GrabCAD

The Jesse
by GrabCAD
Last crawled date: 2 years ago
My heliostat design uses origami folds to compact its size and this improves transport stability. The basic shape is hexagonal. The design can be described in three parts which are assembled to be deployed as a single unit. The three parts are:
The Vertical Beam, The Top Pointer, and the Top Panel.
To deploy it, pressurized air is used to expand bellows which form the vertical beam.
The Jesse is packaged in a sleeve prior to deployment to protect it from lunar dust. When deployment occurs, the bellows will expand using pressurized air to a height. Next, solar heating will expand the top panel as the nitinol rods straighten. The Jesse is now deployed.
The vertical beam which holds up the heliostat panel is a connected series of hexagonal bellows (figure 3). Before deployment, it travels as a compact form (figure 4). It can be constructed out of a light metal such as aluminum. The number of hexagonal bellows depends on the size of the top panel it will support. The beam is deployed by releasing pressurized gas through its hollow center. Pairs of hinges are used to brace the bellow and lock at 90 degrees preventing the bellows from collapsing or tilting. Once expanded, it cannot be collapsed again while on the lunar surface.
The Top Pointer
This pointer located at the top of the beam is also a compliant mechanism. A rotating motor will orient the heliostat to the sun. The heliostat can be tilted 90 degrees. The small motor used for tilting is remotely operated. The motors are insulated to protect them from extreme temperatures.
Attribution: 2 DOF fully compliant space pointing mechanism by BYU_CMR Group is licensed under theCreative Commons - Attribution license. https://creativecommons.org/licenses/by/4.0/
Source: https://www.thingiverse.com/thing:3612786
Attribution: BYU Compliant Mechanisms Research Group https://www.compliantmechanisms.byu.edu/
The hexagonal-shaped top panel uses origami principles known to NASA. The top panel is expanded by the solar heating of nitinol rods bent during assembly, but straightened during deployment by solar heating.
Solar panels are located in the center of the panel. Before deployment, the panel is protected and stable for transport as it is folded tightly (see figure 6) and covered in a protective sleeve.
NASA can use any suitable material (such as mylar) which can be creased and folded. If needed, an additional layer of material can be added to increase tensile strength.
The Vertical Beam, The Top Pointer, and the Top Panel.
To deploy it, pressurized air is used to expand bellows which form the vertical beam.
The Jesse is packaged in a sleeve prior to deployment to protect it from lunar dust. When deployment occurs, the bellows will expand using pressurized air to a height. Next, solar heating will expand the top panel as the nitinol rods straighten. The Jesse is now deployed.
The vertical beam which holds up the heliostat panel is a connected series of hexagonal bellows (figure 3). Before deployment, it travels as a compact form (figure 4). It can be constructed out of a light metal such as aluminum. The number of hexagonal bellows depends on the size of the top panel it will support. The beam is deployed by releasing pressurized gas through its hollow center. Pairs of hinges are used to brace the bellow and lock at 90 degrees preventing the bellows from collapsing or tilting. Once expanded, it cannot be collapsed again while on the lunar surface.
The Top Pointer
This pointer located at the top of the beam is also a compliant mechanism. A rotating motor will orient the heliostat to the sun. The heliostat can be tilted 90 degrees. The small motor used for tilting is remotely operated. The motors are insulated to protect them from extreme temperatures.
Attribution: 2 DOF fully compliant space pointing mechanism by BYU_CMR Group is licensed under theCreative Commons - Attribution license. https://creativecommons.org/licenses/by/4.0/
Source: https://www.thingiverse.com/thing:3612786
Attribution: BYU Compliant Mechanisms Research Group https://www.compliantmechanisms.byu.edu/
The hexagonal-shaped top panel uses origami principles known to NASA. The top panel is expanded by the solar heating of nitinol rods bent during assembly, but straightened during deployment by solar heating.
Solar panels are located in the center of the panel. Before deployment, the panel is protected and stable for transport as it is folded tightly (see figure 6) and covered in a protective sleeve.
NASA can use any suitable material (such as mylar) which can be creased and folded. If needed, an additional layer of material can be added to increase tensile strength.
Similar models
grabcad
free

Lunar Heliostat
...mounted over a fixed platform or a mobile platform. as its size is tubular it can be transported in pairs to sites, and deployed.
grabcad
free

nitinol joint
...equired junctions in a sequence.
the shape of individual panels need not be hexagonal. it can be of any shape like triangles etc.
grabcad
free

