GrabCAD

Exhaust manifold micro ammonia cracker for hydrogen engine
by GrabCAD
Last crawled date: 1 year, 11 months ago
Pochari Systems is designing, manufacturing and commercializing the world’s first highly compact ammonia cracker to produce hydrogen on demand from liquid ammonia for hydrogen engine powered cars, trucks and marine propulsion. The cracker uses 7% wt Ruthenium and 10% wt Cesium promoted CeO2 supported catalyst in a microchannel configuration. The cracker specifications are based on Engelbrecht and Chiuta 2018, Chiuta and Everson 2015 and 2016, Di Carlo and Vecchione 2014, and Hill and Murciano 2014.
The activation energy is as low as 75 kJ/mol of NH3 with high cesium promoter loadings on ceric oxide support, which translates into only 7.2 KW/kg of H2 reformed per hour, allowing for 92% of the required energy for decomposition is provided by exhaust heat from the diesel engine.
The amount of ruthenium and cesium needed is very minimal, only 0.0017 kg and 0.005 kg respectively is required to reform 1 kg of hydrogen per hour at the desired efficiency and power density, translating into a cost of only $200 for the raw materials of the catalyst and promoter based on current market prices for a 2 kg/hr cracker, sufficient for a medium-sized vehicle. The cost of the cerium oxide support comprising 83% of the catalyst mass is negligible. Cesium reserves are estimated to be 84,000 tons, with Ruthenium reserves around 5000 tons, since 5x more cesium is used than Ruthenium, the reserves allow for the production of billions of medium-sized car crackers.
Most of the cost of the cracker is found in manufacturing, not raw materials.
Forming the tiny stainless steel microchannels from a solid block is performed by wire electrical discharge machining. Washcoating and packing of the catalyst inside these tiny grooves completes the manufacturing process of a microreactor. Microreactor technology can be thought of as relatively simple compared to battery manufacturing as an example. The only complexities and difficulties arise from the very small dimensions
These small dimensions found in microreactors (as little as 0.15 mm x 0.25 mm) requires elaborate and costly machinery to fabricate, but nonetheless, the cost of the cracker will be approximately $1000-1500 per kg-hour of capacity at high production volumes, of which 15-20% represents material costs.
The ammonia cracker is located on the exhaust manifold for closed-cycle hydrogen diesel engines, utilizing engine exhaust heat supplying 92% of cracker energy needs, with oxy-hydrogen combustion providing the balance.
The volume of the ammonia cracker for 20 kg/hr, enough for a large class-8 semi-truck at full power, takes up only 20 liters, and weighs less than 10 kg!
The cracker is configured in a modular fashion. The modules consist of a housing, each consisting of multiple microchannels inside. The module is placed directly outside of each exhaust outlet on the cylinder head, allowing the very hot exhaust gas to pass directly into the microchannels before cooling down. This allows heating the catalyst bed to provide the necessary activation energy. Each module is connect to four rails, supplying both gaseous ammonia to the cracker, and passing reform gas to the purifier. The two smaller rails provide oxygen and hydrogen to provide heat during startup.
Reactor type: Micro-channel stainless steel
Catalyst: 7% wt Ru 10% wt Cs promoted on CeO2
Ru Catalyst required per Kg hour H2 reformed: 0.001 kg
Ce Catalyst promoter per Kg hour H2 reformed: 0.005 kg
Gravimetric density: 0.50 kg/kg H2-hr
Volumetric density: 1 L/kg H2-hr
Energy consumption: 6 kw/kg H2-hr
Percent of reforming energy from exhaust heat: 92%
Conversion rate: 99.8%
