GrabCAD
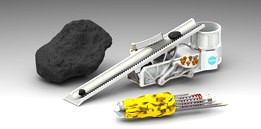
VSS - Vibration sampling system
by GrabCAD
Last crawled date: 1 year, 11 months ago
NASA Lunar Sampling System Design Challenge
VSS- Vibration sampling system
This system is designed to handle sample collection both from the surface and under the surface.
System contains a minimum number of moving parts for a minimum failure rate. In the case of vibration there is a minimum chance of stone jammed.
The main element is the vibrating unit and the grooved feeder, which require installation on:
- One Z-axis in the case of a lunar vehicle where the unit goes forward and picks up the material. System can by lifted up and container directly placed to the return module.
- On a robotic arm in the case of a stationary landing module.
The vibration unit generates a linear feed movement using highly deflection composite springs. This moves the samples up the path. The vibration unit can drive a simple controller or microprocessor.
The power of the control unit will not exceed 20W, and weight of the sampler are 501,9 grams.
By changing the frequency and aptitude, we can control which samples will go after the feeder.
- High frequencies and small amplitude will result in larger stones and at lower frequencies and higher amplitude there will be a better little material.
For throwing too large stones, or with a full container, the servo-positioner arm is activated. He discards all large samples from the track and the container begins to fill with small material.
The percentage of vibration is also transferred to the container in which the samples are stored better and the maximum volume of the container is used.The teeth on the linear feeder, and the grooves on them, can be used as sieves, or even by agitate the surface.
The entire system supervises a 3D camera that measures the surroundings and samples before going to the container.
The camera can work as a real-time transmission to the operator on the Earth or as a fully autonomous system where the camera together with the control unit will evaluate the frequency, amplitude, or servo positioner control to accurately fill the container with correct samples.
As optional, a special impact hammer can be used to take samples from the rocks on the surface.
This tool works on a reciprocating direct-management system.
Contains a set of electric coils that can move by a metal core with an anchor inside the hammer.
The core slides in the chamber over the bushing of the highly resistant Iglidur plastic, which is ultra-low friction.
The chamber is closed and welded by the electron beam in a hard vacuum. this provides the right conditions for the outside of the planet, as there is no dangerous humidity or other gases in the chamber.
Core movement can be controlled by a frequency converter as well as a 3-phase motor. So we can regulate and control the speed of the core in both directions, its strength and its braking.
The hammer has an integrated shock absorber that protects the robotic arm from damage. Power consumption does not exceed 17W.
Thank you
VSS- Vibration sampling system
This system is designed to handle sample collection both from the surface and under the surface.
System contains a minimum number of moving parts for a minimum failure rate. In the case of vibration there is a minimum chance of stone jammed.
The main element is the vibrating unit and the grooved feeder, which require installation on:
- One Z-axis in the case of a lunar vehicle where the unit goes forward and picks up the material. System can by lifted up and container directly placed to the return module.
- On a robotic arm in the case of a stationary landing module.
The vibration unit generates a linear feed movement using highly deflection composite springs. This moves the samples up the path. The vibration unit can drive a simple controller or microprocessor.
The power of the control unit will not exceed 20W, and weight of the sampler are 501,9 grams.
By changing the frequency and aptitude, we can control which samples will go after the feeder.
- High frequencies and small amplitude will result in larger stones and at lower frequencies and higher amplitude there will be a better little material.
For throwing too large stones, or with a full container, the servo-positioner arm is activated. He discards all large samples from the track and the container begins to fill with small material.
The percentage of vibration is also transferred to the container in which the samples are stored better and the maximum volume of the container is used.The teeth on the linear feeder, and the grooves on them, can be used as sieves, or even by agitate the surface.
The entire system supervises a 3D camera that measures the surroundings and samples before going to the container.
The camera can work as a real-time transmission to the operator on the Earth or as a fully autonomous system where the camera together with the control unit will evaluate the frequency, amplitude, or servo positioner control to accurately fill the container with correct samples.
As optional, a special impact hammer can be used to take samples from the rocks on the surface.
This tool works on a reciprocating direct-management system.
Contains a set of electric coils that can move by a metal core with an anchor inside the hammer.
The core slides in the chamber over the bushing of the highly resistant Iglidur plastic, which is ultra-low friction.
The chamber is closed and welded by the electron beam in a hard vacuum. this provides the right conditions for the outside of the planet, as there is no dangerous humidity or other gases in the chamber.
Core movement can be controlled by a frequency converter as well as a 3-phase motor. So we can regulate and control the speed of the core in both directions, its strength and its braking.
The hammer has an integrated shock absorber that protects the robotic arm from damage. Power consumption does not exceed 17W.
Thank you
Similar models
grabcad
free

