Thingiverse
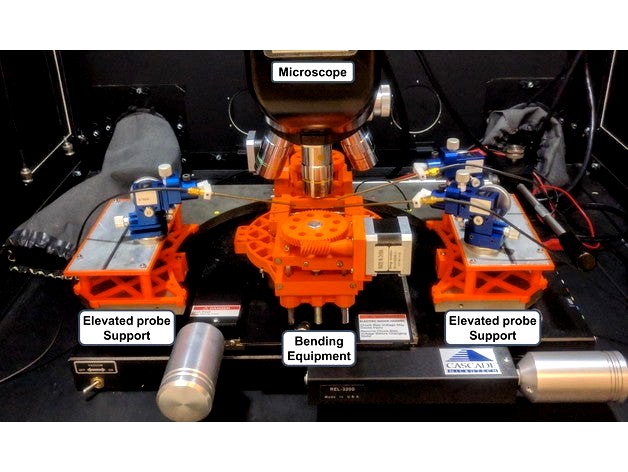
Open Model for External Mechanical Stress of Semiconductors and MEMS for Cascade Microtech REL 3600 probe station by buhler
by Thingiverse
Last crawled date: 3 years ago
This project defines the details of the bending equipment solution and the calibration required for characterization of external mechanical stress in semiconductors and MEMS. The equipment is suited for use in probe station for electrical characterization of devices under controlled external mechanical stress.
References are listed at the bottom.
=============================
The project was developed using the SketchUp 3D modeling software, from Trimble Inc. The bending equipment and the probe support were designed for use in the Cascade Microtech REL 3600 probe station as it was the one available in our laboratory. However, the design files can be easily adapted to other probe stations.
All original design files are made available in the SketchUp “.skp” and the universal “.stl” file format under the CC BY-NC-SA 3.0 license.
It was chosen to ensure that it can continue to be openly developed and distributed to the scientific community. The papers listed in references intends to give the direction in defining the details of the bending equipment and the calibration used for characterization of mechanical stress in semiconductor materials and MEMS.
Having non-encapsulated IC samples in mind, the present bending setup can dose the amount of uniaxial stress induced in the sample. The mechanical bending parts and materials required are described in table 1.
The upper part of the sample will receive a tensile strain and the lower part will receive a compression strain. To change from tensile to compressive, it is necessary the change all the four cylinders’ positions. To the biaxial strain the equipment should apply the tension or compression with two concentric rings.
Table 2 describes the required parts and materials for the elevated probes support.
The bending equipment and the elevated probe supports are projected to fit in the Cascade Microtech REL 3600 probe station, without losing the use of the microscope.
All the main parts were designed and 3D printed with PLA (Polylactic Acid) filament of 1.75mm, reinforced with steel cylinder liner rails to ensure the stability of the equipment.
Two attached step motors are controlled by an Arduino Nano board to control the movement of the bending equipment remotely from outside of the probe station.
All code files for the Arduino and the Android app project will be available soon in a GitHub project. Stay tunned!
=============================
Table 1 - Parts and materials required for the mechanical bending setup:
Quantity - Description
4 pcs -LM8UU steel linear bearing bushing
4 pcs - 90x12mm steel cylinder liner rail (vertical guides)
4 pcs - 10x6mm steel cylinder liner rail
2 pcs - 10mm long 3/8” threaded rod stainless steel
6 pcs - 3/8” stainless steel finished hex nut
2 pcs - 3/8” stainless steel nylon insert lock finished hex nuts
20 pcs - M3x6mm stainless steel zinc-plated phillips pan-head machine screw
4 pcs - M3x20mm stainless steel zinc-plated phillips pan-head machine screw
4 pcs - M3 stainless steel nylon insert lock finished hex nuts
4 pcs - Inside 3/8” outside 1” stainless steel flat washer
372g - PLA (Polylactic Acid) filament of 1.75mm
=============================
Table 2 - Parts and materials required for the elevated probes support:
Quantity - Description
12 pcs - M4 stainless steel finished hex nut
8 pcs - M4x20mm stainless steel zinc-plated phillips pan-head machine screw
4 pcs - M4x10mm stainless steel zinc-plated phillips pan-head machine screw
132g - PLA (Polylactic Acid) filament of 1.75mm
=============================
Table 3 - Parts required for the automation hardware:
Quantity - Description
1 pc - Arduino Nano Developing Board
2 pcs - Step motor SM1.8-A1740CHNBK-CS
1 pc - Bluetooth Module HM-10
2 pcs - Driver DRV8825
2 pcs - Digital Caliper
1 pc - 100 µF 50V Capacitor (C4)
1 pc - 0.33 µF 50V Capacitor (C1)
1 pc - 0.1 µF 50V Capacitor (C3)
1 pc - 0.1 Ω Resistor (R10)
8 pcs - 10 KΩ Resistor (R2 – R9)
1 pc - 1.5 KΩ Resistor (R11)
1 pc - 3.3 KΩ Resistor (R1)
2 pcs - 1 KΩ Resistor (R16; R18)
2 pcs - 2.2 KΩ Resistor (R17; R19)
1 pc - 12V Switched-Mode Power Supply
4 pcs - NPN Transistor 2N3904 (T1 – T4)
=============================
References:
Open Model for External Mechanical Stress of Semiconductors and MEMShttps://doi.org/10.1109/ICMTS.2018.8383795
References are listed at the bottom.
=============================
The project was developed using the SketchUp 3D modeling software, from Trimble Inc. The bending equipment and the probe support were designed for use in the Cascade Microtech REL 3600 probe station as it was the one available in our laboratory. However, the design files can be easily adapted to other probe stations.
All original design files are made available in the SketchUp “.skp” and the universal “.stl” file format under the CC BY-NC-SA 3.0 license.
It was chosen to ensure that it can continue to be openly developed and distributed to the scientific community. The papers listed in references intends to give the direction in defining the details of the bending equipment and the calibration used for characterization of mechanical stress in semiconductor materials and MEMS.
Having non-encapsulated IC samples in mind, the present bending setup can dose the amount of uniaxial stress induced in the sample. The mechanical bending parts and materials required are described in table 1.
The upper part of the sample will receive a tensile strain and the lower part will receive a compression strain. To change from tensile to compressive, it is necessary the change all the four cylinders’ positions. To the biaxial strain the equipment should apply the tension or compression with two concentric rings.
Table 2 describes the required parts and materials for the elevated probes support.
The bending equipment and the elevated probe supports are projected to fit in the Cascade Microtech REL 3600 probe station, without losing the use of the microscope.
All the main parts were designed and 3D printed with PLA (Polylactic Acid) filament of 1.75mm, reinforced with steel cylinder liner rails to ensure the stability of the equipment.
Two attached step motors are controlled by an Arduino Nano board to control the movement of the bending equipment remotely from outside of the probe station.
All code files for the Arduino and the Android app project will be available soon in a GitHub project. Stay tunned!
=============================
Table 1 - Parts and materials required for the mechanical bending setup:
Quantity - Description
4 pcs -LM8UU steel linear bearing bushing
4 pcs - 90x12mm steel cylinder liner rail (vertical guides)
4 pcs - 10x6mm steel cylinder liner rail
2 pcs - 10mm long 3/8” threaded rod stainless steel
6 pcs - 3/8” stainless steel finished hex nut
2 pcs - 3/8” stainless steel nylon insert lock finished hex nuts
20 pcs - M3x6mm stainless steel zinc-plated phillips pan-head machine screw
4 pcs - M3x20mm stainless steel zinc-plated phillips pan-head machine screw
4 pcs - M3 stainless steel nylon insert lock finished hex nuts
4 pcs - Inside 3/8” outside 1” stainless steel flat washer
372g - PLA (Polylactic Acid) filament of 1.75mm
=============================
Table 2 - Parts and materials required for the elevated probes support:
Quantity - Description
12 pcs - M4 stainless steel finished hex nut
8 pcs - M4x20mm stainless steel zinc-plated phillips pan-head machine screw
4 pcs - M4x10mm stainless steel zinc-plated phillips pan-head machine screw
132g - PLA (Polylactic Acid) filament of 1.75mm
=============================
Table 3 - Parts required for the automation hardware:
Quantity - Description
1 pc - Arduino Nano Developing Board
2 pcs - Step motor SM1.8-A1740CHNBK-CS
1 pc - Bluetooth Module HM-10
2 pcs - Driver DRV8825
2 pcs - Digital Caliper
1 pc - 100 µF 50V Capacitor (C4)
1 pc - 0.33 µF 50V Capacitor (C1)
1 pc - 0.1 µF 50V Capacitor (C3)
1 pc - 0.1 Ω Resistor (R10)
8 pcs - 10 KΩ Resistor (R2 – R9)
1 pc - 1.5 KΩ Resistor (R11)
1 pc - 3.3 KΩ Resistor (R1)
2 pcs - 1 KΩ Resistor (R16; R18)
2 pcs - 2.2 KΩ Resistor (R17; R19)
1 pc - 12V Switched-Mode Power Supply
4 pcs - NPN Transistor 2N3904 (T1 – T4)
=============================
References:
Open Model for External Mechanical Stress of Semiconductors and MEMShttps://doi.org/10.1109/ICMTS.2018.8383795
Similar models
grabcad
free

