GrabCAD

nTopology Masking Plugs for Drill Press Casting
by GrabCAD
Last crawled date: 1 year, 12 months ago
A. Company Name and Industry:
I work at ATI metals, where we 3D print parts for aerospace applications.
B. Job Title and Responsibilities:
My name is Austin Brittain, and I am a process engineer at a metal additive manufacturing facility in Connecticut. I help find ways to make the metal 3D printers run more reliably and produce high quality parts for our customers.
C. Application Information:
When I first saw the nTopology fixture generator, its utility was immediately clear to me. From time to time at work we find it necessary to bead blast or grit blast a surface on a part after it has returned from machining. Usually we mask off the machined surfaces with tape and very carefully blast the surfaces that need retouching. The tape application process is very time consuming though, and it would be nice to have reusable plugs that could be moved from part to part quickly.
I cannot post pictures of customer parts on the internet though, so at first I was stumped on what to enter into the competition. As I thought about it, my mind drifted to one of my many side projects. I am restoring an old drill press that I bought at a junk shop, and its castings are covered in rust and grime. The makerspace I belong to just got a blasting cabinet, which would quickly remove the rust, but I was worried about damaging the delicate machined surfaces on the inside of the part. The Statasys nTopology fixture generator was the perfect solution! In an afternoon, I was able to design a part that was representative of the casting, make plugs for all the holes, and quickly export them. Now I can print these plugs and get to blasting.
D. Project Challenges and Goals:
My goal for this project was to finish my first nTopology project. I saw a demo at work a few months ago, and I have wanted to try the software ever since. I had no trouble making plugs for the holes in the castings, but I was not able to get the surface enclosure tool to work. I substituted the surface masking tool with an overhang, and I think that will work for me. Making a whole model of the casting just to make hole plugs was definitely overkill, but It gave me design practice. If this were a work project, we would already have the model from the customer, so the modeling work would be almost eliminated. I look forward to using the remaining days on my trial to further explore this powerful software.
E. Alternate Manufacturing Technology:
All of these plugs could be produced on a lathe if necessary.
F. Additive Advantages:
Setting up a lathe for a run of custom plugs would be a less efficient use of resources than letting a small 3D printer run overnight. 3D Printing would allow the plugs to be made with elastomeric materials which would otherwise be difficult to machine.
G. N/A
H. Use of nTopology
nTopology provided a very streamlined workflow to get from model to fixture. If I had already had a model of the part, I could have had masking plugs designed in minutes. This would be a huge timesaver if I had a situation that required a lot of surfaces to be protected from blasting.
I. Company Printers:
We have several Laser Powder Bed Fusion and Electron Powder Bed Fusion machines at work. We also have access to a Stratasys FDM 3D Printer at one of our other locations. We also have a cantankerous xerox color laser printer. At the makerspace where I will be working on my drill press project, there are a number of Prusa printers.
J. Future Printers:
I do not think I am in a position to discuss this. I think it would be awesome if we got more though.
4. Material:
I will be printing these parts out of PLA on my personal 3D printer, because that is the material that is available to me. The layer thickness will be .1825 mm (calculated from my leadscrew) and I will uses a standard .4mm tip. Ideally I would print these parts on a Stratasys Fortus series machine, in black TPU 92 A. The elastomer would conform to the rough surfaces of the casting, and It would have the abrasion resistance to survive the blasting cabinet.
5. Impact Statement:
This drill press may be a box of parts right now, but those parts go together into a beautiful, antique too. Since the drill press is so old, if I make a mess of a critical surface I cannot go get another. I have one shot at this, and the masks I created using nTopology will help me get this right the first time. A cutting edge tool from this century will make it possible to restore a cutting edge tool from the last. I think that is pretty cool.
