Thingiverse
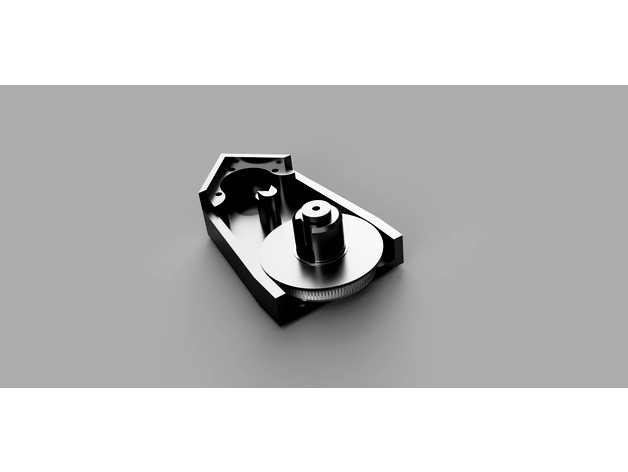
Nema 17 belt drive roller blind by Junkmail90210
by Thingiverse
Last crawled date: 2 years, 11 months ago
I have remixed my previous design. https://www.thingiverse.com/thing:4784786
What this is:
This is an interim release of the design. It's working very nice, I have it currently running on 4 roller blinds. I have since the last design been iteratively improving the design. Currently the design is broken into parts. If you do make this, you will need modify it to adapt to your wall bracket or to change the frame to a direct to wall interface.
Since the last round of changes, I have thickened the frame structure which lessens the twist that did occur (twisted the old frame, which then bent metal wall bracket). I have improved how the clutch works so there is less slop in the action (less creep up or down from day to day)
The motor on the inner side of the rollerblind. I am installing them back to back. You could save some filament by installing the motor outside the rolllerblind (frame-motor riser bit).
The tollerances of my printer aren't great. But the design is intended to spin freely, so if you assemble it all together without the belt and the springs the 100tooth gear should spin nicely on the spindle. The cap should not be chaffing the clutch parts, and the 'clutch on rod' should rotate in place.
Once the design is complete I will print an enclosure for the motor. Currently working on the heavier of the blinds. I think I am reaching the shear limit for printed plastic :-(
Components:
I use a lolin v3 nodemcu as my microcontroller ch340https://tttapa.github.io/ESP8266/Chap04%20-%20Microcontroller.html
I have included in my hardware selection the TCM 2209 stepper motor driver from Trinamic, you can learn more about it here. https://www.trinamic.com/products/integrated-circuits/details/tmc2209-la/
I can't recommend purchasing one enough. It is absolutely silent, you can hear the bearings turn. Here's good youtube comparing them.https://www.youtube.com/watch?v=Lx40lJkk9NQ
I used a simple stepper motor 1.5a. I also implemented the accelstepper library, which supports acceleration (gradual start and stop). I'm not sharing my arduino sketch at this time. If there is interest, perhaps at a later date.https://www.makerguides.com/drv8825-stepper-motor-driver-arduino-tutorial/
The VREF on the 2209 stepper driver is different than the drv2855 or a4988.
Here's a calculator for the vref for my 1.5a I'm putting 1.66vref (keeps silent step active)https://wiki.fysetc.com/Silent2209/#calculator
The 2209 uses a stallguard technology which you can learn about here.https://www.youtube.com/watch?v=Prw7wNa20Gk&t=2s
Stall guard is a new feature, getting it working in arduino is still pretty new, and way outside the scope of what I'm doing now... Here's some usefull information.https://electronics.stackexchange.com/questions/384522/how-do-i-wire-a-tmc2130-stepper-motor-driver-to-an-arduino-uno-in-order-to-contr/518984#518984
Included:
I've uploaded my fusion working files (it's a mess!!!)
I've also included an excel file that you can calculate your life requirements for your motor
parts:
1.5 amp stepper motor.
4 m3 30mm to hold on your motor
1 8-32 2 1/2" bolt and nut for the spindle (double nut or some threadlock)
1 gt2 300 belt (you can adjust how far the motor is from the roller in one of the sketches(should make this a parameter))
What this is:
