Thingiverse

Kodama Trinus E3D v6 mod v2 by vat_pom
by Thingiverse
Last crawled date: 3 years ago
#######################################################################
This is version 2 of the mod. Version 1 can be found here http://www.thingiverse.com/thing:2186559.
Differences between V2 and V1
V2 supports also the new bigger heat block of the E3D v6 and not only the small (old) one (v6 lite is also supported)
V2 has improved "air management" (less air is directed to the heat block and baseplate, important when printed in PLA), up to about 220 °C there is no temperature drop when using the fan close to the bed.
V2 has a stiffer baseplate, helps with higher temps if printed in PLA
V2 the fan duct has a nice snap fit, which fixes the fan duct (it still can be rotated in maintenance position)
V2 moves the nozzle about 3 mm up in z-direction
...and there are some minor changes
#######################################################################
UPDATE 28.04.2017: I have added two fan ducts:
"fan_duct_v3" is my last iterration step. It provides a better view to the 1st layer, is smaller (prints quicker) and doesn´t have the problem all circular fan ducts have. The problem that when the nozzle is close to the bed (or above a horizontal surface), the air is pushed to the nozzle from all directions, but cannot get there because it blocks itself.
Compared to the circular versions, it is also much less sensitive to overheating.
"fan_duct_PLA_v3", same as "fan_duct_v3" but only the air jets/nozzles are cut back, because when testing, i found out, that when printed in PLA in the long term the air jets curled up. So if you want to print it in PLA, i suggest this version.
Both fit for the e3d v6 old and new as well as lite version.
#######################################################################
There is no need to talk about the E3D v6, it is a state of the art reference hot end, you won´t get a better one.
What is the use of the mod, what are the differences compared to the trinus hot end:
Even the E3D v6 has a PTFE inliner, it is a full metal hot end and at the time being only the trinus firmware limits its max temperature.
No PTFE degradation, no changing extrusion problems over time
No unstable extrusion/retraction problems, printing speed is only limited by trinus resonance problems and not by the hot/cold end extrusion capacity, I print PETG infill at 230 °C 0.2mm and 80-100 mm/s, before the mod I struggled to achieve 20 mm/s without problems, 80-100 mm/s will only make sense for some prints on such a small build volume, but it makes a huge difference if you print at e.g. 60-80 mm/s in average than compared to <20 mm/s.
Reliable consistent extrusion, not sometime it works and sometimes not
Much quicker heat up time, better temperature control after PID autotune,
with same heater cartridge higher printing temperatures are possible –but right now they are anyhow limited by the firmware
If the fan blows fully to the nozzle, the temperature drops, but much less
At same printing speeds no bleeding edges, bleeding edges occur much later at much higher printing speeds
If you need spare parts you can get them everywhere (nozzles, heat block, heat break….), quick and cheap, no need to wait for Kodama
no jams/clogging (it is still possible depending on what you do, but only if you do something wrong and not because it is a misconstruction)
much better fan duct (evenness of air flow)
reduction of moving masses
more easy maintenance, no black box which blocks sight
#######################################################################
What you need:
E3d v6 1.75mm Universal with 100k thermistor.
The mod v2 supports the new and the old E3D v6, that means with the small heat block and with the new bigger heat block sold since mid 2016.
The thermistor, as well as the heater cartridge fits for the trinus.
"Clones": An often used name is e.g. "E3D v6 1.75 long distance with PTFE"
E3D v6 clones use the old/small heat block, which is fine and no disadvantage at all. There are 1.75 mm E3D v6 clones available without any PTFE tubing at all - don´t use them (they will not work for PLA at all) !
There is only one part, where quality can be an issue - the heatbreak.
There are clones available with PTFE tubes on both sides of the heatbreak (throat) and others only have a 4.1 mm hole for the 4/2 mm PTFE tube like the genuine version. (and some have no PTFE at all in the heat break, don´t use them !!!).
In principle both version work, but if you want to use the full E3D capacity (e.g. printing PETG, or just best quality), you should look for the heat breaks which have the PTFE tube only at the cold side (4.1 mm bore), there are often called
"E3D v6 1.75 mm full metal throat", although they have the PTFE on one side. The reason why the clones are most often sold with PTFE on both sides is the roughness. PTFE is cheap and foolproof smooth but it is expensive to drill a smooth hole in metal. There are suppliers which sell "smooth full metal throats". Another way is to buy only the genuine E3D v6 heat break from E3D and cold sink and heat block from china.
For assembly see here https://wiki.e3d-online.com/wiki/E3D-v6_Assembly#HotSide
E3D cold end fan including duct (should be part of the E3D v6 order) or you use the existing 40mm trinus cold end fan, which i recommend
PTFE tube 4/2 mm, some cms, in principle it even works without when printing higher glass transition temperature materials and using the trinus 40 mm fan on the cold end, but i don´t recommend without.
the Thingiverse 3D printed parts shown in the pictures above.
Optional parts
Thermal paste to use in between the E3D heatbreak and the round cold end cooling body
Cardboard or Insulation cotton to insulate the nozzle and as air shield
Spare parts, e.g. if I change the nozzle for a print, i just change the whole hot end, because the clones are anyhow very cheap
#######################################################################
assembly:
remove/disassemble the trinus hot end cold end, strip it down until only the alu-block and mounted extruder remains, according to https://www.kodamaforums.com/phpBB3/viewtopic.php?f=22&t=1721 remove parts L, H, M, N. All other parts shown on the picture can remain.
remove also the plate which is screwed onto the x-carriage. The part "E3D_fan_extruder_mounting_plate" gets directly screwed to the x-carriage
mount the part "filament_guide_extruder" and the alu-extruder block. Use the 2 existing worm screws to fix it
prepare the 4/2mm PTFE tube and cut it to about 49 mm, push the PTFE tube into the assembled E3D v6, you will need to push it really "hard" to get it into the heatbreak of the E3D. To other end of the PTFE tube is inserted into the "filament path" of the alu/extruder and by that pushed into the end of the part "filament_guide_extruder". If necessary adjust the length of the PTFE tube, but 49 mm should fit about +-1mm. If the 49mm
seems to be much too long, then you probably didn´t push it into the heatbreak - push harder;)
The E3D including the PTFE tube should now be fitted to the extruder alu-block.