I work at ATI metals, where we 3D print parts for aerospace applications.
B. Job Title and Responsibilities:
My name is Austin Brittain, and I am a process engineer at a metal additive manufacturing facility in Connecticut. I help find ways to make the metal 3D printers run more reliably and produce high quality parts for our customers.
C. Application Information:
When I first saw the nTopology fixture generator, its utility was immediately clear to me. From time to time at work we find it necessary to bead blast or grit blast a surface on a part after it has returned from machining. Usually we mask off the machined surfaces with tape and very carefully blast the surfaces that need retouching. The tape application process is very time consuming though, and it would be nice to have reusable plugs that could be moved from part to part quickly.
I cannot post pictures of customer parts on the internet though, so at first I was stumped on what to enter into the competition. As I thought about it, my mind drifted to one of my many side projects. I am restoring an old drill press that I bought at a junk shop, and its castings are covered in rust and grime. The makerspace I belong to just got a blasting cabinet, which would quickly remove the rust, but I was worried about damaging the delicate machined surfaces on the inside of the part. The Statasys nTopology fixture generator was the perfect solution! In an afternoon, I was able to design a part that was representative of the casting, make plugs for all the holes, and quickly export them. Now I can print these plugs and get to blasting.
D. Project Challenges and Goals:
My goal for this project was to finish my first nTopology project. I saw a demo at work a few months ago, and I have wanted to try the software ever since. I had no trouble making plugs for the holes in the castings, but I was not able to get the surface enclosure tool to work. I substituted the surface masking tool with an overhang, and I think that will work for me. Making a whole model of the casting just to make hole plugs was definitely overkill, but It gave me design practice. If this were a work project, we would already have the model from the customer, so the modeling work would be almost eliminated. I look forward to using the remaining days on my trial to further explore this powerful software.
E. Alternate Manufacturing Technology:
All of these plugs could be produced on a lathe if necessary.
F. Additive Advantages:
Setting up a lathe for a run of custom plugs would be a less efficient use of resources than letting a small 3D printer run overnight. 3D Printing would allow the plugs to be made with elastomeric materials which would otherwise be difficult to machine.
G. N/A
H. Use of nTopology
nTopology provided a very streamlined workflow to get from model to fixture. If I had already had a model of the part, I could have had masking plugs designed in minutes. This would be a huge timesaver if I had a situation that required a lot of surfaces to be protected from blasting.
I. Company Printers:
We have several Laser Powder Bed Fusion and Electron Powder Bed Fusion machines at work. We also have access to a Stratasys FDM 3D Printer at one of our other locations. We also have a cantankerous xerox color laser printer. At the makerspace where I will be working on my drill press project, there are a number of Prusa printers.
J. Future Printers:
I do not think I am in a position to discuss this. I think it would be awesome if we got more though.
4. Material:
I will be printing these parts out of PLA on my personal 3D printer, because that is the material that is available to me. The layer thickness will be .1825 mm (calculated from my leadscrew) and I will uses a standard .4mm tip. Ideally I would print these parts on a Stratasys Fortus series machine, in black TPU 92 A. The elastomer would conform to the rough surfaces of the casting, and It would have the abrasion resistance to survive the blasting cabinet.
5. Impact Statement:
This drill press may be a box of parts right now, but those parts go together into a beautiful, antique too. Since the drill press is so old, if I make a mess of a critical surface I cannot go get another. I have one shot at this, and the masks I created using nTopology will help me get this right the first time. A cutting edge tool from this century will make it possible to restore a cutting edge tool from the last. I think that is pretty cool.
Similar models
grabcad
free

