Thingiverse
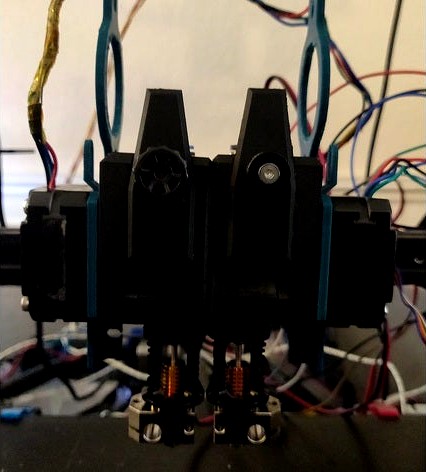
Dual Dragon/V6 Ender 3 DirectDrive Project by undeliverable
by Thingiverse
Last crawled date: 3 years, 3 months ago
WORK STILL IN PROGRESS. At this stage I make no promises it will work.
REQUIRES the 4-wheel X carriage! The mounting plate will not match the stock plate!
This is a remix of eschmidt12's "BMG-X2 Chimera Creality Ender 5 Extruder Mount" remixed to fit a Left and Right BMG geared extruder and 2 Phaetus Dragon hotends (Im guessing the V6 will also work since they blatantly copied much of the V6).
The original is here :https://www.thingiverse.com/thing:4534090/files
This tool cooling shroud seems to work :https://www.thingiverse.com/thing:2089094
First print went pretty well. For a while. Then my SKR 1.3 proved it cant keep a stable temp on both hotends it seems. I did pid tuning but the second extruder is all over the map. Going to add a capacitor to the 5v rail and swap thermistors to see if that solves it. My switch out the MOSFET driving the second heater as well.
Nozzle alignment is tricky. I need to come up with some way of making them +/- .001mm of one another. A servo will probably be introduced at some point. Some of this I solved by staggering the bolts through the extruders, Using 1 50mm, 1 55mm and 1 60mm bolt per extruder allows for better stability. (Pairing the 50mm and 60mm bolts anchors both extruders together)
Test run on heaters and extruders worked well with minimal thermal bleeding between heads.
Custom printer profile is complete as well. Lots of edits needed in Cura to get dual extrusion running with full materials/nozzle/profile support. I think most of the main things are complete and I will run a calibration block tonight to fine tune offsets.
Engineering build has been assembled. Wiring is complete. Software has been updated. My SKR 1.3 needed more variables added to its pins file for the second extruder for some reason. This seems like a pretty big oversight on BTT's part since there are two extruder ports on the board.
#define E1_STEP_PIN P0_01
#define E1_DIR_PIN P0_00
#define E1_ENABLE_PIN P0_10
#ifndef E1_CS_PIN
#define E1_CS_PIN P1_01
#endif
Configuration.h offsets for the heads:
#define HOTEND_OFFSET_X { 0.0, 23.00 } // (mm) relative X-offset for each nozzle
#define HOTEND_OFFSET_Y { 0.0, 0.00 } // (mm) relative Y-offset for each nozzle
#define HOTEND_OFFSET_Z { 0.0, 0.00 } // (mm) relative Z-offset for each nozzle
probe offsets :
#define NOZZLE_TO_PROBE_OFFSET {-39.25, 6, -2 } // Example "2"
Lost build area after relocating the X endstop is 11mm, taking the bed to 224 x 235 x 250 (Staggered left/right for each respective head), or 213 x 235 x 250 for both heads.
The Left/Right extruder setup requires the left stepper to be inverted, in my case I decided that the left hot end was E0 :
#define INVERT_E0_DIR false
#define INVERT_E1_DIR true
Runout distance set to 145mm and will be tuned more later.
Stealthchop off for both extruders. Runout sensors on Z and Y max. BLTouch is currently on Servo, but may be moved to AUX or Z max to allow NeoPixel LEDs to be driven off of the SERVO connections. Or SERVO will drive actual servos if I end up needing head retraction.
I this build uses the CTree 4-wheel X carriage! The spacing for the caster bolts probably wont work for the stock carriage.
