Thingiverse
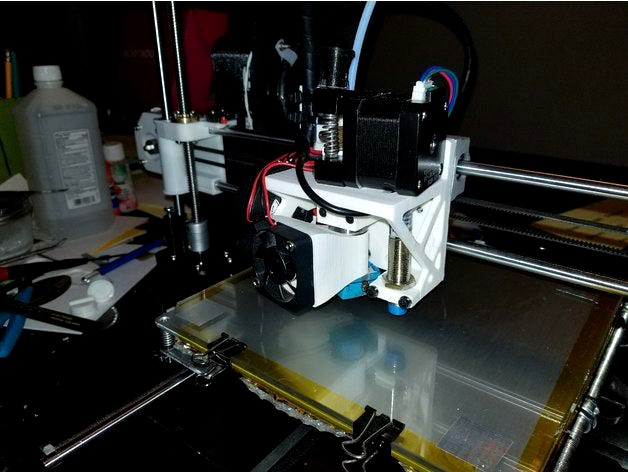
Anet A8 E3D Direct X-Carriage w/ Probe (46mm) by truglodite
by Thingiverse
Last crawled date: 3 years ago
I am giving credit to IsmaelPR1 for his a8 e3d direct mount design, which I used as inspiration for my x carriage design. His original design is unfortunately meant for 45mm rod spacing (older a8's), lacked a decent z probe mount solution (other remixes with probes were off mark IMHO), and had some minor design issues (mainly the X-belt hole fit, and cooling flow arrangement). I also wanted to add a few creature comforts to complete the bill; so I got out my calipers and freecad, and started from scratch for a complete redraw.
This carriage fits newer A8's with 46mm rod spacing. I added a mount for an M12x1 threaded probe, with 0 y offset, and 33mm x offset (...17b.stl, otherwise see update for M18 probes). There is also a teardrop shape hole above the probe mount to give clearance for larger probes (my clone induction probe is LOOOONG and needs that room for the wires). I also redesigned the right side structure to improve air flow. I added a strain relief for the wires, a slotted hole to further secure the extruder motor, and a tons of fillets to make it more robust. I added a small chamfer on the top of the hotend mounting "ring". This small feature is important to keep the extruder locked in the proper position (prusa i3 has it too). I also increased the distance between the top bearings to 18mm. No reason not to do this as it doesn't reduce build volume, and it greatly reduces carriage rocking. Last but not least, I added up arrows to the hotend and probe straps. Hopefully they will never get installed upside down this way. ;)
I have this thing printed in abs, 60% bicubic infill, 1mm walls, and board only supports (recommended settings updated... see below). The strain relief part unfortunately requires support. I chose a 40mm hotend fan duct by ChPech for my BB fan, a Mistral 2.1 part blower duct by Leo_N, and an X-belt clip by Simhopp for my printed accessories. I feel those parts are very well engineered, but other options will likely also fit. Everything fit together like a glove for me. This thing has been installed and printing ABS, PLA, and Nylon for >400hrs with zero issues.
[edit: Anticipating questions about the path from extruder wheel to the hotend... It uses an e3d clone with a bowden style heatsink, with the bowden tube fitting removed. The stock A8 throat is inverted so the wider teflon lined end goes down. To assemble first install the e3d, then slide the nut on top of the e3d. Then cut new teflon tube (about 4" long) just the right length so that the motor sits down completely on the top plate without having to squish hard on the tube, and not being too short so the tube can move with retraction (tighten the heartbreak properly before you trim the tube). Slide this tube in to the inverted stock throat, put the motor/top-throat/tube down the hole into the e3d, and tighten the nut. You may have to use some teflon tape, threadlock compound, or pliers on the throat/motor threads as tightening the nut without may result in pulling the throat up into the extruder wheel (a flex adapter helps prevent this... I used this one https://www.thingiverse.com/thing:2551063). Optionally, you can use the slotted hole to further secure the motor with an M4 screw. I omitted this myself so I could rotate the motor CG closer to the x-bars.]
Update 5-10-18: I recently bought a Winsinn titanium heat break, which has smaller threads than the steel heat break that came with my clone e3d Bowden hotend. I had a spare e3d direct hotend that has smaller threads. To use it I had to shorten the stock heat break tube about 8mm with my dremel cutoff wheel. I also had to shorten the ptfe tube to fit. It has been working great in a 50C enclosure for several prints. The Winsinn came with a decently polished throat, but I went over it with 1000grit wet sandpaper and a dremel to be sure. ...second update re Ti heatbreaks... Occasionally printing Nylon, the Ti heatbreak failed randomly due to heat creep. I went back to a stainless steel throat and the issues have disappeared (I believe the higher specific heat of stainless helps prevent spikes of heat from running up the hotend).
