Thingiverse
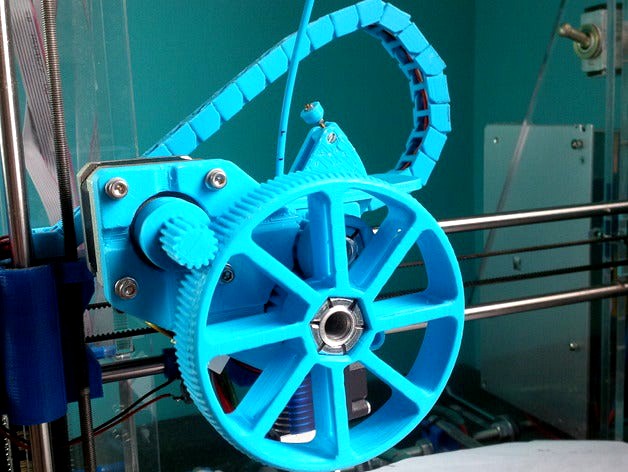
Dual feed extruder by rcmonitor by rcmonitor
by Thingiverse
Last crawled date: 3 years ago
Developed to extrude 3mm (2.85mm) filament via E3D hotend.
Can be modified to use 1.75mm filament by making appropriate hobbed axles.
X carriage mounting bolts offset 24mm
Design goals:
improve extrusion accuracy;
improve extrusion stability;
improve filament reaction;
increase filament pressure;
decrease filament slipping possibility;
increase retraction accuracy;
increase X-axis available print length;
provide easier maintenance;
improve attachement to X-carriage;
achieve low weight;
provide cable management;
Pros:
extrusion is very accurate (+/- 1mm calibration on 100mm extrusion);
very stable results even under pressure (important for first layer on non-planar heatbeds);
very accurate retraction due to almost no backlash;
high maximum filament pressure due to bigger hobbed axle diameter and two hobbed axles;
filament is more responsive due to reduction of length between hobbed axle and nozzle;
extruder stepper motor not crossing Z threaded rod on the left side, so X homing point can be moved to the left (I was able to reach 216mm X by 206 mm Y print area after some heatbed modification);
designed to be easily opened to change filament / cleanup;
remembers filament hold-down tension setting;
gears and hobbed axles can be removed with no tools (nuts can be placed, but are redundant);
places for zip-ties to get cables in place.
really lightweight (for dual extruder) due to hk1210 bearing usage for hobbed axles. With aluminium axles only 90 grams heavier than Wade's extruder;
no need to center drive gear;
more steadily attached to X-carriage due to bigger attachment plane.
Cons:
parts are not easily-printed, especially extruder body and clamp plate;
lots of work to remove supportive structures from body and clamp plate;
lathe required to craft hobbed axles;
some parts are not easy to obtain (M3x50 bolts, M2 threaded rod);
Y axis print area moves 10-15mm towards Ymax (can be fixed by Y-axis calibration).
BOM
printables:
extruder body 1pc
drive gear 1pc
big driven gear 1pc
small driven gear 1pc
clamp plate 1pc
latch 1pc
latch fixer axle 1pc
latch fixer axle knob 1pc
hardware:
DIN 618 hk1210 bearings 4pcs
DIN 625 skf 608 bearings 2pcs
bolt DIN 912 M3x50 3pcs
bolt DIN 912 M3x45 2pcs
bolt DIN 912 M3x14 4pcs
setup screw DIN 913 M8x30 2pcs
setup screw DIN 914 M3x6 1pc
screw DIN 84 M2x12 1pc
nut DIN 934 M3 4pcs
nut DIN 934 M2 5pcs
washer DIN 125 M3 6pcs
either
bolt DIN 931 M12x80 1pc
bolt DIN 931 M12x100 1pc
or
hobbed axle 12x72 1pc
hobbed axle 12x94 1pc
nut DIN 439 M12 2pcs
Can be modified to use 1.75mm filament by making appropriate hobbed axles.
X carriage mounting bolts offset 24mm
Design goals:
improve extrusion accuracy;
improve extrusion stability;
improve filament reaction;
increase filament pressure;
decrease filament slipping possibility;
increase retraction accuracy;
increase X-axis available print length;
provide easier maintenance;
improve attachement to X-carriage;
achieve low weight;
provide cable management;
Pros:
extrusion is very accurate (+/- 1mm calibration on 100mm extrusion);
very stable results even under pressure (important for first layer on non-planar heatbeds);
very accurate retraction due to almost no backlash;
high maximum filament pressure due to bigger hobbed axle diameter and two hobbed axles;
filament is more responsive due to reduction of length between hobbed axle and nozzle;
extruder stepper motor not crossing Z threaded rod on the left side, so X homing point can be moved to the left (I was able to reach 216mm X by 206 mm Y print area after some heatbed modification);
designed to be easily opened to change filament / cleanup;
remembers filament hold-down tension setting;
gears and hobbed axles can be removed with no tools (nuts can be placed, but are redundant);
places for zip-ties to get cables in place.
really lightweight (for dual extruder) due to hk1210 bearing usage for hobbed axles. With aluminium axles only 90 grams heavier than Wade's extruder;
no need to center drive gear;
more steadily attached to X-carriage due to bigger attachment plane.
Cons:
parts are not easily-printed, especially extruder body and clamp plate;
lots of work to remove supportive structures from body and clamp plate;
lathe required to craft hobbed axles;
some parts are not easy to obtain (M3x50 bolts, M2 threaded rod);
Y axis print area moves 10-15mm towards Ymax (can be fixed by Y-axis calibration).
BOM
printables:
extruder body 1pc
drive gear 1pc
big driven gear 1pc
small driven gear 1pc
clamp plate 1pc
latch 1pc
latch fixer axle 1pc
latch fixer axle knob 1pc
hardware:
DIN 618 hk1210 bearings 4pcs
DIN 625 skf 608 bearings 2pcs
bolt DIN 912 M3x50 3pcs
bolt DIN 912 M3x45 2pcs
bolt DIN 912 M3x14 4pcs
setup screw DIN 913 M8x30 2pcs
setup screw DIN 914 M3x6 1pc
screw DIN 84 M2x12 1pc
nut DIN 934 M3 4pcs
nut DIN 934 M2 5pcs
washer DIN 125 M3 6pcs
either
bolt DIN 931 M12x80 1pc
bolt DIN 931 M12x100 1pc
or
hobbed axle 12x72 1pc
hobbed axle 12x94 1pc
nut DIN 439 M12 2pcs
Similar models
thingiverse
free
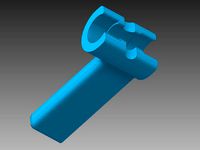
M12 extruder bolt or axle hobbing tool by rcmonitor
...mm hobbed bolt or axle for a filament.
bom
printable:
hobbing tool 1pc
hardware:
din 618 hk1210 bearings 2pcs
thingiverse
free
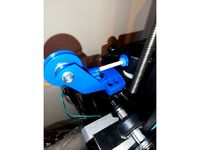
Filament guide for Geeetech A10 + BMG extruder + Runout sensor by Cstom75
... guide with runout sensor for bmg extruder.
bolts:
1pcs m3x10 + nut
1pcs m4x25
2pcs m4 lock nut
2pcs m4 washer
1pcs 688zz bearing
thingiverse
free
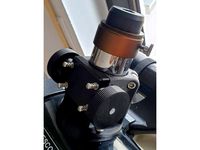
Crayford focuser - upgrade for cheap focuser on your telescope by curly_cz
...5 m4 washers
3pcs din 7380 m4x10 screws
3pcs m4x4 inserts
optional parts for knobs
2pcs din 934 m3 nuts
2pcs din 7380 m3x8 screws
thingiverse
free
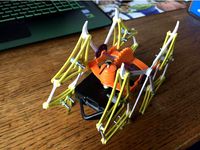
Clock'r Walk'r: the clock powered Theo Jansen Strandbeest by matijahardi
...s
longer arm 2pcs
longer arm2 2pcs
axle 1pcs
axle cap 1pcs
gear 1pcs
worm gear 1pcs
distancer 8pcs
distancer short 8pcs
stub 4pcs
thingiverse
free
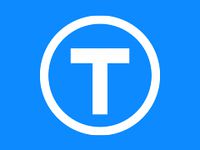
Flight Simulator Joystick and Rudder Pedals by TomStanton
...ro (must be 32u4 processor)
usb lead
30awg wire (atleast 10m total, but preferably different colours for power/ground/signal etc)
thingiverse
free

