Thingiverse
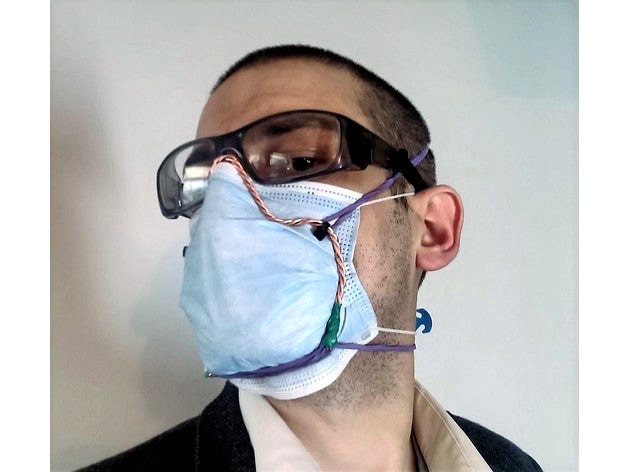
DIY Mask brace / fitter using twisted copper wire cores by FullPlasticScientist
by Thingiverse
Last crawled date: 3 years ago
This is a quick remix listing of the twin and earth DIY 6242Y cable mask brace concept.
This concept is to show that a mask brace can be constructed, so long as there are solid core copper wires available with an area of 2.5mm (approx. 1.78mm diameter) or above. Instead of one specific cable type.
It is constructed by twisting together 3 or more solid copper cores using a vice and drill. Using the same technique that electricians make twisted pair wires for EMF signal noise cancellation.
Bare copper wire of this thickness is hard to find, but is often used in large industrials transformers, generators and motors. Hence it should be more widely available globally than the British 6242Y mains cable type. It was used in this example as proof of concept.
Copper is naturally slowly anti--microbial over a period of hours. But only if it is not tarnished or lacquered. Transformer and motor wire is often lacquered. If so, it can still be used but the mask brace wire surfaces will not be anti-microbial.
To keep its anti-microbial properties, it must be polished daily so that it keeps its shine. If the copper surface becomes dull, which can occur after contact with human sweat, then it will lose its anti-microbial properties. See article below.https://www.sciencedaily.com/releases/2014/06/140617210344.htm
This concept is presented as a good faith effort to help with global pandemic efforts and should be considered as a last resort option only. It should not be used in place of already available and accredited PPE in accordance with local guidelines and regulations.
DOWNSIDES OF THIS CONCEPT
Significantly less comfortable than commercial, printed or 6242Y PVC mask brace variants.
The lower amount of contact area with the surgical mask means it is significantly more difficult to eliminate 100% of the leaks around the edges.
The wire ends are sharp and risk scratching or cutting the wearer’s face. Therefore, it is imperative that when constructing and forming to individual faces that THE WIRE ENDS ARE FOLDED BACK ON THE SIDES, AWAY FROM THE SKIN AND WRAPPED IN SEVERAL LAYERS OF THICK TAPE. If you construct and use this type of brace without bending the ends away from the face, there could be a significant risk of injury. Only use this concept with due caution, knowing the above risk of injury. Anyone given this type of mask brace concept must be made aware of this.
MATERIALS REQUIRED
3x 2.5mm area (approx. 1.78mm diameter) or thicker solid copper wire cores, stripped of their sheaths.
4x 200mm 'trash can' elastic bands
2x zip ties
Thick electrical insulation tape.
TOOLS REQUIRED
Pliers, to help form.
Electrical side cutters, to cut zip ties flush and prevent a sharp plastic burr.
Strong bench vice
Powerful hand drill, capable of slow rotation speed and high torque.
Scissors, to cut the tape.
Diamond file or similar, to deburr sharp ends of copper wire cores.
INSTRUCTIONS
Source 3 or more solid copper wires of 2.5mm area (1.78mm diameter) or thicker.
Straighten out and place side by side. Ensure they are not tangled, Lay out parallel to each other.
Clamp one end of the 3 copper wires firmly into a suitable vice.
Clamp the other end firmly into a powerful hand drill.
Ensure the vice cannot move, then slowly rotate the drill, this will twist the copper wire cores together as shown.
Once maximum twist has been achieved (twisted together without warping, should remain straight), stop the drill.
Cut the ends so that all copper strands end at the same position at either end.
File the ends of the copper wires with a diamond file to remove any sharp edges, must be as dull as possible to reduce risk of injury.
When bending over the ends of the twisted wire assembly, bend away from the direction that will be in contact with the skin to minimise risk of injury.
Wrap the bent over ends in thick and durable tape several times. More layers the better. To reduce risk of injury.
Form the newly twisted wire assembly using the same technique as the 6242Y PVC mask brace. See badge mask fitter video instructions for techniques to ensure it is correctly formed to your nose and cheeks.
Badger seal mask fitter concept.
https://making.engr.wisc.edu/mask-fitter/https://www.youtube.com/watch?v=0CSZrCUAm3g
Fit an ear saver to the mask to be worn, so that it is pulled taut to the face before the brace is fitted. This will significantly improve the chances of achieving a good fit.
