Thingiverse
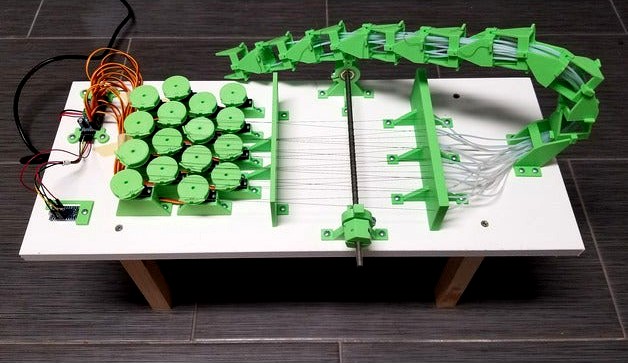
Dumbo 9000 by Jamie_K
by Thingiverse
Last crawled date: 3 years, 1 month ago
This is a tentacle inspired by Richard 9000. Strictly speaking, this incarnation is not a derivative, rather it is more like a clone.
Similarities:
It's a tentacle
Uses PTFE tube and fishing line
Uses 16-channel servo driver driven over I2C
Uses 16 servos to drive 16 degrees of freedom
Green in color
Ran out of PTFE tube partway through construction
Differences:
Cables will be Dyneema fishing line for high strength, minimal stretch
Each joint is one degree of freedom instead of two, meaning 16 joints instead of 8
Joints use metal pins as bearing element
Joints and pulleys have printed features for securing cables, which work quite well
Uses smaller, cheaper servos with tension amplified via capstan (not yet implemented)
The purpose of this robot is as a proof-of-concept for driving many degrees of freedom with relatively strong force at low cost. If viable, the natural application would be a large-ish hexapod or perhaps biped. Hexapods and bipeds already exist with servos as joints, but the strength of servos limits the scale at which these are cost effective. If successful, the method from this experiment might allow larger versions at perhaps 5lbs weight and 3 feet in size.
As of 09/16/2018, I've printed the and mounted 16 servo brackets (4 of each height) and assembled them onto a wooden platform (shelf from Home Depot). I've printed 15 knuckles and assembled them with nails. I purchased some hardened steel cutters to cut the nails into short segments for use as pins. Each knuckle is 35mm in length, axis to axis.
As of 09/16/2018, I've not yet modeled or printed the capstan bearings, nor have I fully solved how I will drive the capstan. My current thought is to use a drill attached to the underside of the platform, using a belt to drive the capstan. I would prefer to minimize the number of special-order parts, but I think a belt will be more forgiving and much quieter than an equivalent gear.
As of 09/16/2018, next steps are to build tentacle base and implement second "holey wall" that guides cords and holds ends of PTFE tubes. Also I need to build bearing blocks for supporting capstan, and build a mechanism to drive it. I'm currently thinking 1/4 inch metal rod for capstan and printed bushings/adapters for a good fit with inside diameter of 608 skate bearings.
As of 09/21/2018, got servo driver working and rudimentary Arduino (using Pro Micro) moving all 16 motors.
As of 09/21/2018, added second holey wall with countersunk holes for PTFE tube, anchor with joint for base of arm, and little brackets to hold the circuit boards. No capstan yet. Currently using a small PC power supply (attached to underside of table) to power servo driver. Arduino currently connected via USB but could be powered by PC power supply.
As of 09/23/2018, added supports for capstan and created bushings to fit 1/4 inch capstan diameter into 8 mm inside diameter of 608 skate bearings. Attached additional PTFE tubes up to 10 pairs total before running out of PTFE tube. Threaded fishing line through tubes and around capstan, and force amplification is working, as demonstrated in this video: https://youtu.be/SXRGQbvma1g. Also modified Arduino code to attempt smooth acceleration to avoid sudden jerks at the ends of movement.
As of 09/28/2018, added tubing and cables to a total of 14 working degrees of freedom, shown here: https://www.youtube.com/watch?v=cjLrB6Ta654 . The joints near the base are of course under higher load. What I'm learning is how high the load is, apparently at the limit of what the PTFE tube can handle. The appearance is that the joints loosen, but I think it's the PTFE failing. Meanwhile, the capstan gets hot in a relatively short time, shorter than I would have hoped, but it's unsurprising given the high stress on the cables for root joints.
As of 09/28/2018 For now I'm parking this, not going to make more updates in its current form. I might start a new one that addresses some of the problems, but I'm afraid this incarnation may have reached its limit.
Similarities:
It's a tentacle
Uses PTFE tube and fishing line
Uses 16-channel servo driver driven over I2C
Uses 16 servos to drive 16 degrees of freedom
Green in color
Ran out of PTFE tube partway through construction
Differences:
Cables will be Dyneema fishing line for high strength, minimal stretch