Update 6-27-18: After building a heated enclosure to print nylon (@50C ambient), I observed 2 things. 1) The probe mount warped downward due to a bit of tension on the probe wire, and 2) The x-belt clip warped and widened enough to let the belt slip a tooth when tensioned. So I reprinted this carriage with 2.5mm walls and 1.7mm floors/cielings for increased strength, and I remixed the x belt clip for an 0.9mm belt clearance vs 1.0mm for a tighter grip. So far I've gone through a half roll of bridge with the enclosure at 50C without issues.
Update 8-2-2018: As requested, I uploaded "17c" version STL's for those who have M18-1 size probes. This carriage has a slightly smaller X probe offset of 32mm (still 0 y offset). You may notice some other changes from my original; round part missing from the strain relief, fillets slightly different, and file size is much larger. The reason for the former changes is the way I modeled the original was a PITA to modify so some things had to get completely redone (and I left out the less important details to save time). The reason the STL's are so large is simple; I upped the resolution of in Freecad so the rendered meshes are much smoother (and larger). Enjoy!
This carriage fits newer A8's with 46mm rod spacing. I added a mount for an M12x1 threaded probe, with 0 y offset, and 33mm x offset (...17b.stl, otherwise see update for M18 probes). There is also a teardrop shape hole above the probe mount to give clearance for larger probes (my clone induction probe is LOOOONG and needs that room for the wires). I also redesigned the right side structure to improve air flow. I added a strain relief for the wires, a slotted hole to further secure the extruder motor, and a tons of fillets to make it more robust. I added a small chamfer on the top of the hotend mounting "ring". This small feature is important to keep the extruder locked in the proper position (prusa i3 has it too). I also increased the distance between the top bearings to 18mm. No reason not to do this as it doesn't reduce build volume, and it greatly reduces carriage rocking. Last but not least, I added up arrows to the hotend and probe straps. Hopefully they will never get installed upside down this way. ;)
I have this thing printed in abs, 60% bicubic infill, 1mm walls, and board only supports (recommended settings updated... see below). The strain relief part unfortunately requires support. I chose a 40mm hotend fan duct by ChPech for my BB fan, a Mistral 2.1 part blower duct by Leo_N, and an X-belt clip by Simhopp for my printed accessories. I feel those parts are very well engineered, but other options will likely also fit. Everything fit together like a glove for me. This thing has been installed and printing ABS, PLA, and Nylon for >400hrs with zero issues.
[edit: Anticipating questions about the path from extruder wheel to the hotend... It uses an e3d clone with a bowden style heatsink, with the bowden tube fitting removed. The stock A8 throat is inverted so the wider teflon lined end goes down. To assemble first install the e3d, then slide the nut on top of the e3d. Then cut new teflon tube (about 4" long) just the right length so that the motor sits down completely on the top plate without having to squish hard on the tube, and not being too short so the tube can move with retraction (tighten the heartbreak properly before you trim the tube). Slide this tube in to the inverted stock throat, put the motor/top-throat/tube down the hole into the e3d, and tighten the nut. You may have to use some teflon tape, threadlock compound, or pliers on the throat/motor threads as tightening the nut without may result in pulling the throat up into the extruder wheel (a flex adapter helps prevent this... I used this one https://www.thingiverse.com/thing:2551063). Optionally, you can use the slotted hole to further secure the motor with an M4 screw. I omitted this myself so I could rotate the motor CG closer to the x-bars.]
Update 5-10-18: I recently bought a Winsinn titanium heat break, which has smaller threads than the steel heat break that came with my clone e3d Bowden hotend. I had a spare e3d direct hotend that has smaller threads. To use it I had to shorten the stock heat break tube about 8mm with my dremel cutoff wheel. I also had to shorten the ptfe tube to fit. It has been working great in a 50C enclosure for several prints. The Winsinn came with a decently polished throat, but I went over it with 1000grit wet sandpaper and a dremel to be sure. ...second update re Ti heatbreaks... Occasionally printing Nylon, the Ti heatbreak failed randomly due to heat creep. I went back to a stainless steel throat and the issues have disappeared (I believe the higher specific heat of stainless helps prevent spikes of heat from running up the hotend).
Update 6-27-18: After building a heated enclosure to print nylon (@50C ambient), I observed 2 things. 1) The probe mount warped downward due to a bit of tension on the probe wire, and 2) The x-belt clip warped and widened enough to let the belt slip a tooth when tensioned. So I reprinted this carriage with 2.5mm walls and 1.7mm floors/cielings for increased strength, and I remixed the x belt clip for an 0.9mm belt clearance vs 1.0mm for a tighter grip. So far I've gone through a half roll of bridge with the enclosure at 50C without issues.
Update 8-2-2018: As requested, I uploaded "17c" version STL's for those who have M18-1 size probes. This carriage has a slightly smaller X probe offset of 32mm (still 0 y offset). You may notice some other changes from my original; round part missing from the strain relief, fillets slightly different, and file size is much larger. The reason for the former changes is the way I modeled the original was a PITA to modify so some things had to get completely redone (and I left out the less important details to save time). The reason the STL's are so large is simple; I upped the resolution of in Freecad so the rendered meshes are much smoother (and larger). Enjoy!
