Thingiverse
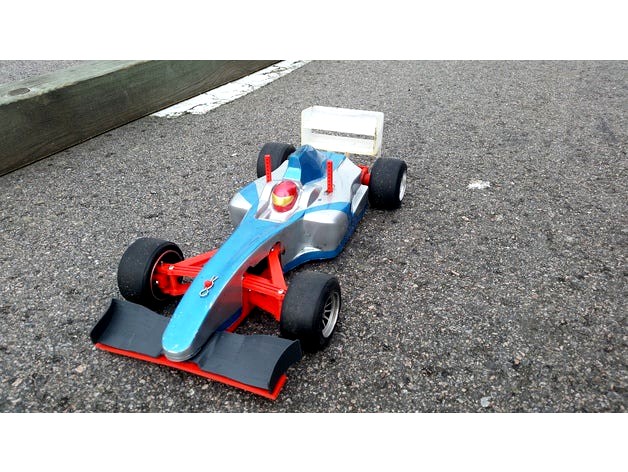
OpenRC HPD F1 Lexan Body version by condac
by Thingiverse
Last crawled date: 3 years ago
This car is designed to meet race regulation in real RC F1 races. And it have the performance to keep up with the real deal! Video of the fastest lap from a race: https://youtu.be/CIAOM8PESa4
This is a version of the HPD F1 to use a Lexan Body. Also the front and middle is redesigned. The front is stronger and middle part takes the battery 90 deg rotated.
It is compatible with the rear cradle but there is also a cradle that you build from several parts included, it is not as strong but easier to change individual parts and less waste of plastic when things break. The rear cradle is compatible with the original HPD version but there is also a wide version for this wider body and side_stabs are 2 different versions depending on combinations.
The car was designed to be printed in Nylon like 910 that is slightly rigid. But my prototype I made with prima value PLA did not break so it is very strong with PLA apart from the wings.
I strongly recommend to print the front wing in Bridge Nylon or something with similar flex. Rear wing I have used Bridge Nylon and it flex good and never breaks.
If you want to go cheap or cant find springs, I have used the spring from a ball pen and cut it to shorter length for front. And for rear you can ignore the side springs completely if you just want to go racing and print the plastic main rear spring that is included.
All parts is made in OpenSCAD and source is at github: https://github.com/condac/hpdf1_lexan
Talk with us on Google+ https://plus.google.com/u/0/communities/117625327650679845498
Or in the OpenR/C Facebook site https://www.facebook.com/groups/OpenRCProject/
2019 Experience update:
Materials!
Not as important as you might think. First time making this car, print all in a PLA to get started, it is cheap and easy to make replacement to things that break. When you are a beginner and learn to drive strong parts will not save you because a crash is a crash. But getting out there and start to drive and make the car work in the first place is more important than trying to figure out print settings and finding plastics.
All parts are printed in 100% infill and 4 perimeters.
Looking at my car now that have been through hell and back there is 3 parts that are original from the first prototype the rest have broken in some crash. And some parts have worn out before breaking! But there are replacement parts that have never failed also and that is what I want to share here what type of plastic that you use for upgrades.
PLA
My main car is still mainly PLA. Different PLA brands are better than other. I mainly use PrimaSelect, PrimaValue and ClasOhlson brand PLA (in Sweden) They have good toughness.
Nylon
The first alternative plastic to get is Bridge Nylon. Generic nylon might work but are often stiffer and break and do not flex in crashes (but still better than any PLA). Also keeping the parts wet and moist after they are printed makes them softer and tougher. Parts that are good in nylon:
Rear wing
Side_stab2
cradle_bottomPlate_wide
plastic_rearspring_10
And some parts that are better in nylon than PLA but will work better in other upgrades later:
Frontwing
cradle_rightBulkhead ( a bit soft and flexing in nylon but if PLA melts from motor temperature getting to hot its better than nothing)
Any temperature resistant plastic
The motor gets hot. During the hottest possible day one should tune the motor to never go over 80c/176f. I have around 55c on normal days (20c air temp) outdoor and then PLA can work. But on hotter days or on indoor tracks where the motor is working harder PLA is not working.
I have tried PETG ABS ASA as they should withstand the temperatures. But they all fail in crashes and are the worst compared to PLA in a crash.
I have also tried a generic Nylon and alloy 910 as it is a bit stiffer than Bridge nylon, but over some time the nylon will warp from the weight of the motor.
When driving indoors i accept the warp from the nylon and use it anyway. Outdoors I still search for a good material, The flex from nylon outdoors make the motor grind hard in the asfalt so not ideal. But as for now the nylon part is almost new and still not warped so it works.
PP (PolyPropylene)
The king of car crashes. Super soft and flexible but awesome toughness. I use this on the frontwing.stl. My first test with this plastic is still on my car 1 year since I made it. It have worn down to more than half its thickness on the tips that sometimes touch the ground and I have made countless front impacts and it just deforms slightly and i bend it back and drive along.
Front wing
Front Arms
There is one part that break that I have experimented with trying to make it better and that is the front arms. But believe it or not, they are extremely good in PLA. When I designed this car I made it so the front arms do not bend in a crash but they compress and send the force into the chassis, and this have worked well. Also they are printed with the plastic grains in the most optimal position. But having a front wing that is catching most of the crash is playing a bigger role.
But I have of course tried it in the indestructible PP and Bridge Nylon. But this seemed like it just moved the breaking part inward and the nose chassis break instead. So at some point something must break so it is much more easy to replace the front arms than the chassis. And having a lot of spare front arms are cheap compared to bigger parts.
But i have had front arms in PLA that have worn down the holes for the pins so the wheel wobble and I have to replace because of wear before they have broken in a crash, that might sum up how well they work.
Conclusion
When racing with this car the most common failure that have caused me to retire the car is impacts on the rear wheels. Breaking side_stabs or the cradle_bottomplate or cradle in general.
Parts that have survived over expectations are the main chassis and nose chassis. Main chassis have been worn down from toughing the ground and needed replacement because of the plastic got to thin. And the very high poles in the nose i have made so you can repair with a screw from underneath but i have never used a screw because it have not broken. The forces are just not there to bend them.
