Thingiverse
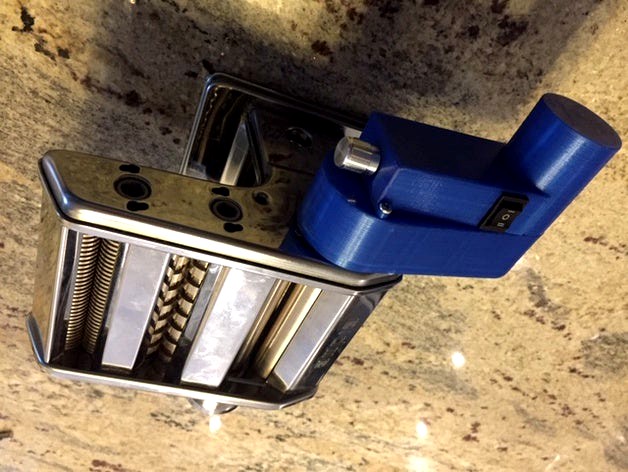
Pasta Machine drive motor
by Thingiverse
Last crawled date: 4 years, 2 months ago
This project started because I had a dead printer scanner going to the tip
I disassembled it and recovered several useful parts.
Since it contained a decent dc motor and power supply I decided to make myself a
drive motor for my pasta machine.
The motor is factory fitted with a metal toothed belt pinion. I filed off the flange and filed a flat onto the pinion
in order to accept the printed pinion. something similar found here. https://www.ebay.co.uk/itm/OEM-Canon-Pixma-iP4300-Printer-Belt-Drive-Motor-QK1-3042/192893271834?hash=item2ce955bf1a:g:btwAAOSwU~VcuQ5q
The printer contained a dia6.9mm steel shaft which I used for the axles of the 2nd and third gear.
axles 28.6mm long.
I filed 2 flats on the remainder of the steel shaft and used it to ream the centre holes of the printed gears.
I used the dia 9.5mm steel paper feed roller to make a square drive shaft to match pasta machine drive.
50mm long. I drilled and pinned the square drive to the final gear.
2 m3x14mm pan head screws make the pegs for the drive.
10 m3 self tapping screws recovered from the printer hold the assembly together.
2 original machine screws from the printer motor fix it in place.
Speed control as well as forward and reverse are provided via the dc motor controller which was purchased for the project.https://www.ebay.co.uk/itm/DC-6V-12V-24V-3A-Reversible-Motor-Speed-Controller-Regulator-Driver-Switch-PWM/173517709342?ssPageName=STRK%3AMEBIDX%3AIT&_trksid=p2057872.m2749.l2649
The 24v supply line from the printer powers the project but I have yet to design an enclosure for it.
The power jack was recovered from an old router which was also going to the tip.
Gears were designed in fusion 360 using the spur gear plugin. Each gear progessively steps up the tooth module to make the teeth stronger as the speed is reduced through the gear train and the torque increases. I used a backlash of 0.2mm. Gears printed in PLA with 0.1mm layer height 20% infill. Initially gears were too tight to mesh but printing at 99% scale solved that problem.
Other parts printed at 0.2mm layer height 20% infill. Print gears with the chamfer side down to reduce elephant foot. The electrics case could benefit from supports as does the bottom case
video https://vimeo.com/user104852921/review/371210122/4805199f0b
I disassembled it and recovered several useful parts.
Since it contained a decent dc motor and power supply I decided to make myself a
drive motor for my pasta machine.
The motor is factory fitted with a metal toothed belt pinion. I filed off the flange and filed a flat onto the pinion
in order to accept the printed pinion. something similar found here. https://www.ebay.co.uk/itm/OEM-Canon-Pixma-iP4300-Printer-Belt-Drive-Motor-QK1-3042/192893271834?hash=item2ce955bf1a:g:btwAAOSwU~VcuQ5q
The printer contained a dia6.9mm steel shaft which I used for the axles of the 2nd and third gear.
axles 28.6mm long.
I filed 2 flats on the remainder of the steel shaft and used it to ream the centre holes of the printed gears.
I used the dia 9.5mm steel paper feed roller to make a square drive shaft to match pasta machine drive.
50mm long. I drilled and pinned the square drive to the final gear.
2 m3x14mm pan head screws make the pegs for the drive.
10 m3 self tapping screws recovered from the printer hold the assembly together.
2 original machine screws from the printer motor fix it in place.
Speed control as well as forward and reverse are provided via the dc motor controller which was purchased for the project.https://www.ebay.co.uk/itm/DC-6V-12V-24V-3A-Reversible-Motor-Speed-Controller-Regulator-Driver-Switch-PWM/173517709342?ssPageName=STRK%3AMEBIDX%3AIT&_trksid=p2057872.m2749.l2649
The 24v supply line from the printer powers the project but I have yet to design an enclosure for it.
The power jack was recovered from an old router which was also going to the tip.
Gears were designed in fusion 360 using the spur gear plugin. Each gear progessively steps up the tooth module to make the teeth stronger as the speed is reduced through the gear train and the torque increases. I used a backlash of 0.2mm. Gears printed in PLA with 0.1mm layer height 20% infill. Initially gears were too tight to mesh but printing at 99% scale solved that problem.
Other parts printed at 0.2mm layer height 20% infill. Print gears with the chamfer side down to reduce elephant foot. The electrics case could benefit from supports as does the bottom case
video https://vimeo.com/user104852921/review/371210122/4805199f0b
Similar models
grabcad
free

