Thingiverse

Prusa Z axis, the best AND the simplest BUT ? by MKSA
by Thingiverse
Last crawled date: 3 years, 1 month ago
NOTE: This is superseded by https://www.thingiverse.com/thing:2594693 which gets rid of the crappy Geeetech sheet metal parts and the flimsy way it holds the bearing/nuts.
Owners of a Prusa Geeetech Al who have carried out all the mod I published here, mainly the Z axis, ( http://www.thingiverse.com/thing:1830451 ) are the proud owners of the best Prusa, no wobble, noise, vibration, fast, accurate AND simple.
See my other things (bearings, filament guide ...)
Here a video of the printing of a 2cm test cube in ABS at 180mm/s. Quality is still OK but I usually print at 100- 120mm/s to get good results as there is usually no need to go slower.
http://vid1053.photobucket.com/albums/s467/MKSA/20170113_180807_zpsobkt9o31.mp4
I was wondering if I could make the Z axis even simpler by getting rid of the Z smooth rods.
Yes indeed it is possible although I reckon a few issues and limitations in the case of my Prusa.
I was quite surprised by the quality of the TR8 screws, straightness and surface finish and I was wondering if I could use them not only to move but to guide the X carriage and therefore remove the Z smooth rods (OK,not super high quality but suitable for simple, low accuracy FFM 3D printers depositing blobs of molten plastic).
So I removed the Geeetech Al Prusa smooth rods and guides, replaced the TR8 by longer ones, added homemade IGUS bearings in the lower plates, replaced the brass nuts by a housing containing the brass nut at the bottom, an IGUS bearing at the top.
Does it work ? Yes indeed BUT:
The section of the TR8 core is about 6mm thus quite thin. Not much radial forces applied to them, static force due to the gravity center of the X assembly not in the plane formed by the two TR8 plus dynamic force due to the accel/decel X carriage.
Note the moving mass in my case is about 260g. So it is fine. The original MK8 plus carriage (close to 600g) would have certainly been an issue.
The real issue though is that my Igus bearings are a very close fit and if the TR8 are not perfectly aligned, they will require far more torque. The Prusa frame makes it impossible to adjust and keep this //. I had to increase the current close to the motor limit.
I could have devised some adjustment mechanism for // but not worth it.
I also tried to replace the brass nut and bushings by two Igus Tr8 nuts I made. Works too, additional benefit, no backlash and not the slightest play either but again need far more torque.
Now, if this is not really suitable for a Prusa, it shows that for an other frame, a sturdy box frame, one could use three TR8 or better TR10 (to be scaled to the machine size), to design a simple Z table for a CoreXY, H bot ... machine.The key is proper // of the TR8s to avoid excessive friction and binding. This requires mechanisms to be able to adjust and keep the TR8s//. Use cast iron, granite ? Just kidding ! The reward would be a simple no play, no backlash, vibration free system. No need for messy lubrication too !
The ABS and PETG test parts have been made at 100mm/s 0.2mm layer. (nozzle .4)
PS: Ball lead screws would of course even be better but overkill for such simple machines. unless you can get them for cheap ! They would even "straighten" the Prusa frame without binding :)
