GrabCAD
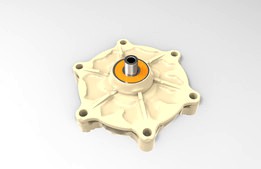
Vane pump for AIrbus
by GrabCAD
Last crawled date: 1 year, 10 months ago
Pump spec :
Weight = 76 grams (topology optimized version 62 grams ) without a motor
Q=7-10l/min (can be controlled with speed of the motor)
H=47m (about 5 bar) It can be modified to produce 10 bar by increasing radius of rotor and enloser by 2 and decreasing the speed of motor by 2.
Design process:
The most applicable pumps to use for this application are centrifugal type, gear, screw pumps and rotary vane pumps due to high pressure requirements and low flow with low pulsation.
Centrifugal pump will require multiple stages to get that small flow with high pressure which will make the assembly bulkier and more expensive to manufacture
Gear and screw pumps have higher pulsation rate than rotary vane as well as slightly lower efficiency. Also they are difficult and expensive to manufacture and maintain.
So I decided that rotary vane pump type is the most suitable in this application due to low pulsation (so we can achieve +-5% of the specified flow) , small size/ low weight , being easy to repair and cheap to manufacture.
Replaceable vanes can be really easily replaced when needed
I decided to design one action pump since the pressure is less 105kg/cm3 which doesn't create excessive pressure on the bearings and doesn't need to be compensated from the opposite side with the second 2nd action pressure.
I decided to use hollow steel shaft to decrease the weight. The shaft can be made from titanium as well to save some weight but it will increase the cost.
See attached picture for calculations proving design (if you need detailed calculations please ask) and FEA.
Safety factor is 2.
The weight turned out to be very small and I was able to decrease it even more using topology optimization
Material choice:
I picked PEEK (Polyether ether ketone) due to PEEK has cheaper manufacturing cost , harder , has better wear and friction , chemical resistance, lower density than aluminum and has cheaper manufacturing cost, has fewer leachables , has better dry wear properties, has better chemical resistance, has lower density than steel.
Bolts :
The force in one pump opening is about 1774 N
I recommend using M5 PEEK bolts reinforced with fiberglass (2160 N proof load per bolt, fiber glass almost triples the strength of peek bolts ).
Also there is an option using Aluminum 6061-T6 (2480 N proof load per bolt ) bolts and Stainless steel bolts (3200 N proof load per bolt ) however it will add some weight.
Manufacturing tips/ Assembly:
Rotor and the body of the pump can be injection molded and then diameters can be machined to spec to allow low cost. (Both parts can be made from aluminum as an option)
Vane gaps must have at least 0.01mm clearance
Press fit the shaft onto the rotor with A/X fit
I also suggest using splined connecting type for shaft / rotor to evenly distribute the load. I modeled it with key connection (still passed fea) due to very limited time.
Motor: 28v ,1080 rpm and 0.149 kWts
Control :
1 Option- Flow can be controlled with simple controller like Atmel ATmega8 and ESC (electronic speed controller)
Put flow meter and pressure meter on the outlet of the pump and feed that information to the controller to make the adjust of the rpm of the motor.
2 Option - to test pressure and flow changes depending on the altitude and then use altimeter feed to adjust the RPM using the same controller. (Let me know if you need more info on that)
BOM/Materials:
Seal 1mm x 7mm (Silicone rubber) x2
Seal 1mm x 62mm (Silicone rubber)
Pump vane (PEEK) X 3
Pump rotor (PEEK)
Pump encloser (PEEK)
Pump encloser upper (PEEK)
Shaft (Carbon steel)
Key (Carbon steel)
Bearing 608RS *2
Socket button head cap screw (PEEK reinforced with fiberglass or use regular steel) x 6
Spring 3m force 0.07 kg x 3
Hex flange nut with thread locker (PEEK reinforced with fiberglass or use regular steel
Cost :
Using injection molding technology the total cost of material can be about $3 a piece
