Thingiverse
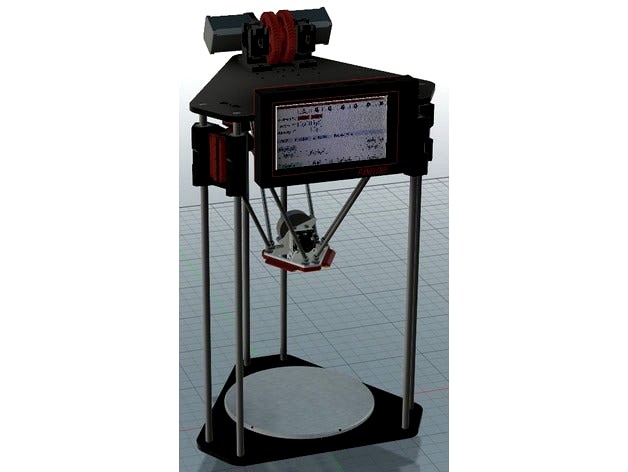
Geeetech G2s Upgrades v2 by LuckyPants
by Thingiverse
Last crawled date: 3 years, 1 month ago
This is version 2 of my upgraded G2s (version 1 http://www.thingiverse.com/thing:2020086) - basically a full overhaul of everything but the top/bottom plates and the linear rods. It is a continuation of trying to make my G2s the best it can be (not really a G2s anymore at this point i guess!).
Quick summary of upgrades:
Custom Carriages.
Magnetic Arms.
Custom Effector.
E3D Cyclops 2in-1out Hotend - or - E3D v6
Part Cooling Fan.
Greg’s Wade Geared Extruders.
Optical Endstops.
Duet Wifi electronics.
7” PanelDue interface.
Increased usable print diameter and height (Ø200mm x 210mm height).
Issues with the G2s:
Motion slop
a. Delta arms have play and design limits ability to accurately calibrate length.
b. 2 bearing carriages have excessive play and torque from the arms causes them to pitch up, having significant influence on the end effector.
c. Design of the stock end effector has the effector center of mass below the rod link locations, which will cause effector tilt and unwanted movement during acceleration/jerk moves.
Hotend performance
a. Stock hotend is difficult to level and reduces usable bed size.
b. Dual nozzle configuration suffers when effector tilt occurs.
c. No part cooling fan included.
Extruder performance
a. The direct drive extruder is ok, but the hobbing on the drive gear is a bit shallow, and the force on the filament could be a bit stronger to handle higher print and retraction speeds. It is likely ok for stock setup, but will not be sufficient once other components are upgraded.
Probing performance
a. Microswitch probe must be manually deployed, sometimes binds in bore causing unrepeatable measures.
Electronics
a. GT2560 board is not capable of driving the axes past ~80mm/sec. Studdering occurs at higher speeds. Interpolation is broken into segments that are too large for higher speed movement.
b. Included limit switches are acceptable, but not repeatable enough to make probing and really dialing in the delta parameters worth it, as each G28 throws it off here or there.
Lighting
a. None!
My solutions to those issues:
Motion slop
a. Haydn’s magnetic arms (http://www.blueeaglelabs.com/products/haydns-carbon-fiber-arms-with-cnc-precision-machined-delrin-sockets). Mine came accurate in length to .01mm.
b. Complete redesign of carriages to accept 4 LMU-N10 bearings (https://us.misumi-ec.com/vona2/detail/110300026540/?HissuCode=LMU-N10) and the mag arms. Carriages work with stock microswitch endstops or optical endstop upgrade.
c. Rather that adapt the stock effector to fit the mag arms, I designed a new one. This effector design is much more modular and makes creating addons easy.
d. With below hotend, center of mass is aligned to mag arm spheres to resist effector tilt.
Hotend performance
a. 2in-1out hotend (http://e3d-online.com/Cyclops), retain dual extrusion ability but without the loss of bed area or difficulty in levelling. Also available with E3D v6 configuration.
b. Influence of effector tilt is greatly reduced with a single nozzle centered on the effector.
c. Integrated part cooling fan into hotend mount.
Extruder performance
a. I ordered 2 of the Greg's Wade Extruder hardware kit at (https://www.ultibots.com/gregs-wade-extruder-hardware-kit/), and printed 2 sets of the extruder parts - 1 regular and 1 mirrored (http://www.thingiverse.com/thing:18379). In order to fit in the location of the original, you need to mirror one of the extruders. In doing so you need to reverse the hobbed bolt - to get the hobbed portion of the bolt aligned with the feeder tube, you'll need the included spacer. In addition, the attached gear has a deeper relief to accept the bolt in the mirrored extruder. Any questions on this let me know.
