Thingiverse
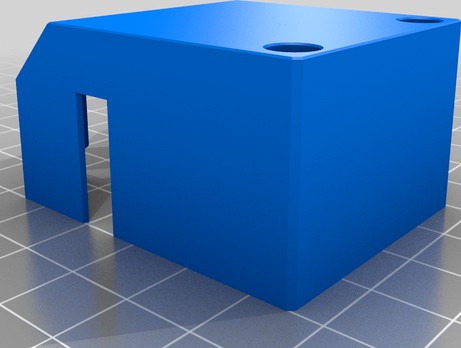
CHANGER - a toolchanger new interpreted by Chuckonelli
by Thingiverse
Last crawled date: 3 years, 4 months ago
Important Note: This Project is still work in progress and will be officially released with a proper YT-trailer.
To follow the Project head over to:
https://hackaday.io/project/175489-changer-a-toolchanger-new-interpreted
Description:
I've had the idea of a toolchanging 3D-printer/motion system for quite a while and started with some concepts to have the same utility as modern cnc milling machines (easy toolswap, fully automated calibration etc.). Approximately one year later I saw the first prototypes of the E3D-Toolchanger and quite liked the toolchanging head and followed the project to see if the toolchanging head improves over time. For my purpose a tested toolchanging head with a proper QM would allow me to focus on the boundary conditions of such a system (interfaces, watercooling, ultralight directdrive printheads, autocalibration of the tools, smart tools with NFC-capabilities). Other than that this System is fully customized with watercooling, HEPA-Filtering, kinematic coupled Z-Axis for non-planar-3D-printing, Air/Vacuumpump for cooling or PnP (vacuum), status LED under the Touchscreen shows progress, optionally: automated loading of the filament, etc.
Inspirations:
As already mentioned I've used the CAD-files from the released E3D-Toolchanger (https://github.com/e3donline/ToolChanger) for a start. I quickly noticed that the E3D-guys didn't use standard parts such as the standoffs etc.
I therefore I started to fully customize the toolchanger with standard parts and heaviliy modified the frame and all of the motion parts.
The standard E3D uses a monorail printbed which works just fine but I will be able to perform non-planar-3d-printing (https://hackaday.com/2016/07/27/3d-printering-non-planar-layer-fdm/) with a always perpendicular printing nozzle.
I therfore implemented the kinematic coupled printbed from the jubilee-printer (https://jubilee3d.com/index.php?title=Main_Page) for a first concept. I like the idea of swappable builtplates.
The consequences of a toolchanger:
Personally I think the motion system such as the E3D-Toolchanger is just the start of beeing called a ''toolchanger''. A toolchanger in a more general sense gives you the freedom to easily interchange tools and even procedures (pcb-milling, PnP...). To achieve this versatility the most important features are:
Defined interfaces/connectors which allow easy toolswap
Room for periphal devices such as vacuum pumps, additional electronics etc.
Swappable or modular builindplatform
The modular mindset:
There is no doubt that the hurdles are high to create such a system but I think the key is to think and search for overlaps between the functions. An example is the vacuum pump. A common vacuum pumps uses a inlet and outlet connector. One way the pump sucks air in and creates an vacuum (if you block the inlet). On the other hand you have the outlet which blows air out (until you block the inlet). Therefore you can use the pump in the printing configuration to cool your printed part and in the pnp-configuration to create to vacuum and grip the components. To change the configuration you just have to switch between inlet and outlet (manually or with a valve) .
I'm trying to implement this mindset as good as currently possible to reach a high modular toolchanging system.
To follow the Project head over to:
https://hackaday.io/project/175489-changer-a-toolchanger-new-interpreted
Description:
I've had the idea of a toolchanging 3D-printer/motion system for quite a while and started with some concepts to have the same utility as modern cnc milling machines (easy toolswap, fully automated calibration etc.). Approximately one year later I saw the first prototypes of the E3D-Toolchanger and quite liked the toolchanging head and followed the project to see if the toolchanging head improves over time. For my purpose a tested toolchanging head with a proper QM would allow me to focus on the boundary conditions of such a system (interfaces, watercooling, ultralight directdrive printheads, autocalibration of the tools, smart tools with NFC-capabilities). Other than that this System is fully customized with watercooling, HEPA-Filtering, kinematic coupled Z-Axis for non-planar-3D-printing, Air/Vacuumpump for cooling or PnP (vacuum), status LED under the Touchscreen shows progress, optionally: automated loading of the filament, etc.
Inspirations:
As already mentioned I've used the CAD-files from the released E3D-Toolchanger (https://github.com/e3donline/ToolChanger) for a start. I quickly noticed that the E3D-guys didn't use standard parts such as the standoffs etc.
I therefore I started to fully customize the toolchanger with standard parts and heaviliy modified the frame and all of the motion parts.
The standard E3D uses a monorail printbed which works just fine but I will be able to perform non-planar-3d-printing (https://hackaday.com/2016/07/27/3d-printering-non-planar-layer-fdm/) with a always perpendicular printing nozzle.
I therfore implemented the kinematic coupled printbed from the jubilee-printer (https://jubilee3d.com/index.php?title=Main_Page) for a first concept. I like the idea of swappable builtplates.
The consequences of a toolchanger:
Personally I think the motion system such as the E3D-Toolchanger is just the start of beeing called a ''toolchanger''. A toolchanger in a more general sense gives you the freedom to easily interchange tools and even procedures (pcb-milling, PnP...). To achieve this versatility the most important features are:
Defined interfaces/connectors which allow easy toolswap
Room for periphal devices such as vacuum pumps, additional electronics etc.
Swappable or modular builindplatform
The modular mindset:
There is no doubt that the hurdles are high to create such a system but I think the key is to think and search for overlaps between the functions. An example is the vacuum pump. A common vacuum pumps uses a inlet and outlet connector. One way the pump sucks air in and creates an vacuum (if you block the inlet). On the other hand you have the outlet which blows air out (until you block the inlet). Therefore you can use the pump in the printing configuration to cool your printed part and in the pnp-configuration to create to vacuum and grip the components. To change the configuration you just have to switch between inlet and outlet (manually or with a valve) .
I'm trying to implement this mindset as good as currently possible to reach a high modular toolchanging system.
Similar models
thingiverse
free

