Thingiverse
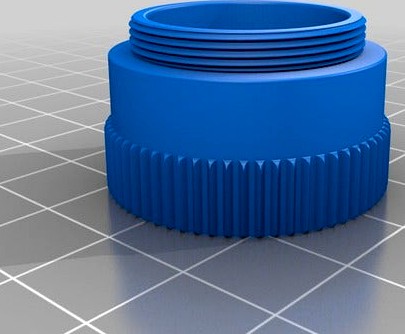
C-mount extender by Dreide1
by Thingiverse
Last crawled date: 3 years, 1 month ago
C-mount extension tubes of different lengths.
Update 08/2018
Fixed thread pitch of the outer thread (was 0.75mm, corrected to 0.794mm=1/32").
Added more tolerance (0.2mm on the thread diameter instead of 0.1mm, for each of the threads).
Reduced model resolution in order to bring down the file size.
Printing
Because of the relatively fine threads, a layer height of 0.15mm or smaller is recommended. Obviously, for the thread to work smoothly, the dimensional accuracy has to be quite high. Over-extrusion should therefore be avoided by all means. If the threads don't fit, one can fix this by changing slicer parameters, either or both the XY scaling factor and the "Surface inset" or "Horizontal size compensation" parameter (or whatever it is called in your slicer). Be aware though that just re-scaling has different effects on the inner and outer thread; one will have more clearance, the other will have less. If you need to get more clearance for both threads, "Surface inset" is the right parameter to play with.
The nominal diameters are 25.2mm (outer thread, most outer diameter) and 24.74 (inner thread, most inner diameter). The average of both numbers is 25mm (exact: 24.97mm), the difference is 0.5mm. If the measured average does not match 25mm, this can be fixed by changing the XY scaling factor. If the measured difference does not match, this can be fixed by changing the surface inset.
Notes
The models have high resolution and that is probably why some slicers see model errors. Simplify3D does not, KISSlicer does (but the slicing results are just fine anyway).
Small changes in tube length can be realized by scaling the part along Z in the slicer, possibly in combination with an accordingly adjusted layer height. Obviously, the threads won't fit anymore if the change was too big. Moreover, if the thread pitches don't match, the forces impacting on the thread are not evenly distributed. Therefore, spacers might be the better solution, for bigger changes like 0.5mm or 1mm anyway (see https://www.thingiverse.com/thing:2802119). Spacers can also be Z-scaled, of course.
The 5mm extender is somewhat critical in that the wall between the inner and the outer thread is rather thin, which makes the part mechanically weaker than the longer tubes. So be careful with heavy lenses. Moreover, light might shine through the thin wall section if the filament is not opaque enough. BTW, the thin wall is basically caused by having an overhang of just 60° instead of 90°, which makes the part printable without support.
Painting the inside of the tubes with black matte color helps reducing stray light. Don't paint the threads though. Normal wall paint actually works pretty well for that.
Material can rub off the threads, especially when being used the first couple of times. Make sure that such debris doesn't land on your lens or the image sensor. I haven't tried, but I guess putting a tiny bit of oil or grease on the threads might help to prevent the debris from flying around.
Update 08/2018
Fixed thread pitch of the outer thread (was 0.75mm, corrected to 0.794mm=1/32").
Added more tolerance (0.2mm on the thread diameter instead of 0.1mm, for each of the threads).
Reduced model resolution in order to bring down the file size.
Printing
Because of the relatively fine threads, a layer height of 0.15mm or smaller is recommended. Obviously, for the thread to work smoothly, the dimensional accuracy has to be quite high. Over-extrusion should therefore be avoided by all means. If the threads don't fit, one can fix this by changing slicer parameters, either or both the XY scaling factor and the "Surface inset" or "Horizontal size compensation" parameter (or whatever it is called in your slicer). Be aware though that just re-scaling has different effects on the inner and outer thread; one will have more clearance, the other will have less. If you need to get more clearance for both threads, "Surface inset" is the right parameter to play with.
The nominal diameters are 25.2mm (outer thread, most outer diameter) and 24.74 (inner thread, most inner diameter). The average of both numbers is 25mm (exact: 24.97mm), the difference is 0.5mm. If the measured average does not match 25mm, this can be fixed by changing the XY scaling factor. If the measured difference does not match, this can be fixed by changing the surface inset.