This is an interim release of the design. It's working very nice, I have it currently running on 4 roller blinds. I have since the last design been iteratively improving the design. Currently the design is broken into parts. If you do make this, you will need modify it to adapt to your wall bracket or to change the frame to a direct to wall interface.
Since the last round of changes, I have thickened the frame structure which lessens the twist that did occur (twisted the old frame, which then bent metal wall bracket). I have improved how the clutch works so there is less slop in the action (less creep up or down from day to day)
The motor on the inner side of the rollerblind. I am installing them back to back. You could save some filament by installing the motor outside the rolllerblind (frame-motor riser bit).
The tollerances of my printer aren't great. But the design is intended to spin freely, so if you assemble it all together without the belt and the springs the 100tooth gear should spin nicely on the spindle. The cap should not be chaffing the clutch parts, and the 'clutch on rod' should rotate in place.
Once the design is complete I will print an enclosure for the motor. Currently working on the heavier of the blinds. I think I am reaching the shear limit for printed plastic :-(
Components:
I use a lolin v3 nodemcu as my microcontroller ch340https://tttapa.github.io/ESP8266/Chap04%20-%20Microcontroller.html
I have included in my hardware selection the TCM 2209 stepper motor driver from Trinamic, you can learn more about it here. https://www.trinamic.com/products/integrated-circuits/details/tmc2209-la/
I can't recommend purchasing one enough. It is absolutely silent, you can hear the bearings turn. Here's good youtube comparing them.https://www.youtube.com/watch?v=Lx40lJkk9NQ
I used a simple stepper motor 1.5a. I also implemented the accelstepper library, which supports acceleration (gradual start and stop). I'm not sharing my arduino sketch at this time. If there is interest, perhaps at a later date.https://www.makerguides.com/drv8825-stepper-motor-driver-arduino-tutorial/
The VREF on the 2209 stepper driver is different than the drv2855 or a4988.
Here's a calculator for the vref for my 1.5a I'm putting 1.66vref (keeps silent step active)https://wiki.fysetc.com/Silent2209/#calculator
The 2209 uses a stallguard technology which you can learn about here.https://www.youtube.com/watch?v=Prw7wNa20Gk&t=2s
Stall guard is a new feature, getting it working in arduino is still pretty new, and way outside the scope of what I'm doing now... Here's some usefull information.https://electronics.stackexchange.com/questions/384522/how-do-i-wire-a-tmc2130-stepper-motor-driver-to-an-arduino-uno-in-order-to-contr/518984#518984
Included:
I've uploaded my fusion working files (it's a mess!!!)
I've also included an excel file that you can calculate your life requirements for your motor
parts:
1.5 amp stepper motor.
4 m3 30mm to hold on your motor
1 8-32 2 1/2" bolt and nut for the spindle (double nut or some threadlock)
1 gt2 300 belt (you can adjust how far the motor is from the roller in one of the sketches(should make this a parameter))
Similar models
thingiverse
free
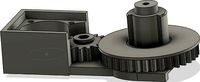
Nema 17 geared Roller Blind by Junkmail90210
...epper-motor-driver-arduino-tutorial/
please check out my next design iteration that uses belts, and silent stepper motor drivers.
grabcad
free