Operating temperature: 500 °C
Additional hydrogen consumed for dissociation: 0%, only during startup.
Ammonia equivalent hydrogen density: 113 kg/m3
Ammonia consumption: 6 kg liquid NH3/kg H2-hr
Startup time: 10 minutes
Cracker cost: $1000/kg-hr capacity
Ruthenium cost: $8000/kg
Cesium cost: $30,000/kg
The activation energy is as low as 75 kJ/mol of NH3 with high cesium promoter loadings on ceric oxide support, which translates into only 7.2 KW/kg of H2 reformed per hour, allowing for 92% of the required energy for decomposition is provided by exhaust heat from the diesel engine.
The amount of ruthenium and cesium needed is very minimal, only 0.0017 kg and 0.005 kg respectively is required to reform 1 kg of hydrogen per hour at the desired efficiency and power density, translating into a cost of only $200 for the raw materials of the catalyst and promoter based on current market prices for a 2 kg/hr cracker, sufficient for a medium-sized vehicle. The cost of the cerium oxide support comprising 83% of the catalyst mass is negligible. Cesium reserves are estimated to be 84,000 tons, with Ruthenium reserves around 5000 tons, since 5x more cesium is used than Ruthenium, the reserves allow for the production of billions of medium-sized car crackers.
Most of the cost of the cracker is found in manufacturing, not raw materials.
Forming the tiny stainless steel microchannels from a solid block is performed by wire electrical discharge machining. Washcoating and packing of the catalyst inside these tiny grooves completes the manufacturing process of a microreactor. Microreactor technology can be thought of as relatively simple compared to battery manufacturing as an example. The only complexities and difficulties arise from the very small dimensions
These small dimensions found in microreactors (as little as 0.15 mm x 0.25 mm) requires elaborate and costly machinery to fabricate, but nonetheless, the cost of the cracker will be approximately $1000-1500 per kg-hour of capacity at high production volumes, of which 15-20% represents material costs.
The ammonia cracker is located on the exhaust manifold for closed-cycle hydrogen diesel engines, utilizing engine exhaust heat supplying 92% of cracker energy needs, with oxy-hydrogen combustion providing the balance.
The volume of the ammonia cracker for 20 kg/hr, enough for a large class-8 semi-truck at full power, takes up only 20 liters, and weighs less than 10 kg!
The cracker is configured in a modular fashion. The modules consist of a housing, each consisting of multiple microchannels inside. The module is placed directly outside of each exhaust outlet on the cylinder head, allowing the very hot exhaust gas to pass directly into the microchannels before cooling down. This allows heating the catalyst bed to provide the necessary activation energy. Each module is connect to four rails, supplying both gaseous ammonia to the cracker, and passing reform gas to the purifier. The two smaller rails provide oxygen and hydrogen to provide heat during startup.
Reactor type: Micro-channel stainless steel
Catalyst: 7% wt Ru 10% wt Cs promoted on CeO2
Ru Catalyst required per Kg hour H2 reformed: 0.001 kg
Ce Catalyst promoter per Kg hour H2 reformed: 0.005 kg
Gravimetric density: 0.50 kg/kg H2-hr
Volumetric density: 1 L/kg H2-hr
Energy consumption: 6 kw/kg H2-hr
Percent of reforming energy from exhaust heat: 92%
Conversion rate: 99.8%
Operating temperature: 500 °C
Additional hydrogen consumed for dissociation: 0%, only during startup.
Ammonia equivalent hydrogen density: 113 kg/m3
Ammonia consumption: 6 kg liquid NH3/kg H2-hr
Startup time: 10 minutes
Cracker cost: $1000/kg-hr capacity
Ruthenium cost: $8000/kg
Cesium cost: $30,000/kg
Similar models
grabcad
free