LT
...centrate the light stream for radiative heat.
total reflective surface: 10.5 m2
solar panels: 2.8 m2
heliostat mass: up to 70 kg
grabcad
free

Nitinol star shade - Nitinol based joints, truss and reflective panels for star shade
...al shape. it can be of any shape like triangles etc.
note: i am not able to upload ppt so pdf version and videos were uploaded
grabcad
free

🌖Torch
... m2
solar panels: 2.8 m2
heliostat mass: up to 100 kg
rover model by daniel loera (🙏)
https://grabcad.com/library/mars-rover-28
grabcad
free

Folding heliostat
...when the heliostat is folded down. folding mechanism is similar to the umbrella folding mechanism. it is driven by...
grabcad
free

Heliostat rover (Ijele)
...ith the necessary dimensions of about 2m by 1.5m an it is then stowed using the harness at the bottom of the primary lunar rover.
grabcad
free

Non-Motorized-Deployment Heliostat
... entire package can be scaled down to fit into or onto a rover. more mirrors can be added to make up for reduced reflecting area.
grabcad
free

Rollup Heliostat
... is a solar panel at the front of the box. the tilt and swivel mechanisms are at the bottom of the housing connected to the rover
grabcad
free

ORIGAS - Origami Gas Inflated Panel - Heliostat design
...oldable surface.
it is designed to be deployed and locked once with only the gas pressure of small tanks located below the panel.
Jesse
design_connected
$11
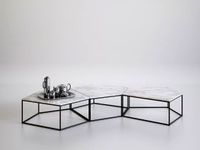
Jess
...jess
designconnected
minotti jess computer generated 3d model. designed by dordoni, rodolfo.
3ddd
$1
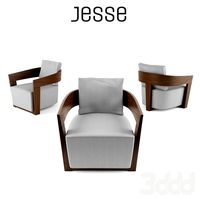
Jesse CINDY
...y
3ddd
jesse , cindy
http://www.gomodern.co.uk/store/jesse-cindy-armchair.html
3ddd
$1

Стеллаж Jesse Aleph
... aleph , jesse
стеллаж для книг от фабрики jesse.
3ddd
$1
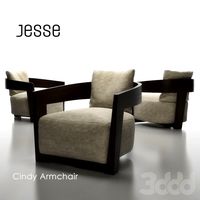
Jesse Cindy Chair
...jesse cindy chair
3ddd
jesse
jesse cindy armchair in 3dsmax2012 vray scene with maps & materials + obj format.
turbosquid
$28

Jesse Daniel
... 3d model jesse daniel for download as max, max, fbx, and obj on turbosquid: 3d models for games, architecture, videos. (1645675)
turbosquid
$12

Nowodvorski jess
... available on turbo squid, the world's leading provider of digital 3d models for visualization, films, television, and games.
turbosquid
$10
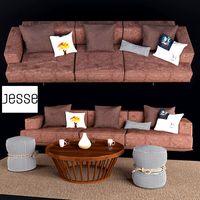
Sofa JESSE Oliver
...
royalty free 3d model sofa jesse oliver for download as max on turbosquid: 3d models for games, architecture, videos. (1198542)
turbosquid
$20
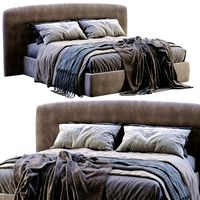
Jesse Bed Prince
...ty free 3d model jesse bed prince for download as max and obj on turbosquid: 3d models for games, architecture, videos. (1644622)
turbosquid
$20
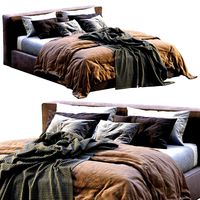
Jesse Bed Mark
...alty free 3d model jesse bed mark for download as max and obj on turbosquid: 3d models for games, architecture, videos. (1643600)
turbosquid
$20
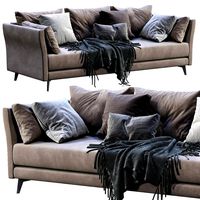
Jesse Sofa Ives
...lty free 3d model jesse sofa ives for download as max and obj on turbosquid: 3d models for games, architecture, videos. (1639129)