Thingiverse
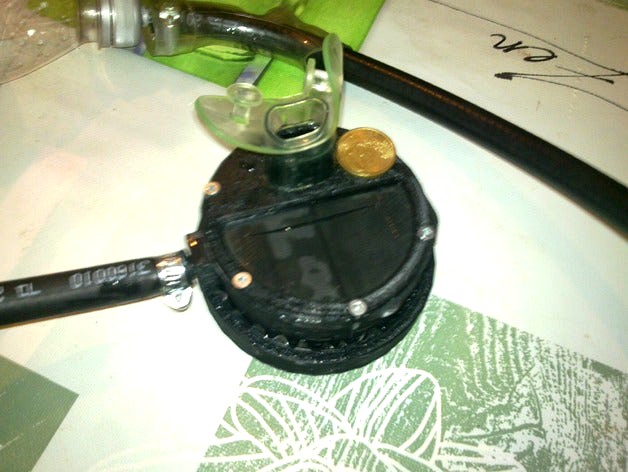
Functional SCUBA Low Pressure Demand Regulator v3.6 by Biketool
by Thingiverse
Last crawled date: 2 years, 12 months ago
This is what 3D modeling and 3D print rapid prototyping excels at, We were able to take some used bicycle tubes, gas hose, and a cut supermarket snorkel to make a functional if crude prototype of an idea based upon a 20 year old memory, and we did it all in the same afternoon. From the press this project has since attracted we reasonably believe this may be the first ever amateur designed and built functional 3D printed low pressure regulator.
WARNING!! I DO NOT GIVE PERMISSION FOR HUMAN OR ANIMAL USE!!! These terms affect the user license and is in addition to and overriding to any terms of the use license. The permissive license only covers the digital files, any real things printed or made in any other way are your own responsibility and may not be used for human or animal purposes or any use which could in any way confer liability to myself my employer or anyone else other than the end users. Only people over the legal age of consent and contractual obligation in both my and their jurisdictions and any jurisdictions of use or legal responsibility may use these files. What I am saying simply is these files if somehow used to make real things are too dangerous for ordinary people for so many reasons do not imperil lives or property, there is no point suing anyone if you did something illegal like pirating these digital files and knowledge for purposes not intended. This is a litigious and ignorant world, the digital files are free-libre but there are limits on using the 3D models to make real world objects for prohibited uses
OpenSCAD files for an easy to source and inexpensive DIY demand low pressure regulator I intend for my personal demonstration use with 120PSI filled 2l carbonated softdrink bottles or a long hose and a home workshop air tank/compressor. Regulator valve lever is included with the inner_mechanism file until v3. Just print this and acquire a blown bicycle tire of sufficient diameter to scavenge the valve and rubber and some wood screws. A supermarket kiddy pool snorkel is an easy way to find a mouthpiece just snip it to length and zip-tie on. The Schrader valve pin pusher on the pivot lever requires some trimming to function correctly. May require sealing the printed body, as my printed walls were so porous that the regulator would flood with water when inspiring, sealing fixed the issue.
Needs a round rubber diaphragm to press the demand lever(bicycle inner-tube rubber) and a bicycle tire Shrader valve to actually do the precision work of the demand valve, a pin for the regulator valve lever, a scuba mouthpiece (or hack one off of a supermarket snorkel), as well as a bit more rubber innertube scrap for a flapper valve for the exhale port. V2.0 files are printed and tested, the v3.x stuff looks nicer,stronger, and better designed IMHO but is vaporware for now and may require a wider sheet of rubber, comment if you do test them. Just to be clear the only precision part in this regulator is a factory made Schrader valve, everything else is just there to press that pin to release breathing air or to valve out any exhaust air and water in the regulator at exhale.
To make a demo soda bottle pressure vessel I removed the valve core and left the rubber round skirt intact to make the seal, I had a 50% success rate making the seal actually hold so I suggest grabbing a few if possible, to this I attached one end of the air hose. At the regulator end I threaded the intact and functional but with circular tube side skirt trimmed off valve stem into the valve block until I could activate the schrader valve by pushing the purge button(hole in regulator where you can push the diaphragm) then I valved out the air, once empty I loosened the clamp and adjusted the hose as a stop collar so I could easily unscrew the valve block and the bottle could be pressurized with a tire pump and have it stop at the correct position.
I added a terrible laptop touchpad freehand graphic to help visualize how simple this and most second stage regulators are. Do you know how hard it is to draw an arrow with a touchpad?!
I only give permissive license to take this these files for academic study and educational demonstration models on how a second stage demand regulator works, I do not give permission to print or use as SCUBA systems or any use for humans or animals. Our lungs are surprisingly fragile and drowning, air embolism, or lung injury are actually pretty easy when dealing with compressed air and depth, especially to untrained divers so don't use this it is a science demo not a real regulator for human use. This is somewhat inspired by an old Soviet rebreather oxygen demand add valve design which used a schrader valve which I liked because you can get Schrader valves anywhere, I seem to remember some Scott Aerospace fire/mine SCBAs using a schrader too. Beyond using a schrader valve, and a lever actuated by a diaphragm it is a clean sheet design without any reference; water goes down, air goes up, pressure differential pushes diaphragms, flapper valves vent only one way, levers push pins, open valves vent higher pressure. Despite linking to a ScubaPro youtube video to show how a commercial regulator is assembled and works this design has nothing to do with ScubaPro and is not inspired in any way by any of their designs, it was added after the fact for educational purposes.
If you need a real acquire-to-use second stage regulator for a scuba or vehicle/aircraft submerged water escape rig buying used and getting serviced is so cheap and you will almost certainly like the results better in any case considering how much effort is required to trip the schrader valve, not to mention you do not have my permission to use this regulator for those purposes. I do very strongly endorse having a 100% separate from your SCUBA spare-air type rig for a rush to the surface should you experience a main equipment failure, also for people piloting aircraft over water in case of ditching and submerged escape(in addition to life preserver, raft, EPIRB, radio, and survival kit) or even 4x4ing where there is a possibility that the vehicle could end up submerged. This is not the basis for that equipment though. I use a regular SpareAir for SCUBA diving and keep a Navy surplus Aqualung SEA when piloting small aircraft over water.