Notes
The models have high resolution and that is probably why some slicers see model errors. Simplify3D does not, KISSlicer does (but the slicing results are just fine anyway).
Small changes in tube length can be realized by scaling the part along Z in the slicer, possibly in combination with an accordingly adjusted layer height. Obviously, the threads won't fit anymore if the change was too big. Moreover, if the thread pitches don't match, the forces impacting on the thread are not evenly distributed. Therefore, spacers might be the better solution, for bigger changes like 0.5mm or 1mm anyway (see https://www.thingiverse.com/thing:2802119). Spacers can also be Z-scaled, of course.
The 5mm extender is somewhat critical in that the wall between the inner and the outer thread is rather thin, which makes the part mechanically weaker than the longer tubes. So be careful with heavy lenses. Moreover, light might shine through the thin wall section if the filament is not opaque enough. BTW, the thin wall is basically caused by having an overhang of just 60° instead of 90°, which makes the part printable without support.
Painting the inside of the tubes with black matte color helps reducing stray light. Don't paint the threads though. Normal wall paint actually works pretty well for that.
Material can rub off the threads, especially when being used the first couple of times. Make sure that such debris doesn't land on your lens or the image sensor. I haven't tried, but I guess putting a tiny bit of oil or grease on the threads might help to prevent the debris from flying around.
Similar models
grabcad
free

Scope Anti-Reflection Cover
...rn on "detect thin walls" in the slicer if the honeycomb is not reproduced
tested successfully with pla
solidworks 2016
thingiverse
free
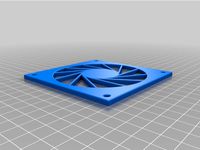
Fan Guard Fully parametric for Fusion 360 by Mamu_05
...ption is there for each parameter to change including fan diameter, aperture diameter, bolt hole diameter, and bolt hole spacing.
thingiverse
free
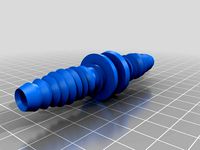
Tube connector for tubes 10/12mm (inner/outer diameter) silicone tubes by swisswuff
...r/outer diameter) silicone tubes by swisswuff
thingiverse
tube connector for tubes 10/12mm (inner/outer diameter) silicone tubes
thingiverse
free
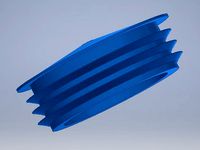
Tube Plug (38mm inner diameter) by GrimbiXcode
...tube plug (38mm inner diameter) by grimbixcode
thingiverse
tube plug for 38mm inner diameter tube (40mm outer diameter)
grabcad
free

Lens Filter Step-Up Ring Adapter (Parametric)
...e tree, select "dd," and you should be able to enter the parameters. it takes a bit of time to recalculate the threads.
thingiverse
free

Slide bearing and sleeve for filament spool
...shape
sleeve inner diameter 47,5mm for a snug fit, will cause problems if printed with a non-flexible filament
sleeve height 18mm
thingiverse
free
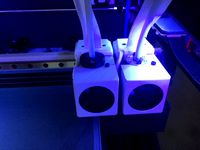
attachment bowden tube by StikDesign
..., and the tube with outer m6 thread (this is done manually!). ths way the tube does not get squeezed and won't pop out again.
thingiverse
free
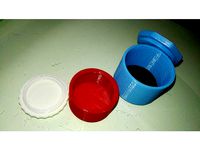
Customizable threaded rounded box by sgonzalezlopez
...an customize the inner diameter of the box. be aware that the outer diameter will be bigger due to the thread width.
enjoy it!!!!
thingiverse
free
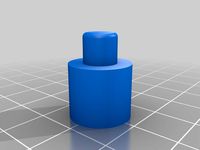
3/8" threaded rod to 806 bearing adapter by tray_withdraw
... match perfectly with the inner diameter of the bearing. this goes on the end of the threaded rod and fits snugly in the bearing.
thingiverse
free
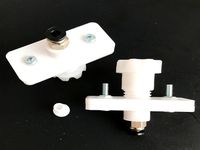
Drybox Filament Pass-Through
...
any comments and suggestions for improvements appreciated ;-)
feel free to remix, fusion 360 files are included in the download.
