Thingiverse
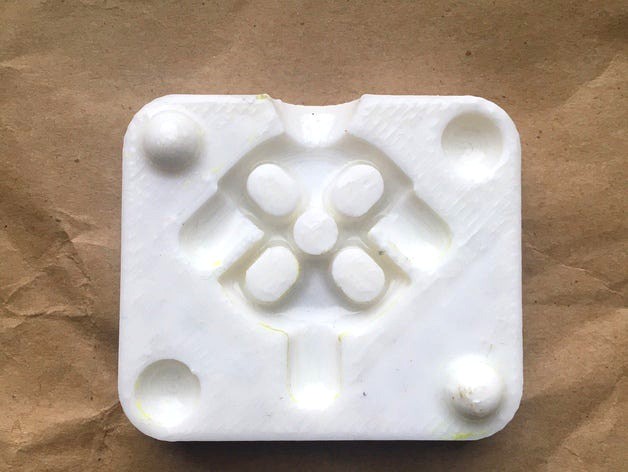
Uber Design U180 - part casting by m4k3r
by Thingiverse
Last crawled date: 3 years ago
I’ve been following the RC groups thread for the insanely powerful Uber Design U180.
I saw my buddy fly the U180 the other day. It looks super cool and crazy fast. I was hesitant to jump in due to the comments of parts breaking during crashes. In the thread people were talking about trying to mold motor mounts and mid plates from actual parts. Previously I tried to mold from 3D printed parts and found it frustrating.
Background:
Creating 3D printable molds in CAD software is a hassle. The steps are well known. However, for every iterate of the part you need redo the whole mold making process.
I was really happy to find Jason Webb’s OpenSCAD script which does much of the heavy lifting. Check out his project http://www.thingiverse.com/thing:31581 There is also further info on his website. http://jason-webb.info
Updates
6/19/2016 – I created two versions of the bottomplate with different thicknesses (beefy and skinny). I also created a jig to drill the carbon fiber rods so it can be joined together with nylon zip ties. I designed a small support to secure the ESCs to the carbon fiber cross bars with zip ties.
The assembly of the Uber went well and I’m happy with the end result. See attached photos
Give them a try and send feedback.
4/26/2016 - The casting approach required the recreation of Theledman’s original design to be mold release friendly. The current designs are coming out of the casting well and the molds have been reusable with no wear.
All designs are dimensionally accurate for the motor mount holes and 10mm OD/8mm ID Carbon Fiber Tube. I created three different designs to address various approaches to the inner cross section connection to the motor mount.
Design 1 is most similar to Theledman’s design but requires the drilling of a hole for - 6mm OD/4mm ID Carbon Fiber Tube
Looking to minimize the amount of post casting work, I thought creating a boss was a better approach. Then I found jolars’ remix and my assumption was confirmed.http://www.thingiverse.com/thing:1406948
Design 2 includes a boss for the - 6mm OD/4mm ID Carbon Fiber Tube. (The STL file has –sb- in the name for small boss)
Design 3 includes a boss for the - 10mm OD/8mm ID Carbon Fiber Tube. (The STL file has –bb- in the name for big boss). – NOTE pay attention to the changes in his BOM which uses all 10mm OD CF tubing.
Of all the designs, I believe that either #1 or #3 are the best approach going forward. Decision criteria. If you want to use the original BOM and are willing to drill the hole, go with Design 1. If you are looking for more durability and are willing to switch to all 10mm OD CF tubing, go with Design 3.
All the necessary files are included so you can remix or tweak on your own.
I saw my buddy fly the U180 the other day. It looks super cool and crazy fast. I was hesitant to jump in due to the comments of parts breaking during crashes. In the thread people were talking about trying to mold motor mounts and mid plates from actual parts. Previously I tried to mold from 3D printed parts and found it frustrating.
Background:
Creating 3D printable molds in CAD software is a hassle. The steps are well known. However, for every iterate of the part you need redo the whole mold making process.
I was really happy to find Jason Webb’s OpenSCAD script which does much of the heavy lifting. Check out his project http://www.thingiverse.com/thing:31581 There is also further info on his website. http://jason-webb.info
Updates
6/19/2016 – I created two versions of the bottomplate with different thicknesses (beefy and skinny). I also created a jig to drill the carbon fiber rods so it can be joined together with nylon zip ties. I designed a small support to secure the ESCs to the carbon fiber cross bars with zip ties.
The assembly of the Uber went well and I’m happy with the end result. See attached photos
Give them a try and send feedback.
4/26/2016 - The casting approach required the recreation of Theledman’s original design to be mold release friendly. The current designs are coming out of the casting well and the molds have been reusable with no wear.
All designs are dimensionally accurate for the motor mount holes and 10mm OD/8mm ID Carbon Fiber Tube. I created three different designs to address various approaches to the inner cross section connection to the motor mount.
Design 1 is most similar to Theledman’s design but requires the drilling of a hole for - 6mm OD/4mm ID Carbon Fiber Tube
Looking to minimize the amount of post casting work, I thought creating a boss was a better approach. Then I found jolars’ remix and my assumption was confirmed.http://www.thingiverse.com/thing:1406948
Design 2 includes a boss for the - 6mm OD/4mm ID Carbon Fiber Tube. (The STL file has –sb- in the name for small boss)
Design 3 includes a boss for the - 10mm OD/8mm ID Carbon Fiber Tube. (The STL file has –bb- in the name for big boss). – NOTE pay attention to the changes in his BOM which uses all 10mm OD CF tubing.
Of all the designs, I believe that either #1 or #3 are the best approach going forward. Decision criteria. If you want to use the original BOM and are willing to drill the hole, go with Design 1. If you are looking for more durability and are willing to switch to all 10mm OD CF tubing, go with Design 3.
All the necessary files are included so you can remix or tweak on your own.
Similar models
thingiverse
free