Demand valves and positive pressure demand valves are also used in firefighting, environmental suit, and mining SCBA rigs, demand valve oxygen add is also used in closed loop C02 scrubbing rigs in space suits, escape rigs, and rebreather diving systems. Demand valves are found in many gas and liquid systems, you could also use this to simply measure or switch based on pressure or vacuum rather than a adding Schrader valve. Use it for any other quick and dirty same day proof of concept reduction to practice as long as nobody threatens anyone's life safety or property with it.
The mechanism is explained here:https://en.wikipedia.org/wiki/Diving_regulator
andhttps://en.wikipedia.org/wiki/Schrader_valve
and
start at 7:00 for the second stage https://www.youtube.com/watch?v=dEaRXTjV9qM
The regulator works like this:
Sucking air from the mouthpiece drops pressure in the sealed regulator body,
the air or water outside pushes inwards the rubber diaphragm which is sealed against the valve block body
The pressure difference also presses the flapper exhaust valve shut
The diaphragm pushes against the pusher disk which centers diaphragm push pressure against
the valve lever
the valve lever is pushed backwards
pivots and
the push pin on the lever pushes against the Schrader valve pin
the Schrader valve opens
air enters the regulator through the schrader valve from
the air hose or tank for as long as there is suction
the entering air balances the suction until
the lungs fill
the suction stops,
inside and outside pressure are again balanced
the diaphragm returns to normal position and
the lever returns to a normal position
the valve closes
then the diver exhales
the exhaled air along with any water in the regulator body exits through the one way flapper valve over the vent
the inhale exhale cycle repeats until the compressed air supply is exhausted
You can also push through the hole in the front cover exposing the rubber diaphragm to purge your regulator, though with the carbonated beverage bottle setup it is not like you have to air to waste with a purge, but if you are making a demo which sources from an air tank or compressed air system it is an easy way to functionally demonstrate without sucking directly on the regulator.
Edits
7-18, upgraded everything to 2.0 added assembly screw holes did some test prints and made the valve block work though requires some trim on the pin pusher, actually activates the pin vs v1, bicycle tire Schrader valve screws tight into valve block now. I hope to do a v3 with a m2 screw rather than plastic on the lever to give better adjustability. Added pusher disk for between diaphragm and valve lever and to make sucking air easier.
7-20, edited the back cover again so that you just put a membrane of rubber over the valve&body and sandwich it with the mouthpiece part. It works when tested but leaks on inspiration and needs a better seal at the back and possibly around the front diaphragm. I did a bead of chewing gum sandwiched between the body and mouthpiece opening in keeping with the available at a supermarket rules. Everything secured with round head wood screws.
7-21, Learned something about pneumatics and FDM printing, it turns out that the body, ABS printed at 100%, 0.5mm layers, 250C is so porous that it requires sealing to prevent water entering the regulator. I am soaking some acetone into the walls to see if that is sufficient, then had to use an ABS acetone paste and caulked the inner walls with that. System is now well sealed, trimmed the diaphragm to fit inside the outer protective cap so it is easier to re-assemble, going to bake at 60c to dive off the acetone. once the acetone is gone I think I can call this finished. Tested in a pool, it releases a bit slowly from a 100psi soda bottle, certainly not the familiar hard rushing air blast from a real high pressure SCUBA rig but works as a demo, the sealing held and the exhaust valve works too, the regulator stays dry between between the sealing and purging any leak water on exhale.
8-3, v3.0 Enlarged the screw holes and made thick housings for them as well as moving them outwards to keep the main wall inner integrity and keep it smooth to make sealing easier. added O-ring groove around mouthpiece mating area and six screw holes use with rubber washers or o-rings. Left v2.0 files as they have been field tested successfully, v2.0 also works with simple wood screws.
8-3.2 Did a v3.5 body and split off the valve activator arm as it's own file and replace the plastic valve pusher nub with a machine screw.
8-3.3 v3.6 mod on the valve block body assembly, just added a stop block to prevent the valve activator from bending or breaking if pushed too hard, not likely from sucking against the diaphragm but makes me feel better when pushing the purge valve.
A cheap demo SCUBA tank:
We neutralized the buoyancy of the ~1.5l softdrink bottle air tank with a 2kg sledgehammer head, so obviously it held 2l of air displacing 2l or 2kg of water; buoyancy was perfectly neutral and the weighted bottle would hang in the water wherever placed. the tank was made by wrapping a 1.5l carbonated drink bottle with 3M nylon strapping tape. we drilled the cap and removed the seal disk. We cut the schrader valve and the rubber disc where it attaches to the innertube from a bicycle innertube and removed the valve core. The valve stem was pushed through the hole in the bottle cap until the disc was forward of the cap threads, then the bottle cap was screwed down seating the rubber disc against the bottle opening. Rubber gas hose was hose clamped onto the protruding schrader valve stem. A second bicycle valve stem with the attachment disc trimmed off was hose clamped at the end of the hose, this one with the schrader valve core intact. the system is filled through the functional schrader valve at the end of the hose with a bicycle pump to 100psi; once full the valve is screwed into the regulator until air is heard escaping, then back off unscrewing until the air is no longer heard. We moved the hose to the point where the threads had a bit of friction when fully tightened speeding assembly.
Again I must stress that even with these proposed upgrades this regulator was designed as an educational demo and I would not want to hear of it being used to dive, it is not designed or tested for use at depth. I have no idea what the actual pressure rating for a cheap bicycle schrader valve is, or gas hose but I would not imagine anyone designing over 150psi/20bar. Be smart only use diving life support gear from a trusted modern manufacturer source with a known and logbooked history, your life depends on it. Also take a SCUBA refresher class from a real instructor on a regular basis to shake off your bad, dangerous, or deadly habits.
Perhaps posting this thing will inspire a trained, experienced, and certified engineer who is willing to take on the perilous legal responsibility which many countries put onto makers to review, test, fork, and release this design as certified or endorsed as safe to dive; until then I am the only person with permission to print for human diving purposes if that even turns out to be legal, all others are pirating my design if they dive or even breathe with it or use it in a design which could ever be used or accessed by a human or animal. For you all this is a functional demonstrator model no more usable for real world application than the printable jet engine models found on thingiverse. I simply do not have the deep pockets or insurance coverage to accept the liability to ever release this as a working device.
