Thingiverse
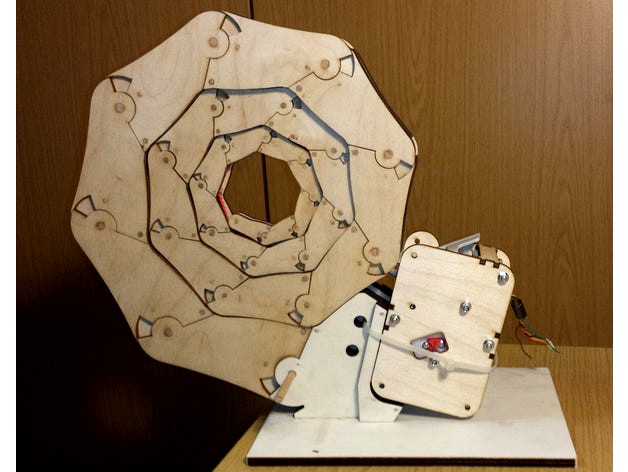
Articulated Spiral Arm by juewei
by Thingiverse
Last crawled date: 2 years, 10 months ago
An articulated arm made out of plywood. Its movement reminds me of an unfolding fern leaf, or a (somewhat stiff) octopus arm.
This object was inspired by John Edmark, who invented more fantastic things.
The lasercut parts are designed with inkscape. The sides of the arm are drawn in their rolled up position, they almost completely fill the plane.
You can still see how the grains of wood continue, when the arm fully rolled up.
I am adding different amounts of spacers between the two sides, to that the arm becomes a more natural 3-dimensional object.
The sides are cut out of 4mm birch plywood using arm-8er-shaped_laser3mm.svg (arm-8er-shaped_laser4mm.svg has the same for 3mm sides).
Either svg file also includes the needed spacers. For the spacers you need 3, 4 and 5 mm plywood, so that they can be stacked for all the
different widths needed. See spacers.txt for the exact stacking. The shafts for mounting the segments are cut from beechwood rods with are
6mm, 4mm, 3mm, and 2mm diameter. The 2mm ones are simply toothpics. I love toothpicks. You'll need lots of them, the often also serve as alignment pins.
My design includes 26 segments, with 8 segments per revolution.
You can hold the arm in your hands and pull the string to play with it. But as it is rather large and heavy, I also made a mount and an electric drive for it.
The mount is made out of 8mm plywood. Gluing the tabs firmly into the base plate is important. As the arm gives a strong pull there, when fully extended.
The base should be secured to the table with a clamp or several kg of counterweight to prevent it from flipping over.
There are several holes in the base. You can use them to mount the base on a tripod (if you dare), or connect multiple bases side by side fanning out the arms in
in 15°, 30° or 45° angle (just in case you want to complete an octopus eventually).
The electric drive is based on an inexpensive worm gear motor found on ebay. It runs from 12v and takes less than 1A.
It is built into a gearbox with lasercut gears from 3mm POM and a 3D-printed spool for winding up the string. The 3D-print design was made with FreeCAD.
All the STL-files in the drive folder were exported from the drum.FCstd drawing.
The motor is controlled by an Atmel ATTINY 2313 microcontroller connected to an L298N motor bridge.
the logic is very simple. The winds up the string, until the arm is fully curled up and hits a push-button in the mount. Then the motor rotation is reversed, so that it unrolls again. There is no reversal needed for the unrolled position, as the spool simply winds up the string again after it was fully unrolled.
You can also use an arudino-nano or similar instead of the bare metal 2313 -- programming a nano or uno is easier than. But for some reason I prefered to be minimalistic with the electronics. (Well, the 128 bytes RAM are almost full.)
If you can come up with a mechanical reversal switch that reliably works with this arm, please let me know. I failed to come up with something sufficiently robust, and went for the electronic solution instead.
This object was inspired by John Edmark, who invented more fantastic things.