Hand cranked cast iron drill press
... had to do some assumptions of some of the inner dimensions and working, while i wasn't allowed to dissamble the drill press.
grabcad
free

Grains Autofill machine (Automatic Packing)
...the 3d models.
-it was a challenge for me to design the mechanisms and using surfacing tools and sheet metal forming tools in sw.
grabcad
free

Customizable Tool for Handling and Orientienting Magnets
...amond shape tube for rapid horizontal printing with no support structures to produce smooth surfaces for the magnets to slide on.
grabcad
free

Flexi Press Tool Racking
...sign custom to fit the space in the work area.
my 3d printing crowdfunder:
https://www.crowdfunder.co.uk/3d-printer-for-engineer
cg_trader
$12
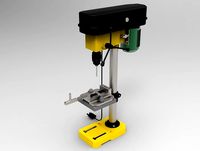
Drill Press
... power technology drill bit press electricity puley belt chuck radial part hardware work lathe turn industrial industrial machine
grabcad
free

Turbo Nut
...rabcad
work in progress; a depth stop for mills and drill presses that can be positioned quickly with a blast of compressed air.
grabcad
free

Vslot Gear Track
... this on my machine when i need to get a straight cut or drill press a hole in projects since i only have a 3d printer. snug fit.
thingiverse
free
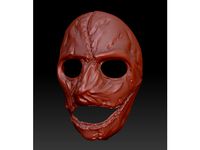
Slipknot Corey Taylor Vol 3 Mask by ChrisThePropGuy
...ommercial file as per usual but if you would like to make a mould of this to sell it shoot me a pm and we can work something out.
grabcad
free

undercut drill
...undercut drill
grabcad
undercut tool we had made for a part at work.
thingiverse
free
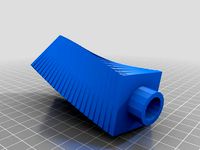
Surface roughness test part by loicEconolyst
... by loiceconolyst
thingiverse
this part was made for a project where we had to make roughness measurement for different machines
Ntopology
thingiverse
free
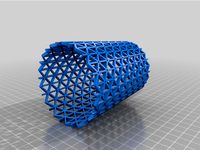
Isogrid Lattice Pipe (nTopology) by nTopology
...m in different parts to save time
don't have a license of ntop platform yet? get a trial here: https://ntopolo.gy/thingiverse
thingiverse
free
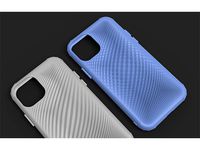
Textured Phone Cases nTopology by nTopology
...n and mix functions to create unprecedented designs
don't have ntop platform yet? try it here: https://ntopolo.gy/thingiverse
thingiverse
free
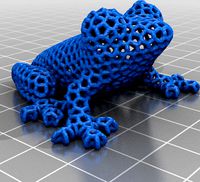
Voronoi Frog Ornament by Finerze77
...thingiverse a voronoi sculpture of a frog made using ntopology best printed at a 45 degree angle with touching-bed...
thingiverse
free

Mesoextructuring by pedrolcs8
...thingiverse lattice connection rod design in solidworks and element ntopology designer is marlon cunico fabrication and implementation has been...
thingiverse
free
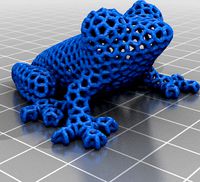
Voronoi Frog Ornament by Finerze77
...a voronoi scuplture of a tree frog made in ntopology i made for my desk, best printed at a...
thingiverse
free
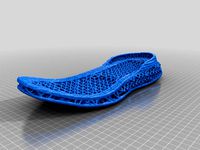
Futurecraft 4D alike Lattice Design by LeeOh
...to improve the design let me know. tools used: ntopology element shoe size: 45...
thingiverse
free
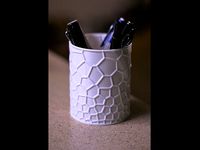
Voronoi Cup - Vase Mode Capable
...mode capable thingiverse i designed this using the amazing ntopology platform software. it can be printed in vase mode...
thingiverse
free
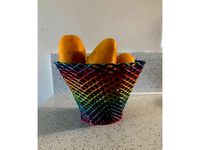
Mesh Bowl by kzeller94
...mesh bowl! created the solid in solidworks, then used ntopology to create a diamond lattice with a ramped thickness,...
thingiverse
free
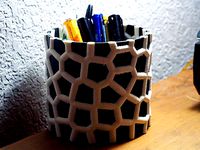
Multi-Material Voronoi Cup
...voronoi cup thingiverse i designed this voronoi cup using ntopology platform to be printed using two different colors with...
thingiverse
free
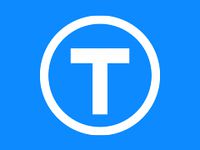
Sierpinski Pyramid Skeleton - 5th Order by TurboDork
...sierpinski design. this design was created using the incredible ntopology platform which can do some crazy crazy powerful stuff...
Casting
3ddd
free
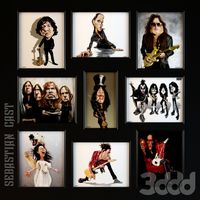
Sebastian Cast
...sebastian cast
3ddd
sebastian cast
карикатуры от себастьяна каста
3ddd
$1
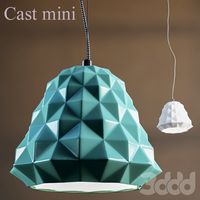
Cast mini
...cast mini
3ddd
present time
подвесной светильник cast mini
материал: керамика
размер: 20x166
производитель: present time
turbosquid
$19
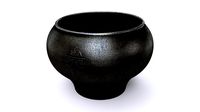
Cast Iron
...rbosquid
royalty free 3d model cast iron for download as max on turbosquid: 3d models for games, architecture, videos. (1609108)
3d_export
$6
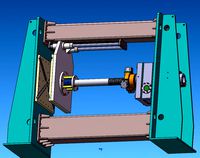
Design of die casting machine
...design of die casting machine
3dexport
design of die casting machine
3ddd
$1

