GrabCAD
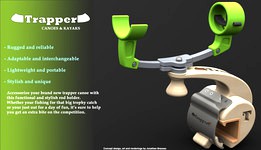
Rod Holder Concept 6/concept 3 update:
by GrabCAD
Last crawled date: 1 year, 10 months ago
This is an update to my third concept design, “The Hammerhead”. It can also be used with my previous concept, “The Blade”. It uses the exact same base as the Hammerhead but the carrier shown here is completely new in design. It offers a cheaper and more easily built option from which to choose.
Materials:
-Aluminum
-Plastic
-wood
This design is simple, super functional and strong and very cheap and easy to manufacture. As the competition wares on, I’ve noticed a lot of entries using bowed steel Roding as the material for the main rod holder. I really liked that design style, structural and aesthetically but my concern is that the cost involved with making it would be high because a welder would need to be hired and the welding process would be time consuming and intricate. I wanted to leave welding out of the equation.
Notes on manufacturing:
This design uses just a simple piece of aluminum as the main backbone for the rod carrier, .4” squared. The aluminum can be made from simple, raw stock purchased at an aluminum supplier. It then has a simple machining operation performed on it to round the edges and corners and to cut the two screw holes out. It’s then annealed and bent, preferably by automation. No welding is involved.
Two plastic components are attached by two screws on the front and back of the aluminum backbone to grasp the rod and hold it in place. The plastic can either be injection molded or 3D printed but IM is the cheaper solution. These would be the ideal materials, however wood can be substituted.
Because these two components are bolt on’s, it allows for interchangeability. The idea would be to start out with a single rod holder design and then introduce other accessories as sales progress, dual rod holder, specialty rod holders etc. It’s a very powerful design concept and allows for adaptability and extra revenue streams later on. This is the first design to deliberately incorporate "interchangeability" into it, I think it's an important criteria to consider, from a business perspective and for product performance.
Finally, the backbone assembly is held in place by two CNC machined aluminum pressure plates. When the knob is loosened the rod carrier can be slide back and forth for different inclinations and rotated 360 degrees.
thanks for looking
Jonathan-
***UPDATE!!
I have received some pricing estimates for injection molding from a popular turnkey manufacturer. It gives a real world idea of the pricing for some of the plastic parts. These quotes are 100% real world and the parts could be at your doorstep in 15 business days. Still waiting on quotes for the CNC aluminum parts.
The knob part (Knob_concept6.sldprt) if made from plastic as opposed to wood.
- tooling cost : 3645$ US dollars, good for unlimited usage
qty: 25-100 = 2.9$ per unit
1000 = 2.64$ per unit
5,000 = 1.79$ per unit
10,000 = 1.75$ per unit
the rear plastic part (carrierbackpart_concept6.sldpart)
tooling cost: 6480$US
qty: 25-1000 = 3.09 per unit
5000 = 2.27 per unit
10000 = 2.22 per unit
The carrier front part(carrierfrontpart_concept6.sldprt)
tooling cost: 6140$
qty: 25-1000 = 2.9$US per unit
5000= 2.07$US per unit
10,000= 2.03$US per unit.
Materials:
-Aluminum
-Plastic
-wood
This design is simple, super functional and strong and very cheap and easy to manufacture. As the competition wares on, I’ve noticed a lot of entries using bowed steel Roding as the material for the main rod holder. I really liked that design style, structural and aesthetically but my concern is that the cost involved with making it would be high because a welder would need to be hired and the welding process would be time consuming and intricate. I wanted to leave welding out of the equation.
Notes on manufacturing:
This design uses just a simple piece of aluminum as the main backbone for the rod carrier, .4” squared. The aluminum can be made from simple, raw stock purchased at an aluminum supplier. It then has a simple machining operation performed on it to round the edges and corners and to cut the two screw holes out. It’s then annealed and bent, preferably by automation. No welding is involved.
Two plastic components are attached by two screws on the front and back of the aluminum backbone to grasp the rod and hold it in place. The plastic can either be injection molded or 3D printed but IM is the cheaper solution. These would be the ideal materials, however wood can be substituted.
Because these two components are bolt on’s, it allows for interchangeability. The idea would be to start out with a single rod holder design and then introduce other accessories as sales progress, dual rod holder, specialty rod holders etc. It’s a very powerful design concept and allows for adaptability and extra revenue streams later on. This is the first design to deliberately incorporate "interchangeability" into it, I think it's an important criteria to consider, from a business perspective and for product performance.
Finally, the backbone assembly is held in place by two CNC machined aluminum pressure plates. When the knob is loosened the rod carrier can be slide back and forth for different inclinations and rotated 360 degrees.
thanks for looking
Jonathan-
***UPDATE!!
I have received some pricing estimates for injection molding from a popular turnkey manufacturer. It gives a real world idea of the pricing for some of the plastic parts. These quotes are 100% real world and the parts could be at your doorstep in 15 business days. Still waiting on quotes for the CNC aluminum parts.
The knob part (Knob_concept6.sldprt) if made from plastic as opposed to wood.
- tooling cost : 3645$ US dollars, good for unlimited usage
qty: 25-100 = 2.9$ per unit
1000 = 2.64$ per unit
5,000 = 1.79$ per unit
10,000 = 1.75$ per unit
the rear plastic part (carrierbackpart_concept6.sldpart)
tooling cost: 6480$US
qty: 25-1000 = 3.09 per unit
5000 = 2.27 per unit
10000 = 2.22 per unit
The carrier front part(carrierfrontpart_concept6.sldprt)
tooling cost: 6140$
qty: 25-1000 = 2.9$US per unit
5000= 2.07$US per unit
10,000= 2.03$US per unit.
Similar models
grabcad
free

