GrabCAD
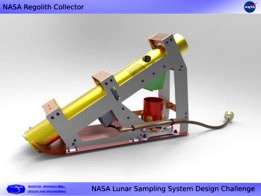
NASA Regolith Collector
by GrabCAD
Last crawled date: 1 year, 10 months ago
This concept is very simple consisting of aluminum and plastic parts. It's designed to be used on a robotic arm. Currently, the design uses laser cut sheet metal parts held together by nuts and bolts. Perhaps spot welding would be better to save some weight and for simplicity. Also, using aluminum rods and joints could save additional weight. The plastic parts are the sample container holder and compaction assembly.
The operating principle is using a tube with an internal screw to extract regolith from the lunar surface and filtered out through holes in the cylinder. Excess regolith larger than 2 cm will continue to travel past the filter and falls off the back of the tube.
The filtered regolith first separates the dust then the particles less than 2 cm into the hopper/chute then falls into the sample container. The compaction assembly consists of a sample container holder suspended by 4 tension springs and compacted and by a vibration motor to get the desired result.
The cylinder/tube is rotated by a stepper motor. I chose to use the Nema 14 bipolar motor with a power consumption of 3.75 W. https://www.omc-stepperonline.com/hybrid-stepper-motor/nema-14-bipolar-18deg-23ncm-326ozin-05a-75v-35x35x42mm-4-wires-14hs17-0504s.html Based on testing, the motor could be downsized if less torque is required.
For the vibration motor, I chose to use a brushed dc motor of power approximately 1.5 W. Total power will be less than 6 W. https://www.amazon.com/dp/B00977HHVW/ref=twister_B07GR6KJSP?th=1
The compaction assembly ensured that fine/loose regolith and rocks less than 2 cm are nicely packed in the sample container until the mass and volume requirements are met.
Samples only come in contact with aluminum components and the stoppers at the front of the unit ensures that samples are collected in the upper 10 cm of lunar regolith.
A camera can be positioned at the back of the unit that views down the tube to see the sample before depositing. The contents of the sample container can also be easily seen. If the sample viewed in the tube is undesirable, it can be rejected by reversing the direction of the screw to dump the regolith back on the surface. The robotic arm can then move the assembly to a new location to try again.
It is possible to complete the collection process in a few minutes. My concept is not affected by temperature or hard vacuum. The electrical connector is connected to the robotic arm for power. When sample collection is complete, the tube can be emptied by reversing the screw direction again.
Thanks to NASA and GrabCad for this design exercise, I really enjoyed it. Good luck to everyone and if you like my concept, don't forget to click the like button. :)
Check out my other entry:
https://grabcad.com/library/nasa-simplified-collector-1
The operating principle is using a tube with an internal screw to extract regolith from the lunar surface and filtered out through holes in the cylinder. Excess regolith larger than 2 cm will continue to travel past the filter and falls off the back of the tube.
The filtered regolith first separates the dust then the particles less than 2 cm into the hopper/chute then falls into the sample container. The compaction assembly consists of a sample container holder suspended by 4 tension springs and compacted and by a vibration motor to get the desired result.
The cylinder/tube is rotated by a stepper motor. I chose to use the Nema 14 bipolar motor with a power consumption of 3.75 W. https://www.omc-stepperonline.com/hybrid-stepper-motor/nema-14-bipolar-18deg-23ncm-326ozin-05a-75v-35x35x42mm-4-wires-14hs17-0504s.html Based on testing, the motor could be downsized if less torque is required.
For the vibration motor, I chose to use a brushed dc motor of power approximately 1.5 W. Total power will be less than 6 W. https://www.amazon.com/dp/B00977HHVW/ref=twister_B07GR6KJSP?th=1
The compaction assembly ensured that fine/loose regolith and rocks less than 2 cm are nicely packed in the sample container until the mass and volume requirements are met.
Samples only come in contact with aluminum components and the stoppers at the front of the unit ensures that samples are collected in the upper 10 cm of lunar regolith.
A camera can be positioned at the back of the unit that views down the tube to see the sample before depositing. The contents of the sample container can also be easily seen. If the sample viewed in the tube is undesirable, it can be rejected by reversing the direction of the screw to dump the regolith back on the surface. The robotic arm can then move the assembly to a new location to try again.
It is possible to complete the collection process in a few minutes. My concept is not affected by temperature or hard vacuum. The electrical connector is connected to the robotic arm for power. When sample collection is complete, the tube can be emptied by reversing the screw direction again.
Thanks to NASA and GrabCad for this design exercise, I really enjoyed it. Good luck to everyone and if you like my concept, don't forget to click the like button. :)
Check out my other entry:
https://grabcad.com/library/nasa-simplified-collector-1
Similar models
grabcad
free

NASA Simplified Collector
...t, don't forget to click the like button. :)
check out my other model:
https://grabcad.com/library/nasa-regolith-collector-1
grabcad
free