Each joint is one degree of freedom instead of two, meaning 16 joints instead of 8
Joints use metal pins as bearing element
Joints and pulleys have printed features for securing cables, which work quite well
Uses smaller, cheaper servos with tension amplified via capstan (not yet implemented)
The purpose of this robot is as a proof-of-concept for driving many degrees of freedom with relatively strong force at low cost. If viable, the natural application would be a large-ish hexapod or perhaps biped. Hexapods and bipeds already exist with servos as joints, but the strength of servos limits the scale at which these are cost effective. If successful, the method from this experiment might allow larger versions at perhaps 5lbs weight and 3 feet in size.
As of 09/16/2018, I've printed the and mounted 16 servo brackets (4 of each height) and assembled them onto a wooden platform (shelf from Home Depot). I've printed 15 knuckles and assembled them with nails. I purchased some hardened steel cutters to cut the nails into short segments for use as pins. Each knuckle is 35mm in length, axis to axis.
As of 09/16/2018, I've not yet modeled or printed the capstan bearings, nor have I fully solved how I will drive the capstan. My current thought is to use a drill attached to the underside of the platform, using a belt to drive the capstan. I would prefer to minimize the number of special-order parts, but I think a belt will be more forgiving and much quieter than an equivalent gear.
As of 09/16/2018, next steps are to build tentacle base and implement second "holey wall" that guides cords and holds ends of PTFE tubes. Also I need to build bearing blocks for supporting capstan, and build a mechanism to drive it. I'm currently thinking 1/4 inch metal rod for capstan and printed bushings/adapters for a good fit with inside diameter of 608 skate bearings.
As of 09/21/2018, got servo driver working and rudimentary Arduino (using Pro Micro) moving all 16 motors.
As of 09/21/2018, added second holey wall with countersunk holes for PTFE tube, anchor with joint for base of arm, and little brackets to hold the circuit boards. No capstan yet. Currently using a small PC power supply (attached to underside of table) to power servo driver. Arduino currently connected via USB but could be powered by PC power supply.
As of 09/23/2018, added supports for capstan and created bushings to fit 1/4 inch capstan diameter into 8 mm inside diameter of 608 skate bearings. Attached additional PTFE tubes up to 10 pairs total before running out of PTFE tube. Threaded fishing line through tubes and around capstan, and force amplification is working, as demonstrated in this video: https://youtu.be/SXRGQbvma1g. Also modified Arduino code to attempt smooth acceleration to avoid sudden jerks at the ends of movement.
As of 09/28/2018, added tubing and cables to a total of 14 working degrees of freedom, shown here: https://www.youtube.com/watch?v=cjLrB6Ta654 . The joints near the base are of course under higher load. What I'm learning is how high the load is, apparently at the limit of what the PTFE tube can handle. The appearance is that the joints loosen, but I think it's the PTFE failing. Meanwhile, the capstan gets hot in a relatively short time, shorter than I would have hoped, but it's unsurprising given the high stress on the cables for root joints.
As of 09/28/2018 For now I'm parking this, not going to make more updates in its current form. I might start a new one that addresses some of the problems, but I'm afraid this incarnation may have reached its limit.
Similar models
thingiverse
free
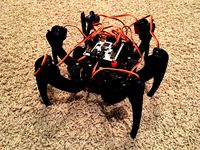
Hexapod with 12g servos by Jrlowe
... various boards. in my version, i used a servotor32 board from an old arduino hexapod and i power it with a 12v power supply box.
thingiverse
free
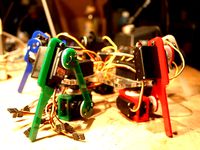
Basic Pentapod by phooky
...he up/down shoulder joints as currently designed. i plan to shorten those members, and get more powerful servos to support them.
thingiverse
free
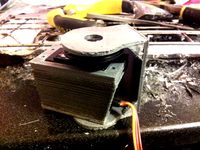
Servo joint box (Prototype for Hexapod) by Anthromod
...t.
very early days and i'm just sorting out the basic dimensions and print strategy. files to follow once they're working
thingiverse
free
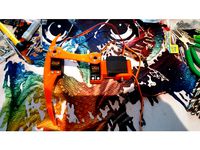
JAH - Jet Another Hexapod (Servo Bracket) by bula87
...for nuts to the other side) and made nut holes a little bigger
new photo of the assembled leg (tibia and femur from andy project)
grabcad
free