Perform a user mask fit / seal checkhttps://www.cdc.gov/niosh/docs/2018-130/pdfs/2018-130.pdf
Wherever leaks are found around the edge of the mask, gently reform the twisted wire assembly by hand in order to improve its fit to the specific contours of your face. Repeat this process until no leakage is present and glasses do not fog up.
The commercial offerings from fix the mask and badger mask fitter are far better than this DIY stopgap solution. If you have access to an accredited commercial offering, that should be your first choice. This concept is intended to provide yet another alternative for those who cannot access appropriate certified commercial solutions where the pandemic still rages globally.
Disclaimer
This concept presented as a good faith effort to help with global pandemic efforts and should be considered as a last resort option only. It should not be used in place of already available and accredited PPE in accordance with local guidelines and regulations.
The author cannot provide any guarantees as to this concept’s ability to improve mask fit and hence protection factor of a surgical mask. It will be highly dependent on the skill of the person constructing it, and their ability to form it to the contours of a specific face. They should not be provided to others without significant instruction on how to form and perform a seal check. With due warning regarding risk of injury from frayed wire ends. Hence, it is an individual specific solution and not something that should be sold commercially on mass. It is a stop gap concept only for use when there are no other accredited PPE options available. It is untested and not verified by certified laboratories. Use at your own risk.
This concept is to show that a mask brace can be constructed, so long as there are solid core copper wires available with an area of 2.5mm (approx. 1.78mm diameter) or above. Instead of one specific cable type.
It is constructed by twisting together 3 or more solid copper cores using a vice and drill. Using the same technique that electricians make twisted pair wires for EMF signal noise cancellation.
Bare copper wire of this thickness is hard to find, but is often used in large industrials transformers, generators and motors. Hence it should be more widely available globally than the British 6242Y mains cable type. It was used in this example as proof of concept.
Copper is naturally slowly anti--microbial over a period of hours. But only if it is not tarnished or lacquered. Transformer and motor wire is often lacquered. If so, it can still be used but the mask brace wire surfaces will not be anti-microbial.
To keep its anti-microbial properties, it must be polished daily so that it keeps its shine. If the copper surface becomes dull, which can occur after contact with human sweat, then it will lose its anti-microbial properties. See article below.https://www.sciencedaily.com/releases/2014/06/140617210344.htm
This concept is presented as a good faith effort to help with global pandemic efforts and should be considered as a last resort option only. It should not be used in place of already available and accredited PPE in accordance with local guidelines and regulations.
DOWNSIDES OF THIS CONCEPT
Significantly less comfortable than commercial, printed or 6242Y PVC mask brace variants.
The lower amount of contact area with the surgical mask means it is significantly more difficult to eliminate 100% of the leaks around the edges.
The wire ends are sharp and risk scratching or cutting the wearer’s face. Therefore, it is imperative that when constructing and forming to individual faces that THE WIRE ENDS ARE FOLDED BACK ON THE SIDES, AWAY FROM THE SKIN AND WRAPPED IN SEVERAL LAYERS OF THICK TAPE. If you construct and use this type of brace without bending the ends away from the face, there could be a significant risk of injury. Only use this concept with due caution, knowing the above risk of injury. Anyone given this type of mask brace concept must be made aware of this.
MATERIALS REQUIRED
3x 2.5mm area (approx. 1.78mm diameter) or thicker solid copper wire cores, stripped of their sheaths.
4x 200mm 'trash can' elastic bands
2x zip ties
Thick electrical insulation tape.
TOOLS REQUIRED
Pliers, to help form.
Electrical side cutters, to cut zip ties flush and prevent a sharp plastic burr.
Strong bench vice
Powerful hand drill, capable of slow rotation speed and high torque.
Scissors, to cut the tape.
Diamond file or similar, to deburr sharp ends of copper wire cores.
INSTRUCTIONS
Source 3 or more solid copper wires of 2.5mm area (1.78mm diameter) or thicker.
Straighten out and place side by side. Ensure they are not tangled, Lay out parallel to each other.
Clamp one end of the 3 copper wires firmly into a suitable vice.
Clamp the other end firmly into a powerful hand drill.
Ensure the vice cannot move, then slowly rotate the drill, this will twist the copper wire cores together as shown.
Once maximum twist has been achieved (twisted together without warping, should remain straight), stop the drill.
Cut the ends so that all copper strands end at the same position at either end.
File the ends of the copper wires with a diamond file to remove any sharp edges, must be as dull as possible to reduce risk of injury.
When bending over the ends of the twisted wire assembly, bend away from the direction that will be in contact with the skin to minimise risk of injury.
Wrap the bent over ends in thick and durable tape several times. More layers the better. To reduce risk of injury.
Form the newly twisted wire assembly using the same technique as the 6242Y PVC mask brace. See badge mask fitter video instructions for techniques to ensure it is correctly formed to your nose and cheeks.
Badger seal mask fitter concept.
https://making.engr.wisc.edu/mask-fitter/https://www.youtube.com/watch?v=0CSZrCUAm3g
Fit an ear saver to the mask to be worn, so that it is pulled taut to the face before the brace is fitted. This will significantly improve the chances of achieving a good fit.