Unified Steel Phillips Rounded Head Screws for Sheet Metal
..., 1 1/2" long - 90935a365
• phillips rounded head screw for sheet metal, black-oxide steel, no. 14, 2" long - 90935a370
grabcad
free

CUBESAT2
...mbly
1. top part (stainless steel)
2 bottom part (stainless steel)
3. face (4 pcs)
4. screw (4 pcs)
can be assemble as 2u and 3u
3dwarehouse
free
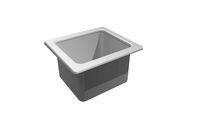
Drop in Pan 1/6 size
...ehouse
stainless steel food pan 1/6 size #16 #coldwell #drop_in #dropin #equipment #food #kitchen #pan #ran2p #restaurant #steel
thingiverse
free
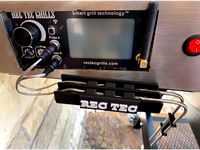
REC TEC Temperature Probes Holder by greylingj77
...r $1.18 https://www.homedepot.com/p/everbilt-10-x-3-4-in-phillips-pan-head-zinc-plated-sheet-metal-screw-10-pack-806481/204275204
3dwarehouse
free
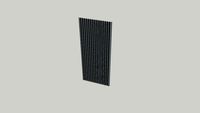
Stainless Steel Folded Zinc
...stainless steel folded zinc
3dwarehouse
stainless steel folded zinc #stainless_steel_folded_zinc
3dwarehouse
free
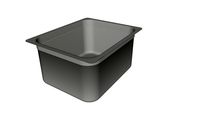
Steam Pan 1/2 size
...e steam pan #steampan #steam #pan #kitchen #cooking #pot #steamtable #chef #stainless #cook #food #service #restaurant #equipment
grabcad
free

1 inch mechanical valve (thread 3-4 NPT) Stainless Steel DIN 304
...ve (thread 3-4 npt) stainless steel din 304
grabcad
1 inch mechanical valve (thread 3-4 npt)
material: stainless steel din 304
cg_trader
free
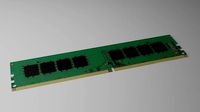
RAM for PC
...storage ram storage computer equipment ram ram storage computer equipment component ram storage computer equipment component main
grabcad
free

