Thingiverse
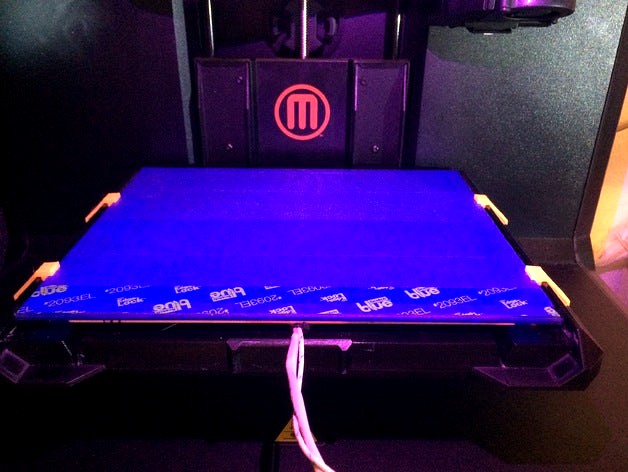
Makerbot 5th Gen Heated Print Bed (HPB) by lanyx
by Thingiverse
Last crawled date: 3 years ago
Ever wanted to print something other than PLA on your MB 5thGen? Having issues with warped edges? Time to put a heated print bed (HPB) on it. MB does not have any options for an HPB so I had to make my own design. I am now able to print perfectly flat using ABS, PET+, and PLA. I am sure it will do others but have not experimented yet. The HPB will easily heat to 110° C. It will use your existing glass plate. Keep in mind that this will NOT be integrated with the MB software. You will have to manually turn off/on the HPB before/after you print. The temperature controller will maintain whatever temperature you set and I also enabled a safety feature so that if the thermocouple fails or a relay fails closed, it will automatically turn off the power supply to prevent a fire. Materials needed:
350w 12-24v DC power supply http://www.amazon.com/gp/product/B00KXV4WH8?psc=1&redirect=true&ref_=oh_aui_detailpage_o03_s02
PCB heatbed hot plate (i got the one with the LEDs already soldered) http://www.amazon.com/gp/product/B015369VT6?psc=1&redirect=true&ref_=oh_aui_detailpage_o03_s03
12v relay 30/40amp with wiring harness (you only need 1, i bought a 5 pack) http://www.amazon.com/gp/product/B005HFYE1O?psc=1&redirect=true&ref_=oh_aui_detailpage_o03_s02
Temperature controller able to go above 100°C http://www.amazon.com/gp/product/B00OLOGO9M?psc=1&redirect=true&ref_=oh_aui_detailpage_o03_s01
Some 14ga wire
5 amp 120v fuse and holder
Heat shrink tubing
120v plug
Masking tape
Painters tape
2 paint sticks or yard sticks that are 5mm thick (Update: changing to Aluminum strips. May have to adjust clips as they are only 3.5mm thick.)
120v LED Panel mount (to let you know if the power supply is running, not required)
SPST panel mount switch (to turn off power to HPB but still leave the control unit on)
110v Power switch ( to turn the HPB and Temp Controller on/off)
Plastic or metal enclosure 4x5x6” to hold all components (recommend plastic if you don't have a nibbler to cut metal squares/holes
Banana female connectors for the ability to unplug Thermocouple
High amperage 12v connector like an XT60 or Dean's for the ability to unplug the HPB.
Both of the above connectors are recommended to be able to remove HPB and remove/replace the blue tape.
Some soldering skills
Some electrical skills
Work very slowly and make sure all your connections are 100% correct prior to energizing. This is a lot of power and easy to make mistakes
Steps:
Build temperature controller
Get plastic enclosure box and cut out square opening for Temperature Controller
Drill holes for the banana plugs, switches, power cables and anything you need in/out of the box
Refer to the wiring diagram on how everything ties together
Use 14ga wire for anything that will have high current
Refer to Inkbird on how the temperature controller operates for the ITC-100RH
Be sure to ground your power supply and case if using a metal box
Remember you are dealing with 120v in the case. Be careful if operating with case open and any shorts or incorrect wiring
Build Heated Print Bed
Print 4 clips prior to dismanteling your print bed
o 100% infil, Standard resolution (200mm)
o Order of preferance on filament (PET+, ABS,PLA)
Remove print bed tray and remove glass
Clean glass of all material and finish with an alcohol wipe
Store print bed plastic tray. Will no longer need
On PCB heater, solder power connections to bottom of PCB (side with the LED connector)
o Make sure the top is flat even at the solder pads
o Make sure there is solder going all the way through the PCB to ensure heating elements on top are getting power
Cut paint sticks/yard sticks 1x235mm, 2x108mm
o Maker sure the paint sticks are 5mm thick (homedepot/lowes)
Center PCB heating element side (noticable by all the rows of traces on the board) on the glass
Tape (masking tape) PCB to glass. Do not wrap tape around edges of glass
Bend thermocouple tip 90° and place in center hold of PCB (update: use some hose bib rubber washers taped around the tip to keep in place over time.)