Mini Desktop Belt Conveyor
...mini desktop belt conveyor
grabcad
24v dc worm gear motor can be controller forword/reverse, variable speed.
thingiverse
free
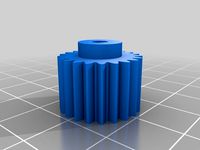
Motor Pinion Gear for Power Wheels Gearbox by hwswfun
...ft bore stronger such as more shell layers. as for me, i just reprinted it:).
i am using this for our initial snow removal robot
grabcad
free

accelerator pedal with potentiometer
...control speed project
high power 2000w 40a forward and reverse motor speed controller pwm brush motor controller dc 12v 24v 36v
thingiverse
free
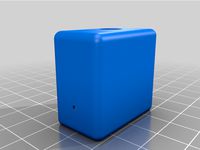
pwm motor controller case
...962512163
or if the link is broken a "3v-35v 12v 24v pwm dc 5a motor speed controller adjustable switch led fan dimmer"
grabcad
free

Johnson geared high torque DC motor
...equips metal bushes which makes these dc gear motors shaft wear-resistant. the shaft of the motor has a hole for better coupling.
thingiverse
free
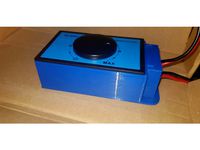
Speed Controller Box by Bastlwastl84
...controller: https://www.ebay.de/itm/20a-10-60v-12v-24v-36v-48v-pwm-dc-drehzahlregler-schalter-motor-speed-controller/363066144261
thingiverse
free
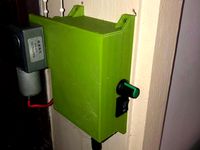
DIY Motorised Blind
...ed some m3 screws, both self tapping and normal for mounting the wall mount, motor and flange coupling. 10mm long should be fine.
thingiverse
free
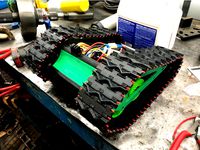
speed tank drive gear traxxas 32p pinion by derrick84
... bolt to drive wheel and will need to use shim to modify and drill the traxxas gear 68t shim is only used if you use traxxas gear
grabcad
free

Gear Pump Drive Motor
...gear pump drive motor
grabcad
use dc 24v
thingiverse
free
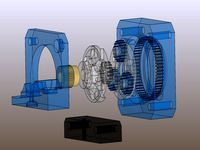
3:1 Planetary Geared Extruder
...f bearings
added pinion gear for smaller motor without recess or full length d drive to cater for extended d drine on the pinion.
Pasta
turbosquid
$39
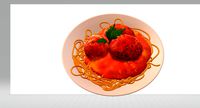
Pasta
...a
turbosquid
royalty free 3d model pasta for download as fbx on turbosquid: 3d models for games, architecture, videos. (1238387)
turbosquid
$15
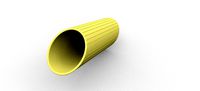
pasta
...a
turbosquid
royalty free 3d model pasta for download as 3dm on turbosquid: 3d models for games, architecture, videos. (1516385)
3ddd
free
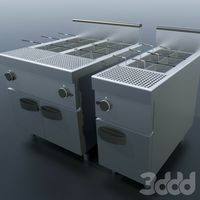
Pasta Cooker
...pasta cooker
3ddd
плита
pasta cooker
3d_export
$5
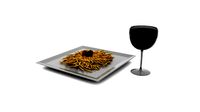
pasta and wine
...pasta and wine
3dexport
a plate of pasta with meatloaf and a glass of wine
archive3d
free
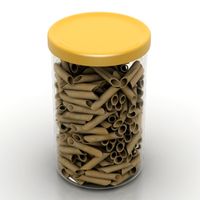
Pasta 3D Model
...odel
archive3d
pasta macaroni jar
pasta - 3d model (*.gsm+*.3ds) for interior 3d visualization.
3d_ocean
$5

