Thingiverse
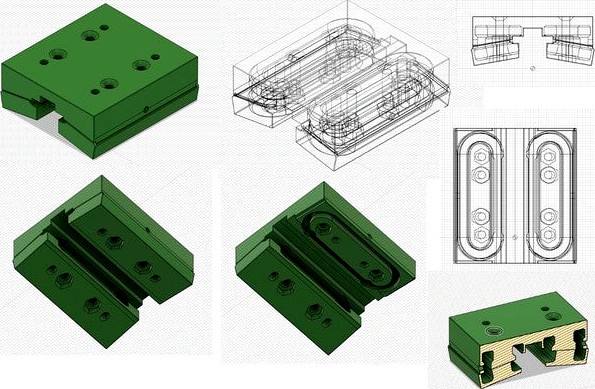
3DP linear bearing (recirculating) and DIY linear rail 4.5mm bb (Final version) by Baltojikale
by Thingiverse
Last crawled date: 3 years, 3 months ago
Attention: aluminium profiles not always up to spec thus model (cad fusion 360) should be eddited (added slimmer outer part model for under spec aluminum beam, in my case bought 15x2 m but actually it was 15x1.8mm)
DP linear bearing and DIY linear rail (4.5mm bb) (final version??)
Introduction
Been searching cheap alternative which can be 3d printable (partially) and made from easily acquirable materials from home depo or similar home improvement shops. Main challenge was to innovate linear rail design which could have mounting holes to flat surface. There are few recirculating linear bearing designs on thingiverse or other depositories. Most of them designed to be used with 3dp rails or V or T aluminum profiles. T or V slot aluminum profiles ware out of question as their not that accessible locally. Thus simple profiles were used to produce linear rail. For linear bearing prototype was made with 3mm steel ball bearings. Updated versions include 6mm airsoft bullet bb's and 4.5mm pneumatic gun bullet bb's. All mentioned bb's are also available and common sizes used for real bearings. One could try to find bbs in local stores which specializes in bearings for machinery, airsoft/gun/hunting equipment shop (pneumatic bullets).
BB
Main difference between real bb from steel bullets bb is the bb precision and price. Bullets precision usually two decimals places while real bb can be 3 and more (for example 6.00mm and real bb 6.0000mm). From price point difference is substantial: 4.5mm pneumatic steel bullet bbs 1500 bb/pack - 7euros ; 4.5000mm real ball bearings 100 bb/pack -3euros (local prices, internet/online prices can be lower but tendency is same). Plastic bb if available are very cheap.
Design
Linear rail
Rail was produced from rectangular 15x2 mm aluminum beam and from 10x10 mm aluminum square tube (10x10+15x2mm). Two pieces were center drilled and riveted to acquire shape which can provide rolling surface for BB’s. Making rail involves printing alignment jig (or jigs). For hole drilling best to use calipers and pointy punch to mark drilling holes.
Linear bearing
Design was improved upon few iterations. Design required to incorporate tensioning mechanics towards linear rail. Thus bearing is made up from 3 printable parts (hardware not accounted). Size is kept as small as possible but also leaving some thick zones for sturdiness. Left opening to manually access bb grooves/tracks. Sometimes some derby are left after printing thus openings allow to clean them with pointy files. "Outer" parts have designed holes for lubrication. Because bb grooves are open, grease(or oil) can reach all 4 tracks in linear bearing. For grease, personally I used petroleum gel (vaseline for machinery, at least that what was written on gel tube).
Contact points
This rail and bearing design incorporates at least 6 points of contact between rail and BB. At contact points were BB meats plastic round shape was changed to square or rounded square to minimize friction as round object cannot run in round groove as linear velocities at different points of spherical bb aren't the same as overall bb movement linear speed.
Printing
Used Pla with 25-35% infill, for dimensional accuracy printed outer walls first and very slowly (~10mm/s) 0.4mm nozzle. Printer slicing profile should be calibrated, at least for inner holes. For my set up I scale up models by 0.5% to compensate for part shrinking. Used 4.5 mm BB thus model has incorporated 4.8 mm diameter BB guide grooves.
Tensioning system
Current model has incorporated 10 degree tapered surface which also acts as tensioning mechanism when two meeting parts are bolted together. Parts during bolting slides one against other thus tensioning force are created at 10 degree angle which allows small (0.5mm) adjustment towards linear rail center. "Inner" parts have oval shaped holes thus M3 screws have space for sideways movement.
Why 4.5mm???
3mm version works the best. Smallest linear carriage most smooth performance. Due to small size sometimes is hard to get good bb groove as tolerances are small thus printer should be calibrated well. 3mm bb dont have any alternative(no airsoft/gun application or at least i dont know any at this moment) , thus only genuine ones can be used. Genuine bb price starts 1~2e per 100bb/pack. One linear bearing takes up about ~120bb.
6mm version is best for bb source because one can use airsoft steel or plastic bullets and genuine bb. Plastic bullets slide most quietly and are very cheap (5000bb/pack -7e). Steel bb either for airsoft or genuine ones are costly. Drawbacks are that printed bearing is quite big, thus longer printing time but its easier to clean up (stringing or similar 3dp artifacts).
Need wider linear rail as aluminum strip should be at least 6mm wider than aluminum square tube, thus first size starts at 15x15+25x2mm
4.5mm very cheap alternatives for genuine bb's with various surface finishes (1500bb/pack -7e). Size vise linear bearing isn't much bigger than 3mm version. can be made to fit 10x10+15x2 mm linear rail. Size vise easy to print and clean up. Many options for bb's.
Aluminium vs anodized aluminum
anodized aluminum should be used with steel bb as steel is much harder than aluminum thus protective coat should prolong work time of rail, as steel bb can grind in to aluminum. for 4.5mm version one can use copper coated lead core or plastic bbs. Copper and lead are quite soft metals, thus aluminum should not wear that much.