Similar models
thingiverse
free
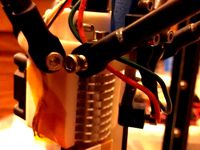
Kossel E3D bowden effector by timpetrillo
... probe tip. the config.h settings are 20mm offset and the z probe is 21.5 offset in the y direction if mounted the standard way.
thingiverse
free
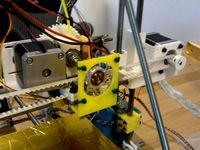
RepRap Prusa extruder fan mount by maakit
...riage and extruder in abs.
so i designed a simple mounting plate for a 4cm fan which bolts on to the bottom of the x-belt clamps.
thingiverse
free
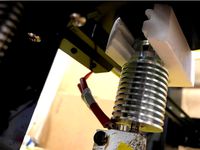
Anet A6 E3D V6 mount plate by ant82
... screw hotend on to m6 bolt, then insert mounting plate (i heated top of e3d with hot air) and tighten the screw to the carriage.
thingiverse
free
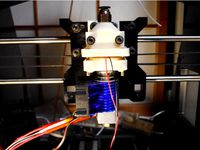
Precision Piezo and E3D V6, holder for E3D V6 and one touch connector by YMita
...touch connector which holds teflon tube.
i use precision piezo - piezo20 hotend z probe https://www.thingiverse.com/thing:2319993
thingiverse
free
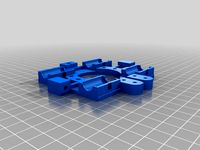
X Carriage for E3D Nozzle by Emadine
...m and most x carriage have not enough room for it so i make this, this is for the 50mm apart smooth rod and 50mm extruder mount.
thingiverse
free
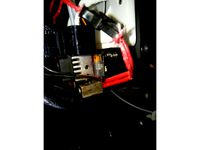
LPA Modular X Carriage Daughter Plates with BLTouch by bkbreyme
...with the fan mount facing downward.
added additional diamond mount based on lhartmann's version with extra attachment points.
thingiverse
free
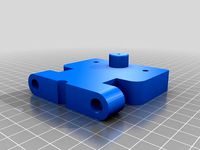
Bowden setup for E3D Hotend on Prusa I2 by Neodd70
...at comes with the e3d hotend. it has been designed to mount the majority of the hotend above the x carriage to maximize z travel.
thingiverse
free
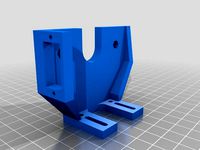
Graber I3 extruder support with servo mount by AlexBorro
...support and about 20% infill.
the extruder mount holes are 50mm spaced and the x-carriage mount holes are 30mm spaced.
enjoy.
thingiverse
free
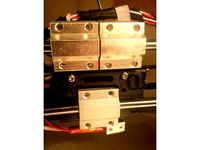
Anet X Belt Mount by Schneiderg
...ar) a8 (2016 edition)
i used the original screws that mount the belt to the extruder carriage so no need for additional hardware
thingiverse
free

x carriage by shocker
...ker
thingiverse
i had to redesign my x carriage to fit my bulldog lite extruder with a hexagon hotend, it is for the echoprinter
Truglodite
thingiverse
free
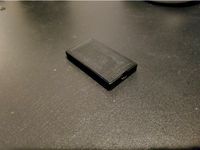
RCWL-0516 Cover by truglodite
... made it thin but with some clearance, to save filament and minimize interference. it fits nicely for me printed in abs on my a8.
thingiverse
free
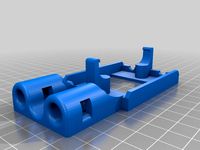
SSR Cover (Remix) by truglodite
.... a pair of zipties may be used to secure the wires in their tubes. sized to work with larger wires and crimp on spade terminals.
thingiverse
free
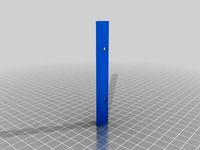
8mm LED Strip Clip by truglodite
... have to remove the adhesive backing, but loose enough to where you can still slide the strip in even if the adhesive is exposed.
thingiverse
free

Ramps Enclosure Remix (lid pin added) by truglodite
.... so i did this remix to add a flange and holes to accept a pin/bolt that locks the lid shut (so it won't fall from gravity).
thingiverse
free
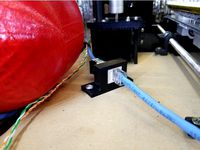
Keystone Surface Mount (single) by truglodite
...small gap on 2 sides of the keystone's face once installed, but it's barely noticeable and they still hold very securely.
thingiverse
free
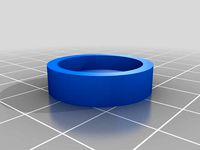
Anet A8 20mm Printed Rubber Foot by truglodite
... flat headed screws. i just used some small self tapping flat heads, but a set of machine screws and nuts could also get it done.