The model is pretty rough and will need more tweaks and tests .
Weight = 76 grams (topology optimized version 62 grams ) without a motor
Q=7-10l/min (can be controlled with speed of the motor)
H=47m (about 5 bar) It can be modified to produce 10 bar by increasing radius of rotor and enloser by 2 and decreasing the speed of motor by 2.
Design process:
The most applicable pumps to use for this application are centrifugal type, gear, screw pumps and rotary vane pumps due to high pressure requirements and low flow with low pulsation.
Centrifugal pump will require multiple stages to get that small flow with high pressure which will make the assembly bulkier and more expensive to manufacture
Gear and screw pumps have higher pulsation rate than rotary vane as well as slightly lower efficiency. Also they are difficult and expensive to manufacture and maintain.
So I decided that rotary vane pump type is the most suitable in this application due to low pulsation (so we can achieve +-5% of the specified flow) , small size/ low weight , being easy to repair and cheap to manufacture.
Replaceable vanes can be really easily replaced when needed
I decided to design one action pump since the pressure is less 105kg/cm3 which doesn't create excessive pressure on the bearings and doesn't need to be compensated from the opposite side with the second 2nd action pressure.
I decided to use hollow steel shaft to decrease the weight. The shaft can be made from titanium as well to save some weight but it will increase the cost.
See attached picture for calculations proving design (if you need detailed calculations please ask) and FEA.
Safety factor is 2.
The weight turned out to be very small and I was able to decrease it even more using topology optimization
Material choice:
I picked PEEK (Polyether ether ketone) due to PEEK has cheaper manufacturing cost , harder , has better wear and friction , chemical resistance, lower density than aluminum and has cheaper manufacturing cost, has fewer leachables , has better dry wear properties, has better chemical resistance, has lower density than steel.
Bolts :
The force in one pump opening is about 1774 N
I recommend using M5 PEEK bolts reinforced with fiberglass (2160 N proof load per bolt, fiber glass almost triples the strength of peek bolts ).
Also there is an option using Aluminum 6061-T6 (2480 N proof load per bolt ) bolts and Stainless steel bolts (3200 N proof load per bolt ) however it will add some weight.
Manufacturing tips/ Assembly:
Rotor and the body of the pump can be injection molded and then diameters can be machined to spec to allow low cost. (Both parts can be made from aluminum as an option)
Vane gaps must have at least 0.01mm clearance
Press fit the shaft onto the rotor with A/X fit
I also suggest using splined connecting type for shaft / rotor to evenly distribute the load. I modeled it with key connection (still passed fea) due to very limited time.
Motor: 28v ,1080 rpm and 0.149 kWts
Control :
1 Option- Flow can be controlled with simple controller like Atmel ATmega8 and ESC (electronic speed controller)
Put flow meter and pressure meter on the outlet of the pump and feed that information to the controller to make the adjust of the rpm of the motor.
2 Option - to test pressure and flow changes depending on the altitude and then use altimeter feed to adjust the RPM using the same controller. (Let me know if you need more info on that)
BOM/Materials:
Seal 1mm x 7mm (Silicone rubber) x2
Seal 1mm x 62mm (Silicone rubber)
Pump vane (PEEK) X 3
Pump rotor (PEEK)
Pump encloser (PEEK)
Pump encloser upper (PEEK)
Shaft (Carbon steel)
Key (Carbon steel)
Bearing 608RS *2
Socket button head cap screw (PEEK reinforced with fiberglass or use regular steel) x 6
Spring 3m force 0.07 kg x 3
Hex flange nut with thread locker (PEEK reinforced with fiberglass or use regular steel
Cost :
Using injection molding technology the total cost of material can be about $3 a piece
The model is pretty rough and will need more tweaks and tests .
Similar models
grabcad
free