Über Design Ü180 -- Uber Design U180 by theledman
...g each rod. ensure that rods going through mid are inserted into motormounts before compressing the frame to fully seat each rod.
thingiverse
free
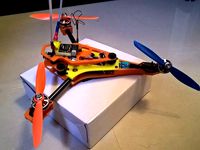
modified for 10mm OD carbon tube by metalnow
...w
thingiverse
carbon tube 10mm od, 8mm id, cut to 110mm length
test flight footage:https://www.youtube.com/watch?v=jxf2w932uly
thingiverse
free
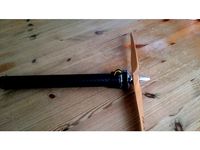
Motor mount for 30mm carbon fiber tube for airplane by Flying_Ginger
...or mounting the t-motor mn3508-20 580kv to a carbon fiber tube. i am going to use this as a nose for a very streamline fpv plane.
thingiverse
free
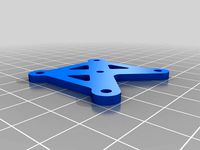
Uber U180 EZPrint Remixed for easier FDM printing by The_Wizard
...an be printed flat, or vertically. if printed vertically separate/delete the support pieces in your slicer.
step files included.
grabcad
free

Carbon Fiber Gear Box Shroud
...mechanism required a three gear train. for aesthetics and weight reduction we incorporated a cf shroud to enclose the gear train.
thingiverse
free
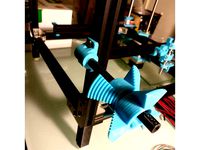
10mm Rod Bracket for Tech2C Spool Holder by superjamie
...tely not going anywhere!
openscad source is included if you want to remix it. cc-sa so please re-share any derivative you create.
thingiverse
free

Stand for Handheld Gimbal by droneking_pw
...stand for handheld gimbal by droneking_pw
thingiverse
i used 10mm carbon fiber tubes.
grabcad
free

Brushless motor mount
...ize brushless motor mount for carbon fiber 10mm pipe.
solid part and stl
my working e-maill for your design
rwork18422@gmail.com
thingiverse
free
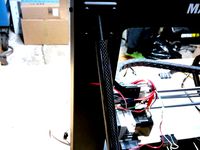
Malyan M150 Z Brace Modified for 16mm Carbon tubes( Wanhao Duplicator i3) by The_Wizard
...parts for second side. should be compatible with other similar machines such as the wanhao duplicator i3 etc. amazon...
thingiverse
free
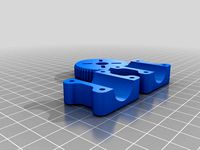
22XX Motor Mount 18MM CF Tube by FPV_Pilot
...otors to 18mm carbon fiber tube.
did not print yet. probably needs supports. 100% infill for strength
abs or petg recommended.
U180
thingiverse
free

