GrabCAD
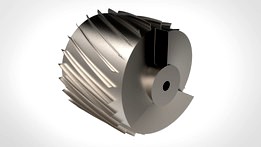
NASA RASSOR BUCKET DRUM
by GrabCAD
Last crawled date: 1 year, 11 months ago
Here's my entry for NASA RASSOR Bucket Drum Design Challenge.
Maximum length = 360mm
Maximum diameter = 440mm
Weight = 4.81Kg
Material = Aluminium 6061
Manufacturing type = SLS additive manufacturing using EOS P760 with 86% fill density.
Total volume = 38.04 litres
Volume captured = 29.04 litres
Fill ratio = 76.34%
Time required to fill the drum = 148.5 seconds.
Number of scoops = 3
Scoop dimension = 60x125mm
Designed in Creo parametric 5.0 and simulated in Altair EDEM, ANSYS Workbench.
Whole design development process can be accessed through the pdf documentation available as a downloadable file.
I started to develop the design by first dividing the problem statement into primary and secondary objectives. I developed three different designs to study the parameters such as Fill ratio and Filling rate. After identifying the parameters I started the development of final design which provides the best compromise between all the parameters. In order to do so i took inspiration from Archimedes screw and python digestion system.
The drum is designed using Creo parametric for 3D printing using aluminium 6061 and 86% fill density.
SIMULATION:
Further in order to verify the results a simulation was carried out in EDEM to measure the fill ratio and time required to achieve that fill ratio.
The drum has a fill ratio of about 76% when operated through a definite cycle which is explained in documentation provided in the downloads.
I don't have a workstation PC so in order to reduce computation time, power and memory I decided to keep the Drum stationary at one point and rotate at 35 rpm and the particles were added to a polygon defined as an inlet with unlimited particles(10000 particles/second) and time step was 1 second, the particles possess the same properties as that of sand and gravity was set to 1.62m/sec^2. These steps really helped me to complete the simulation, after that I derived the important parameters from the simulation so as to see the possible result of the drum had it been rotated at 20rpm.
Through this process I calculated that the maximum amount of regolight captured is 29 litres and 76.34% of the total volume. I have also uploaded the video of extraction of regolith in the downloads, so see how the drum achieves a fill ratio of 76.34% and how its works please refer to the documentation provided in the downloads.
Finally for manufacturing purpose I chose SLS additive manufacturing technology using EOS P760 Machine which has a large bed of size 700 × 380 × 580 mm that can easily accommodate the component.
VIDEO LINK: https://drive.google.com/open?id=1nkAUrkJT0UXI0hnzjcHqWGVjpwYYn656
Included in downloads: Design Documentation, Renderings, Regolith extraction simulation video, Step file, STL file.
Maximum length = 360mm
Maximum diameter = 440mm
Weight = 4.81Kg
Material = Aluminium 6061
Manufacturing type = SLS additive manufacturing using EOS P760 with 86% fill density.
Total volume = 38.04 litres
Volume captured = 29.04 litres
Fill ratio = 76.34%
Time required to fill the drum = 148.5 seconds.
Number of scoops = 3
Scoop dimension = 60x125mm
Designed in Creo parametric 5.0 and simulated in Altair EDEM, ANSYS Workbench.
Whole design development process can be accessed through the pdf documentation available as a downloadable file.
I started to develop the design by first dividing the problem statement into primary and secondary objectives. I developed three different designs to study the parameters such as Fill ratio and Filling rate. After identifying the parameters I started the development of final design which provides the best compromise between all the parameters. In order to do so i took inspiration from Archimedes screw and python digestion system.
The drum is designed using Creo parametric for 3D printing using aluminium 6061 and 86% fill density.
SIMULATION:
Further in order to verify the results a simulation was carried out in EDEM to measure the fill ratio and time required to achieve that fill ratio.
The drum has a fill ratio of about 76% when operated through a definite cycle which is explained in documentation provided in the downloads.
I don't have a workstation PC so in order to reduce computation time, power and memory I decided to keep the Drum stationary at one point and rotate at 35 rpm and the particles were added to a polygon defined as an inlet with unlimited particles(10000 particles/second) and time step was 1 second, the particles possess the same properties as that of sand and gravity was set to 1.62m/sec^2. These steps really helped me to complete the simulation, after that I derived the important parameters from the simulation so as to see the possible result of the drum had it been rotated at 20rpm.
Through this process I calculated that the maximum amount of regolight captured is 29 litres and 76.34% of the total volume. I have also uploaded the video of extraction of regolith in the downloads, so see how the drum achieves a fill ratio of 76.34% and how its works please refer to the documentation provided in the downloads.
Finally for manufacturing purpose I chose SLS additive manufacturing technology using EOS P760 Machine which has a large bed of size 700 × 380 × 580 mm that can easily accommodate the component.
VIDEO LINK: https://drive.google.com/open?id=1nkAUrkJT0UXI0hnzjcHqWGVjpwYYn656
Included in downloads: Design Documentation, Renderings, Regolith extraction simulation video, Step file, STL file.
Similar models
grabcad
free