LV8729 Stepper Driver Module
...than 1.5a.
electric scheme has taken from here https://github.com/bigtreetech/bigtreetech-stepper-motor-driver/tree/master/lv8729
grabcad
free

TB6600 Stepper motor driver by taitran
... output 4a peak current, which is enough for the most of stepper motors. the stepper driver supports speed and direction control.
grabcad
free

TB6600 stepper motor driver by prodes
... output 4a peak current, which is enough for the most of stepper motors. the stepper driver supports speed and direction control.
grabcad
free

TB6600 Stepper motor driver by Tdesign
... output 4a peak current, which is enough for the most of stepper motors. the stepper driver supports speed and direction control.
grabcad
free

TB6600 Stepper motor driver by Taitran Technic
... output 4a peak current, which is enough for the most of stepper motors. the stepper driver supports speed and direction control.
grabcad
free

TB6600 stepper motor driver by proma
... output 4a peak current, which is enough for the most of stepper motors. the stepper driver supports speed and direction control.
grabcad
free

Unipolar Stepper Motor Driver
...il current, and the driver is designed to work with my pic dev board (https://grabcad.com/library/pic16f876-development-board-1).
thingiverse
free
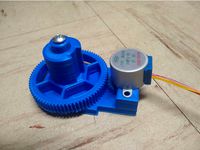
Roller Curtain with clutch and power by Junkmail90210
...rope to drive the clutch. i simply kept things similar and modified to print from plastic. the spring is...
thingiverse
free
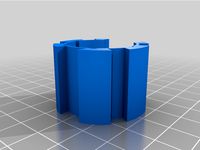
Adaptor for Roller Blind Motors by sillyfrog
...ed to customise it for your blinds, i have uploaded all of my source files here: https://github.com/sillyfrog/rollerblindadaptors
Junkmail90210
thingiverse
free
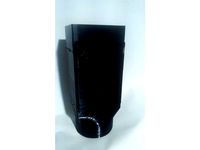
Downspout Filter by Junkmail90210
...downspout filter by junkmail90210
thingiverse
simple downspout filter with removable basket/door.
thingiverse
free
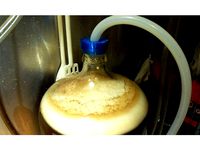
BlowoffCap by Junkmail90210
...ap by junkmail90210
thingiverse
printed tpu
fits;
55mm outer diameter spout of glass carboy
18mm outer diameter silicone tubing.
thingiverse
free
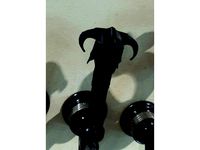
Dovahkiin Beer Tap by Junkmail90210
...dovahkiin beer tap by junkmail90210
thingiverse
messy file, still learning f360 so will post file if someone wants.
thingiverse
free
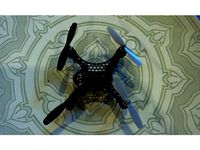
Quadcopter Frame by Junkmail90210
...fit the screw holes for the propel zipp nano. also put some legs on to support the wires a bit as the zipp nano flies belly down.
thingiverse
free
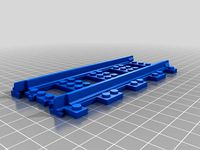
Lego Train Track, Straight by Junkmail90210
...lego train track, straight by junkmail90210
thingiverse
adjusted to make it easier to connect.
printed in pla, no supports
thingiverse
free
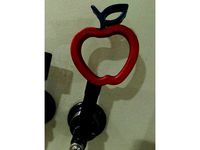
Apple Cider Tap by Junkmail90210
...210
thingiverse
remix of the cider tap from rniice to adapt to a soda tap. printed it flat with no supports. painted by kids :-)
thingiverse
free
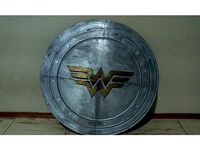
WW_Shield by Junkmail90210
...warm water to get the curve/size right.
also included a shield holder (mirror print with supports) to mount the shield to a wall.
thingiverse
free