Dreide1
thingiverse
free
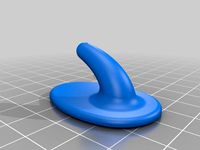
Hook by Dreide1
...hook by dreide1
thingiverse
yet another hook. to be attached with double-sided adhesive tape.
thingiverse
free
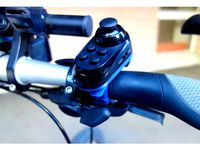
R1 Remote controller handlebar mount by Dreide1
...mount adapter has been found, the mount adapter should be glued to the bottom of the device (without glueing in the screw tough).
Extender
turbosquid
$39
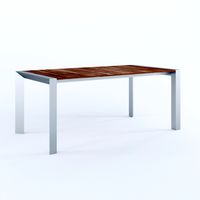
Extending table
...id
royalty free 3d model extending table for download as max on turbosquid: 3d models for games, architecture, videos. (1290552)
turbosquid
$5
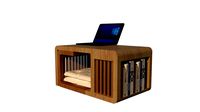
Extend Table
...squid
royalty free 3d model extend table for download as skp on turbosquid: 3d models for games, architecture, videos. (1372508)
turbosquid
$40
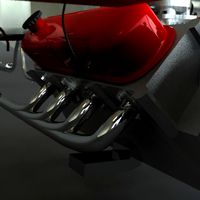
Engine Extended
... available on turbo squid, the world's leading provider of digital 3d models for visualization, films, television, and games.
turbosquid
$12

Triple extender
... available on turbo squid, the world's leading provider of digital 3d models for visualization, films, television, and games.
turbosquid
$99
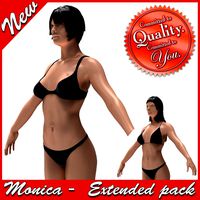
Monica (Extended Pack)
... available on turbo squid, the world's leading provider of digital 3d models for visualization, films, television, and games.
turbosquid
$19
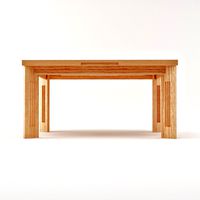
Berlino Extendable Table
... available on turbo squid, the world's leading provider of digital 3d models for visualization, films, television, and games.
turbosquid
$3
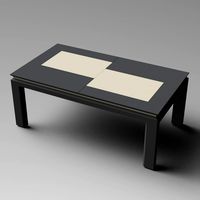
Extendable Modern Table
... available on turbo squid, the world's leading provider of digital 3d models for visualization, films, television, and games.
3d_export
$32
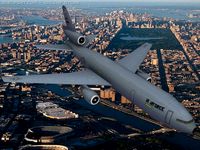
KC10 Extender 3D Model
...c 10 aircraft jet fighter bomber close support interceptor spy attacker plane
kc10 extender 3d model martialartist 24527 3dexport
3d_export
$50
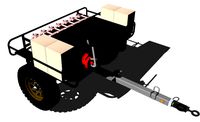
Extended Range Trailer 3D Model
...railer 3d model
3dexport
extended range trailer military patrol equipment
extended range trailer 3d model dougmavs 75684 3dexport
design_connected
$13

Big Dining Tables Extended
...ining tables extended
designconnected
bonaldo big dining tables extended computer generated 3d model. designed by gilles, alain.
C
3ddd
$1
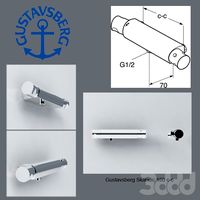
Gustavsberg Skandic 160 c-c
...gustavsberg skandic 160 c-c
3ddd
gustavsberg , смеситель
3dmax 2009
3ddd
$1
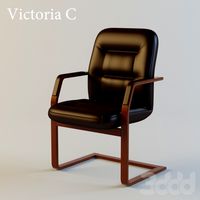
Кресло Victoria C
...кресло victoria c
3ddd
victoria c , стул
victoria c
design_connected
$25
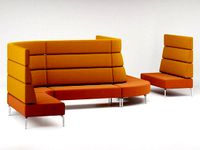
Mobius C
...mobius c
designconnected
zenith mobius c computer generated 3d model. designed by schamburg, marc.