Also required are :
2 pancake stepper motors
12 M3 3x3mm threaded inserts
6 55mm M5 bolts
2 5015 fans
1 40mm fan
Once my build is complete I will post photos and setup instructions.
REQUIRES the 4-wheel X carriage! The mounting plate will not match the stock plate!
This is a remix of eschmidt12's "BMG-X2 Chimera Creality Ender 5 Extruder Mount" remixed to fit a Left and Right BMG geared extruder and 2 Phaetus Dragon hotends (Im guessing the V6 will also work since they blatantly copied much of the V6).
The original is here :https://www.thingiverse.com/thing:4534090/files
This tool cooling shroud seems to work :https://www.thingiverse.com/thing:2089094
First print went pretty well. For a while. Then my SKR 1.3 proved it cant keep a stable temp on both hotends it seems. I did pid tuning but the second extruder is all over the map. Going to add a capacitor to the 5v rail and swap thermistors to see if that solves it. My switch out the MOSFET driving the second heater as well.
Nozzle alignment is tricky. I need to come up with some way of making them +/- .001mm of one another. A servo will probably be introduced at some point. Some of this I solved by staggering the bolts through the extruders, Using 1 50mm, 1 55mm and 1 60mm bolt per extruder allows for better stability. (Pairing the 50mm and 60mm bolts anchors both extruders together)
Test run on heaters and extruders worked well with minimal thermal bleeding between heads.
Custom printer profile is complete as well. Lots of edits needed in Cura to get dual extrusion running with full materials/nozzle/profile support. I think most of the main things are complete and I will run a calibration block tonight to fine tune offsets.
Engineering build has been assembled. Wiring is complete. Software has been updated. My SKR 1.3 needed more variables added to its pins file for the second extruder for some reason. This seems like a pretty big oversight on BTT's part since there are two extruder ports on the board.
#define E1_STEP_PIN P0_01
#define E1_DIR_PIN P0_00
#define E1_ENABLE_PIN P0_10
#ifndef E1_CS_PIN
#define E1_CS_PIN P1_01
#endif
Configuration.h offsets for the heads:
#define HOTEND_OFFSET_X { 0.0, 23.00 } // (mm) relative X-offset for each nozzle
#define HOTEND_OFFSET_Y { 0.0, 0.00 } // (mm) relative Y-offset for each nozzle
#define HOTEND_OFFSET_Z { 0.0, 0.00 } // (mm) relative Z-offset for each nozzle
probe offsets :
#define NOZZLE_TO_PROBE_OFFSET {-39.25, 6, -2 } // Example "2"
Lost build area after relocating the X endstop is 11mm, taking the bed to 224 x 235 x 250 (Staggered left/right for each respective head), or 213 x 235 x 250 for both heads.
The Left/Right extruder setup requires the left stepper to be inverted, in my case I decided that the left hot end was E0 :
#define INVERT_E0_DIR false
#define INVERT_E1_DIR true
Runout distance set to 145mm and will be tuned more later.
Stealthchop off for both extruders. Runout sensors on Z and Y max. BLTouch is currently on Servo, but may be moved to AUX or Z max to allow NeoPixel LEDs to be driven off of the SERVO connections. Or SERVO will drive actual servos if I end up needing head retraction.
I this build uses the CTree 4-wheel X carriage! The spacing for the caster bolts probably wont work for the stock carriage.
Also required are :
2 pancake stepper motors
12 M3 3x3mm threaded inserts
6 55mm M5 bolts
2 5015 fans
1 40mm fan
Once my build is complete I will post photos and setup instructions.
Similar models
thingiverse
free
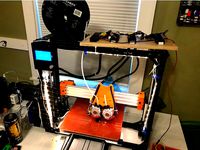
Dual Titan Aero for Taz 5 by StorageJarett
.... i need to redesign.
this was mocked up in tinkercad, so it's a bit less than pristine. if you can clean it up, please do!
thingiverse
free
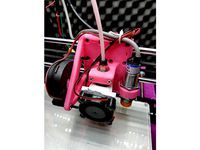
E3D V6 Carriage with Autoleveling and M3 Nut by Tobi97l
...se to hitting the plastik on the side. if you are not comfortable with this change the left probe bed position to a higher value.