Sith Acolyte Mast Beer Tap by Junkmail90210
...sith acolyte mast beer tap by junkmail90210
thingiverse
remix of killonious awesome mask to fit a beer tap (soda tap).
thingiverse
free
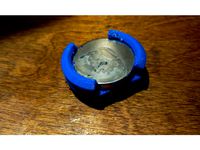
BeerBottleScrubber by Junkmail90210
...of water
lay carboy on it's side
slide the scrubber into bottle
use second magnet to move the scrubber and take off the gunk!
thingiverse
free
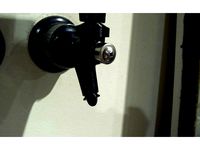
Beer Tap Plug by Junkmail90210
...your beer-tap to keep out pesky fruit-flies. i have soda taps with an inner diameter of 11mm so scale up or down to fit your tap.
Nema
3d_export
$5
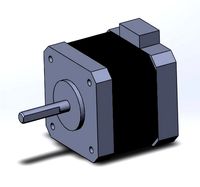
Electric Motor Nema 17
...electric motor nema 17
3dexport
40mm stepper motor nema 17 1.5a (17hs4401) motor 4-wire for 3d printer
turbosquid
$3
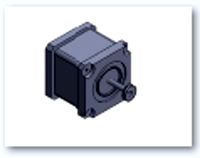
Nema 17
...rbosquid
royalty free 3d model nitro engine for download as on turbosquid: 3d models for games, architecture, videos. (1449252)
turbosquid
$1
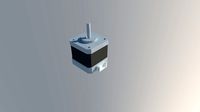
Nema 17 Stepper motor
... available on turbo squid, the world's leading provider of digital 3d models for visualization, films, television, and games.
turbosquid
$1
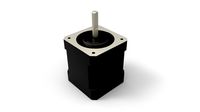
Nema 17 Stepper Motor 59Nm
... available on turbo squid, the world's leading provider of digital 3d models for visualization, films, television, and games.
turbosquid
$3
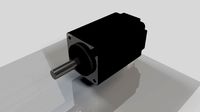
Simple model of Nema 8 stepper motor
...del of nema 8 stepper motor for download as ipt, obj, and stl on turbosquid: 3d models for games, architecture, videos. (1543132)
3d_export
$5

simple model of nema 17 stepper motor
...ort
simple model, useful to prototype robots, 3d printers and other electronic diy projects<br>step and .ipt file included
3d_export
$5
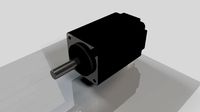
simple model of nema 8 stepper motor
...robots, 3d printers and other electronic diy projects<br>current model: 20bygh33-0604a<br>step and .ipt file included
3ddd
free
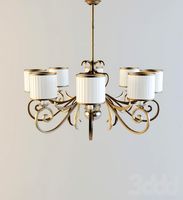
Larte Luce
...class="star five "></div></div></li><li><img src="http://b.3ddd.ru/media/cache/sky_user_avatar_comment/avatar/users/117489.jpg" alt="ci-nema" width="35" height="35" class="img"><div class="name"><a href="/users/ci-nemaquot;>ci-nema</a></div><div class="raiting"><div class="star five "></div></div></li></ul><div class="more"><a href="/3dmodels/show/larte_luce/voted">еще</a></div></div><div class="number" rating="30" count="6"...
thingiverse
free

Nema 14 to Nema 17 Adapter by lukepat
...nema 14 to nema 17 adapter by lukepat
thingiverse
created a adapter for nema 14 to nema 17 mount.
thingiverse
free
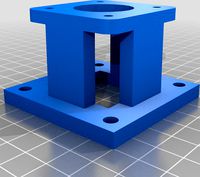
Distance Nema 17 and Nema 23 by Krzysztof_Handtke
...distance nema 17 and nema 23 by krzysztof_handtke
thingiverse
distance to nema motors to build a cnc milling machine.
Blind
archibase_planet
free

Blind
...blind
archibase planet
blind venetian blind jalousie
blind - 3d model for interior 3d visualization.
archibase_planet
free
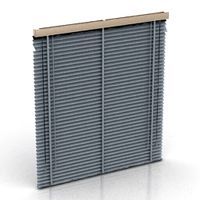
Blinds
...blinds
archibase planet
blinds blind jalousie
blinds n270313 - 3d model (*.gsm+*.3ds) for interior 3d visualization.
archibase_planet
free
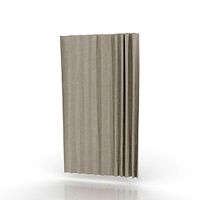
Blind
...blind
archibase planet
blind venetian blind jalousie
blind n031007 - 3d model (*.gsm+*.3ds) for interior 3d visualization.
archibase_planet
free
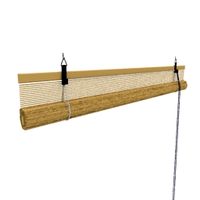
Blind
...blind
archibase planet
blind jalousie
blind - 3d model for interior 3d visualization.
archibase_planet
free
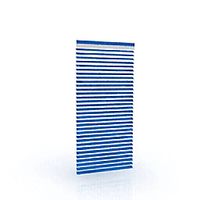
Blind
...blind
archibase planet
blind sunblind jalousie
blind - 3d model for interior 3d visualization.
archibase_planet
free