screw the extruder block to the part "E3D_fan_extruder_mounting_plate"
press the E3D into its snap fit, the E3D snap fit is quite tight, maybe you need to put it to a table and press it into it. Be careful and look which side of the "E3D bracket" needs to be up.
mount the fan duct including the 50mm trinus fan to the "E3D_fan_extruder_mounting_plate" using the hole which fixes the fan duct to the "E3D_fan_extruder_mounting_plate"
use the upper hole to screw the other end of the 50mm fan to the "E3D_fan_extruder_mounting_plate"
rotate the fan duct to its end position and snap it onto the 50mm fan
check the distance between fan duct and bed, when the nozzle touches the bed, it should be exactly 2mm
mount the cold end fan, if you want to use the trinus 40mm fan, you have to print the part "trinus_40mm_cold_end_fan_mount_E3D"
use the holes for the zip ties to zip cables as you like
the removed screws of the trinus can be used, you don´t need additional screws, the M3 small screws are used to mount the extruder/alu-block, the bigger M4 screws to mount the 50mm fan and the M3 worm screws are used to fix the filament guide
you will need to rewire connectors of the E3D 30mm cold end fan, or better use the 40mm trinus fan ("trinus_40mm_cold_end_fan_mount_E3D")
######################################################################
IMPORTANT:
Before you use the E3D v6, you need to change the PID-tuning with gcode commands, e.g. with M106 S255; M303 S200; see here http://www.kodamaforums.com/phpBB3/viewtopic.php?t=1762
readjust your z-end stop
######################################################################
Because the trinus has a 40mm cold end fan, it is an advantage to use it as E3D cold end fan instead of the standard E3D 30mm cold end fan e.g. --> part "trinus_40mm_cold_end_fan_mount_E3D"
######################################################################
Maintenance position:
In order ot change nozzles and so on, the fan duct can be easily rotated by 180 ° to give free access to the nozzle/heater block, see very last right picture above.
######################################################################
3D printed Parts:
all parts can be printed without supports, i used 3 outlines and 15 % infill, works with 0.4 and 0.5 mm nozzle and various filaments
"Filament_guide_extruder"
Optional, in principle stiff filaments work also without, but there is no disadvantage to use it
can be printed in every filament
i would prefer 0.1 mm layer height, but it works also with 0.2 mm
"E3D_extruder_fan_mounting_plate"
PLA might not work, or only for low printing temperatures (200-210°C), at least PETG, BDP, ABS, ASA or filaments with high heat resistance are much better
0.1 -0.2 mm layer height
If you use PLA increase number of outer lines to 4/5 and solid top/bottom layers to e.g. 5* 0.2 mm
Infill about >= 15%, according to number of top layers and material
"E3D_bracket"
Use filament with at least same heat resistance as 3
0.1 -0.2 mm layer height
It is the only part which could be printed using supports, I don´t use supports, this gives some unwanted bridges on the horizontal overhang, which can be removed easily afterward, so no supports needed
fan duct
Use a filament with the highest possible heat resistance, PLA works for about 210 °C and 50-60°C HTB fine, but higher temperatures will deform it. I use extrudr BDP which survives about 115 °C without problems and can be easily printed at low temperatures, without heated bed and enclosure
The V2 fan duct blocks the air upwards to the heater block by itself better than V1, so this has improved.
the fan duct design was optimized for evenness of airflow from all directions, design verified with CFD simulation, the target was not to maximize air flow, because this also can disturb the print, it should direct the cold air exactly where it is needed, therefore much less airflow is needed compared to not circular fan ducts
The ducts bedside has massive overhangs. They won´t print perfect, but that doesn´t matter. The duct uses the coanda effect to direct the air to the nozzle. so if the overhangs are rough, it doesn´t matter at all and nobody sees it....
trinus 40mm cold end fan
The E3D should come with a 30 mm cold end fan, which is fine, but the 40 mm trinus fan will provide even better cooling (sharper transition from cold to hot), if you want to use the trinus fan print the part "trinus_40mm_cold_end_fan_mount_E3D". Another advantage of the 40mm trinus fan is, that the electric connectors will fit.
insulation/heat block (not 3Dprinted), if you notice that the fan duct doesn´t survive because the lower part "melts/deforms" (especially PLA might melt where the heat block screw is), just put a cardboard or insulation cotton between the fan duct and the heat block
#######################################################################
Outlook and improvement potential
Optimize air management further
Improve sight to 1st layer --> modify fan duct further, try different (smaller) ducts
Maybe reduce weight further by exchanging the extruder block with 3D printed parts
If some wants add a casin
#######################################################################
If one needs some small mods of the mod, i could probably change it.
This is version 2 of the mod. Version 1 can be found here http://www.thingiverse.com/thing:2186559.
Differences between V2 and V1
V2 supports also the new bigger heat block of the E3D v6 and not only the small (old) one (v6 lite is also supported)
V2 has improved "air management" (less air is directed to the heat block and baseplate, important when printed in PLA), up to about 220 °C there is no temperature drop when using the fan close to the bed.
V2 has a stiffer baseplate, helps with higher temps if printed in PLA
V2 the fan duct has a nice snap fit, which fixes the fan duct (it still can be rotated in maintenance position)
V2 moves the nozzle about 3 mm up in z-direction
...and there are some minor changes
#######################################################################
UPDATE 28.04.2017: I have added two fan ducts:
"fan_duct_v3" is my last iterration step. It provides a better view to the 1st layer, is smaller (prints quicker) and doesn´t have the problem all circular fan ducts have. The problem that when the nozzle is close to the bed (or above a horizontal surface), the air is pushed to the nozzle from all directions, but cannot get there because it blocks itself.
Compared to the circular versions, it is also much less sensitive to overheating.
"fan_duct_PLA_v3", same as "fan_duct_v3" but only the air jets/nozzles are cut back, because when testing, i found out, that when printed in PLA in the long term the air jets curled up. So if you want to print it in PLA, i suggest this version.