Formed Stainless Steel pan
...formed stainless steel pan
grabcad
heavy wall 1 inch formed stainless steel
thingiverse
free
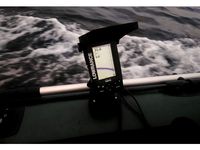
Lowrance echo sounder Elite-4 cover by And69
...lowrance echo sounder elite-4 cover by and69
thingiverse
m4x16 bolt 2 pcs, m4 nut 2 pcs and m3x10 screw 2 pcs. stainless steel.
Buhler
grabcad
free

válvula buhler
...válvula buhler
grabcad
dosificados aspas
grabcad
free

Buhler geared DC motor
...buhler geared dc motor
grabcad
buhler geared motor for mercedes-benz sun shade curtain motor
grabcad
free

1.61.102.002.190 - DC motor-Buhler-6v-35rpm-2turq
...1.61.102.002.190 - dc motor-buhler-6v-35rpm-2turq
grabcad
1.61.102.002.190 - dc motor-buhler-6v-35rpm-2turq
step-jpg
grabcad
free

buhler dc motor type 1.16.011
...buhler dc motor type 1.16.011
grabcad
dc motor 12/24 volt for labeler printer
grabcad
free

HAMMER MILL BUHLER DFZC-1265
...ill buhler dfzc-1265
grabcad
bühler's horizontal hammer mill is for pre-grinding and post-grinding in animal feed production
grabcad
free

Buhler 24v DC motor 147-0070-01
...les seem to be m4. i will characterize the motor performance and make that public once my motor characterization rig is complete.
grabcad
free

Buhler 1.61.046.103.02 with HOA2004-001 Encoder
...motor diameter 31 mm
body length 87 mm
5mm dia. x 10mm flattened steel shaft.
3 metric (m3) threaded mounting holes.
cg_trader
$38
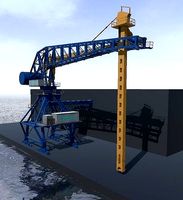
Buhler ship loader 3d low-poly model
...industrial shipping logistic grains terminal transport portalink mechanical conveyor port exterior industrial exterior port crane
grabcad
free

Water In Oil Detector
...this is a water in oil detector made by buhler the model is...
Microtech
turbosquid
$20
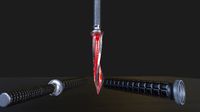
Microtech Jagdkommando Tri-Edge Dagger Low Poly
... tri-edge dagger low poly for download as obj, fbx, and blend on turbosquid: 3d models for games, architecture, videos. (1250289)
thingiverse
free
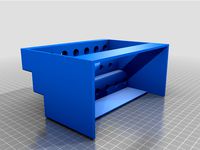
Microtech stand by Smisou
...microtech stand by smisou
thingiverse
thingiverse
free
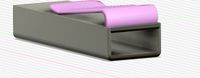
microtech knive case by Remilebel
...microtech knive case by remilebel
thingiverse
knive case
designed for microtech knives
adaptable
thingiverse
free
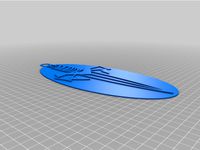
Microtech logos by NarcolepticInsomniac
...e printable microtech logos, in various sizes. each one has a loop on top for hanging. i modeled both the talon and dagger logos.
thingiverse
free
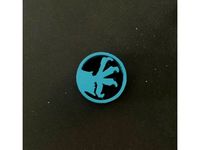
Microtech Claw Bead by Jerryz05
...thingiverse
i saw everyone buying one for $20, just figured i could print it out and stick it on my microtech with some paracord
thingiverse
free
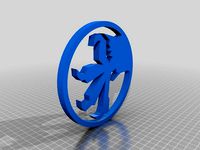
Microtech Eagle Claw by The_LAB
...microtech eagle claw by the_lab
thingiverse
knife maker
thingiverse
free
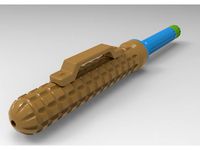
Microtech Jagdkommando remix v2 by dav88
...he blade and handle can be printed in separate pieces and the screwed together with a screw. the rest was already done by nikola.
thingiverse
free
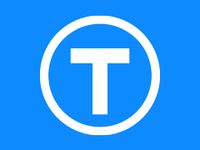
Microtech Triangle Wrench
...se screws are only meant to be finger-tight to begin with, so this is not a screwdriver "bit". this is the entire tool.
thingiverse
free

Microtech screwdriver bit by Xylitol
...o avoid tampering, and due to the difficulty to find the screwdriver bit i did this 3d model.
the hex is 10mm and pins are 1.45mm
thingiverse
free
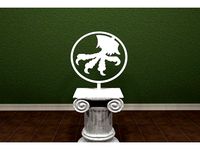
Microtech Knife Logo by AwesomeA
...ost recent expansion to bradford, pa, founder anthony marfione remains committed to keeping"
http://www.microtechknives.com/
Mems
design_connected
$16
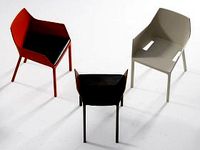
Mem
...mem
designconnected
kristalia mem computer generated 3d model. designed by pillet, christophe.
3ddd
$1
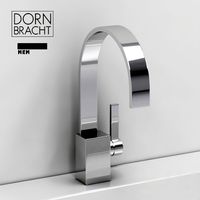
Dorn Bracht MEM
... mem , смеситель
смеситель для умывальника однорычажный
dorn bracht mem
3ddd
$1
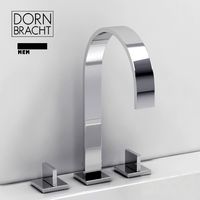
Dorn Bracht MEM
... смеситель
смеситель для умывальника на три отверстия с отдельными розетками
dorn bracht mem
3ddd
$1
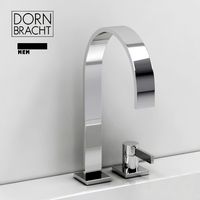
Dorn Bracht MEM
... смеситель
смеситель для умывальника однорычажный на два отверстия с отдельными розетками
dorn bracht mem
turbosquid
$9
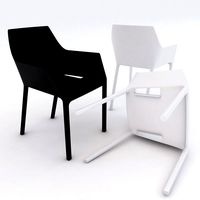
MEM Chair
... available on turbo squid, the world's leading provider of digital 3d models for visualization, films, television, and games.
3ddd
$1
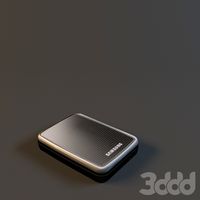
mini mem
...mini mem
3ddd
samsung , жесткий диск
mini hard disk samsung
turbosquid
$15
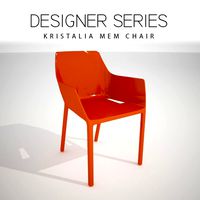
Kristalia Mem Chair
...free 3d model kristalia mem chair for download as 3ds and max on turbosquid: 3d models for games, architecture, videos. (1147273)
turbosquid
$6
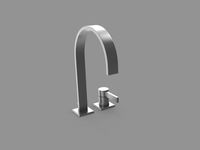
Mem Two Hole Basin
...del mem two hole basin for download as 3ds, max, obj, and fbx on turbosquid: 3d models for games, architecture, videos. (1501763)
3d_export
$15