3mm versionhttps://www.thingiverse.com/thing:4671314
6mm versionhttps://www.thingiverse.com/thing:4672409
Short demonstrationhttps://youtu.be/ryh3pSujLEY
Further development
Application in cnc project. Currently working on test model of corexy laser cnc. Still testing.
DP linear bearing and DIY linear rail (4.5mm bb) (final version??)
Introduction
Been searching cheap alternative which can be 3d printable (partially) and made from easily acquirable materials from home depo or similar home improvement shops. Main challenge was to innovate linear rail design which could have mounting holes to flat surface. There are few recirculating linear bearing designs on thingiverse or other depositories. Most of them designed to be used with 3dp rails or V or T aluminum profiles. T or V slot aluminum profiles ware out of question as their not that accessible locally. Thus simple profiles were used to produce linear rail. For linear bearing prototype was made with 3mm steel ball bearings. Updated versions include 6mm airsoft bullet bb's and 4.5mm pneumatic gun bullet bb's. All mentioned bb's are also available and common sizes used for real bearings. One could try to find bbs in local stores which specializes in bearings for machinery, airsoft/gun/hunting equipment shop (pneumatic bullets).
BB
Main difference between real bb from steel bullets bb is the bb precision and price. Bullets precision usually two decimals places while real bb can be 3 and more (for example 6.00mm and real bb 6.0000mm). From price point difference is substantial: 4.5mm pneumatic steel bullet bbs 1500 bb/pack - 7euros ; 4.5000mm real ball bearings 100 bb/pack -3euros (local prices, internet/online prices can be lower but tendency is same). Plastic bb if available are very cheap.
Design
Linear rail
Rail was produced from rectangular 15x2 mm aluminum beam and from 10x10 mm aluminum square tube (10x10+15x2mm). Two pieces were center drilled and riveted to acquire shape which can provide rolling surface for BB’s. Making rail involves printing alignment jig (or jigs). For hole drilling best to use calipers and pointy punch to mark drilling holes.
Linear bearing
Design was improved upon few iterations. Design required to incorporate tensioning mechanics towards linear rail. Thus bearing is made up from 3 printable parts (hardware not accounted). Size is kept as small as possible but also leaving some thick zones for sturdiness. Left opening to manually access bb grooves/tracks. Sometimes some derby are left after printing thus openings allow to clean them with pointy files. "Outer" parts have designed holes for lubrication. Because bb grooves are open, grease(or oil) can reach all 4 tracks in linear bearing. For grease, personally I used petroleum gel (vaseline for machinery, at least that what was written on gel tube).
Contact points
This rail and bearing design incorporates at least 6 points of contact between rail and BB. At contact points were BB meats plastic round shape was changed to square or rounded square to minimize friction as round object cannot run in round groove as linear velocities at different points of spherical bb aren't the same as overall bb movement linear speed.
Printing
Used Pla with 25-35% infill, for dimensional accuracy printed outer walls first and very slowly (~10mm/s) 0.4mm nozzle. Printer slicing profile should be calibrated, at least for inner holes. For my set up I scale up models by 0.5% to compensate for part shrinking. Used 4.5 mm BB thus model has incorporated 4.8 mm diameter BB guide grooves.
Tensioning system
Current model has incorporated 10 degree tapered surface which also acts as tensioning mechanism when two meeting parts are bolted together. Parts during bolting slides one against other thus tensioning force are created at 10 degree angle which allows small (0.5mm) adjustment towards linear rail center. "Inner" parts have oval shaped holes thus M3 screws have space for sideways movement.
Why 4.5mm???
3mm version works the best. Smallest linear carriage most smooth performance. Due to small size sometimes is hard to get good bb groove as tolerances are small thus printer should be calibrated well. 3mm bb dont have any alternative(no airsoft/gun application or at least i dont know any at this moment) , thus only genuine ones can be used. Genuine bb price starts 1~2e per 100bb/pack. One linear bearing takes up about ~120bb.
6mm version is best for bb source because one can use airsoft steel or plastic bullets and genuine bb. Plastic bullets slide most quietly and are very cheap (5000bb/pack -7e). Steel bb either for airsoft or genuine ones are costly. Drawbacks are that printed bearing is quite big, thus longer printing time but its easier to clean up (stringing or similar 3dp artifacts).
Need wider linear rail as aluminum strip should be at least 6mm wider than aluminum square tube, thus first size starts at 15x15+25x2mm
4.5mm very cheap alternatives for genuine bb's with various surface finishes (1500bb/pack -7e). Size vise linear bearing isn't much bigger than 3mm version. can be made to fit 10x10+15x2 mm linear rail. Size vise easy to print and clean up. Many options for bb's.
Aluminium vs anodized aluminum
anodized aluminum should be used with steel bb as steel is much harder than aluminum thus protective coat should prolong work time of rail, as steel bb can grind in to aluminum. for 4.5mm version one can use copper coated lead core or plastic bbs. Copper and lead are quite soft metals, thus aluminum should not wear that much.
3mm versionhttps://www.thingiverse.com/thing:4671314
6mm versionhttps://www.thingiverse.com/thing:4672409
Short demonstrationhttps://youtu.be/ryh3pSujLEY
Further development
Application in cnc project. Currently working on test model of corexy laser cnc. Still testing.