automatic machine,bowl feeder,parts feeder
...feeder can be specified. vibratory feeder manufacturers can use stainless steel to meet sanitary requirements in food processing.
grabcad
free

Lunar sampling system
...m controlled by level sensors.
the later filtering mechanism can slide to allow the sampling container to be removed or replaced.
grabcad
free

NEMA KANJENG LUNAR SAMPLING
... the arm has risen more than 60 degrees regolith will be slipped into the container that has been filtered between rock and dust.
grabcad
free

NASA Lunar Sampling System
...r sampling system
grabcad
nasa lunar sampling system
it will be given by a simple motor movement. and to connect to a robot arm
grabcad
free

NASA Lunar Sampling System
...r sampling system
grabcad
nasa lunar sampling system
it will be given by a simple motor movement. and to connect to a robot arm
grabcad
free

NASA Lunar Sampling System
...r sampling system
grabcad
nasa lunar sampling system
it will be given by a simple motor movement. and to connect to a robot arm
grabcad
free

NASA Lunar Sampling System
...nasa lunar sampling system
grabcad
can be mounted on a simple robot arm. motor helical system
grabcad
free

Lunar Sampler_9
...sampler is constructed of aluminum, except the material sweepers which are teflon. sample container carriage could be 3d printed.
grabcad
free

Regolith Lunar Sampler Sorter (RLSS)
...tion to assist movement of material.
*sorted material can be viewed through a slot in the top of the feed chute prior to deposit.
grabcad
free

Lunar Sampling System tool
...1. return to working position;
12. 180-degree turn;
13. opening capture (unloading the remaining samples of inappropriate size);
Vss
turbosquid
$5
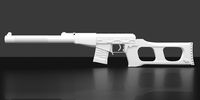
VSS
...3d model vss "" for download as obj, fbx, and blend on turbosquid: 3d models for games, architecture, videos. (1441719)
3ddd
free
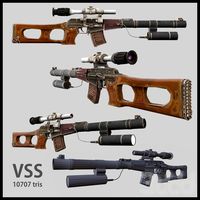
Low-poly VSS
...low-poly vss
3ddd
vss
игровая low-poly модель vss 10707 tris
turbosquid
$24
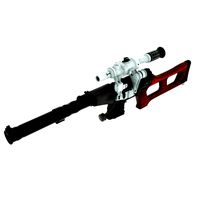
VSS Vintorez
...squid
royalty free 3d model vss vintorez for download as obj on turbosquid: 3d models for games, architecture, videos. (1310195)
3d_export
$15

Vss Vintorez v2
...vss vintorez v2
3dexport
soviet and russian silent sniper rifle vss vintorez
3d_export
$15
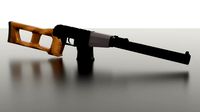
Vss Vintorez
...vss vintorez
3dexport
turbosquid
$100
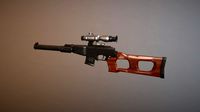
vss texture
... available on turbo squid, the world's leading provider of digital 3d models for visualization, films, television, and games.
turbosquid
$45
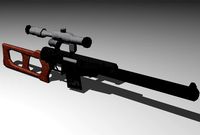
VSS Vintorez
... available on turbo squid, the world's leading provider of digital 3d models for visualization, films, television, and games.
turbosquid
$40
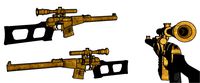
vss vintorez
... available on turbo squid, the world's leading provider of digital 3d models for visualization, films, television, and games.
turbosquid
$5