This is a version of the HPD F1 to use a Lexan Body. Also the front and middle is redesigned. The front is stronger and middle part takes the battery 90 deg rotated.
It is compatible with the rear cradle but there is also a cradle that you build from several parts included, it is not as strong but easier to change individual parts and less waste of plastic when things break. The rear cradle is compatible with the original HPD version but there is also a wide version for this wider body and side_stabs are 2 different versions depending on combinations.
The car was designed to be printed in Nylon like 910 that is slightly rigid. But my prototype I made with prima value PLA did not break so it is very strong with PLA apart from the wings.
I strongly recommend to print the front wing in Bridge Nylon or something with similar flex. Rear wing I have used Bridge Nylon and it flex good and never breaks.
If you want to go cheap or cant find springs, I have used the spring from a ball pen and cut it to shorter length for front. And for rear you can ignore the side springs completely if you just want to go racing and print the plastic main rear spring that is included.
All parts is made in OpenSCAD and source is at github: https://github.com/condac/hpdf1_lexan
Talk with us on Google+ https://plus.google.com/u/0/communities/117625327650679845498
Or in the OpenR/C Facebook site https://www.facebook.com/groups/OpenRCProject/
2019 Experience update:
Materials!
Not as important as you might think. First time making this car, print all in a PLA to get started, it is cheap and easy to make replacement to things that break. When you are a beginner and learn to drive strong parts will not save you because a crash is a crash. But getting out there and start to drive and make the car work in the first place is more important than trying to figure out print settings and finding plastics.
All parts are printed in 100% infill and 4 perimeters.
Looking at my car now that have been through hell and back there is 3 parts that are original from the first prototype the rest have broken in some crash. And some parts have worn out before breaking! But there are replacement parts that have never failed also and that is what I want to share here what type of plastic that you use for upgrades.
PLA
My main car is still mainly PLA. Different PLA brands are better than other. I mainly use PrimaSelect, PrimaValue and ClasOhlson brand PLA (in Sweden) They have good toughness.
Nylon
The first alternative plastic to get is Bridge Nylon. Generic nylon might work but are often stiffer and break and do not flex in crashes (but still better than any PLA). Also keeping the parts wet and moist after they are printed makes them softer and tougher. Parts that are good in nylon:
Rear wing
Side_stab2
cradle_bottomPlate_wide
plastic_rearspring_10
And some parts that are better in nylon than PLA but will work better in other upgrades later:
Frontwing
cradle_rightBulkhead ( a bit soft and flexing in nylon but if PLA melts from motor temperature getting to hot its better than nothing)
Any temperature resistant plastic
The motor gets hot. During the hottest possible day one should tune the motor to never go over 80c/176f. I have around 55c on normal days (20c air temp) outdoor and then PLA can work. But on hotter days or on indoor tracks where the motor is working harder PLA is not working.
I have tried PETG ABS ASA as they should withstand the temperatures. But they all fail in crashes and are the worst compared to PLA in a crash.
I have also tried a generic Nylon and alloy 910 as it is a bit stiffer than Bridge nylon, but over some time the nylon will warp from the weight of the motor.
When driving indoors i accept the warp from the nylon and use it anyway. Outdoors I still search for a good material, The flex from nylon outdoors make the motor grind hard in the asfalt so not ideal. But as for now the nylon part is almost new and still not warped so it works.
PP (PolyPropylene)
The king of car crashes. Super soft and flexible but awesome toughness. I use this on the frontwing.stl. My first test with this plastic is still on my car 1 year since I made it. It have worn down to more than half its thickness on the tips that sometimes touch the ground and I have made countless front impacts and it just deforms slightly and i bend it back and drive along.
Front wing
Front Arms
There is one part that break that I have experimented with trying to make it better and that is the front arms. But believe it or not, they are extremely good in PLA. When I designed this car I made it so the front arms do not bend in a crash but they compress and send the force into the chassis, and this have worked well. Also they are printed with the plastic grains in the most optimal position. But having a front wing that is catching most of the crash is playing a bigger role.
But I have of course tried it in the indestructible PP and Bridge Nylon. But this seemed like it just moved the breaking part inward and the nose chassis break instead. So at some point something must break so it is much more easy to replace the front arms than the chassis. And having a lot of spare front arms are cheap compared to bigger parts.
But i have had front arms in PLA that have worn down the holes for the pins so the wheel wobble and I have to replace because of wear before they have broken in a crash, that might sum up how well they work.
Conclusion
When racing with this car the most common failure that have caused me to retire the car is impacts on the rear wheels. Breaking side_stabs or the cradle_bottomplate or cradle in general.
Parts that have survived over expectations are the main chassis and nose chassis. Main chassis have been worn down from toughing the ground and needed replacement because of the plastic got to thin. And the very high poles in the nose i have made so you can repair with a screw from underneath but i have never used a screw because it have not broken. The forces are just not there to bend them.
Similar models
thingiverse
free
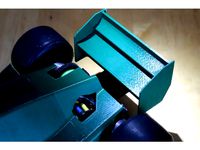
Crash resistant rear wing to F1 cars by KentAsplund
...nd
thingiverse
a crash resistant rear wing for 1:10 scale f1 r/c cars.
fits the hpd f1: http://www.thingiverse.com/thing:1718069
thingiverse
free