Probing performance
a. Force Sensitive Resistor (FSR) probing system (https://www.ultibots.com/fsr-kit/).
b. FSR’s live under the bed and probing is done directly when the nozzle contacts the bed. They are not affected by choice of bed (glass/non-conductive/etc).
Electronics
a. Duet Wifi (https://duet3d.com/DuetWifi). Tons of processing HP to deal with the calculations needed to drive a delta bot. Firmware configuration is very easy and powerful. Program transfer and machine control via WiFi through the web interface is awesome. Interpolating at 300mm/s with no issues.
b. PanelDue (https://miscsolutions.wordpress.com/paneldue/). 7” touchscreen that allows easy control of the bot, plus a nice menu to execute custom macros for filament loading/probing/etc.
c. Optical endstops (http://www.ebay.ca/itm/282247383661). Plenty on eBay if you search “RAMPS 1.4 Optical Endstop”. Enstops are shielded from sunlight interference in a protective housing.
Lighting
a. Enclosure mounted LED’s for overall interior lighting.
b. Effector mounted LED’s for part lighting.
c. LED brightness controllable by M code.
Quick summary of upgrades:
Custom Carriages.
Magnetic Arms.
Custom Effector.
E3D Cyclops 2in-1out Hotend - or - E3D v6
Part Cooling Fan.
Greg’s Wade Geared Extruders.
Optical Endstops.
Duet Wifi electronics.
7” PanelDue interface.
Increased usable print diameter and height (Ø200mm x 210mm height).
Issues with the G2s:
Motion slop
a. Delta arms have play and design limits ability to accurately calibrate length.
b. 2 bearing carriages have excessive play and torque from the arms causes them to pitch up, having significant influence on the end effector.
c. Design of the stock end effector has the effector center of mass below the rod link locations, which will cause effector tilt and unwanted movement during acceleration/jerk moves.
Hotend performance
a. Stock hotend is difficult to level and reduces usable bed size.
b. Dual nozzle configuration suffers when effector tilt occurs.
c. No part cooling fan included.
Extruder performance
a. The direct drive extruder is ok, but the hobbing on the drive gear is a bit shallow, and the force on the filament could be a bit stronger to handle higher print and retraction speeds. It is likely ok for stock setup, but will not be sufficient once other components are upgraded.
Probing performance
a. Microswitch probe must be manually deployed, sometimes binds in bore causing unrepeatable measures.
Electronics
a. GT2560 board is not capable of driving the axes past ~80mm/sec. Studdering occurs at higher speeds. Interpolation is broken into segments that are too large for higher speed movement.
b. Included limit switches are acceptable, but not repeatable enough to make probing and really dialing in the delta parameters worth it, as each G28 throws it off here or there.
Lighting
a. None!
My solutions to those issues:
Motion slop
a. Haydn’s magnetic arms (http://www.blueeaglelabs.com/products/haydns-carbon-fiber-arms-with-cnc-precision-machined-delrin-sockets). Mine came accurate in length to .01mm.
b. Complete redesign of carriages to accept 4 LMU-N10 bearings (https://us.misumi-ec.com/vona2/detail/110300026540/?HissuCode=LMU-N10) and the mag arms. Carriages work with stock microswitch endstops or optical endstop upgrade.
c. Rather that adapt the stock effector to fit the mag arms, I designed a new one. This effector design is much more modular and makes creating addons easy.
d. With below hotend, center of mass is aligned to mag arm spheres to resist effector tilt.
Hotend performance
a. 2in-1out hotend (http://e3d-online.com/Cyclops), retain dual extrusion ability but without the loss of bed area or difficulty in levelling. Also available with E3D v6 configuration.
b. Influence of effector tilt is greatly reduced with a single nozzle centered on the effector.
c. Integrated part cooling fan into hotend mount.
Extruder performance
a. I ordered 2 of the Greg's Wade Extruder hardware kit at (https://www.ultibots.com/gregs-wade-extruder-hardware-kit/), and printed 2 sets of the extruder parts - 1 regular and 1 mirrored (http://www.thingiverse.com/thing:18379). In order to fit in the location of the original, you need to mirror one of the extruders. In doing so you need to reverse the hobbed bolt - to get the hobbed portion of the bolt aligned with the feeder tube, you'll need the included spacer. In addition, the attached gear has a deeper relief to accept the bolt in the mirrored extruder. Any questions on this let me know.