Using masking tape, put ~3 layers of tape on thermocouple to hold in center of PCB and provide some insulation
Tape (masking tape) wood pieces to PCB as shown in pictures
o Two shorter pieces are for placing on the front side with space for the thermocouple wiring
Cover top of glass with Blue Painters tape. Wipe with an alcohol wipe. This creates a fantastic surface for all filaments. Wipe gets rid of any residue or grease on the surface.
Install new heater print bed on bed platform
Install clips starting top first and snap at the bottom of the platform edge
Admire your creation
Perform level process based on your printer. On the MB 5th gen, I first start with an auto level then finish with a manual level.
o Turn off printer
o Manually turn bed Z rod to move the print bed to within a couple mm of the print head
Use a paper towel or something as this has grease on it
You will want to recoat the rod after you are done with grease as this should be done periodically anyways
o Manually move the print head to the center of the print bed
o Use a business card and bring print bed up to the thickness of the business card. You should be able to move the business in an out with minimal friction
o Move the print head to the front center
o Measure with business card again. Adjust front/back knob to same friction as center
o Move print head to rear center, measure and adjust. Do this several times to get front and back as close as possible
o Move print head to right center, then left center and adjust the left/right knob until the exact same
o Do this process several times to get the entire surface of the print bed the same height.
o Keep in mind that the glass may not be 100% flat and that the print head rods may also not be 100% flat. I ALWAYS print with a raft on the MB to eliminate as much unlevel as possible
Once you have everything setup and operational, the below settings should get you started. Adjust for your brand of filament. This entire setup also helps in eliminating any variances you may be seeing by your room temperature. Before I had to put the printer in a closet with a space heater as my house was too cold causing a lot of warping. Now with the HPB I don't have to use a space heater, my prints are near 100% flat and I am able to do stronger filaments.
Filament starting temperature (all numbers in C)
o ABS HPB 110° Extruder 235° Speed 90% (Infill,inset, raft)
o PET+ HPB 70° Extruder 245° Speed 50%
o PLA HPB 50° Extruder 215° Speed 100%
350w 12-24v DC power supply http://www.amazon.com/gp/product/B00KXV4WH8?psc=1&redirect=true&ref_=oh_aui_detailpage_o03_s02
PCB heatbed hot plate (i got the one with the LEDs already soldered) http://www.amazon.com/gp/product/B015369VT6?psc=1&redirect=true&ref_=oh_aui_detailpage_o03_s03
12v relay 30/40amp with wiring harness (you only need 1, i bought a 5 pack) http://www.amazon.com/gp/product/B005HFYE1O?psc=1&redirect=true&ref_=oh_aui_detailpage_o03_s02
Temperature controller able to go above 100°C http://www.amazon.com/gp/product/B00OLOGO9M?psc=1&redirect=true&ref_=oh_aui_detailpage_o03_s01
Some 14ga wire
5 amp 120v fuse and holder
Heat shrink tubing
120v plug
Masking tape
Painters tape
2 paint sticks or yard sticks that are 5mm thick (Update: changing to Aluminum strips. May have to adjust clips as they are only 3.5mm thick.)
120v LED Panel mount (to let you know if the power supply is running, not required)
SPST panel mount switch (to turn off power to HPB but still leave the control unit on)
110v Power switch ( to turn the HPB and Temp Controller on/off)
Plastic or metal enclosure 4x5x6” to hold all components (recommend plastic if you don't have a nibbler to cut metal squares/holes
Banana female connectors for the ability to unplug Thermocouple
High amperage 12v connector like an XT60 or Dean's for the ability to unplug the HPB.
Both of the above connectors are recommended to be able to remove HPB and remove/replace the blue tape.