The lasercut parts are designed with inkscape. The sides of the arm are drawn in their rolled up position, they almost completely fill the plane.
You can still see how the grains of wood continue, when the arm fully rolled up.
I am adding different amounts of spacers between the two sides, to that the arm becomes a more natural 3-dimensional object.
The sides are cut out of 4mm birch plywood using arm-8er-shaped_laser3mm.svg (arm-8er-shaped_laser4mm.svg has the same for 3mm sides).
Either svg file also includes the needed spacers. For the spacers you need 3, 4 and 5 mm plywood, so that they can be stacked for all the
different widths needed. See spacers.txt for the exact stacking. The shafts for mounting the segments are cut from beechwood rods with are
6mm, 4mm, 3mm, and 2mm diameter. The 2mm ones are simply toothpics. I love toothpicks. You'll need lots of them, the often also serve as alignment pins.
My design includes 26 segments, with 8 segments per revolution.
You can hold the arm in your hands and pull the string to play with it. But as it is rather large and heavy, I also made a mount and an electric drive for it.
The mount is made out of 8mm plywood. Gluing the tabs firmly into the base plate is important. As the arm gives a strong pull there, when fully extended.
The base should be secured to the table with a clamp or several kg of counterweight to prevent it from flipping over.
There are several holes in the base. You can use them to mount the base on a tripod (if you dare), or connect multiple bases side by side fanning out the arms in
in 15°, 30° or 45° angle (just in case you want to complete an octopus eventually).
The electric drive is based on an inexpensive worm gear motor found on ebay. It runs from 12v and takes less than 1A.
It is built into a gearbox with lasercut gears from 3mm POM and a 3D-printed spool for winding up the string. The 3D-print design was made with FreeCAD.
All the STL-files in the drive folder were exported from the drum.FCstd drawing.
The motor is controlled by an Atmel ATTINY 2313 microcontroller connected to an L298N motor bridge.
the logic is very simple. The winds up the string, until the arm is fully curled up and hits a push-button in the mount. Then the motor rotation is reversed, so that it unrolls again. There is no reversal needed for the unrolled position, as the spool simply winds up the string again after it was fully unrolled.
You can also use an arudino-nano or similar instead of the bare metal 2313 -- programming a nano or uno is easier than. But for some reason I prefered to be minimalistic with the electronics. (Well, the 128 bytes RAM are almost full.)
If you can come up with a mechanical reversal switch that reliably works with this arm, please let me know. I failed to come up with something sufficiently robust, and went for the electronic solution instead.
Similar models
thingiverse
free
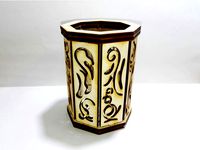
wind proofed lantern V2 - lasercut by Peter02
... of 4mm plywood. to get it wind proofed, you need 3mm acrylic glass.
i posted it as a remix, so you can get to the first version.
thingiverse
free
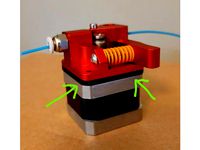
Extruder Motor Spacer for 3DFused Direct Drive mount by Critterninja
...ere, just a 3mm thick spacer, set to the same shape of the standard 42x42mm motor and a hole in the middle to fit over the shaft.
thingiverse
free

