GrabCAD

Inexpensive/Budget CNC Plasma Table
by GrabCAD
Last crawled date: 1 year, 11 months ago
Complete real-world build with simple plasma cut/routed parts, a few easy bends, low unique part count, and common parts/fasteners on scrap/drop 2" steel tube and phenolic resin (lab countertop material). Cutting videos added below (2 years after build).
Update: The first cuts were perfect, and no mechanical changes or adjustments have been made except to increase height of rail supports (increase Z), replace Z plate (to better support the torch cable), (much latter) smaller pulleys for greater acceleration, lower shelf to catch parts and debris, and a water nozzle and solenoid for cooling thin material while cutting. There have been no scrap parts except those caused by CAM or operator error. The torch has yet to contact material while cutting and the "temporary" 3D printed PLA torch mount has survived (so far) without any bruises or scars. There have been no issues with the cheapo NEMA 17, it's sloppy brass-like nut and captive rolled T8 thread rod, or motor damper as the THC makes any vertical Z inaccuracies disappear. Very cold temperatures required reducing rapid speeds by 50%.
Due to the ultra low construction cost, even after going a little overboard on electronics, it has more than paid for itself. Only things I'd change if building again would be to use stainless steel wherever possible, powder coat everything else, not weld slats to the table (I didn't think I'd end up cutting as much as I do...), and make cutting area a little larger. With custom post processor and LinuxCNC/PlasmaC, cutting usually only requires manually jogging to start of a nest, zeroing X and Y, and pressing play.
RM2-2RS ($2.50 eBay) bearings in routed grooves on resin X/Y rails and NSK linear rail (scrap yard) for Z. NEMA 23 ($20 - eBay) with XL pulleys and 3/8" Gates belt (McMaster-Carr) for X and Y. Delrin idler pulleys (OpenBuilds) with 688 bearings (eBay) (latter replaced with identical aluminum idler pulleys). 3D printer grade (ie: junk) NEMA 17 ($22 Amazon) with 8mm captive lead and included brass nut for Z. 12mm PNP inductive sensors ($2 - eBay) for X, Y1/Y2 min, Z max, and floating Z switch.
Motion and control via. Gecko G540, custom ARM/FPGA running LinuxCNC/Plasmac, and a couple of cheap/small touch screens. Acceleration and feed rates all greatly exceed those necessary for plasma cutting. Many of the cables are shielded and there have been no noise issues.
The only critical dimensions are depth of V grooves routed into the rails (other materials could be used), spacers, belt anchor locations (based on selected pulleys/idlers), and bend for the Z nut mount.
Completed machine produces very accurate cuts, awesome holes, with no obvious deflection in any axis. Shortcomings in Z (stacked rails and the low-quality NEMA 17 assembly with brass nut on poorly rolled T8 threads) don't appears in cuts and/or are offset by a good THC and motion control.
Z rail support/stiffener on X gantry is 1" Purebond oak plywood (sealed with poly and then painted) that provides some isolation between X and Z, is light, and possibly results in quieter low speed motion than an earlier resin component.
Torch was originally a Hypertherm PAC120 hand torch and gets fed mostly generic/aftermarket consumables. The best cuts are obtained with Hypertherm 120092 "pipe saddle" nozzles and OEM or generic 120573 electrodes. Standard 020350 "gouging" nozzles work best when their faces have been machined flat but require more frequent cleaning (modified or not) during use than 120092.
STEP and IGES via. F360. DXF (by request) includes unfolded sheet metal parts. Clearances not added in CAD unless noted in part name. Steel parts were cut directly from DXF exports, slowing to 60% for holes and slots, which added enough clearance for assembly. Smaller fasteners could replace all except 3/8" supporting the RM2 bearings. All of the 3/8" fasteners were torqued to 24 ft. lbs.
Final cost was less than $300 USD without electronics.