Probing performance
a. Force Sensitive Resistor (FSR) probing system (https://www.ultibots.com/fsr-kit/).
b. FSR’s live under the bed and probing is done directly when the nozzle contacts the bed. They are not affected by choice of bed (glass/non-conductive/etc).
Electronics
a. Duet Wifi (https://duet3d.com/DuetWifi). Tons of processing HP to deal with the calculations needed to drive a delta bot. Firmware configuration is very easy and powerful. Program transfer and machine control via WiFi through the web interface is awesome. Interpolating at 300mm/s with no issues.
b. PanelDue (https://miscsolutions.wordpress.com/paneldue/). 7” touchscreen that allows easy control of the bot, plus a nice menu to execute custom macros for filament loading/probing/etc.
c. Optical endstops (http://www.ebay.ca/itm/282247383661). Plenty on eBay if you search “RAMPS 1.4 Optical Endstop”. Enstops are shielded from sunlight interference in a protective housing.
Lighting
a. Enclosure mounted LED’s for overall interior lighting.
b. Effector mounted LED’s for part lighting.
c. LED brightness controllable by M code.
Similar models
thingiverse
free

Set for Greg's Wade extruder with Jhead by JotaErre
...ot;greg´s wade" extruder.
included in this set:
cooler for hotend and filament (for 50mm fan).
mount for servo.
endstop arm.
thingiverse
free

Anti hotend wiggling with 18mm probe mount for Prusa i3 Greg's Wade extruder E3D V5 by nakeib
...r and e3d v5 hotend. project include 18mm z probe mount.
the probe offset is:
x: 42mm (or -42 if you will print it fliped)
y: 0mm
thingiverse
free
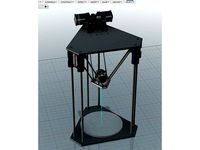
Geeetech G2s Upgrades by LuckyPants
...he printer seems much smoother. if you plan to do these upgrades, let me know and i'll upload the correct configuration file.
thingiverse
free
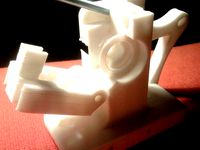
i3 jonaskuehling-gregs-wade extruder by xoan
...hling upgrades.
for both 24-30 mm. carriage hole separation.
source code: https://github.com/xoan/jonaskuehling-gregs-wade-i3
thingiverse
free
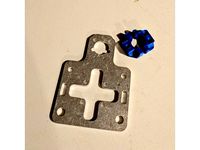
E3D and Tevo AIO Hotend Parts(Old Style) by isaacfank
...tock hotend, or you can upgrade to an e3d style.
https://www.fankhauser.me/products/e3d-and-stock-carriage-aio-for-tevo-tarantula
thingiverse
free
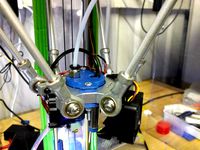
Geeetech G2S E3D V6 and inductive auto bed level upgrade by techwit
...the existing see the before and after marvins picture is have uploaded.
auto level is actually usable unlike the g2s stock sensor
thingiverse
free
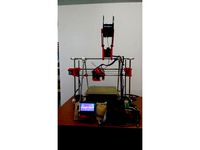
Original Mendel upgrade to i3 X Axis by SysopJ
...usa mk2
x carriage & endstop: http://www.thingiverse.com/thing:1103976
hotend holder: http://www.thingiverse.com/thing:723803
thingiverse
free
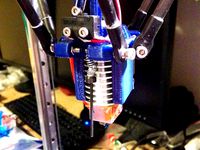
Mini Kossel Effector for E3D Hotend with Z Probe by Thorpydo
...p screws are under z probe.
v4 are the originals
v5 reflects the changes florian requested; screw heads sitting outside clamp
thingiverse
free
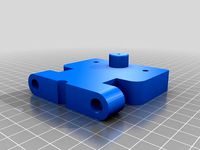
Bowden setup for E3D Hotend on Prusa I2 by Neodd70
...at comes with the e3d hotend. it has been designed to mount the majority of the hotend above the x carriage to maximize z travel.
