GrabCAD

Bell Crank Lever
by GrabCAD
Last crawled date: 1 year, 11 months ago
Name: Ankush Sharma
School: ABES Engineering College
3D printing machine and method: EOS M 290 - Selective Laser Sintering (SLS)
Initial weight of the component = 453 gm
Final weight of the component = 158 gm
Total mass reduction = 65%
In a racing vehicle, every gram accounts for performance and thus optimization of each and every part is important in order to unleash more power on the track.
This project highlights the optimum design of a bell crank lever to be used in a Formula student vehicle by utilizing the capabilities of Topology optimization and additive manufacturing to lower down the weight of the component and not compromising on the strength of the part.
Our main objective is to lower down the weight of a bell crank lever used for transmitting the forces form the pushrod to the shock absorbers.
I started with pen and paper and noted down all the constraints and forces that the part will experience. I used PTC Creo parametric to model the existing bell crank lever used in the previous vehicle. The next step was to simulate the lever and find out exactly from where the material could be removed, for this purpose ANSYS Workbench was used. The results from the simulation suggested that a lot of excess material can be removed which does not contribute to the load-bearing capacity. Topology optimization was then carried out with DfAM in Altair Inspire using maximum stiffness criteria and an optimum shape was extracted from the simulation. After CAD regeneration I simulated the Bell crank in ANSYS again in order to validate the design. The overall mass has been reduced by 65% and the component can bear the maximum stresses it will experience.
SLS 3d printing technology is to be used for the manufacturing of this component. The prefered orientation and support structures were generated in Autodesk Netfabb with the help of EOS M 290 additive manufacturing machine workspace.
Refer to the Documentation for detailed description of design process.
Included in the download: renderings, full design documentation with simulations, STL file of the part with and without support, STEP file of the part and some development images.
School: ABES Engineering College
3D printing machine and method: EOS M 290 - Selective Laser Sintering (SLS)
Initial weight of the component = 453 gm
Final weight of the component = 158 gm
Total mass reduction = 65%
In a racing vehicle, every gram accounts for performance and thus optimization of each and every part is important in order to unleash more power on the track.
This project highlights the optimum design of a bell crank lever to be used in a Formula student vehicle by utilizing the capabilities of Topology optimization and additive manufacturing to lower down the weight of the component and not compromising on the strength of the part.
Our main objective is to lower down the weight of a bell crank lever used for transmitting the forces form the pushrod to the shock absorbers.
I started with pen and paper and noted down all the constraints and forces that the part will experience. I used PTC Creo parametric to model the existing bell crank lever used in the previous vehicle. The next step was to simulate the lever and find out exactly from where the material could be removed, for this purpose ANSYS Workbench was used. The results from the simulation suggested that a lot of excess material can be removed which does not contribute to the load-bearing capacity. Topology optimization was then carried out with DfAM in Altair Inspire using maximum stiffness criteria and an optimum shape was extracted from the simulation. After CAD regeneration I simulated the Bell crank in ANSYS again in order to validate the design. The overall mass has been reduced by 65% and the component can bear the maximum stresses it will experience.
SLS 3d printing technology is to be used for the manufacturing of this component. The prefered orientation and support structures were generated in Autodesk Netfabb with the help of EOS M 290 additive manufacturing machine workspace.
Refer to the Documentation for detailed description of design process.
Included in the download: renderings, full design documentation with simulations, STL file of the part with and without support, STEP file of the part and some development images.
Similar models
grabcad
free

ULA Geometry Optimization
...: 0.972lbm
optimum geometry: 0.416lbm
reduction of 43%
results (stress)
original geometry: 2894.4psi
optimum geometry: 2948.7psi
grabcad
free

Bell crank lever
...bell crank lever
grabcad
design of a bell crank lever
grabcad
free

Simulation Buggy Front Suspension System (Bell Crank Lever)
...on of buggy front suspension system to check total deflection and bell crank lever working and also check strength and stability.
grabcad
free

Crank Shaft
...crank shaft
grabcad
its a 4 cylinder crankshaft with ansys simulations for force loading and heat dissipation simulations
grabcad
free