Both fit for the e3d v6 old and new as well as lite version.
#######################################################################
There is no need to talk about the E3D v6, it is a state of the art reference hot end, you won´t get a better one.
What is the use of the mod, what are the differences compared to the trinus hot end:
Even the E3D v6 has a PTFE inliner, it is a full metal hot end and at the time being only the trinus firmware limits its max temperature.
No PTFE degradation, no changing extrusion problems over time
No unstable extrusion/retraction problems, printing speed is only limited by trinus resonance problems and not by the hot/cold end extrusion capacity, I print PETG infill at 230 °C 0.2mm and 80-100 mm/s, before the mod I struggled to achieve 20 mm/s without problems, 80-100 mm/s will only make sense for some prints on such a small build volume, but it makes a huge difference if you print at e.g. 60-80 mm/s in average than compared to <20 mm/s.
Reliable consistent extrusion, not sometime it works and sometimes not
Much quicker heat up time, better temperature control after PID autotune,
with same heater cartridge higher printing temperatures are possible –but right now they are anyhow limited by the firmware
If the fan blows fully to the nozzle, the temperature drops, but much less
At same printing speeds no bleeding edges, bleeding edges occur much later at much higher printing speeds
If you need spare parts you can get them everywhere (nozzles, heat block, heat break….), quick and cheap, no need to wait for Kodama
no jams/clogging (it is still possible depending on what you do, but only if you do something wrong and not because it is a misconstruction)
much better fan duct (evenness of air flow)
reduction of moving masses
more easy maintenance, no black box which blocks sight
#######################################################################
What you need:
E3d v6 1.75mm Universal with 100k thermistor.
The mod v2 supports the new and the old E3D v6, that means with the small heat block and with the new bigger heat block sold since mid 2016.
The thermistor, as well as the heater cartridge fits for the trinus.
"Clones": An often used name is e.g. "E3D v6 1.75 long distance with PTFE"
E3D v6 clones use the old/small heat block, which is fine and no disadvantage at all. There are 1.75 mm E3D v6 clones available without any PTFE tubing at all - don´t use them (they will not work for PLA at all) !
There is only one part, where quality can be an issue - the heatbreak.
There are clones available with PTFE tubes on both sides of the heatbreak (throat) and others only have a 4.1 mm hole for the 4/2 mm PTFE tube like the genuine version. (and some have no PTFE at all in the heat break, don´t use them !!!).
In principle both version work, but if you want to use the full E3D capacity (e.g. printing PETG, or just best quality), you should look for the heat breaks which have the PTFE tube only at the cold side (4.1 mm bore), there are often called
"E3D v6 1.75 mm full metal throat", although they have the PTFE on one side. The reason why the clones are most often sold with PTFE on both sides is the roughness. PTFE is cheap and foolproof smooth but it is expensive to drill a smooth hole in metal. There are suppliers which sell "smooth full metal throats". Another way is to buy only the genuine E3D v6 heat break from E3D and cold sink and heat block from china.
For assembly see here https://wiki.e3d-online.com/wiki/E3D-v6_Assembly#HotSide
E3D cold end fan including duct (should be part of the E3D v6 order) or you use the existing 40mm trinus cold end fan, which i recommend
PTFE tube 4/2 mm, some cms, in principle it even works without when printing higher glass transition temperature materials and using the trinus 40 mm fan on the cold end, but i don´t recommend without.
the Thingiverse 3D printed parts shown in the pictures above.
Optional parts
Thermal paste to use in between the E3D heatbreak and the round cold end cooling body
Cardboard or Insulation cotton to insulate the nozzle and as air shield
Spare parts, e.g. if I change the nozzle for a print, i just change the whole hot end, because the clones are anyhow very cheap
#######################################################################
assembly:
remove/disassemble the trinus hot end cold end, strip it down until only the alu-block and mounted extruder remains, according to https://www.kodamaforums.com/phpBB3/viewtopic.php?f=22&t=1721 remove parts L, H, M, N. All other parts shown on the picture can remain.
remove also the plate which is screwed onto the x-carriage. The part "E3D_fan_extruder_mounting_plate" gets directly screwed to the x-carriage
mount the part "filament_guide_extruder" and the alu-extruder block. Use the 2 existing worm screws to fix it
prepare the 4/2mm PTFE tube and cut it to about 49 mm, push the PTFE tube into the assembled E3D v6, you will need to push it really "hard" to get it into the heatbreak of the E3D. To other end of the PTFE tube is inserted into the "filament path" of the alu/extruder and by that pushed into the end of the part "filament_guide_extruder". If necessary adjust the length of the PTFE tube, but 49 mm should fit about +-1mm. If the 49mm
seems to be much too long, then you probably didn´t push it into the heatbreak - push harder;)
The E3D including the PTFE tube should now be fitted to the extruder alu-block.
screw the extruder block to the part "E3D_fan_extruder_mounting_plate"
press the E3D into its snap fit, the E3D snap fit is quite tight, maybe you need to put it to a table and press it into it. Be careful and look which side of the "E3D bracket" needs to be up.
mount the fan duct including the 50mm trinus fan to the "E3D_fan_extruder_mounting_plate" using the hole which fixes the fan duct to the "E3D_fan_extruder_mounting_plate"
use the upper hole to screw the other end of the 50mm fan to the "E3D_fan_extruder_mounting_plate"
rotate the fan duct to its end position and snap it onto the 50mm fan
check the distance between fan duct and bed, when the nozzle touches the bed, it should be exactly 2mm
mount the cold end fan, if you want to use the trinus 40mm fan, you have to print the part "trinus_40mm_cold_end_fan_mount_E3D"
use the holes for the zip ties to zip cables as you like
the removed screws of the trinus can be used, you don´t need additional screws, the M3 small screws are used to mount the extruder/alu-block, the bigger M4 screws to mount the 50mm fan and the M3 worm screws are used to fix the filament guide
you will need to rewire connectors of the E3D 30mm cold end fan, or better use the 40mm trinus fan ("trinus_40mm_cold_end_fan_mount_E3D")
######################################################################
IMPORTANT:
Before you use the E3D v6, you need to change the PID-tuning with gcode commands, e.g. with M106 S255; M303 S200; see here http://www.kodamaforums.com/phpBB3/viewtopic.php?t=1762
readjust your z-end stop
######################################################################
Because the trinus has a 40mm cold end fan, it is an advantage to use it as E3D cold end fan instead of the standard E3D 30mm cold end fan e.g. --> part "trinus_40mm_cold_end_fan_mount_E3D"
######################################################################
Maintenance position:
In order ot change nozzles and so on, the fan duct can be easily rotated by 180 ° to give free access to the nozzle/heater block, see very last right picture above.