Videos (after 2 years of use) here at link below:
https://youtu.be/cc8HTh48V4s
https://youtu.be/xRbEficCp3U
https://youtu.be/qcVhlMZEud0
Update: The first cuts were perfect, and no mechanical changes or adjustments have been made except to increase height of rail supports (increase Z), replace Z plate (to better support the torch cable), (much latter) smaller pulleys for greater acceleration, lower shelf to catch parts and debris, and a water nozzle and solenoid for cooling thin material while cutting. There have been no scrap parts except those caused by CAM or operator error. The torch has yet to contact material while cutting and the "temporary" 3D printed PLA torch mount has survived (so far) without any bruises or scars. There have been no issues with the cheapo NEMA 17, it's sloppy brass-like nut and captive rolled T8 thread rod, or motor damper as the THC makes any vertical Z inaccuracies disappear. Very cold temperatures required reducing rapid speeds by 50%.
Due to the ultra low construction cost, even after going a little overboard on electronics, it has more than paid for itself. Only things I'd change if building again would be to use stainless steel wherever possible, powder coat everything else, not weld slats to the table (I didn't think I'd end up cutting as much as I do...), and make cutting area a little larger. With custom post processor and LinuxCNC/PlasmaC, cutting usually only requires manually jogging to start of a nest, zeroing X and Y, and pressing play.
RM2-2RS ($2.50 eBay) bearings in routed grooves on resin X/Y rails and NSK linear rail (scrap yard) for Z. NEMA 23 ($20 - eBay) with XL pulleys and 3/8" Gates belt (McMaster-Carr) for X and Y. Delrin idler pulleys (OpenBuilds) with 688 bearings (eBay) (latter replaced with identical aluminum idler pulleys). 3D printer grade (ie: junk) NEMA 17 ($22 Amazon) with 8mm captive lead and included brass nut for Z. 12mm PNP inductive sensors ($2 - eBay) for X, Y1/Y2 min, Z max, and floating Z switch.
Motion and control via. Gecko G540, custom ARM/FPGA running LinuxCNC/Plasmac, and a couple of cheap/small touch screens. Acceleration and feed rates all greatly exceed those necessary for plasma cutting. Many of the cables are shielded and there have been no noise issues.
The only critical dimensions are depth of V grooves routed into the rails (other materials could be used), spacers, belt anchor locations (based on selected pulleys/idlers), and bend for the Z nut mount.
Completed machine produces very accurate cuts, awesome holes, with no obvious deflection in any axis. Shortcomings in Z (stacked rails and the low-quality NEMA 17 assembly with brass nut on poorly rolled T8 threads) don't appears in cuts and/or are offset by a good THC and motion control.
Z rail support/stiffener on X gantry is 1" Purebond oak plywood (sealed with poly and then painted) that provides some isolation between X and Z, is light, and possibly results in quieter low speed motion than an earlier resin component.
Torch was originally a Hypertherm PAC120 hand torch and gets fed mostly generic/aftermarket consumables. The best cuts are obtained with Hypertherm 120092 "pipe saddle" nozzles and OEM or generic 120573 electrodes. Standard 020350 "gouging" nozzles work best when their faces have been machined flat but require more frequent cleaning (modified or not) during use than 120092.
STEP and IGES via. F360. DXF (by request) includes unfolded sheet metal parts. Clearances not added in CAD unless noted in part name. Steel parts were cut directly from DXF exports, slowing to 60% for holes and slots, which added enough clearance for assembly. Smaller fasteners could replace all except 3/8" supporting the RM2 bearings. All of the 3/8" fasteners were torqued to 24 ft. lbs.
Final cost was less than $300 USD without electronics.
Videos (after 2 years of use) here at link below:
https://youtu.be/cc8HTh48V4s
https://youtu.be/xRbEficCp3U
https://youtu.be/qcVhlMZEud0
Similar models
3dwarehouse
free
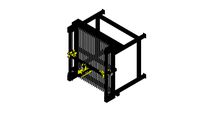
Inexpensive CNC Plasma Table
...adcad link below. exported from cad, but modification of su file to fix orientation results in a huge skp file (at least for me).
grabcad
free

3D Printer 051
...cad components. stray holes in x rail allowed bolting dissimilar x and y rails together (see photos) to route...