thingiverse
free
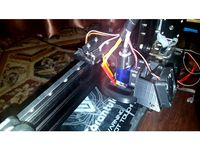
Tevo Tarantula X carriage for E3D V6 with BlTouch sensor mount by sergey130978
...m_extruder 64 // y offset: -front +behind [the nozzle]
z_probe_offset_from_extruder 0 // z offset: -below +above [the nozzle]
thingiverse
free

Anet A8 Sensor Bracket by Jako124
...t_probe_bed_position 25
define right_probe_bed_position 194
define back_probe_bed_position 170
define front_probe_bed_position 20
thingiverse
free
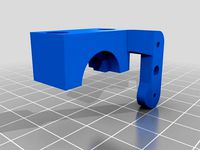
E3d V6 and Bl Touch Clamp by AustenT
...ht [of the nozzle]
define y_probe_offset_from_extruder -2 // y offset: -front +behind [the nozzle]
edit your z offset from tests
thingiverse
free
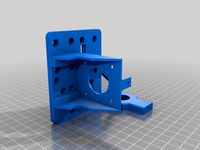
Holder for original e3d extruder + hot-end and LJ18A3-8-Z / BX
... // x offset: -left +right [of the nozzle]
//#define y_probe_offset_from_extruder -3 // y offset: -front +behind [the nozzle]
thingiverse
free
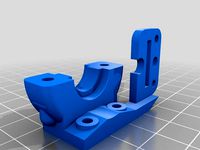
Creality CR-10 E3D V6 3D Touch by loganhaupt
...m_extruder -2 // z offset: -below +above [the nozzle]
[/code]
z offset will need to be calibrated for your own (but mine was -2)
thingiverse
free
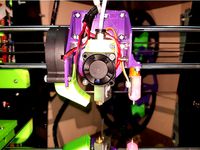
Anet A8 Modular E3D V6 / Volcano Carriage by FerociousDesigns
...truder 0 // y offset: -front +behind [the nozzle]
#define z_probe_offset_from_extruder -1.33 // genuine bltouch at top of mount
thingiverse
free
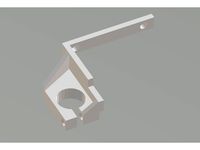
12 mm Sensor mount for Anet A6 by Askot
...-5 // y offset: -front +behind [the nozzle]
#define z_probe_offset_from_extruder 0 // z offset: -below +above [the nozzle]
thingiverse
free
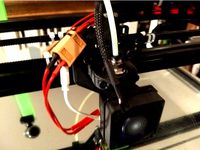
Tronxy E3D V6 lightened Carriage by Eyegoresky
...eems to be working well so far.
this is remix of my tronxy dual v6 extruder carriage. https://www.thingiverse.com/thing:2816039
Directdrive
thingiverse
free
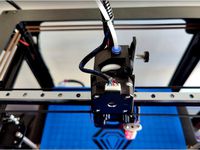
Sapphire Plus DirectDrive by Zulan
...sapphire plus directdrive by zulan
thingiverse
conversion sapphire plus to direct drive, or mini bowden ;)
thingiverse
free
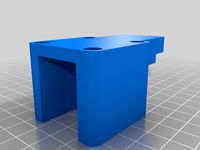
X Cover Ender 3 for DirectDrive
...ps://www.thingiverse.com/thing:3816051
you must glue the x endstop with hotglue into the gap. it fits perfect and it look great !
thingiverse
free
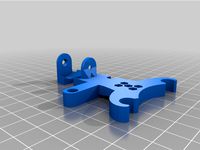
Hotend Side Link for Ender3 DirectDrive by Mrnx3
...
this is better hotend side link for ender3 directdrive.
you must have a direct drive plate for ender 3 and 2x m3 screw (longer).
thingiverse
free
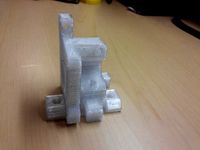
MakerFarm Pegasus 12 - DirectDrive reinforced mount by leadpan
... version of makerfarm directdrive mount with reinforced nut spacer. this helps prevent cracking during installation of extruder.