Perform a user mask fit / seal checkhttps://www.cdc.gov/niosh/docs/2018-130/pdfs/2018-130.pdf
Wherever leaks are found around the edge of the mask, gently reform the twisted wire assembly by hand in order to improve its fit to the specific contours of your face. Repeat this process until no leakage is present and glasses do not fog up.
The commercial offerings from fix the mask and badger mask fitter are far better than this DIY stopgap solution. If you have access to an accredited commercial offering, that should be your first choice. This concept is intended to provide yet another alternative for those who cannot access appropriate certified commercial solutions where the pandemic still rages globally.
Disclaimer
This concept presented as a good faith effort to help with global pandemic efforts and should be considered as a last resort option only. It should not be used in place of already available and accredited PPE in accordance with local guidelines and regulations.
The author cannot provide any guarantees as to this concept’s ability to improve mask fit and hence protection factor of a surgical mask. It will be highly dependent on the skill of the person constructing it, and their ability to form it to the contours of a specific face. They should not be provided to others without significant instruction on how to form and perform a seal check. With due warning regarding risk of injury from frayed wire ends. Hence, it is an individual specific solution and not something that should be sold commercially on mass. It is a stop gap concept only for use when there are no other accredited PPE options available. It is untested and not verified by certified laboratories. Use at your own risk.
Similar models
thingiverse
free
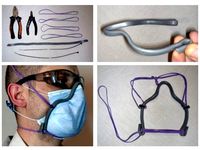
DIY Mask brace / fitter using 6242Y SOLID core twin and earth by FullPlasticScientist
...the zip tie flush using electrical side cutters or similar to ensure no sharp burs are left on the...
thingiverse
free
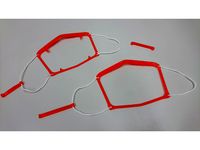
Mask brace / fitter by kazmar
...mask brace / fitter by kazmar
thingiverse
mask fitter.
string for mask is need.
use tpu or other flex materials.
thingiverse
free
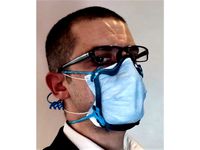
Anti Fog TPU Anti-Microbial Surgical Mask Brace - Adjustable by FullPlasticScientist
...sk fit. it should not be used in place of accredited commercially offered mask braces & ppe. follow your local regulations.
grabcad
free

PPE face mask
...hose who are in regular contact with infected patients.
maintain social distancing and stay safe and cooperate with authorities.
thingiverse
free
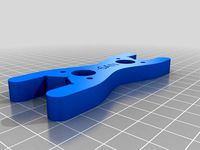
-AN Wrenches and 4in vice soft jaw by ericmattessich
...the risk of over tightening and scratching the finishes.
the vice jaws will require two.
** all fittings should be safety wired
thingiverse
free
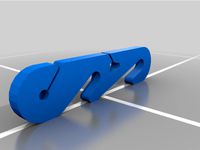
Face Mask Buckle by JosephSeph
...educe the cause of snag on the doctor/nurses' ppe and/or hair as to prevent the discomfort of removal of the face mask or ppe
thingiverse
free

Mask Filter Box by Tsingtao_1903
...ith no support.
use at your own risk. i accept no responsibility for any liability nor injuries nor harm from using this design.
cg_trader
$4
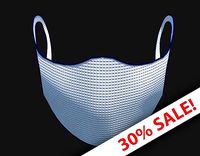
PPE Safety Face Mask Medical or Construction
...onstruction
cg trader
ppe safety face mask medical or 3d asset covid19, available in obj, fbx, ma, ready for 3d animation and ot
grabcad
free

Wire twist test machine
...wire twist test machine
grabcad
wire twist test machine
for copper wire
thingiverse
free
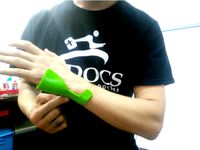
Wrist brace by rct227
... by dr. matthew markert.
safety note:
-use gloves while thermoforming
-apply soft cotton clothes around patients wrist before use
Fullplasticscientist
thingiverse
free
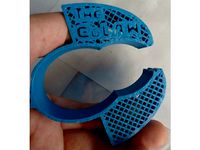
The CuLAW by FullPlasticScientist
... can also be used to open simple door handles
scale by ~70-80% in xy for children's size. listing is for generic adult size.
thingiverse
free
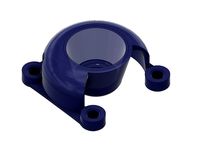
Axial fan exhaust covers by FullPlasticScientist
...sideways as part of the clear mask usb mask dryer. see my other designs.
leave a comment if you would like a different fan size.
thingiverse
free
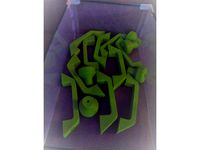
Anti-Microbial general purpose handles by FullPlasticScientist
.... designed for optimal strength whilst using minimal material. see the original listing if you want to customize your own size.