Microchannel cracker
...microchannel cracker
grabcad
microchannel cracker
3dwarehouse
free
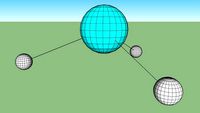
Ammonia
...ammonia
3dwarehouse
the structure of a molecule of ammonia (nh3) #ammonia #molecule #nh3 #shape_of_molecule #structure
cg_trader
$2
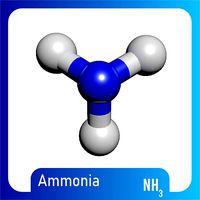
Ammonia 3D Model NH3
...the detailed model having labeling and showing angles between bonds and length of bonds.
white = hydrogen (h)
blue = nitrogen (n)
3dwarehouse
free
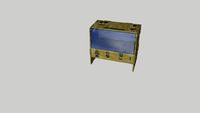
Electrolyzer, Hydrogen Generator, H2 Fueling station
...es, heatings, boilers, converted gazoline cars and all other hydrogen applications. it produces 160 nl per hour dry hydrogen gas.
grabcad
free

ammonia cracker and purifier for PEM fuel cell
...the combustor via a small electrically driven rotary compressor, similar to a turbocharger. the cracker operates at 600-650 c,...
cg_trader
$6
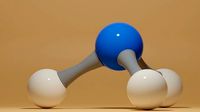
Ammonia Molecule NH3
...cule nh3
cg trader
3d asset ammonia molecule nh3 , formats include obj, fbx, c4d, stl, blend, dae, ready for 3d animation and ot
grabcad
free

Aqua Converter and Ammonia Storage
... two nh3 pressure vessel tanks (28,000-gal & 30,000-gal) support the conversion process as well as trans-loading in and out.
grabcad
free

Microchannel
...microchannel
grabcad
microchannel heat transfer .
grabcad
free

microchannel heat sink
...microchannel heat sink
grabcad
heat transfer enhancement in microchannel heat sink of rib and secondary channel
sketchfab
$6
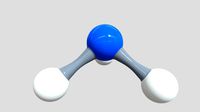
Ammonia Molecular NH3
...end . fbx . obj, c4d,dae,fbx,unity.
thank you. - ammonia molecular nh3 - buy royalty free 3d model by philip storm (@xingyun777)
Ammonia
turbosquid
$3
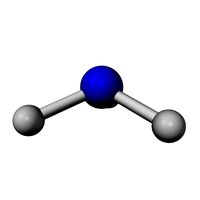
Ammonia
... available on turbo squid, the world's leading provider of digital 3d models for visualization, films, television, and games.
turbosquid
$15
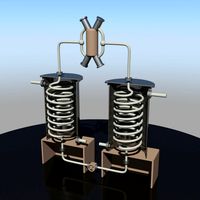
Ammonia Compressor
... available on turbo squid, the world's leading provider of digital 3d models for visualization, films, television, and games.
3d_export
$14
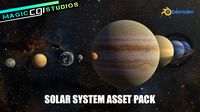
solar system asset pack - blender
...venus - sulfuric acid, jupiter - hydrogen, neptune - ammonia & methane, saturn - water & ammonia, mars -...
sketchfab
$6
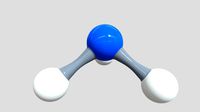
Ammonia Molecular NH3
...end . fbx . obj, c4d,dae,fbx,unity.
thank you. - ammonia molecular nh3 - buy royalty free 3d model by philip storm (@xingyun777)
thingiverse
free
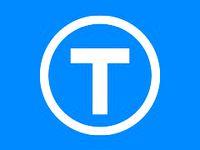
NH3-Ammonia by NW3D
... learning and visualizing the molecular geometry, and how this geometry dictates how the molecule interacts with other molecules.
thingiverse
free
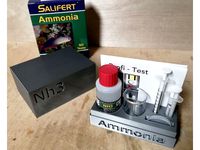
Salifert Profi Test Ammonia storage box by Haggy_23
...ly stowed in this box, after removing the hood, all parts including instructions are easily accessible and nothing can fall over.
thingiverse
free
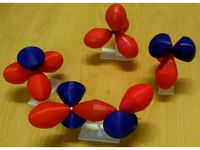
molecule models by Phokas
...molecule models by phokas thingiverse molecule models of methane, ammonia water and hydrogen...
thingiverse
free
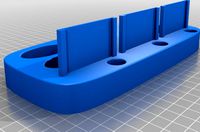
Aquarium API Test Kit Organizer by Squirrelzar
...you have any suggestions. i only included spots for ammonia ( 2 bottles ), nitrite ( 1 bottle ),...
thingiverse
free
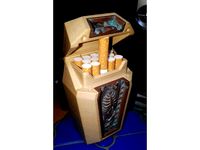
cigarette case coffin by buho29
...(layer 0.1mm) copperfill is oxidized with a mixture of ammonia vinegar and salt shaft used dia:1mm (hole 1.4mm) magnets...
thingiverse
free
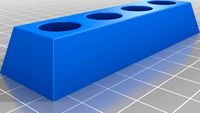
Water test tube holder by ximon
...tube holder by ximon thingiverse note: the symbol for ammonia is incorrect, it should be nh3, i lost the...
Cracker
3d_export
$5
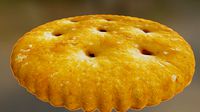
cracker
...cracker
3dexport
cracker obj,fbx,blend
turbosquid
$45
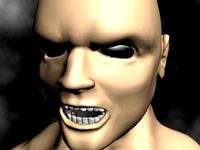
Cracker
... available on turbo squid, the world's leading provider of digital 3d models for visualization, films, television, and games.
turbosquid
$4
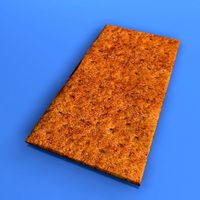
Cracker
... available on turbo squid, the world's leading provider of digital 3d models for visualization, films, television, and games.
turbosquid
$29
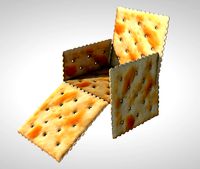
cracker chair
...free 3d model cracker chair for download as 3ds, c4d, and fbx on turbosquid: 3d models for games, architecture, videos. (1513069)
turbosquid
$15
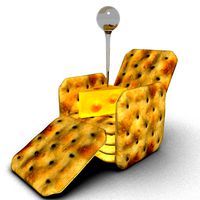
Cheese and Crackers
...d model cheese and crackers for download as max, obj, and fbx on turbosquid: 3d models for games, architecture, videos. (1291101)
turbosquid
$4

