbonate plastic
polycarbonate sheet a little bit oversized for better visualization.
turbosquid
$15
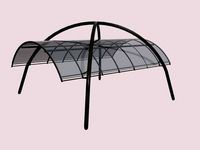
Polycarbonate Pergola Model 1
... available on turbo squid, the world's leading provider of digital 3d models for visualization, films, television, and games.
turbosquid
$15
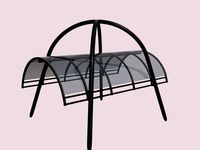
Polycarbonate Pergola Model 5
... available on turbo squid, the world's leading provider of digital 3d models for visualization, films, television, and games.
turbosquid
$15
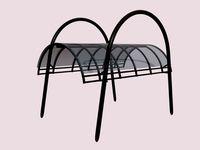
Polycarbonate Pergola Model 4
... available on turbo squid, the world's leading provider of digital 3d models for visualization, films, television, and games.
turbosquid
$15
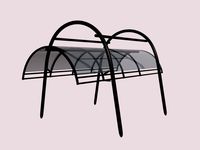
Polycarbonate Pergola Model 2
... available on turbo squid, the world's leading provider of digital 3d models for visualization, films, television, and games.
3ddd
$1
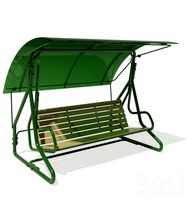
TMK-Pro Garden Swings Polycarbonate
... модификаторов открыт. геометрию можно легко модифицировать, увеличить количество полигонов для близких планов при необходимости.
turbosquid
$100
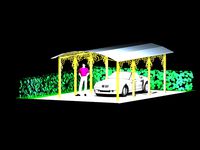
carport with elements of artistic forging and coating of polycarbonate
... available on turbo squid, the world's leading provider of digital 3d models for visualization, films, television, and games.
3ddd
$1
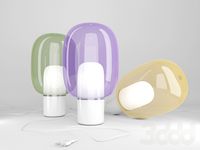
Foscarini YOKO
...yoko 3ddd foscarini , yoko foscarini yoko materials: pmma/ polycarbonate color: orange, green,...
3ddd
$1
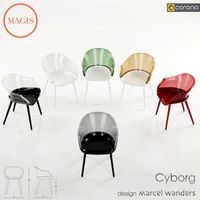
Magis / Cyborg Armchair
...of production: 2011. material: seat and legs in airmoulded polycarbonate back in standard injection-moulded polycarbonate. model available in 3dsmax,...
Ender
3ddd
$1
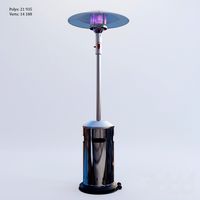
Enders / Elegance
...enders / elegance
3ddd
обогреватель
уличный газовый обогреватель enders elegance
высота: 2200 мм
3d_export
free
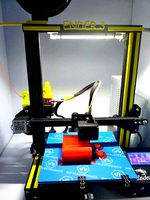
ender 3 frame cavity covers
... of the creality ender 3 - makes it look a bit more attractive it just slides into the open channels of the aluminium framework
turbosquid
$1
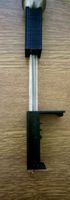
pen support for ender 3
...y free 3d model pen support for ender 3 for download as blend on turbosquid: 3d models for games, architecture, videos. (1611282)
3d_ocean
$9
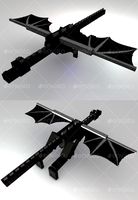
Ender Dragon Minecraft
...ojang obj poly videogames
ender dragon minecraft created with cinema 4d r15 formats included: max 2013 – fbx 2012 – c4d r15 – obj
3d_export
free

Creality ender enclosure webcam mount
...e creality enclosure. sure is better than a tripod. change it up if it helps. i printed pla with 50% infill on my dd ender 3 pro.
3d_export
free
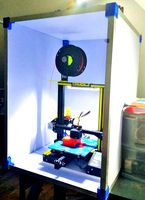
ender 3 enclosure corners
...er corners and 4 upper corners, using 25mmx25mm angled aluminium pieces that gets covered on inside of the frame with plexiglass
3d_export
free
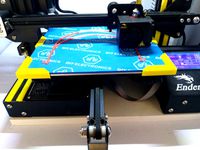
ender 3 3d print bed clips
...ed + normal aluminium bed frame of the creality ender 3 = 6mm (b) these clips are designed for glass plate + aluminium bed = 4mm
3d_export
$5
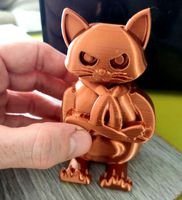
GRUMPY CAT
...grumpy cat 3dexport grumpy cat to print in ender ...
3d_export
$5
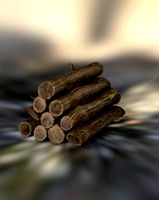
Logs fire
...with one multi material for corona and vray r ender. albedo, normal, uvmap, roughness format jpg 4096x4096 models:...
3d_export
$42
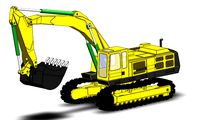
excavator
...is the original size. 0.12 mm printing surface creality ender5 ...