Some soldering skills
Some electrical skills
Work very slowly and make sure all your connections are 100% correct prior to energizing. This is a lot of power and easy to make mistakes
Steps:
Build temperature controller
Get plastic enclosure box and cut out square opening for Temperature Controller
Drill holes for the banana plugs, switches, power cables and anything you need in/out of the box
Refer to the wiring diagram on how everything ties together
Use 14ga wire for anything that will have high current
Refer to Inkbird on how the temperature controller operates for the ITC-100RH
Be sure to ground your power supply and case if using a metal box
Remember you are dealing with 120v in the case. Be careful if operating with case open and any shorts or incorrect wiring
Build Heated Print Bed
Print 4 clips prior to dismanteling your print bed
o 100% infil, Standard resolution (200mm)
o Order of preferance on filament (PET+, ABS,PLA)
Remove print bed tray and remove glass
Clean glass of all material and finish with an alcohol wipe
Store print bed plastic tray. Will no longer need
On PCB heater, solder power connections to bottom of PCB (side with the LED connector)
o Make sure the top is flat even at the solder pads
o Make sure there is solder going all the way through the PCB to ensure heating elements on top are getting power
Cut paint sticks/yard sticks 1x235mm, 2x108mm
o Maker sure the paint sticks are 5mm thick (homedepot/lowes)
Center PCB heating element side (noticable by all the rows of traces on the board) on the glass
Tape (masking tape) PCB to glass. Do not wrap tape around edges of glass
Bend thermocouple tip 90° and place in center hold of PCB (update: use some hose bib rubber washers taped around the tip to keep in place over time.)
Using masking tape, put ~3 layers of tape on thermocouple to hold in center of PCB and provide some insulation
Tape (masking tape) wood pieces to PCB as shown in pictures
o Two shorter pieces are for placing on the front side with space for the thermocouple wiring
Cover top of glass with Blue Painters tape. Wipe with an alcohol wipe. This creates a fantastic surface for all filaments. Wipe gets rid of any residue or grease on the surface.
Install new heater print bed on bed platform
Install clips starting top first and snap at the bottom of the platform edge
Admire your creation
Perform level process based on your printer. On the MB 5th gen, I first start with an auto level then finish with a manual level.
o Turn off printer
o Manually turn bed Z rod to move the print bed to within a couple mm of the print head
Use a paper towel or something as this has grease on it
You will want to recoat the rod after you are done with grease as this should be done periodically anyways
o Manually move the print head to the center of the print bed
o Use a business card and bring print bed up to the thickness of the business card. You should be able to move the business in an out with minimal friction
o Move the print head to the front center
o Measure with business card again. Adjust front/back knob to same friction as center
o Move print head to rear center, measure and adjust. Do this several times to get front and back as close as possible
o Move print head to right center, then left center and adjust the left/right knob until the exact same
o Do this process several times to get the entire surface of the print bed the same height.
o Keep in mind that the glass may not be 100% flat and that the print head rods may also not be 100% flat. I ALWAYS print with a raft on the MB to eliminate as much unlevel as possible
Once you have everything setup and operational, the below settings should get you started. Adjust for your brand of filament. This entire setup also helps in eliminating any variances you may be seeing by your room temperature. Before I had to put the printer in a closet with a space heater as my house was too cold causing a lot of warping. Now with the HPB I don't have to use a space heater, my prints are near 100% flat and I am able to do stronger filaments.
Filament starting temperature (all numbers in C)
o ABS HPB 110° Extruder 235° Speed 90% (Infill,inset, raft)
o PET+ HPB 70° Extruder 245° Speed 50%
o PLA HPB 50° Extruder 215° Speed 100%
Similar models
thingiverse
free

Adjustable Power Source - Hot Wheels by NHSE
...o-universal-switching-replacement-connectors/dp/b013p01udc?ie=utf8&psc=1&redirect=true&ref_=oh_aui_detailpage_o01_s00
thingiverse
free
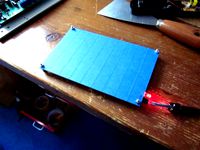
100x160mm PCB standard sized heated bed by jjshortcut
...urning the potentiometer.
more info about it at http://jjshortcut.wordpress.com/2011/11/21/555-timer-controlled-heated-print-bed/
thingiverse
free
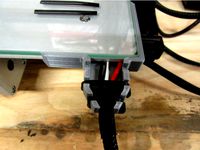
Creality CR-10 Wire management, Strain relief and Glass holder by Evanrude
...r glass is to small then you can just put a piece of zip tie in there to hold it which allows you more front and back print area.
thingiverse
free
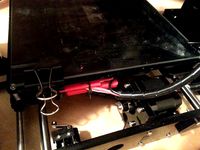
A8 Heat bed Solder Support by Radem
...or and supports the connection. i attached it to the the acrylic frame with 2 sided tape, then attached the wires with a zip tie.