Blind
...blind
archibase planet
blind curtain
blind - 3d model (*.gsm+*.3ds) for interior 3d visualization.
archibase_planet
free
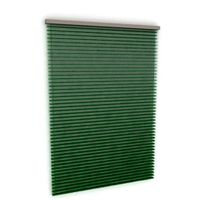
Blind
...blind
archibase planet
blind jalousie
venetian blind 1- 3d model for interior 3d visualization.
archibase_planet
free
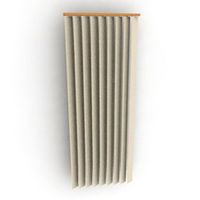
Blind
...blind
archibase planet
venetian blind jalousie
venetian blind 2 - 3d model for interior 3d visualization.
3d_ocean
$9
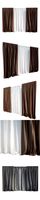
Blinds
...blinds
3docean
blinds curtain decor decoration drapes flat furniture home house interior jalousie
?urtains and blinds
archibase_planet
free
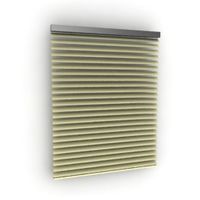
Blind
...blind
archibase planet
venetian blind jalousie
so blinds - 3d model (*.gsm+*.3ds) for interior 3d visualization.
Roller
turbosquid
$26
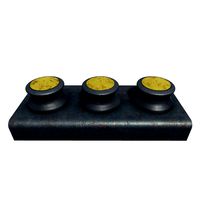
Roller A
...urbosquid
royalty free 3d model roller a for download as fbx on turbosquid: 3d models for games, architecture, videos. (1350603)
turbosquid
$3
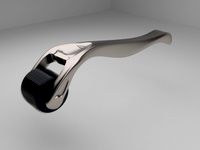
Roller
...oyalty free 3d model roller for download as 3ds, max, and obj on turbosquid: 3d models for games, architecture, videos. (1460818)
3ddd
$1

edilkamin roller
...edilkamin roller
3ddd
камин
edilkamin roller 360
3ddd
$1
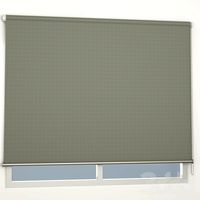
Roller Blinds
...roller blinds
3ddd
рулонная
roller blinds black out finish
turbosquid
$50
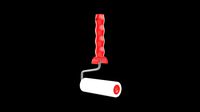
Roller
... roller for download as max, max, c4d, max, max, fbx, and obj on turbosquid: 3d models for games, architecture, videos. (1700762)
3d_export
$10
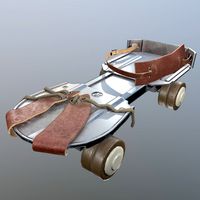
rollers
...lers
3dexport
this is low-poly model of rollers.<br>model:<br>- low-poly<br>- textured<br>- uv unwrapped
3d_export
$28

Roller 3D Model
...roller 3d model
3dexport
roller construction boss evil
roller 3d model adagio15740837 50561 3dexport
3d_export
$6