Option Cradle for HPD F1 V2 by KentAsplund
...option cradle for hpd f1 v2 by kentasplund
thingiverse
this cradle is allowing usage of motors with rear facing connectors.
thingiverse
free
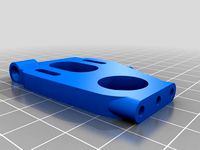
HPD F1 Multi-part cradle by condac
...ade in openscad and source code is included in the same project as my other lexan body car. https://github.com/condac/hpdf1_lexan
thingiverse
free
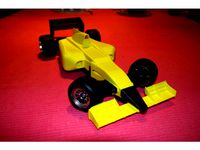
HPD F1 V2.0 A competition grade R/C car by KentAsplund
...r mount is now on a separate plate which makes it easier to adapt to different length dampers.
nose cone is now screwed on place.
thingiverse
free
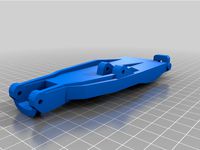
Redcat Racing Shredder Front Arm by billsmith221
...rm at 30 degree angle and with a 100% infill to get the strongest prints.
i will be posting the rear arms after i break them lol
thingiverse
free
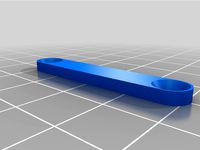
Team Corally Chassis Brace by rivado
...han without! :d
team corally - chassis brace stiffener:
front: c-00180-254
rear: c-00180-253
use m3x8 flex flat head cap screws.
thingiverse
free