Animal Crackers
... available on turbo squid, the world's leading provider of digital 3d models for visualization, films, television, and games.
turbosquid
$1
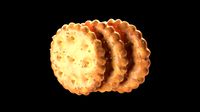
crackers cookies
... available on turbo squid, the world's leading provider of digital 3d models for visualization, films, television, and games.
3d_ocean
$5

Cream Cracker
... normal and specular jpg maps are all included in this download! displacement map can also be used as a bump map. created in c...
3d_ocean
$5
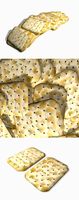
Plain Cracker
... normal and specular jpg maps are all included in this download! displacement map can also be used as a bump map. created in c...
3d_ocean
$5
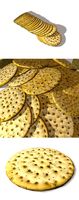
Poppyseed Cracker
...ent, normal and specular jpg maps are all included in this download! displacement map can also be used as a bump map. created ...
Hydrogen
turbosquid
$15
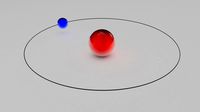
hydrogen
...
royalty free 3d model hydrogen 3d model for download as c4d on turbosquid: 3d models for games, architecture, videos. (1616190)
turbosquid
$10
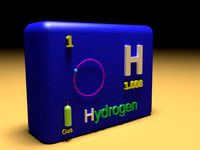
Hydrogen
...alty free 3d model hydrogen for download as 3ds, obj, and fbx on turbosquid: 3d models for games, architecture, videos. (1293493)
turbosquid
$3
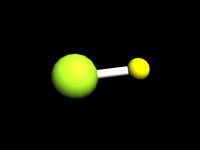
Hydrogen halides
... available on turbo squid, the world's leading provider of digital 3d models for visualization, films, television, and games.
turbosquid
$5
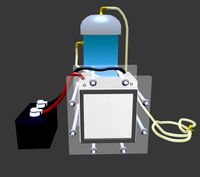
hydrogen generator
... generator for download as 3ds, obj, fbx, blend, dae, and stl on turbosquid: 3d models for games, architecture, videos. (1280110)
3d_export
$5
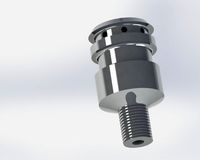
Hydrogen burner 3D Model
...hydrogen burner 3d model
3dexport
hydrogen burner 3d model keep 78880 3dexport
cg_studio
$40