Owners of a Prusa Geeetech Al who have carried out all the mod I published here, mainly the Z axis, ( http://www.thingiverse.com/thing:1830451 ) are the proud owners of the best Prusa, no wobble, noise, vibration, fast, accurate AND simple.
See my other things (bearings, filament guide ...)
Here a video of the printing of a 2cm test cube in ABS at 180mm/s. Quality is still OK but I usually print at 100- 120mm/s to get good results as there is usually no need to go slower.
http://vid1053.photobucket.com/albums/s467/MKSA/20170113_180807_zpsobkt9o31.mp4
I was wondering if I could make the Z axis even simpler by getting rid of the Z smooth rods.
Yes indeed it is possible although I reckon a few issues and limitations in the case of my Prusa.
I was quite surprised by the quality of the TR8 screws, straightness and surface finish and I was wondering if I could use them not only to move but to guide the X carriage and therefore remove the Z smooth rods (OK,not super high quality but suitable for simple, low accuracy FFM 3D printers depositing blobs of molten plastic).
So I removed the Geeetech Al Prusa smooth rods and guides, replaced the TR8 by longer ones, added homemade IGUS bearings in the lower plates, replaced the brass nuts by a housing containing the brass nut at the bottom, an IGUS bearing at the top.
Does it work ? Yes indeed BUT:
The section of the TR8 core is about 6mm thus quite thin. Not much radial forces applied to them, static force due to the gravity center of the X assembly not in the plane formed by the two TR8 plus dynamic force due to the accel/decel X carriage.
Note the moving mass in my case is about 260g. So it is fine. The original MK8 plus carriage (close to 600g) would have certainly been an issue.
The real issue though is that my Igus bearings are a very close fit and if the TR8 are not perfectly aligned, they will require far more torque. The Prusa frame makes it impossible to adjust and keep this //. I had to increase the current close to the motor limit.
I could have devised some adjustment mechanism for // but not worth it.
I also tried to replace the brass nut and bushings by two Igus Tr8 nuts I made. Works too, additional benefit, no backlash and not the slightest play either but again need far more torque.
Now, if this is not really suitable for a Prusa, it shows that for an other frame, a sturdy box frame, one could use three TR8 or better TR10 (to be scaled to the machine size), to design a simple Z table for a CoreXY, H bot ... machine.The key is proper // of the TR8s to avoid excessive friction and binding. This requires mechanisms to be able to adjust and keep the TR8s//. Use cast iron, granite ? Just kidding ! The reward would be a simple no play, no backlash, vibration free system. No need for messy lubrication too !
The ABS and PETG test parts have been made at 100mm/s 0.2mm layer. (nozzle .4)
PS: Ball lead screws would of course even be better but overkill for such simple machines. unless you can get them for cheap ! They would even "straighten" the Prusa frame without binding :)
Similar models
thingiverse
free
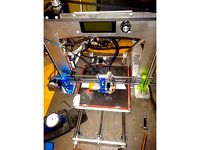
Prusa Z axis, the best AND the simplest ! by MKSA
...furthermore to implement this requires knowledge and skills that make these superfluous. qualified people i am ok to help though.
thingiverse
free
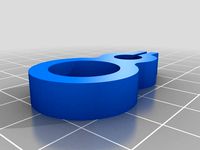
Prusa i3 Wood frame z-rod bearing holder by gggkkk
...se
this is a simple z-axis rod holder for a 625 bearing. it works on the wood frame.
z-rod: 5mm
bearing: 625
z-axis shaft: 8mm
grabcad
free