thingiverse
free
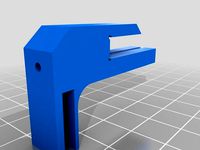
3/16" Clip for Glass Heated Bed for M3D Printer by bkibalo
... 3/16" glass heated bed into the micro m3d printer. this clip has a hole to hold a thermocouple for temperature montioring.
thingiverse
free
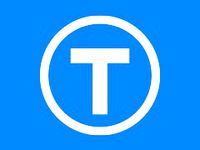
Heated Bed Wire/Solder Support Clip by Walk3rt
...ace. i did create this model in sketchup, so if you would like to download the file to edit to your needs, just let me know. :)
cg_trader
$50
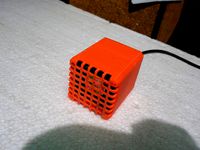
Smallest Incubator Heater | 3D
...ler. temperature controller i used,
https://www.amazon.in/robocraze-w1209-50-100-temperature-controller-thermostat/dp/b072kt75d3
thingiverse
free
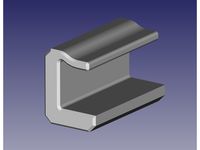
Heat-Bed Clamp 6mm by Sisul
...few hours at 50-60°c, and only noticed a slight stress fatigue. the clamp is still holding the glass bed well on the heating bed.
grabcad
free

Wave Soldering Machine
...achine: 3280 / w1200 / h1650 (mm) - see more at: http://www.robotdigg.com/product/868/wave+soldering+machine#sthash.8qogz9i9.dpuf
thingiverse
free
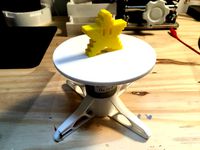
Turntable by jwilcott
...
and this motor controller: http://www.amazon.com/gp/product/b00dvggwc0?psc=1&redirect=true&ref_=oh_aui_search_detailpage
Lanyx
thingiverse
free
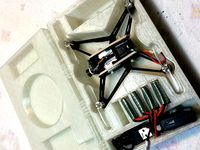
Case for Parrot Drone by lanyx
... to allow you to customize to your liking.
update 3/2/2016: modified case to handle turnigy 750mah batteries and to fix hinges.
thingiverse
free
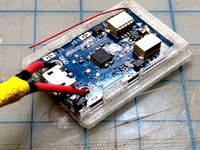
SciSky FC (Quanum PICO) in Parrot Frame by lanyx
...ngr923 http://www.thingiverse.com/thing:1302382.
updated 2016-03-02: updated fc cover to hold better. be sure to use supports.
thingiverse
free
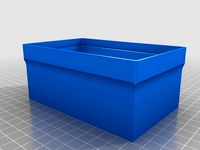
Quanum FPV Goggles v1 & v2 Extension Tube for 4.3" & 5" Monitor by lanyx
...mechanical (excellent 3d software for free), i've included the native files for you to play with and customize as you desire.
thingiverse
free

Mini Camera Holder for Parrot Rolling Spider Frame by yoannwyffels
...spider frame by yoannwyffels thingiverse camera holder redesigned from lanyx original design for the mini 600tvl camera: http://www.banggood.com/600tvl-8_0mp-14-2_8mm-cmos-fpv-170-degree-wide-anlge-lens-camera-palntsc-p-984345.html or...
Hpb
thingiverse
free
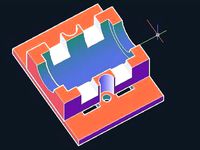
LM8UU Y Axis for HPB Deluxe Kit by Kempy
...hpb deluxe kit has 25mm or 23~mm pitch on screws, all others apear to be wider @ 30mm pitch. hence my requirement to adjust this.
thingiverse
free
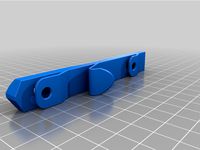
MPCNC Primo 25mm nut trap by hpb
... falling out if you change the tool mount.
no idea why i can't mark this as a remix
https://www.thingiverse.com/thing:4550789
thingiverse
free
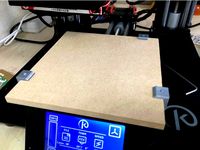
Trinus 3D Laser Wasteboard clips by 3dnoobie
...as a wasteboard for the laser. protect your expensive hpb with some cheap material before you risk damaging it....
thingiverse
free

Front Panel powered Printer by cr3a7ure
...12v without hpb, and plus 11a @ 12v with hpb be sure your psu has enough wattage to power...