Part Carrier
... cardboard box. this allows for different sizes and quantities for the supplier, along with a low cost, non -returnable container
thingiverse
free
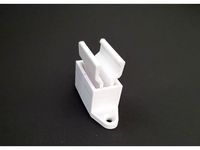
Crank Rod Holder Adjustable by Sisul
...pla i am not sure if this material would not break if used for a longer time.
one clamp and two clamp mounts are needed per unit.
grabcad
free

Rod Holder Challenge
...that was structurally sound while maintaining the aesthetic of similar pieces of equipment that can be found for fishing,...
thingiverse
free

Prusa i3 spool holder by mahdikhashan
...; parts and 10mm threaded rod for filament holding.
use two cable tie to fasten "bottom" part to the plexiglass plate.
thingiverse
free

Prusa i2 Revamp - Cubic Structure Conversion by redhatman
...x-axis or near the edges. if you have a similar issue, or want to convert to this, i've been...
grabcad
free

Rod Holder Challenge Concept 5: The slider
...nges would need to be made but it could be done.
overall dimensions are 12x12x2.5”, nice and compact.
thanks for looking-
jon-
thingiverse
free
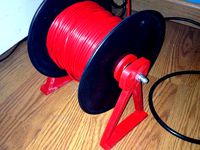
A simple filament spool holder by mscourch
...holder by mscourch
thingiverse
a simple spool holder using some 5/16" threaded rod, 5/16" bolts, and two 608 bearings.
thingiverse
free
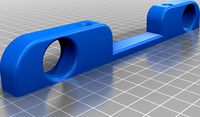
Filament spool storage brackets using 3/4" aluminum rod by Hyperload
...acket i whipped up to store my filament spools between two cabinets. i used 3/4" aluminum rods and place the spools on them.
grabcad
free

Paper towel holder
... a cylindrical steel counterweight. the "spinner" slides over the rod and is kept from lifting out by a fancy wing nut.
thingiverse
free