Hydrogen Gas Station3d model
... station3d model
cgstudio
.max - hydrogen gas station 3d model, royalty free license available, instant download after purchase.
3d_export
$19
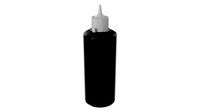
Hydrogen Peroxide Plastic Bottle
...; x 1.74" x 5.52"<br>- model parts: 2<br>- material count: 2<br>- xform: yes<br>- boxtrick: yes
3d_export
$6
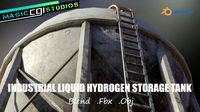
industrial liquid hydrogen spherical storage tank
...color, metallic, roughness, normal + height maps if you wish to use them hope you enjoy the model thanks again for your interest!
3d_export
$5

Formula of water - H-2-O
...are animated - two oxygens fly around a large hydrogen their chemical stick-bonds glow.<br>these molecules are suitable for designing...
3d_export
$80

Gas balloon 3D Model
...gas balloon 3d model 3dexport gas balloon blimp helium hydrogen balloons baloon gas balloon 3d model tartino 29189...
Manifold
3d_export
$25
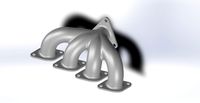
exhaust manifold
...exhaust manifold
3dexport
this is a 3d design of an exhaust manifold used in automobile.
3ddd
free
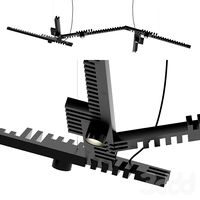
Manifold
...manifold
3ddd
ingo maurer
дизайнер: axel schmid
производитель: ingo maurer
turbosquid
$96
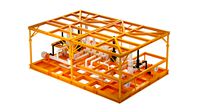
Subsea Manifold
...l subsea manifold for download as max, fbx, 3ds, dwg, and obj on turbosquid: 3d models for games, architecture, videos. (1664666)
3d_export
free
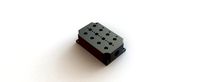
pneumatic manifold block
...atic manifold block
3dexport
modified pneumatic manifold block for shooting particles, using festo valves installed on its face.
3d_export
free

exhaust manifold
...t;here i have designed a car part in solid works. inside the folder there are files such as <br>,<br> and <br>.
turbosquid
$1
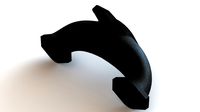
HS6 Exhaust Manifold - A Series Engine
...ld - a series engine for download as ige, obj, stl, and sldpr on turbosquid: 3d models for games, architecture, videos. (1243223)
turbosquid
$300
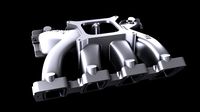
LSX-LS7 Carburetor intake manifold
... available on turbo squid, the world's leading provider of digital 3d models for visualization, films, television, and games.
turbosquid
$2
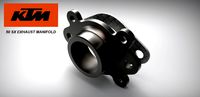
KTM 50 SX EXHAUST MANIFOLD
... available on turbo squid, the world's leading provider of digital 3d models for visualization, films, television, and games.
turbosquid
$1
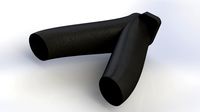
HS6 Exhaust Manifold (A-Series Engine) Long Runner Concept Mk1
...g runner concept mk1 for download as ige, obj, stl, and sldpr on turbosquid: 3d models for games, architecture, videos. (1246847)
turbosquid
$1

