GrabCAD

Wells CUBESAT
by GrabCAD
Last crawled date: 1 year, 12 months ago
-Summary-
The Wells CubeSat consists of a 1-piece, ribbed isogrid, 3D printable structure that is capable of withstanding the environments associated with spaceflight (random vibration, thermal, etc.). The design meets the technical requirements given in the “CubeSat Design Specifications” and uses current materials that are available for additive manufacturing.
The Wells CubeSat was specifically designed to:
1. Reduce the overall part count by designing a 1-piece unibody structure, allowing for a more simplified producibility using materials that are commercially available, reducing overall cost.
2. Reduce the weight of the structure while maintaining enough strength to survive the environmental requirements.
3. Create a structure that would reduce the CubeSat payload environment by reducing the loads generated by the vehicle and qualification random vibration environments.
-Material & Additive Manufacturing Technique-
This design was intended to utilize printed Ultem 2300 using the Fused Deposition Modeling additive manufacturing technique. Ultem 2300 is an extruded 30% glass reinforced polyetherimide. The glass reinforcement yields a product with an exceptional strength-to-weight ratio while at elevated temperatures with long-term heat resistance. Ultem can also be further reinforced with conductive fibers, or plated for EMI resistance. Ultem meets ASTME595 outgassing requirements, UL94 flammability requirements as well as zero halogen outgassing requirements.
-Design-
To maintain a 1-piece unibody design, an access door was created using a 3D printed hinge. This hinged access door allows full access to the electronics to simplify the PCB mounting installation. After the electronics are mounted, the hinged access door is secured by snap-fit connections as well as two (2) 4-40 flathead machine screws. This design also implements a ribbed-stiffened isogrid structure to maintain a lightweight structure while possessing a strength-to-weight ratio to meet the launch vehicle payload environmental requirements. Isogrid structures are generally used for space applications but are commonly machined out of a single plate of material. By 3D printing the isogrid structure, the majority of the stiffness and strength is maintained while reducing material cost and weight. Considerations were made during the design phase so that the structure can be built without support material, reducing cost, time and post processing.
Design Specifications
Ultem 2300 Density = 1.51 g/cm^2
Build Volume = 102.79 cm^3
Structure Mass = 155 grams
-Random Vibration Reduction-
A major benefit of using composite thermoplastics is reduced vibration excitation through damping. Polymer plastics are less subject to harmonic resonance than metallic structures, reducing the overall load experienced by the CubeSat payload when subjected to vehicle and component qualification random vibration environments, reducing overall design and testing costs. A preliminary quasi-static strength assessment using the predicted 3-sigma acceleration environment generated from the qualification random vibration environment (50 g’s peak) shows positive margin, providing design feasibility.
The Wells CubeSat consists of a 1-piece, ribbed isogrid, 3D printable structure that is capable of withstanding the environments associated with spaceflight (random vibration, thermal, etc.). The design meets the technical requirements given in the “CubeSat Design Specifications” and uses current materials that are available for additive manufacturing.
The Wells CubeSat was specifically designed to:
1. Reduce the overall part count by designing a 1-piece unibody structure, allowing for a more simplified producibility using materials that are commercially available, reducing overall cost.
2. Reduce the weight of the structure while maintaining enough strength to survive the environmental requirements.
3. Create a structure that would reduce the CubeSat payload environment by reducing the loads generated by the vehicle and qualification random vibration environments.
-Material & Additive Manufacturing Technique-
This design was intended to utilize printed Ultem 2300 using the Fused Deposition Modeling additive manufacturing technique. Ultem 2300 is an extruded 30% glass reinforced polyetherimide. The glass reinforcement yields a product with an exceptional strength-to-weight ratio while at elevated temperatures with long-term heat resistance. Ultem can also be further reinforced with conductive fibers, or plated for EMI resistance. Ultem meets ASTME595 outgassing requirements, UL94 flammability requirements as well as zero halogen outgassing requirements.
-Design-
To maintain a 1-piece unibody design, an access door was created using a 3D printed hinge. This hinged access door allows full access to the electronics to simplify the PCB mounting installation. After the electronics are mounted, the hinged access door is secured by snap-fit connections as well as two (2) 4-40 flathead machine screws. This design also implements a ribbed-stiffened isogrid structure to maintain a lightweight structure while possessing a strength-to-weight ratio to meet the launch vehicle payload environmental requirements. Isogrid structures are generally used for space applications but are commonly machined out of a single plate of material. By 3D printing the isogrid structure, the majority of the stiffness and strength is maintained while reducing material cost and weight. Considerations were made during the design phase so that the structure can be built without support material, reducing cost, time and post processing.
Design Specifications
Ultem 2300 Density = 1.51 g/cm^2
Build Volume = 102.79 cm^3
Structure Mass = 155 grams
-Random Vibration Reduction-
A major benefit of using composite thermoplastics is reduced vibration excitation through damping. Polymer plastics are less subject to harmonic resonance than metallic structures, reducing the overall load experienced by the CubeSat payload when subjected to vehicle and component qualification random vibration environments, reducing overall design and testing costs. A preliminary quasi-static strength assessment using the predicted 3-sigma acceleration environment generated from the qualification random vibration environment (50 g’s peak) shows positive margin, providing design feasibility.
Similar models
grabcad
free

Simplified CubeSat Frame Design
... of the cubesat. for a more detailed description of the design please see the pdf file located within the project.
thanks,
-jeff
grabcad
free