Daydreaming/sketch notes:
It would be fun to find a CO2 tank for a soda fountain and fill it using a scavenged refrigerator pump with an air filter on the intake side. Most can produce 600-800psi and that is about the typical room temp pressure of compressed CO2 so is a good match for available hardware. This would require a first stage regulator to take tank pressure down to about 200PSI for this regulator. Might print in PLA and do al lost PLA cast in brass and lathe/drill&tap to spec.
I might also modify a smaller seltzer maker CO2 bottle adding a first stage, on/off valve, gauge, and a fill port and carry it like a spare-air along with a regular dive rig for my own(and nobody else's) testing purposes at depth.
If I do that then we also need a pressure gauge, a depth gauge is easy marking a plastic tube with 1/2 way at 33ft or 10m 3/4 the way at 66ft/20m etc. and a luminous compass.
Of course these pressures get dangerous fast so perhaps better to stick with a commercial first stage.
WARNING!! I DO NOT GIVE PERMISSION FOR HUMAN OR ANIMAL USE!!! These terms affect the user license and is in addition to and overriding to any terms of the use license. The permissive license only covers the digital files, any real things printed or made in any other way are your own responsibility and may not be used for human or animal purposes or any use which could in any way confer liability to myself my employer or anyone else other than the end users. Only people over the legal age of consent and contractual obligation in both my and their jurisdictions and any jurisdictions of use or legal responsibility may use these files. What I am saying simply is these files if somehow used to make real things are too dangerous for ordinary people for so many reasons do not imperil lives or property, there is no point suing anyone if you did something illegal like pirating these digital files and knowledge for purposes not intended. This is a litigious and ignorant world, the digital files are free-libre but there are limits on using the 3D models to make real world objects for prohibited uses
OpenSCAD files for an easy to source and inexpensive DIY demand low pressure regulator I intend for my personal demonstration use with 120PSI filled 2l carbonated softdrink bottles or a long hose and a home workshop air tank/compressor. Regulator valve lever is included with the inner_mechanism file until v3. Just print this and acquire a blown bicycle tire of sufficient diameter to scavenge the valve and rubber and some wood screws. A supermarket kiddy pool snorkel is an easy way to find a mouthpiece just snip it to length and zip-tie on. The Schrader valve pin pusher on the pivot lever requires some trimming to function correctly. May require sealing the printed body, as my printed walls were so porous that the regulator would flood with water when inspiring, sealing fixed the issue.
Needs a round rubber diaphragm to press the demand lever(bicycle inner-tube rubber) and a bicycle tire Shrader valve to actually do the precision work of the demand valve, a pin for the regulator valve lever, a scuba mouthpiece (or hack one off of a supermarket snorkel), as well as a bit more rubber innertube scrap for a flapper valve for the exhale port. V2.0 files are printed and tested, the v3.x stuff looks nicer,stronger, and better designed IMHO but is vaporware for now and may require a wider sheet of rubber, comment if you do test them. Just to be clear the only precision part in this regulator is a factory made Schrader valve, everything else is just there to press that pin to release breathing air or to valve out any exhaust air and water in the regulator at exhale.
To make a demo soda bottle pressure vessel I removed the valve core and left the rubber round skirt intact to make the seal, I had a 50% success rate making the seal actually hold so I suggest grabbing a few if possible, to this I attached one end of the air hose. At the regulator end I threaded the intact and functional but with circular tube side skirt trimmed off valve stem into the valve block until I could activate the schrader valve by pushing the purge button(hole in regulator where you can push the diaphragm) then I valved out the air, once empty I loosened the clamp and adjusted the hose as a stop collar so I could easily unscrew the valve block and the bottle could be pressurized with a tire pump and have it stop at the correct position.
I added a terrible laptop touchpad freehand graphic to help visualize how simple this and most second stage regulators are. Do you know how hard it is to draw an arrow with a touchpad?!
I only give permissive license to take this these files for academic study and educational demonstration models on how a second stage demand regulator works, I do not give permission to print or use as SCUBA systems or any use for humans or animals. Our lungs are surprisingly fragile and drowning, air embolism, or lung injury are actually pretty easy when dealing with compressed air and depth, especially to untrained divers so don't use this it is a science demo not a real regulator for human use. This is somewhat inspired by an old Soviet rebreather oxygen demand add valve design which used a schrader valve which I liked because you can get Schrader valves anywhere, I seem to remember some Scott Aerospace fire/mine SCBAs using a schrader too. Beyond using a schrader valve, and a lever actuated by a diaphragm it is a clean sheet design without any reference; water goes down, air goes up, pressure differential pushes diaphragms, flapper valves vent only one way, levers push pins, open valves vent higher pressure. Despite linking to a ScubaPro youtube video to show how a commercial regulator is assembled and works this design has nothing to do with ScubaPro and is not inspired in any way by any of their designs, it was added after the fact for educational purposes.
If you need a real acquire-to-use second stage regulator for a scuba or vehicle/aircraft submerged water escape rig buying used and getting serviced is so cheap and you will almost certainly like the results better in any case considering how much effort is required to trip the schrader valve, not to mention you do not have my permission to use this regulator for those purposes. I do very strongly endorse having a 100% separate from your SCUBA spare-air type rig for a rush to the surface should you experience a main equipment failure, also for people piloting aircraft over water in case of ditching and submerged escape(in addition to life preserver, raft, EPIRB, radio, and survival kit) or even 4x4ing where there is a possibility that the vehicle could end up submerged. This is not the basis for that equipment though. I use a regular SpareAir for SCUBA diving and keep a Navy surplus Aqualung SEA when piloting small aircraft over water.
Demand valves and positive pressure demand valves are also used in firefighting, environmental suit, and mining SCBA rigs, demand valve oxygen add is also used in closed loop C02 scrubbing rigs in space suits, escape rigs, and rebreather diving systems. Demand valves are found in many gas and liquid systems, you could also use this to simply measure or switch based on pressure or vacuum rather than a adding Schrader valve. Use it for any other quick and dirty same day proof of concept reduction to practice as long as nobody threatens anyone's life safety or property with it.