Vex 393 motor mount for tetrix
...and claw from vex, in result we have a very strong mount.
two directions - 3d printing or lasercut plywood 3mm and plastic 0.5mm.
grabcad
free

Vex 393 motor mount for tetrix
...nd claw from vex, in result we have a very strong mount.
two directions - 3d printing or lasercut plywood 3mm and plastic 0.5mm.
thingiverse
free
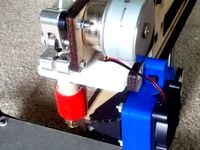
2014 Printrbot Simple 3mm Geared motor mount by metaled
...he plug if your motor runs in reverse/
this is an exact replacement for the 2014 printerbot simple's extruder mounting plate.
thingiverse
free
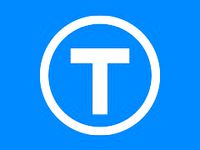
Drawbot NEMA 17 flat motor mount by skrubis
...
my pla motor mounts warped due to me not adjusting the current accordingly, so i made some out of plywood to be lasercut. enjoy.
thingiverse
free
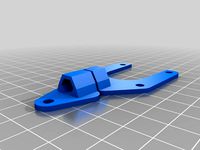
Spring-loaded Ultimaker short belt tensioner by JelleBoomstra
...ve the newer plastic spacers you probably need screws a little longer (2mm) or you can get by with 2mm less thread in the motors?
thingiverse
free
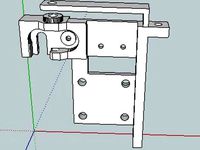
3mm version of UP! printer filament feeder by RonLight
... arm direction.
added support from the pcb holder to motor holder.
added 'ramps' to additionally hold the motor in place.
thingiverse
free
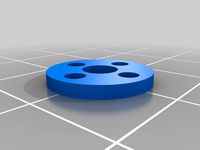
110x Motor Spacer
...ng out the mount screws on some motors, allow for more space for the snap ring on others, and to shim motors on yet other builds.
thingiverse
free
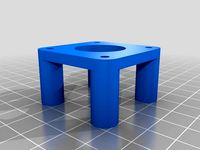
motor mount by XennoNL
...n move the motor out of the way and do not need to reverse the settings in the firmware. you just need long m3 bolts and washers.
Juewei
thingiverse
free
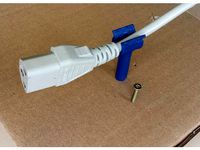
CarlosCableClip by juewei
...carloscableclip by juewei
thingiverse
just made this for a friend, because i just love parameterized sketches with freecad.
thingiverse
free

RPI_CamBow_jw by juewei
...variation of http://www.thingiverse.com/thing:96736 but with nice mounting ears at the back, so that it can be secured to a wall.
thingiverse
free
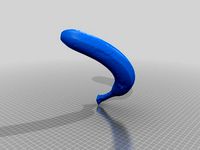
Banana for Scale by juewei
...banana for scale by juewei
thingiverse
just a banana. not to scale.
ideas welcome, how the texture could be applied.
thingiverse
free
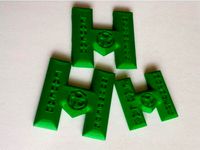
Hack&Make chocolate model by juewei
...hack&make chocolate model by juewei
thingiverse
this is a model for making chocolate
thingiverse
free
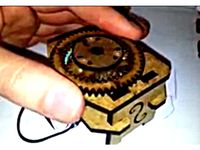
HaPla-Drive by juewei
...jnweiger/hapla-drive
sorry for the blurry photo and hairlines svg. this dates back to 2013, when the internet was very different.
thingiverse
free
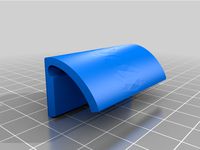
Ketten-Rollator by juewei
...r chains to use in rough terrain.
the first video below was broadcast on december 21, 2020 in br3, "abendschau aktuell"
thingiverse
free
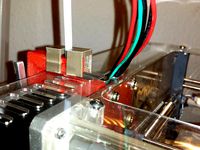
Makibox JW Upgrade by juewei
...ewei
thingiverse
there are a lot of small mods i did to my makibox.
if anybody asks for it, i'll upload drawings and specs..
thingiverse
free
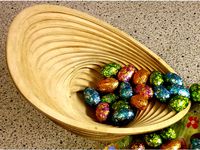
Ostereierschale by juewei
... assembly aid. use toothpicks to align the rings.
originally published at https://wiki.fablab-nuernberg.de/w/ding:ostereierschale
thingiverse
free
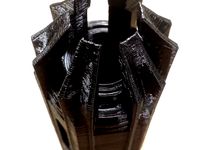
NERF-barrel-extension-dracohex-claw by juewei
...hex-claw by juewei
thingiverse
hexagon remix from http://www.thingiverse.com/thing:451186
with extra evil fingers at the nozzle.
thingiverse
free
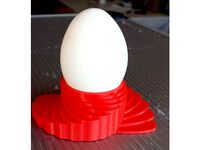
2.5D Eierbecher by juewei
...s see there.
printed on a tronxy-xy100 with 0.1mm in pla.
the top surfaces demonstrate the concentric fill pattern found in cura.
Articulated
turbosquid
$60