thingiverse
free
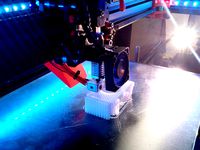
C-Bot, D-Bot DirectDrive Hexagon by totof06
...bot directdrive hexagon by totof06
thingiverse
modification du support directdrive de la c-bot pour le montage d'une hexagon
thingiverse
free
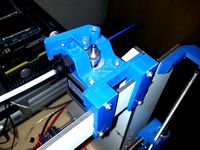
Clamp DirectDrive Prusa I3 by bzijlstra
...clamp directdrive prusa i3 by bzijlstra
thingiverse
two clamps to hold the direct drive of a prusa i3.
thingiverse
free
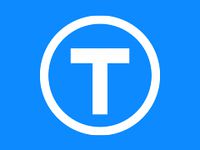
Anycubic Mega Pro Nearly Directdrive by PT90
...anycubic mega pro nearly directdrive by pt90
thingiverse
originalextruder als nahezu direktdrive extruder
thingiverse
free
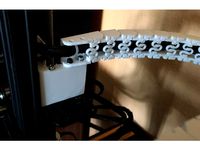
CR-10 DirectDrive Chain adapter by szili83
...cr-10 directdrive chain adapter by szili83
thingiverse
this is adapter for direct drive cable chain.
thingiverse
free
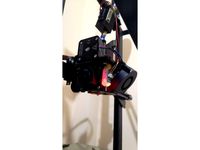
Adapter for bltouch with directdrive mount by Lanius
...touch with directdrive mount by lanius
thingiverse
adapter for bltouch with this mount for direct drive
offset: x-32.3 y-32.3
thingiverse
free
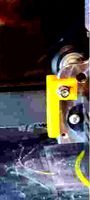
Microswiss X Axis Endstop for DirectDrive by ericthetazman
... by ericthetazman
thingiverse
i made this to account for new position of x endstop with microswiss direct drive on my longer lk4
V6
3d_export
$100
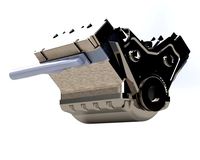
v6 engine
...engine
3dexport
complete v6 engine modeled on solidworks 2017 along with .stl, .sldprt and .sldasm of all th parts and assembly.
3d_export
$10
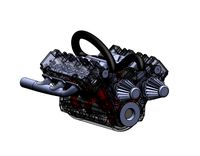
V6 engine
... the first v6 engines were designed and produced independently by marmon motor car company, deutz gasmotoren fabrik and delahaye.
3d_export
$35

v6 engine
...s a complete model of a v6 engine containing over 400 components. you can contact me for a video of all the components assembling
3d_export
$10
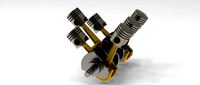
v6 engine
...v6 engine
3dexport
turbosquid
$25
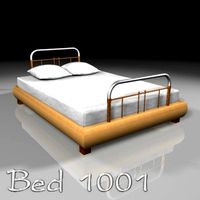
Bed1001-v6
... available on turbo squid, the world's leading provider of digital 3d models for visualization, films, television, and games.
turbosquid
$22
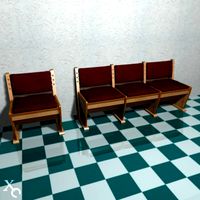
Chair2-v6
... available on turbo squid, the world's leading provider of digital 3d models for visualization, films, television, and games.
turbosquid
$20
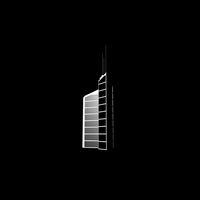
V6.mb
... available on turbo squid, the world's leading provider of digital 3d models for visualization, films, television, and games.
3d_export
$20
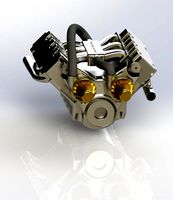
V6 engine
...rovided in this package is all the parts in sldprt format and assembly in sldasm format. i can also convert the format on demand.
3ddd
$1
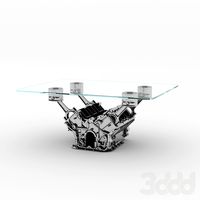
Стол V6
...6" в стиле дизельпанк изготовлен из блока двигателя, 4х поршней и 4х шатунов.