Wood Casting by Hilla Shamia
...wood casting by hilla shamia
3ddd
wood casting by hilla shamia
turbosquid
$30
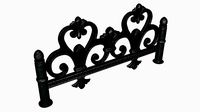
Cast iron fenceClassic
...alty free 3d model cast iron fenceclassic for download as max on turbosquid: 3d models for games, architecture, videos. (1630755)
turbosquid
$15
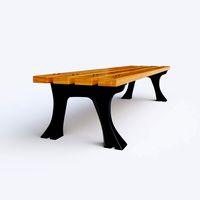
Cast-iron bench
...id
royalty free 3d model cast-iron bench for download as max on turbosquid: 3d models for games, architecture, videos. (1239991)
turbosquid
$15

Cast-iron bench
...id
royalty free 3d model cast-iron bench for download as max on turbosquid: 3d models for games, architecture, videos. (1239993)
turbosquid
$13
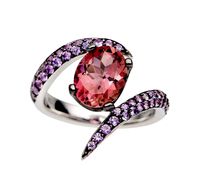
Ring with 2 casts
...
royalty free 3d model ring with 2 casts for download as 3dm on turbosquid: 3d models for games, architecture, videos. (1375610)
turbosquid
free
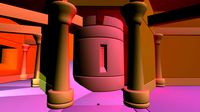
Caste Room with pillars
... 3d model caste room with pillars for download as xsi and fbx on turbosquid: 3d models for games, architecture, videos. (1305991)
Masking
turbosquid
$1
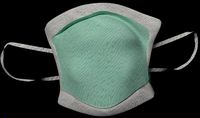
Dust Mask Medical Mask Face Mask Surgical Mask
...k face mask surgical mask for download as blend, fbx, and obj on turbosquid: 3d models for games, architecture, videos. (1533329)
3d_export
$5
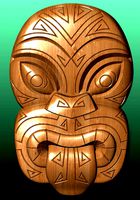
Mask
...mask
3dexport
african mask
turbosquid
$2
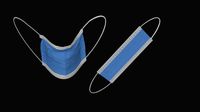
Riggged Surgical mask face mask dust mask medical mask
...sk dust mask medical mask for download as blend, fbx, and obj on turbosquid: 3d models for games, architecture, videos. (1536257)
archibase_planet
free
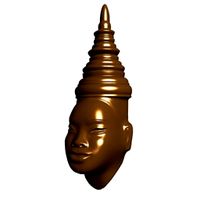
Mask
...mask
archibase planet
mask sculpture decor
mask - 3d model for interior 3d visualization.
3d_export
$19
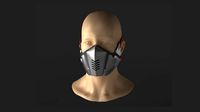
masks tech metal masks wearable futuristic masks
... tech metal masks wearable futuristic masks
3dexport
masks, tech metal masks, wearable, futuristic masks zip contain fbx obj max
archibase_planet
free
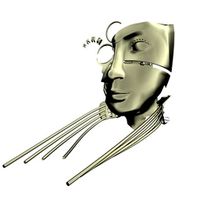
Mask
...mask
archibase planet
mask sculpture decor
mask-decor - 3d model for interior 3d visualization.
archibase_planet
free