CubeSat AMI
...nufacture parts
on demand manufacturing
saving mass from structure to have more payload
better resistance to load and vibrations.
grabcad
free

Adaptable CubeSat Structure for Additive Manufacturing
...enceshow/syd-uni--team-prepares-for-blast-off-in-utah/6507108
missouri s&t’s hper design team: http://aavg.mst.edu/hper-team/
grabcad
free

Unibody CubeSat
...e as a structural support/central-axis for the cubesat with the holes serving as the means for the payload to look down at earth.
thingiverse
free
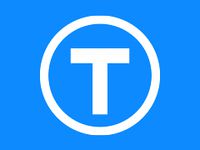
Wall Mount Spool Holder by Maverick_3D
...
remix that removes some of the mass and reduces the time and material required to print while maintaining structural integrity.
grabcad
free

GrabCAD Airplane Bearing Bracket Challenge
... airplane bearing bracket for strength and weight, while maintaining the design to fit within the required installation envelope.
grabcad
free

Structural hook
...ing some strength. overall i think the mass only being 26.66g it holds pretty well up to 58lb with a strength coefficient of 2.75
grabcad
free

Lattice Structure in Part
...t while keeping the part's mechanical properties. this technology can be used by sla material and technology for 3d printing.
grabcad
free

SastoSat CanSat
...sastosat cansat
grabcad
picosatellite cubesat formfactor of 50mm x 50mm (0.5u)
unibody structure with top to hold parachute
grabcad
free

1U 2 Piece CubeSat with Built in Fasteners
...tom boards or components if he/she decides.
note: solar panels and flight computer board download links are in the word document.
Cubesat
thingiverse
free

CubeSat
...cubesat
thingiverse
cubesat structure w/ space for placing raspberry pi camera.
10x10x10cm
m3 screws.
thingiverse
free

CubeSat by 5665
...cubesat by 5665
thingiverse
cube sat
thingiverse
free
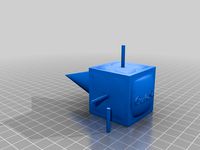
CubeSat by Novitas3d
... astronomy. i'm new in designing, so i hope that when i'll be better i'll publish a new version. print with supports.
thingiverse
free

Aerostat cubesat by michaelchen0220
...sat by michaelchen0220
thingiverse
modular aerostat instrument box. more parts coming up. general framework reference coming up.
thingiverse
free
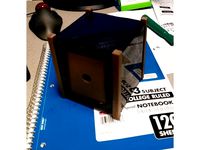
1U CubeSat by TJEmsley
...terior of the satellite.
the brown panel in the cutaway side was a scrap from a previous design and not included in the stl file.
thingiverse
free

Universal 2U Cubesat by Juliano85
...d inserts for the raspberry pi cam v2 module.
please refer to the instructions below on assembly, and selection of configuration.
thingiverse
free
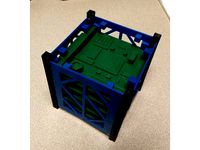
1U Cubesat model v3 by TJEmsley
...;ll need to print 5 or 6 circuit cards to fill the cube. you can use one of the circuit cards for the bottom instead of a cover.
thingiverse
free
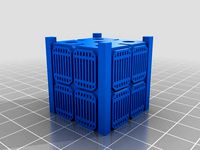
SPEX Mini Cubesat Keychain by wkomm1
... dimensions, it is entirely made from scratch and my imagination.
here is a video of it in action: https://youtu.be/k6n3dkmdlpe
thingiverse
free
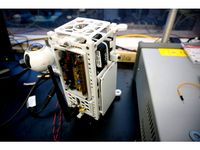
CubeSat HAB STRATO - MkV by rricup
...ter, magnetometer, compass, gps, and a 360 degree samsung camera. the flight footage is found here: https://youtu.be/-ry8s5ulqqc.
thingiverse
free

ArduSat - The Arduino CubeSat Satellite (full scale model) by MAKERFAM
...n-space?ref=live
https://www.facebook.com/pages/nanosatisfi/307866409295499
http://www.youtube.com/user/nanosatisfi?feature=watch
Wells
3ddd
$1

Well
...well
3ddd
well
кресло well
3ddd
$1

Well
...well
3ddd
well
диван двухместный well
3ddd
$1
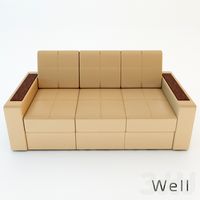
Well
...well
3ddd
well
диван трехместный well
3d_ocean
$5
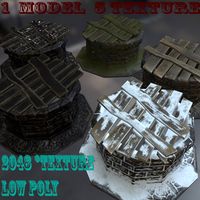
Well
...ell medi evil well old well stone well well
well 2048*2048 texture 1 model 5 texture pack obj and fbx format low poly 296 polygon
3d_export
$5

well
...well
3dexport
well low poly. blender
3d_export
$5

well
...well
3dexport
well, exterior, environment, environment, water
3d_export
$5
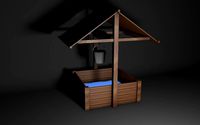
well
...well
3dexport
3d model of a wooden well, all textures are present.
3d_export
$5

Well
...well
3dexport
a wonderful well that can decorate your room or game
3d_export
free
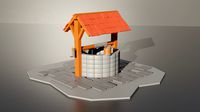
Well
...well
3dexport
low poly model of the well. the original file was created in blender
3d_export
free
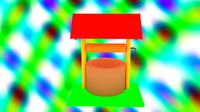
well
...well
3dexport
well x-97.1 y-95.6 mm z-110