All aluminum Y axis based on thing 21638 by xtreme712
...ate except for the two rod mounts parts 5a and 5b which are 1/4" thick. the bushing holes and 8mm rod holders are press fit.
Rod
archibase_planet
free
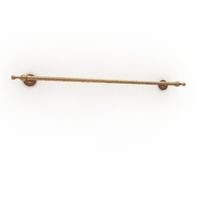
Rod
...rod
archibase planet
shank rod
so rod - 3d model (*.gsm+*.3ds) for interior 3d visualization.
archibase_planet
free
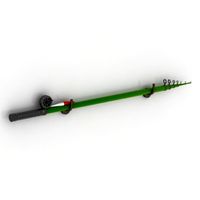
Spinning rod
...g rod
archibase planet
spinning rod spinning rod fishing-rod
spinning rod - 3d model (*.gsm+*.3ds) for interior 3d visualization.
3d_export
$5
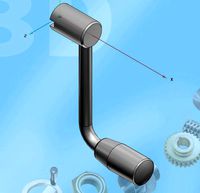
rod handle
...rod handle
3dexport
rod handle
3ddd
$1
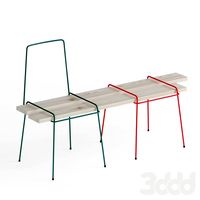
bench with rods
...bench with rods
3ddd
скамейка
bench with rods
3ddd
$1
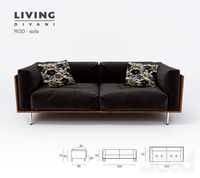
диван ROD
...диван rod
3ddd
rod , living divani
http://www.livingdivani.it/
3ddd
$1
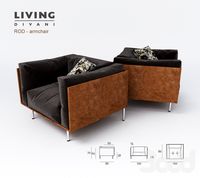
кресло ROD
...кресло rod
3ddd
rod , living divani
http://www.livingdivani.it/
design_connected
$18
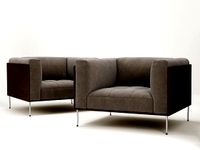
Rod Armchair
...rod armchair
designconnected
living divani rod armchair computer generated 3d model. designed by lissoni, piero.
archive3d
free
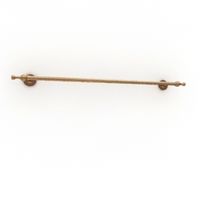
Rod 3D Model
...rod 3d model
archive3d
shank rod
so rod - 3d model (*.gsm+*.3ds) for interior 3d visualization.
turbosquid
$15
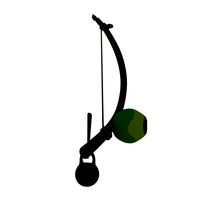
Fishing rod
...urbosquid
royalty free 3d model fishing rod for download as on turbosquid: 3d models for games, architecture, videos. (1684756)
archive3d
free
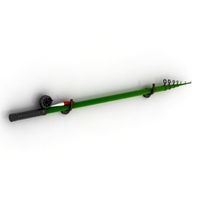
Spinning rod 3D Model
...d spinning rod fishing-rod
spinning rod - 3d model (*.gsm+*.3ds) for interior 3d visualization.
Concept
3d_export
$5
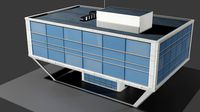
concept house
...concept house
3dexport
concept house blend.
turbosquid
$20
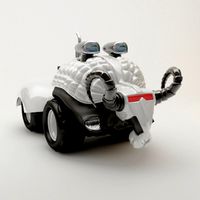
concept
... available on turbo squid, the world's leading provider of digital 3d models for visualization, films, television, and games.
turbosquid
free

concept
... available on turbo squid, the world's leading provider of digital 3d models for visualization, films, television, and games.
turbosquid
free

Concept
... available on turbo squid, the world's leading provider of digital 3d models for visualization, films, television, and games.
turbosquid
free

Concept
... available on turbo squid, the world's leading provider of digital 3d models for visualization, films, television, and games.
3ddd
$1

Bo concept
...bo concept
3ddd
boconcept , декоративный набор
bo concept
3d_ocean
$45

Dreamcar concept
...cept cars from the past.before i became 3d modeler i sketched a lot futuristic cars.when i want it to look more realistic,i st...
3d_ocean
$49

Buggy Concept
... poly massive outdoor robust vehicle
just a model of are own buggy concept vehicle. maybe you can make a beautiful renders of it!
3d_export
free

concept s ii
...concept s ii
3dexport
concept car
3d_export
free

concept s iii
...concept s iii
3dexport
concept car
Update
turbosquid
$5

orthographic room (updated)
...ee 3d model orthographic room (updated) for download as blend on turbosquid: 3d models for games, architecture, videos. (1375451)
turbosquid
$95

Romantic Bedroom - Updated
... available on turbo squid, the world's leading provider of digital 3d models for visualization, films, television, and games.
turbosquid
$39
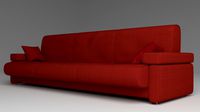
Sofa. Updated release
... available on turbo squid, the world's leading provider of digital 3d models for visualization, films, television, and games.
turbosquid
$15

Procedurally updating cartoon crystal
...l procedurally updating cartoon crystal for download as blend on turbosquid: 3d models for games, architecture, videos. (1525853)
3d_export
$5
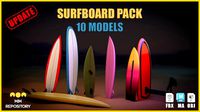
10 Surfboard s UPDATE
...10 surfboard s update
3dexport
3d_export
$10
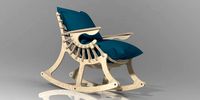
chair updated rocking
...chair updated rocking
3dexport
armchair renewed plywood 18 mm. for cnc machines. layout in the stp archive.
turbosquid
free