thingiverse
free
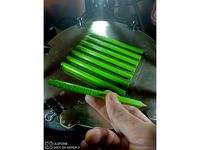
Cu NANO Pen by FullPlasticScientist
...lock and let ink flow. small enough so if the ink cartridge leaks it should remain within the pen body and struggle to leak out.
thingiverse
free
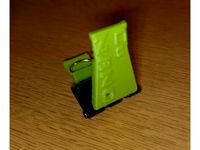
Cu NANO Clip V1 by FullPlasticScientist
...nd width as necessary. prototype in normal pla first if scaling for other sizes to avoid wasting any plactive on printer tuning.
thingiverse
free
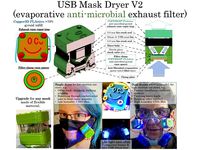
Mask Dryer V2 by FullPlasticScientist
... particles. this is an unproven concept device intended to aid development of clear mask technology and should be viewed as such.
thingiverse
free
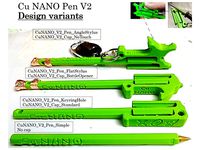
Cu NANO Pen V2 by FullPlasticScientist
...m magnets or 2 off 10x3mm magnets)
-design for manufacture geometry optimisations
-optimised interference fit for biro ink insert
thingiverse
free
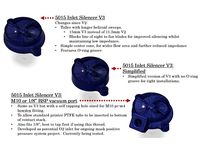
5015 fan silencer by FullPlasticScientist
...f additive manufacturing technologies for acoustic applications"https://link.springer.com/article/10.1007/s00170-020-05853-2
thingiverse
free
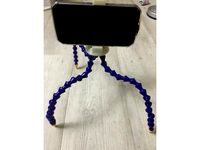
Helping hands phone tripod mount armor 9 by FullPlasticScientist
...one in place.
-optional fibre stick on pads for smaller phones such as old iphone 6. from anti scuff furniture leg sticker pads.
thingiverse
free
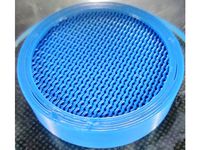
Antimicrobial filter mesh by FullPlasticScientist
...and produce better disease outcomes for all...
*the time has come to awaken him.... i command you to rise stribog! coming soon ;)
Fitter
turbosquid
$5
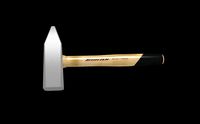
fitter's hammer
... available on turbo squid, the world's leading provider of digital 3d models for visualization, films, television, and games.
3d_export
$5
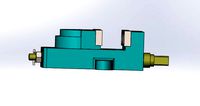
vise
...stabilize the workpiece, which is the necessary tool for fitter workshop. the rotary clamp body can be rotated to...
3d_export
$60
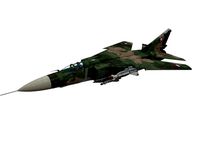
mikoyan gurevich mig-23 flogger
...fighter, alongside similar soviet aircraft such as the su-17 "fitterquot;. it was the first soviet fighter to field a...
3d_export
$5
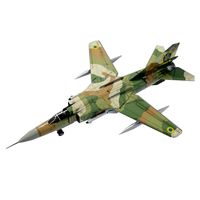
MIG-23 Flogger lowpoly jet fighter
...fighter, alongside similar soviet aircraft such as the su-17 “fitter. it was the first soviet fighter to field a...
thingiverse
free
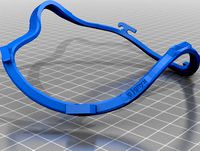
Mask Fitter by enote
...mask fitter by enote
thingiverse
mask fitter
thingiverse
free
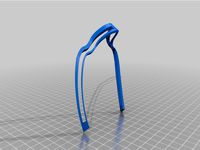
Mask Fitter by dlor
...
thingiverse
mask fitter for surgical and cloth masks. included x3d file incase you want to adjust the proportions for yourself.
thingiverse
free
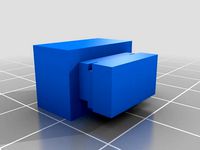
USB fitter by akira378
...usb fitter by akira378
thingiverse
for sandisk flashdrive
thingiverse
free
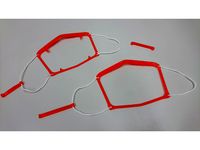
Mask brace / fitter by kazmar
...mask brace / fitter by kazmar
thingiverse
mask fitter.
string for mask is need.
use tpu or other flex materials.
thingiverse
free
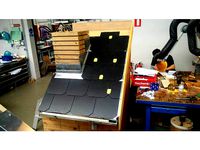
skiffertak (Slating tiles fitter) skiffertag by drbrandt
...ertak (slating tiles fitter) skiffertag by drbrandt
thingiverse
skiffertak platta med 3 mm mellanrum.
slating plate fitter 3 mm
thingiverse
free
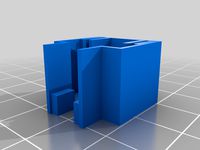
heatsink fitter TMC2208 LV8729
...heatsink fitter tmc2208 lv8729
thingiverse
if you need to fine tune, use fusion360. f3d is also included.