Articulated doll
...e 3d model articulated doll for download as max, obj, and ztl on turbosquid: 3d models for games, architecture, videos. (1277424)
turbosquid
$10
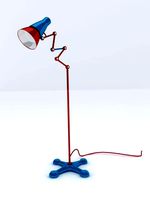
articulated lamp
... available on turbo squid, the world's leading provider of digital 3d models for visualization, films, television, and games.
design_connected
$11
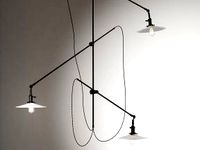
Articulated Industrial Light
...articulated industrial light
designconnected
o. c. white articulated industrial light computer generated 3d model.
cg_studio
$169
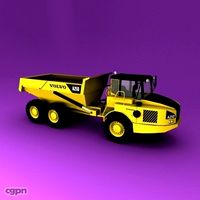
Articulated Truck3d model
...cgstudio
.3ds .c4d .lwo .max .obj - articulated truck 3d model, royalty free license available, instant download after purchase.
3d_export
$90
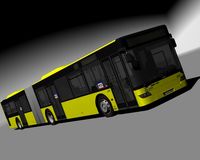
Design Bus Articuled 3D Model
...design bus articuled 3d model
3dexport
design bus articuled
design bus articuled 3d model basshunter 8620 3dexport
turbosquid
$59
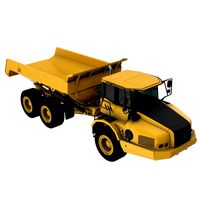
Articulated truck 45f
... available on turbo squid, the world's leading provider of digital 3d models for visualization, films, television, and games.
3d_ocean
$130

Caterpillar 725 Articulated Truck
...for close-up renders. scene contain textures, standart scanline, mentalray and vray materials. - high quality polygonal model ...
3d_export
$22

articulated dump truck
...ost popular and not very 3d file formats, as well as textures for shaders.<br>format: 3ds max, obj, fbx, 3ds, lwo, c4d, dae
turbosquid
free

Rigged articulated bus acordion bus for games
...or download as max, max, unitypackage, max, fbx, obj, and 3ds on turbosquid: 3d models for games, architecture, videos. (1599911)
3d_export
$24
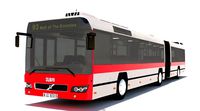
dubai bus articulated
...ed check if our models are useful for your project and leave a like if you like this model.<br>thank you for your interest!
Spiral
3ddd
$1

italamp spirale
...italamp spirale
3ddd
italamp , spirale
italamp spirale
3ddd
free
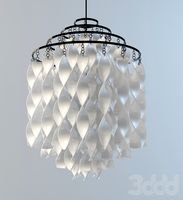
Verpan / Spiral
...verpan / spiral
3ddd
spiral , verpan
verpan люстра spiral
3d_export
free
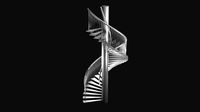
Spiral staircase
...spiral staircase
3dexport
spiral staircase
turbosquid
$5
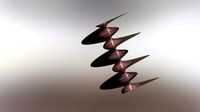
Spiral
...quid
royalty free 3d model spiral for download as and sldpr on turbosquid: 3d models for games, architecture, videos. (1214311)
3d_export
$5