Similar models
thingiverse
free
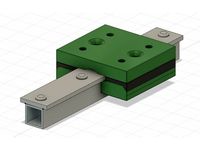
3DP linear bearing (recirculating) and DIY linear rail (old version) by Baltojikale
...made from easily acquirable materials from home depo or similar home improvement shops. main challenge was to innovate linear...
thingiverse
free
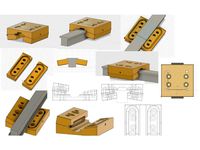
3DP linear bearing (recirculating) and DIY linear rail V2 (old version) by Baltojikale
...s as elephant foot.
current design could be aplicable in 3d printers.
also working on 6 mm bb version. posible cnc aplications.
thingiverse
free
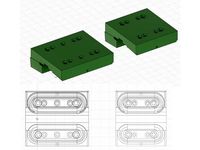
3DP linear bearing (recirculating) and DIY linear rail 6mm bb by Baltojikale
...as reference only. too much wrong operations.
https://www.thingiverse.com/thing:4662854
https://www.thingiverse.com/thing:4671314
thingiverse
free
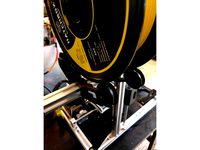
A filament reel holder that uses Airsoft bb's as bearings by btnewman
...ust slide 1 around to accommodate different widths of reels. the bearings are held on the braces using 3mm x 7mm or longer bolts.
thingiverse
free
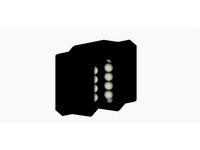
Recirculating linear bearing 20x20 profile by GreyHunter147
...ion. work with 6mm sfere, airsoft bbs can be used for testing.
update
i correct the internal rail, now work better with 6mm balls
thingiverse
free
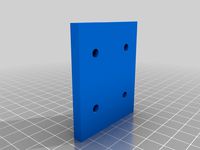
Linear bearing .177 - 4.5mm bb for 1/2 inch emt conduit
...linear bearing .177 - 4.5mm bb for 1/2 inch emt conduit
thingiverse
use 4.5 mm - .177 bbs.
untested
thingiverse
free
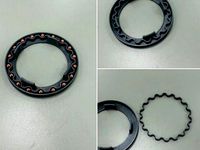
FOR 4.5mm BB by CruiseLee
...for 4.5mm bb by cruiselee
thingiverse
for 4.5mm bb bullet
thingiverse
free
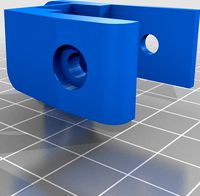
MGN12 Endcap for 2020 Aluminum Profile System by TehseenulHasan
...rse
this is the endcap for mgn12 linear rail bearing (mgn12h). it is designed to mount on 2020 aluminum profile using m4 screws.
thingiverse
free
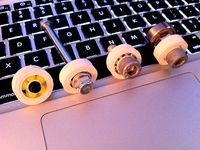
Parametric split-hub printable bearing by whosawhatsis
...ith a 3mm shaft, 4.5mm metal bbs with a 6mm shaftt, 4.5mm metal bbs with an 8mm shaft, and 3mm spherical beads with an 8mm shaft.
thingiverse
free
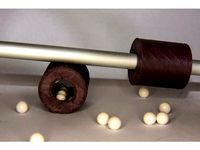
Linear bearing with 6mm airsoft bbs for 8mm rod by SirioB
...earing, it' exactly 23.32 mm.
i'm not anglophone so if you notice some errors in the text please leave a comment, thanks!
Baltojikale
thingiverse
free
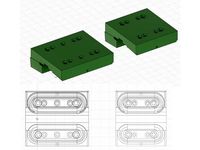
3DP linear bearing (recirculating) and DIY linear rail 6mm bb by Baltojikale
...as reference only. too much wrong operations.
https://www.thingiverse.com/thing:4662854
https://www.thingiverse.com/thing:4671314
thingiverse
free

Neopixel progress bar CURA plugin for klipper by Baltojikale
...ted in voron standarts: 4 perimeters, 5 tops and bottoms and 40 infill. ( for thin parts likethese it unintentionaly becomes 100%
thingiverse
free
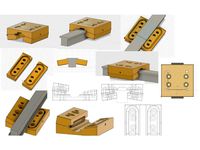
3DP linear bearing (recirculating) and DIY linear rail V2 (old version) by Baltojikale
...s as elephant foot.
current design could be aplicable in 3d printers.
also working on 6 mm bb version. posible cnc aplications.
thingiverse
free
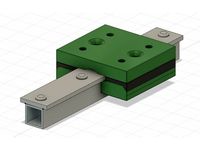
3DP linear bearing (recirculating) and DIY linear rail (old version) by Baltojikale
...ounting mechanism thus one cannot over tighten mounting screw as they can possible deform part and interfere with bb circulation.
thingiverse
free
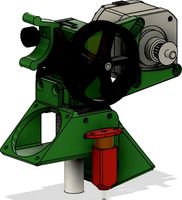
SILVIUS extruder: Belted 1:5 BMG dual gear by Baltojikale
...iangle labs volcano hot end clone kit was not used as it was louder. thus designed that “monstrosity” which is present in photos.