Prusa X axis end brackets with flanged nut for TR8.
...ified to use tr8 leadscrews. also i don't like cantilever supported idle bearings so i added a support for the idle bearing.
thingiverse
free

Improved Geeetech Aluminum Anti-Wobble Bracket by B-Cup
... a tower to place supports on, so do not forget to add supports in between!
it uses the original brass nuts for the z axis rods.
thingiverse
free
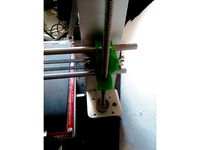
Prusa Z axis, so many problems yet one simpe solution, simplified ! by MKSA
...inear bearing or try with tr10. no point publishing something that is not fully satisfactory. just that i have many things to do.
thingiverse
free

X-axis carriage for linear stepping motor. by jspark
... linear stepping motor when i buy it.
there is a backlash, but not big.
i wonder how the backlash would affect the print results.
thingiverse
free
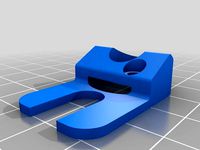
Anti wobble Z Axis for Geeetech I3 Pro B by Aerotronic
...arriages.
if you have the geeetech prusa i3 pro b acrylic, that thing fits directly.
you'll have to print 2 parts, of course
thingiverse
free
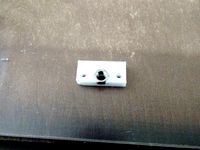
Anti-backlash Z-Axis nut trap by gmelenka
...art my z-axis homing and positioning has become extremely reliable.
this design is for a m5 nut that comes with the prusa i3v.
thingiverse
free
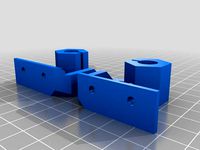
Prusa MK2 Clone - Z Top Axis with bearing 688ZZ for TR8 300mm (with support) by invitro
...d. for x axis, you can use https://www.thingiverse.com/thing:2415037
22 july 2017
bearing holes cap is added, to avoid from dust.
thingiverse
free
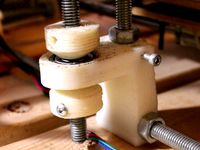
Prusa Plastic Z Lock by LordM
...tle nut inside the pocket and fix your bars without having nuts again. i had problems of z axis jamming before this modification.
Mksa
thingiverse
free
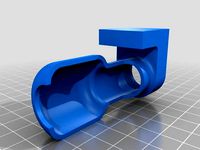
Dremel universal holder by MKSA
...ith a small c clamp. cut or stop the print if you want partial or no protection.
100% infill makes it strong enough without bulk.
thingiverse
free

Sako 300 Win magazine follower by MKSA
... smooth where required for smooth operation.
print in red if you have the filament for. will help see when the magazine is empty.
thingiverse
free
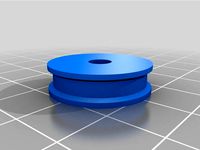
Torque measurement by MKSA
...t your motot can deliver and adjust its current accordingly.
ok, its static, keep that in mind when adjusting your motor current.
thingiverse
free
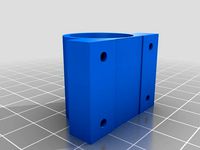
Silentblock SC8UU by MKSA
...d is not comparable to what i am now getting. biggest gain due to replacing the z lead screws and one motor. see my other things.
thingiverse
free
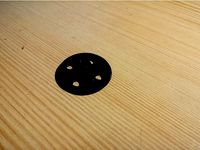
NO SCREW, Hot glue hook by MKSA
...lue gun put a big blob of glue on them and immediately apply to the wall. the glue will go through the 4 holes securing the bond.
thingiverse
free
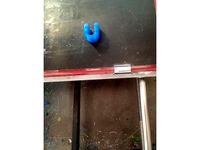
Micro switch bracket for smooth rod. by MKSA
...se petg or abs as it is strong and won't break.
suitable for x and y, for z you need something that provides fine adjustment.
thingiverse
free
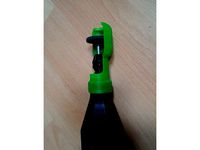
Dremel protection by MKSA
...t publishing real working things even remixes i won't have to criticize ? some jerks even have nothing to show, just insults.
thingiverse
free

GT2 Belt tension adjustement by MKSA
...se crappy ones made out of acrylic sheets watch out that it may bend and even break so you now have an excuse to get rid of it :)
thingiverse
free

Simple glass plate holder by MKSA
...p edges that can lead to injury to the eyes or make you bleed ! too much bleeding will cause death. proceed at your own risk. :)
thingiverse
free
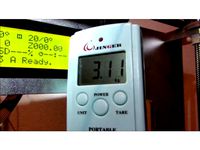
Extruder push measurement. by MKSA
...because of thinkverse, not used.
plenty more things to write about but. anyone knowledgeable can fill in the blanks or comment :)
Simplest
3d_export
$5

Cyber Sword
...cyber sword 3dexport the simplest low-poly sword that you can use in your...
3d_export
$24

Low Poly Farmhouse and Environmental Pack Low-pol
...performance gain. although it can be the fastest and simplest solution for your architectural and promotional projects, you can...
3d_export
$62
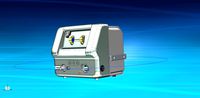
ventilator assembly
...lungs is called breathing, or, more formally, ventilation. the simplest mechanical device we could devise to assist a person’s...
3d_export
$30
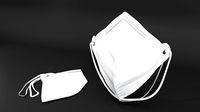
protection mask
...mask and the tapes are included. this is the simplest way to animate and render the mask.<br>8192x 8192px textures...
3d_export
$30

protection mask
...mask and the tapes are included. this is the simplest way to animate and render the mask.<br>8192x 8192px textures...
3d_export
$119
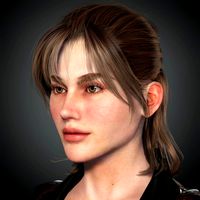
naina female rigged character
...and evee, some with mental ray. mental ray: the simplest lighting scheme is used to render the preview images...
thingiverse
free
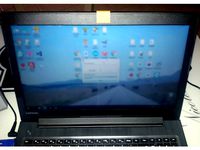
Simplest laptop webcam cover by haxl
...simplest laptop webcam cover by haxl
thingiverse
simplest camera cover for laptop
thingiverse
free