thingiverse
free

MK3 RHD Fan Duct Rev. C for Volcano Hotend by dragsterbox
...ersion of the:
mk3 nozzle rhd rev. c
by
rh_dreambox
fits the e3d volcano hotend upgrade on both stock and bondtech extruder mount
Luckypants
thingiverse
free
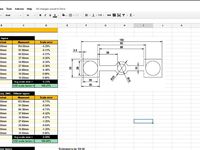
Shrinkage calculation object by LuckyPants
...le sheet shown in the images:https://docs.google.com/spreadsheets/d/10cfmuad_anwwsmppas5jzbknkithyhfe8xmzlksgmfo/edit?usp=sharing
thingiverse
free
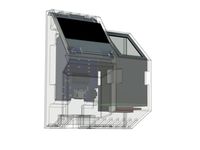
IoT Fingerprint Scanner w/ OLED by LuckyPants
...ct surfaces ~75%.
fusion360 source file included for tinkering.
arduino sketch: https://github.com/luckypants123/fingerprint-mqtt
thingiverse
free
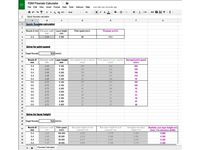
Extrusion Flowrate Calculator by LuckyPants
... my creator pro with all metal microswiss hotend.
https://drive.google.com/open?id=19fvxnxfebbd4txkqhsfrooux7gwcbx5uawkq1ag1lge
thingiverse
free

Flashforge Creator Pro Bed Level code by LuckyPants
...00mm thick) it will be wrong!
2.the attached calibration cube is just here because thingiverse won't let me just upload code.
thingiverse
free
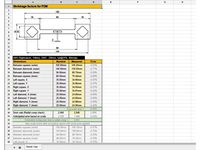
Dimensional Calibration Tool v9 by LuckyPants
...iterations of this, but in my case once was good enough to get me to less than 100um over the 150mm part, which i was happy with.
thingiverse
free
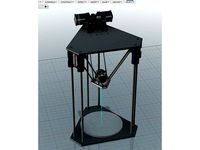
Geeetech G2s Upgrades by LuckyPants
...he printer seems much smoother. if you plan to do these upgrades, let me know and i'll upload the correct configuration file.
thingiverse
free

Scaling and Horizontal Compensation Calibration by jlambier
...also added a series of small holes that can be tested with drill bits to see how small of a hole that i could produce accurately.
thingiverse
free
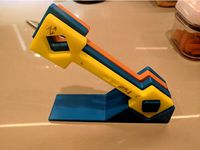
Dimensional thermal test jig (for annealing) by punkgeek
...is a companion for the dimensional calibration tool by luckypants it allows you to place up to 4 of...
G2S
3ddd
$1
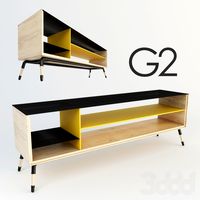
Stand G2
..., stand , ar3
комод-паттерн (g2) design by ar3+
turbosquid
$25
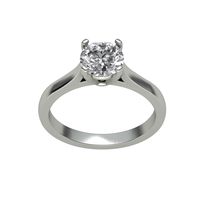
Ring G2
...turbosquid
royalty free 3d model ring g2 for download as stl on turbosquid: 3d models for games, architecture, videos. (1215199)
turbosquid
$19
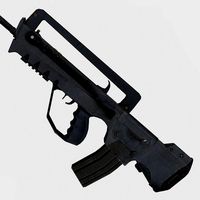
FAMAS G2
...urbosquid
royalty free 3d model famas g2 for download as fbx on turbosquid: 3d models for games, architecture, videos. (1537479)
3d_ocean
$14
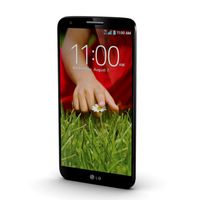
Mobile phone LG G2
... animation and rendering was done in softimage 2013. i am uploading obj. file with textures as well as softimage 2013 file whi...
turbosquid
$29
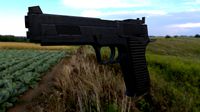
Pindad G2 Elite
...ree 3d model pindad g2 elite for download as ma, obj, and fbx on turbosquid: 3d models for games, architecture, videos. (1446515)
3d_export
$99
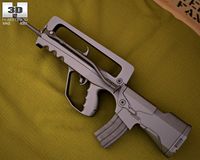
FAMAS G2 3D Model
...ic famas g2 france french fully gun mas rifle semi weapon 3d models assault weapon gun
famas g2 3d model humster3d 94303 3dexport
3d_export
$49
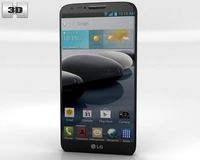
LG G2 3D Model
...g 3g android droid smartphone cell phone mobile cellular tft lcd touchscreen touch screen
lg g2 3d model humster3d 85156 3dexport
turbosquid
$100
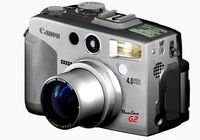
Canon PowerShot G2
... available on turbo squid, the world's leading provider of digital 3d models for visualization, films, television, and games.