kristalia mem
...modeled to real-world scale (mm) all materials and objects are properly named scene includes only the model with v-ray materials.
turbosquid
$39

Dornbracht MEM & Antonio Lupi WANDA
...acht mem & antonio lupi wanda for download as max and fbx on turbosquid: 3d models for games, architecture, videos. (1153912)
Semiconductors
3d_export
$5
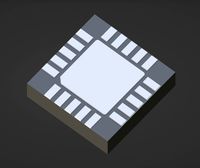
Semiconductor
...semiconductor
3dexport
semiconductor, smd element<br>verts 710<br>faces 1144
3d_export
$10
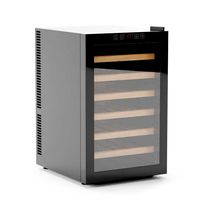
Semiconductor 28 wine cellar BW
...painter available for all software<br>ue4. ue5. blender. maya. 3d max. unity. c4d.<br>formats: .obj .gltf .fbx .blend
3d_export
$5
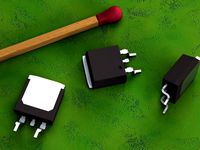
IC SMD Package TO263
...package to263 3dexport is used for different types of semiconductors such as transistor, mosfet, voltage regulators and etcetra. a...
3d_export
$10
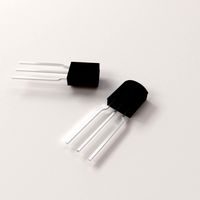
Transistor 3D Model
...ier industrial electric terminal
transistor 3d model download .c4d .max .obj .fbx .ma .lwo .3ds .3dm .stl firdz3d 106717 3dexport
3d_export
$15

Microchip 3D Model
...ammable computer programmer multi
microchip 3d model download .c4d .max .obj .fbx .ma .lwo .3ds .3dm .stl firdz3d 108721 3dexport
3d_export
$10
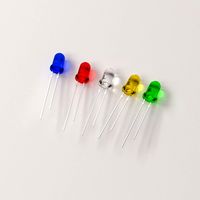
Light Emitting Diode 3D Model
...ode cathode industrial
light emitting diode 3d model download .c4d .max .obj .fbx .ma .lwo .3ds .3dm .stl firdz3d 106605 3dexport
3d_ocean
$2
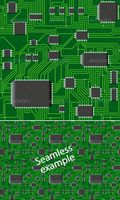
Seamless Chipset
...ern science seamless semiconductor silicon system technology texture tile wallpaper
tileable electronic board chip-set background
3d_ocean
$6
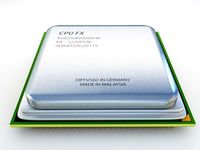
CPU chips
... without the cover and the circuits are visible. each one of chips have 65 092 polygons. the scene is made in 3ds max 2010 wit...
thingiverse
free
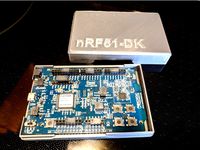
Nordic Semiconductor nRF51-DK case by jperson
... nrf51-dk development board. there are openings in the 3 of the case sides for wire routing to connect externals as well as usb.
thingiverse
free
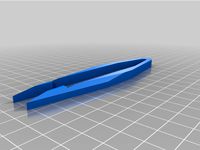
Tweezers for semiconductor wafer by RomZaN
... semiconductor wafer by romzan
thingiverse
just my design of a insta360 go camera mount for the diatone tinawhoop. super simple.
3600
3ddd
$1
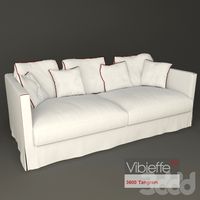
Vibieffe 3600 Tangram bed sofa 197
...vibieffe 3600 tangram bed sofa 197
3ddd
vibieffe
диван спальный раскладной 3600 tangram bed sofa 197 от производителя vibieffe
3d_export
$12
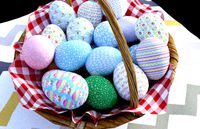
Pack eggs easter with basket
...pack eggs easter with basket 3dexport 27 textures jpg 3600 x 3600 triangles 1.3k quads 15k total triangles 31.3k...
3ddd
$1
![Hippo [Orazio CR_3600]](/t/976499.jpg)
Hippo [Orazio CR_3600]
...orazio cr/3600
cm 34x17xh23http://www.stile-creazioni.com/catalogue.php?id=cr/3600&idcat;=1&next;=⟨=en
3ddd
$1
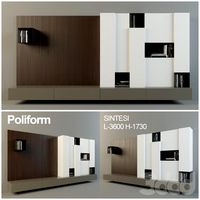
Poliform Sintesi set1
...poliform sintesi set1 3ddd poliform , sintesi poliform sintesi l-3600 ...
3ddd
$1
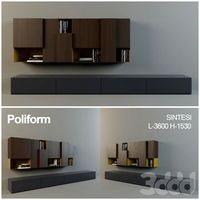
Poliform Sintesi set 3
...sintesi set 3 3ddd poliform , sintesi poliform sintesi l-3600 ...
3ddd
$1
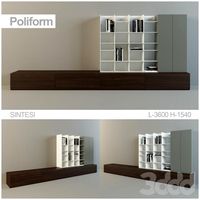
Poliform Sintesi set 5
...sintesi set 5 3ddd poliform , sintesi poliform sintesi l-3600 ...
3ddd
$1
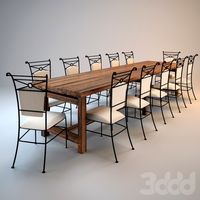
Стол и стул
...и стул 3ddd ковка , обеденный стол из массива 36001000 кресло из...
3ddd
$1