grabcad
free

Another Inexpensive/Budget CNC Plasma Table
.... idler pulleys are openbuilds smooth idler style with 688 bearings and shim. nylock nuts will be used everywhere.
sc plasma 023
thingiverse
free
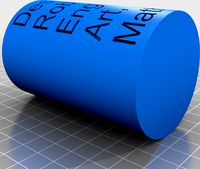
Hypertherm Plasma Torch model HPR 130xd by KrAZyKarl037
...hypertherm plasma torch model hpr 130xd by krazykarl037
thingiverse
hypertherm plasma torch model hpr 130xd
grabcad
free

CNC Router - RM2 Bearings in "C" Rails - HGR15R/HGH15CA Z - NEMA 23
...for cnc router with rm2 bearings in "c" rails (similar to an openbuilds extrusion but more rigid), hgr15r/hgh15ca linear...
thingiverse
free
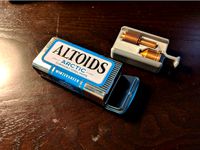
Altoids tin plasma cutter consumables tray by funkenjaeger
...lasma cutter at makeit labs in nashua, nh.
the consumable part numbers, for reference, are 120932 (nozzle) and 120926 (electrode)
grabcad
free

Hypertherm Powermax 45 Plasma Torch
...hypertherm powermax 45 plasma torch
grabcad
a rough rendering of the hypertherm powermax 45, close to exact dimensions
thingiverse
free
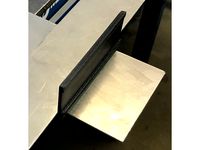
Hypertherm Plasma Cutter Offset Guide by mklange
...art you want is on the straight-edge side), wide end is for cut to the inside of the line (part you want will be the offcut side.
grabcad
free

Economy CNC Plasma Table
...t be kept clear of obstructions (dried bird droppings can cause missed steps).
photos will be added when i receive them.
sc 029
grabcad
free

Neuron Plasma Torch Height Control - Controller
...ad
neuron plasma thc, model provided to allow for space allocation and marking / cutting of mounting holes
http://neuroncnc.com/
Inexpensive
3d_export
$5
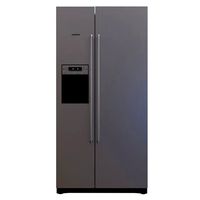
Fridge BOSCH
...fridge bosch 3dexport a good and inexpensive model for shooting...
3d_export
$5
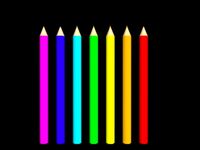
Collection of colored pencils 3D Model
...colored pencils 3d model 3dexport collections rainbow pencils color inexpensivey collection of colored pencils 3d model mixanik 57025...
3d_export
$25
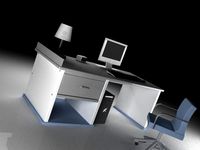
Computer Desk 3D Model
...desk computer 3ds max simple mouse monitor keyboard cheap inexpensive computer desk 3d model banana 8536...
3d_export
free
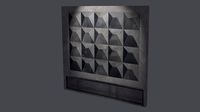
Soviet stone fence
...approached by officials with a demand to develop an inexpensive universal fence for strategic objects. it is from this...
3d_export
$15
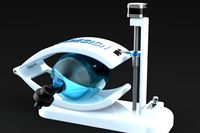
ambubag ventilator covid-19 crisis
...covid-19 crisis 3dexport this is the coceptual design for inexpensive ventilator to save people who are infected with the...
3d_export
$75
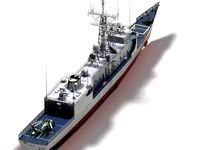
uss fahrion ffg22 ohp class frigate
...united states in the mid-1970s as general-purpose escort vessels inexpensive enough to be bought in large numbers to replace...
thingiverse
free
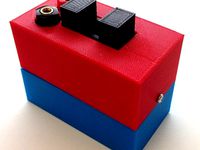
Inexpensive Colorimeter by jamesdmendez
...ive colorimeter by jamesdmendez
thingiverse
this is a colorimeter that relies on leds for both the light source and measurement.