PCA9685 PWM Servo driver for Arduino
...pca9685 pwm servo driver for arduino
grabcad
16-channel 12-bit pwm/servo driver - i2c interface - pca9685
thingiverse
free
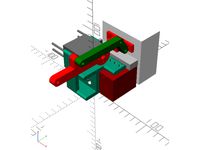
Servo drive window actuator
...270 degree servo which can go to 135. it should be enough for fresh air.
added a videohttps://www.youtube.com/watch?v=zjf7tr8amog
thingiverse
free

Hexapod Robot printable +/-400x450mm by mano1979
... on what hardware you're using. there is lots of info about software and electronics for the hexapod on http://lynxmotion.com
thingiverse
free
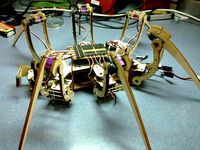
SpiderBot (Hexapod) by mind
...u may make the upper and lower legs shorter to get shorter leverage.
finally the parts get assembled with m2 thread rod and nuts.
thingiverse
free
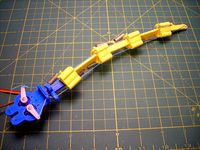
Robotic Tentacle Arm by RoboBaggins
...do anything useful yet, but be used as a part of whatever you can come up with.
video: http://www.youtube.com/watch?v=yk7muaigd4k
thingiverse
free
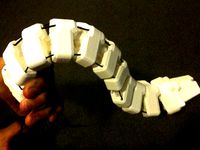
Mechanical Tentacle by Misguided
...rted, i'll hook it up to some servos and the obligatory arduino.
video of it "working": http://youtu.be/evmathngc6s
Dumbo
3d_export
$5
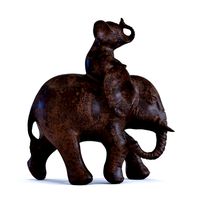
deco figurine elefant dumbo uno
...deco figurine elefant dumbo uno
3dexport
deco figurine elefant dumbo uno
turbosquid
$18
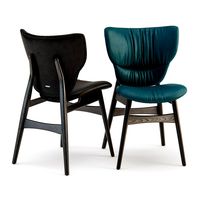
Cattelan Italia Dumbo chair
...free 3d model cattelan italia dumbo chair for download as max on turbosquid: 3d models for games, architecture, videos. (1169040)
turbosquid
$20
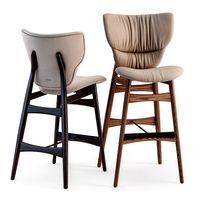
Cattelan Italia Dumbo stool
...model cattelan italia dumbo stool for download as max and obj on turbosquid: 3d models for games, architecture, videos. (1296083)
3d_export
$40

disneys dumbo zbrush sculpt character
...disneys dumbo zbrush sculpt character
3dexport
zbrush sculpt and polypaint file.
cg_studio
$12

Cartoon Baby Elephant RIGGED3d model
...model cgstudio elephant cartoon baby character animal toon pachyderm dumbo mammal africa zoo cute .fbx .3ds .stl .obj .max...
3d_export
$12
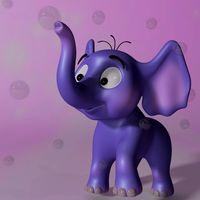
Cartoon baby elephant RIGGED 3D Model
...model 3dexport elephant cartoon baby character animal toon pachyderm dumbo mammal africa zoo cute cartoon baby elephant rigged 3d...
3d_ocean
$19

Cartoon baby elephant RIGGED
...elephant rigged 3docean africa animal baby cartoon character cute dumbo elephant mammal pachyderm toon zoo low poly of a...
thingiverse
free