Brace
archive3d
free
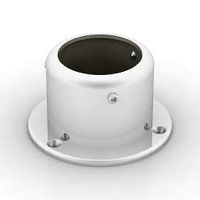
Bracing 3D Model
...
holder bracing strengthening
bracing 4 - 3d model (*.gsm+*.3ds) for interior 3d visualization.
archive3d
free
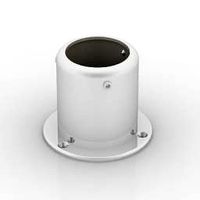
Bracing 3D Model
...
bracing strengthening holder
bracing 2 - 3d model (*.gsm+*.3ds) for interior 3d visualization.
turbosquid
$5
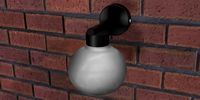
brace PARIS
...osquid
royalty free 3d model brace paris for download as max on turbosquid: 3d models for games, architecture, videos. (1284415)
archive3d
free
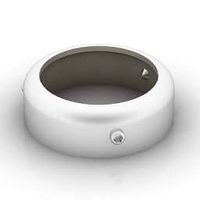
Bracing 3D Model
...older fastening strengthening
bracing 1 - 3d model (*.gsm+*.3ds) for interior 3d visualization.
archive3d
free
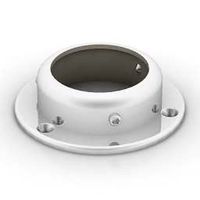
Bracing 3D Model
...older fastening strengthening
bracing 3 - 3d model (*.gsm+*.3ds) for interior 3d visualization.
turbosquid
$20
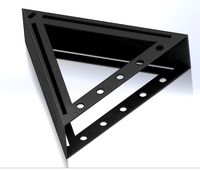
Corner Brace Bracket
...oyalty free 3d model corner brace bracket for download as stl on turbosquid: 3d models for games, architecture, videos. (1322777)
turbosquid
$10
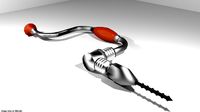
Craftsman Handtools - Brace
... available on turbo squid, the world's leading provider of digital 3d models for visualization, films, television, and games.
turbosquid
$2
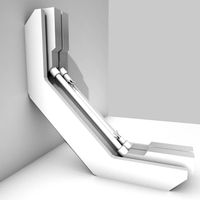
Degree Brace 4
...el degree brace 4 for download as 3ds, max, obj, c4d, and fbx on turbosquid: 3d models for games, architecture, videos. (1205705)
turbosquid
$1
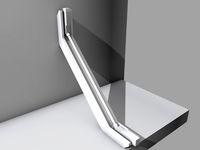
Degree Brace 3
...el degree brace 3 for download as 3ds, max, obj, c4d, and fbx on turbosquid: 3d models for games, architecture, videos. (1205719)
turbosquid
$1
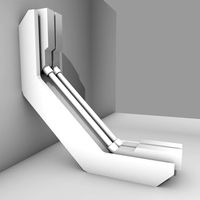
Degree Brace 2
...el degree brace 2 for download as 3ds, max, obj, c4d, and fbx on turbosquid: 3d models for games, architecture, videos. (1205714)
Copper
3d_export
free

Copper Golem
...copper golem
3dexport
the minecraft copper golem
3ddd
$1
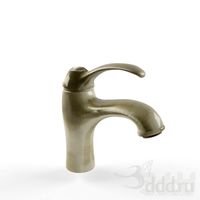
COPPER FAUCET
...copper faucet
3ddd
смеситель
a copper faucet made for a client
3d_export
$5

copper
...copper
3dexport
a robot made of gold material
3d_ocean
$5
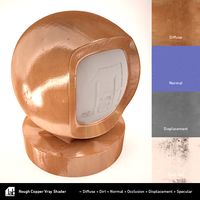
Rough Copper
...ng fixture elements et cetera. this is a v-ray shader intended for use in 3ds max, although the texture maps provided can be u...
design_connected
$16

Copper Bowls
...copper bowls
designconnected
smallaccents copper bowls computer generated 3d model.
design_connected
free

Copper Lights
...copper lights
designconnected
free 3d model of copper lights by vij5 designed by derksen, david.
3ddd
$1
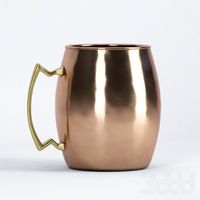
Moscow copper mug
...moscow copper mug
3ddd
copper , mug
3d model of moscow copper mug
3d_export
$5
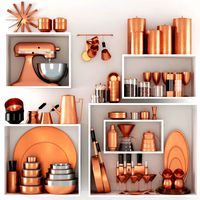
copper set
...copper set
3dexport
copper kitchen accessories platform: 3dsmax + obj version: 3dsmax2018 unit: centimeters
design_connected
$13
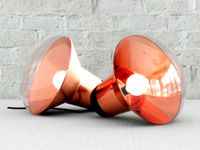
Copper Blow
...copper blow
designconnected
tom dixon copper blow computer generated 3d model. designed by dixon, tom.