Mods
design_connected
$13
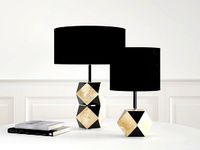
MOD. 4233 - MOD. 4234 Table Lamp
...mod. 4233 - mod. 4234 table lamp
designconnected
arcahorn mod. 4233 - mod. 4234 table lamp computer generated 3d model.
design_connected
$11
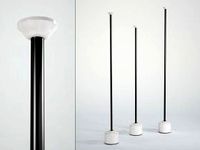
MOD.1095
...mod.1095
designconnected
mod.1095 computer generated 3d model. designed by sarfatti, gino.
3ddd
$1
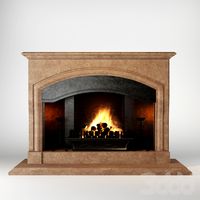
fireplaces mod Spec
...fireplaces mod spec
3ddd
камин
fireplaces mod spec 180x90x125h
3ddd
free
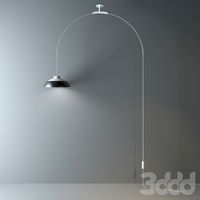
Flos Mod. 2129
... mod
фабрика: flos
модель: mod. 2129
описание: подвесной светильник, металл, белый, черный.
сайт: www.flos.com
turbosquid
$32
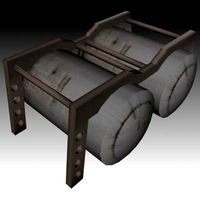
MOD A 001
... available on turbo squid, the world's leading provider of digital 3d models for visualization, films, television, and games.
turbosquid
$29
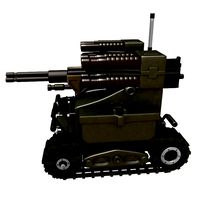
Maars Mod
... available on turbo squid, the world's leading provider of digital 3d models for visualization, films, television, and games.
turbosquid
$15
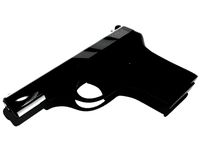
Mod 70..
... available on turbo squid, the world's leading provider of digital 3d models for visualization, films, television, and games.
turbosquid
$10
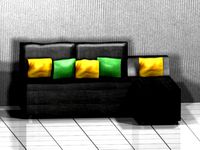
MOD Sofa
... available on turbo squid, the world's leading provider of digital 3d models for visualization, films, television, and games.
turbosquid
$1
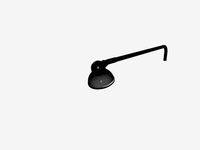
Mod-Lite
... available on turbo squid, the world's leading provider of digital 3d models for visualization, films, television, and games.
turbosquid
$1
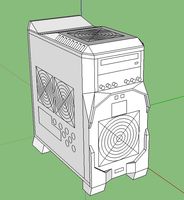
pc mod
... available on turbo squid, the world's leading provider of digital 3d models for visualization, films, television, and games.
Pc
archibase_planet
free
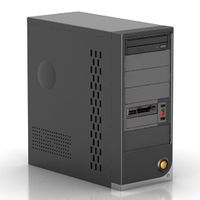
PC
...pc
archibase planet
pc case pc tower pc equipment system unit
pc - 3d model (*.gsm+*.3ds) for interior 3d visualization.
3d_export
free
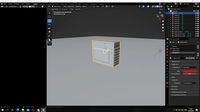
Pc
...pc
3dexport
pc
archibase_planet
free
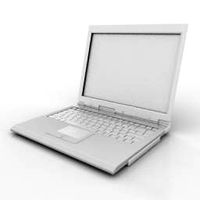
PC
...pc
archibase planet
notebook pc computer equipment
pc - 3d model (*.gsm+*.3ds) for interior 3d visualization.
archibase_planet
free
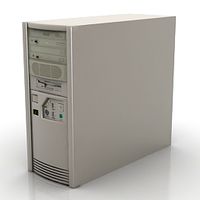
PC
...pc
archibase planet
system unit pc equipment
pc - 3d model (*.gsm+*.3ds) for interior 3d visualization.
archibase_planet
free
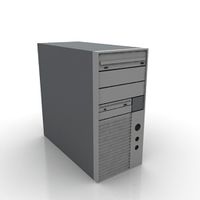
PC
...pc
archibase planet
pc equipment cabinet system unit
pc 70 - 3d model (*.gsm+*.3ds) for interior 3d visualization.
3d_export
$5
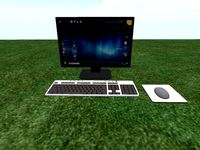
pc
...pc
3dexport
computer
archibase_planet
free
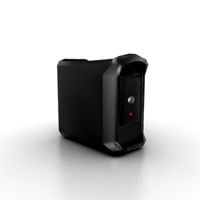
PC
...pc
archibase planet
cabinet chassis system unit
pc case n241107 - 3d model (*.gsm+*.3ds) for interior 3d visualization.
turbosquid
$3
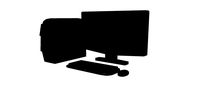
PC
...id
royalty free 3d model pc for download as ma, obj, and fbx on turbosquid: 3d models for games, architecture, videos. (1159175)
turbosquid
$7
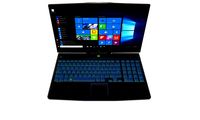
lap top ,pc portable, PC
...ty free 3d model lap top ,pc portable, pc for download as c4d on turbosquid: 3d models for games, architecture, videos. (1352084)
turbosquid
$100
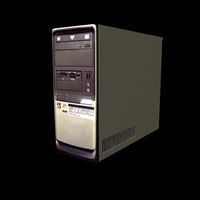
PC
... available on turbo squid, the world's leading provider of digital 3d models for visualization, films, television, and games.