HS6 Exhaust Manifold (A-Series Engine) Long Runner Concept Mk1
...g runner concept mk1 for download as ige, obj, stl, and sldpr on turbosquid: 3d models for games, architecture, videos. (1246846)
Exhaust
turbosquid
$2
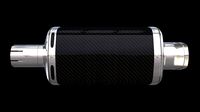
Exhaust
...id
royalty free 3d model exhaust for download as c4d and fbx on turbosquid: 3d models for games, architecture, videos. (1603373)
turbosquid
$1
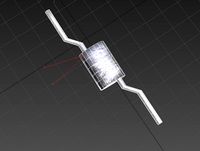
Exhaust
... available on turbo squid, the world's leading provider of digital 3d models for visualization, films, television, and games.
turbosquid
free
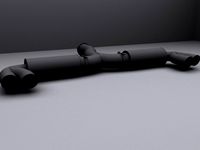
exhaust
... available on turbo squid, the world's leading provider of digital 3d models for visualization, films, television, and games.
turbosquid
free
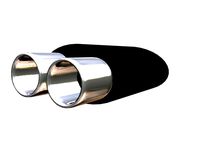
exhaust
... available on turbo squid, the world's leading provider of digital 3d models for visualization, films, television, and games.
3d_export
$25
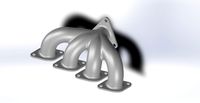
exhaust manifold
...exhaust manifold
3dexport
this is a 3d design of an exhaust manifold used in automobile.
archive3d
free
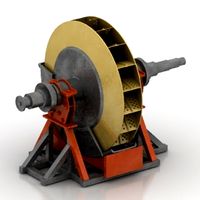
Exhauster 3D Model
... air exhauster hoover
exhauster n101015 - 3d model (*.gsm+*.3ds) for interior 3d visualization.
3d_export
$13
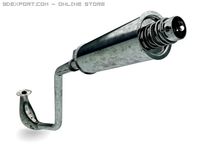
Exhaust 3D Model
...exhaust 3d model
3dexport
exhaust smoke engine motor bike car detail detailed
exhaust 3d model cesar_vonc 12007 3dexport
turbosquid
free
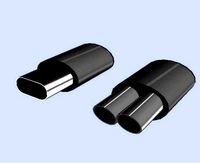
MSX EXHAUSTS
... available on turbo squid, the world's leading provider of digital 3d models for visualization, films, television, and games.
turbosquid
free
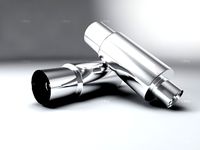
exhaust sport
... available on turbo squid, the world's leading provider of digital 3d models for visualization, films, television, and games.
turbosquid
free
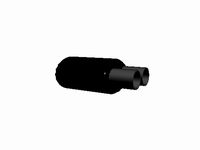
car exhaust
... available on turbo squid, the world's leading provider of digital 3d models for visualization, films, television, and games.
Micro
3ddd
$1
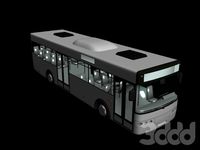
Micro
...micro
3ddd
автобус
turbosquid
$80
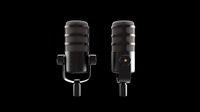
MICRO
...ty free 3d model micro for download as max, c4d, obj, and fbx on turbosquid: 3d models for games, architecture, videos. (1700743)
3ddd
$1