Recirculating
3d_export
$5
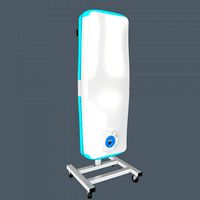
recirculator
...recirculator
3dexport
medical recirculator. under subdi.
turbosquid
$10
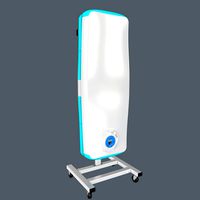
recirculator
...odel recirculator for download as c4d, c4d, fbx, obj, and stl on turbosquid: 3d models for games, architecture, videos. (1681233)
cg_studio
$99

EGR engine3d model
...ulation gasturbine turbine
.obj .fbx .max - egr engine 3d model, royalty free license available, instant download after purchase.
thingiverse
free
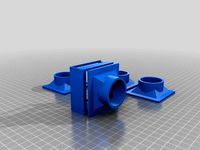
Recirculating air filter by Manxian
...inatly safe its best not to take chances with you or your families health this is designed to help maintain heat in the enclosure
thingiverse
free
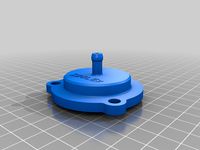
Opel Vauxhall internal recirculation Valve BOV 2.0 Turbo
...nal recirculation valve bov 2.0 turbo
thingiverse
opel/vauxhall 2.0 turbo internal recirculation valve (bov) for
z20lex engines.
thingiverse
free
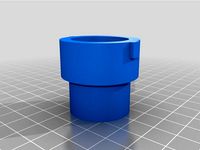
HKS SSQV Recirculating Adapter by notarikon
...ted, and currently resides in my vehicle. underbonnet temps have shown no issue (printed in pla), with no deformation or warping.
thingiverse
free
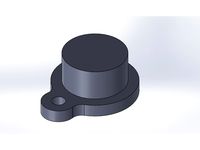
Saab T7 recirculation block off by hardov
...ecirculation path if you use td04 or gt17 turbo and cobra pipe. it is necessary if you want to install blow off valve to the car.
thingiverse
free
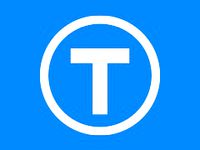
HKS SSQV Recirculation fitting with Whistle/Chirp by Skuce
...hks ssqv recirculation fitting with whistle/chirp by skuce
thingiverse
sketchup 2017
thingiverse
free
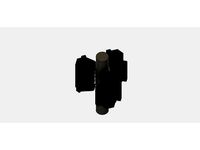
Recirculating linear bearing (modular) by GreyHunter147
...nd screw them together with simple m3 screws. it's small and cheap to print. next, i also add the 20x20 square frame version.
thingiverse
free
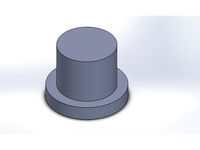
Saab T5 recirculation block off by hardov
...necessary if you want to install blow off valve to the car. works good with pla. i have used it a year on my car and no problems.
3Dp
turbosquid
$15
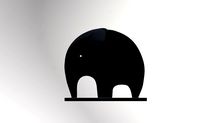
ELEPHANT / / 3DP Animation Studio
... available on turbo squid, the world's leading provider of digital 3d models for visualization, films, television, and games.
turbosquid
$15
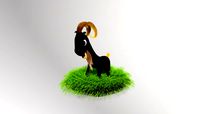
GOAT / / 3DP Animation Studio
... available on turbo squid, the world's leading provider of digital 3d models for visualization, films, television, and games.
turbosquid
$100
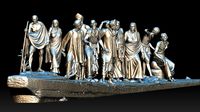
Gandhi Salt March 3DP
...ds, dxf, lwo, obj, wrl, x, c4d, fbx, 3dm, blend, lxo, and dae on turbosquid: 3d models for games, architecture, videos. (1447208)
3d_export
free
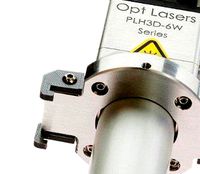
z-morph 3dp rear hook opt lasers
...also accessible on:<br>to find out more about the functionality of laser 3d printers, take a look at the following webpage:
3d_export
free
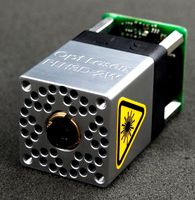
cnc 3dp laser engraving head opt lasers
...n also be found for free at:<br>if you want to take a look at the specifications of this laser head, please visit the link:
3d_export
free
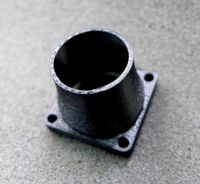
cnc 3dp laser nozzle for 2w laser opt lasers
...logy that gave birth to cutting and engraving laser heads this laser nozzle was designed for, read the article in the link below:
3d_export
free

z-morph 3dp front hook opt lasers
...k is also available from:<br>to find out more about the 3d laser printer engraver technology, you can visit the link below:
3d_export
free
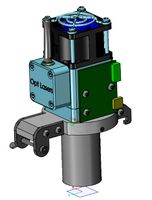
z-morph 3dp 6w engraving laser head
...e via:<br>if you want to learn the specifications of the 6w opt lasers cutting and engraving laser head, visit the website:
3d_export
$5

katar
...occlusion, curvature, world space normals, thickness, position.<br>fbx, obj, blend, 3dp 3ds, glb, ply, stl, usdc, x3d, mtl, dae,...
thingiverse
free
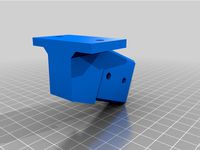
Robotics Feed 3DP
...ector-2
side wall extrusion 3dp connector-2
bevel box -1
l dt connector 1-2
l dt connector 2-2
arc and back plate 3dp connector-1
Bb
design_connected
$13
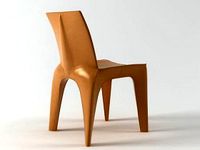
BB
...bb
designconnected
poliform bb computer generated 3d model. designed by borghi, matteo.
turbosquid
$5

bbs
... available on turbo squid, the world's leading provider of digital 3d models for visualization, films, television, and games.
turbosquid
free

bb
... available on turbo squid, the world's leading provider of digital 3d models for visualization, films, television, and games.