The mechanism is explained here:https://en.wikipedia.org/wiki/Diving_regulator
andhttps://en.wikipedia.org/wiki/Schrader_valve
and
start at 7:00 for the second stage https://www.youtube.com/watch?v=dEaRXTjV9qM
The regulator works like this:
Sucking air from the mouthpiece drops pressure in the sealed regulator body,
the air or water outside pushes inwards the rubber diaphragm which is sealed against the valve block body
The pressure difference also presses the flapper exhaust valve shut
The diaphragm pushes against the pusher disk which centers diaphragm push pressure against
the valve lever
the valve lever is pushed backwards
pivots and
the push pin on the lever pushes against the Schrader valve pin
the Schrader valve opens
air enters the regulator through the schrader valve from
the air hose or tank for as long as there is suction
the entering air balances the suction until
the lungs fill
the suction stops,
inside and outside pressure are again balanced
the diaphragm returns to normal position and
the lever returns to a normal position
the valve closes
then the diver exhales
the exhaled air along with any water in the regulator body exits through the one way flapper valve over the vent
the inhale exhale cycle repeats until the compressed air supply is exhausted
You can also push through the hole in the front cover exposing the rubber diaphragm to purge your regulator, though with the carbonated beverage bottle setup it is not like you have to air to waste with a purge, but if you are making a demo which sources from an air tank or compressed air system it is an easy way to functionally demonstrate without sucking directly on the regulator.
Edits
7-18, upgraded everything to 2.0 added assembly screw holes did some test prints and made the valve block work though requires some trim on the pin pusher, actually activates the pin vs v1, bicycle tire Schrader valve screws tight into valve block now. I hope to do a v3 with a m2 screw rather than plastic on the lever to give better adjustability. Added pusher disk for between diaphragm and valve lever and to make sucking air easier.
7-20, edited the back cover again so that you just put a membrane of rubber over the valve&body and sandwich it with the mouthpiece part. It works when tested but leaks on inspiration and needs a better seal at the back and possibly around the front diaphragm. I did a bead of chewing gum sandwiched between the body and mouthpiece opening in keeping with the available at a supermarket rules. Everything secured with round head wood screws.
7-21, Learned something about pneumatics and FDM printing, it turns out that the body, ABS printed at 100%, 0.5mm layers, 250C is so porous that it requires sealing to prevent water entering the regulator. I am soaking some acetone into the walls to see if that is sufficient, then had to use an ABS acetone paste and caulked the inner walls with that. System is now well sealed, trimmed the diaphragm to fit inside the outer protective cap so it is easier to re-assemble, going to bake at 60c to dive off the acetone. once the acetone is gone I think I can call this finished. Tested in a pool, it releases a bit slowly from a 100psi soda bottle, certainly not the familiar hard rushing air blast from a real high pressure SCUBA rig but works as a demo, the sealing held and the exhaust valve works too, the regulator stays dry between between the sealing and purging any leak water on exhale.
8-3, v3.0 Enlarged the screw holes and made thick housings for them as well as moving them outwards to keep the main wall inner integrity and keep it smooth to make sealing easier. added O-ring groove around mouthpiece mating area and six screw holes use with rubber washers or o-rings. Left v2.0 files as they have been field tested successfully, v2.0 also works with simple wood screws.
8-3.2 Did a v3.5 body and split off the valve activator arm as it's own file and replace the plastic valve pusher nub with a machine screw.
8-3.3 v3.6 mod on the valve block body assembly, just added a stop block to prevent the valve activator from bending or breaking if pushed too hard, not likely from sucking against the diaphragm but makes me feel better when pushing the purge valve.
A cheap demo SCUBA tank:
We neutralized the buoyancy of the ~1.5l softdrink bottle air tank with a 2kg sledgehammer head, so obviously it held 2l of air displacing 2l or 2kg of water; buoyancy was perfectly neutral and the weighted bottle would hang in the water wherever placed. the tank was made by wrapping a 1.5l carbonated drink bottle with 3M nylon strapping tape. we drilled the cap and removed the seal disk. We cut the schrader valve and the rubber disc where it attaches to the innertube from a bicycle innertube and removed the valve core. The valve stem was pushed through the hole in the bottle cap until the disc was forward of the cap threads, then the bottle cap was screwed down seating the rubber disc against the bottle opening. Rubber gas hose was hose clamped onto the protruding schrader valve stem. A second bicycle valve stem with the attachment disc trimmed off was hose clamped at the end of the hose, this one with the schrader valve core intact. the system is filled through the functional schrader valve at the end of the hose with a bicycle pump to 100psi; once full the valve is screwed into the regulator until air is heard escaping, then back off unscrewing until the air is no longer heard. We moved the hose to the point where the threads had a bit of friction when fully tightened speeding assembly.
Again I must stress that even with these proposed upgrades this regulator was designed as an educational demo and I would not want to hear of it being used to dive, it is not designed or tested for use at depth. I have no idea what the actual pressure rating for a cheap bicycle schrader valve is, or gas hose but I would not imagine anyone designing over 150psi/20bar. Be smart only use diving life support gear from a trusted modern manufacturer source with a known and logbooked history, your life depends on it. Also take a SCUBA refresher class from a real instructor on a regular basis to shake off your bad, dangerous, or deadly habits.
Perhaps posting this thing will inspire a trained, experienced, and certified engineer who is willing to take on the perilous legal responsibility which many countries put onto makers to review, test, fork, and release this design as certified or endorsed as safe to dive; until then I am the only person with permission to print for human diving purposes if that even turns out to be legal, all others are pirating my design if they dive or even breathe with it or use it in a design which could ever be used or accessed by a human or animal. For you all this is a functional demonstrator model no more usable for real world application than the printable jet engine models found on thingiverse. I simply do not have the deep pockets or insurance coverage to accept the liability to ever release this as a working device.
Daydreaming/sketch notes:
It would be fun to find a CO2 tank for a soda fountain and fill it using a scavenged refrigerator pump with an air filter on the intake side. Most can produce 600-800psi and that is about the typical room temp pressure of compressed CO2 so is a good match for available hardware. This would require a first stage regulator to take tank pressure down to about 200PSI for this regulator. Might print in PLA and do al lost PLA cast in brass and lathe/drill&tap to spec.