thingiverse
free
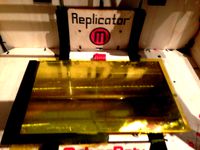
Lazy Man's Kapton Jig (Replicator) by CrazyJaw
...up both sides of kapton tape for the replicator hpb doing it by hand always takes me a dozen...
thingiverse
free
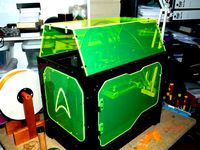
Replicator 1 Cover - "The Carbonator" by solertron
...the supplied dxf files. you will note that the hpb arms are from "bottleworks" - i highly recommend these....
thingiverse
free
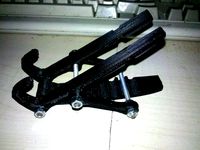
foldable and adjustable Tablet PC Stand by Ijon
...that thing again, as soon as we have a hpb in...
thingiverse
free
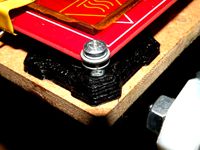
Prusa V2 Y-Axis Corner Nut Traps by Justblair
...possibility of backlash originating from the mounting of the hpb i have included the stl file that should produce...
thingiverse
free
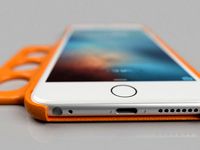
Ergo iPhone 6 Plus Case - For Limited Hand Mobility by daveyclk
...temp - layer 1 - 220c all others 200c hpb - 52c speed 70mm/s infil - 100% notes: this...
5Th
3ddd
$1
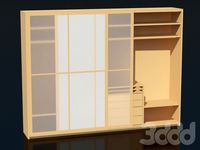
Molteni_gliss 5th
...molteni_gliss 5th
3ddd
шкаф molteni, модель gliss 5th (италия).
turbosquid
$4
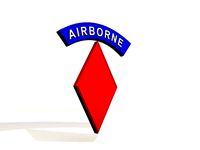
5th ID LRSD
... available on turbo squid, the world's leading provider of digital 3d models for visualization, films, television, and games.
turbosquid
$4
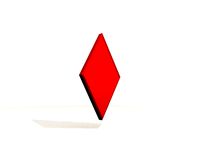
5th Infantry Division
... available on turbo squid, the world's leading provider of digital 3d models for visualization, films, television, and games.
turbosquid
$16
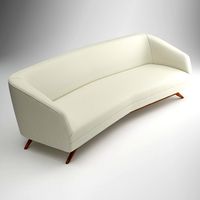
Kagan 5th Avenue Sofa
...model kagan 5th avenue sofa for download as max, obj, and fbx on turbosquid: 3d models for games, architecture, videos. (1500180)
3ddd
$1
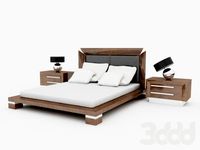
MALERBA. The 5th Avenue
...
mav-161 california size bed
см 231х245х115h
nightstand - mav-062 nightstand
см85х52х50h
turbosquid
$15
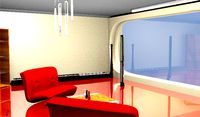
5th floor living room apartment
... available on turbo squid, the world's leading provider of digital 3d models for visualization, films, television, and games.
turbosquid
free
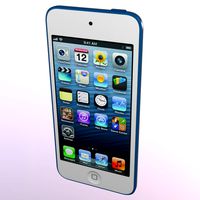
Apple iPod Touch 5th Generation
... available on turbo squid, the world's leading provider of digital 3d models for visualization, films, television, and games.
3ddd
$1
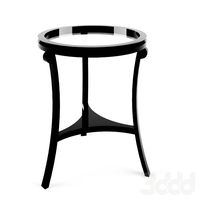
Bocadolobo, 5th . Side table Soho Collection
... круглый
5th . side table
soho collection
measures:
diameter: 50 cm (20 in.)
height: 60 cm (24 in.)
cg_studio
$50
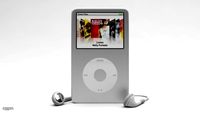
Apple Ipod Classic 5th Generation3d model
...3ds .lwo .max .obj - apple ipod classic 5th generation 3d model, royalty free license available, instant download after purchase.
turbosquid
$15
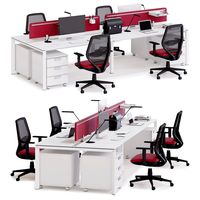
Office workspace LAS 5TH ELEMENT v3
...fice workspace las 5th element v3 for download as max and fbx on turbosquid: 3d models for games, architecture, videos. (1444722)
Gen
turbosquid
$15

gen
... available on turbo squid, the world's leading provider of digital 3d models for visualization, films, television, and games.