thingiverse
free
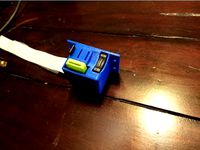
Micro SD Card Extension, Cards, & Stick Mount by truglodite
... room is for my larger usb3 readers to fit, but the standard usb hole inside secures smaller sticks too. prints without supports.
thingiverse
free
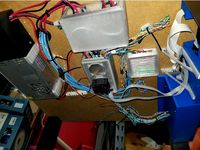
4ch Mosfet Enclosure by truglodite
...assive cooling. the slots alone are adequate for my application, but comment if you need me to add a lid with a fan port instead.
thingiverse
free
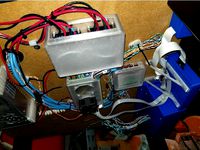
Double Mosfet Box by truglodite
...n to save filament. the dimensions are designed for a 0.45mm printer line width (0.4mm nozzle), but other settings may work fine.
thingiverse
free
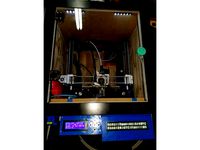
IEE VFD Enclosure Control Box by truglodite
...cts where you want a honkin' big vfd with "3 button menus". i made the rear compartment over sized for this reason.
46Mm
3d_export
$35

samsung galaxy watch 4 classic 46mm
...** blender 2.93.6.0** we reserve the rights to minor deviations and errors. previews images are sometimes hard to create as real.
3d_export
$20
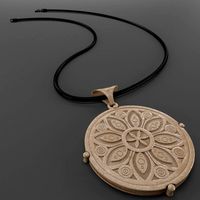
beauty pendant
...file format: max 2013, (vray)(corona) render, fbx, obj, 3ds,stl<br>size 46mm x 59mm x...
3d_export
$10
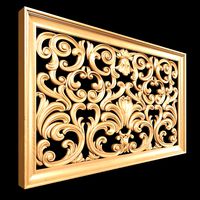
classical decorative screen
...(l * h * d): 833 x 499 x 46mmlt;br>* polys: 305 940<br>* .stl file included<br>3d model detailed enough...
3d_export
$35
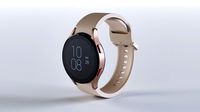
samsung galaxy watch 4 44mm
...samsung galaxy watch 4 44mm 3dexport info dimensions: 46mm 44.4 x 43.3 x 9.8mm, 30.3g (approximately) you get...
thingiverse
free
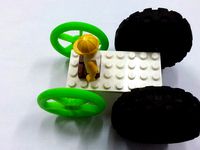
Lego 46mm wheel by mogey336
...lego 46mm wheel by mogey336
thingiverse
lego 46mm wheel
thingiverse
free
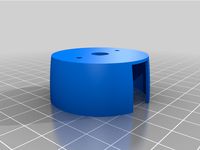
Spinner 46mm
...meter of 46mm so it matches perfectly with middle piece of 47mm. use small, short wood screw to assemble the two pieces together.
thingiverse
free
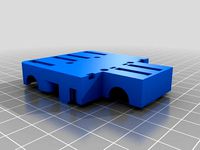
46mm a8 carrier by MrblueGray
...46mm a8 carrier by mrbluegray
thingiverse
46mm carrier with holes to match e3d v6 mount i remixed
thingiverse
free

Adapter filter 46mm to Gopro 3 by Martin_Tandil
...adapter filter 46mm to gopro 3 by martin_tandil
thingiverse
adapter filter 46mm
thingiverse
free
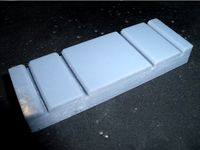
H0 NEM 46mm tracks spacer by droz1
...h0 nem 46mm tracks spacer by droz1
thingiverse
h0 nem 46mm tracks spacer
thingiverse
free

WPL race wheel 46mm
...wpl race wheel 46mm
thingiverse
fits to meccano tires
Probe
turbosquid
$25
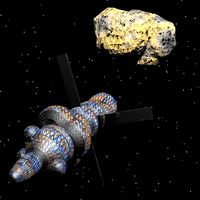
Probe
... available on turbo squid, the world's leading provider of digital 3d models for visualization, films, television, and games.