Simplest Xbox Controller Holder by xlsergval
...simplest xbox controller holder by xlsergval
thingiverse
updated! simplest xbox 360 controller holder
thingiverse
free

The simplest filament dust filter by diamened
...ment dust filter by diamened
thingiverse
the simplest filament dust filter ever. just add a piece of foam.
freecad file included
thingiverse
free

The Simplest Headphone Wrapper by Pentland_Designs
...ilosophy, if someone can't remember how to use it after being shown once, it is too complicated.
https://youtu.be/wnr0d2nclec
Prusa
turbosquid
$2
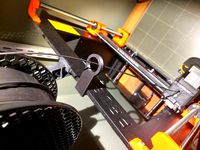
Frame Filament Guide Clip-On for Prusa Mk3
...rame filament guide clip-on for prusa mk3 for download as stl on turbosquid: 3d models for games, architecture, videos. (1634730)
3d_export
free
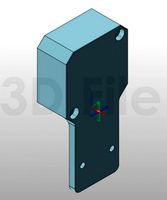
prusa i3 mk3s laser mount for opt lasers
...to learn more about the blue laser technology that conceived the cutting and engraving laser heads from opt lasers, please visit:
turbosquid
free
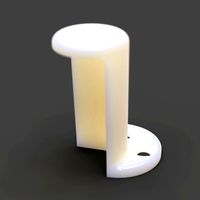
Prusa small printer adapter holder
...er for download as ipt, skp, dwg, dxf, fbx, ige, obj, and stl on turbosquid: 3d models for games, architecture, videos. (1642936)
3d_export
$30
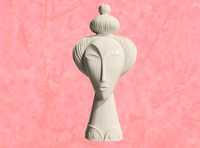
geisha by jonathan adler
...** i did a 3d printing test in the prusa software, you can find it among the attached images.<br>exchange:<br>.blend...
thingiverse
free
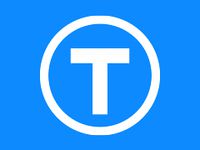
Prusa without Prusa (rc2) by madless
...prusa without prusa (rc2) by madless
thingiverse
just the main part of prusa rc2 faceshield, without writing.
enjoy :)
thingiverse
free
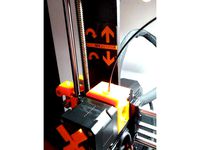
Prusa by acejbc
...prusa by acejbc
thingiverse
prusa knob info
m3 8mm screw
thingiverse
free
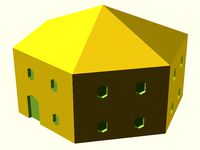
Prusa house
...prusa house
thingiverse
how prusa house could look like...
thingiverse
free
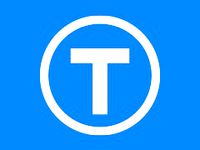
Prusa Mk2 "Fake Prusa" LCD cover by anraf1001
...r by anraf1001
thingiverse
version of prusa's lcd cover with "fake prusa" instead of "original prusa"
thingiverse
free
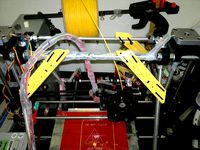
Prusa stabilizator by gutiueugen