vss vintorez
... available on turbo squid, the world's leading provider of digital 3d models for visualization, films, television, and games.
3d_export
$5
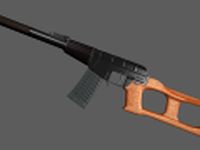
VSS Vintorez 3D Model
...vss vintorez 3d model
3dexport
vss vintorez rifle gun bullet ak 47
vss vintorez 3d model i.love.milka8242940 87841 3dexport
Vibration
design_connected
$16

Vibration Rug
...vibration rug
designconnected
ligne roset vibration rug computer generated 3d model. designed by tordjman, vincent.
3d_export
$15
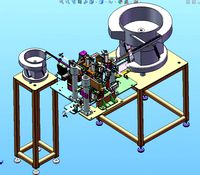
20 sets of vibrating plate direct vibration feeding mechanism
...oading and distribution structure of oil nozzle vibration plate, bearing vibration plate and conveyor belt distribution structure
turbosquid
$35
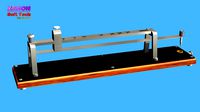
Vibrating Reed
...alty free 3d model vibrating reed for download as 3ds and fbx on turbosquid: 3d models for games, architecture, videos. (1197281)
turbosquid
$5

Vibrating conveyor,
...model vibrating conveyor, for download as ige, stl, and sldas on turbosquid: 3d models for games, architecture, videos. (1227258)
3d_export
$5
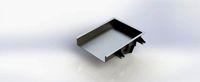
sorting-machine-vibrating-feeder
...sorting-machine-vibrating-feeder
3dexport
a simple and applicable sorting machine vibrating feeder model.
turbosquid
$9
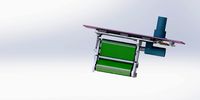
Vibration polishing module
...olishing module for download as 3ds, ige, obj, stl, and sldas on turbosquid: 3d models for games, architecture, videos. (1224249)
3d_export
$19

Full set of vibrating screen exciter
...g, eccentric shaft drawing, balance wheel drawing, shaft cover flange drawing, etc. 30 drawings, welcome to download and produce!
3d_export
$7
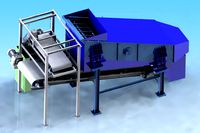
vibrating screening magnetic separation system
...vibrating screening magnetic separation system
3dexport
vibrating screening magnetic separation system
3d_export
$18
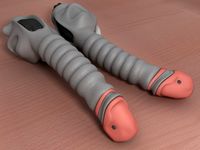
Penis shaped Vibrator 3D Model
...ed vibrator 3d model
3dexport
penis dick vibrator toy sex genital porno porn
penis shaped vibrator 3d model scyrus 85666 3dexport
turbosquid
free
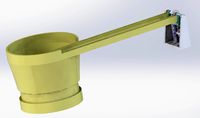
Vibrating plate feeding mechanism
...brating plate feeding mechanism for download as sldas and ige on turbosquid: 3d models for games, architecture, videos. (1655940)
Sampling
turbosquid
$15
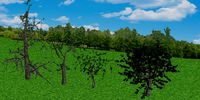
Tree Sample
...royalty free 3d model tree sample for download as max and fbx on turbosquid: 3d models for games, architecture, videos. (1238276)
turbosquid
$9

Blood Sample
... free 3d model blood sample for download as max, obj, and fbx on turbosquid: 3d models for games, architecture, videos. (1305026)
turbosquid
$2