Ковер LivingCarpets Kerschan
...ковер livingcarpets серии kerschan. размер ковра (мм): 2500 х 3600 ...
3ddd
$1

Мебельная стенка
...мебельная стенка 3ddd дятьково мебельная стенка. габариты 3600 х 600 х 2400h. материал дсп 18 мм., крашеное...
3d_ocean
$15
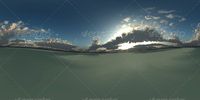
Dusky Sky HDRI
...environment mapping or just a moody background. resolution is 36001800 ...
Cascade
design_connected
$18
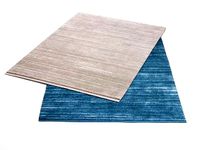
Cascade
...cascade
designconnected
kinnasand cascade computer generated 3d model.
3ddd
$1
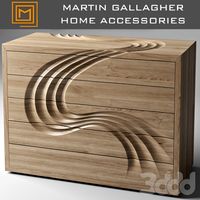
Cascade
... комод
комод cascade, от дизайнера martin gallagher.
размер l 1000mm x h 750mm x w 450mm
в архиве файл для 3dsmax 2011, obj.
3ddd
$1
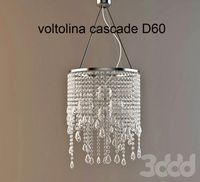
voltolina cascade
...ascade
3ddd
voltolina , cascade
http://www.lumiera.ru/lamps/voltolina/cascade/
turbosquid
$5
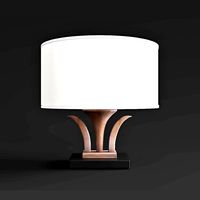
Cascade
...yalty free 3d model cascade for download as max, obj, and fbx on turbosquid: 3d models for games, architecture, videos. (1223675)
turbosquid
$8
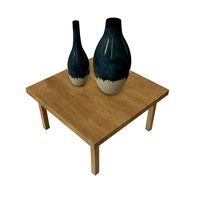
Cascade Vases
...quid
royalty free 3d model cascade vases for download as fbx on turbosquid: 3d models for games, architecture, videos. (1486416)
turbosquid
$30
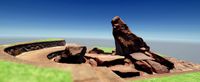
Rock Cascade
...oyalty free 3d model rock cascade for download as fbx and obj on turbosquid: 3d models for games, architecture, videos. (1542220)
3ddd
$1
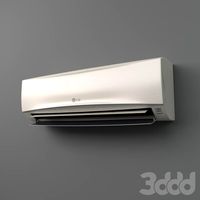
Кондиционер LG CASCADE
...кондиционер lg cascade
3ddd
кондиционер , lg
кондиционер lg cascade s12lhq
3ddd
$1
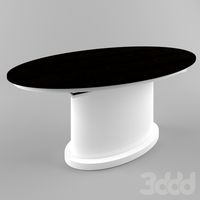
Cascade / Black Pearl
... овальный
турецкая фабрика "cascade", серия "black pearl".http://cascade.com.tr/
turbosquid
$19
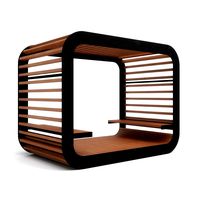
Gazebo Cascade
...ree 3d model gazebo cascade for download as max, fbx, and obj on turbosquid: 3d models for games, architecture, videos. (1624753)
turbosquid
$34
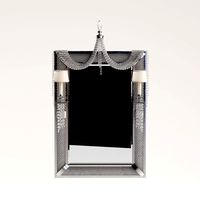
CASCADES MIRROR
... available on turbo squid, the world's leading provider of digital 3d models for visualization, films, television, and games.
Probe
turbosquid
$25
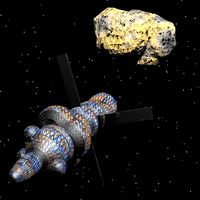
Probe
... available on turbo squid, the world's leading provider of digital 3d models for visualization, films, television, and games.
turbosquid
$12
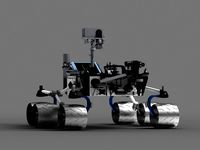
Mars probe space space exploration lunar probe
...be space space exploration lunar probe for download as max on turbosquid: 3d models for games, architecture, videos. (1630876)
turbosquid
$35