U180 VTX Mount by Jonny1983
... the main body. it's designed to fit over the hex standoffs i was using, not sure how it'll fit over circular stand offs.
thingiverse
free
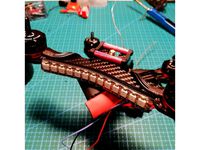
U180 quadcopter 3D-printed parts by Ledimestari
... the battery and the other enables you to have leds on your "top" arm.
print the ledmount vertically without supports.
thingiverse
free
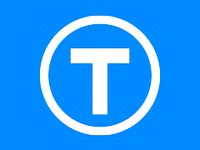
Uber Design U180 Tube Calculator by Pseudonymite
...ut, so you'll need to save the file and open with openscad to modify. results are given with the echo command to the console.
thingiverse
free
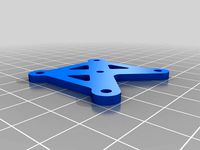
Uber U180 EZPrint Remixed for easier FDM printing by The_Wizard
...an be printed flat, or vertically. if printed vertically separate/delete the support pieces in your slicer.
step files included.
thingiverse
free

Über Design Ü180 -- Uber Design U180 by theledman
...g each rod. ensure that rods going through mid are inserted into motormounts before compressing the frame to fully seat each rod.
M4K3R
thingiverse
free

FrSky holder for the Morphite 180 by m4k3r
...hite 180 by m4k3r
thingiverse
while upgrading my morphite i decided to design a stackable modular holder for the frsky receiver.
thingiverse
free
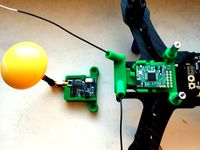
TS5840 holder for the Morphite 180 by m4k3r
... the morphite 180 by m4k3r
thingiverse
while upgrading my morphite i decided to design a stackable modular holder for ts5840 vtx
thingiverse
free
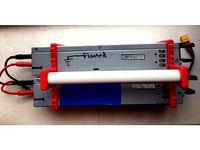
DPS-600 Power Supply Caddy by m4k3r
...power supply caddy by m4k3r
thingiverse
here is an easy way to mount and carry a pair dps-600 power supplies for field charging.
thingiverse
free

DPS-1200 Power Supply Caddy by m4k3r
...ower supply caddy by m4k3r
thingiverse
here is an easy way to mount and carry a pair dps-1200 power supplies for field charging.
thingiverse
free

Buzzer mount on standoff with offset by m4k3r
...t offset versions in the files.
i’ve also attached the 123d design files so you can tweak the design to meet your specific needs.
thingiverse
free
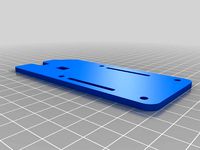
Morphite 180 Top plate for the modular TS5840 VTX holder by m4k3r
...plate is designed to work with the modular ts5840 vtx holder.
cutouts are correctly aligned for the antenna and vtx dip switches.
thingiverse
free

FPV racing gate connectors by m4k3r
...und ends are meant to be inserted into pvc pipes. the ones with the fan configuration are mean to be inserted into pool noodles.
thingiverse
free
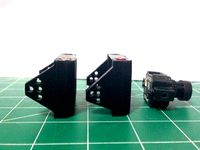
Fatshark camera mount - adjustable by m4k3r
...pired me to create a design that can be easily extended to other fpv aircraft. autocad 123d source files included. remix it.
thingiverse
free
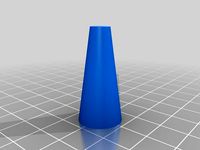
ZMR and Armattan Morphite Legs / Landing Gear by m4k3r
...he 123d cad files in case you want to customize the leg height further.
the hole is designed to accommodate a m3 12-16mm screw.
Uber
turbosquid
$9
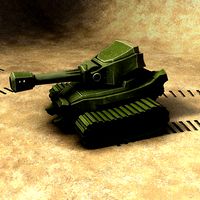
Uber tank
...d
royalty free 3d model 3d tank uber scetch for download as on turbosquid: 3d models for games, architecture, videos. (1699599)
turbosquid
$49