Front Wing arm shaft for 144001 (144001-1267 - Part A) by AdrienB69
...9;m trying to print it with a 30° angle to make it stronger. i'll tell if it works.
otherwise i will try using petg or abs...
thingiverse
free
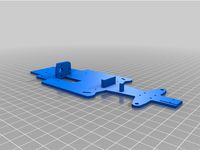
Open RC F1 - Modified Chassis and front wing (allows fastening together) by rose840
...://www.thingiverse.com/thing:2816828
thanks to skissografen
and of course thanks to daniel norée for making any of this possible.
thingiverse
free
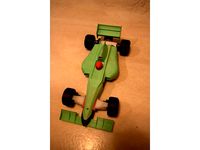
HPD F1 V2.1 A competition grade R/C car by KentAsplund
...ar which is good on slippery tracks (obviously) but also on super high grip circuits where the smallest slide might cause a roll.
thingiverse
free
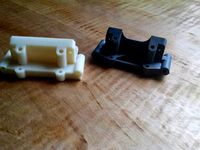
Traxxas bulkhead by waterfan2
...nd the flat plate of the chassis attaches to the angled part. i've had a few break in the past from rough crashes and stuff.
Condac
thingiverse
free

UntitledGame Card Holder - Flipped by condac
...untitledgame card holder - flipped by condac
thingiverse
same as my other cardholder but with the connectors flipped.
thingiverse
free

Game card holder by condac
...ade with the same dimentions as the previous blender project.
also avaible on github: https://github.com/condac/gamecardholder
thingiverse
free
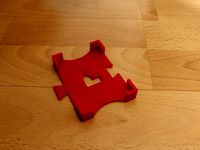
Customizable Game Card Holder by condac
... by condac
thingiverse
customizable version of my settlers of catan gamecard holder. make it the size of any game card you have.
thingiverse
free
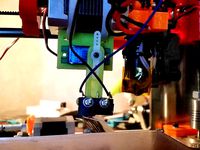
Ghetto servo mount (micro servo) by condac
...vo mount (micro servo) by condac
thingiverse
servo mount for micro servo to use cable tie to mount a micro servo where you want.
thingiverse
free

Customizable tray Fixed SCAD code by condac
...en i used openscad localy. the reason was the rounded box imported from some library. i fixed by making my own roundedbox module.
thingiverse
free
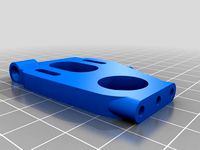
HPD F1 Multi-part cradle by condac
...ade in openscad and source code is included in the same project as my other lexan body car. https://github.com/condac/hpdf1_lexan
thingiverse
free