3d_export
$49
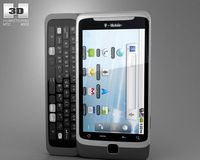
TMobile G2 3D Model
...se gingerbread 233 droid cell phone mobile cellular tft lcd touchscreen touch screen
tmobile g2 3d model humster3d 51180 3dexport
3ddd
$1
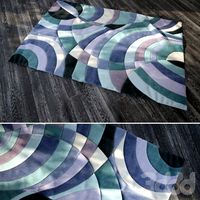
Ковёр G2
...ковёр g2
3ddd
ковёр
форматы в архиве:
max.2014
max.2011
obj
fbx
все текстуры присутствуют
Geeetech
3d_export
free
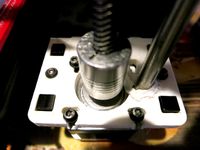
part right for geeetech acrylic i 3
...part right for geeetech acrylic i 3
3dexport
the engine can be shifted
3d_export
free
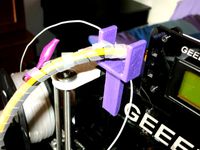
cable holder
...cable holder 3dexport for geeetech acrylic i...
thingiverse
free
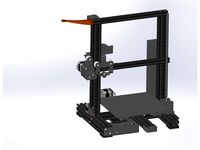
geeetech a10 by Igor_garbuz
...geeetech a10 by igor_garbuz
thingiverse
model geeetech a10 ( solidworks).
thingiverse
free
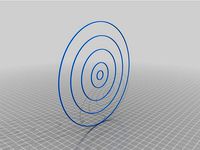
geeetech calibration by muffler1979
...geeetech calibration by muffler1979
thingiverse
just a calibration test for the bed on a geeetech
thingiverse
free

Fan for Geeetech proB
...fan for geeetech prob
thingiverse
this is my fan for the geeetech pro b i3.
thingiverse
free

Chain for Geeetech A30
...chain for geeetech a30
thingiverse
this is my personal review of chain for geeetech a30.
thingiverse
free
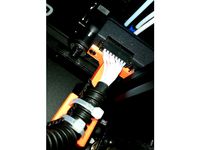
Zugentlastung Hotend Geeetech A30T / Strain relief Geeetech A30T by 3DDennis1983
...zugentlastung hotend geeetech a30t / strain relief geeetech a30t by 3ddennis1983
thingiverse
zugentlastung hotend geeetech a30t
thingiverse
free
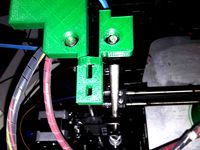
Kettenhalter i3x geeetech by Autark
...kettenhalter i3x geeetech by autark
thingiverse
geeetech i3x
thingiverse
free
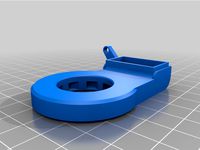
Geeetech A10 Fanduct by stefan177gr
...geeetech a10 fanduct by stefan177gr
thingiverse
fanduct for geeetech a10
thingiverse
free
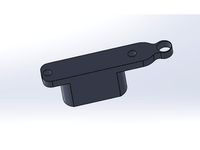
Geeetech filament guide by RicardoZ2018
...geeetech filament guide by ricardoz2018
thingiverse
desing for geeetech i3x
Upgrades
turbosquid
$15
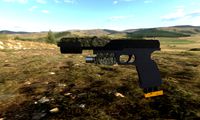
Upgraded Glock
...e 3d model upgraded glock for download as obj, fbx, and blend on turbosquid: 3d models for games, architecture, videos. (1185950)
3ddd
$1
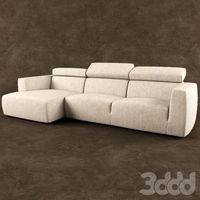
Calligaris / UPGRADE
...calligaris / upgrade
3ddd
calligaris
c материалом
3d_export
free
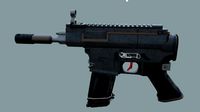
cz upgrade
...cz upgrade
3dexport
https://www.buymeacoffee.com/mestrezen3d https://linktr.ee/mestrezen3
turbosquid
$80
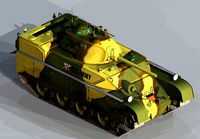
Custer Tank upgrade
... available on turbo squid, the world's leading provider of digital 3d models for visualization, films, television, and games.
turbosquid
$39
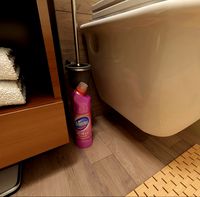
Domestos 1 upgrade
... available on turbo squid, the world's leading provider of digital 3d models for visualization, films, television, and games.