turbosquid
$12
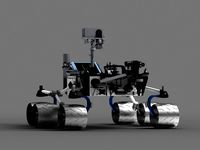
Mars probe space space exploration lunar probe
...be space space exploration lunar probe for download as max on turbosquid: 3d models for games, architecture, videos. (1630876)
turbosquid
$35

Space Probe
...osquid
royalty free 3d model space probe for download as c4d on turbosquid: 3d models for games, architecture, videos. (1571168)
turbosquid
$15
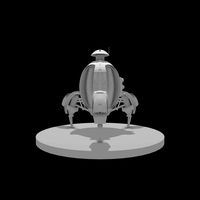
Space Probe
...osquid
royalty free 3d model space probe for download as obj on turbosquid: 3d models for games, architecture, videos. (1314864)
turbosquid
$25
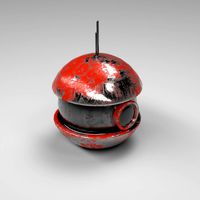
Robot Probe
...y free 3d model robot probe for download as fbx, obj, and dae on turbosquid: 3d models for games, architecture, videos. (1537490)
turbosquid
$1
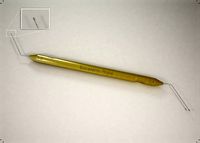
Dental Probe
...e 3d model dental probe for download as ma, obj, fbx, and stl on turbosquid: 3d models for games, architecture, videos. (1312400)
turbosquid
$60
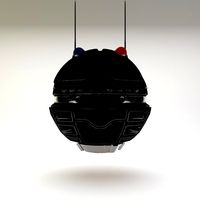
Police Probe
... available on turbo squid, the world's leading provider of digital 3d models for visualization, films, television, and games.
turbosquid
$10
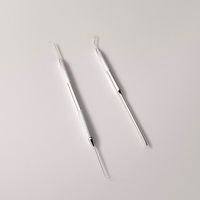
Dental Probe
... available on turbo squid, the world's leading provider of digital 3d models for visualization, films, television, and games.
turbosquid
$9
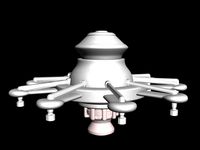
Space probe
... available on turbo squid, the world's leading provider of digital 3d models for visualization, films, television, and games.
turbosquid
free
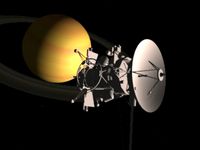
Cassini Probe
... available on turbo squid, the world's leading provider of digital 3d models for visualization, films, television, and games.
A8
turbosquid
$47
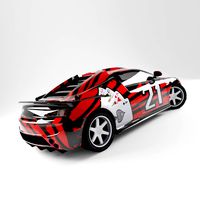
Car A8
...
turbosquid
royalty free 3d model car a8 for download as max on turbosquid: 3d models for games, architecture, videos. (1196060)
turbosquid
$50
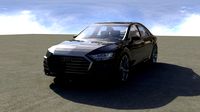
Audi A8
...yalty free 3d model audi a8 for download as 3dm, obj, and fbx on turbosquid: 3d models for games, architecture, videos. (1580187)
turbosquid
$15
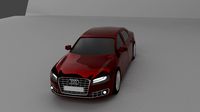
Audi A8
...lty free 3d model audi a8 for download as obj, fbx, and blend on turbosquid: 3d models for games, architecture, videos. (1387519)
turbosquid
$500
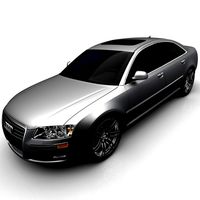
Audi A8
... available on turbo squid, the world's leading provider of digital 3d models for visualization, films, television, and games.
3d_export
$5
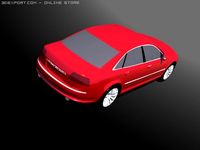
Audi A8 3D Model
...audi a8 3d model
3dexport
audi a8 cars car
audi a8 3d model ma 20351 3dexport
3d_export
$5
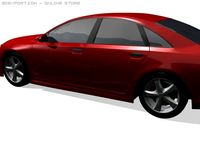
Audi A8 3D Model
...audi a8 3d model
3dexport
3d model of audi a8
audi a8 3d model badyaka 12136 3dexport
3d_ocean
$89
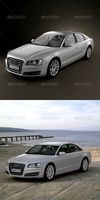
Audi A8 2010
...usiness car car class class f f german german luxury luxury s s s8 s8 sedan sedan vehicle vehicle
new audi a8 2010 detaled model.
turbosquid
$39
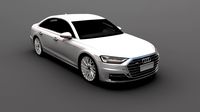
A8 2018
...a8 2018 for download as 3ds, obj, wrl, c4d, fbx, dae, and stl on turbosquid: 3d models for games, architecture, videos. (1345349)
turbosquid
free
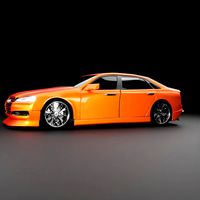
audi a8 l
...rbosquid
royalty free 3d model audi a8 l for download as obj on turbosquid: 3d models for games, architecture, videos. (1663016)
3d_ocean
$45
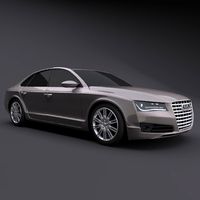
Audi A8 restyled
...our door vehicle was created in blender3d 2.62.realistic renderings were created with yafaray 0.1.2 realistic plugin.rendering...