Space Probe
...osquid
royalty free 3d model space probe for download as c4d on turbosquid: 3d models for games, architecture, videos. (1571168)
turbosquid
$15
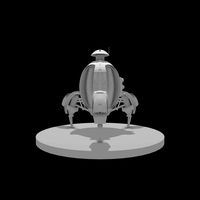
Space Probe
...osquid
royalty free 3d model space probe for download as obj on turbosquid: 3d models for games, architecture, videos. (1314864)
turbosquid
$25
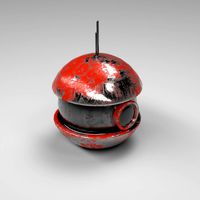
Robot Probe
...y free 3d model robot probe for download as fbx, obj, and dae on turbosquid: 3d models for games, architecture, videos. (1537490)
turbosquid
$1
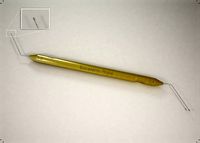
Dental Probe
...e 3d model dental probe for download as ma, obj, fbx, and stl on turbosquid: 3d models for games, architecture, videos. (1312400)
turbosquid
$60
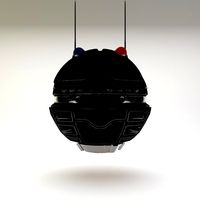
Police Probe
... available on turbo squid, the world's leading provider of digital 3d models for visualization, films, television, and games.
turbosquid
$10
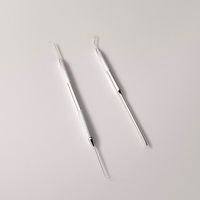
Dental Probe
... available on turbo squid, the world's leading provider of digital 3d models for visualization, films, television, and games.
turbosquid
$9
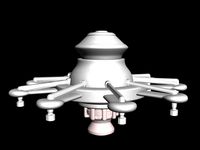
Space probe
... available on turbo squid, the world's leading provider of digital 3d models for visualization, films, television, and games.
turbosquid
free
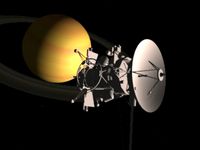
Cassini Probe
... available on turbo squid, the world's leading provider of digital 3d models for visualization, films, television, and games.
Stress
3d_export
$5

Anti stress kit
...anti stress kit
3dexport
anti stress kit wall sign
turbosquid
$1
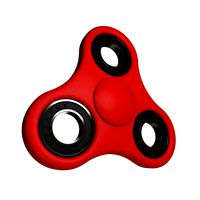
Fidget Spinner Hand Spinner Stress Toy
...el fidget spinner hand spinner stress toy for download as c4d on turbosquid: 3d models for games, architecture, videos. (1162699)
turbosquid
$1
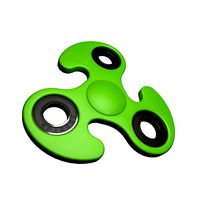
Fidget Spinner Hand Spinner Stress Toy
...el fidget spinner hand spinner stress toy for download as c4d on turbosquid: 3d models for games, architecture, videos. (1162705)
3d_export
$12
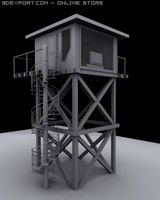
Tower 3D Model
...tower 3d model 3dexport tower hide stress problem window stairs tower 3d model zzzsotti 2460...
3d_export
$60
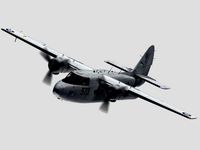
hunting percival prince
...it was a twin-engine, high-wing, cantilever monoplane of all-metal stressd-skin construction; the undercarriage was of retractable, tricycle type. the...
3d_export
$25
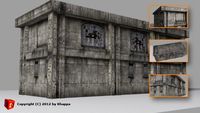
Damaged Building 3D Model
...damaged building 3d model 3dexport building ruins postatomic aged stressd future halo city concrete skyscrape window war sci -fi...
3ddd
$1
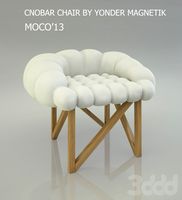
MOCO'13
...chair is all about coziness, relaxation and relieving the stress ...
3d_ocean
$4
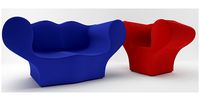
Moroso Double Soft Big Easy
...moroso is a sofa with frame in steel and stressresistant polyurethane foam upholstered with polyester fibre. it can be...
3ddd
$1
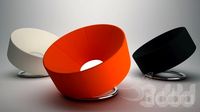
Ferlea / Pop
...designed by enzo berti 2003 wooden frame padded with stress resistant high density polyurethane foam. base in chromate...
3d_export
free
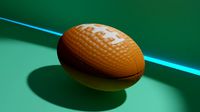
foam football ball
...ball 3dexport a foam football that i use to de-stress myself and as a toy for my dog.<br>i did...
Rel
3ddd
free

04 Remont Rels
...04 remont rels
3ddd
рельсы , ремонт
обновил в архиве obj - теперь ок.
turbosquid
$20
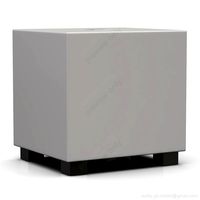
REL Tzero Gloss White Lacquer
...l tzero gloss white lacquer for download as 3ds, max, and obj on turbosquid: 3d models for games, architecture, videos. (1145679)
turbosquid
$20
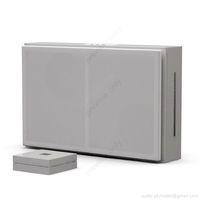
REL Habitat1 Gloss White Lacquer
...abitat1 gloss white lacquer for download as 3ds, max, and obj on turbosquid: 3d models for games, architecture, videos. (1145677)
turbosquid
$20
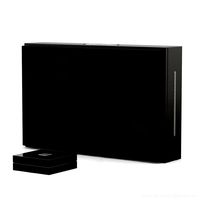
REL Habitat1 Gloss Piano Black
... habitat1 gloss piano black for download as 3ds, max, and obj on turbosquid: 3d models for games, architecture, videos. (1145676)
turbosquid
$60
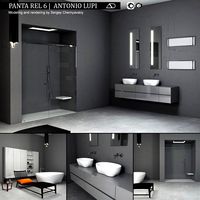
Bathroom furniture set Panta Rel 6
...m furniture set panta rel 6 for download as max, obj, and fbx on turbosquid: 3d models for games, architecture, videos. (1192539)
turbosquid
$60
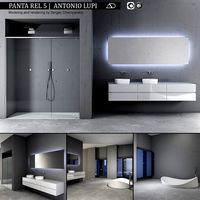
Bathroom furniture set Panta Rel 5
...m furniture set panta rel 5 for download as max, obj, and fbx on turbosquid: 3d models for games, architecture, videos. (1190928)
turbosquid
$60