Hydraulic Vane Pump
...lsation, i.e. constant flow. as such, vane pumps produce less noise while maintaining a relatively high speed of up to 3,000 rpm.
grabcad
free

Centrifugal pump with flow meter
... a rotor consisting of plastic. due to the range of temperatures however the rotor in this application can surely not be plastic.
grabcad
free

Impeller
...inlet to accept incoming fluid, vanes to push the fluid radially, and a splined, keyed, or threaded bore to accept a drive-shaft.
grabcad
free

Rotor vane pump
...p
grabcad
this is a model of rotor vane pump, the shaft and vanes are movable. remove the back cover to view the inner assembly.
grabcad
free

Yuken Vane Pump
...ixed displacement - 9.5 cc/rev
max operating pressure - 175 bar
flange mounting
5.8 kgs weight
shaft speed range - 750 - 1800 rpm
grabcad
free

Vacuum Impeller
...tion engine or by steam driven turbine. the rotor usually names both the spindle and the impeller when they are mounted by bolts.
grabcad
free

Twin Screw Pump
... additive manufacturing technology like metal 3d printing with aluminium or titanium to assist in easier manufacturing of parts.
grabcad
free

Power Steering Pump 2002-2007 Toyota
...raulic pressure in the central vanes and rotor to mechanical motion, turning the rack and pinion assembly in the steering column.
grabcad
free

Impeller for Centrifugal Pump
...impeller for centrifugal pump
grabcad
an impeller is a rotor used to increase the pressure and flow of a fluid.
grabcad
free

Radial Vane Damper
...erglass construction.
used to manage rotational exhaust flow to lineal. thereby recovering forward velocity and static pressure.
Airbus
grabcad
free

AIRBUS
...airbus
grabcad
airbus surface
grabcad
free

AIRBUS
...airbus
grabcad
simple model of airbus
grabcad
free

Airbus
...airbus
grabcad
airbus aircraft, passenger jet
grabcad
free

AirBus
...airbus
grabcad
3d modeling of airbus using catia v5
grabcad
free

AIRBUS A380
...airbus a380
grabcad
airbus
grabcad
free

Airbus A3xx
...airbus a3xx
grabcad
airbus, aircraft
grabcad
free

Airbus A380
...airbus a380
grabcad
airbus a380
grabcad
free

AIRBUS A350
...airbus a350
grabcad
airbus a350
grabcad
free

Airbus A330
...airbus a330
grabcad
airbus a330
grabcad
free

AIRBUS A950
...airbus a950
grabcad
concept airbus
Vane
grabcad
free

vane
...vane
grabcad
vane
grabcad
free

vane
...vane
grabcad
vane
grabcad
free

vane
...vane
grabcad
vane
grabcad
free

vanes
...vanes
grabcad
design of a vane
grabcad
free

VANE
...vane
grabcad
its a simple vane with 3 blades,
grabcad
free

vane
...vane
grabcad
k
grabcad
free

Vane
...vane
grabcad
windmill
grabcad
free

vane model
...vane model
grabcad
vane model
grabcad
free

vane model
...vane model
grabcad
vane model
grabcad
free

Weather Vane
...weather vane
grabcad
a modern weather vane
Pump
grabcad
free

PUMP WHEEL FOR PUMP
...pump wheel for pump
grabcad
pump wheel for pump
grabcad
free

pump
...pump
grabcad
this pump used for air pumping
grabcad
free

Pump operating pump
...pump operating pump
grabcad
radno kolo centrifugalne pumpe
grabcad
free

Pump
...pump
grabcad
this pump is used for pumping technical liquids
grabcad
free

Pumps
...pumps
grabcad
come on! let's pump it, pump it!
grabcad
free

Pump
...pump
grabcad
pump
grabcad
free

Pump
...pump
grabcad
pump
grabcad
free

pump
...pump
grabcad
pump
grabcad
free

pump
...pump
grabcad
pump
grabcad
free

PUMP
...pump
grabcad
pump