I might also modify a smaller seltzer maker CO2 bottle adding a first stage, on/off valve, gauge, and a fill port and carry it like a spare-air along with a regular dive rig for my own(and nobody else's) testing purposes at depth.
If I do that then we also need a pressure gauge, a depth gauge is easy marking a plastic tube with 1/2 way at 33ft or 10m 3/4 the way at 66ft/20m etc. and a luminous compass.
Of course these pressures get dangerous fast so perhaps better to stick with a commercial first stage.
Similar models
thingiverse
free
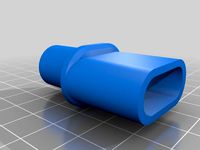
Scuba regulator mouthpiece to 16 mm tube by kdiy
...ece to 16 mm tube by kdiy
thingiverse
connect a standard scuba diving regulator mouthpiece to a tube with a 16mm inner diameter.
thingiverse
free
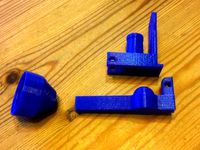
Float valve for hose by JMK54
...attached a float ( levier + 4mm diameter rod + float)
i use a rubber ball stuck on piece parts such as seal ( red in the picture)
3dwarehouse
free
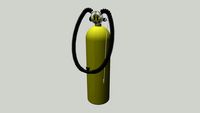
Vintage Dual-hose scuba regulator setup
...tsuit #tank #regulator #dual_hose #compressed_air #air #sports #aluminum #mouthpiece #reserve #backpack #breath #us_divers #diver
3dwarehouse
free
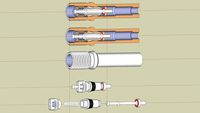
Schrader valve
...schrader valve
3dwarehouse
schrader valve (used on automobile and bicycle tyres) #schrader_valve_tyre
grabcad
free

Air pressure regulator and solenoid valves
...air pressure regulator and solenoid valves
grabcad
air pressure regulator and solenoid valves
grabcad
free

Presta Valve
...ir. instead, the valve's gasket forms an air tight seal with the rim and the compressed air inflates the bicycle tire itself.
grabcad
free

Schrader valve
...schrader valve
grabcad
schrader valve of bicycle
grabcad
free

Air Regulator
...air regulator
grabcad
to regulate pressure output from bottle to pneumatic, and to filter from water
grabcad
free

Pressure regulator 213 series Concoa
... regulator 213 series concoa
grabcad
2- stage pressure regulator, concoa 213 series with cylinder connection and diaphragm valve
thingiverse
free
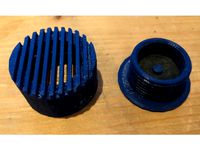
breathing valve (exhale) for self-made masks by r_lauber
...f-made masks by r_lauber
thingiverse
it's the exhale valve for a self-made mask.
seal is punched out of an old bicycle tire.
Biketool
thingiverse
free
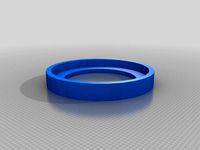
Bezel cover by Biketool
... disguises an expensive watch with some plastic if traveling in a high crime area without reducing the timekeeping functionality.
thingiverse
free
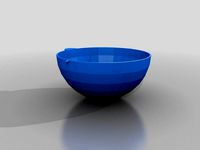
Popcorn Air Popper Measuring/Dump Cup by Biketool
...ol
thingiverse
70mm popcorn dump/measuring cup and cap for a grandix air popper, has pivots and handle tab. made with openscad.
thingiverse
free
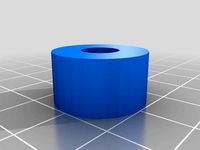
20mm Dishwasher Power Button by Biketool
...ears. the button has a small slot on the back which sticks onto an extension on the switch, view the model to understand better.
thingiverse
free
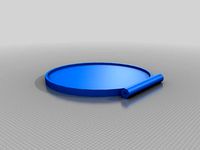
Helmet Mounted Bicycle Mirror by Biketool
...generic mirror mount, more common mirror disc mount for one inch 25.4mm mirror discs, and a stencil for diy cutting mirror discs.
thingiverse
free
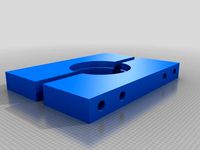
11.5 Ligne Watchmakers Movement Holder by Biketool
...6mm) such as a miyota 85xx movements or a chinese dg28xx/38xx movements so that you have a stable place to do your delicate work.
thingiverse
free
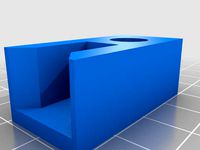
Window Frame Locking Lug by Biketool
...part that is outside the mounting track, now if kids slam it with the locking lugs down i need to realign it, no big deal though.
thingiverse
free
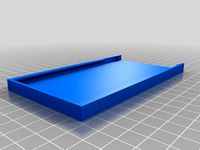
FX-260 Calculator, Slide on Cover by Biketool
...borted a print as my bed was out of allignment, so caveat emptor but more importantly equum dono accipitis ne dentes inspicerent.
thingiverse
free
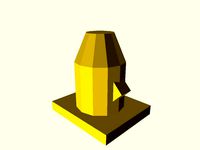
Dash panel gromet (Toyota?) by Biketool
... the abs hot ~255c and at a high enough % to get the layers to stick properly, i also soaked in acetone to strengthen the layers.
thingiverse
free
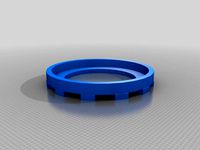
Bezel/Clock Fonts and a 41mm Bezel Cap by Biketool
...30, 35, 40, 45, 50, 55, a round pip, a bar, and a triangle.
attaching an incomplete gen2 watch bezel cap with blank 5min markers.
thingiverse
free
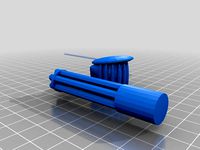
OpenSCAD Fast Predator Head Demo by Biketool
... five lines. not intended for printing.
use thingiview to rotate as thingiverse rendered the model looking away from the viewer.