3d_export
$5
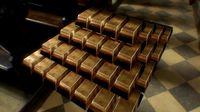
copper bar
...
the copper bar. this model is ideal for any project. it is perfect for cinematic scenes, as well as ideal for any game project.
Diy
3d_export
free
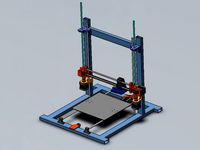
DIY 3D Printer
...diy 3d printer
3dexport
diy 3d printer model
turbosquid
$10
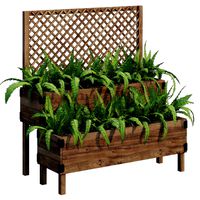
Diy tiered
...l diy tiered for download as max, max, max, max, fbx, and obj on turbosquid: 3d models for games, architecture, videos. (1603709)
turbosquid
$3
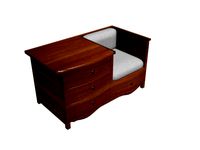
Diy Desk to Bench
...odel diy desk to bench for download as 3ds, max, obj, and fbx on turbosquid: 3d models for games, architecture, videos. (1506589)
turbosquid
$2
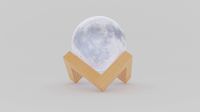
DIY Moon Light
...model diy moon light for download as obj, fbx, blend, and dae on turbosquid: 3d models for games, architecture, videos. (1501170)
3d_export
$8
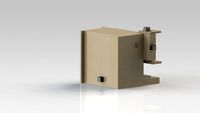
DIY CNC Router 3D Model
...diy cnc router 3d model
3dexport
cnc; router; diy; homemade
diy cnc router 3d model maikeru86 58463 3dexport
turbosquid
$5
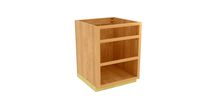
Diy Kitchen Cabinets
...itchen cabinets for download as 3ds, obj, fbx, blend, and dae on turbosquid: 3d models for games, architecture, videos. (1197373)
3d_export
free
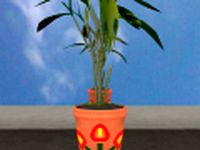
Download free Diying Plant 3D Model
...download free diying plant 3d model
3dexport
diying plant blender
diying plant 3d model visitorsama 98607 3dexport
3ddd
$1
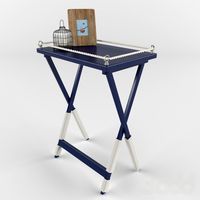
DIY coffee table + decor
... рамка для фото
кофейный столик diy 400х350х600(h) мм. моделился по фото. внимание: материалы - corona.
turbosquid
$3

Diy Wire Lamp Shade
...free 3d model diy wire lamp shade for download as 3ds and fbx on turbosquid: 3d models for games, architecture, videos. (1347605)
cg_studio
$12
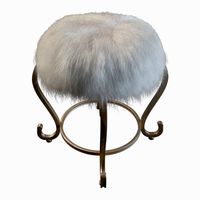
DIY MONGOLIAN LAMB STOOLS3d model
... hair soft pile white
.max - diy mongolian lamb stools 3d model, royalty free license available, instant download after purchase.
Twisted
3ddd
$1

Twist
...twist
3ddd
merx
twist, компания merx
3ddd
$1
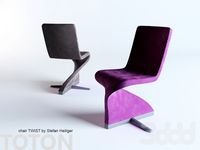
Twist
...twist
3ddd
toton
название: twist/
дизайнер: stefan heiliger/
производитель: toton
3ddd
$1
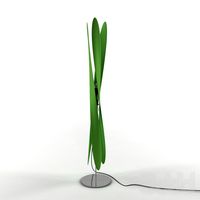
Торшер Twist
...торшер twist
3ddd
twist
закрученный торшер twist
design_connected
$7
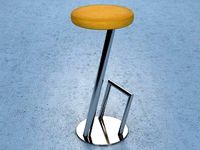
Twist
...twist
designconnected
plank collezioni twist computer generated 3d model. designed by juen, georg.
3ddd
$1
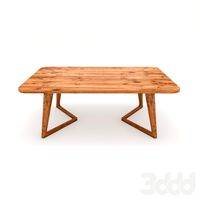
TWIST COUCH
... couch , журнальный
twist couch
размер: 320x600x900mm
3ddd
$1
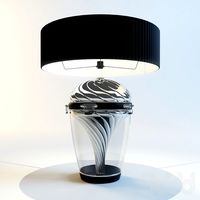
Twisted Lamp
...twisted lamp
3ddd
лампа twisted
3ddd
$1
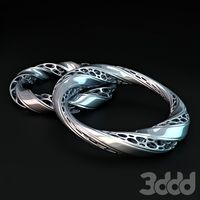
Twisted Bracelets
...twisted bracelets
3ddd
браслет
twisted bracelets
3ddd
$1
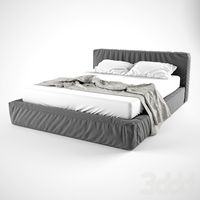
Кровать Rossetto Twist
...twist , rossetto , twist
кровать rossetto twist
turbosquid
$20
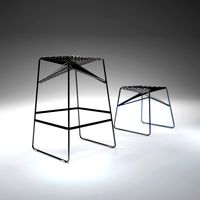
Twist
... available on turbo squid, the world's leading provider of digital 3d models for visualization, films, television, and games.
design_connected
$16
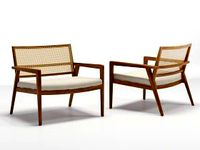
Twist Chair
...twist chair
designconnected
decameron twist chair computer generated 3d model.