3d_export
$10
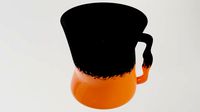
Upgraded tea cup
...upgraded tea cup
3dexport
a cup with an unusual design and a unique shape for a more enjoyable tea experience
3d_export
$8
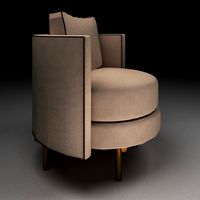
dixy outlander classic style upgraded poplar wood lounge chair
...utlander classic style upgraded poplar wood lounge chair
3dexport
dixy outlander classic style upgraded poplar wood lounge chair
turbosquid
free

AK-12 + Upgrades low-poly 3D model
...ow-poly 3d model for download as fbx, blend, and unitypackage on turbosquid: 3d models for games, architecture, videos. (1501145)
evermotion
$700
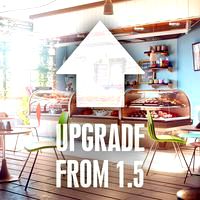
Upgrade from V-ray 1.5 to 3.5 for 3ds max
...here is no need to purchase a new dongle - your current dongles will be reprogrammed to carry v-ray 3. evermotion 3d models shop.
evermotion
$300
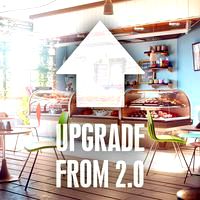
Upgrade from V-Ray 2.0 to V-ray 3.5 for 3ds Max
... interface (gui) for editing settings on one machine and one render node for rendering on one machine. evermotion 3d models shop.
V2
3d_export
free
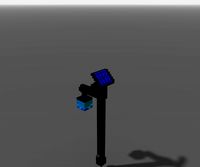
Lamp v2
...lamp v2
3dexport
lamp v2 with solar panel
3d_export
$5
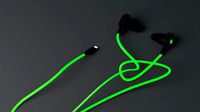
hammerhead v2
...hammerhead v2
3dexport
razer hammerhead v2 headphones, modeled in cinema 4d, render in corona
3d_export
$5
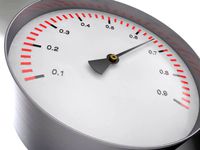
manometer v2
...manometer v2
3dexport
3d_export
$5

potato v2
...potato v2
3dexport
turbosquid
$52
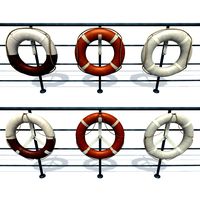
Lifebuoys v2
...squid
royalty free 3d model lifebuoys v2 for download as fbx on turbosquid: 3d models for games, architecture, videos. (1560870)
turbosquid
$2
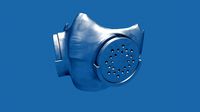
Mask v2
...turbosquid
royalty free 3d model mask v2 for download as stl on turbosquid: 3d models for games, architecture, videos. (1527741)
turbosquid
free

Flashlight V2
...d
free 3d model flashlight v2 for download as , obj, and fbx on turbosquid: 3d models for games, architecture, videos. (1663559)
turbosquid
$29
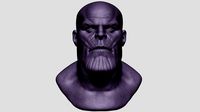
Thanos v2
...
royalty free 3d model thanos v2 for download as ztl and obj on turbosquid: 3d models for games, architecture, videos. (1651077)
turbosquid
$29
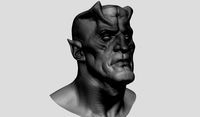
Titan v2
...d
royalty free 3d model titan v2 for download as ztl and obj on turbosquid: 3d models for games, architecture, videos. (1540228)
turbosquid
$29
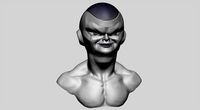
Frieza v2
...
royalty free 3d model frieza v2 for download as ztl and obj on turbosquid: 3d models for games, architecture, videos. (1701238)