NASA Lunar Sampling System
...mbly can collect and store samples. it has compact design and smaller footprint. with telescopic expandable arm it can be shrink.
grabcad
free

NASA LUNAR REGOLITH SAMPLING ROBOT
...nasa lunar regolith sampling robot
grabcad
low mass and low power lunar regolith sampling robot with bldc motor drive
grabcad
free

Nasa Rotating arm machine
...olith will be collect into container.my design requires only one stepper motor. my designed machine can be attach to robotic arm.
grabcad
free

NASA Lunar Sampling System
...r sampling system
grabcad
nasa lunar sampling system
it will be given by a simple motor movement. and to connect to a robot arm
grabcad
free

NASA Lunar Sampling System
...r sampling system
grabcad
nasa lunar sampling system
it will be given by a simple motor movement. and to connect to a robot arm
grabcad
free

NASA Lunar Sampling System
...r sampling system
grabcad
nasa lunar sampling system
it will be given by a simple motor movement. and to connect to a robot arm
grabcad
free

NEMA KANJENG LUNAR SAMPLING
... the arm has risen more than 60 degrees regolith will be slipped into the container that has been filtered between rock and dust.
grabcad
free

NASA Lunar Sampling System Design Challenge- Option 1
... ppt snapshots. please review and provide feedback.
ps: i am working on a variation of this concept and will be submitting soon.
grabcad
free

NASA Lunar Sampling System
...nasa lunar sampling system
grabcad
can be mounted on a simple robot arm. motor helical system
Regolith
3d_sky
free
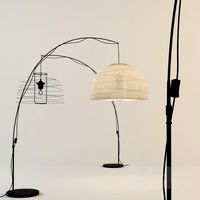
Ikea regolith
...ikea regolith
3dsky
ikea
floor lamp, curvedhttp://www.ikea.com/ru/ru/catalog/products/50103406/
thingiverse
free
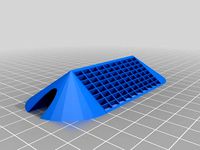
Customizable struts for regolith-shielded dugout houses by drxenocide
...golith.
*edit (2014jun01) added support for model making and sheet building. because if i win, makerbot will want to print one.
thingiverse
free
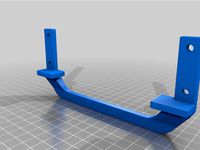
HP V1910-24G Tabletop Stand by Regolith
...006a) switch on my desk and be able to organize patch cables below. foot uses the mounting locations for rack ears. requires two.
thingiverse
free

Replacement knob for Harbor Freight ladder by Regolith
...nob for the folding hinge. printed this in pla and it's held up fine. maybe abs or petg if you want it to be super bombproof.
thingiverse
free
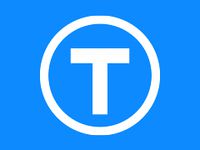
Headrest Maglite Mount by Regolith
...10mm rods). the clip installs by twisting onto the headrest rods, and the maglite adds a rigid connection between the two mounts.
thingiverse
free
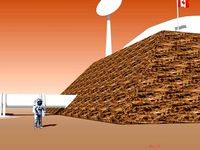
Mars complex: Regolith construction by smichel
...cal factories wii extract oxygen and chlorates from the abundant minerals to fuel the trip back and forth between earth and mars.
3d_sky
free
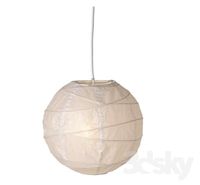
Ikea01
...ikea01 3dsky regolith lamp from ikea...
3d_sky
$8

IKEA / REGOLIT
...ikea / regolit 3dsky lampshade ikea regolith regolit shade diameter: 45...
thingiverse
free
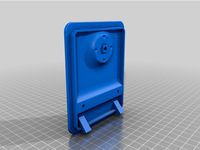
Tekonsha P3 Mount (Toyota Tacoma Gen1) by Regolith
...l using an earlier revision (this version has the mounting screws moved outboard to hold the hoop a little tighter to the panel).
thingiverse
free
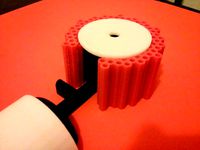
Mars Research Station Two by xmbrst
...habs are printed in black in the photos.) 3d-printed regolith structures -- to provide better radiation and structural protection,...
Collector
3ddd
$1
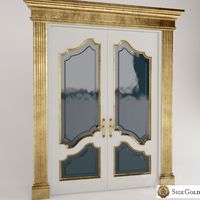
двери Collector
... collector , sigegold
collector collection коллекции дверей sigegold
turbosquid
free