...prusa stabilizator by gutiueugen
thingiverse
prusa stabilizator
thingiverse
free
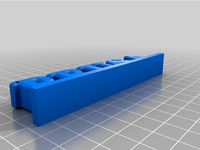
Keychain Prusa by rbarbalho
...keychain prusa by rbarbalho
thingiverse
keychain with text prusa.
Axis
3ddd
$1
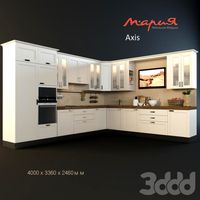
Мария Axis
...
3ddd
кухня , классическая , axis
модель кухни.
3d_export
$22
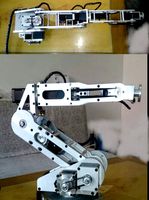
Axis robot 6-axis robotic arm
...ing parts drawings, standard parts purchased parts list, can be produced directly according to the drawings, welcome to download!
3ddd
free
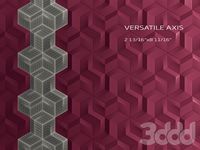
Versatile Axis
...ddd
nexus , плитка
http://bvtileandstone.com/ceramic-porcelain/versatile-axis/
3d_export
$19
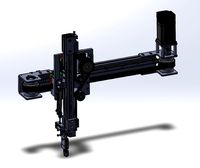
robot 2 axis
...robot 2 axis
3dexport
robot 2 axis
turbosquid
$40
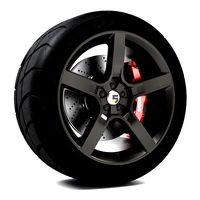
Axis R5F
... available on turbo squid, the world's leading provider of digital 3d models for visualization, films, television, and games.
turbosquid
$40
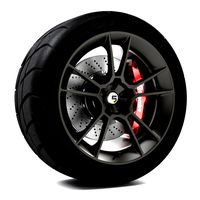
Axis S5F
... available on turbo squid, the world's leading provider of digital 3d models for visualization, films, television, and games.
turbosquid
$30
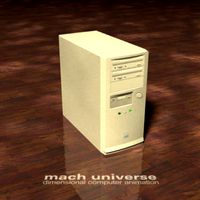
Axis Athlon
... available on turbo squid, the world's leading provider of digital 3d models for visualization, films, television, and games.
turbosquid
$10
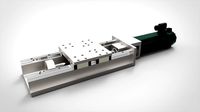
Linear Axis
... available on turbo squid, the world's leading provider of digital 3d models for visualization, films, television, and games.
3d_export
$15
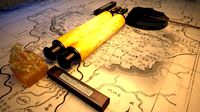
drawing axis
...drawing axis
3dexport
simple rendering of the scene file
3ddd
$1
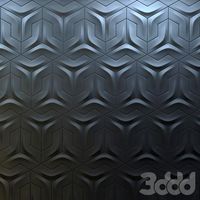
versatile axis ARC
...versatile axis arc
3ddd
versatile , плитка
versatile axis arc red dot design award
Z
3d_export
$5
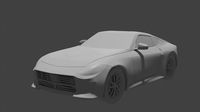
nissan z
...nissan z
3dexport
nissan z
3ddd
$1
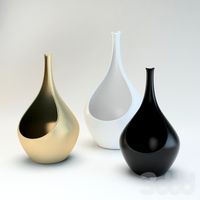
Vase Z
...vase z
3ddd
vase z
3ddd
$1
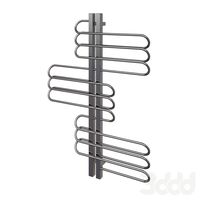
полотенцесушить Z
...полотенцесушить z
3ddd
полотенцесушитель
полотенцесушить z
design_connected
free