Scuba
3d_export
$32
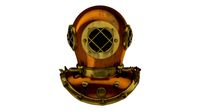
Old scuba helmet
...old scuba helmet
3dexport
old scuba helmet - pbr 4k - uv unwrapped
3ddd
$1
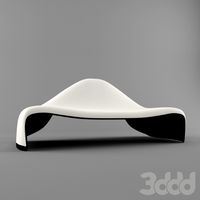
Domodinamika / Scuba
...ль кресла scuba от domodinamika.
моделирование по фотографии. размеры сохранены. цветовое решение изменено, по просьбе заказчика.
turbosquid
$29
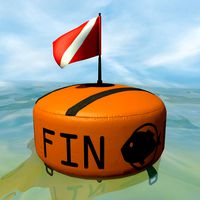
Scuba Buoy
... available on turbo squid, the world's leading provider of digital 3d models for visualization, films, television, and games.
turbosquid
$15
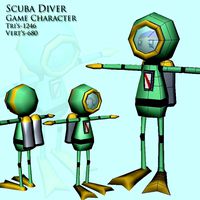
Scuba Diver
... available on turbo squid, the world's leading provider of digital 3d models for visualization, films, television, and games.
turbosquid
$10
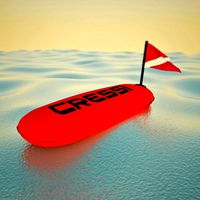
SCUBA BUOY
... available on turbo squid, the world's leading provider of digital 3d models for visualization, films, television, and games.
3d_ocean
$12

Scuba Gear
...w polygonal models, easy to animate. - poly count: 1612 ( combined ) - formats: max /obj /fbx/3ds/dxf - high detail was preser...
3d_export
$19
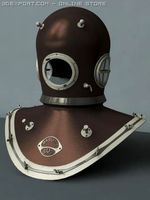
Scuba helmet 3D Model
...scuba helmet 3d model
3dexport
scuba helmet underwater diving diving-apparatus sea
scuba helmet 3d model godzik 14298 3dexport
3d_export
$25
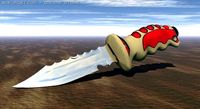
Scuba Diving Knife 3D Model
...scuba diving knife 3d model
3dexport
scuba diving knife sword dagger
scuba diving knife 3d model shaputer 30796 3dexport
turbosquid
$19
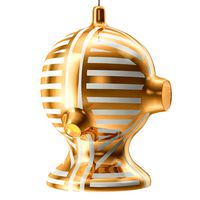
Bosa Scuba Model A
...del bosa scuba model a for download as 3ds, max, obj, and fbx on turbosquid: 3d models for games, architecture, videos. (1221101)
cg_studio
$79
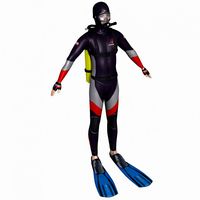
Scuba Diver3d model
... jacket realtime low poly
.obj .max .fbx - scuba diver 3d model, royalty free license available, instant download after purchase.
Demand
3d_export
$9

wall lamp 02
...wall lamp 02 3dexport copy to demand wall lamp 3d...
3d_export
$5

donut
...donut 3dexport donut donut donut donut. suitable for some non-demandng ...
3d_export
$5
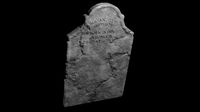
Tombstone with inscription
...tombstone with an inscription that can be changed by demand easy to use in your...
3d_export
free
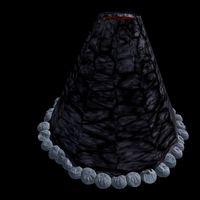
volcano
...3dexport a volcano surrounded by stones<br>perfect for simple, unre demandng ...
3d_export
$20
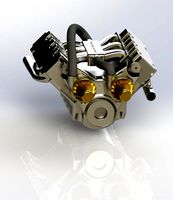
V6 engine
...sldasm format. i can also convert the format on demand ...
3d_export
$9
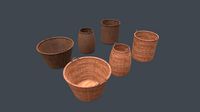
Pack Baskets
...games, architectural renderings, animations or any other project that demand fast rendering. texture 2k. two kinds of textures, lighter...
3d_export
$5
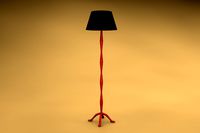
floor lamps brave and eco
...floor lamps made in different styles, but equally in demand in interior design. these models are made in accordance...
3d_ocean
$16
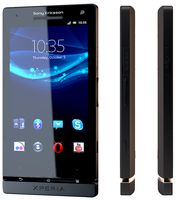
Sony Ericsson Xperia S
...poly retained so smoothness can be adjusted according to demand. ...
3d_export
$5

honda prelude 5
...in 2000 due to high production costs and low demand all models were produced with front-wheel drive and only...
3d_ocean
$89
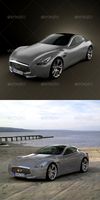
Infiniti Essence 2011
...taken to the extremes to satisfy the world’s most demandng car enthusiasts…...
Regulator
turbosquid
$39
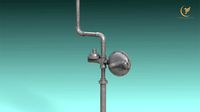
Gas Regulator
...gulator for download as ma, max, 3ds, fbx, gltf, obj, and stl on turbosquid: 3d models for games, architecture, videos. (1633579)
turbosquid
$30
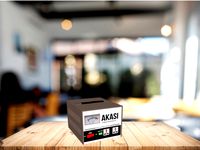
Automatic Voltage Regulator
...free 3d model automatic voltage regulator for download as obj on turbosquid: 3d models for games, architecture, videos. (1240422)
3d_export
$100
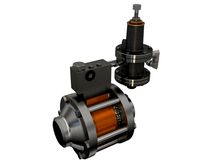
Gas Pressure Regulator 3D Model
...gas pressure regulator 3d model
3dexport
gas pressure regulator
gas pressure regulator 3d model bnv84 32757 3dexport
turbosquid
$24
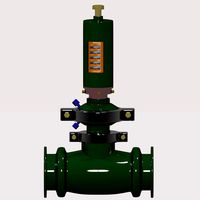
Flow regulator AGZU
... available on turbo squid, the world's leading provider of digital 3d models for visualization, films, television, and games.
turbosquid
$10
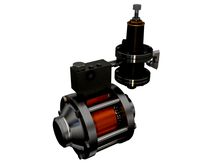
gas pressure regulator
... available on turbo squid, the world's leading provider of digital 3d models for visualization, films, television, and games.