collectors tin.lwo
... available on turbo squid, the world's leading provider of digital 3d models for visualization, films, television, and games.
3d_export
$5
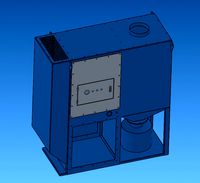
Double Cartridge Dust Collector
...double cartridge dust collector
3dexport
double cartridge dust collector
evermotion
$15
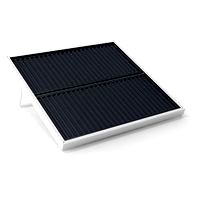
solar collector 06 AM74
...tor design with all textures, shaders and materials. it is ready to use, just put it into your scene.. evermotion 3d models shop.
evermotion
$15
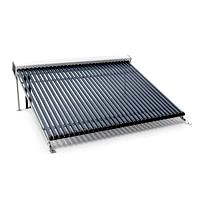
solar collector 03 AM74
...tor design with all textures, shaders and materials. it is ready to use, just put it into your scene.. evermotion 3d models shop.
evermotion
$15
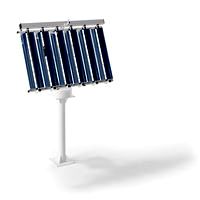
solar collector 07 AM74
...tor design with all textures, shaders and materials. it is ready to use, just put it into your scene.. evermotion 3d models shop.
evermotion
$15
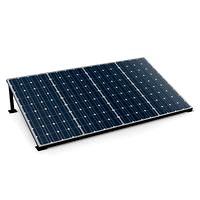
solar collector 12 AM74
...tor design with all textures, shaders and materials. it is ready to use, just put it into your scene.. evermotion 3d models shop.
evermotion
$15
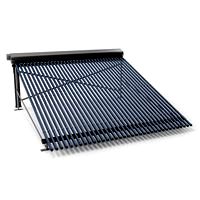
solar collector 04 AM74
...tor design with all textures, shaders and materials. it is ready to use, just put it into your scene.. evermotion 3d models shop.
evermotion
$15
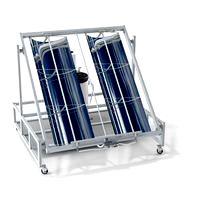
solar collector 08 AM74
...tor design with all textures, shaders and materials. it is ready to use, just put it into your scene.. evermotion 3d models shop.
evermotion
$15
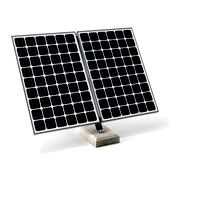
solar collector 09 AM74
...tor design with all textures, shaders and materials. it is ready to use, just put it into your scene.. evermotion 3d models shop.
Nasa
turbosquid
$49
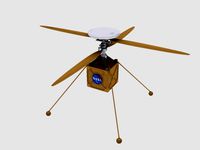
Nasa Marscopter
...id
royalty free 3d model nasa marscopter for download as max on turbosquid: 3d models for games, architecture, videos. (1323349)
turbosquid
$500

NASA Crawler
... available on turbo squid, the world's leading provider of digital 3d models for visualization, films, television, and games.
turbosquid
$5
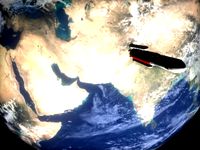
Nasa Rocket
... available on turbo squid, the world's leading provider of digital 3d models for visualization, films, television, and games.
turbosquid
$1

NASA Spool.max
... available on turbo squid, the world's leading provider of digital 3d models for visualization, films, television, and games.
3d_export
$15
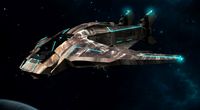
US NASA 3D Model
...us nasa 3d model
3dexport
spaceship ship nasa battle blender
us nasa 3d model antonielfelain 96625 3dexport
turbosquid
$99
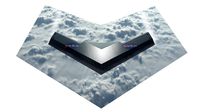
NASA MIT Wing
...oyalty free 3d model nasa mit wing for download as ma and max on turbosquid: 3d models for games, architecture, videos. (1510099)
turbosquid
$29
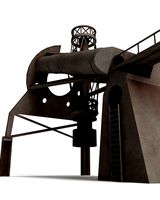
NASA Electronic Telescope
... available on turbo squid, the world's leading provider of digital 3d models for visualization, films, television, and games.
turbosquid
$6
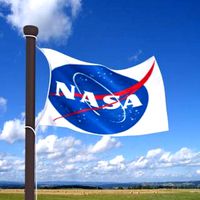
Real flag NASA
... available on turbo squid, the world's leading provider of digital 3d models for visualization, films, television, and games.
3d_export
$41
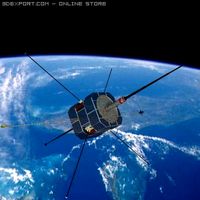
NASA FAST Satellite 3D Model
...odel
3dexport
nasa space satellite earth aurora sensor panel solar orbit
nasa fast satellite 3d model visualmotion 20244 3dexport
3d_export
$20
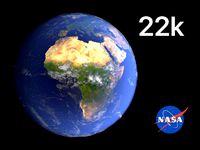
22k photorealistic earth - nasa
...tures directly from nasa.<br>nasa solar system bundle coming soon!<br>contact info@teichmanmedia.eu for all iquiries.