turbosquid
$2
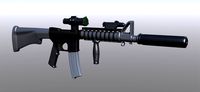
Gen. Rifle
...bosquid
royalty free 3d model gen. rifle for download as fbx on turbosquid: 3d models for games, architecture, videos. (1374075)
3d_export
$8
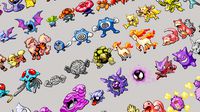
pokemon sprite voxel 1 gen
...pokemon sprite voxel 1 gen
3dexport
pokemon voxel 1 gen
turbosquid
$45

Chest Next-Gen
... available on turbo squid, the world's leading provider of digital 3d models for visualization, films, television, and games.
turbosquid
$39
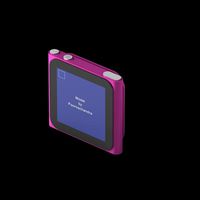
Nano 6th Gen
... available on turbo squid, the world's leading provider of digital 3d models for visualization, films, television, and games.
3d_export
$8
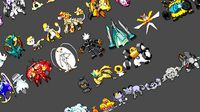
pokemon sprite voxel 7 gen
...pokemon sprite voxel 7 gen
3dexport
pokemon sprite voxel 7 gen
3d_export
$8
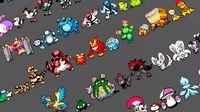
pokemon sprite voxel 5 gen
...pokemon sprite voxel 5 gen
3dexport
pokemon sprite voxel 5 gen
3d_export
$8
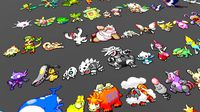
pokemon sprite voxel 3 gen
...pokemon sprite voxel 3 gen
3dexport
pokemon sprite voxel 3 gen
3d_export
$8
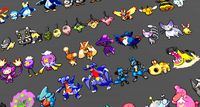
pokemon sprite voxel 4 gen
...pokemon sprite voxel 4 gen
3dexport
4 gen pokemon voxel sprites
3d_export
$8
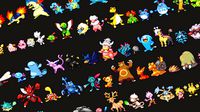
pokemon sprite voxel 2 gen
...pokemon sprite voxel 2 gen
3dexport
pokemon sprite voxel 2 gen
Makerbot
thingiverse
free
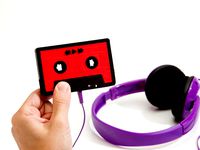
MakerBot Mixtape by MakerBot
...t.com/makerbot-mixtape.html
designed by john b., matt k. and john d.
a collaborative project with playbutton
www.playbutton.com
thingiverse
free
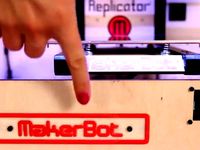
MakerBot Nameplate by MakerBot
...plicator. this was seen in episode 5 of season 2 of makerbot tv http://www.youtube.com/watch?v=k815gaeelw8
created by todd blatt
thingiverse
free
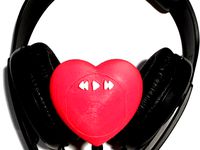
Makerbot Mixtape Heart by MakerBot
... about a makerbot mixtape in a heart!
made by using the makerbot mixtape negative file
designed by john briscella and matt kroner
thingiverse
free
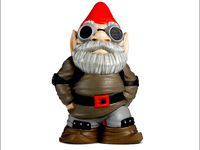
MakerBot Gnome by MakerBot
...at details that were not lost.
for more information on the makerbot digitizer desktop 3d scanner, visit makerbot.com/digitizer.
thingiverse
free
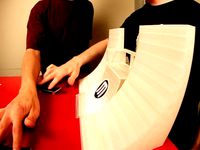
Makerbot Skate Park by MakerBot
...makerbot skate park by makerbot
thingiverse
a complete fingerboarding skate park.
thingiverse
free

MakerBot BotStep17 REVE by MakerBot
...esigned by harry mulliken.
this is part of the makerbot replicator, which you can find at http://www.thingiverse.com/thing:18813
thingiverse
free

Makerbot Mixtape Negative by MakerBot
...ngiverse
now your can make a makerbot mixtape out of almost any thing on thingiverse.
designed by john briscella and matt kroner
thingiverse
free
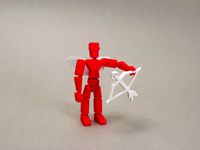
MakerBot Man Cupid by MakerBot
...piece at once and get moving parts right off the build plate.