CoreXY Tool Changer Motion System by smoki3
...plemented the tool change script directly into the marlin firmware:https://github.com/smoki3/marlin/tree/bugfix-2.0.x-toolchanger
grabcad
free

CoreXY (e3d toolchanging motion system mock)
...e holes for the extrusions are probably not correct, i just guessed for now. also they should be countersunk. using mgnh12 rails.
grabcad
free

Hydraulic Pump
... inlet line to the pump and by mechanical action delivers this liquid to the pump outlet and forces it into the hydraulic system.
grabcad
free

Hydraulic Pump
...inlet line to the pump, and by mechanical action delivers this liquid to the pump outlet and forces it into the hydraulic system.
grabcad
free

Hydraulic Pump
... inlet line to the pump and by mechanical action delivers this liquid to the pump outlet and forces it into the hydraulic system.
cg_trader
$20
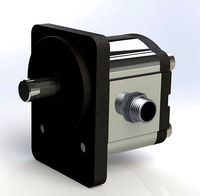
Hydraulic Pump
...inlet line to the pump, and by mechanical action delivers this liquid to the pump outlet and forces it into the hydraulic system.
thingiverse
free
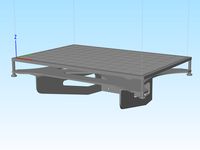
E3D ToolChanger Simplify3D Model
... and choose your color.
if you have problems with disappearing model, look here:https://forum.simplify3d.com/viewtopic.php?t=3758
grabcad
free