столешница изготовлена из стекла толщиной 8мм.
cg_studio
$199
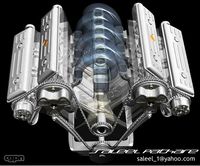
V6 VVTi3d model
...v6 vvti3d model
cgstudio
.3ds - v6 vvti 3d model, royalty free license available, instant download after purchase.
Ender
3ddd
$1
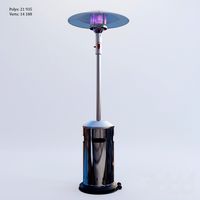
Enders / Elegance
...enders / elegance
3ddd
обогреватель
уличный газовый обогреватель enders elegance
высота: 2200 мм
3d_export
free
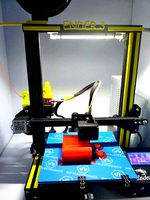
ender 3 frame cavity covers
... of the creality ender 3 - makes it look a bit more attractive it just slides into the open channels of the aluminium framework
turbosquid
$1
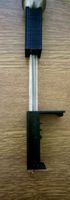
pen support for ender 3
...y free 3d model pen support for ender 3 for download as blend on turbosquid: 3d models for games, architecture, videos. (1611282)
3d_ocean
$9
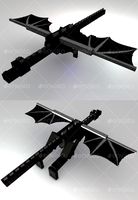
Ender Dragon Minecraft
...ojang obj poly videogames
ender dragon minecraft created with cinema 4d r15 formats included: max 2013 – fbx 2012 – c4d r15 – obj
3d_export
free

Creality ender enclosure webcam mount
...e creality enclosure. sure is better than a tripod. change it up if it helps. i printed pla with 50% infill on my dd ender 3 pro.
3d_export
free
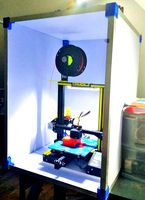
ender 3 enclosure corners
...er corners and 4 upper corners, using 25mmx25mm angled aluminium pieces that gets covered on inside of the frame with plexiglass
3d_export
free
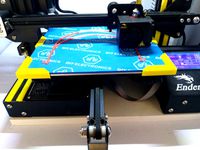
ender 3 3d print bed clips
...ed + normal aluminium bed frame of the creality ender 3 = 6mm (b) these clips are designed for glass plate + aluminium bed = 4mm
3d_export
$5
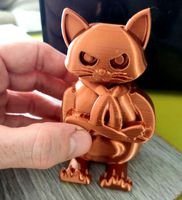
GRUMPY CAT
...grumpy cat 3dexport grumpy cat to print in ender ...
3d_export
$5
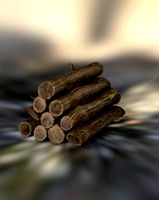
Logs fire
...with one multi material for corona and vray r ender. albedo, normal, uvmap, roughness format jpg 4096x4096 models:...
3d_export
$42
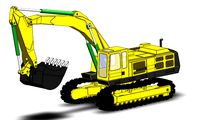
excavator
...is the original size. 0.12 mm printing surface creality ender5 ...
Dragon
3d_export
$15
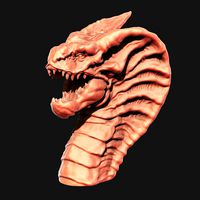
dragon
...dragon
3dexport
dragon
3d_export
$15

dragon
...dragon
3dexport
dragon
3d_export
$5
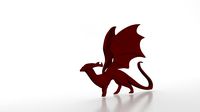
dragon
...dragon
3dexport
dragon figurine
3d_export
$6

dragon
...dragon
3dexport
cool dragon for decoration
3d_export
$20

dragon
...dragon
3dexport
glass dragon made in blender.