######################################################################
3D printed Parts:
all parts can be printed without supports, i used 3 outlines and 15 % infill, works with 0.4 and 0.5 mm nozzle and various filaments
"Filament_guide_extruder"
Optional, in principle stiff filaments work also without, but there is no disadvantage to use it
can be printed in every filament
i would prefer 0.1 mm layer height, but it works also with 0.2 mm
"E3D_extruder_fan_mounting_plate"
PLA might not work, or only for low printing temperatures (200-210°C), at least PETG, BDP, ABS, ASA or filaments with high heat resistance are much better
0.1 -0.2 mm layer height
If you use PLA increase number of outer lines to 4/5 and solid top/bottom layers to e.g. 5* 0.2 mm
Infill about >= 15%, according to number of top layers and material
"E3D_bracket"
Use filament with at least same heat resistance as 3
0.1 -0.2 mm layer height
It is the only part which could be printed using supports, I don´t use supports, this gives some unwanted bridges on the horizontal overhang, which can be removed easily afterward, so no supports needed
fan duct
Use a filament with the highest possible heat resistance, PLA works for about 210 °C and 50-60°C HTB fine, but higher temperatures will deform it. I use extrudr BDP which survives about 115 °C without problems and can be easily printed at low temperatures, without heated bed and enclosure
The V2 fan duct blocks the air upwards to the heater block by itself better than V1, so this has improved.
the fan duct design was optimized for evenness of airflow from all directions, design verified with CFD simulation, the target was not to maximize air flow, because this also can disturb the print, it should direct the cold air exactly where it is needed, therefore much less airflow is needed compared to not circular fan ducts
The ducts bedside has massive overhangs. They won´t print perfect, but that doesn´t matter. The duct uses the coanda effect to direct the air to the nozzle. so if the overhangs are rough, it doesn´t matter at all and nobody sees it....
trinus 40mm cold end fan
The E3D should come with a 30 mm cold end fan, which is fine, but the 40 mm trinus fan will provide even better cooling (sharper transition from cold to hot), if you want to use the trinus fan print the part "trinus_40mm_cold_end_fan_mount_E3D". Another advantage of the 40mm trinus fan is, that the electric connectors will fit.
insulation/heat block (not 3Dprinted), if you notice that the fan duct doesn´t survive because the lower part "melts/deforms" (especially PLA might melt where the heat block screw is), just put a cardboard or insulation cotton between the fan duct and the heat block
#######################################################################
Outlook and improvement potential
Optimize air management further
Improve sight to 1st layer --> modify fan duct further, try different (smaller) ducts
Maybe reduce weight further by exchanging the extruder block with 3D printed parts
If some wants add a casin
#######################################################################
If one needs some small mods of the mod, i could probably change it.
Similar models
thingiverse
free
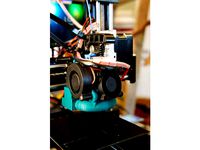
Kodama Trinus E3D v6 mod v1 by vat_pom
...############################################################
if one needs some small mods of the mod, i could probably change it.
thingiverse
free
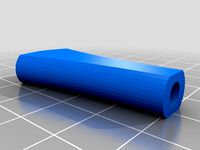
Dual Print Switch, Y-Piece, One Nozzle by Tonda93
...piece for dual print with one hotend. works best with ptfe tube up to the nozzle like the e3d v6 with heatbreak with 4.1 mm bore.
thingiverse
free
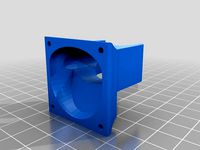
Raise3D E3D v6 adapter 35mm fan duct by Firesped
...e raise3d n-series printers.
so far35mm fan duct for cold end only35mm fan duct with "always on" volcano hotend cooling
thingiverse
free
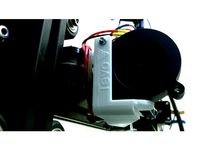
E3D v6 Upgrades (Tevo Tarantula) 5015 fan by arun2118
.... if you have oem v6 and have followed their assembly procedure please reprint extended version and let us know.
thank you "
thingiverse
free
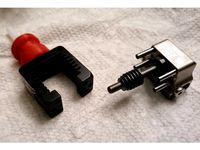
Mosquito / Dragon Hotend E3D V6 Mount by Superuser23
...uality is amazing.
use a drop of superglue in the little side holes of the mount to ensure there is no movement of the ptfe tube.
thingiverse
free
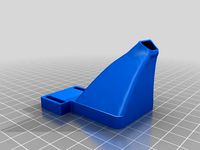
Lulzbot TAZ Extended / Adjustable Nozzle Fan Duct for e3D / hexagon hot ends by SuperSolid_3D
...re you can slide it up and down for adjustment, and doesn't require heat-set insert nuts for mounting the fan with m3 screws.
thingiverse
free
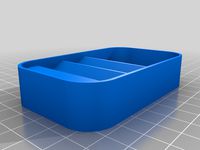
Volcano Nozzle Organizer
... it has 10 slots for nozzles and a small empty area that you can then store other hot end parts in (ptfe tubes, heatbreaks, etc).
thingiverse
free
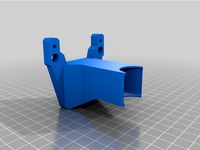
SK-Go invisible hotend cooling duct e3d v6 (note: Precision Piezo users only) by superhans
...onto the heat sink and heater block.