Marble Table Updated
...el marble table for download as 3ds, obj, fbx, blend, and dae on turbosquid: 3d models for games, architecture, videos. (1201300)
turbosquid
$35
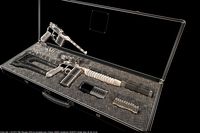
Mauser 1930the model is updated with the kits
... available on turbo squid, the world's leading provider of digital 3d models for visualization, films, television, and games.
turbosquid
$145
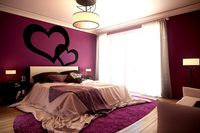
Contemporary Bedroom Collection Vol 1 - Updated
... available on turbo squid, the world's leading provider of digital 3d models for visualization, films, television, and games.
turbosquid
$16

B&B Mart Armchair MPRN (Updated)
...art armchair mprn (updated) for download as max, obj, and fbx on turbosquid: 3d models for games, architecture, videos. (1284355)
Holder
archibase_planet
free
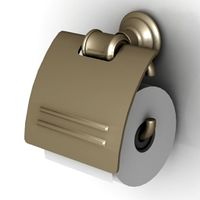
Holder
...holder
archibase planet
holder toilet paper holder
holder paper n070712 - 3d model (*.gsm+*.3ds) for interior 3d visualization.
archibase_planet
free
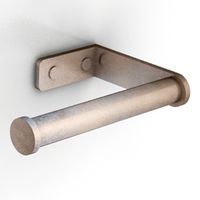
Holder
...e planet
holder rack toilet paper holder
holder toilet roll n240715 - 3d model (*.gsm+*.3ds+*.max) for interior 3d visualization.
archibase_planet
free
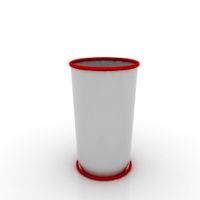
Holder
...holder
archibase planet
pen holder support prop
pen holder - 3d model for interior 3d visualization.
archibase_planet
free

Holder
...holder
archibase planet
pole post holder
сhurch cross pole holder - 3d model for interior 3d visualization.
archibase_planet
free
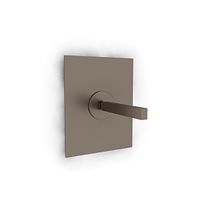
Holder
...holder
archibase planet
holder bathroom ware
shower holder - 3d model (*.gsm+*.3ds) for interior 3d visualization.
archibase_planet
free
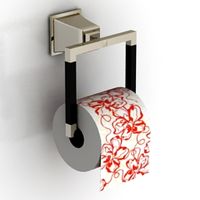
Holder
...oilet paper holder
holder paper devon&devon; time black n241113 - 3d model (*.gsm+*.3ds+*.max) for interior 3d visualization.
archibase_planet
free

Holder
...holder
archibase planet
holder hanger hanger for towel
holder 7 - 3d model (*.gsm+*.3ds) for interior 3d visualization.
archibase_planet
free
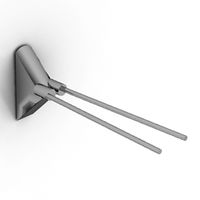
Holder
...holder
archibase planet
holder hanger hanger for towel
holder 3 - 3d model (*.gsm+*.3ds) for interior 3d visualization.
archibase_planet
free
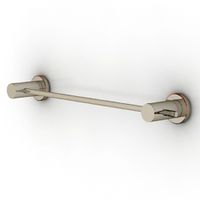
Holder
...holder
archibase planet
holder towel rack towel-horse
holder - 3d model (*.gsm+*.3ds) for interior 3d visualization.
archibase_planet
free
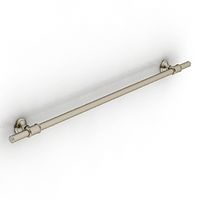
Holder
...lder
archibase planet
holder hanger hanger for towel
holder towel n250912 - 3d model (*.gsm+*.3ds) for interior 3d visualization.
6
3d_export
$18
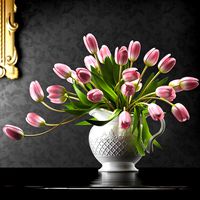
tulip 6
...tulip 6
3dexport
tulip 6
3d_export
$5
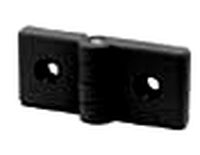
hinge 6
...hinge 6
3dexport
hinge 6
3ddd
$1
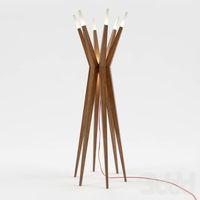
MASIERO / FLASHWOOD STL 6 + 6
...6
3ddd
masiero
торшер flashwood stl 6 + 6 фабрики masiero
http://www.masierogroup.com/c87_697/it/flashwood%20stl%206%20+%206.ashx
turbosquid
$110