3d_export
$8
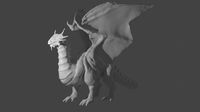
dragon
...dragon
3dexport
3d model of the dragon (sculpting)
3d_export
$5
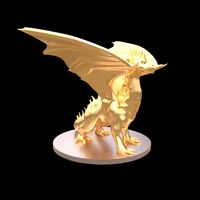
dragon
...dragon
3dexport
dragon 3d model printing
3d_export
$5
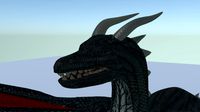
dragon
...dragon
3dexport
black dragon with model+render
archibase_planet
free
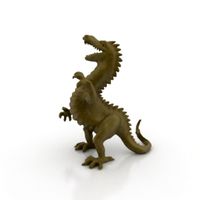
Dragon
...dragon
archibase planet
toy dragon
dragon n170508 - 3d model (*.gsm+*.3ds) for interior 3d visualization.
archibase_planet
free
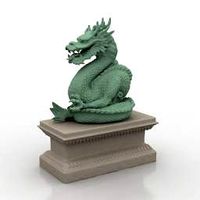
Dragon
...dragon
archibase planet
sculpture dragon statue
dragon 1- 3d model (*.3ds) for interior 3d visualization.
Dual
turbosquid
free
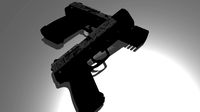
Dual Pistols
...ls
turbosquid
free 3d model dual pistols for download as fbx on turbosquid: 3d models for games, architecture, videos. (1320360)
turbosquid
$2

Dual Axe
...urbosquid
royalty free 3d model dual axe for download as fbx on turbosquid: 3d models for games, architecture, videos. (1332372)
turbosquid
$10
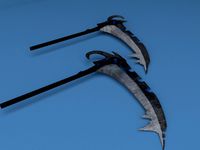
Dual Lesaths
... available on turbo squid, the world's leading provider of digital 3d models for visualization, films, television, and games.
3ddd
$1
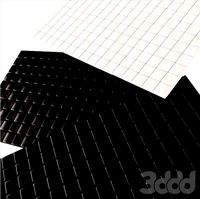
плитка Dual Bianco (Испания)
...й плитки venis dual (испания). технические качества: устойчивость к стирания, отличная геометрия, отсутствие проблем при укладке.
turbosquid
$35
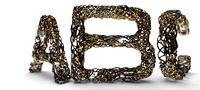
Dual Mesh Fonts
...ree 3d model dual mesh fonts for download as ma, obj, and fbx on turbosquid: 3d models for games, architecture, videos. (1352989)
turbosquid
$29
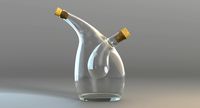
Dual Flask with Bungs
...del dual flask with bungs for download as obj, fbx, and blend on turbosquid: 3d models for games, architecture, videos. (1210512)
turbosquid
$19
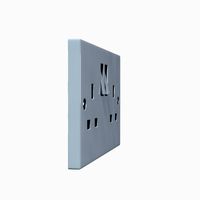
Dual Socket Plug
...3d model dual socket plug for download as obj, fbx, and blend on turbosquid: 3d models for games, architecture, videos. (1303912)
turbosquid
$13
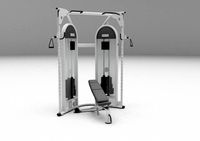
Dual Adjustable Pulley
... available on turbo squid, the world's leading provider of digital 3d models for visualization, films, television, and games.
turbosquid
$10
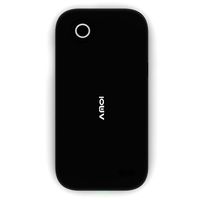
Amoi N809 Dual
... available on turbo squid, the world's leading provider of digital 3d models for visualization, films, television, and games.
turbosquid
$5

Dual Turret Tank
... available on turbo squid, the world's leading provider of digital 3d models for visualization, films, television, and games.
Project
3d_export
$7
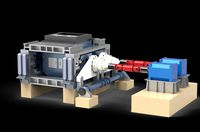
project
...project
3dexport
project
3d_export
$20
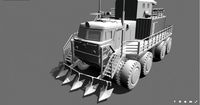
Project
...project
3dexport
design_connected
$16
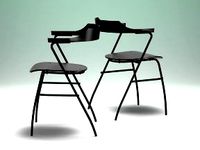
Project Chair
...project chair
designconnected
rex kralj project chair computer generated 3d model. designed by žitnik, marjan.