OpenRC Tractor Printed steering linkage by condac
...arts when you can make it yourself. sure it will have a lot of play and getting tight at certain angles, but it is a toy tractor!
thingiverse
free

Expandable Throttle Joystick by condac
...e soon. everything is still under development.
use linear pots!
b50k ohm linear taper potentiometer pot 17mm shaft with dust seal
thingiverse
free

Open Source key chain logo by condac
...o make som guesses so it might not be exactly the same. but i have included my openscad file for you to make your own adjustment.
thingiverse
free
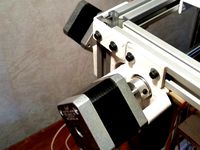
Direct motor mount for Ultimaker 2 Aluminium clone by condac
...ce maintenance to re-tighten the motors.
big thanks to jasonatepaint for the original great design of this printer. i love it!
Hpd
thingiverse
free

(Deprecated) HPD F1 V1.0 a competition grade F1 R/C by KentAsplund
... 1 of the car and has been superseded by hpd f1 v2.0.
discussion forum: https://plus.google.com/communities/117625327650679845498
thingiverse
free

Option Cradle for HPD F1 V2 by KentAsplund
...option cradle for hpd f1 v2 by kentasplund
thingiverse
this cradle is allowing usage of motors with rear facing connectors.
thingiverse
free
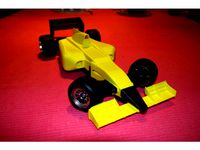
HPD F1 V2.0 A competition grade R/C car by KentAsplund
...r mount is now on a separate plate which makes it easier to adapt to different length dampers.
nose cone is now screwed on place.
thingiverse
free
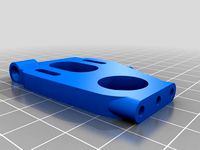
HPD F1 Multi-part cradle by condac
...ade in openscad and source code is included in the same project as my other lexan body car. https://github.com/condac/hpdf1_lexan
thingiverse
free
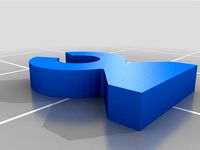
Spacer clips for F1 by KentAsplund
...thingiverse spacer clips to adjust front ride height on hpd f1 and other f1...
thingiverse
free

F1 Friction Damper by rhoagland
...rhoagland thingiverse friction damper for use on openrc and hpd f1 cars. mounting holes are designed for m3...
thingiverse
free
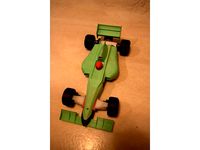
HPD F1 V2.1 A competition grade R/C car by KentAsplund
...ar which is good on slippery tracks (obviously) but also on super high grip circuits where the smallest slide might cause a roll.
thingiverse
free
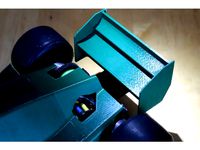
Crash resistant rear wing to F1 cars by KentAsplund
...wing for 1:10 scale f1 r/c cars. fits the hpd f1:...
thingiverse
free
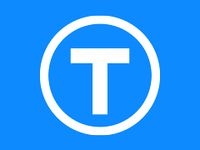
Roland PDS-10 Adapter for Camera Tripod by shanecp
...don't need another one. this will suit roland handsonic hpd20, spd-20, spd-sx, apc-33. it might also work for yamaha...
Lexan
cg_studio
$150
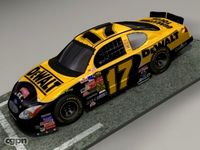
NASCAR Ford 13d model
...car race racing auto automobile sport goodyear dewalt ice lexan .3ds .max - nascar ford 1 3d model, royalty...
3d_export
$23
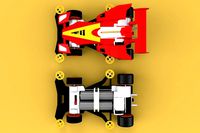
3D TAMIYA MINI 4WD SONIC MAGNUM AVANTE CAR TOY
...cornering. the body is designed from hard plastic or lexan there are three specifications that characterize all motors: rpm,...
thingiverse
free