Pasta Dinner
... is also low poly model but it is not include here. the high poly model weigh between 120mb to 150mb for the .blend and .obj f...
turbosquid
$5
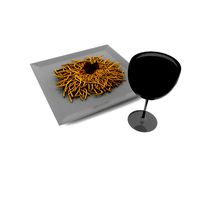
Pasta And Wine
...osquid
royalty free 3d model pasta and wine for download as on turbosquid: 3d models for games, architecture, videos. (1680643)
turbosquid
$40
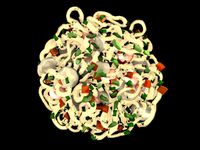
seafood pasta
... available on turbo squid, the world's leading provider of digital 3d models for visualization, films, television, and games.
turbosquid
$29

Pasta Box
... available on turbo squid, the world's leading provider of digital 3d models for visualization, films, television, and games.
turbosquid
$13
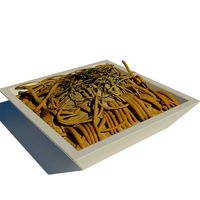
pasta (chicken)
... available on turbo squid, the world's leading provider of digital 3d models for visualization, films, television, and games.
Drive
turbosquid
$90
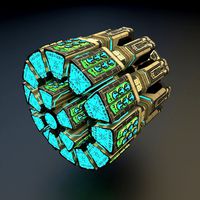
Drive
...turbosquid
royalty free 3d model drive for download as blend on turbosquid: 3d models for games, architecture, videos. (1654393)
3d_export
$10
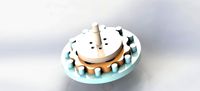
cycloidal drive
...cycloidal drive
3dexport
cycloidal drive
3d_ocean
$5
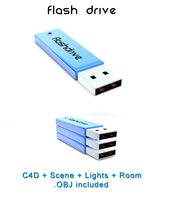
Flash Drive
...h drive included : – materials – scene ( lighs / room ) – .c4d + .obj for any questions please feel free to contact me thank you.
3d_ocean
$5
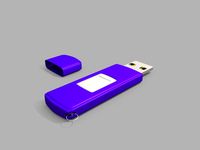
Usb drive
...s shaders and a lighting setup. it also has a small animation of it going in and out. i saved it out as both a .blend file and...
3d_ocean
$5
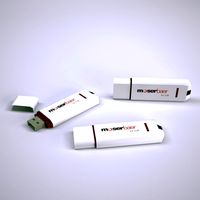
Pen Drive
...est computer drive game model good low poly new pen pen drive textured unwrapped uv very low poly
a very beautiful low poly model
3d_ocean
$10
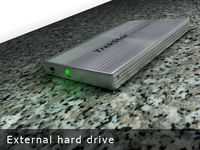
External hard drive
... is a detailed model of a trekstor external hard drive. you can easily modify the label on the top. simply edit the text objects.
turbosquid
$60