3ddd
$1
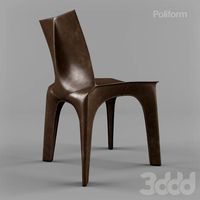
Poliform Bb chair
...poliform bb chair
3ddd
poliform , bb
poliform bb chair
3ddd
$1
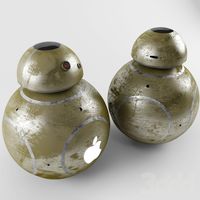
bb-8 apple
...bb-8 apple
3ddd
apple
bb-8 apple
turbosquid
$49
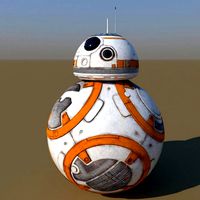
BB ROBOT
...urbosquid
royalty free 3d model bb robot for download as max on turbosquid: 3d models for games, architecture, videos. (1556522)
turbosquid
$11
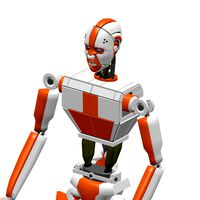
ROBOT BB
...bosquid
royalty free 3d model robot bb for download as blend on turbosquid: 3d models for games, architecture, videos. (1336640)
turbosquid
$4
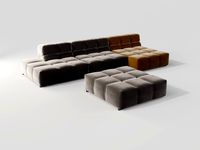
sofa bb
...turbosquid
royalty free 3d model sofa bb for download as obj on turbosquid: 3d models for games, architecture, videos. (1658053)
3ddd
$1
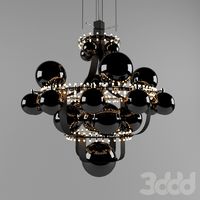
Quasar Royal BB
... , quasar
светильник royal bb
бренд: quasar
страна:голландия
дизайнер: van vliet edward
3d_export
free
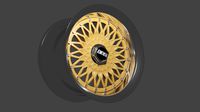
BBS disc
...bbs disc
3dexport
Diy
3d_export
free
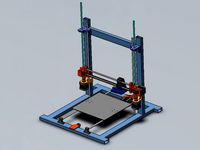
DIY 3D Printer
...diy 3d printer
3dexport
diy 3d printer model
turbosquid
$10
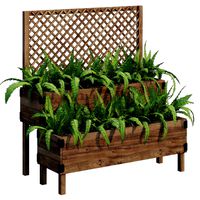
Diy tiered
...l diy tiered for download as max, max, max, max, fbx, and obj on turbosquid: 3d models for games, architecture, videos. (1603709)
turbosquid
$3
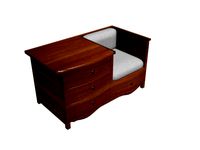
Diy Desk to Bench
...odel diy desk to bench for download as 3ds, max, obj, and fbx on turbosquid: 3d models for games, architecture, videos. (1506589)
turbosquid
$2
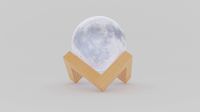
DIY Moon Light
...model diy moon light for download as obj, fbx, blend, and dae on turbosquid: 3d models for games, architecture, videos. (1501170)
3d_export
$8
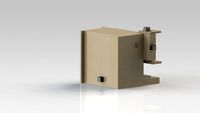
DIY CNC Router 3D Model
...diy cnc router 3d model
3dexport
cnc; router; diy; homemade
diy cnc router 3d model maikeru86 58463 3dexport
turbosquid
$5
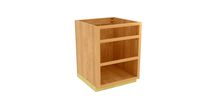
Diy Kitchen Cabinets
...itchen cabinets for download as 3ds, obj, fbx, blend, and dae on turbosquid: 3d models for games, architecture, videos. (1197373)
3d_export
free
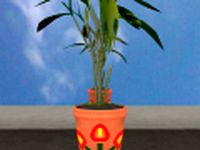
Download free Diying Plant 3D Model
...download free diying plant 3d model
3dexport
diying plant blender
diying plant 3d model visitorsama 98607 3dexport
3ddd
$1
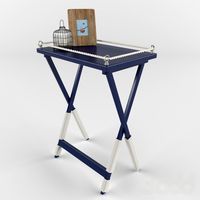
DIY coffee table + decor
... рамка для фото
кофейный столик diy 400х350х600(h) мм. моделился по фото. внимание: материалы - corona.
turbosquid
$3

Diy Wire Lamp Shade
...free 3d model diy wire lamp shade for download as 3ds and fbx on turbosquid: 3d models for games, architecture, videos. (1347605)
cg_studio
$12
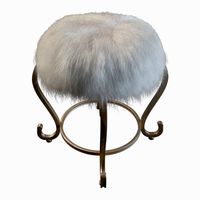
DIY MONGOLIAN LAMB STOOLS3d model
... hair soft pile white
.max - diy mongolian lamb stools 3d model, royalty free license available, instant download after purchase.
Linear
3ddd
$1
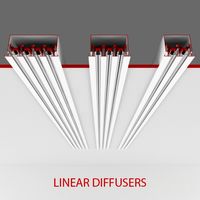
Linear Diffusers
...linear diffusers
3ddd
диффузор
set of linear diffusers for ceiling.
design_connected
$27
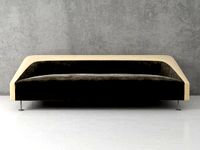
Linear Sofa
...linear sofa
designconnected
scp linear sofa computer generated 3d model.
design_connected
$18
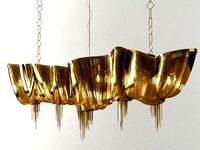
Atlantis linear
...atlantis linear
designconnected
terzani atlantis linear pendant lights computer generated 3d model. designed by barlas baylar.