Lexan Corner 3mm enclosure by Tactix
...lexan corner 3mm enclosure by tactix
thingiverse
lexan corner enclosure to be used with straight and end pieces
thingiverse
free
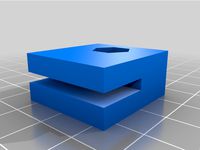
Race car Lexan window holder by chrisjdavis0307
...race car lexan window holder by chrisjdavis0307
thingiverse
tabs to mount rear side glass lexan windows on a bmw.
thingiverse
free
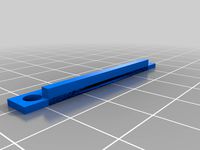
BZ3 rear lexan body posts stiffener
...bz3 rear lexan body posts stiffener
thingiverse
hello this is a rear stiffener for lexan body posts for atomic bz3
thingiverse
free

Lexan Case for Stratux - CNC fabricated by billvt1
...mm (.118") thick lexan
the lexan used was 3mm - translucent white
note: do not use acrylic as it cracks and shatters easily.
thingiverse
free
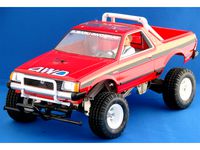
Tamiya Subaru Brat Lexan Body Posts
...posts
thingiverse
posts to suit the lexan body which seems to be near impossible to find.
2 x required for rear mounting pounts.
thingiverse
free

Lexane by DennisBuntrock
...mplate.
du möchtest auch deinen namen/text in 3d? schreibe mich an und ich erstelle auch für deinen n. eine kostenlose vorlage.
thingiverse
free
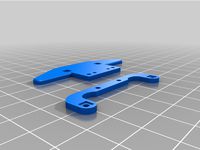
GL racing GLA lexan body mount by DTESTER88
...body mount by dtester88
thingiverse
lexan body mount set for gl racing gla. you will need the body posts whether it be pn or gl.
thingiverse
free
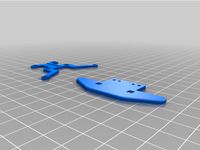
kyosho mr03 lexan body mount set by DTESTER88
...lexan body mount set by dtester88
thingiverse
kyosho mini z mr03 lexan body mount set. you will need either pn or gl body posts.
Openrc
thingiverse
free
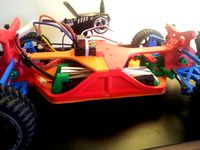
Battery holder for OpenRC by Wiero
...battery holder for openrc by wiero
thingiverse
battery holder for openrc
thingiverse
free

Front Wing OpenRC F1 by scarpantes
...front wing openrc f1 by scarpantes
thingiverse
front wing openrc f1
thingiverse
free
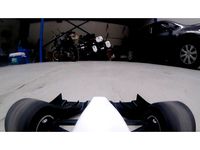
OpenRC f1 GoPro Mount by iClint
...openrc f1 gopro mount by iclint
thingiverse
pov mount for openrc f1 car
thingiverse
free

OpenRC F1 Bushings by rbrutsky
...openrc f1 bushings by rbrutsky
thingiverse
rear 12x18x4 bushings for the openrc formula 1 car. you must scale the bushings x10
thingiverse
free

OpenRC Truggy Trailer by Steamerzone
...verse
openrc truggy trailer with working suspension. the white suspension parts in the pictures are printed with taulman bridge.
thingiverse
free
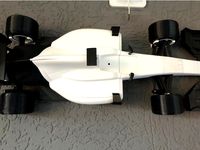
Wall mount OpenRC F1 horizontal
...wall mount openrc f1 horizontal
thingiverse
this is a wall mount for the openrc f1 car in a horizontal position.
thingiverse
free