hopper roller conveyor
...hopper roller conveyor
3dexport
hopper roller conveyor
3d_export
$12
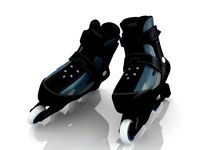
roller skates
...roller skates
3dexport
3d_ocean
$19
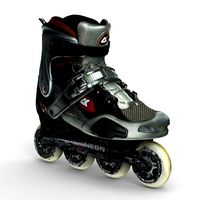
roller skate
...can scanned skates skating sport
3d scan of roller skate. the model has been retopologized and made fully compatible with zbrush.
Belt
3d_export
$6
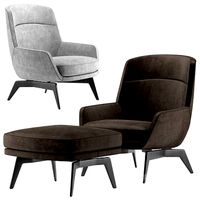
belt
...d then comes off and fastens at the front of the seat. version: 2015 units: millimetres x-form: yes polys: 120 950 verts: 163 944
3d_export
$7
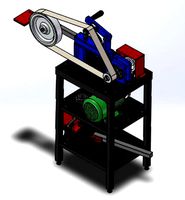
belt grinder
...belt grinder
3dexport
belt grinder
3d_export
$5
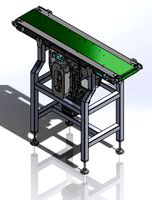
Belt conveyor
...belt conveyor
3dexport
belt conveyor
3ddd
$1
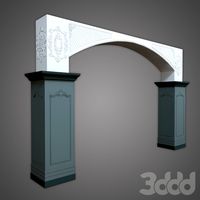
column belt
...column belt
3ddd
колонна
column belt
turbosquid
$5
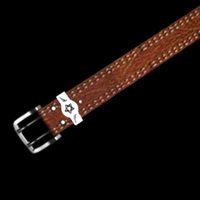
Belt
... available on turbo squid, the world's leading provider of digital 3d models for visualization, films, television, and games.
3d_ocean
$5
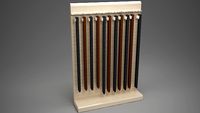
Leather Belt
...ather belt is created in 3dsmax 2011 and rendered with vray 1.5 and it has all the texture included with the multiple obj format.
3d_ocean
$5
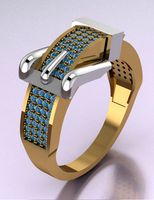
Belt Ring
...belt ring
3docean
belt jewelry ring
belt ring 3d model. total weight 3.5 gram & 1.1 stone size. 3dm and obj file format.
design_connected
$11
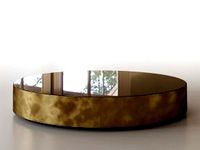
Belt Oval
...belt oval
designconnected
meridiani belt oval computer generated 3d model. designed by parisio, andrea.
design_connected
$11
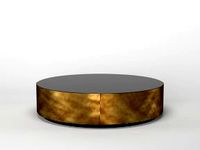
Belt Round
...belt round
designconnected
meridiani belt round computer generated 3d model. designed by parisio, andrea.
design_connected
$11
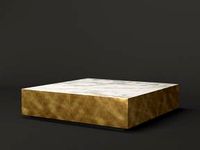
Belt Square
...belt square
designconnected
meridiani belt square computer generated 3d model. designed by parisio, andrea.
17
3d_export
$6
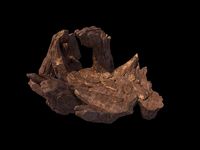
rocks 17
...rocks 17
3dexport
rocks 3d model 17
3ddd
$1
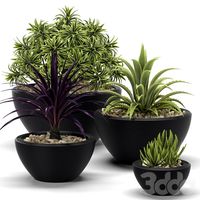
PLANTS 17
...plants 17
3ddd
цветок , горшок
plants 17,, pots in diameter 100,80,60,40cm,,, enjoy
3d_export
$6
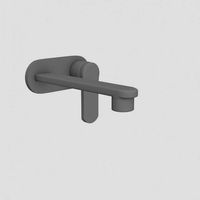
tap-17
...tap-17
3dexport
3d_export
$6
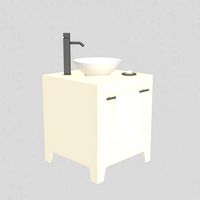
set-17
...set-17
3dexport
3d_export
$27
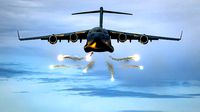
C-17 Globemaster
...c-17 globemaster
3dexport
c-17 globemaster
3ddd
free
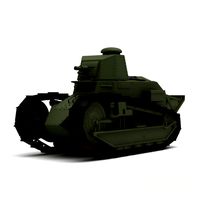
Renault FT-17
...renault ft-17
3ddd
ft-17 , renault , танк
turbosquid
$40