3d_export
$5
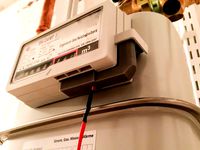
gas meter with regulator
...gas meter with regulator
3dexport
american gas meter is one of the mechanical gas meters
turbosquid
$49
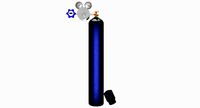
Compressed Gas Cylinder and Regulator
...odel compressed gas cylinder and regulator for download as ma on turbosquid: 3d models for games, architecture, videos. (1170670)
3ddd
$1
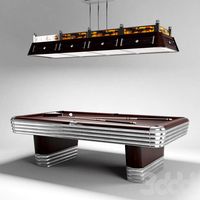
Centennial Regulation Pool Table by RI Anderson
...by ri anderson
3ddd
brunswick
бильярдный стол в стиле ар-деко centennial regulation pool table by ri anderson
размеры 264x147x81h
3d_export
$80
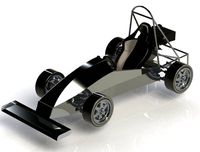
fsae race car assembly according to regulation
...ll measures according to the regulation. part of the descriptions and part names are in portuguese any questions, make a comment.
3d_export
$13
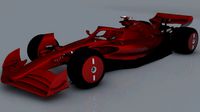
Formula 1 2022 concept model 2022 fia f1 regulations
...you choosing my 3d models and hope they will be of use. i look forward to continuously dealing with you. sincerely yours, hugoalf
V3
3d_export
$5
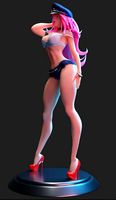
Poison-v3
...poison-v3
3dexport
poison-v3
3ddd
$1
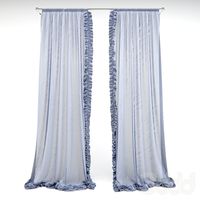
Curtain v3
...curtain v3
3ddd
полупрозрачная штора v3
turbosquid
free
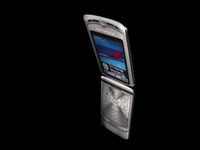
v3
... available on turbo squid, the world's leading provider of digital 3d models for visualization, films, television, and games.
3d_export
$5
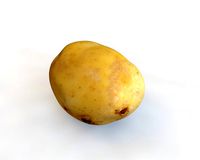
potato v3
...potato v3
3dexport
turbosquid
$2
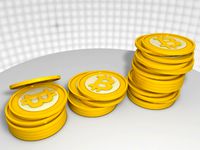
Bitcoin v3
...
royalty free 3d model bitcoin v3 for download as c4d and prj on turbosquid: 3d models for games, architecture, videos. (1182845)
turbosquid
$10
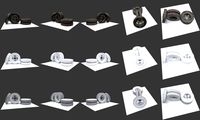
Wheel V3S
...e 3d model wheel v3s for download as 3ds, obj, fbx, and blend on turbosquid: 3d models for games, architecture, videos. (1344250)
turbosquid
$6
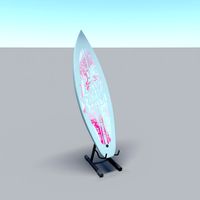
surfboard V3
...e 3d model surfboard v3 for download as ma, max, obj, and fbx on turbosquid: 3d models for games, architecture, videos. (1168641)
turbosquid
$30
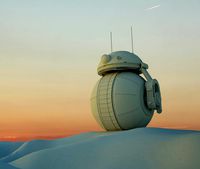
Droid V3
... available on turbo squid, the world's leading provider of digital 3d models for visualization, films, television, and games.
turbosquid
$19
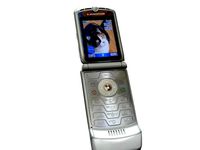
MOTO V3
... available on turbo squid, the world's leading provider of digital 3d models for visualization, films, television, and games.
turbosquid
$10
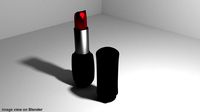
Lipstick v3
... available on turbo squid, the world's leading provider of digital 3d models for visualization, films, television, and games.
Pressure
3d_export
$5
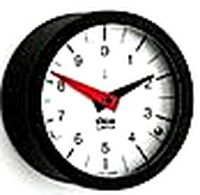
pressure gauge
...pressure gauge
3dexport
pressure gauge
3d_export
$40
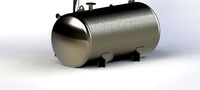
Pressure Vessel
...pressure vessel
3dexport
pressure vessel assembly render 3d modelling design
3d_export
$5
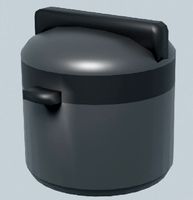
Pressure cooker
...pressure cooker
3dexport
simple low-poly pressure cooker model. not removable parts.
3d_export
$5
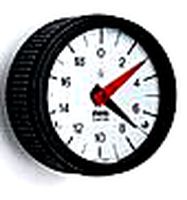
protected pressure gauge
...protected pressure gauge
3dexport
protected pressure gauge
turbosquid
$20
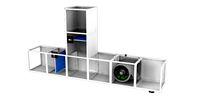
PRESSURIZATION FAN
...
royalty free 3d model pressurization fan for download as max on turbosquid: 3d models for games, architecture, videos. (1269534)
turbosquid
$20
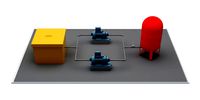
Pressurization Pumps
...oyalty free 3d model pressurization pumps for download as max on turbosquid: 3d models for games, architecture, videos. (1270559)
turbosquid
$23
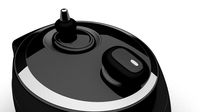
Pressure cooker
...ee 3d model pressure cooker for download as max, obj, and fbx on turbosquid: 3d models for games, architecture, videos. (1440991)
turbosquid
$25

pressure cooker
... available on turbo squid, the world's leading provider of digital 3d models for visualization, films, television, and games.
turbosquid
$3
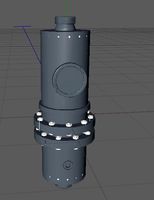
Pressure Controller
... available on turbo squid, the world's leading provider of digital 3d models for visualization, films, television, and games.
turbosquid
$2
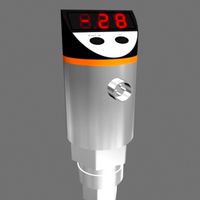
Pressure Switch.max
... available on turbo squid, the world's leading provider of digital 3d models for visualization, films, television, and games.