RASSOR
... (rassor) with major highlight is the excavation blade is a angle of 30 degree. the software used in particle simulation is edem
grabcad
free

NASA RASSOR Drum Bucket
...only be estimated to about 65 %.
material: polyether ether petone (peek)
manufacturing: selective laser sintering
mass: ~4.95 kg
grabcad
free

SimEx Regolith Collector
...res/bucket drum
for more information on the simulation, please feel free to contact us.
we hope you'll enjoy our design! :)
grabcad
free

EVN Flap Drum
...epresents an average fill ratio of 70%. 10s is needed to dump the entirety of the contained regolith.
i hope you will apreciate.
grabcad
free

RASSOR Bucket Drum Design
...0 mm
volume of regolith captured: approximately 19 liters
fill ratio: approximately 70%
materials:
cfrp
5052-h38 aluminium alloy
grabcad
free

RASSOR Bucket Drum
...s strength and weldability.
personal email: sinhlun68@gmail.com
business email: nguyenchisinh68@gmail.com
tel: (+84) 868 188 473
grabcad
free

NASA Regolith Drum E2
...tries for this challenge:
https://grabcad.com/library/nasa-regolith-drum-e1-1
https://grabcad.com/library/nasa-regolith-drum-e3-1
grabcad
free

NASA Regolith Drum E1
...tries for this challenge:
https://grabcad.com/library/nasa-regolith-drum-e2-1
https://grabcad.com/library/nasa-regolith-drum-e3-1
grabcad
free

Trapezoidal Drum
...e is no moving part inside or outside except the entire drum itself which rotates.
please, do read the file conceptual_draft.pdf.
grabcad
free

NASA SQUARE RASSOR DRUM
...egolith reverse the rassor drum.
specks
maximum scoops width 108 mm
mass 4.34 kg
diameter 366 mm
length 226.6 mm
volume 22 liters
Rassor
grabcad
free

RASSOR
...rassor
grabcad
just tried to design rassor
hope you like it :)
grabcad
free

Rassor
...s effesien used for mining in outer space, the system used is the mortar mixing system. this drum rassor uses horizontal rotation
grabcad
free

Rassor
...rassor
grabcad
modeling of rassor drums for the collection of extraterrestrial soil. rhinoceros, file stl and renderings
grabcad
free

Rassor Bucket
...rassor bucket
grabcad
nasa rassor challenge
grabcad
free

RASSOR
... (rassor) with major highlight is the excavation blade is a angle of 30 degree. the software used in particle simulation is edem
grabcad
free

