Thingiverse
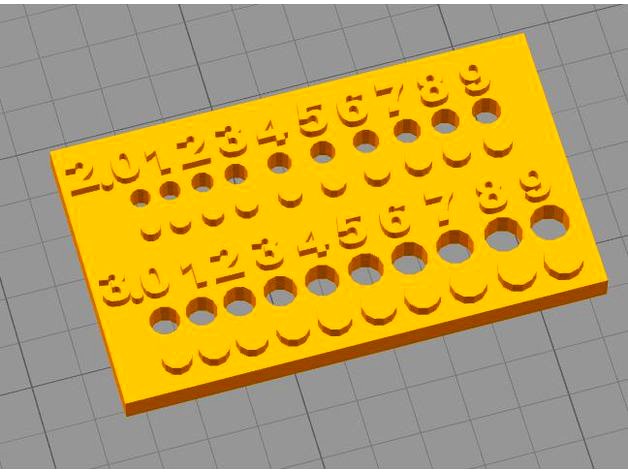
Diameter Calibration for Holes and Cylinders (2,0-3,9 _ 0,1Steps) (updated) by educa_thor
by Thingiverse
Last crawled date: 4 years, 2 months ago
this is basically a small plate with different cylinders ( =outer diameters) and holes ( =inner diameters) from 2,0mm-3,9mm increasing by 0,1mm steps
had lots of trouble in the past with tolerances and now i know why... my printer is off.
i messured the print, did some excel-magic and BOOM:
the maximum differences are from +0,1mm to -0,44mm
(see the graphs: the closer the line is to the blue one, the better)
right now i know HOW MUCH it is off, but not HOW to FIX the issue. (see my printer settings below)
maybe this is a hint: to roughly fit the messurements of a model (the 20mm calibration cube for example) i constantly have to scale them up for ~2% - but only in the x&y axes...
suggestions are welcome!!
=========================================
[update 30.03.2017]
first of all: thanks for the many suggestions, you came up with!!
1) check stepper-driver voltage (by shooter40000)
if the motors don't get enough energy, the magnets can't hold the correct position.
so things like layer-shifting appears
--> didn't help, because i already did this months ago :-)
--> but it's RECOMMENDED TO CHECK THIS OUT!
2) material's shrinkage (J741)
as the warm plastic gets cold, it shrinks. especially ABS is very well known for its warping "qualities"
--> common issue with 3d printing
3) check the stepper motor's "steps per mm" in the firmware (by Solarenemy and J741)
[see the pic "2nd try"]
the printer has to be told, how long the distance of one step is, it's stepper motors actually do.
--> well, i didn't got rid of the problem, but it helped to get more even results (0,0 to -0,26mm). and from now on i don't have to increase the models in my slicer to x&y=102% anymore.
--> So IT ACTUALLY HELPED!! :-)
for a HOW-TO, check out
Kossel / Delta Dimensional Calibration with Instructions (by Coffea)(http://www.thingiverse.com/thing:2201324)
my Make with instructions for a non-delta printer with Marlin firmware
(http://www.thingiverse.com/make:319801)
4) try slower printing speed (by Plust)
[see the pic "3rd try"]
to increase the details on your prints, it's good to go slow.
the printer is more accurate, and the plastic has more time to cool down = the 2nd layer doesn't melt the 1st layer.
--> the difference between normal speed (2nd try) and half speed is interesting:
the inner diameter got worse at the <3,0mm holes. but above it got closer and even matched the design parameters two times (3,5mm & 3,8mm)!
the outer diameter got improved by an average 0,05mm.
--> definitely worth a try!!
5) it's the polygons fault (by chantling and Scabby)
3D-models are made out of many little triangles. so every round shape differs to it's original. this is why we need to consider tolerances up to 0,5mm while designing for FDM-printing. and the smaller it gets, the more difficult it becomes.
--> common issue with 3d printing
--> chantling provided two informative links in the comment section, check them out!
had lots of trouble in the past with tolerances and now i know why... my printer is off.
i messured the print, did some excel-magic and BOOM:
the maximum differences are from +0,1mm to -0,44mm
(see the graphs: the closer the line is to the blue one, the better)
right now i know HOW MUCH it is off, but not HOW to FIX the issue. (see my printer settings below)
maybe this is a hint: to roughly fit the messurements of a model (the 20mm calibration cube for example) i constantly have to scale them up for ~2% - but only in the x&y axes...
suggestions are welcome!!
=========================================
[update 30.03.2017]
first of all: thanks for the many suggestions, you came up with!!
1) check stepper-driver voltage (by shooter40000)
if the motors don't get enough energy, the magnets can't hold the correct position.
so things like layer-shifting appears
--> didn't help, because i already did this months ago :-)
--> but it's RECOMMENDED TO CHECK THIS OUT!
2) material's shrinkage (J741)
as the warm plastic gets cold, it shrinks. especially ABS is very well known for its warping "qualities"
--> common issue with 3d printing
3) check the stepper motor's "steps per mm" in the firmware (by Solarenemy and J741)
[see the pic "2nd try"]
the printer has to be told, how long the distance of one step is, it's stepper motors actually do.
--> well, i didn't got rid of the problem, but it helped to get more even results (0,0 to -0,26mm). and from now on i don't have to increase the models in my slicer to x&y=102% anymore.
--> So IT ACTUALLY HELPED!! :-)
for a HOW-TO, check out
Kossel / Delta Dimensional Calibration with Instructions (by Coffea)(http://www.thingiverse.com/thing:2201324)
my Make with instructions for a non-delta printer with Marlin firmware
(http://www.thingiverse.com/make:319801)
4) try slower printing speed (by Plust)
[see the pic "3rd try"]
to increase the details on your prints, it's good to go slow.
the printer is more accurate, and the plastic has more time to cool down = the 2nd layer doesn't melt the 1st layer.
--> the difference between normal speed (2nd try) and half speed is interesting:
the inner diameter got worse at the <3,0mm holes. but above it got closer and even matched the design parameters two times (3,5mm & 3,8mm)!
the outer diameter got improved by an average 0,05mm.
--> definitely worth a try!!
5) it's the polygons fault (by chantling and Scabby)
3D-models are made out of many little triangles. so every round shape differs to it's original. this is why we need to consider tolerances up to 0,5mm while designing for FDM-printing. and the smaller it gets, the more difficult it becomes.
--> common issue with 3d printing
--> chantling provided two informative links in the comment section, check them out!