Mask
turbosquid
$1
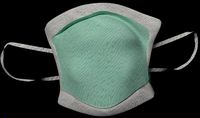
Dust Mask Medical Mask Face Mask Surgical Mask
...k face mask surgical mask for download as blend, fbx, and obj on turbosquid: 3d models for games, architecture, videos. (1533329)
3d_export
$5
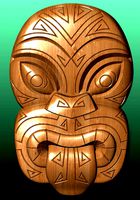
Mask
...mask
3dexport
african mask
turbosquid
$2
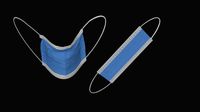
Riggged Surgical mask face mask dust mask medical mask
...sk dust mask medical mask for download as blend, fbx, and obj on turbosquid: 3d models for games, architecture, videos. (1536257)
archibase_planet
free
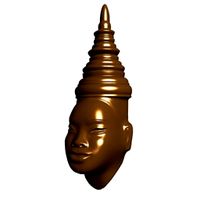
Mask
...mask
archibase planet
mask sculpture decor
mask - 3d model for interior 3d visualization.
3d_export
$19
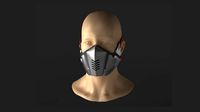
masks tech metal masks wearable futuristic masks
... tech metal masks wearable futuristic masks
3dexport
masks, tech metal masks, wearable, futuristic masks zip contain fbx obj max
archibase_planet
free
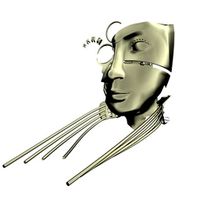
Mask
...mask
archibase planet
mask sculpture decor
mask-decor - 3d model for interior 3d visualization.
archibase_planet
free

Mask
...mask
archibase planet
mask
swimming mask - 3d model (*.gsm+*.3ds) for interior 3d visualization.
archibase_planet
free
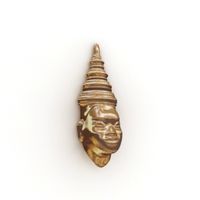
Mask
...mask
archibase planet
picturesque element mask
mask n050608 - 3d model (*.gsm+*.3ds) for interior 3d visualization.
archibase_planet
free
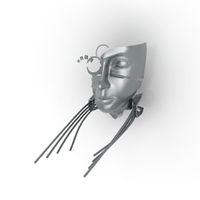
Mask
...mask
archibase planet
mask picturesque element
mask n230708 - 3d model (*.gsm+*.3ds) for interior 3d visualization.
archibase_planet
free
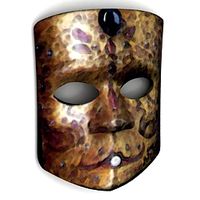
Mask
...mask
archibase planet
mask ornament decoration
mask decor n240211 - 3d model (*.gsm+*.3ds) for interior 3d visualization.
Cores
turbosquid
$143
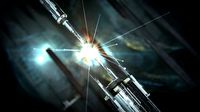
In the core
... available on turbo squid, the world's leading provider of digital 3d models for visualization, films, television, and games.
3ddd
$1
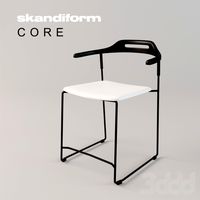
Skandiform Core
...skandiform core
3ddd
skandiform
кресло фирмы skandiform, модель core.
габаритные размеры (шхвхг): 530х700х510 мм
turbosquid
$8

Chandelier CORE
...id
royalty free 3d model chandelier core for download as max on turbosquid: 3d models for games, architecture, videos. (1673910)
turbosquid
free
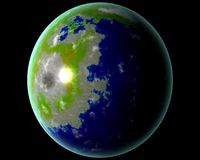
Planet Core
... available on turbo squid, the world's leading provider of digital 3d models for visualization, films, television, and games.
3ddd
$1
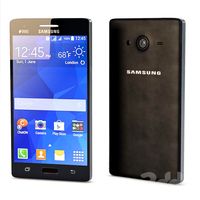
Samsung Galaxy Core 2
...samsung galaxy core 2
3ddd
телефон
samsung galaxy core 2
turbosquid
$10
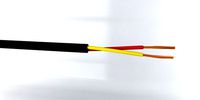
cable 2 core
... available on turbo squid, the world's leading provider of digital 3d models for visualization, films, television, and games.
turbosquid
$10
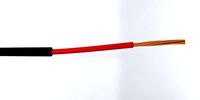
cable 1 core
... available on turbo squid, the world's leading provider of digital 3d models for visualization, films, television, and games.