3d_export
$5
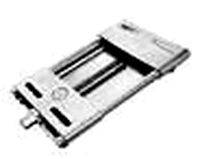
light linear unit
...light linear unit
3dexport
light linear unit
turbosquid
$5
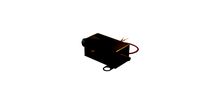
Linear Actuator
...
royalty free 3d model linear actuator for download as blend on turbosquid: 3d models for games, architecture, videos. (1589061)
turbosquid
$29
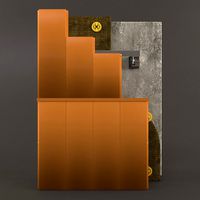
Linear panel
...oyalty free 3d model linear panel for download as max and obj on turbosquid: 3d models for games, architecture, videos. (1391254)
turbosquid
$12
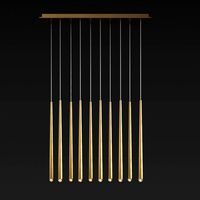
Linear Chandelier
...y free 3d model linear chandelier for download as max and obj on turbosquid: 3d models for games, architecture, videos. (1574289)
turbosquid
$10
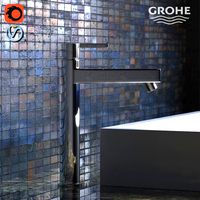
Grohe Lineare
... available on turbo squid, the world's leading provider of digital 3d models for visualization, films, television, and games.
turbosquid
$10
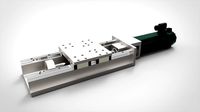
Linear Axis
... available on turbo squid, the world's leading provider of digital 3d models for visualization, films, television, and games.
3d_export
$5
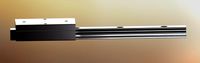
Linear Unit 3D Model
...linear unit 3d model
3dexport
linear unit force torque velocity
linear unit 3d model fau 71218 3dexport
5Mm
3d_export
$25
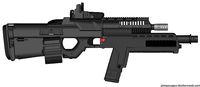
5mm Explosive Flechette 3D Model
...xplosive flechette 3d model
3dexport
assault rifle grenade launchers
5mm explosive flechette 3d model awnonbhowmik 74565 3dexport
turbosquid
$15
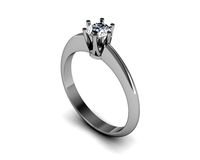
engagement simple ring with diamond (5mm)
...engagement simple ring with diamond (5mm) for download as 3dm on turbosquid: 3d models for games, architecture, videos. (1157278)
turbosquid
$1
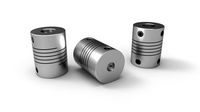
Flexible shaft coupling 5mm x 8mm
... available on turbo squid, the world's leading provider of digital 3d models for visualization, films, television, and games.
3d_export
$7
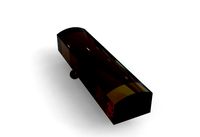
Tiny bracelet clasp lock 20mm X 5mm
... your bracelet parts to the clasp, also there is the original file in the files so you can change it on your own simply. enjoy it
3d_export
$5
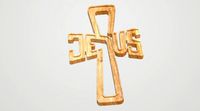
cross with text jesus
...the text jesus is in an contur offset with 5mm ...
3d_export
$5
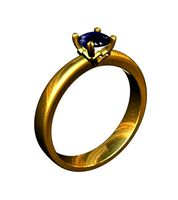
ring
...ring 3dexport lovely ring, adopt for print, one stown 5mm material : white / yellow gold/ silver. stl,...
3d_export
$11
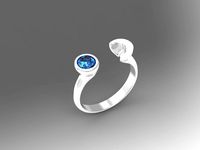
crescent ring
...ring size is 17mm.<br>ring rail size is 53.4<br>stone size 5mm ...
3d_export
$5
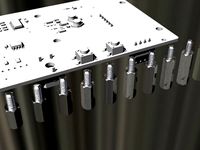
Hex Spacers M3 Male-Female
...male-female 3dexport hex spacers m3 male-female with length from 5mm to 60mm for printed circuit boards. step...
3ddd
$1

LOOP RACK
...вешалка the clothes rack’s elegant frame is made of 5mmthick steel. it creates simple shapes, that vary depending on...
3d_export
free

solar rechargeable single led flashing light
...ties onto a pole etc, i used a single 5mm red/blue alternating flasher that pushes snugly into the 5mm...
Rail
3d_ocean
$5
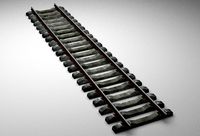
rails
...rails
3docean
old rails rails sleepers
old rails
archibase_planet
free
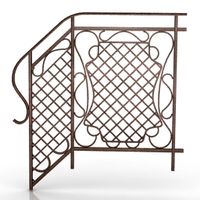
Rail
...chibase planet
rail railing handrail guard-rail
rail forged fence n310814 - 3d model (*.gsm+*.3ds) for exterior 3d visualization.
archibase_planet
free
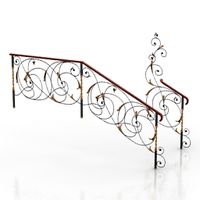
Rail
...rail
archibase planet
handrail railing guard-rail
rail n220914 - 3d model (*.gsm+*.3ds) for interior 3d visualization.
archibase_planet
free
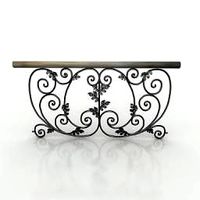
Rail
...rail
archibase planet
railing hand-rail banisters
rail n130309 - 3d model (*.gsm+*.3ds) for interior 3d visualization.
archibase_planet
free
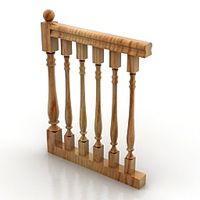
Rail
...rail
archibase planet
railing hand-rail banisters
rail n270510 - 3d model (*.gsm+*.3ds) for interior 3d visualization.