thingiverse
free
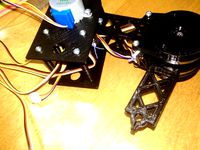
Inexpensive SCARA arm (2D) w/ 28BYJ-48 steppers by dacb
...b in mcp folder: https://github.com/beckdac/scara ) to control the arm from the command line includes threaded server with homing
thingiverse
free
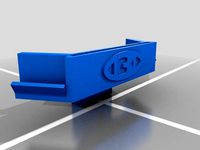
BI 2.5 Inexpensive enclosure 2.5 by joker55
... 1/14/15 i still need to make some flaps to fill the gap at the bottom sides & gopro mount.. will post when i can get to it.
thingiverse
free

Inexpensive Replicator 2 Side Enclosure. by byllc
...on me that if you coated one side of a 'wall' with mylar you could use just about anything to create the enclosure walls.
Budget
turbosquid
$3
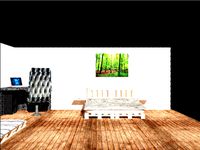
Low Budget Room
...id
royalty free 3d model low budget room for download as max on turbosquid: 3d models for games, architecture, videos. (1528865)
turbosquid
$3
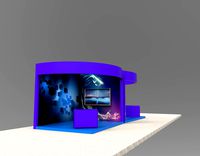
Simple Low Budget Stalls
...ty free 3d model simple low budget stalls for download as skp on turbosquid: 3d models for games, architecture, videos. (1304971)
turbosquid
$3
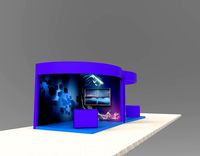
Simple Low Budget Stalls
...ty free 3d model simple low budget stalls for download as skp on turbosquid: 3d models for games, architecture, videos. (1305613)
turbosquid
$3
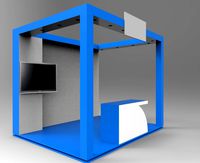
Simple Low Budget 3D Stall
... free 3d model simple low budget 3d stall for download as skp on turbosquid: 3d models for games, architecture, videos. (1304969)
cg_studio
$129
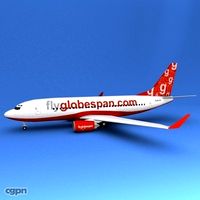
Boeing 737 FlyGlobeSpan Budget Airline3d model
...dxf .max .obj - boeing 737 flyglobespan budget airline 3d model, royalty free license available, instant download after purchase.
3d_export
$15
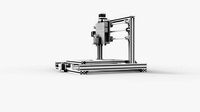
prototype cnc router small budget
...onforming components have been adjusted<br>unit : mm<br>machine size 50x50x30 cm<br>formats: iges, step and stl
3d_export
$25
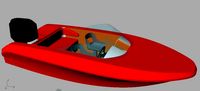
PowerboatNeptun 3D Model
...engine speed yacht pleasure hull моторная лодка project of budget ...
3d_export
$48
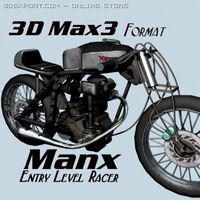
Manx 3D Model
...model manx entry level racing bike cafe motorcycle speedster budget racer jawa ducati triumph norton manx 3d model zarday321...
3d_export
$68
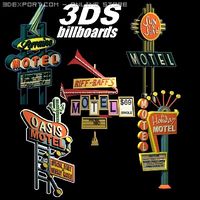
Motel Signs Pack of 5 3D Model
...hotel sign post billboard ad advert room vacancy accommodation budget neon motel signs pack of 5 3d model zarday321...
3d_ocean
$7
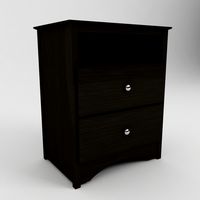
Prepac Sonoma 2 Drawer Tall Night Stand
...for those looking for designer styles without the designer budget ...
Plasma
3d_ocean
$25
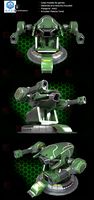
Plasma Cannon, Plasma Turret
...ily be used in any sf type of game, especially in tower defense games. - plasma cannon: 4462 polygons - textures: 6000...