Adapter with rotation for Mantis Gripper to EEZYbotARM MK2
..._mount_b
1pcs martins_gripper_claw_3_r
1pcs martins_gripper_claw_3_l
1pcs martins_gripper_gear
2pcs martins_gripper_bearingfix_2x
thingiverse
free
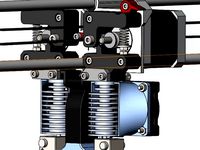
Prusa i3 Dual Direct Extruder E3D hotend by beyondwind
...r no support. fan shroud mounting holes can be m3 tapped for mounting without nut.
update:
video: https://youtu.be/qd0btv66sbs
thingiverse
free
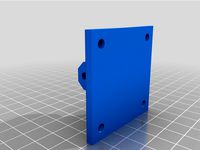
Painting stand for scale Vehicle models by KubesKo
...
z axis
din 985 nut m4 1pcs.
din 125 for m4 1pcs.
din 967 scr. m4 x16 1pcs.
y axis
din 933 scr. m4 x30 1pcs.
din 934 nut m4 1pcs.
thingiverse
free
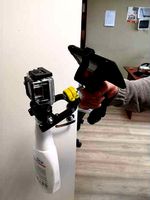
Bottle cap mount for Go Pro, stabilizer for wi-fi camera. by Artformer
...4pc.
nut m8 4pc.
nut m3 8pc.
puck m8 8pc.
bolt m8x70 1pc.
bolt m8x30 2pc.
screw m3x16 8pc.
thingiverse
free
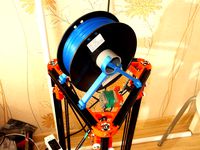
spool holder for profile delta lightweight by codavr
...crew m4 bolts, thread length 6mm: 4pcs
printed:
rod 1: 2pcs
rod 2: 2pcs
joint 1: 2pcs
joint 2: 1pcs
joint 3: 1pcs
pla amount: 50g
Feed
3d_export
$10
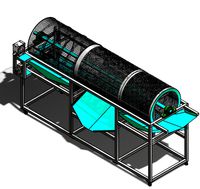
Feed chang
...feed chang
3dexport
turbosquid
$10
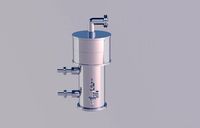
Feed-Pump
...lty free 3d model feed-pump for download as 3ds, obj, and c4d on turbosquid: 3d models for games, architecture, videos. (1456492)
3d_export
$10
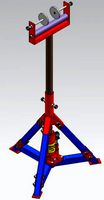
Hydraulic in-feed out-feed support roller
...s at adjustable height, while machining such as cutting, drilling and etc. it is operated by hydraulic and modeled in nx siemens.
turbosquid
$5
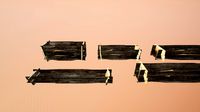
Feeding Troughs and Buckets
...free 3d model feeding troughs and buckets for download as fbx on turbosquid: 3d models for games, architecture, videos. (1582798)
3d_export
$180