available in the makerbot store gumball machine for a limited time!
thingiverse
free
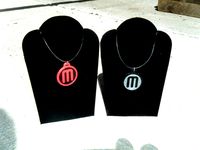
MakerBot Pendant by MakerBot
...39;t go wrong sporting this necklace! wear it with pride. both dualstrusion and one color models are available.
created by todd
thingiverse
free
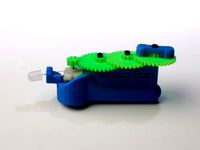
MakerBot Dynamo by MakerBot
...
and if a led not exciting enough for you, just think of all the other wonderful things you can power, one hand crank at a time.
Heated
3d_export
$5

heat
...heat
3dexport
heat tool
3ddd
$1
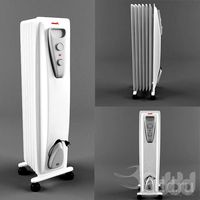
electric heating
...electric heating
3ddd
обогреватель
electric heating
3d_export
$6
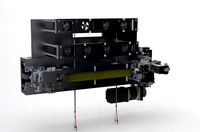
The heating module
...any questions also you can email to me. designed with solidworks 2017, render with keyshot **************************************
turbosquid
$2
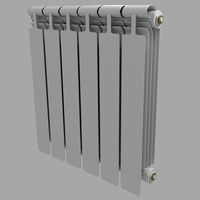
Heating Radiator
...
royalty free 3d model heating radiator for download as blend on turbosquid: 3d models for games, architecture, videos. (1561908)
3d_export
$35
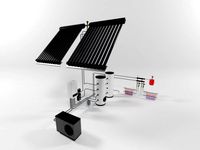
heating instalation with heat pump and solar system
...el , please contact me. before buying a model, you can try to download one of my free models and testing. thank you for watching.
turbosquid
$29
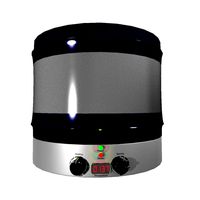
Heating Mantle
... available on turbo squid, the world's leading provider of digital 3d models for visualization, films, television, and games.
turbosquid
$25
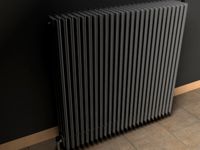
Heating Radiator
... available on turbo squid, the world's leading provider of digital 3d models for visualization, films, television, and games.
turbosquid
$20
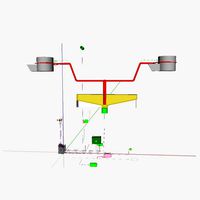
AT_airship_control_stand_(heated)
... available on turbo squid, the world's leading provider of digital 3d models for visualization, films, television, and games.
turbosquid
$20
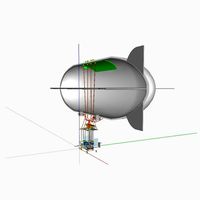
AT_airship_(heated)
... available on turbo squid, the world's leading provider of digital 3d models for visualization, films, television, and games.
turbosquid
$10
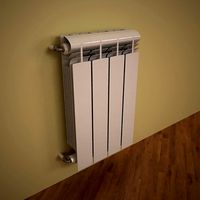
Heating radiator
... available on turbo squid, the world's leading provider of digital 3d models for visualization, films, television, and games.