Bathroom furniture set Panta Rel 3
...m furniture set panta rel 3 for download as max, obj, and fbx on turbosquid: 3d models for games, architecture, videos. (1171360)
turbosquid
$60
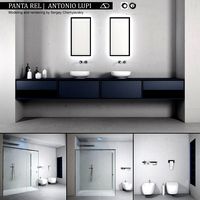
Bathroom furniture set Panta Rel 2
...m furniture set panta rel 2 for download as max, obj, and fbx on turbosquid: 3d models for games, architecture, videos. (1167055)
3d_export
$5
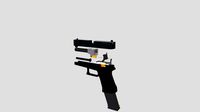
Glock
...glock 3dexport a reltively common...
3ddd
free
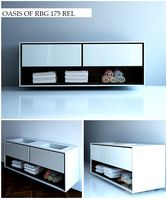
OASIS
...oasis 3ddd oasis oasis of rbg 175 rel ...
External
3ddd
free
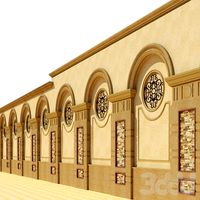
External wall
...external wall
3ddd
забор
external wall of the villa in a classic style
3d_export
$7
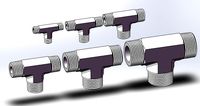
mt external tee
...mt external tee
3dexport
mt external tee
turbosquid
$8
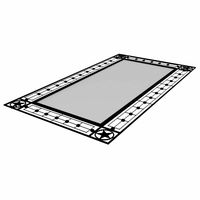
External mirror
...id
royalty free 3d model external mirror for download as fbx on turbosquid: 3d models for games, architecture, videos. (1638607)
turbosquid
$1
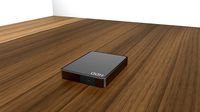
External HDD
...squid
royalty free 3d model external hdd for download as c4d on turbosquid: 3d models for games, architecture, videos. (1250314)
turbosquid
$10
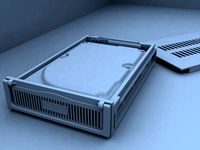
Extern HDD
... available on turbo squid, the world's leading provider of digital 3d models for visualization, films, television, and games.
3d_ocean
$10
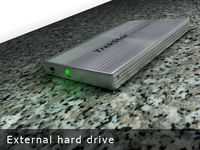
External hard drive
... is a detailed model of a trekstor external hard drive. you can easily modify the label on the top. simply edit the text objects.
turbosquid
$4
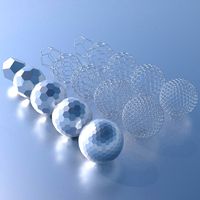
External Hard Drive
...royalty free 3d model external hard drive for download as fbx on turbosquid: 3d models for games, architecture, videos. (1298038)
cg_studio
$10
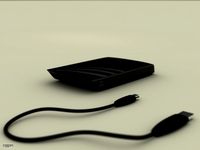
External HDD3d model
...odel
cgstudio
.3dm .3ds .c4d .max .obj - external hdd 3d model, royalty free license available, instant download after purchase.
turbosquid
$5
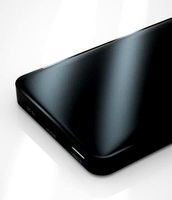
External Hard Drive
...free 3d model external hard drive for download as c4d and fbx on turbosquid: 3d models for games, architecture, videos. (1520823)
turbosquid
$2
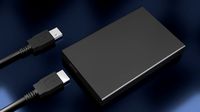
External hard disk
... free 3d model external hard disk for download as 3ds and obj on turbosquid: 3d models for games, architecture, videos. (1251009)
Station
3d_export
$5
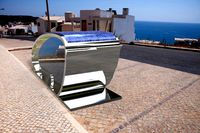
station
...station
3dexport
station
archibase_planet
free
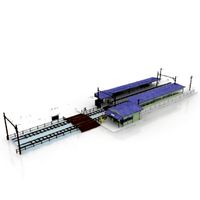
Station
...station
archibase planet
railroad station railway station bay
railway station n160707 - 3d model for interior 3d visualization.
archibase_planet
free
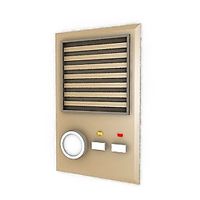
Station
...station
archibase planet
intercom station equipment
intercom station - 3d model for interior 3d visualization.
archibase_planet
free

Station
...station
archibase planet
station
station n260108 - 3d model (*.gsm+*.3ds) for interior 3d visualization.
3d_export
$5
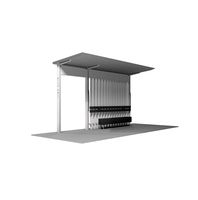
Station
...station
3dexport
low poly bus station
archibase_planet
free
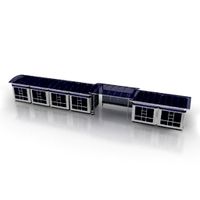
Station
...station
archibase planet
building station construction
station n170708 - 3d model(*.gsm+*.3ds) for interior 3d visualization.
archibase_planet
free