3d_ocean
$19
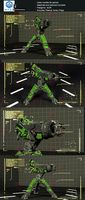
Plasma Turret
... be used in any sf type of game, especially in tower defense games. - plasma turret: 6239 polygons - props: 522 polygons - tex...
turbosquid
$10
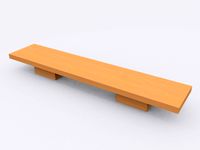
Plasma
... available on turbo squid, the world's leading provider of digital 3d models for visualization, films, television, and games.
3d_export
$5
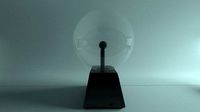
plasma lamp
...plasma lamp
3dexport
detailed normal scale plasma lamp used indoors as a decorative object
turbosquid
$3
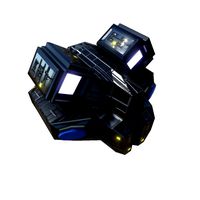
Plasma drone
...rbosquid
royalty free 3d model plasma drone for download as on turbosquid: 3d models for games, architecture, videos. (1337186)
turbosquid
$15
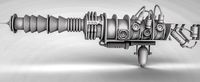
plasma gun
...bosquid
royalty free 3d model plasma gun for download as fbx on turbosquid: 3d models for games, architecture, videos. (1324248)
turbosquid
$12
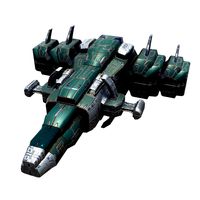
Plasma Corvette
...id
royalty free 3d model plasma corvette for download as obj on turbosquid: 3d models for games, architecture, videos. (1442325)
turbosquid
$1
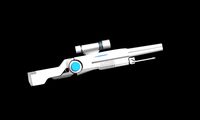
Plasma Rifle
...squid
royalty free 3d model plasma rifle for download as obj on turbosquid: 3d models for games, architecture, videos. (1485980)
turbosquid
$25
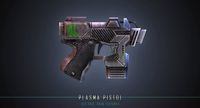
Plasma Pistol
...free 3d model plasma pistol for download as max, fbx, and obj on turbosquid: 3d models for games, architecture, videos. (1559545)
turbosquid
$10
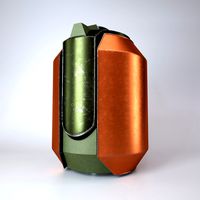
Plasma Grenade
...d model plasma grenade for download as max, obj, c4d, and fbx on turbosquid: 3d models for games, architecture, videos. (1280730)
Cnc
3d_export
$35
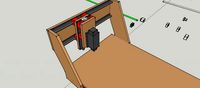
Cnc
...cnc
3dexport
the cnc machine is unfinished
3d_export
$10
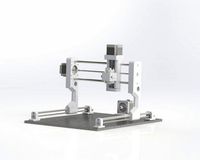
cnc router
...cnc router
3dexport
prototipe cnc router
3d_export
$10
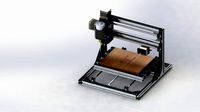
cnc machine
...cnc machine
3dexport
cnc machine model with individual model files with assembly
3d_export
$5
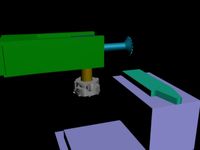
Cnc 3D Model
...cnc 3d model
3dexport
cnc
cnc 3d model csiszar 61289 3dexport
turbosquid
$10
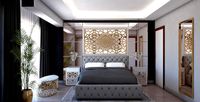
cnc bedroom
...osquid
royalty free 3d model cnc bedroom for download as max on turbosquid: 3d models for games, architecture, videos. (1494981)
turbosquid
$9
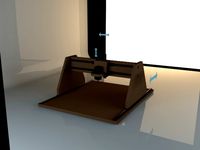
cnc(wood)
...rbosquid
royalty free 3d model cnc(wood) for download as max on turbosquid: 3d models for games, architecture, videos. (1189189)
turbosquid
$1
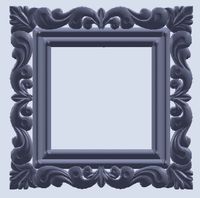
CNC Frame
...rbosquid
royalty free 3d model cnc frame for download as stl on turbosquid: 3d models for games, architecture, videos. (1371706)
turbosquid
free
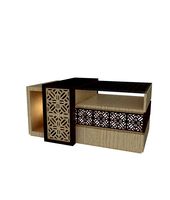
cnc table
...rbosquid
royalty free 3d model cnc table for download as max on turbosquid: 3d models for games, architecture, videos. (1500926)
turbosquid
$30
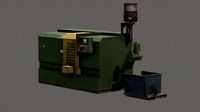
CNC Lathe
...