Spiral lamp
...spiral lamp
3dexport
spiral lamp in modern style.
turbosquid
$59
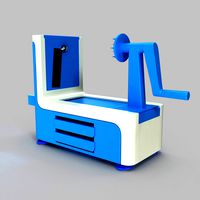
Spiralizer
... available on turbo squid, the world's leading provider of digital 3d models for visualization, films, television, and games.
3d_ocean
$4

Spiral stairs
...spiral stairs
3docean
spiral stairs
spiral stairs 270 cm high inner radius 40 cm outer radius 120 cm
3d_export
$5
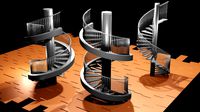
Spiral stairs
...spiral stairs
3dexport
spiral stairs<br>.blend
3d_export
$9
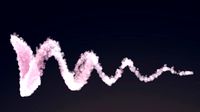
vdb spiral
...vdb spiral
3dexport
vdb spiral with different resolutions: low, middle and high
3d_ocean
$17
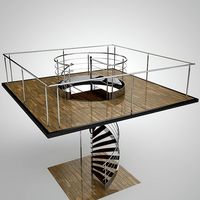
Spiral staircase
...uble handle handrail interior lux luxury metal modern open stairs realistic render spiral stair staircase stairs
spiral staircase
Arm
archibase_planet
free
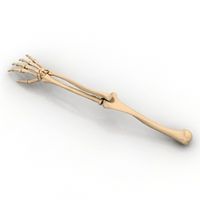
Arm
...ase planet
arm hand right hand skeleton
arm human skeleton right arm n030515 - 3d model (*.gsm+*.3ds+*.max) for 3d visualization.
3ddd
$1
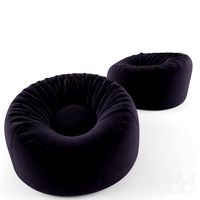
arm chair
...arm chair
3ddd
arm chair , пуф
arm chair
turbosquid
$5
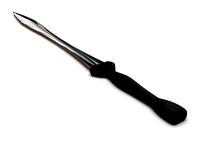
arm
...arm
turbosquid
royalty free 3d model arm for download as obj on turbosquid: 3d models for games, architecture, videos. (1306158)
turbosquid
free
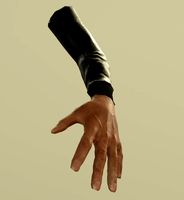
Arm
...arm
turbosquid
free 3d model arm for download as obj and fbx on turbosquid: 3d models for games, architecture, videos. (1346955)
turbosquid
$29
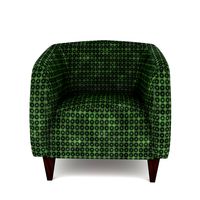
Arm
...osquid
royalty free 3d model arm for download as obj and fbx on turbosquid: 3d models for games, architecture, videos. (1382436)
3d_export
$5
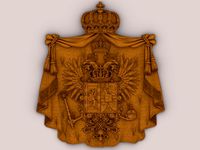
coat of arms
...coat of arms
3dexport
coat of arms
3ddd
$1
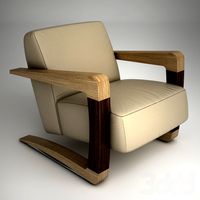
ARM SOFA
...arm sofa
3ddd
arm sofa
3ddd
$1
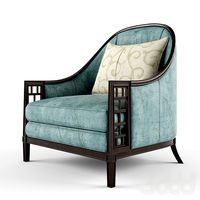
Arm chair
...arm chair
3ddd
arm chair
3ddd
$1
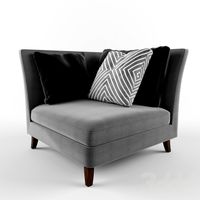
Arm chair
...arm chair
3ddd
угловое
arm chair
3ddd
$1
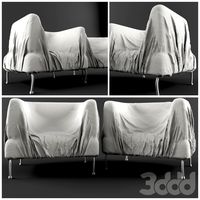
ARM CHAIR
...arm chair
3ddd
arm chair clothes