the matching part cooling fan duct from the photo: https://www.thingiverse.com/thing:4700411
thingiverse
free
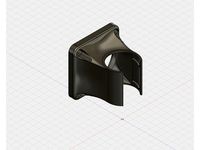
E3D air duct by Intector
...lastics which can be ordered here:https://www.mcmaster.com/#94180a351/=1crfn7g
the whole thing is a test part for my new printer.
thingiverse
free
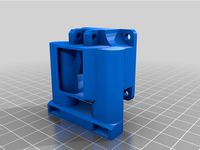
Part Cooling Fan Duct 4 Wades Direct with E3D V6 by Mohvee
... is designed to cool both heat break as well as printed part. it fits on the front mount of a standard wades geared extruder body
Kodama
3ddd
$1
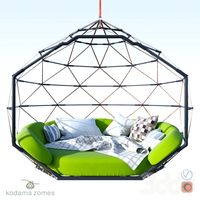
Kodama_Zomes_Pod
...ray додаются библиотекой материалов, радии экономии размера архива.
в модели два варианта монтажа, отдельно стоячие и подвесное.
thingiverse
free
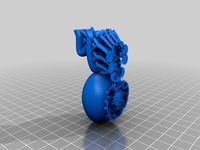
Kodama wiht supports
...kodama wiht supports
thingiverse
kodama supports
thingiverse
free
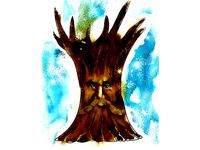
The Kodama Tree by Kodama3D
...o the incredible new ideas and inventions the future will bring in layer by layer, like the rings of the trees kodamas reside in.
thingiverse
free
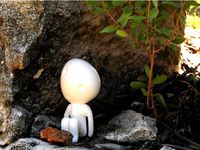
KODAMA by ccamp104
...a by ccamp104
thingiverse
kodama forest spirit from studio ghibli's princess mononoke. sits flush to the ground when printed
thingiverse
free

Kodama Sitting by LadyDretza
... first scratch design of the kodama in meshmixer.
finished model, painted with stone paint, eyes filled in with permanent marker.
thingiverse
free
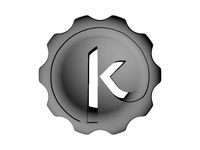
Kodama Makercoin by Cbturtle2
...
makercoin with the kodama logo on it. feel free to print as you wish, just upload a photo for everyone to see. happy printing!!!
thingiverse
free
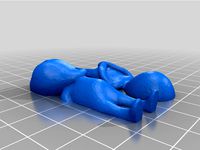
kodama by MisterSister
...kodama by mistersister
thingiverse
sliced and shrunk add mason jar solar light
thingiverse
free
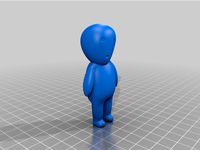
Kodama Forest Spirit by SpaceLord87
...est spirit by spacelord87
thingiverse
kodama forest spirit from princess mononoke. sculpted in zbrush. one file includes a base.
thingiverse
free
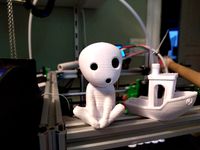
Kodama mashup
...kodama mashup
thingiverse
lzys/timfous head on dretzas body. also slightly re-sculpted.
does need support
thingiverse
free
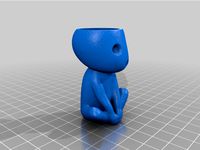
Kodama Planter by kleenecks
...kodama planter by kleenecks
thingiverse
remixed to add a well for your favorite succulent.
Trinus
thingiverse
free

Panowin / Trinus enclosure by vaudered
...panowin / trinus enclosure by vaudered
thingiverse
panowin , trinus enclosure
thingiverse
free
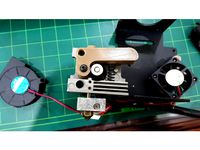
Trinus Extruder Handle by kebs37th
...trinus extruder handle by kebs37th
thingiverse
trinus extruder handle ~
thingiverse
free
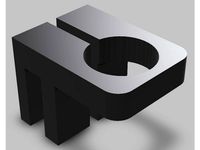
Trinus filament guide by Kullamannen
...trinus filament guide by kullamannen
thingiverse
filament guide for the kodama trinus printer.
thingiverse
free
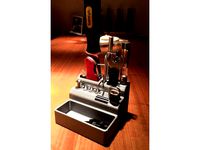
Trinus desktop tool station by BeerPercussion
...trinus desktop tool station by beerpercussion
thingiverse
tool station for kodama trinus essentials.
thingiverse
free
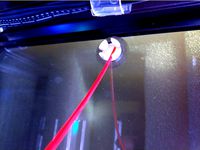
TRINUS filament hole cover by SheepsFeaTheR
...trinus filament hole cover by sheepsfeather
thingiverse
kodama trinus filament hole cover
thingiverse
free
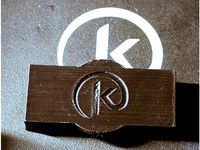
Trinus Rail Bearing Cover by Boyd84
...trinus rail bearing cover by boyd84
thingiverse
simple dust cover for the ends of the trinus rails.
thingiverse
free
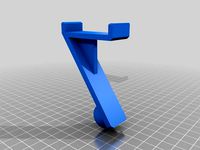
Spoleholder Ø55 Trinus 250/750g by Aladeath2000
...spoleholder ø55 trinus 250/750g by aladeath2000
thingiverse
spoleholder for trinus 3d.
thingiverse
free
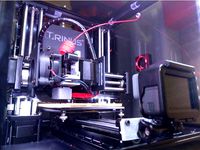
Trinus Gopro center mount by SheepsFeaTheR
... gopro center mount by sheepsfeather
thingiverse
trinus gopro light center mount
can be installed without removing the enclosure
thingiverse
free
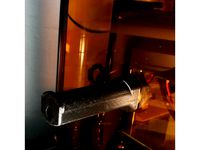
Kodama Trinus Enclosure Spool Holder by ark19
...kodama trinus enclosure spool holder by ark19
thingiverse
this is a spool holder for the kodama trinus enclosure.
thingiverse
free
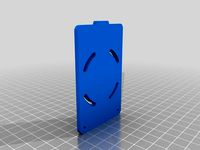
Trinus Dial Indicator by SgtSiff
...unt for the trinus 3d printer to allow accurate bed levelling.
remove back plate from dial and use screws to affix to this plate.