HAD1-T Helineo Uber
...free 3d model had1-t helineo uber for download as max and fbx on turbosquid: 3d models for games, architecture, videos. (1605816)
3d_export
free

Download free Uber sword 3D Model
...download free uber sword 3d model
3dexport
youtoo32
uber sword 3d model bouchet 50494 3dexport
turbosquid
$10
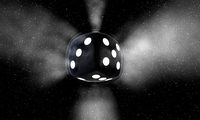
Uber Super Spacey Dice Planet
... available on turbo squid, the world's leading provider of digital 3d models for visualization, films, television, and games.
3d_export
$5
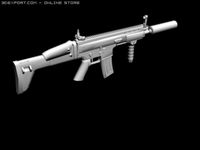
FN SCAR 3D Model
...obj weapon gun fn scar fn scar 3d model uber 19559...
3dfindit
free

UBER
...uber
3dfind.it
catalog: a&t
thingiverse
free

Uber Gnome by megane008
...uber gnome by megane008
thingiverse
my one of the kind gnome for the competition
renderosity
$9

Uber Suit for V4
.../>
- second skin suit,<br />
- helmet,<br />
- boots,<br />
- 5 materials for poser and daz studio</p>
thingiverse
free
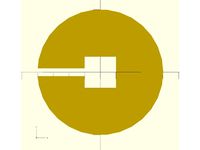
Fast And Basic Clothing Hanger Divider (Uberized) by mofosyne
...ce think?
unlike the original design, this is not too practical. as the hole inside 20cm. unless you have a 20cm diameter hanger?
unity_asset_store
$35
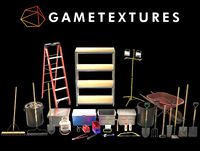
Garage & Toolshed Prop Uber Pack by GameTextures
...hed prop uber pack by gametextures asset from gametextures.com. find this & other props options on the unity asset store.
Casting
3ddd
free
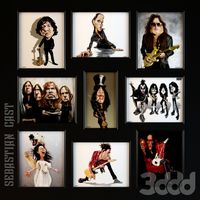
Sebastian Cast
...sebastian cast
3ddd
sebastian cast
карикатуры от себастьяна каста
3ddd
$1
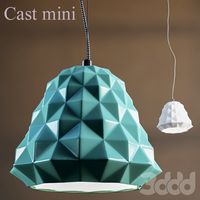
Cast mini
...cast mini
3ddd
present time
подвесной светильник cast mini
материал: керамика
размер: 20x166
производитель: present time
turbosquid
$19
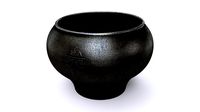
Cast Iron
...rbosquid
royalty free 3d model cast iron for download as max on turbosquid: 3d models for games, architecture, videos. (1609108)
3d_export
$6
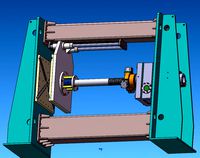
Design of die casting machine
...design of die casting machine
3dexport
design of die casting machine
3ddd
$1

Wood Casting by Hilla Shamia
...wood casting by hilla shamia
3ddd
wood casting by hilla shamia
turbosquid
$30
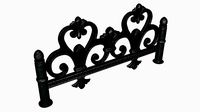
Cast iron fenceClassic
...alty free 3d model cast iron fenceclassic for download as max on turbosquid: 3d models for games, architecture, videos. (1630755)
turbosquid
$15

Cast-iron bench
...id
royalty free 3d model cast-iron bench for download as max on turbosquid: 3d models for games, architecture, videos. (1239993)
turbosquid
$15
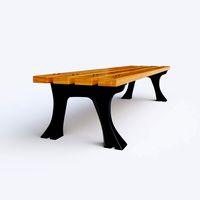
Cast-iron bench
...id
royalty free 3d model cast-iron bench for download as max on turbosquid: 3d models for games, architecture, videos. (1239991)
turbosquid
$13
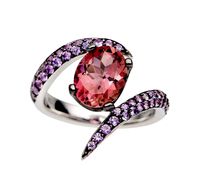
Ring with 2 casts
...
royalty free 3d model ring with 2 casts for download as 3dm on turbosquid: 3d models for games, architecture, videos. (1375610)
turbosquid
free
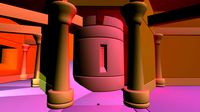
Caste Room with pillars
... 3d model caste room with pillars for download as xsi and fbx on turbosquid: 3d models for games, architecture, videos. (1305991)
Part
3d_export
$5
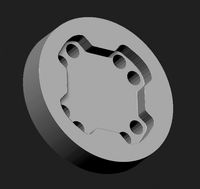
Parts
...parts
3dexport
parts
3d_export
$5
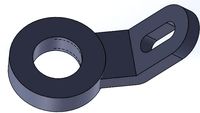
Part
...part
3dexport
part
3d_export
$5