Station
...station
archibase planet
bus station bus stop
station 1 - 3d model (*.gsm+*.3ds) for interior 3d visualization.
archibase_planet
free
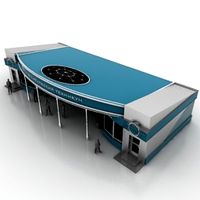
Station
...station
archibase planet
bus station bus stop
station 2 - 3d model (*.gsm+*.3ds) for interior 3d visualization.
archibase_planet
free
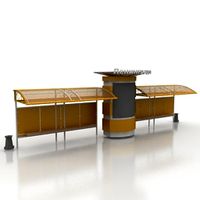
Station
...station
archibase planet
bus station bus stop
station 3 - 3d model (*.gsm+*.3ds) for interior 3d visualization.
3d_ocean
$19
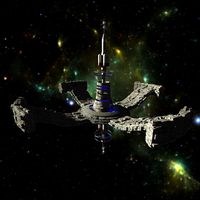
Space station
...space station
3docean
space station
space station
Mechanical
3d_export
$50
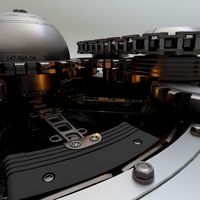
Mechanism
...mechanism
3dexport
mechanism -------- animation is present only in the blender file.
3d_export
$5
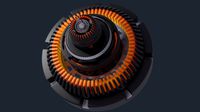
mechanics
...mechanics
3dexport
turbosquid
$50
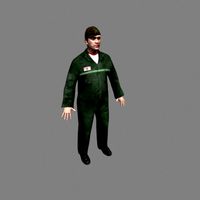
mechanic
... available on turbo squid, the world's leading provider of digital 3d models for visualization, films, television, and games.
3ddd
$1
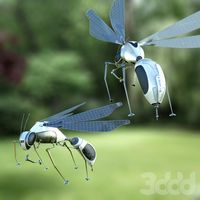
Mechanical Wasp
...mechanical wasp
3ddd
робот
mechanical wasp
3d_export
$20
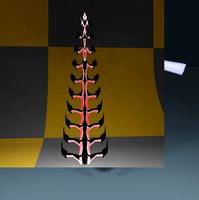
Mechanical tail
...mechanical tail
3dexport
mechanical tail<br>four-part movement
3d_export
$5
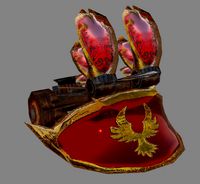
mechanical ballista
...mechanical ballista
3dexport
a mechanical ballista useful for medieval or fantasy games does not contain animations
turbosquid
$59
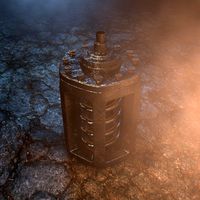
Mechanical Part
...id
royalty free 3d model mechanical part for download as c4d on turbosquid: 3d models for games, architecture, videos. (1410833)
turbosquid
$50
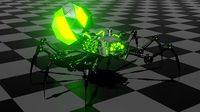
Mechanical Spider
...royalty free 3d model mechanical spider for download as blend on turbosquid: 3d models for games, architecture, videos. (1599864)
turbosquid
$45

Mechanical Pencil
...royalty free 3d model mechanical pencil for download as blend on turbosquid: 3d models for games, architecture, videos. (1503379)
turbosquid
$35
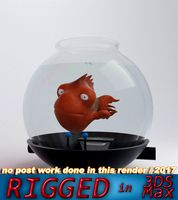
Mechanical fish
...id
royalty free 3d model mechanical fish for download as max on turbosquid: 3d models for games, architecture, videos. (1152530)
Open
3d_export
free
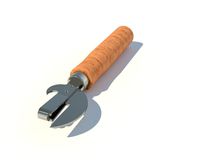
Opener
...r
3dexport
3d model of can opener. its my first work, if u can please show me my mistakes. this 3d model was created in autocad.
3d_export
free
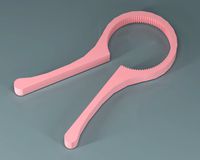
Cap opener
...cap opener
3dexport
handy cap opener, more files/formats here:
3ddd
$1
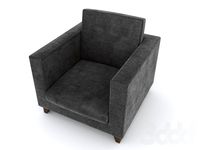
Кресло, Open Oreon.
...кресло, open oreon.
3ddd
open , oreon
кресло, open oreon.
3d_ocean
$4
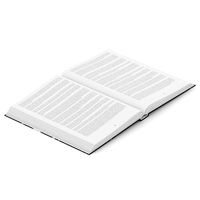
Open Book
...r interior max mental model open ray reading shelf text vray
open hardcover book with unique texture map on front and back cover.
turbosquid
$6
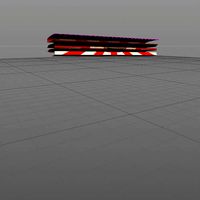
Opening Flag
...squid
royalty free 3d model opening flag for download as c4d on turbosquid: 3d models for games, architecture, videos. (1593555)
turbosquid
$10
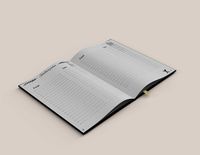
Open book
...
royalty free 3d model open book for download as skp and obj on turbosquid: 3d models for games, architecture, videos. (1690781)
turbosquid
$2
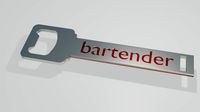
bottle opener
...lty free 3d model bottle opener for download as blend and obj on turbosquid: 3d models for games, architecture, videos. (1621201)
turbosquid
$24
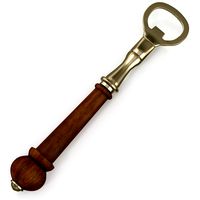
Bottle Opener
...free 3d model bottle opener for download as max, obj, and fbx on turbosquid: 3d models for games, architecture, videos. (1300948)
turbosquid
$20
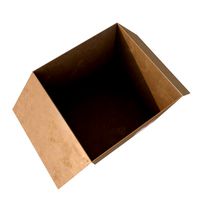
Open Box
...yalty free 3d model open box for download as ma, obj, and fbx on turbosquid: 3d models for games, architecture, videos. (1481218)
turbosquid
$10

Wine Opener
...ty free 3d model wine opener for download as ma, obj, and fbx on turbosquid: 3d models for games, architecture, videos. (1240730)