E3D
turbosquid
$23
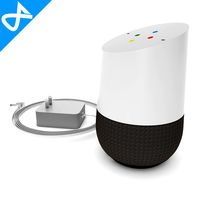
E3D - Google Home
... 3d model e3d - google home for download as max, obj, and c4d on turbosquid: 3d models for games, architecture, videos. (1192509)
cg_studio
free
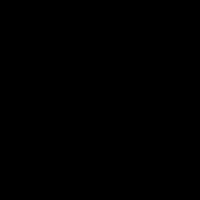
e3d model
...e3d model
cgstudio
- e 3d model, royalty free license available, instant download after purchase.
turbosquid
$2
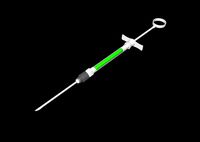
Syringe C4D (E3D Ready)
...lty free 3d model syringe c4d (e3d ready) for download as c4d on turbosquid: 3d models for games, architecture, videos. (1336720)
turbosquid
$12
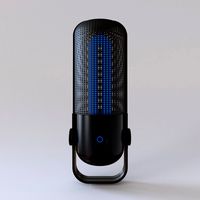
Microphone USB E3D and C4D
...ree 3d model microphone usb e3d & c4d for download as c4d on turbosquid: 3d models for games, architecture, videos. (1568216)
turbosquid
$29
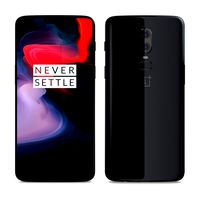
E3D - OnePlus 6 Black
...model e3d - oneplus 6 black for download as max, obj, and c4d on turbosquid: 3d models for games, architecture, videos. (1358534)
turbosquid
$29
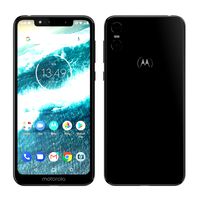
E3D - Motorola One 2018
...del e3d - motorola one 2018 for download as max, obj, and c4d on turbosquid: 3d models for games, architecture, videos. (1358533)
turbosquid
$29
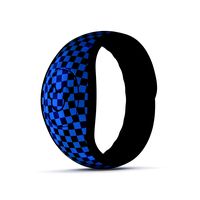
E3D - Disney MagicBands 2
...l e3d - disney magicbands 2 for download as max, obj, and c4d on turbosquid: 3d models for games, architecture, videos. (1355515)
turbosquid
$29

E3D - Samsung Z4 Smartphone
...e3d - samsung z4 smartphone for download as max, obj, and c4d on turbosquid: 3d models for games, architecture, videos. (1182179)
turbosquid
$23
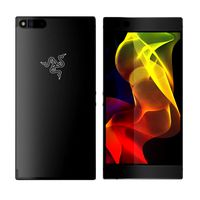
E3D - Razer Phone model
...del e3d - razer phone model for download as max, obj, and c4d on turbosquid: 3d models for games, architecture, videos. (1231207)
turbosquid
$23
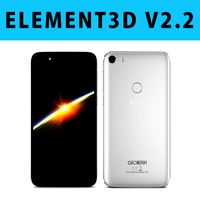
E3D - Alcatel Idol 5
... model e3d - alcatel idol 5 for download as max, obj, and c4d on turbosquid: 3d models for games, architecture, videos. (1212799)
Anet
thingiverse
free
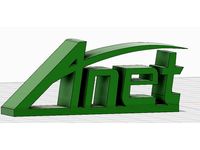
Anet by derbodesign
...anet by derbodesign
thingiverse
logo anet
thingiverse
free
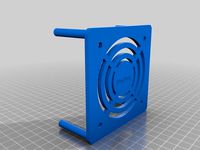
Anet e10 , Anet v1.0 by jonathan_943D
...anet e10 , anet v1.0 by jonathan_943d
thingiverse
soporte de ventilador de 80mm, para controladora anet v1.0
thingiverse
free
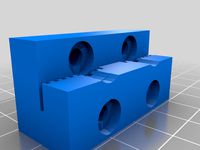
Anet A8 Anet AM8 Y belt holder
...anet a8 anet am8 y belt holder
thingiverse
anet a8 anet am8 y belt holder
thingiverse
free
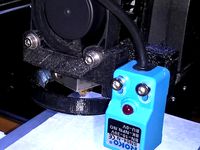
Anet A8 Probe Bracket for anet sensor by chelrix
...anet a8 probe bracket for anet sensor by chelrix
thingiverse
anet a8 probe bracket for anet official sensor and marlin firmware
thingiverse
free
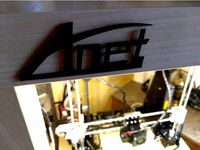
Anet logo by JUST3D_PRNTNG
...anet logo by just3d_prntng
thingiverse
anet logo
thingiverse
free
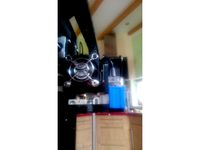
Fan nozzle for Anet A8 with original Anet levelsensor by peteruhlmann
...et levelsensor by peteruhlmann
thingiverse
here is an improved fan nozzle for the anet a8 with original level sensor from anet.