Bed
3ddd
$1
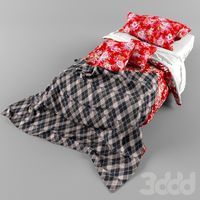
bed
...bed
3ddd
bed , постельное белье
bed
3ddd
$1
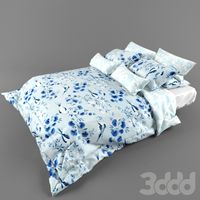
bed
...bed
3ddd
bed , постельное белье
bed
3ddd
$1
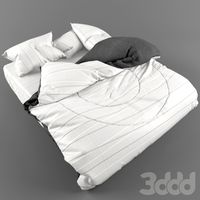
bed
...bed
3ddd
bed , постельное белье
bed
3ddd
$1
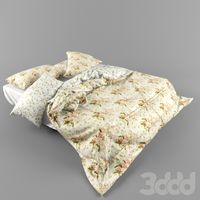
bed
...bed
3ddd
bed , постельное белье
bed
3ddd
$1
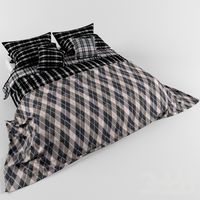
bed
...bed
3ddd
bed , постельное белье
bed
3ddd
$1
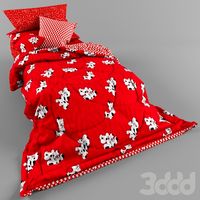
bed
...bed
3ddd
bed , постельное белье
bed
3ddd
free
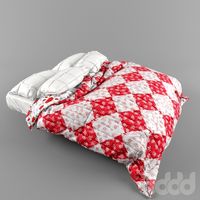
bed
...bed
3ddd
bed , постельное белье
bed
3ddd
free
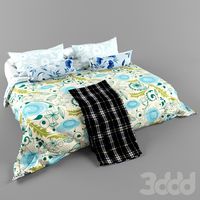
bed
...bed
3ddd
bed , постельное белье
bed
3ddd
$1
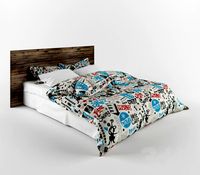
Bed
...bed
3ddd
bed , постельное белье , постель
bed
3d_export
$7
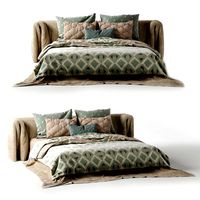
bed adairs bed
...rs bed
3dexport
bed adairs bed in modern style. if you want a smoother surface, please turn on turbosmooth in the modifier list.
design_connected
$27
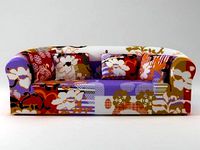
...print
designconnected
moroso print computer generated 3d model. designed by wanders, marcel.
3ddd
free
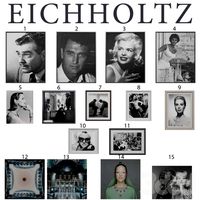
Eichholtz Prints
...- eichholtz print central station i
13 - eichholtz print central station ii
14 - eichholtz print marisa
15 - eichholtz print tish
3ddd
$1
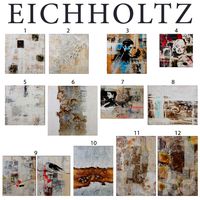
Eichholtz Prints
...print abstract - set of 2
10 - eichholtz print orange abstract
11 - eichholtz print buddha right
12 - eichholtz print buddha left
turbosquid
$1
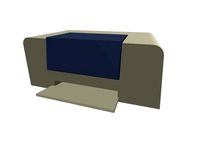
... available on turbo squid, the world's leading provider of digital 3d models for visualization, films, television, and games.
3ddd
free
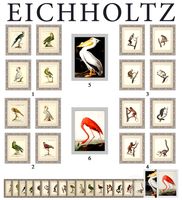
Eichholtz Prints
...of 4
2 - print dunbar 2 set of 4
3 - print guadeloupe 1 set of 4
4 - print guadeloupe 2 set of 4
5 - print giles
6 - print trett
3ddd
$1
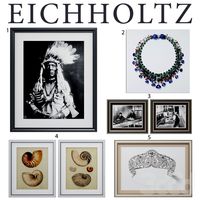
Eichholtz Prints
...nt tutti frutti
3 - eichholtz prints watson - set of 2
4 - eichholtz prints antique nautilus - set of 2
5 - eichholtz print tiara
3d_export
$5
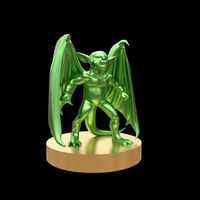
Monster for printing
...monster for printing
3dexport
monster 3d model printing
3ddd
free
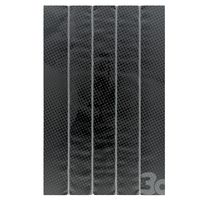
printed rug
...printed rug
3ddd
ковер
very creative printed rug
3ddd
free
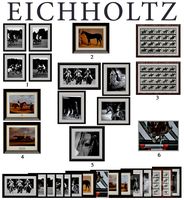
Eichholtz Prints
...иал: бумага
габариты (вхш): 72 x 62 см
описание: print sweetmeat - постер в деревянной раме.
3 - prints varsity set of 2
арти
3ddd
free
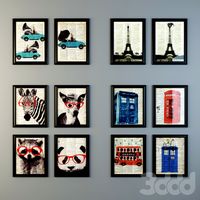
Art Print Posters
...art print posters
3ddd
прованс
art print posters by patrician prints