RASSOR
...rassor
grabcad
this is a very simple and innovative plan
grabcad
free

RASSOR Regolith Miner
...rassor regolith miner
grabcad
designed for the nasa rassor bucket challenge
grabcad
free

rassor de Alonso
...rassor de alonso
grabcad
eta es una pala para el sistema rassor
grabcad
free

RASSOR Scoop Drum
...rassor scoop drum
grabcad
stl / jpeg / txt file submission for nasa rassor scoop challenge
grabcad
free

NASA RASSOR BUCKET
... is a design for nasa rassor bucket. the total weight of the bucket is 4.94 kg. for unloading rotate the bucket counterclockwise.
Nasa
turbosquid
$49
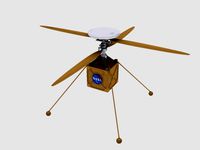
Nasa Marscopter
...id
royalty free 3d model nasa marscopter for download as max on turbosquid: 3d models for games, architecture, videos. (1323349)
turbosquid
$500

NASA Crawler
... available on turbo squid, the world's leading provider of digital 3d models for visualization, films, television, and games.
turbosquid
$5
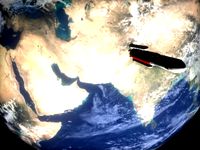
Nasa Rocket
... available on turbo squid, the world's leading provider of digital 3d models for visualization, films, television, and games.
turbosquid
$1

NASA Spool.max
... available on turbo squid, the world's leading provider of digital 3d models for visualization, films, television, and games.
3d_export
$15
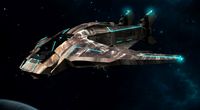
US NASA 3D Model
...us nasa 3d model
3dexport
spaceship ship nasa battle blender
us nasa 3d model antonielfelain 96625 3dexport
turbosquid
$99
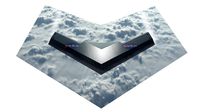
NASA MIT Wing
...oyalty free 3d model nasa mit wing for download as ma and max on turbosquid: 3d models for games, architecture, videos. (1510099)
turbosquid
$29
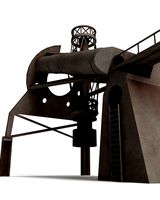
NASA Electronic Telescope
... available on turbo squid, the world's leading provider of digital 3d models for visualization, films, television, and games.
turbosquid
$6
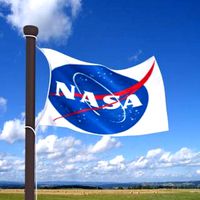
Real flag NASA
... available on turbo squid, the world's leading provider of digital 3d models for visualization, films, television, and games.
3d_export
$41
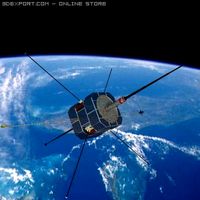
NASA FAST Satellite 3D Model
...odel
3dexport
nasa space satellite earth aurora sensor panel solar orbit
nasa fast satellite 3d model visualmotion 20244 3dexport
3d_export
$20
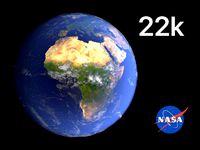
22k photorealistic earth - nasa
...tures directly from nasa.<br>nasa solar system bundle coming soon!<br>contact info@teichmanmedia.eu for all iquiries.
Bucket
archibase_planet
free
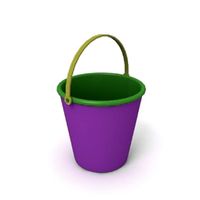
Bucket
...bucket
archibase planet
pail bucket tub
bucket - 3d model for interior 3d visualization.
3d_ocean
$5
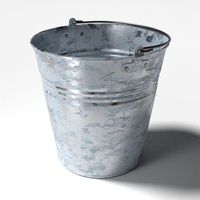
Bucket
...bucket
3docean
bucket cleaning galvanized gavanised stainless steel zinc zinc coated
a galvanized bucket
turbosquid
free