JBL Micro Wireless
... micro , колонка , плеер
jbl micro wireless
turbosquid
$10
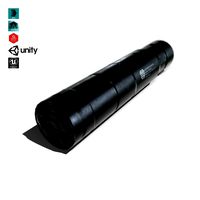
Suppressor Micro
...quid
royalty free 3d model suppressor micro for download as on turbosquid: 3d models for games, architecture, videos. (1380433)
turbosquid
$20
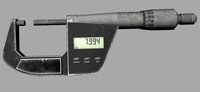
Micro Meter
...osquid
royalty free 3d model micro meter for download as fbx on turbosquid: 3d models for games, architecture, videos. (1350448)
turbosquid
$7
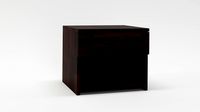
NIghtstand Micro
...d
royalty free 3d model nightstand micro for download as max on turbosquid: 3d models for games, architecture, videos. (1248117)
3ddd
$1
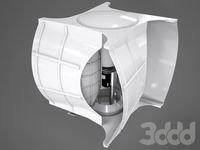
Micro wind turbine
...micro wind turbine
3ddd
турбина
micro wind turbine for your green building projects
turbosquid
$29
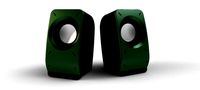
Micro Speakers
... available on turbo squid, the world's leading provider of digital 3d models for visualization, films, television, and games.
turbosquid
$29
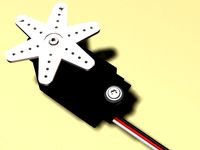
Micro Servo.max
... available on turbo squid, the world's leading provider of digital 3d models for visualization, films, television, and games.
turbosquid
$20
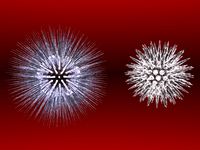
Micro cells
... available on turbo squid, the world's leading provider of digital 3d models for visualization, films, television, and games.
Engine
3d_export
$5
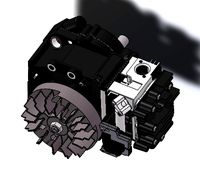
engine
...engine
3dexport
engine
3d_export
free

Engine
...engine
3dexport
engine
archibase_planet
free
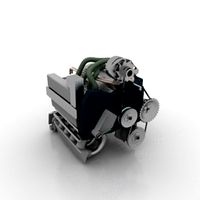
Engine
...engine
archibase planet
motor engine
engine - 3d model for interior 3d visualization.
archibase_planet
free
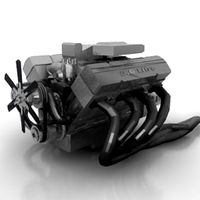
Engine
...engine
archibase planet
motor engine mover
engine n170708 - 3d model (*.3ds) for interior 3d visualization.
archibase_planet
free
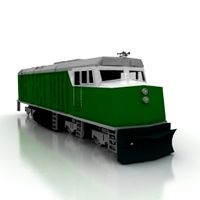
Engine
...engine
archibase planet
engine locomotive train
locomotive - 3d model for interior 3d visualization.
turbosquid
$49
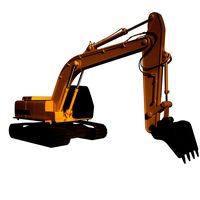
ENGINE
...
turbosquid
royalty free 3d model engine for download as max on turbosquid: 3d models for games, architecture, videos. (1206116)
turbosquid
$1
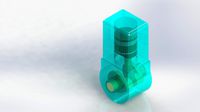
ENGINE
...osquid
royalty free 3d model ic engine for download as sldas on turbosquid: 3d models for games, architecture, videos. (1382781)
3d_export
$5
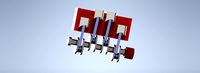
engine
...engine
3dexport
3d_export
free
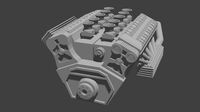
engine
...engine
3dexport
turbosquid
$7
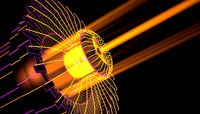
Engine
...d model animated engine mograph element3d for download as c4d on turbosquid: 3d models for games, architecture, videos. (1380716)