archibase_planet
free
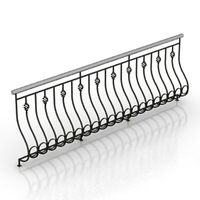
Railing
...
archibase planet
railing handrail fence guard-rail
railing n140314 - 3d model (*.gsm+*.3ds+*.max) for exterior 3d visualization.
archibase_planet
free

Railing
...railing
archibase planet
railing
railing- 3d model (*.gsm+*.3ds) for interior 3d visualization.
archibase_planet
free
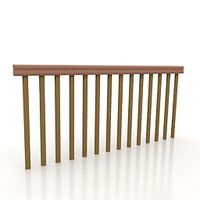
Railing
...railing
archibase planet
railing enclosure barrier
light railing - 3d model for interior 3d visualization.
archibase_planet
free
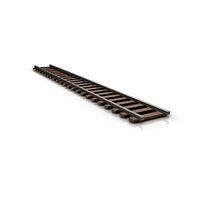
Rail
...rail
archibase planet
metal railing
rail n280608 - 3d model (*.gsm+*.3ds) for interior 3d visualization.
archibase_planet
free
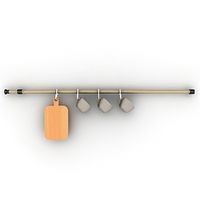
Railing
...railing
archibase planet
railing kitchen ware
railing 1 - 3d model (*.gsm+*.3ds) for interior 3d visualization.
Final
3ddd
$1
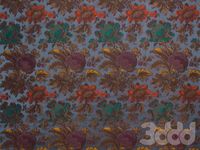
Ardecora-Finale
...ardecora-finale
3ddd
ardecora
ткань итальянского производителя ardecora, артикул finale. в архиве 7 цветов. ткань портьерная.
turbosquid
$3
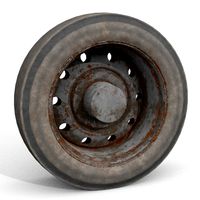
Wheel Final
...osquid
royalty free 3d model wheel final for download as fbx on turbosquid: 3d models for games, architecture, videos. (1364402)
turbosquid
free
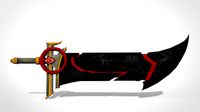
Final Sword
...osquid
royalty free 3d model final sword for download as max on turbosquid: 3d models for games, architecture, videos. (1428573)
turbosquid
$16
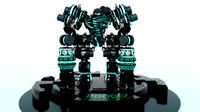
Yeti final
...lty free 3d model yeti final for download as ma, obj, and fbx on turbosquid: 3d models for games, architecture, videos. (1374065)
turbosquid
$180
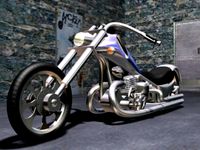
moto final
... available on turbo squid, the world's leading provider of digital 3d models for visualization, films, television, and games.
turbosquid
$80
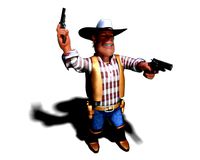
final cowboy.max
... available on turbo squid, the world's leading provider of digital 3d models for visualization, films, television, and games.
turbosquid
$36
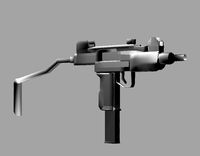
Final UZI
... available on turbo squid, the world's leading provider of digital 3d models for visualization, films, television, and games.
turbosquid
$25
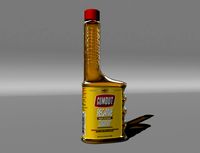
Gumout Final
... available on turbo squid, the world's leading provider of digital 3d models for visualization, films, television, and games.
turbosquid
$15
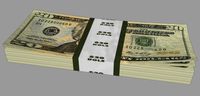
money finals
... available on turbo squid, the world's leading provider of digital 3d models for visualization, films, television, and games.
turbosquid
$15
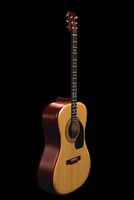
guitar final
... available on turbo squid, the world's leading provider of digital 3d models for visualization, films, television, and games.
Bearing
3d_export
$6
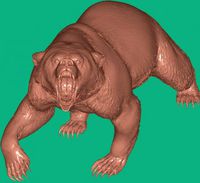
Bear
...bear
3dexport
bear
3d_export
$5
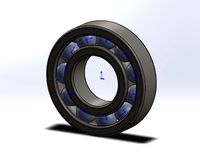
bearing
...bearing
3dexport
bearing
3d_export
$12
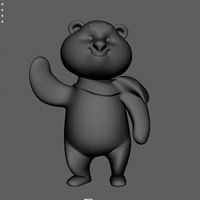
bear
...bear
3dexport
bear for 3d printing toy
3d_ocean
$9
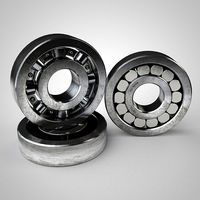
Bearing
...ne ball ballbea bearing bearings engine hard industrial machine mechanic metal part piece plastic ring screw sphere steel
bearing
archibase_planet
free

Bear
...bear
archibase planet
statuette bear picturesque element
bear - 3d model (*.gsm+*.3ds) for interior 3d visualization.
3d_export
$5
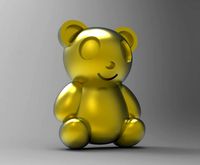
bear
...bear
3dexport
bear have a stl.,3dm files
archibase_planet
free
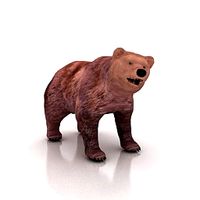
Bear
...bear
archibase planet
bear animals omnivorous animal
bear angry n250907- 3d model (*.gsm+*.3ds) for interior 3d visualization.
archibase_planet
free
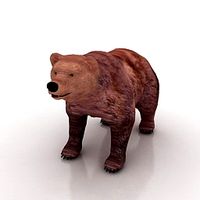
Bear
...bear
archibase planet
bear animals omnivorous animal
bear easy n250907 - 3d model (*.gsm+*.3ds) for interior 3d visualization.