thingiverse
free
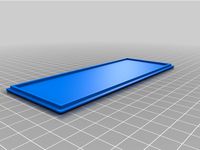
Anet Et4 Box
...anet et4 box
thingiverse
tool box for anet et4
thingiverse
free
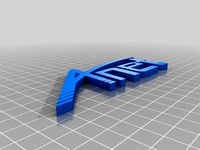
Anet Logo by Superflex_Plastic_Fantastic
...anet logo by superflex_plastic_fantastic
thingiverse
anet logo to incorporate into designs.
thingiverse
free
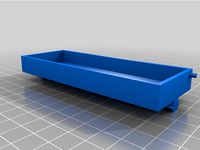
Box for Anet ET4
...box for anet et4
thingiverse
this is a simple box for tool of anet et4
thingiverse
free
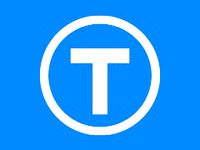
Anet V1.0 Board Kühlung (80mm Lüfter) / Anet A8 by MadCre8
...anet v1.0 board kühlung (80mm lüfter) / anet a8 by madcre8
thingiverse
anet v1.0 board kühlung (80mm lüfter) / anet a8
Carriage
archibase_planet
free
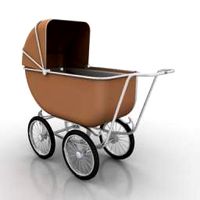
Carriage
...arriage
archibase planet
perambulator baby carriage pram
carriage n250908 - 3d model (*.gsm+*.3ds) for interior 3d visualization.
3d_export
free
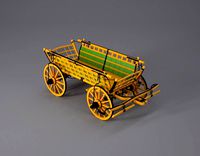
carriage
...carriage
3dexport
old fashion carriage model, more files here:
turbosquid
$140
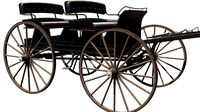
Carriage
...urbosquid
royalty free 3d model carriage for download as max on turbosquid: 3d models for games, architecture, videos. (1482052)
turbosquid
$25
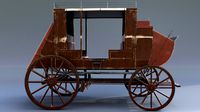
Carriage
...urbosquid
royalty free 3d model carriage for download as max on turbosquid: 3d models for games, architecture, videos. (1285944)
3d_export
free
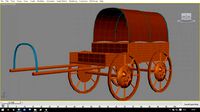
carriage
...carriage
3dexport
game cart
3d_ocean
$15
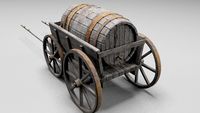
Barrel Carriage
...ieval oak old transport wheels wine wood
this model contains a barrel and a carriage. it is a medieval type of wood oak carriage.
turbosquid
$40
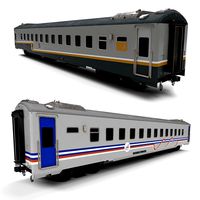
Carriage
...ty free 3d model carriage for download as obj, fbx, and blend on turbosquid: 3d models for games, architecture, videos. (1290094)
turbosquid
free
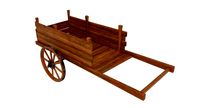
Carriage
...yalty free 3d model carriage for download as ma, obj, and fbx on turbosquid: 3d models for games, architecture, videos. (1239157)
3d_export
$5
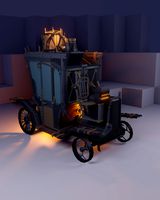
Medieval carriage
...medieval carriage
3dexport
medieval carriage in fairy style
turbosquid
$58
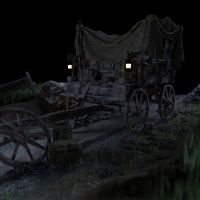
Carriage
...d model carriage with scene for download as max, obj, and fbx on turbosquid: 3d models for games, architecture, videos. (1276262)
Direct
design_connected
free
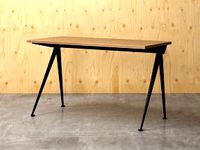
Compas Direction
...compas direction
designconnected
free 3d model of compas direction by vitra designed by prouvé, jean.
design_connected
$18
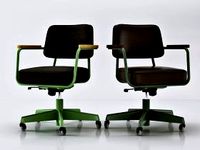
Direction Pivotant
...direction pivotant
designconnected
vitra direction pivotant computer generated 3d model. designed by prouvé, jean.
turbosquid
$6
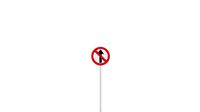
not direct the front
...oyalty free 3d model not direct the front for download as max on turbosquid: 3d models for games, architecture, videos. (1213034)
turbosquid
$10
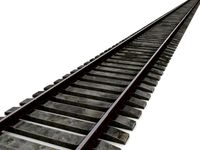
Rails Direct
... available on turbo squid, the world's leading provider of digital 3d models for visualization, films, television, and games.