Mask
...mask
archibase planet
mask
swimming mask - 3d model (*.gsm+*.3ds) for interior 3d visualization.
archibase_planet
free
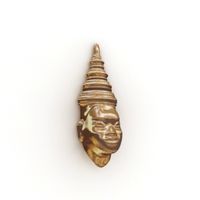
Mask
...mask
archibase planet
picturesque element mask
mask n050608 - 3d model (*.gsm+*.3ds) for interior 3d visualization.
archibase_planet
free
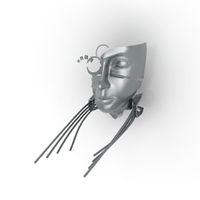
Mask
...mask
archibase planet
mask picturesque element
mask n230708 - 3d model (*.gsm+*.3ds) for interior 3d visualization.
archibase_planet
free
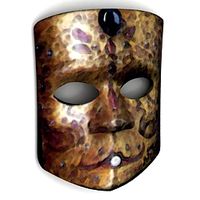
Mask
...mask
archibase planet
mask ornament decoration
mask decor n240211 - 3d model (*.gsm+*.3ds) for interior 3d visualization.
Press
archibase_planet
free
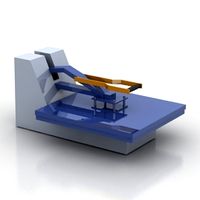
Press
...ibase planet
press squeezer masher
press garment heat press n131213 - 3d model (*.gsm+*.3ds+*.max) for interior 3d visualization.
archibase_planet
free
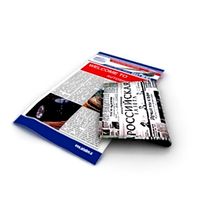
Press
...press
archibase planet
newspaper daily paper magazine
press - 3d model for interior 3d visualization.
archibase_planet
free
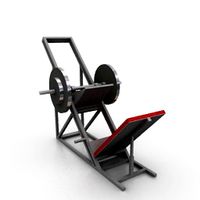
Press
...press
archibase planet
gymnastic apparatus gym
gym leg press - 3d model (*.gsm+*.3ds) for interior 3d visualization.
archibase_planet
free

Press bench
...press bench
archibase planet
bench press press bench gym
press bench - 3d model (*.gsm+*.3ds) for exterior 3d visualization.
3d_export
$20
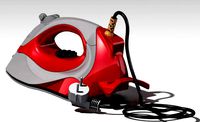
iron press
...iron press
3dexport
iron press
3d_export
$15
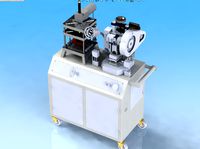
punch press
...punch press
3dexport
punch press
3d_export
$10
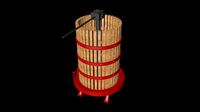
Grape press
...grape press
3dexport
grape press
3d_ocean
$9
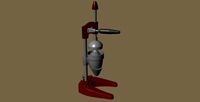
Fruit Press
...fruit press
3docean
food and drinks fruit press furnishing
fruit press,food and drinks, furnishing
turbosquid
$20
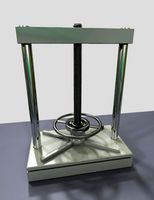
Press
... available on turbo squid, the world's leading provider of digital 3d models for visualization, films, television, and games.
turbosquid
$10
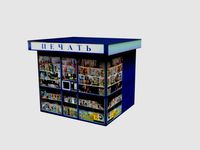
Press
... available on turbo squid, the world's leading provider of digital 3d models for visualization, films, television, and games.
Drill
archibase_planet
free
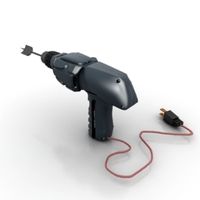
Drill
...drill
archibase planet
drill electric drill power drill
drill n091107 - 3d model (*.gsm+*.3ds) for interior 3d visualization.
archibase_planet
free
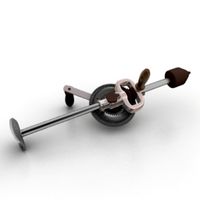
Drill
...drill
archibase planet
drill hand drill
drill 1 - 3d model (*.gsm+*.3ds) for interior 3d visualization.
archibase_planet
free
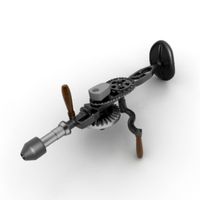
Drill
...drill
archibase planet
drill hand drill
drill 2 - 3d model (*.gsm+*.3ds) for interior 3d visualization.
archibase_planet
free
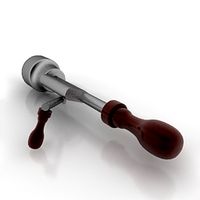
Drill
...drill
archibase planet
drill hand drill
drill 3- 3d model (*.gsm+*.3ds) for interior 3d visualization.
archibase_planet
free
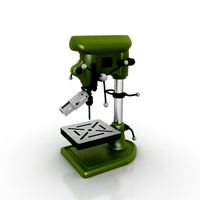
Drill
...drill
archibase planet
boring rig rig drill
drill n070807 - 3d model for interior 3d visualization.
archibase_planet
free
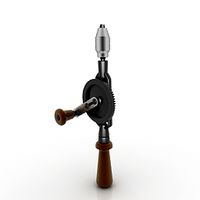
Drill
...drill
archibase planet
hand drill toolware
drill 2 - 3d model (*.gsm+*.3ds) for interior 3d visualization.
archibase_planet
free
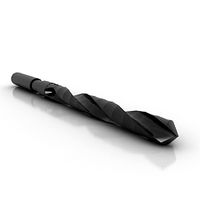
Drill
...drill
archibase planet
perforator drill auger
drill 3 - 3d model (*.gsm+*.3ds) for interior 3d visualization.
turbosquid
$25
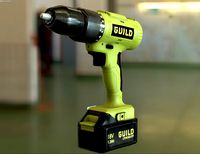
Drill
...ll
turbosquid
royalty free 3d model drill for download as ma on turbosquid: 3d models for games, architecture, videos. (1203923)
turbosquid
free
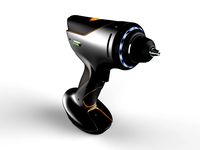
Drill
...l
turbosquid
free 3d model drill for download as fbx and obj on turbosquid: 3d models for games, architecture, videos. (1628646)
archibase_planet
free
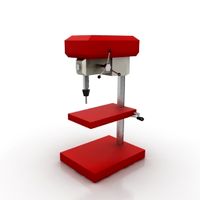
Drill
...drill
archibase planet
boring mill perforator driller
drill pro 1 - 3d model (*.gsm+*.3ds) for interior 3d visualization.
Plugs
3d_export
$5
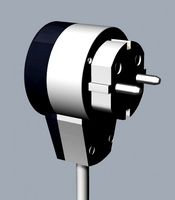
plug
...plug
3dexport
3d_export
$5