Star Drive
...squid
royalty free 3d model star drive for download as blend on turbosquid: 3d models for games, architecture, videos. (1254314)
turbosquid
$50
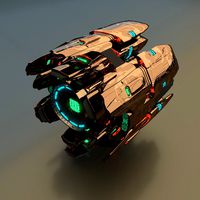
Star Drive
...squid
royalty free 3d model star drive for download as blend on turbosquid: 3d models for games, architecture, videos. (1263524)
turbosquid
$45
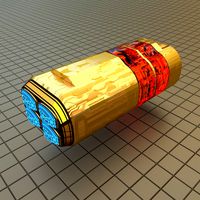
Star Drive
...squid
royalty free 3d model star drive for download as blend on turbosquid: 3d models for games, architecture, videos. (1287060)
turbosquid
$40
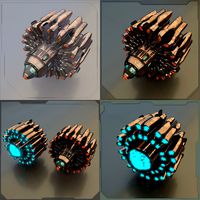
Star Drive
...squid
royalty free 3d model star drive for download as blend on turbosquid: 3d models for games, architecture, videos. (1261902)
Motor
archibase_planet
free
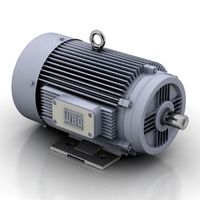
Motor
...base planet
motor motor engine engine electric motor
motor wagner n250213 - 3d model (*.gsm+*.3ds) for interior 3d visualization.
archibase_planet
free
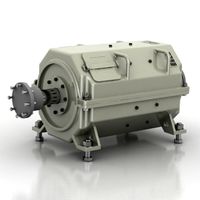
Motor
...motor
archibase planet
motor motor engine engine
motor n151112 - 3d model (*.gsm+*.3ds) for interior 3d visualization.
archibase_planet
free
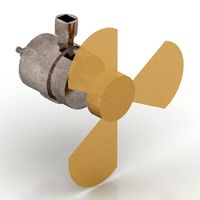
Motor
...motor
archibase planet
motor motor engine engine
motor n150615 - 3d model (*.gsm+*.3ds+*.max) for interior 3d visualization.
turbosquid
$15
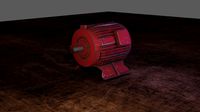
Motor
...otor
turbosquid
royalty free 3d model motor for download as on turbosquid: 3d models for games, architecture, videos. (1639404)
3d_ocean
$5
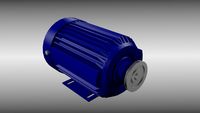
Electric motor
...electric motor
3docean
car electric engine industry motor phase train vehicle
an electric motor enjoy!
3d_ocean
$18
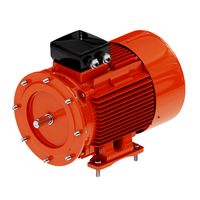
Electric Motor
...electric motor
3docean
electric motor engine machine mover parts
3d model electric motor for hoist crane
turbosquid
$29
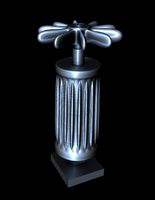
Motor
... available on turbo squid, the world's leading provider of digital 3d models for visualization, films, television, and games.
turbosquid
$5
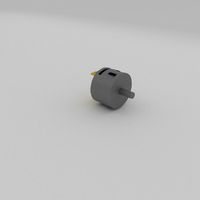
Motor
... available on turbo squid, the world's leading provider of digital 3d models for visualization, films, television, and games.
3d_export
$5
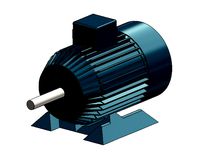
electric motor
...electric motor
3dexport
electric motor use for industrial purposes
3d_export
$5
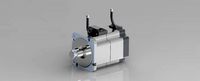
servo motor
...tor
3dexport
it's a simple part of servo motor 0.75kw for used in machines assembly to show specified motor in own project.
Machine
archibase_planet
free
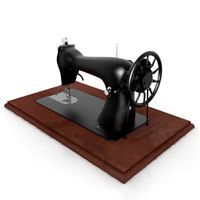
Machine
...machine
archibase planet
sewing-machine sewing machine equipment
singer machine- 3d model for interior 3d visualization.
archibase_planet
free
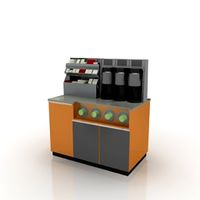
Machine
...hine
archibase planet
percolator equipment coffee-machine
machine n230708 - 3d model (*.gsm+*.3ds) for interior 3d visualization.
archibase_planet
free
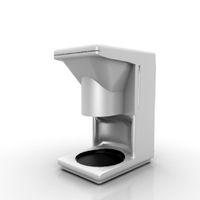
Machine
...chibase planet
percolator coffee-machine kitchen equipment
coffee machine - 3d model (*.gsm+*.3ds) for interior 3d visualization.
archibase_planet
free
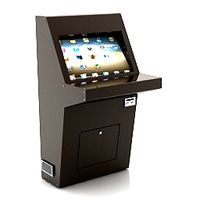
Slot machine
...ase planet
slot machine slot-machine playing machine
slot machine n260311 - 3d model (*.gsm+*.3ds) for interior 3d visualization.
turbosquid
$7

Machine
...ne
turbosquid
royalty free 3d model machine for download as on turbosquid: 3d models for games, architecture, videos. (1391792)
3d_ocean
$10
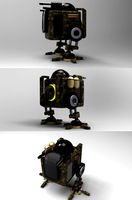
War machine
...war machine
3docean
camuflage machine robot war war machine
war machine created in 3dmax 2009 15.497-poly count
turbosquid
$7
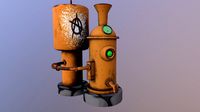
machine
...turbosquid
royalty free 3d model machine for download as obj on turbosquid: 3d models for games, architecture, videos. (1452674)
3d_ocean
$12
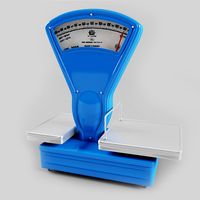
Weighing-machine
...weighing-machine
3docean
market shop weighing-machine
3d model weighing-machine
archibase_planet
free
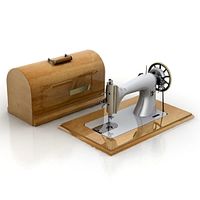
Sewing machine
...ine
archibase planet
sewing machine sewing-machine
sewing machine n080311 - 3d model (*.gsm+*.3ds) for interior 3d visualization.
archibase_planet
free
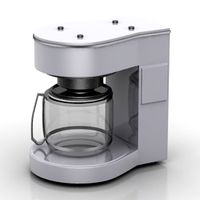
Coffee machine
...se planet
coffee machine percolator coffee-machine
coffee machine n010715 - 3d model (*.gsm+*.3ds) for interior 3d visualization.