Thingiverse
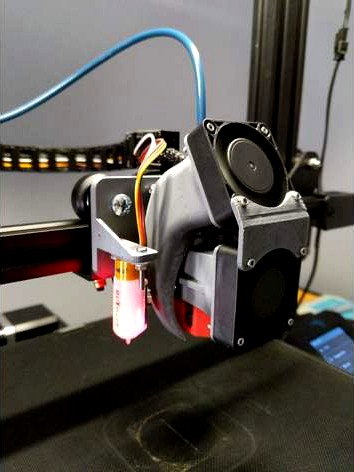
Ender 3 v2 Phaetus Dragon Hotend by jlangholzj
by Thingiverse
Last crawled date: 4 years, 2 months ago
I wanted to upgrade my hotend on the Ender 3 v2 to give some additional capacity for printing larger, draft quality prints at an accelerated speed. After doing some looking around the Phaetus/Triangle Labs Dragon, Slice Mosquito, and e3d V6 were the three that stood out. The Dragon basically is a mashup between the Slice and e3d hotends, there are plenty of reviews out there so go see those for more information. These files should give you everything you need to mount the Dragon to your existing Ender3 v2. I'm assuming the gantry plates have some compatibility between the v2 and the Ender 3 / Pro but I've not tested.
Note that the thread size for the bowden fitting on the hotend is the same as your EXTRUDER (PC4xM6), not your stock hotend . I've had good luck with my Capricorn tube kit which comes with two of each. The "thread test" file I've included is a great way to test fitment for that.
File List
bowden_thread_test - Test print for the bowden fitting threads for the hotend.
gantry_mount - Plate that attaches to the existing ender 3 gantry plate
hotend_duct - cooling for the hotend
part_cooler - filament cooler, these are the "fangs"
fan_brace - attaches to the front of the 4010 fans for stability
Additional Parts required
100k NTC thermistor - Pick whatever you feel comfortable with. You'll have to compile firmware as well.
M5x35 caphead bolts - qty 3 - These will replace the stock M5x30 bolts on your gantry
M2x12 machine screws - qty 6 - Used to mount the cooling ducts
M2x16 machine screws - qty 8 - These are what I used for mounting the fans.
M2 nuts - qty 14
I've included the native files in 2015 SLDPRT and STEP AP214 as well. Happy Mixing!
Known Issues/Improvements Being Tracked
(LAST EDIT 2021-04-20)
-The original design of the "part cooler duct" has a tight clearance around the hotend block/silicon sock as well as the heater cart. This makes it harder to remove and/or replace the sock when changing nozzles.
-The original design of the "part cooler duct" also can benefit from a slightly different exit angle that points at the nozzle. After testing, a more direct point at the nozzle exit would likely improve bridging ability without sacrificing too much in cooling the actual nozzle. This poses a challenge in part/bed clearance and positioning.
-A new design for the "part cooler duct" is being worked on to address the two above issues. It will still maintain a smooth flowpath but will have an expanded exit nozzle, better positioning for cooling, and better clearance. In the meantime feel free to remix your own design!
Note that the thread size for the bowden fitting on the hotend is the same as your EXTRUDER (PC4xM6), not your stock hotend . I've had good luck with my Capricorn tube kit which comes with two of each. The "thread test" file I've included is a great way to test fitment for that.
File List
bowden_thread_test - Test print for the bowden fitting threads for the hotend.
gantry_mount - Plate that attaches to the existing ender 3 gantry plate
hotend_duct - cooling for the hotend
part_cooler - filament cooler, these are the "fangs"
fan_brace - attaches to the front of the 4010 fans for stability
Additional Parts required
100k NTC thermistor - Pick whatever you feel comfortable with. You'll have to compile firmware as well.
M5x35 caphead bolts - qty 3 - These will replace the stock M5x30 bolts on your gantry
M2x12 machine screws - qty 6 - Used to mount the cooling ducts
M2x16 machine screws - qty 8 - These are what I used for mounting the fans.
M2 nuts - qty 14
I've included the native files in 2015 SLDPRT and STEP AP214 as well. Happy Mixing!
Known Issues/Improvements Being Tracked
(LAST EDIT 2021-04-20)
-The original design of the "part cooler duct" has a tight clearance around the hotend block/silicon sock as well as the heater cart. This makes it harder to remove and/or replace the sock when changing nozzles.
-The original design of the "part cooler duct" also can benefit from a slightly different exit angle that points at the nozzle. After testing, a more direct point at the nozzle exit would likely improve bridging ability without sacrificing too much in cooling the actual nozzle. This poses a challenge in part/bed clearance and positioning.
-A new design for the "part cooler duct" is being worked on to address the two above issues. It will still maintain a smooth flowpath but will have an expanded exit nozzle, better positioning for cooling, and better clearance. In the meantime feel free to remix your own design!