Hydraulic pump
...adjusted, or variable displacement pumps, which have a more complicated construction that allows the displacement to be adjusted.
3dwarehouse
free
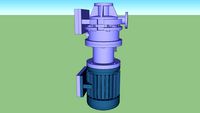
Goulds Pump
...goulds pump
3dwarehouse
1.5' inlet - 1' outlet - 3298 family
thingiverse
free
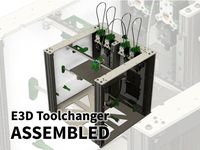
E3D Tool Changer - Assembled
... step, and f3z files for use in 3d modelling software. namely fusion 360 (what i use), or other surface/solid modelling software.
Chuckonelli
thingiverse
free
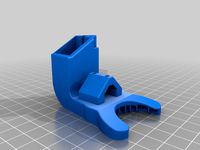
Partcooling BLV mgn Cube, flow optimized Volcano Hotend
...volcano hotend thingiverse the partcooling duct is based on chuckonelli#39;s duct, but has the adopted height from xylenc4's volcano...
thingiverse
free
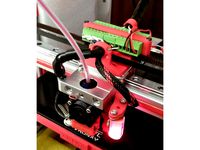
BLV MGN12 Anet A6 A8 Full Metal Head Quick Connector by Buszmen61
...of the: partcooling blv mgn cube, flow optimized by chuckonelli on thingiverse:...
Toolchanger
thingiverse
free
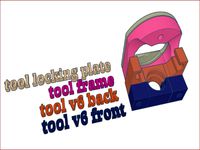
3D-printed toolchanger
...ed toolchanger
thingiverse
3d-printed toolchanger
latest version on github - https://github.com/vladbabii/3d_printed_toolchanger
thingiverse
free
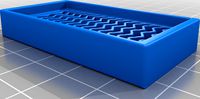
Mold for silicone brush toolchanger by hanshogeland
...mold for silicone brush toolchanger by hanshogeland
thingiverse
a silicone brush mold for toolchanger
thingiverse
free
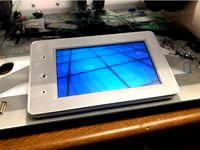
E3D’s ToolChanger – PanelDue i7 case by Skimmy
...oolchanger-paneldue-i7-case
sourcefiles are available for my patrons at https://rene-jurack.de/e3ds-toolchanger-paneldue-i7-case/
thingiverse
free
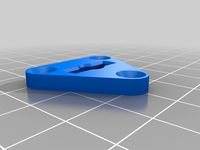
Jays Toolchanging CoreXY
...they become available). the files are all hosted on github(https://github.com/jaysuk/jaystoolchanger in solidworks/step file formats with the printables also in...
thingiverse
free
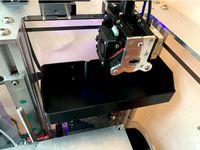
ToolCatcher for E3D ToolChanger by twamueller
...ction with other tools like hemera print-heads.
required screws/nuts:
4x m3x10
4x m3 nuts
currently only available for t2 and t3.
thingiverse
free
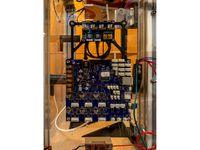
Duet 3 Adapter for E3D Toolchanger by twamueller
...2 for mounting tool distribution board
4-8x m4 nuts + m4x12 for mounting adapter to toolchanger
total size is about 222 x 143 mm.
thingiverse
free
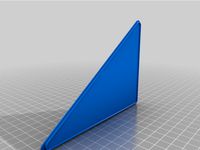
E3D ToolChanger bottom cover plates. by IAtkinI_GTE
... not rattle away when printing.
these were printed in htpla .2mm layer height, please check orientation so no supports required.
thingiverse
free
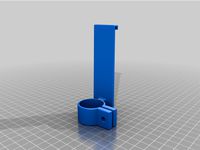
Stepcraft dustcollector for HF500 spindle with toolchanger by DanielSchoeren
...thout making a mess.
there is also a holder for the tube and a adaptor for a makita shopvac.
please let me know what you think!
thingiverse
free