Functional
turbosquid
$1
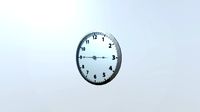
functional clock
...d
royalty free 3d model functional clock for download as fbx on turbosquid: 3d models for games, architecture, videos. (1378928)
turbosquid
$5
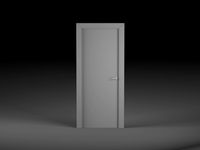
functional door
... model functional door for download as 3ds, obj, c4d, and stl on turbosquid: 3d models for games, architecture, videos. (1483785)
3d_export
$5

multi function box
...multi function box
3dexport
it is multi function box in iges format
3ddd
$1
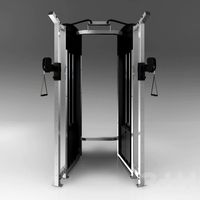
Fitness Equipament - Functional
...fitness equipament - functional
3ddd
треножер
fitness equipament functional, modeled from real model.
turbosquid
$19
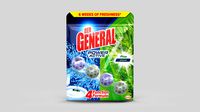
Four function formula
...
royalty free 3d model four function formula for download as on turbosquid: 3d models for games, architecture, videos. (1154985)
turbosquid
$1
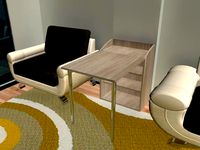
functional work table
...yalty free 3d model functional work table for download as max on turbosquid: 3d models for games, architecture, videos. (1198733)
3d_export
free
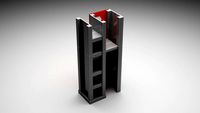
Multi-functional anaquel
...multi-functional anaquel
3dexport
https://www.dock4all.com/
turbosquid
$12
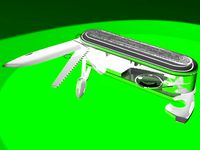
Multi-Function Knife
... available on turbo squid, the world's leading provider of digital 3d models for visualization, films, television, and games.
turbosquid
$9
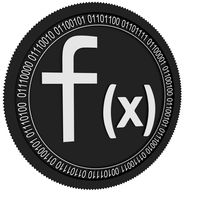
function x black coin
...yalty free 3d model function x black coin for download as max on turbosquid: 3d models for games, architecture, videos. (1457828)
3ddd
free
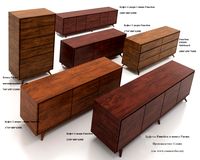
Буфеты Function и комод Parma
...д , тумба , parma
буфеты function и комод parma
6
3d_export
$18
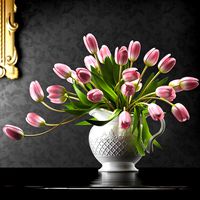
tulip 6
...tulip 6
3dexport
tulip 6
3d_export
$5
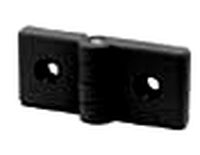
hinge 6
...hinge 6
3dexport
hinge 6
3ddd
$1
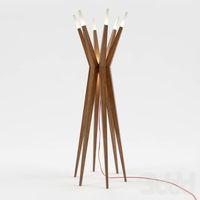
MASIERO / FLASHWOOD STL 6 + 6
...6
3ddd
masiero
торшер flashwood stl 6 + 6 фабрики masiero
http://www.masierogroup.com/c87_697/it/flashwood%20stl%206%20+%206.ashx
turbosquid
$39
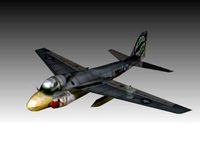
A-6
... available on turbo squid, the world's leading provider of digital 3d models for visualization, films, television, and games.
3ddd
$1
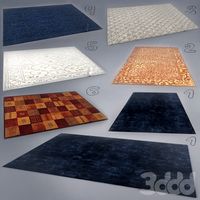
6 ковров
...6 ковров
3ddd
ковры , ковер
6 ковров
turbosquid
$12
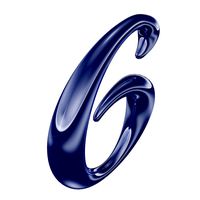
Calligraphic Digit 6 Number 6
...hic digit 6 number 6 for download as max, obj, fbx, and blend on turbosquid: 3d models for games, architecture, videos. (1389336)
turbosquid
$19
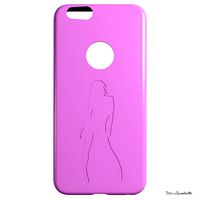
Case For Phone 6 Girl 6
... available on turbo squid, the world's leading provider of digital 3d models for visualization, films, television, and games.
3ddd
free
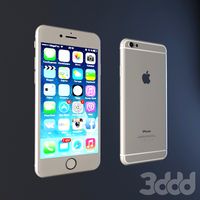
IPhone 6
... 6
3ddd
apple , iphone , телефон
apple iphone 6
3ddd
$1
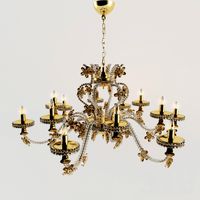
Люстра Masiero classica 6145 6+6
... masiero classica 6145 6+6
3ddd
masiero
люстра - masiero
каталог -сlassica
артикул - 6145 6+6
диаметр - 1300 мм
высота - 600 мм
3ddd
$1
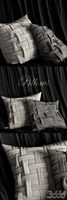
Pillows #6
...pillows #6
3ddd
подушка
pillows #6
3ds max 2011, fbx + textures