3d_export
$5
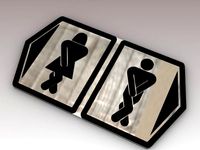
Picto toilet directions
...lude 3d files next to rhino6: x3dv, step, igus, obj and stl. double-sided, flipping changes the gender directions to the toilets.
3ddd
$1
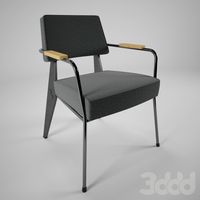
fauteuli direction
...d
chair , vitra , fauteuli
fauteuli vitra chair
design_connected
$18
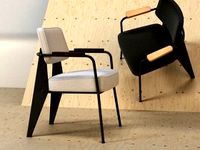
Fauteuil Direction, 1951
...fauteuil direction, 1951
designconnected
vitra fauteuil direction, 1951 computer generated 3d model. designed by prouvé, jean.
3d_export
$5
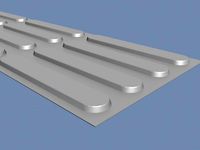
Directional tactile 3D Model
...tactile 3d model
3dexport
directional tactile braille tile flooring interior
directional tactile 3d model renob000 71068 3dexport
turbosquid
$26

Radio direction finder A
...ty free 3d model radio direction finder a for download as fbx on turbosquid: 3d models for games, architecture, videos. (1212490)
turbosquid
$7
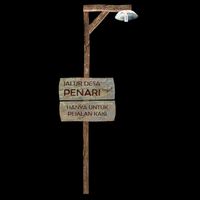
Wooden direction signage
...ty free 3d model wooden direction signage for download as max on turbosquid: 3d models for games, architecture, videos. (1453747)
W
3ddd
$1
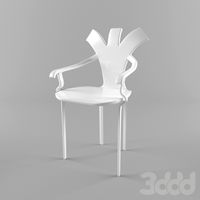
chair W
...chair w
3ddd
chair w
3ddd
$1
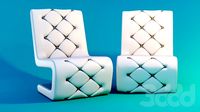
кресло w
...кресло w
3ddd
капитоне
кресло w
3ddd
$1
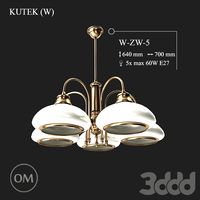
KUTEK (W) W-ZW-5
...kutek (w) w-zw-5
3ddd
kutek
3d модель люстри (w) w-zw-5 фабрики kutek. в архиве: max2012, obj, fbx, mat.(два варианта металла)
3ddd
$1

KUTEK (W) W-ZW-3
...kutek (w) w-zw-3
3ddd
kutek
3d модель люстри (w) w-zw-3 фабрики kutek. в архиве: max2012, obj, fbx, mat. (два варианта металла)
3ddd
$1
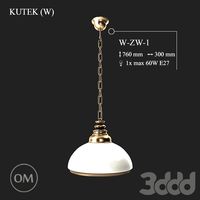
KUTEK (W) W-ZW-1
...kutek (w) w-zw-1
3ddd
kutek
3d модель люстри (w) w-zw-1 фабрики kutek. в архиве: max2012, obj, fbx, mat (два варианта металла).
3ddd
free
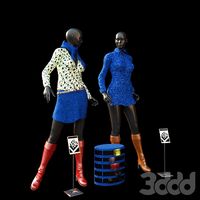
aneken W&W
...aneken w&w
3ddd
2 женских манекена, ценники и фолио. материалы и текстуры прилагаются.
design_connected
$9
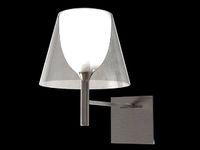
KTribe W
...ktribe w
designconnected
ktribe w computer generated 3d model. designed by starck, philippe.
design_connected
$16
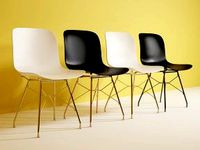
Troy W
...troy w
designconnected
magis troy w computer generated 3d model. designed by wanders, marcel.
turbosquid
$9
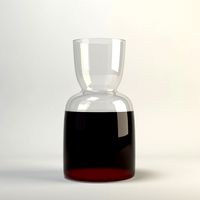
Menu - Benjamin Hubert - W W Carafe
... available on turbo squid, the world's leading provider of digital 3d models for visualization, films, television, and games.
turbosquid
$9
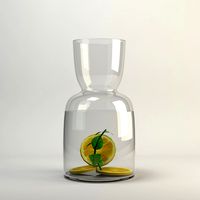
Menu - Benjamin Hubert - W W Carafe
... available on turbo squid, the world's leading provider of digital 3d models for visualization, films, television, and games.