Pom
3ddd
free
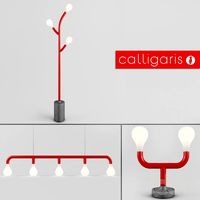
POM POM
...pom "table lamps"
article: cs/8024-t
model: pom pom "suspension lamps"
article: cs/8024-s
www.calligaris.com
turbosquid
$7
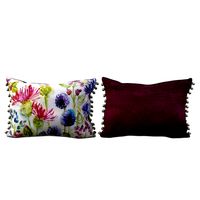
Voyage Cushion - Thistles (Pom Pom Pillow)
... available on turbo squid, the world's leading provider of digital 3d models for visualization, films, television, and games.
3d_export
$10
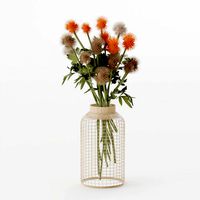
Roland Pom Pom Chrysanthemum Flower
...~ 100,000 model parts: 1 texture format: .png .jpg resolution: 1024*1024 pbr in substance painter formats: .obj .gltf .fbx .blend
turbosquid
$20
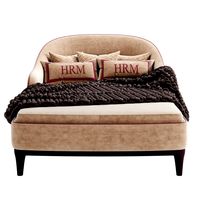
Atelierlilu pom pon
... model atelier lilu pom pon for download as max, obj, and fbx on turbosquid: 3d models for games, architecture, videos. (1455870)
3ddd
free
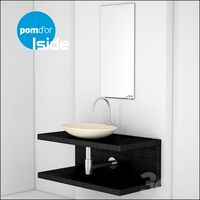
Pom'dor / Iside
...pom'dor. изготавливается из шпона дуба цвета венге. смеситель немецкой фабрики dornbracht. все текстуры и материалы в архиве.
3d_export
$10
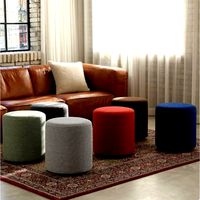
Pom Pom Fabric Round Stool
...xture format: .png .jpg<br>resolution: 1024*1024<br>pbr in substance painter<br>formats: .obj .gltf .fbx .blend
3ddd
free
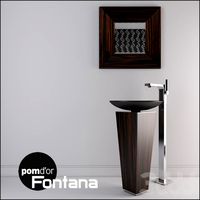
Pom'dor / Fontana
...овина из композита. напольный смеситель немецкой фабрики dornbracht (точную коллекцию не вспомню). материалы и текстуры в архиве.
3ddd
$1
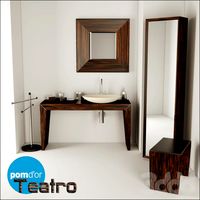
Pom'Dor / Teatro
... коллекции к2, аксессуары на столешнице коллекция iside фабрики pom'dor. раковина из композита на основе тригидрата алюминия.
3ddd
free
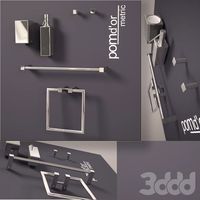
POM'dor
...othbrush holder
- полотенцедержатель 38.10.40.002 chrome towel rail 40
- кольцо-полотенцедержатель 38.20.05.002 chrome towel ring
3ddd
$1
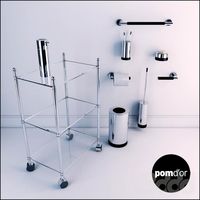
Pom'Dor аксессуары - K2, Dina, Micra
...е предметы из коллекции к2, этажерка коллекции dina, а дозатор на этажерке из коллекции micra. материалы и текстуры присутствуют.
Vat
turbosquid
$49
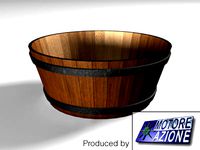
vat
... available on turbo squid, the world's leading provider of digital 3d models for visualization, films, television, and games.
turbosquid
$5
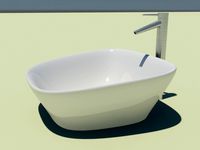
vat
... available on turbo squid, the world's leading provider of digital 3d models for visualization, films, television, and games.
turbosquid
$19
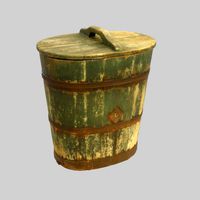
Wooden Vat Closed
...y free 3d model wooden vat closed for download as max and obj on turbosquid: 3d models for games, architecture, videos. (1197266)
turbosquid
$19
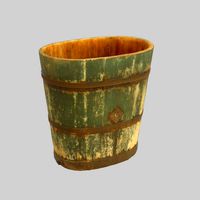
Wooden Vat 03
...yalty free 3d model wooden vat 03 for download as max and obj on turbosquid: 3d models for games, architecture, videos. (1197209)
turbosquid
$19
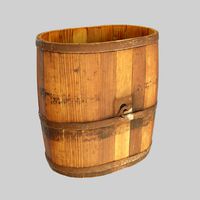
Wooden Vat 02
...yalty free 3d model wooden vat 02 for download as max and obj on turbosquid: 3d models for games, architecture, videos. (1197207)
turbosquid
$280
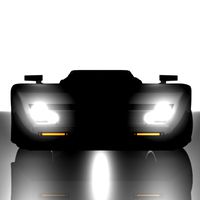
VAT RASER 02.jpg
... available on turbo squid, the world's leading provider of digital 3d models for visualization, films, television, and games.
turbosquid
$265
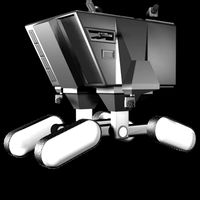
VAT SP 07.jpg
... available on turbo squid, the world's leading provider of digital 3d models for visualization, films, television, and games.