Boiler Feed Unit 3D Model
...boiler feed unit 3d model
3dexport
boiler feed unit
boiler feed unit 3d model briancrosdale 76895 3dexport
turbosquid
$6
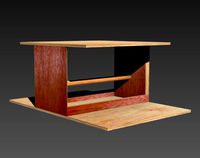
Bird Feed House
... available on turbo squid, the world's leading provider of digital 3d models for visualization, films, television, and games.
3d_export
$7
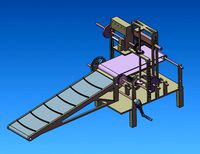
Conveyor belt feeding punching machine
...conveyor belt feeding punching machine
3dexport
conveyor belt feeding punching machine
3d_export
$6
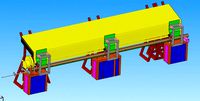
automatic feeding and pipe cutting machine
...automatic feeding and pipe cutting machine
3dexport
automatic feeding and pipe cutting machine
3d_export
$6
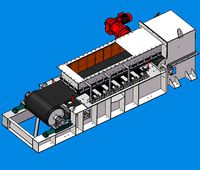
ore feeding equipment mining machinery
...ore feeding equipment mining machinery
3dexport
ore feeding equipment mining machinery
3d_export
$5

feed system
...omponent and the executive element constitute the mechanical transmission system, the detection element and the feedback circuit.
Dual
turbosquid
free
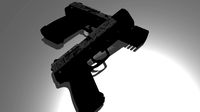
Dual Pistols
...ls
turbosquid
free 3d model dual pistols for download as fbx on turbosquid: 3d models for games, architecture, videos. (1320360)
turbosquid
$2