3ddd
$1

Teddy bear
...teddy bear
3ddd
teddy bear , медведь
teddy bear :)
3d_ocean
$12

Bear
... formats. created with 3d max 9.0. this file is very useful for learning & rigging. it can be used for any professional work.
4
turbosquid
$9
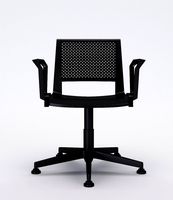
Office Chair 4-4
... available on turbo squid, the world's leading provider of digital 3d models for visualization, films, television, and games.
3d_export
$5
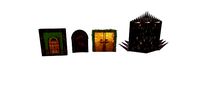
doors- 4
...doors- 4
3dexport
doors 4
3d_export
$5
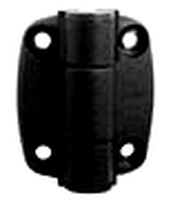
hinge 4
...hinge 4
3dexport
hinge 4
3ddd
$1
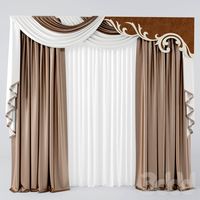
Штора №4
...штора №4
3ddd
штора №4
3d_export
free
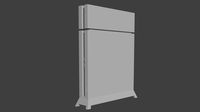
playstation 4
...playstation 4
3dexport
playstation 4
turbosquid
$1
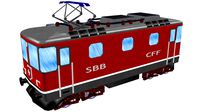
re 4-4 electric locomotive
... free 3d model re 4 4 electric locomotive for download as obj on turbosquid: 3d models for games, architecture, videos. (1707845)
3ddd
$1
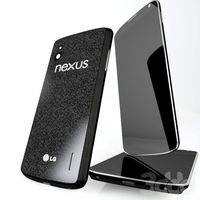
nexus 4
...nexus 4
3ddd
lg , телефон
nexus 4
3ddd
$1
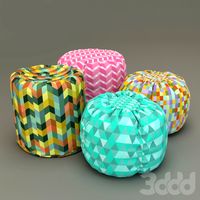
4 Poufs
...4 poufs
3ddd
пуф
4 soft poufs
turbosquid
$12
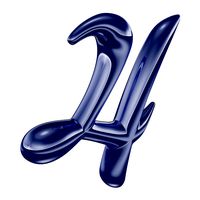
Calligraphic Digit 4 Number 4
...hic digit 4 number 4 for download as max, obj, fbx, and blend on turbosquid: 3d models for games, architecture, videos. (1389332)
3ddd
$1
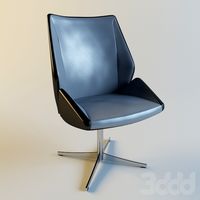
Dauphin 4+
...dauphin 4+
3ddd
кресло
dauphin 4+ конференц кресло
Version
3ddd
$1
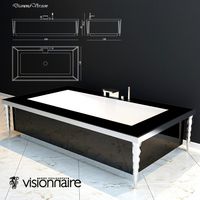
Diamond version
...nd , version , ванна
visionnaire - diamond bath
turbosquid
$50
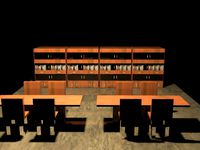
LibraryMini Version
...free 3d model librarymini version for download as max and jpg on turbosquid: 3d models for games, architecture, videos. (1617724)
design_connected
$34
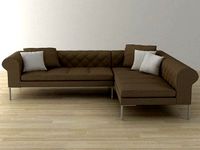
Barocco Version 01
...barocco version 01
designconnected
zanotta barocco version 01 computer generated 3d model. designed by progetti, emaf.
design_connected
$27
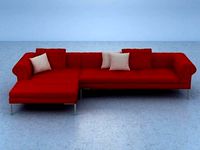
Barocco Version 02
...barocco version 02
designconnected
zanotta barocco version 02 computer generated 3d model. designed by progetti, emaf.
turbosquid
free
![Door [2 versions]](/t/13243146.jpg)
Door [2 versions]
...rbosquid
free 3d model door [2 versions] for download as fbx on turbosquid: 3d models for games, architecture, videos. (1223985)
turbosquid
$2
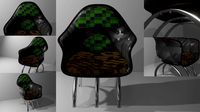
seat version 0.1
...
royalty free 3d model seat version 0.1 for download as blend on turbosquid: 3d models for games, architecture, videos. (1432653)
turbosquid
$12
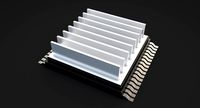
Chip Version 03
...lty free 3d model chip version 03 for download as c4d and fbx on turbosquid: 3d models for games, architecture, videos. (1241145)
3d_export
$10

magnolia grandiflora mature version
...magnolia grandiflora mature version
3dexport
magnolia grandiflora mature version
3d_export
$8
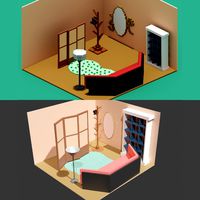
room assets and voxel version
...room assets and voxel version
3dexport
room assets and voxel version
turbosquid
$35
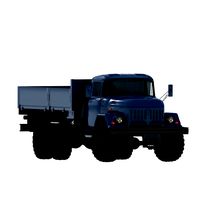
Zil Civilian version
... model zil civilian version for download as cgf, fbx, and obj on turbosquid: 3d models for games, architecture, videos. (1639420)