royalty free 3d model cnc lathe for download as max and obj on turbosquid: 3d models for games, architecture, videos. (1284634)
turbosquid
$25
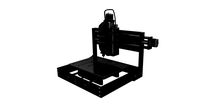
CNC Machine
...
royalty free 3d model cnc machine for download as ma and fbx on turbosquid: 3d models for games, architecture, videos. (1307199)
Table
3ddd
free
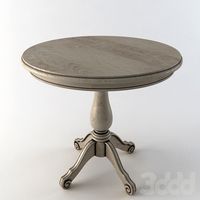
Table
...table
3ddd
table
table
archibase_planet
free
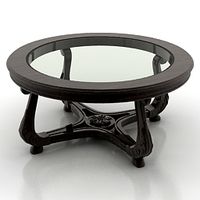
Table
...table
archibase planet
table glass-table round table glass table
table n240311 - 3d model (*.3ds) for interior 3d visualization.
archibase_planet
free
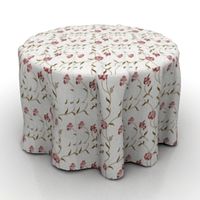
Table
...e
archibase planet
table dining-room table dinner table round table
table - 3d model (*.gsm+*.3ds) for interior 3d visualization.
3d_export
$5
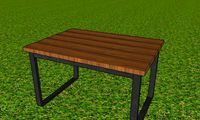
table
...table
3dexport
table classic-table
archibase_planet
free
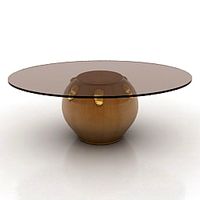
Table
...se planet
table glass table round table glass-table
table tonin habitat n280111 - 3d model (*.3ds) for interior 3d visualization.
archibase_planet
free
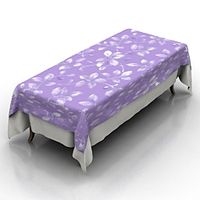
Table
...table
archibase planet
table dining-room table dinner table
table - 3d model (*.3ds) for interior 3d visualization.
archibase_planet
free
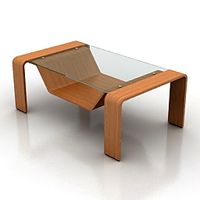
Table
...table
archibase planet
table coffee table glass table
table - 3d model (*.gsm+*.3ds) for interior 3d visualization.
archibase_planet
free
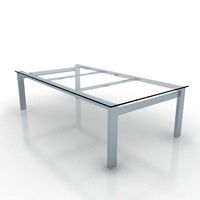
Table
...table
archibase planet
table glass-table coffee table
table - 3d model (*.gsm+*.3ds) for interior 3d visualization.
archibase_planet
free
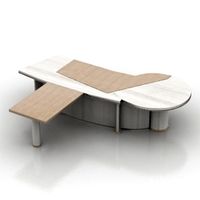
Table
...table
archibase planet
table writing table office table
table - 3d model (*.gsm+*.3ds) for interior 3d visualization.
3d_ocean
$5
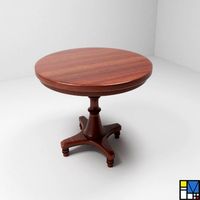
Table
...table
3docean
dining table furniture home kitchen table
simple wooden table.