Part
...part
3dexport
machine part
3d_export
$65
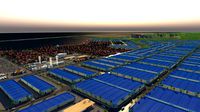
Part
...part
3dexport
simple rendering of the scene file
3d_export
$65
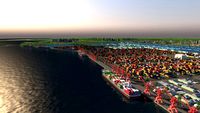
Part
...part
3dexport
simple rendering of the scene file
3d_export
$30

fan part
...fan part
3dexport
this is a part of fan of pedastal
3d_export
$10
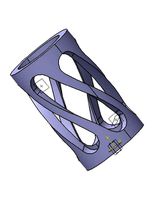
machine parts
...machine parts
3dexport
3d part modeling work ,contact for 3d work
turbosquid
$59
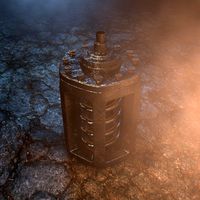
Mechanical Part
...id
royalty free 3d model mechanical part for download as c4d on turbosquid: 3d models for games, architecture, videos. (1410833)
turbosquid
$17
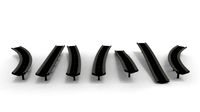
Road parts
...bosquid
royalty free 3d model road parts for download as 3ds on turbosquid: 3d models for games, architecture, videos. (1192967)
turbosquid
$9

Cutter Parts
...squid
royalty free 3d model cutter parts for download as stl on turbosquid: 3d models for games, architecture, videos. (1220010)
Design
3ddd
$1
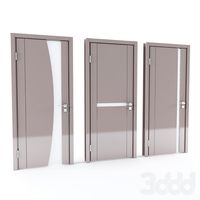
LINE DESIGN (Doors Design)
...line design (doors design)
3ddd
дверь
modern doors design - line design concept
turbosquid
$5

designer
...alty free 3d model designer for download as max, obj, and fbx on turbosquid: 3d models for games, architecture, videos. (1422665)
3ddd
$1
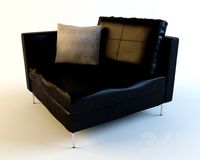
VER DESIGN
...ver design
3ddd
ver design
кресло ver design
3ddd
$1
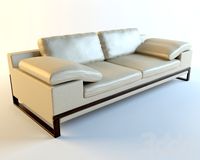
VER DESIGN
...ver design
3ddd
ver design
диван ver design
3ddd
$1
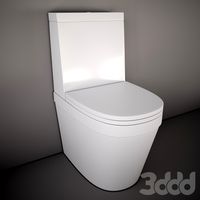
Bagno design
...bagno design
3ddd
bagno design , унитаз
санитария bagno design
3ddd
free
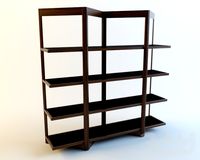
VER DESIGN
...ver design
3ddd
ver design , стеллаж
полка ver design
3ddd
$1
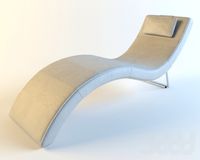
VER DESIGN
...ver design , лежак , шезлонг
шезлонг ver design
3d_export
free
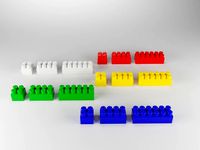
designer
..., trees and much more. the model has 3 types of parts: - 4 cells - 6 cells - 8 cells the *.max file contains 5 colored materials.
3d_export
$19
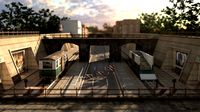
level design
...level design
3dexport
you can use this design (level design) in your own game.
3d_export
$7
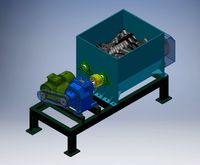
Crusher design
...crusher design
3dexport
crusher design