Z-Chair
...z-chair
designconnected
free 3d model of z-chair designed by karman, aleksei.
design_connected
$11
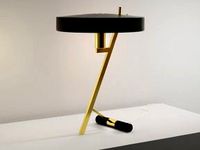
Z Lamp
...z lamp
designconnected
phillips z lamp computer generated 3d model. designed by kalff, louis.
3d_export
$5
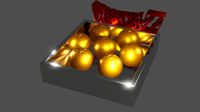
Dragon balls z
...dragon balls z
3dexport
dragon ball z
turbosquid
$20
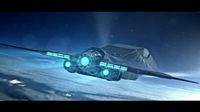
Fighter Z
...
turbosquid
royalty free 3d model fighter z for download as on turbosquid: 3d models for games, architecture, videos. (1292563)
turbosquid
$9
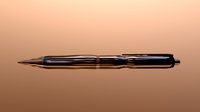
Pen Z
...pen z
turbosquid
free 3d model pen z for download as obj on turbosquid: 3d models for games, architecture, videos. (1686775)
turbosquid
free
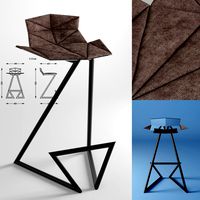
z chair
...z chair
turbosquid
free 3d model z chair for download as max on turbosquid: 3d models for games, architecture, videos. (1410230)
turbosquid
$5
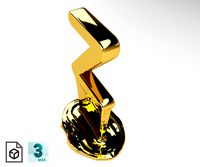
Letter Z
...urbosquid
royalty free 3d model letter z for download as max on turbosquid: 3d models for games, architecture, videos. (1408540)
Best
3ddd
$1
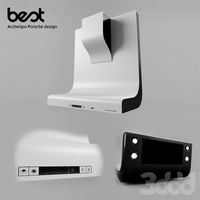
Best
...best
3ddd
best , вытяжка
вытяжка фирмы best, выполнена в размерах, текстуры в архиве
turbosquid
$49

BEST
...best
turbosquid
royalty free 3d model best for download as on turbosquid: 3d models for games, architecture, videos. (1153993)
3ddd
free
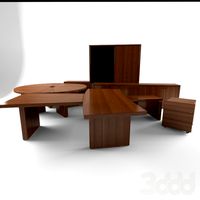
Best
... стол , шкаф
моделил для себя, делюсь со всеми, делал по фото и чертежам из журнала.
3ddd
free
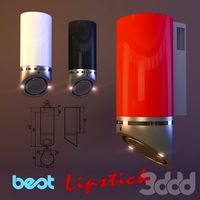
BEST / Lipstick
.... 7840 полигонов.
wall mounted range hood best lipstick, best platinum series. 7480 polygons.
file: max 2010, 2012; fbx; obj.
3ddd
$1
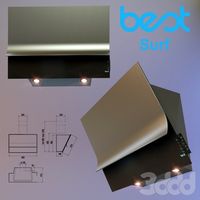
Best / Surf
...тяжка пристенная best surf.
5030 полигонов.
wall mounted range hood best surf.
5030 polygons.
file: max 2010, 2012; fbx; obj.
3ddd
$1
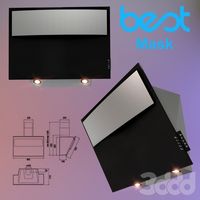
Best / Mask
...тяжка пристенная best mask.
1720 полигонов.
wall mounted range hood best mask.
1720 polygons.
file: max 2010, 2012; fbx; obj.
3ddd
$1
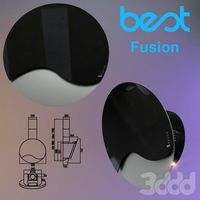
Best. Fusion
...а пристенная best fusion.
5930 полигонов.
wall mounted range hood best fusion.
5930 polygons.
file: max 2010, 2012; fbx; obj.
3ddd
$1
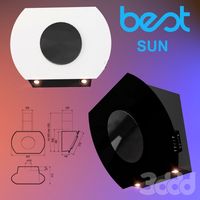
Best / Sun
...вытяжка пристенная best sun.
1900 полигонов.
wall mounted range hood best sun.
1900 polygons.
file: max 2010, 2012; fbx; obj.
3ddd
$1
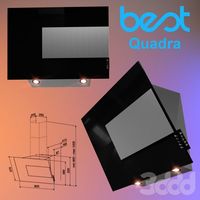
Best / Quadra
...а пристенная best quadra.
1610 полигонов.
wall mounted range hood best quadra.
1610 polygons.
file: max 2010, 2012; fbx; obj.
3ddd
free
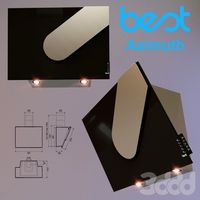
Best / Azimuth
...пристенная best azimuth.
5050 полигонов.
wall mounted range hood best azimuth.
5050 polygons.
file: max 2010, 2012; fbx; obj.