OpenRC Wheel Nut Wrench by barspin
...openrc wheel nut wrench by barspin
thingiverse
wheel nut wrench for the 1:10 openrc project cars.
thingiverse
free
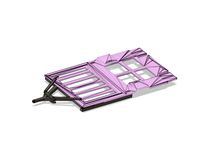
OpenRC Tractor Trailer by Merikisseli
...openrc tractor trailer by merikisseli
thingiverse
...
thingiverse
free

OpenRC Logo by SSwede
... logo, i haven't made the logo, just the 3d model and i'm uploading it by request.
feel free to use it anyway you like :)
thingiverse
free
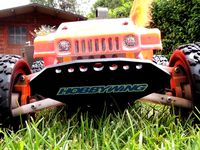
Bumper/Skidplate for the OpenRC Truggy by Steamerzone
...nted the plate in abs and the damper in taulman bridge. it uses existing holes/mounting points of the openrc truggy for mounting.
F1
3d_export
free
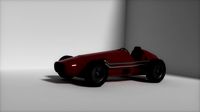
f1
...f1
3dexport
model 3d f1
3d_export
$5
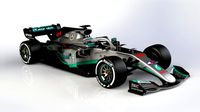
mercedes f1
...mercedes f1
3dexport
racing car mercedes f1
3ddd
$1
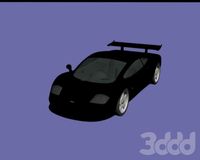
McLaren F1
...mclaren f1
3ddd
mclaren f1 без текстур.
3d_ocean
$25
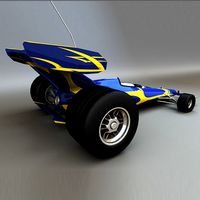
RC F1
...rc f1
3docean
auto car control f1 formula race rc remote speed
remote control f1 car
3d_export
$7
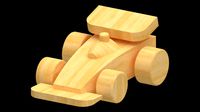
f1 toy
...f1 toy
3dexport
this is a f1 car toy representative of mexcan artists.
3d_export
$15
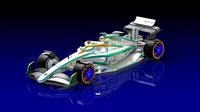
f1 car mercedes
...f1 car mercedes
3dexport
f1 racing f1 car mercedes
3d_ocean
$19
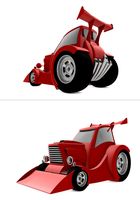
F1 Tractor
...f1 tractor
3docean
f1 futuristic race tractor red tractor
simple futuristic race tractor model.
3d_ocean
$30

Formula F1
...ic f1 formula indianapolis indy luxury muscle race racer sedan sports street transport tuner vehicle
generic formula f1 race car.
3d_ocean
$50
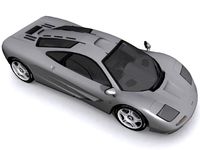
McLaren F1
...uxury mc mclaren muscle race sedan sports street transport tuner vehicle
highly detailed exterior and interior of the mclaren f1.
turbosquid
$100
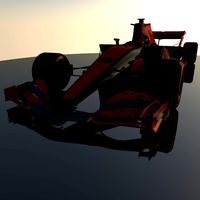
F1 Car
...
turbosquid
royalty free 3d model f1 car for download as obj on turbosquid: 3d models for games, architecture, videos. (1263925)
Body
3d_ocean
$39
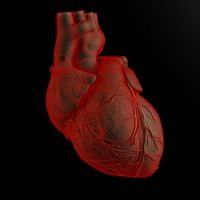
Heart and body
...heart and body
3docean
blood body heart human organ
heart and body highpoly heart inside human body.
3ddd
$1

body
...body
3ddd
маникен
corona mtl
turbosquid
$50
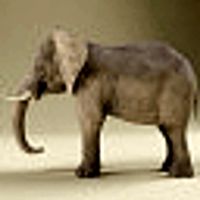
body
... available on turbo squid, the world's leading provider of digital 3d models for visualization, films, television, and games.
turbosquid
$45