Bucket bucket With Water
... available on turbo squid, the world's leading provider of digital 3d models for visualization, films, television, and games.
archibase_planet
free
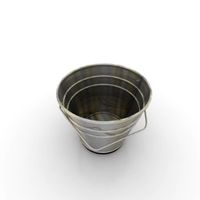
Bucket
...bucket
archibase planet
bucket pail
bucket n250308 - 3d model (*.gsm+*.3ds) for interior 3d visualization.
archibase_planet
free
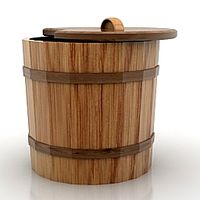
Bucket
...bucket
archibase planet
tub bucket pail
bucket - 3d model (*.gsm+*.3ds) for interior 3d visualization.
archibase_planet
free
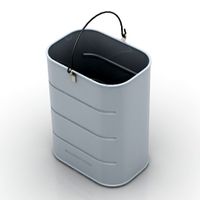
Bucket
...bucket
archibase planet
bucket pail bin
bucket n280612 - 3d model (*.gsm+*.3ds) for interior 3d visualization.
archibase_planet
free
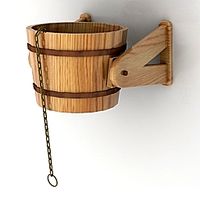
Bucket
...bucket
archibase planet
pail bucket tub
bucket 2 - 3d model (*.gsm+*.3ds) for interior 3d visualization.
archibase_planet
free

Bucket
...bucket
archibase planet
fire fighting equipment dip-bucket
bucket - 3d model (*.gsm+*.3ds) for interior 3d visualization.
3d_export
$5
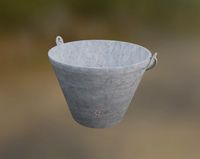
bucket
...bucket
3dexport
scratched galvanized bucket. fbx, obj, blend, and testura formats
3ddd
$1
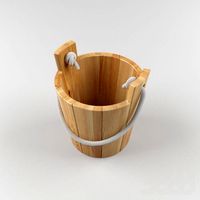
Wooden bucket
...wooden bucket
3ddd
wooden bucket , ведро
wooden bucket
Drum
3d_export
$5
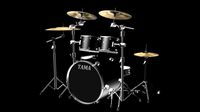
drums
...drums
3dexport
drums
3d_ocean
$20
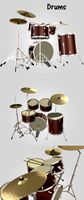
Drums
...iled model of drums. charleston,bass drum, tamtam drums, cymbal,etc. available in .blend, .obj, and .lwo format. ready for render
archibase_planet
free

Drum
...hibase planet
drum musical instrument tambour drum kit
drum taiko n091115 - 3d model (*.gsm+*.3ds) for interior 3d visualization.
design_connected
$9

Drum
...drum
designconnected
brent comber drum computer generated 3d model. designed by comber, brent.
turbosquid
$4
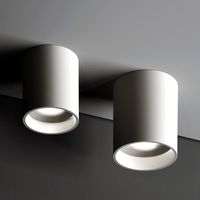
Drum 7 Drum 12
... model drum 7 drum 12 for download as max, max, fbx, and obj on turbosquid: 3d models for games, architecture, videos. (1641795)
3d_export
$15

Conga Drum
...conga drum
3dexport
conga drums
3d_export
$10
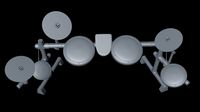
electro drums
...electro drums
3dexport
electro drums
3d_export
$5
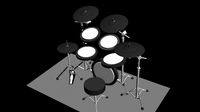
electric drums
...electric drums
3dexport
electric drums
turbosquid
$1

Drums
...s
turbosquid
royalty free 3d model drums for download as max on turbosquid: 3d models for games, architecture, videos. (1240112)
turbosquid
$1

Drum
...turbosquid
royalty free 3d model drum for download as blend on turbosquid: 3d models for games, architecture, videos. (1480093)