Dumbo by zacleung
...ng
thingiverse
mother file and tutorial:http://www.portionstudio.com/model-bar/dumbo
file format:
-igs
-stp
-solidwork
-stl
-obj
thingiverse
free
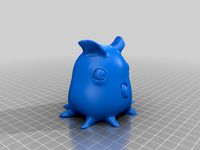
Dumbo Octopus (Grimpoteuthis)
...dumbo octopus (grimpoteuthis)
thingiverse
dumbo octopus (grimpoteuthis) sculpted in zbrush. shouldn't need any supports.
thingiverse
free
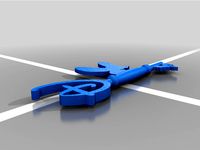
Dumbo Disney Key by August_Moon
...dumbo disney key by august_moon
thingiverse
a disney key with the addition of dumbo.
Jamie
3ddd
free
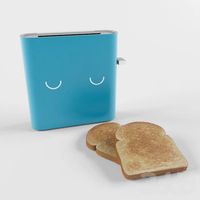
Jamy Toaster
...jamy toaster
3ddd
тостер
+ библиотека материалов
3ddd
$1
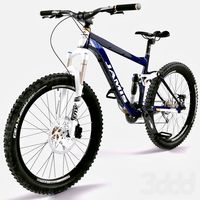
велосипед Jamis
... спорт конкурс
горный велосипед jamis dakar amt 650 comp 2014 года.
модель размещена в категории фри по желанию автора
3ddd
$1

Acacia Table Lamp / Jamie Young
... table lamp / jamie young
3ddd
коряга , jamie young
настольный светильник от jamie young
3d_export
$30
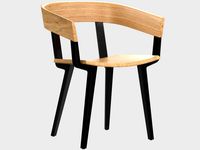
odin chair jamie mclellan
...odin chair jamie mclellan
3dexport
odin chair jamie mclellan max fbx obj
3ddd
$1
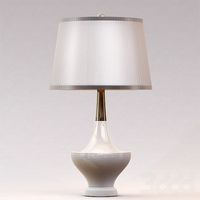
Jamie Young Hialeah Table Lamp
...w.laylagrayce.com/products/jamie-young-hialeah-table-lamp__jy1hialtlgm2conet868cl.aspx
3dsmax 2013+2010+obj+.fbx+.3ds
3ddd
$1
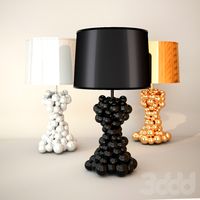
Jamie Hayon Gold Bubbles Lamp
...jamie hayon gold bubbles lamp
3ddd
jamie hayon
277 000 polys
особое спасибо melnick98
design_connected
$7
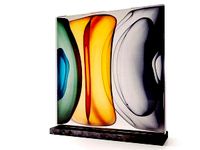
JAMIE HARRIS Infusion Block Sculpture
...jamie harris infusion block sculpture
designconnected
jamie harris infusion block sculpture computer generated 3d model.
turbosquid
$28
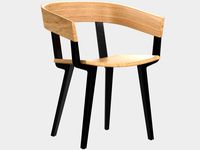
Odin Chair Jamie McLellan
...y free 3d model odin chair jamie mclellan for download as max on turbosquid: 3d models for games, architecture, videos. (1698305)
turbosquid
$12
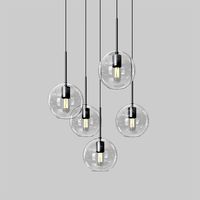
Jamie Cluster Pendant Light
...model jamie cluster pendant light for download as max and obj on turbosquid: 3d models for games, architecture, videos. (1602493)
turbosquid
$15
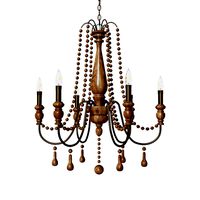
Jamie Young Home Accents Chandelier
...model jamie young home accents chandelier for download as max on turbosquid: 3d models for games, architecture, videos. (1577499)
9000
turbosquid
$45
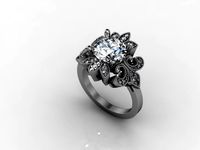
9000
... available on turbo squid, the world's leading provider of digital 3d models for visualization, films, television, and games.
design_connected
$10
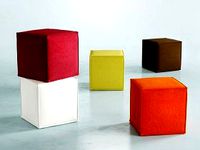
9000 Triton
...9000 triton
designconnected
intertime 9000 triton computer generated 3d model.
turbosquid
$39
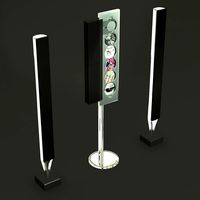
Beosound 9000
... available on turbo squid, the world's leading provider of digital 3d models for visualization, films, television, and games.
turbosquid
$1
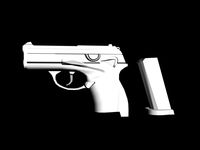
Beretta 9000
... available on turbo squid, the world's leading provider of digital 3d models for visualization, films, television, and games.
3d_export
$59
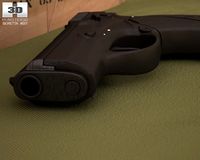
Beretta 9000 3D Model
...tomatic beretta bullet gaston gun italia italian pistol semi semi-automatic weapon
beretta 9000 3d model humster3d 79309 3dexport
3ddd
free