3ddd
$1
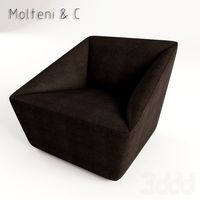
Molteni & C
...molteni & c
3ddd
molteni&c
molteni & c
turbosquid
$10
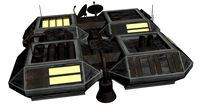
Raids house C&C Tiberian sun
... raids house c&c tiberian sun for download as max and fbx on turbosquid: 3d models for games, architecture, videos. (1188376)
turbosquid
$10
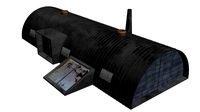
Civilian Asylum C&C Tiberian sun
...ilian asylum c&c tiberian sun for download as max and fbx on turbosquid: 3d models for games, architecture, videos. (1188365)
3ddd
$1
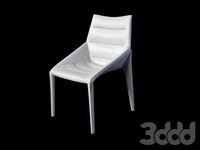
Molteni & C
...molteni & c
3ddd
molteni&c
стул molteni & c
3ddd
free
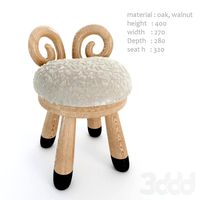
kamina&c
...kamina&c
3ddd
kamina-c , табурет барашек
sheep chair by kamina-c
design_connected
$29
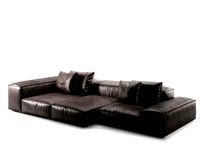
Extrasoft C
...extrasoft c
designconnected
living divani extrasoft c computer generated 3d model. designed by lissoni, piero.
design_connected
$4
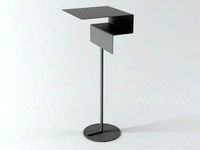
Mono C
...mono c
designconnected
scp mono c tables computer generated 3d model. designed by konstantin grcic.
Mount
3d_export
free
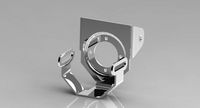
mounting bracket
...mounting plate is the portion of a hinge that attaches to the wood. mounting plates can be used indoors, cabinetry and furniture.
turbosquid
$2
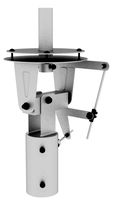
MOUNTING
... available on turbo squid, the world's leading provider of digital 3d models for visualization, films, television, and games.
turbosquid
free
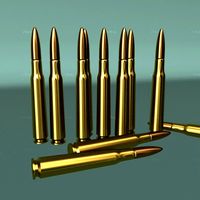
Mounts
... available on turbo squid, the world's leading provider of digital 3d models for visualization, films, television, and games.
turbosquid
free
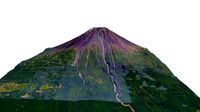
Mount Fuji
...fuji
turbosquid
free 3d model mount fuji for download as obj on turbosquid: 3d models for games, architecture, videos. (1579977)
3d_export
$5
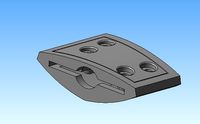
Headphone mount LR
...headphone mount lr
3dexport
headphone mount l+r
turbosquid
$39
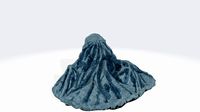
Mount rainier
...quid
royalty free 3d model mount rainier for download as fbx on turbosquid: 3d models for games, architecture, videos. (1492586)
turbosquid
$5
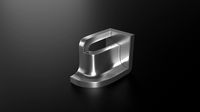
pipe mounting
...quid
royalty free 3d model pipe mounting for download as obj on turbosquid: 3d models for games, architecture, videos. (1293744)
turbosquid
$3
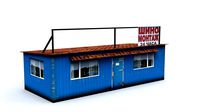
Mounting Tires
...uid
royalty free 3d model mounting tires for download as fbx on turbosquid: 3d models for games, architecture, videos. (1708511)
3d_export
$5
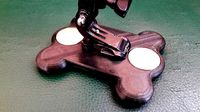
Magnetic GoPro Mount
...pro mount
3dexport
cool magnetic mount for gopro. allows you to mount the camera on flat metal surfaces and get exclusive shots.
turbosquid
$5
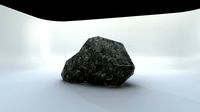
Stone Mount
...ty free 3d model stone mount for download as ma, obj, and fbx on turbosquid: 3d models for games, architecture, videos. (1370306)