Atmos Cannon 2000 6*6
...yalty free 3d model atmos cannon 2000 6*6 for download as skp on turbosquid: 3d models for games, architecture, videos. (1528591)
turbosquid
$1
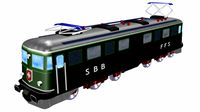
ae 6 6 electric locomotive
... free 3d model ae 6 6 electric locomotive for download as obj on turbosquid: 3d models for games, architecture, videos. (1707537)
turbosquid
$39
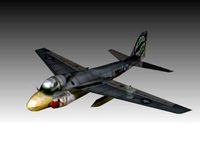
A-6
... available on turbo squid, the world's leading provider of digital 3d models for visualization, films, television, and games.
3ddd
$1
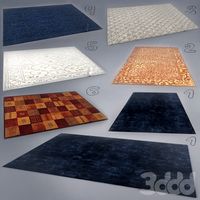
6 ковров
...6 ковров
3ddd
ковры , ковер
6 ковров
turbosquid
$12
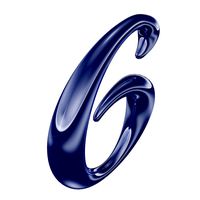
Calligraphic Digit 6 Number 6
...hic digit 6 number 6 for download as max, obj, fbx, and blend on turbosquid: 3d models for games, architecture, videos. (1389336)
turbosquid
$19
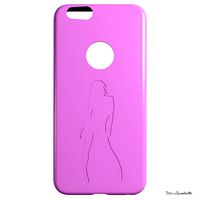
Case For Phone 6 Girl 6
... available on turbo squid, the world's leading provider of digital 3d models for visualization, films, television, and games.
turbosquid
$35
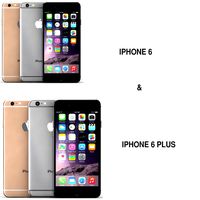
Iphone 6 & 6 Plus All
... available on turbo squid, the world's leading provider of digital 3d models for visualization, films, television, and games.
3
turbosquid
$10
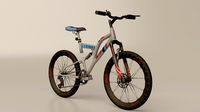
Mountain Bike 3 -3 of 3
...model mountain bike 3 (#3 of 3) for download as fbx and blend on turbosquid: 3d models for games, architecture, videos. (1438752)
turbosquid
$6

Rock 3-3
...urbosquid
royalty free 3d model rock 3-3 for download as obj on turbosquid: 3d models for games, architecture, videos. (1628065)
turbosquid
$29

Books 150 pieces 3-3-3
...books 150 pieces 3-3-3 for download as max, obj, fbx, and stl on turbosquid: 3d models for games, architecture, videos. (1384033)
turbosquid
$3
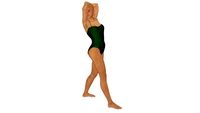
Genesis 3 Clothing 3
... available on turbo squid, the world's leading provider of digital 3d models for visualization, films, television, and games.
3d_export
$5

hinge 3
...hinge 3
3dexport
hinge 3
3ddd
$1
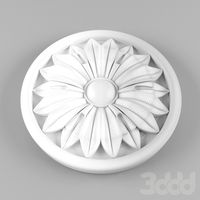
Розетка 3
...розетка 3
3ddd
розетка
розетка 3
turbosquid
$50
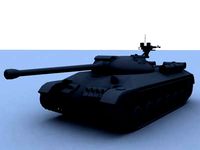
is-3
... available on turbo squid, the world's leading provider of digital 3d models for visualization, films, television, and games.
turbosquid
$10
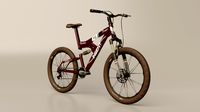
Mountain Bike 3 -2 of 3
...model mountain bike 3 (#2 of 3) for download as fbx and blend on turbosquid: 3d models for games, architecture, videos. (1438750)
turbosquid
$10
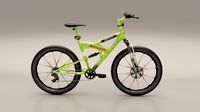
Mountain Bike 1 -3 of 3
...model mountain bike 1 (#3 of 3) for download as fbx and blend on turbosquid: 3d models for games, architecture, videos. (1438743)
3d_export
$5
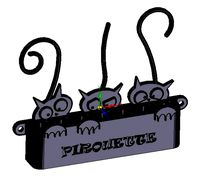
3 CATS
...3 cats
3dexport
3 cats pen holder