Kinnarps 9000 cv
...kinnarps 9000 cv
3ddd
kinnarps
enjoy
3d_export
$20
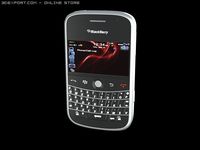
BlackBerry Bold 9000 3D Model
...blackberry bold 9000 3d model
3dexport
phone blackberry bold 9000
blackberry bold 9000 3d model creativeartmind 14386 3dexport
turbosquid
$25
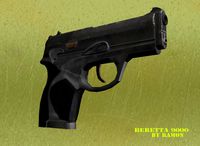
Beretta 9000 Package
... available on turbo squid, the world's leading provider of digital 3d models for visualization, films, television, and games.
turbosquid
$2
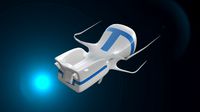
Space Speeder 9000
... available on turbo squid, the world's leading provider of digital 3d models for visualization, films, television, and games.
3d_export
$35
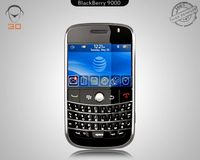
BlackBerry 9000 3D Model
...bile smart android touch screen 2011 pc new copy detail tablet qwerty button usa
blackberry 9000 3d model blacks3d 57937 3dexport
K
turbosquid
$1
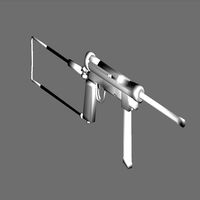
Swedish-K / K-Pist
... available on turbo squid, the world's leading provider of digital 3d models for visualization, films, television, and games.
3ddd
free
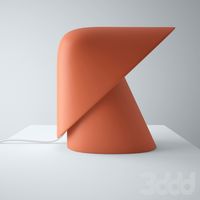
K lamp
...k lamp
3ddd
k lamp
3ddd
free

Giano K
...giano k
3ddd
стеллаж
книжные полки giano k
3ddd
$1
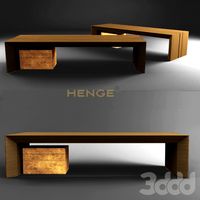
K-table
...k-table
3ddd
henge furniture , письменный
k-table by henge furnitures
design_connected
$13

Thin-K
...thin-k
designconnected
kristalia thin-k computer generated 3d model. designed by bertoncini, luciano.
design_connected
$9
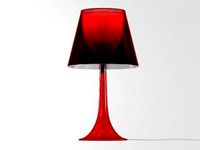
Miss K
...miss k
designconnected
flos miss k table lights computer generated 3d model. designed by philippe cramer.
3ddd
$1
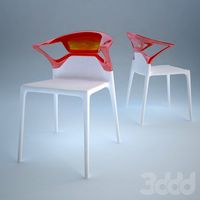
Papatya / Ego-K
...papatya / ego-k
3ddd
papatya
papatya / ego-k
3ddd
$1
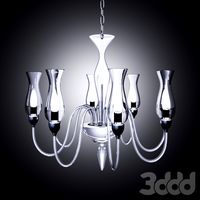
DeMajo 2612/K
...demajo 2612/k
3ddd
demajo
люстра demajo 2612/k
turbosquid
$14
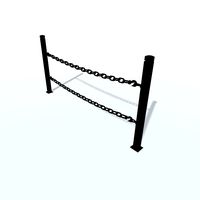
Fence K
...turbosquid
royalty free 3d model fence k for download as fbx on turbosquid: 3d models for games, architecture, videos. (1314643)
turbosquid
$7
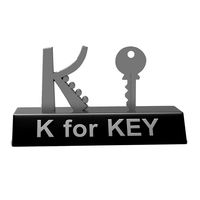
K for Key
...rbosquid
royalty free 3d model k for key for download as max on turbosquid: 3d models for games, architecture, videos. (1689776)