turbosquid
$180
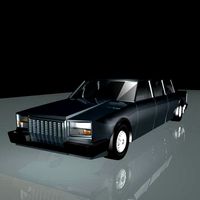
VAT LUX 02.jpg
... available on turbo squid, the world's leading provider of digital 3d models for visualization, films, television, and games.
turbosquid
$2
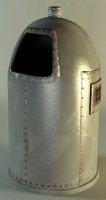
Large Cartoony Oil Vat
... available on turbo squid, the world's leading provider of digital 3d models for visualization, films, television, and games.
turbosquid
$3
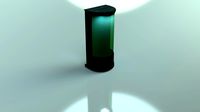
Sci-fi cloning vats
...cloning vats for download as 3ds, obj, wrl, x, fbx, and blend on turbosquid: 3d models for games, architecture, videos. (1290168)
E3D
turbosquid
$23
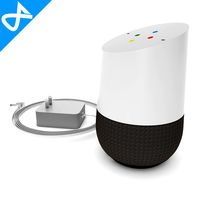
E3D - Google Home
... 3d model e3d - google home for download as max, obj, and c4d on turbosquid: 3d models for games, architecture, videos. (1192509)
cg_studio
free
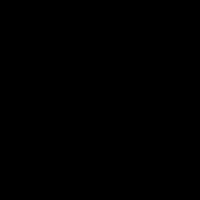
e3d model
...e3d model
cgstudio
- e 3d model, royalty free license available, instant download after purchase.
turbosquid
$2
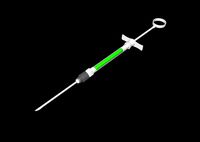
Syringe C4D (E3D Ready)
...lty free 3d model syringe c4d (e3d ready) for download as c4d on turbosquid: 3d models for games, architecture, videos. (1336720)
turbosquid
$12
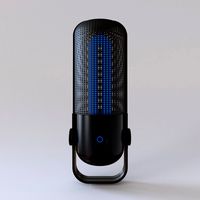
Microphone USB E3D and C4D
...ree 3d model microphone usb e3d & c4d for download as c4d on turbosquid: 3d models for games, architecture, videos. (1568216)
turbosquid
$29
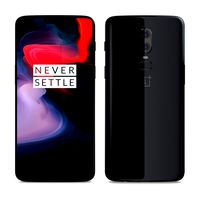
E3D - OnePlus 6 Black
...model e3d - oneplus 6 black for download as max, obj, and c4d on turbosquid: 3d models for games, architecture, videos. (1358534)
turbosquid
$29
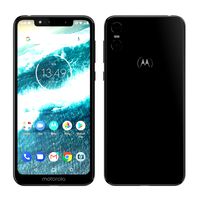
E3D - Motorola One 2018
...del e3d - motorola one 2018 for download as max, obj, and c4d on turbosquid: 3d models for games, architecture, videos. (1358533)
turbosquid
$29
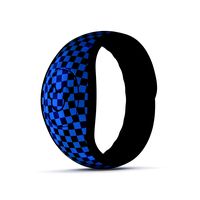
E3D - Disney MagicBands 2
...l e3d - disney magicbands 2 for download as max, obj, and c4d on turbosquid: 3d models for games, architecture, videos. (1355515)
turbosquid
$29

E3D - Samsung Z4 Smartphone
...e3d - samsung z4 smartphone for download as max, obj, and c4d on turbosquid: 3d models for games, architecture, videos. (1182179)
turbosquid
$23
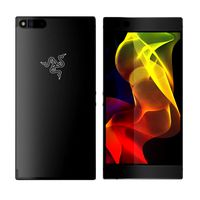
E3D - Razer Phone model
...del e3d - razer phone model for download as max, obj, and c4d on turbosquid: 3d models for games, architecture, videos. (1231207)
turbosquid
$23
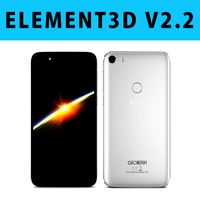
E3D - Alcatel Idol 5
... model e3d - alcatel idol 5 for download as max, obj, and c4d on turbosquid: 3d models for games, architecture, videos. (1212799)
V6
3d_export
$100
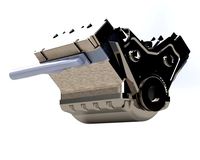
v6 engine
...engine
3dexport
complete v6 engine modeled on solidworks 2017 along with .stl, .sldprt and .sldasm of all th parts and assembly.
3d_export
$10
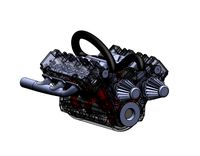
V6 engine
... the first v6 engines were designed and produced independently by marmon motor car company, deutz gasmotoren fabrik and delahaye.
3d_export
$35

v6 engine
...s a complete model of a v6 engine containing over 400 components. you can contact me for a video of all the components assembling
3d_export
$10
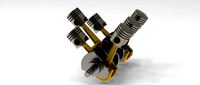
v6 engine
...v6 engine
3dexport
turbosquid
$25
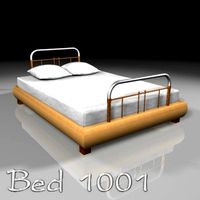
Bed1001-v6
... available on turbo squid, the world's leading provider of digital 3d models for visualization, films, television, and games.
turbosquid
$22
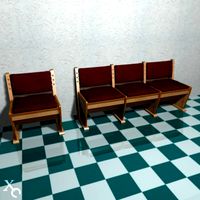
Chair2-v6
... available on turbo squid, the world's leading provider of digital 3d models for visualization, films, television, and games.
turbosquid
$20
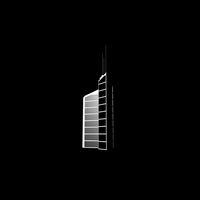
V6.mb
... available on turbo squid, the world's leading provider of digital 3d models for visualization, films, television, and games.