3ddd
$1
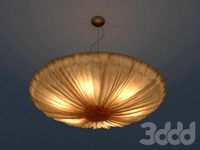
lectric Project
...настроены. сетка очень плотная.
доступно только для группы "profi"
про группу "profi" можно прочитать в чаво
3d_ocean
$19
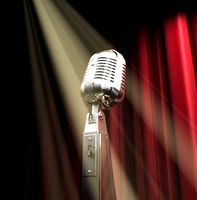
Soon project
...kup. made in 3ds max 2013 1- 3dsmax with vray render included material and light 2- obj file 3- fbx file hope you like it plea...
turbosquid
$49
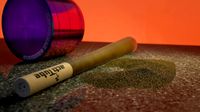
Joint | Project
...squid
royalty free 3d model joint | project for download as on turbosquid: 3d models for games, architecture, videos. (1297983)
turbosquid
$11
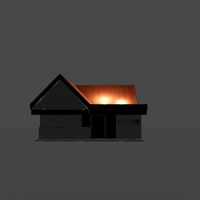
house project
...bosquid
royalty free 3d model house project for download as on turbosquid: 3d models for games, architecture, videos. (1672482)
turbosquid
$450
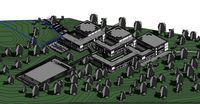
University project
...
royalty free 3d model university project for download as rvt on turbosquid: 3d models for games, architecture, videos. (1463354)
turbosquid
$30
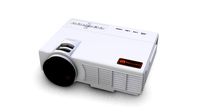
smart projecter
...lty free 3d model smart projecter for download as max and obj on turbosquid: 3d models for games, architecture, videos. (1236214)
3d_export
$5
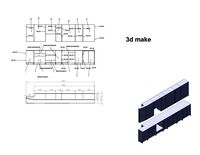
project drawing
...project drawing
3dexport
project drawing and 3d model<br>format jpg sldprt dwg<br>by 3d make
3
turbosquid
$10
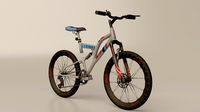
Mountain Bike 3 -3 of 3
...model mountain bike 3 (#3 of 3) for download as fbx and blend on turbosquid: 3d models for games, architecture, videos. (1438752)
turbosquid
$6

Rock 3-3
...urbosquid
royalty free 3d model rock 3-3 for download as obj on turbosquid: 3d models for games, architecture, videos. (1628065)
turbosquid
$29

Books 150 pieces 3-3-3
...books 150 pieces 3-3-3 for download as max, obj, fbx, and stl on turbosquid: 3d models for games, architecture, videos. (1384033)
turbosquid
$3
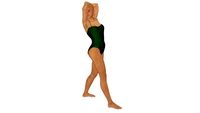
Genesis 3 Clothing 3
... available on turbo squid, the world's leading provider of digital 3d models for visualization, films, television, and games.
3d_export
$5

hinge 3
...hinge 3
3dexport
hinge 3
3ddd
$1
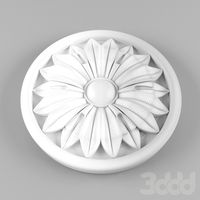
Розетка 3
...розетка 3
3ddd
розетка
розетка 3
turbosquid
$50
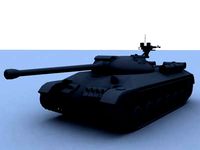
is-3
... available on turbo squid, the world's leading provider of digital 3d models for visualization, films, television, and games.
turbosquid
$10
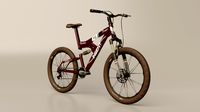
Mountain Bike 3 -2 of 3
...model mountain bike 3 (#2 of 3) for download as fbx and blend on turbosquid: 3d models for games, architecture, videos. (1438750)
turbosquid
$10
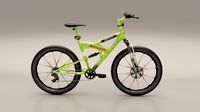
Mountain Bike 1 -3 of 3
...model mountain bike 1 (#3 of 3) for download as fbx and blend on turbosquid: 3d models for games, architecture, videos. (1438743)
3d_export
$5
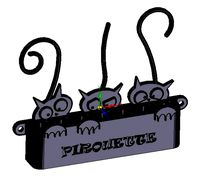
3 CATS
...3 cats
3dexport
3 cats pen holder