plug cover
...plug cover
3dexport
plug cover
3d_export
$5
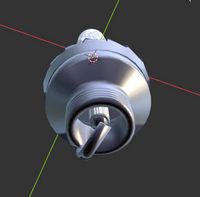
spark plug
...spark plug
3dexport
spark plug
3d_export
free
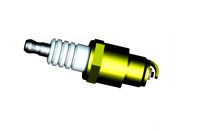
spark plug
...spark plug
3dexport
spark plug
turbosquid
$30
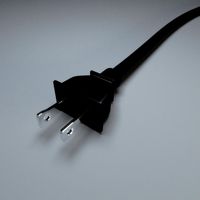
plug
... available on turbo squid, the world's leading provider of digital 3d models for visualization, films, television, and games.
turbosquid
$15
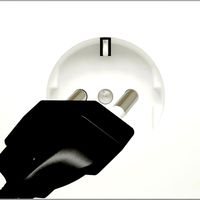
plug
... available on turbo squid, the world's leading provider of digital 3d models for visualization, films, television, and games.
turbosquid
$10
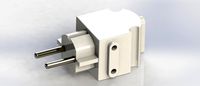
Plug
... available on turbo squid, the world's leading provider of digital 3d models for visualization, films, television, and games.
turbosquid
$10
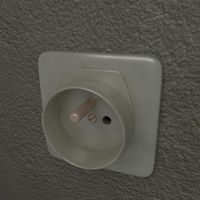
Plug
... available on turbo squid, the world's leading provider of digital 3d models for visualization, films, television, and games.
turbosquid
$1
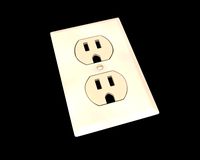
Plug
... available on turbo squid, the world's leading provider of digital 3d models for visualization, films, television, and games.
turbosquid
free
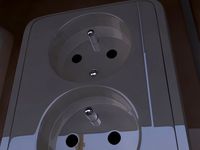
plug
... available on turbo squid, the world's leading provider of digital 3d models for visualization, films, television, and games.