Body
... available on turbo squid, the world's leading provider of digital 3d models for visualization, films, television, and games.
turbosquid
$25
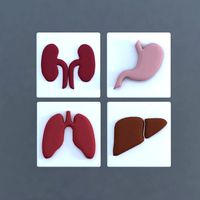
bodies
... available on turbo squid, the world's leading provider of digital 3d models for visualization, films, television, and games.
turbosquid
$20

Body
... available on turbo squid, the world's leading provider of digital 3d models for visualization, films, television, and games.
turbosquid
$5
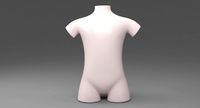
Body
... available on turbo squid, the world's leading provider of digital 3d models for visualization, films, television, and games.
turbosquid
$3

body
... available on turbo squid, the world's leading provider of digital 3d models for visualization, films, television, and games.
turbosquid
$1

body
... available on turbo squid, the world's leading provider of digital 3d models for visualization, films, television, and games.
turbosquid
free
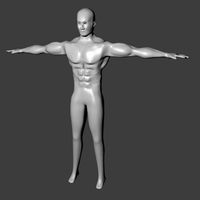
Body
... available on turbo squid, the world's leading provider of digital 3d models for visualization, films, television, and games.
Version
3ddd
$1
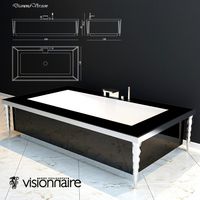
Diamond version
...nd , version , ванна
visionnaire - diamond bath
turbosquid
$50
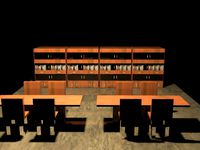
LibraryMini Version
...free 3d model librarymini version for download as max and jpg on turbosquid: 3d models for games, architecture, videos. (1617724)
design_connected
$34
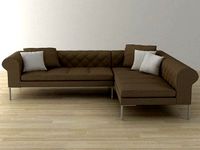
Barocco Version 01
...barocco version 01
designconnected
zanotta barocco version 01 computer generated 3d model. designed by progetti, emaf.
design_connected
$27
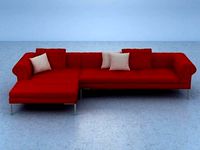
Barocco Version 02
...barocco version 02
designconnected
zanotta barocco version 02 computer generated 3d model. designed by progetti, emaf.
turbosquid
free
![Door [2 versions]](/t/13243146.jpg)
Door [2 versions]
...rbosquid
free 3d model door [2 versions] for download as fbx on turbosquid: 3d models for games, architecture, videos. (1223985)
turbosquid
$2
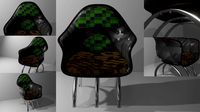
seat version 0.1
...
royalty free 3d model seat version 0.1 for download as blend on turbosquid: 3d models for games, architecture, videos. (1432653)
3d_export
$10

magnolia grandiflora mature version
...magnolia grandiflora mature version
3dexport
magnolia grandiflora mature version
3d_export
$8
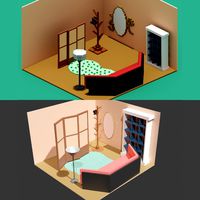
room assets and voxel version
...room assets and voxel version
3dexport
room assets and voxel version
turbosquid
$35
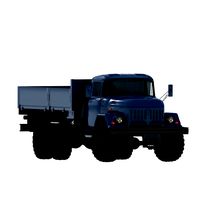
Zil Civilian version
... model zil civilian version for download as cgf, fbx, and obj on turbosquid: 3d models for games, architecture, videos. (1639420)
turbosquid
$3
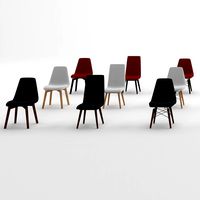
Chair 3 versions
...3d model chair 3 versions for download as blend, fbx, and obj on turbosquid: 3d models for games, architecture, videos. (1657530)