E3D Toolchanger Spoolmount 12mm + Brass Inserts
...inal) hole for mounting a 12mm shaft.
5 degree angle
4mm holes intended for a 3mm brass insert
grub screw hole for securing shaft
Changer
3d_export
free

baby changer
...baby changer
3dexport
turbosquid
$8
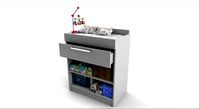
Furniture Baby Changer Crib Bed
...ure baby changer..crib..bed for download as c4d, 3ds, and obj on turbosquid: 3d models for games, architecture, videos. (1712493)
3d_export
$20
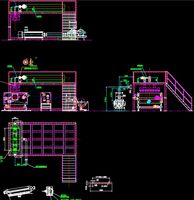
1600 Meltblown cloth production line set drawing CAD
...structure frame, feeding host, extrusion screw, heating system, screen changer metering pump, melting it is formed by a combination...
3d_export
$10

LAD LED Par56 Spotlight 3D Model
...3d model of l.a.d. (light audio design) led par-56 spotlight-colorchangermade in lightwave 10.archive contains 3d model (*.lwo), test scene...
3d_export
$10
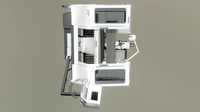
MILLING MACHINE GAME READY 3D MODEL
...into machining centers: milling machines augmented by automatic tool changer, tool magazines or carousels, cnc capability, coolant systems, and...
thingiverse
free
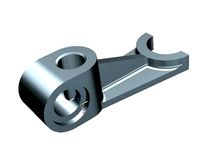
changer joint by vladac
...changer joint by vladac
thingiverse
changer joint for heavy duty gearbox
3dfindit
free
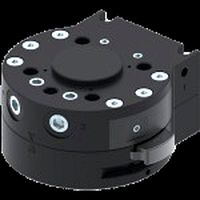
Tool changer
...tool changer
3dfind.it
catalog: zimmer group
3dfindit
free
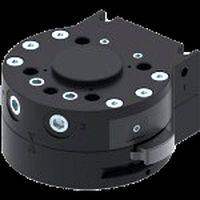
Tool changer
...tool changer
3dfind.it
catalog: zimmer group
3d_sky
free