Bell Crank
...bell crank
grabcad
part name : bell crank
software used : catia v5
rendering : -
module : part design
thingiverse
free
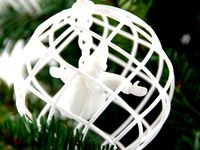
Santa in a Christmas Decoration by imaterialise
...en both designed and tested for use with a high degree of recycled powder. we have not tested to see if it works on makerbot etc.
grabcad
free

Bell Crank Lever
...bell crank lever
grabcad
it's a type of lever...
grabcad
free

Bell Crank Lever
...bell crank lever
grabcad
catia basic training
grabcad
free

crank slotted-lever arm assembly
...crank slotted-lever arm assembly
grabcad
used in manufacturing industries
grabcad
free

Bike Crank
...bike crank
grabcad
bike crank with ansys simulation and results
Crank
3d_export
free
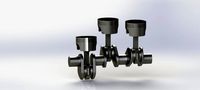
crank shaft
...crank shaft
3dexport
crank shaft with piston with different materials
turbosquid
$3
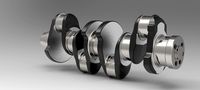
Crank Shaft
...lty free 3d model crank shaft for download as x, ige, and stl on turbosquid: 3d models for games, architecture, videos. (1694841)
turbosquid
$5
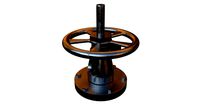
Steel Crank
... available on turbo squid, the world's leading provider of digital 3d models for visualization, films, television, and games.
design_connected
$13
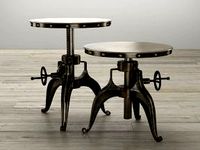
Crank 22 End Table
...crank 22 end table
designconnected
four hands crank 22 end table computer generated 3d model.
turbosquid
$50
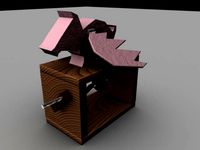
Wooden Crank Toy
... available on turbo squid, the world's leading provider of digital 3d models for visualization, films, television, and games.
turbosquid
$19

Crank Wheel Highpoly
... available on turbo squid, the world's leading provider of digital 3d models for visualization, films, television, and games.
3d_export
$7
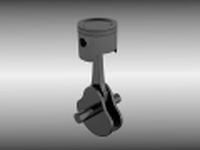
Piston and crank 3D Model
...ycle bearing pulley push rod valve bolt spring screw metal new moped stroke
piston and crank 3d model dragosburian 80941 3dexport
3d_export
$15

Hand Cranked Sharpener 3D Model
...cranked spring office supplies sharp supply tools equipment school writing
hand cranked sharpener 3d model firdz3d 84605 3dexport
3d_export
$9
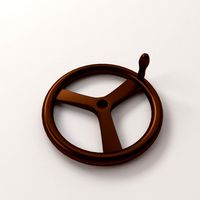
Crank Wheel 3D Model
...ainless iron industrial machine
crank wheel 3d model download .c4d .max .obj .fbx .ma .lwo .3ds .3dm .stl firdz3d 105897 3dexport
turbosquid
free
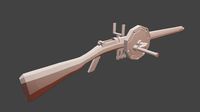
Low Poly Crank Gun
...bosquid
free 3d model low poly crank gun for download as fbx on turbosquid: 3d models for games, architecture, videos. (1436642)
Lever
turbosquid
$1
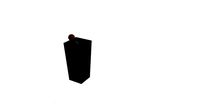
Lever
... available on turbo squid, the world's leading provider of digital 3d models for visualization, films, television, and games.
turbosquid
$26
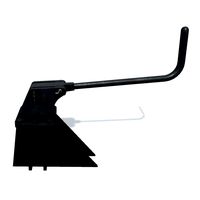
Stopper lever
...quid
royalty free 3d model stopper lever for download as fbx on turbosquid: 3d models for games, architecture, videos. (1255553)
3ddd
$1
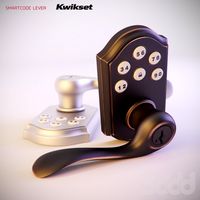
Kwikset / SmartCode Lever
...kwikset / smartcode lever
3ddd
дверная ручка
kwikset smartcode lever
3d_ocean
$28
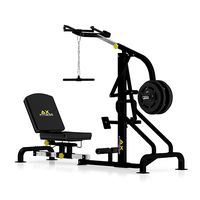
Lever Gym Machine
...equipement gym gymnastic indoor lever machine pull sport workout yellow
3d model of black lever gym machine with yellow elements.
turbosquid
$15