3d_export
$20
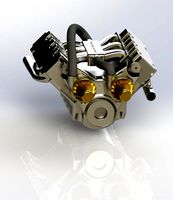
V6 engine
...rovided in this package is all the parts in sldprt format and assembly in sldasm format. i can also convert the format on demand.
3ddd
$1
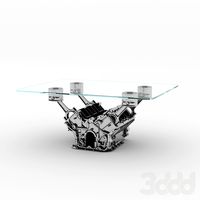
Стол V6
...6" в стиле дизельпанк изготовлен из блока двигателя, 4х поршней и 4х шатунов.
столешница изготовлена из стекла толщиной 8мм.
cg_studio
$199
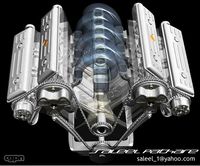
V6 VVTi3d model
...v6 vvti3d model
cgstudio
.3ds - v6 vvti 3d model, royalty free license available, instant download after purchase.
Mod
design_connected
$13
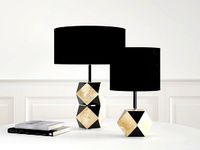
MOD. 4233 - MOD. 4234 Table Lamp
...mod. 4233 - mod. 4234 table lamp
designconnected
arcahorn mod. 4233 - mod. 4234 table lamp computer generated 3d model.
design_connected
$11
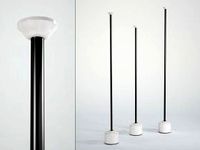
MOD.1095
...mod.1095
designconnected
mod.1095 computer generated 3d model. designed by sarfatti, gino.
3ddd
$1
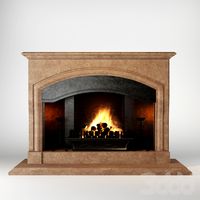
fireplaces mod Spec
...fireplaces mod spec
3ddd
камин
fireplaces mod spec 180x90x125h
3ddd
free
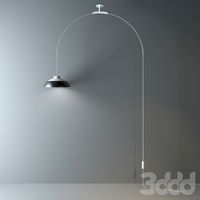
Flos Mod. 2129
... mod
фабрика: flos
модель: mod. 2129
описание: подвесной светильник, металл, белый, черный.
сайт: www.flos.com
turbosquid
$34
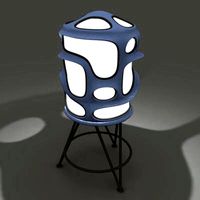
Mod Lamp.c4d
... available on turbo squid, the world's leading provider of digital 3d models for visualization, films, television, and games.
turbosquid
$32
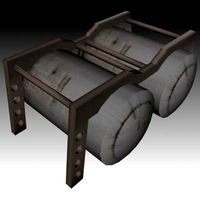
MOD A 001
... available on turbo squid, the world's leading provider of digital 3d models for visualization, films, television, and games.
turbosquid
$29
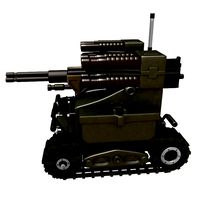
Maars Mod
... available on turbo squid, the world's leading provider of digital 3d models for visualization, films, television, and games.
turbosquid
$15
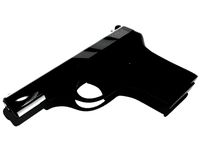
Mod 70..
... available on turbo squid, the world's leading provider of digital 3d models for visualization, films, television, and games.
turbosquid
$10
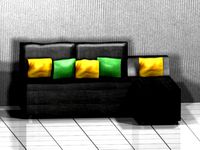
MOD Sofa
... available on turbo squid, the world's leading provider of digital 3d models for visualization, films, television, and games.
turbosquid
$1
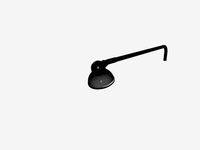
Mod-Lite
... available on turbo squid, the world's leading provider of digital 3d models for visualization, films, television, and games.
V2
3d_export
free
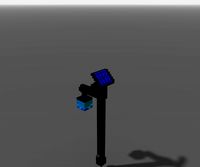
Lamp v2
...lamp v2
3dexport
lamp v2 with solar panel
3d_export
$5
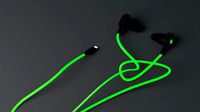
hammerhead v2
...hammerhead v2
3dexport
razer hammerhead v2 headphones, modeled in cinema 4d, render in corona
3d_export
$5
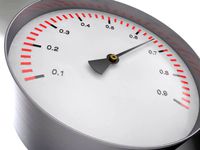
manometer v2
...manometer v2
3dexport
3d_export
$5

potato v2
...potato v2
3dexport
turbosquid
$52
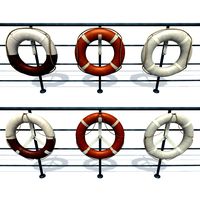
Lifebuoys v2
...squid
royalty free 3d model lifebuoys v2 for download as fbx on turbosquid: 3d models for games, architecture, videos. (1560870)
turbosquid
$2
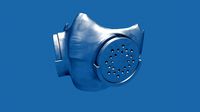
Mask v2
...turbosquid
royalty free 3d model mask v2 for download as stl on turbosquid: 3d models for games, architecture, videos. (1527741)
turbosquid
free

Flashlight V2
...d
free 3d model flashlight v2 for download as , obj, and fbx on turbosquid: 3d models for games, architecture, videos. (1663559)
turbosquid
$29
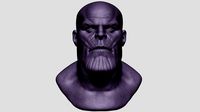
Thanos v2
...
royalty free 3d model thanos v2 for download as ztl and obj on turbosquid: 3d models for games, architecture, videos. (1651077)
turbosquid
$29
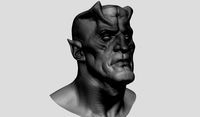
Titan v2
...d
royalty free 3d model titan v2 for download as ztl and obj on turbosquid: 3d models for games, architecture, videos. (1540228)
turbosquid
$29
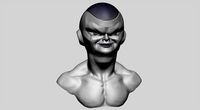
Frieza v2
...
royalty free 3d model frieza v2 for download as ztl and obj on turbosquid: 3d models for games, architecture, videos. (1701238)