Tire changer HOFMANN
...tire changer hofmann
3dsky
tire machine
tire changer hofmann. textures, materials, rezvertka.
thingiverse
free
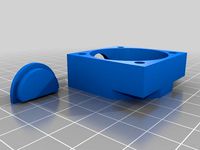
Easy filament changer by bastoof
...easy filament changer by bastoof
thingiverse
easy filament changer
Interpreted
3d_export
$65
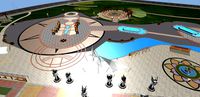
Interpretation of the square
...interpretation of the square
3dexport
simple rendering of the scene file
turbosquid
free
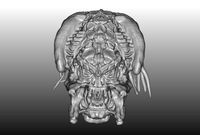
Yautja Predator Interpretation
...e 3d model yautja predator interpretation for download as stl on turbosquid: 3d models for games, architecture, videos. (1217132)
3d_export
$5
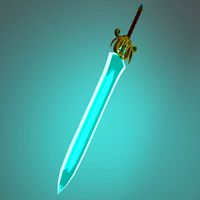
Fantasy sword
...fantasy sword
3dexport
fantasy sword, free interpretation. suitable for 3d printing
3ddd
$1
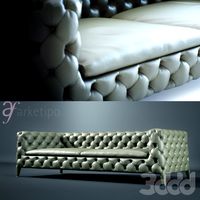
Arketipo Windsor
...ketipo , windsor
beautiful modern interpretation of a classic chesterfield leather sofa.
cg_studio
$12
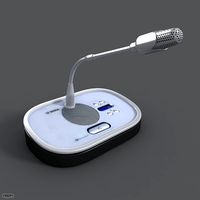
Desk Interpreter3d model
...udio
.3ds .dwg .fbx .max .obj .stl - desk interpreter 3d model, royalty free license available, instant download after purchase.
3ddd
$1
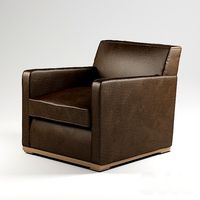
Antonio Citterio Maxalto Imprimatur armchair
...etations. the first, more casual solution displays a seat split into two portions and a backrest with cushions of different sizes
3ddd
$1
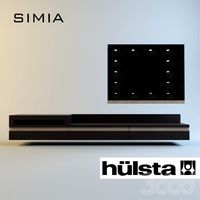
Hulsta Simia
...urite rhythm but also to your individual interpretation of a perfect lighting show.http://www.huelsta.com/simia/int_en/
3ddd
free
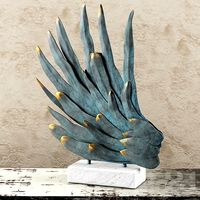
Phoenix Wing
...30"h
7.80374
studio a's interpretation of the iconic phoenix wing. this two-sided sculpture is mounted on white marble.
3d_ocean
$12
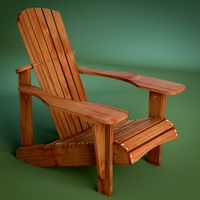
Pine Wooden Outdoor Adirondack Chair
...an adirondack chair. there are a few distinct features that set this model apart from the traditional version. this piece has ...
3d_ocean
$89
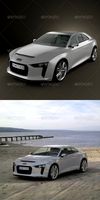
Audi Quattro Concept 2012
...i is presenting a show car at the 2010 paris motor show that moves a futuristic interpretation of this concept into the fast l...
New
turbosquid
$119
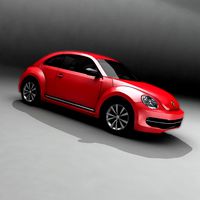
New New Beetle
... available on turbo squid, the world's leading provider of digital 3d models for visualization, films, television, and games.
3d_export
$5
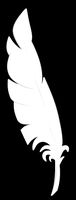
New-feather
...new-feather
3dexport
new-feather
3d_export
$6
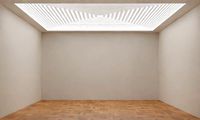
new style
...new style
3dexport
new style room
3ddd
free
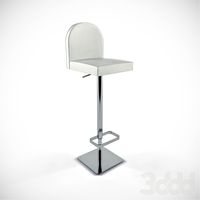
New Items
...ew items
3ddd
new items , барный
барный стул от китайского производителя фирмы new items
3d_export
$6
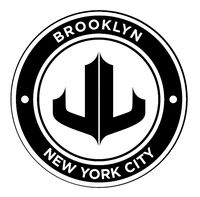
Logo new
...logo new
3dexport
new american style logo
3d_export
$10
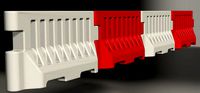
New jersey
...new jersey
3dexport
new jersey stp and stl format
design_connected
$20
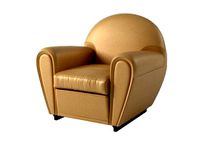
New Deal
...new deal
designconnected
new deal computer generated 3d model.
3d_ocean
$15
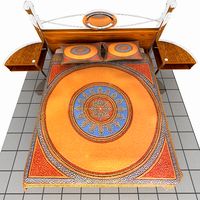
New bed
... for this bed all this file format include in zip file 3ds,obj,max,zip file change material and re-size very easy very for render
3ddd
free
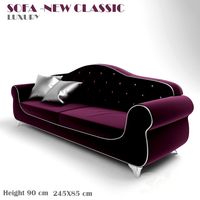
Sofa-New Classic
...sofa-new classic
3ddd
new classic
sofa,new classic
design_connected
$13
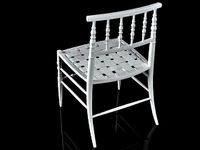
New Antiques
...new antiques
designconnected
cappellini new antiques computer generated 3d model. designed by wanders, marcel.