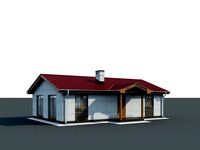
cottage 17
...bosquid
royalty free 3d model cottage 17 for download as max on turbosquid: 3d models for games, architecture, videos. (1377003)
turbosquid
$30
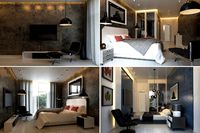
Apartment 17
...squid
royalty free 3d model apartment 17 for download as max on turbosquid: 3d models for games, architecture, videos. (1432680)
turbosquid
$7
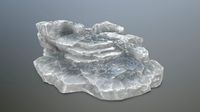
Rock 17
...turbosquid
royalty free 3d model rock 17 for download as obj on turbosquid: 3d models for games, architecture, videos. (1486522)
turbosquid
$5
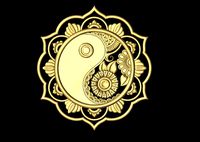
Decor 17
...urbosquid
royalty free 3d model decor 17 for download as stl on turbosquid: 3d models for games, architecture, videos. (1677126)
Drive
3d_export
$10
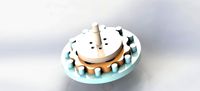
cycloidal drive
...cycloidal drive
3dexport
cycloidal drive
3d_ocean
$5
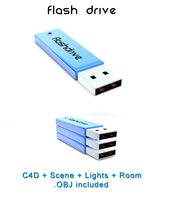
Flash Drive
...h drive included : – materials – scene ( lighs / room ) – .c4d + .obj for any questions please feel free to contact me thank you.
3d_ocean
$5
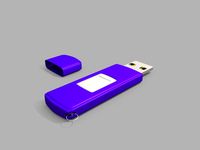
Usb drive
...s shaders and a lighting setup. it also has a small animation of it going in and out. i saved it out as both a .blend file and...
3d_ocean
$5
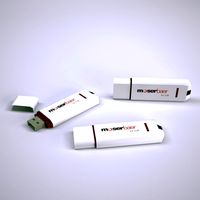
Pen Drive
...est computer drive game model good low poly new pen pen drive textured unwrapped uv very low poly
a very beautiful low poly model
3d_ocean
$10
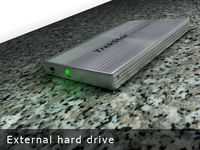
External hard drive
... is a detailed model of a trekstor external hard drive. you can easily modify the label on the top. simply edit the text objects.
turbosquid
$1
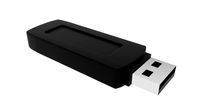
Flash Drive
...quid
royalty free 3d model flash drive for download as blend on turbosquid: 3d models for games, architecture, videos. (1231573)
turbosquid
$10
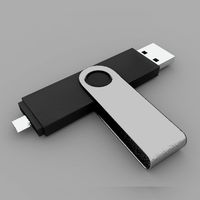
Flash Drive
...id
royalty free 3d model usb flash drive for download as obj on turbosquid: 3d models for games, architecture, videos. (1325282)
turbosquid
$1
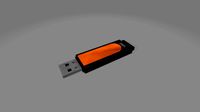
USB Drive
...
royalty free 3d model usb drive for download as obj and fbx on turbosquid: 3d models for games, architecture, videos. (1701787)
3d_ocean
$4
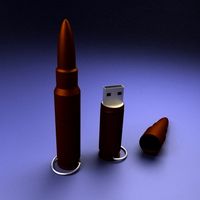
USB Flash Drive
...usb flash drive
3docean
computer disk drive electronic flash mac memory pc pen usb
usb flash drive. the cartridge form
turbosquid
$10
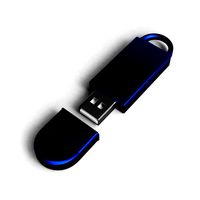
Flash Drive
...y free 3d model flash drive for download as lxo, lxo, and obj on turbosquid: 3d models for games, architecture, videos. (1551742)