Clutch lever
... available on turbo squid, the world's leading provider of digital 3d models for visualization, films, television, and games.
turbosquid
free
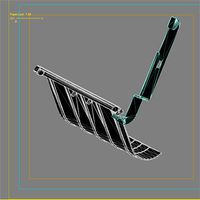
LEVER TEST.max
... available on turbo squid, the world's leading provider of digital 3d models for visualization, films, television, and games.
turbosquid
$129
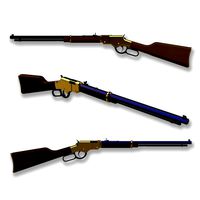
Lever Action Rifle
...
royalty free 3d model lever action rifle for download as obj on turbosquid: 3d models for games, architecture, videos. (1327623)
turbosquid
$59
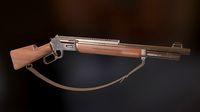
Winchester Lever Rifle
...alty free 3d model winchester lever rifle for download as fbx on turbosquid: 3d models for games, architecture, videos. (1244383)
turbosquid
$3
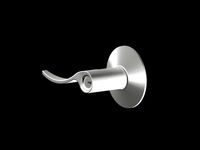
DOOR LEVER ADA
...uid
royalty free 3d model door lever ada for download as max on turbosquid: 3d models for games, architecture, videos. (1178553)
turbosquid
$26
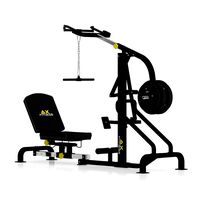
Lever Gym Machine
... available on turbo squid, the world's leading provider of digital 3d models for visualization, films, television, and games.
Bell
archibase_planet
free
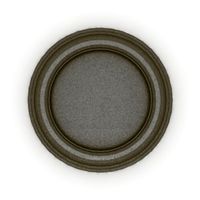
Bell
...bell
archibase planet
doorbell bell electric bell
bell n050707 - 3d model for interior 3d visualization.
archibase_planet
free
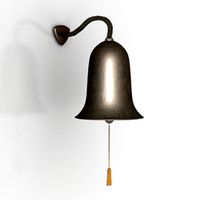
Bell
...bell
archibase planet
bell hand bell
bell n020613 - 3d model (*.gsm+*.3ds) for interior 3d visualization.
3d_export
$5
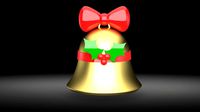
bell
...bell
3dexport
bell ornament
design_connected
$13
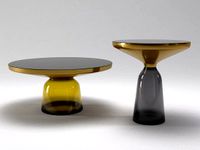
Bell
...bell
designconnected
classicon bell computer generated 3d model. designed by herkner, sebastian.
design_connected
$16

Bell
...bell
designconnected
normann copenhagen bell computer generated 3d model. designed by lund, andreas.
design_connected
$13
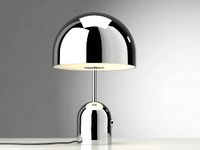
Bell
...bell
designconnected
tom dixon bell computer generated 3d model. designed by dixon, tom.
design_connected
$16
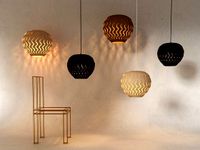
Belle
...belle
designconnected
david trubridge design belle computer generated 3d model. designed by trubridge, david.
3d_ocean
$5
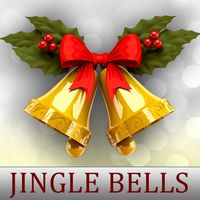
Christmas Bell
...stmas bell jingle bell
this model created in 3ds max 2013 rendering using vray. it is very easy to use. the poly count is 124604.
turbosquid
$25
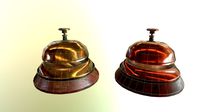
Bell
...ll
turbosquid
royalty free 3d model bell for download as obj on turbosquid: 3d models for games, architecture, videos. (1513176)
3d_export
$17
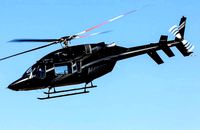
Bell 427
...bell 427
3dexport
bell 427