3ddd
$1
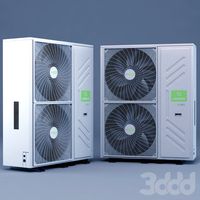
Кондиционер ICE CORE
...кондиционер ice core
3ddd
кондиционер
37 000 полигонов
turbosquid
$65

Insulated Multi Core Cable
... available on turbo squid, the world's leading provider of digital 3d models for visualization, films, television, and games.
turbosquid
$29
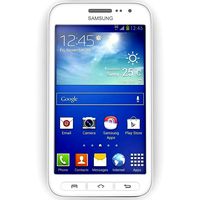
Samsung Galaxy Core Advance
... available on turbo squid, the world's leading provider of digital 3d models for visualization, films, television, and games.
Wire
design_connected
$11
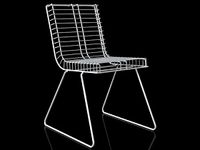
Wired
...wired
designconnected
wired computer generated 3d model.
design_connected
$11
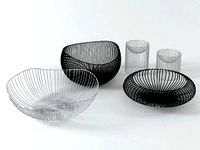
Wires
...wires
designconnected
wires computer generated 3d model.
design_connected
$11
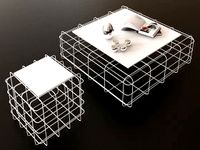
Wire
...wire
designconnected
ronda design wire computer generated 3d model. designed by roccadadria, luca.
3d_export
$5
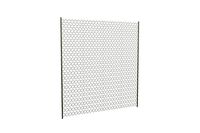
wire
...wire
3dexport
wire 180x180 cm arhive rar 3dmax2019. obj. fbx. mat corona
turbosquid
$2
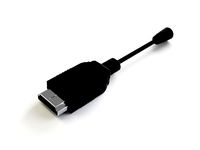
HDMI wire
... 3d model hdmi wire for download as wire, wire, fbx, and wire on turbosquid: 3d models for games, architecture, videos. (1644937)
turbosquid
free
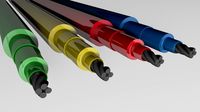
wires
...bosquid
free 3d model wires for download as ma, obj, and fbx on turbosquid: 3d models for games, architecture, videos. (1214233)
3ddd
$1
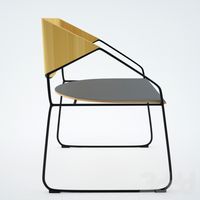
Wire chair
...wire chair
3ddd
wire chair
turbosquid
$10
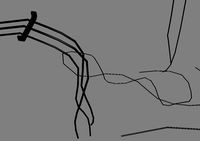
wires
... available on turbo squid, the world's leading provider of digital 3d models for visualization, films, television, and games.
turbosquid
$2
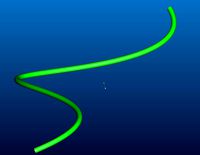
Wire
... available on turbo squid, the world's leading provider of digital 3d models for visualization, films, television, and games.
3d_export
$10
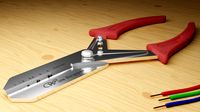
wire stripper
...wire stripper
3dexport
wire stripper 5 in 1
Using
3ddd
$1
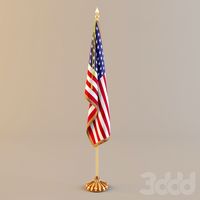
US flag
...us flag
3ddd
флаг
us flag
3d_export
free

Among us
...among us
3dexport
among us red
3d_export
free
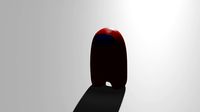
Among Us
...among us
3dexport
this 3d-model of a character from the game "among us". it can be used as a toy or decoration.
3d_export
$6

among us
...among us
3dexport
doll from among us in red
3d_export
$5
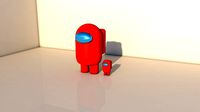
amoung us
...amoung us
3dexport
amoung us character. was created by cinema 4d 19
3d_export
$5
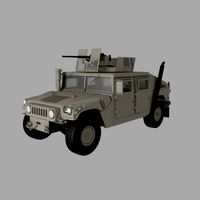
Humvee us
...humvee us
3dexport
humvee us 3d model good quality for animation
3d_export
$15
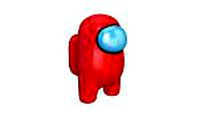
among us
...among us
3dexport
turbosmooth modifier can be used to increase mesh resolution if necessary
3d_export
$25
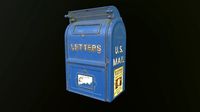
mailbox us
...mailbox us
3dexport
low poly model mailbox us. modeling in the blender, texturing in substance painter
design_connected
$13
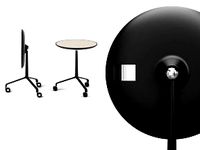
Use Me
...use me
designconnected
sitland use me computer generated 3d model. designed by paolo scagnellato.
3d_export
$5
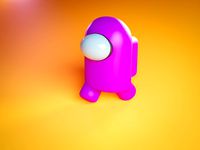
Among Us
...rt
the among us model comes in a variety of colors that can be customized by anyone, and even works with little in the animation