Face Sample
...free 3d model face sample for download as blend, fbx, and obj on turbosquid: 3d models for games, architecture, videos. (1586198)
turbosquid
$3
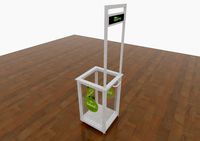
Sampling Bin
... 3d model sampling bin for download as max, fbx, 3ds, and obj on turbosquid: 3d models for games, architecture, videos. (1596035)
turbosquid
$39
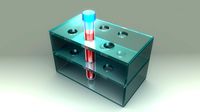
Blood sample
... available on turbo squid, the world's leading provider of digital 3d models for visualization, films, television, and games.
turbosquid
free

monkey sample
... available on turbo squid, the world's leading provider of digital 3d models for visualization, films, television, and games.
3d_export
$5
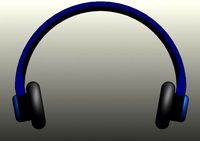
Headphone Sample
...created as a sample using solidworks. the rar file contains .sldprt file and .stl file. the 3d model can be used for 3d printing.
turbosquid
$30
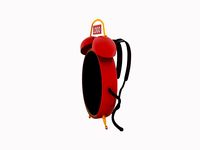
coffee Sampling Bag
...royalty free 3d model coffee sampling bag for download as 3ds on turbosquid: 3d models for games, architecture, videos. (1697356)
turbosquid
$7

Medicine Bottle Sample
...e 3d model medicine bottle sample for download as obj and fbx on turbosquid: 3d models for games, architecture, videos. (1332437)
turbosquid
$10
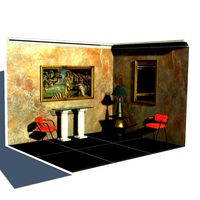
Living Room Sample
...living room sample for download as unitypackage, max, and fbx on turbosquid: 3d models for games, architecture, videos. (1705843)
System
archibase_planet
free
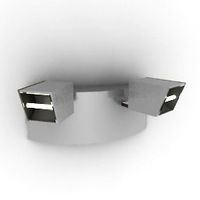
System
...m
archibase planet
fire alarm system fire alarm box
security light system - 3d model (*.gsm+*.3ds) for interior 3d visualization.
archibase_planet
free
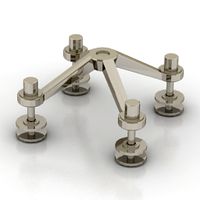
Spider system
...stem spider glass system
spider system to fix glass stefano galli n050912 - 3d model (*.gsm+*.3ds) for interior 3d visualization.
3ddd
$1
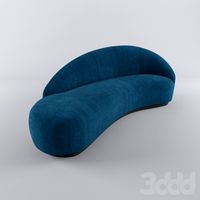
Euforia System
...euforia system
3ddd
euforia
euforia system
3d_export
$50
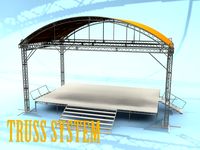
Roof system Truss system 3D Model
...oof system truss system 3d model
3dexport
roof system truss truss stage
roof system truss system 3d model aleksbel 38970 3dexport
3ddd
$1
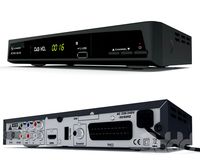
DVD System
...dvd system
3ddd
dvd , schneider
dvd system
design_connected
free
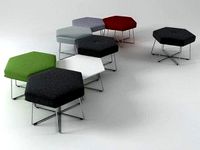
Seating system
...seating system
designconnected
free 3d model of seating system
3d_export
$5
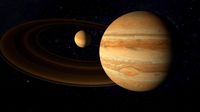
solar system
...solar system
3dexport
solar system in c4d, with 8k nasa textures
3ddd
$1
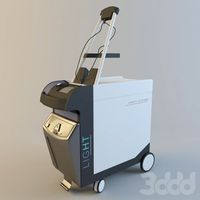
Quanta System
...quanta system
3ddd
медицина
quanta system.
лазерное оборудование для медицинских центров
3d_export
$15
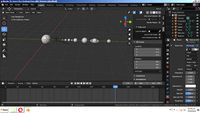
solar system
...nd the other the sun, the earth and the moon, the latter has an animation with camera movement included, the files are in spanish
3d_export
$14
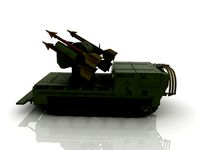
missile system
...missile system
3dexport