Dual Axe
...urbosquid
royalty free 3d model dual axe for download as fbx on turbosquid: 3d models for games, architecture, videos. (1332372)
turbosquid
$10
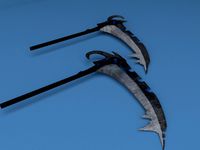
Dual Lesaths
... available on turbo squid, the world's leading provider of digital 3d models for visualization, films, television, and games.
3ddd
$1
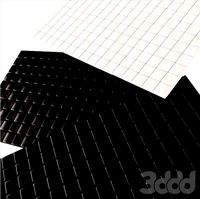
плитка Dual Bianco (Испания)
...й плитки venis dual (испания). технические качества: устойчивость к стирания, отличная геометрия, отсутствие проблем при укладке.
turbosquid
$35
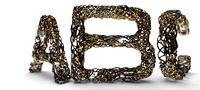
Dual Mesh Fonts
...ree 3d model dual mesh fonts for download as ma, obj, and fbx on turbosquid: 3d models for games, architecture, videos. (1352989)
turbosquid
$29
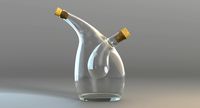
Dual Flask with Bungs
...del dual flask with bungs for download as obj, fbx, and blend on turbosquid: 3d models for games, architecture, videos. (1210512)
turbosquid
$19
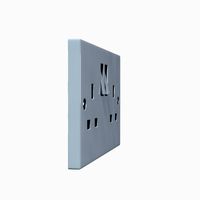
Dual Socket Plug
...3d model dual socket plug for download as obj, fbx, and blend on turbosquid: 3d models for games, architecture, videos. (1303912)
turbosquid
$13
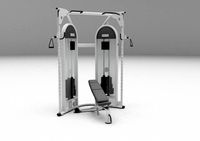
Dual Adjustable Pulley
... available on turbo squid, the world's leading provider of digital 3d models for visualization, films, television, and games.
turbosquid
$10
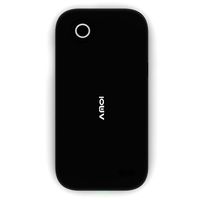
Amoi N809 Dual
... available on turbo squid, the world's leading provider of digital 3d models for visualization, films, television, and games.
turbosquid
$5

Dual Turret Tank
... available on turbo squid, the world's leading provider of digital 3d models for visualization, films, television, and games.
Extruder
3ddd
$1
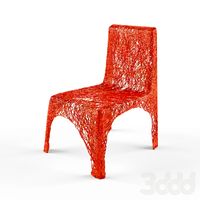
Extruded Chair
...extruded chair
3ddd
extruded , tom dixon
inspired by tom dixon extruded chair
turbosquid
$15
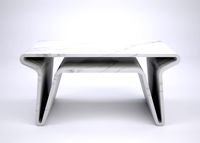
Extruded Table
... extruded table for download as blend, dae, fbx, obj, and stl on turbosquid: 3d models for games, architecture, videos. (1634137)
turbosquid
$2
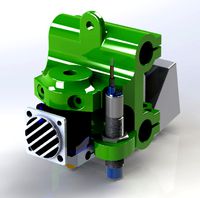
3D Printer Extruder
...d
royalty free 3d model 3d printer extruder for download as on turbosquid: 3d models for games, architecture, videos. (1537359)
turbosquid
$1
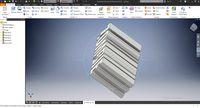
Zombie extruded text
...oyalty free 3d model zombie extruded text for download as obj on turbosquid: 3d models for games, architecture, videos. (1322198)
turbosquid
$4
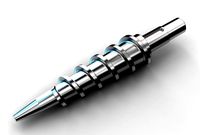
Extruder conical screw
...el extruder conical screw for download as sldpr, ige, and stl on turbosquid: 3d models for games, architecture, videos. (1524433)
turbosquid
$50
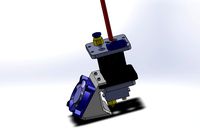
3d PRINTER - Extruder
... available on turbo squid, the world's leading provider of digital 3d models for visualization, films, television, and games.
turbosquid
$15
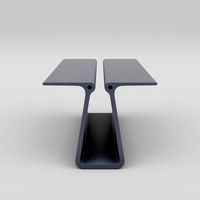
Extruded Table 2
...xtruded table 2 for download as blend, dae, fbx, obj, and stl on turbosquid: 3d models for games, architecture, videos. (1621846)
turbosquid
$10

Maya Extrude Tool
... available on turbo squid, the world's leading provider of digital 3d models for visualization, films, television, and games.
3d_export
$5
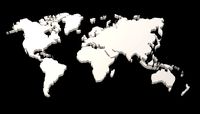
world earth extrude map
...world earth extrude map
3dexport
3ddd
$1

Simply Elegant Extruded Tree Coffee Table Design
...ble by link studios. the silhouette of a tree is visible at one angle, extruded from the surface to create the support structure.