GrabCAD

NASA HCA
by GrabCAD
Last crawled date: 1 year, 11 months ago
Built and functionality of my HCA NASA proposal.
1. My design consist of just one printed part without any additional features
2. My HCA proposal is snap on type feature with auto locking mechanism
3. Way of assembling and disassembling the clamp. PLease have a look at some renderings for reference.
Four teeth are supported by lever sliding above them, with rectangular feature at the end, and of a support rib above. This creates locked and tightly fitted clamp as teeth can't travel up or down as they are beein locked by the lever supported by the rib above and any movement downwards is locked by the rail. If one wants to disassemble the clamp, then only finger pressing the four levers towards middle rib is required (square ends of the levers will reveal the beam of the teeth and will allow them to travel upwards) and slight pull the clamp to bend four teeth support. At this point teeth beams will lock the lever against springing back, so user will be able tu pull the clamp in most convenient way, with just friction reaction of the clamp.
The clamp is very well locked when assembled and the teeth being locked against outside movement, create very good locking feature. In case of pulling load exceeding maximum values, the beam has got side pattern of protrusions, which will keep the clamp still assembled even if the beam of the teeth connection will be broken.
I have started designing the clamp on 15th of February so I haven't rigorously checked it's structural capabilities but quick calculations show that Z Tensile (build direction): 50 lbf will create just 6MPa on the teeth beam , which is 6 times less than Re of ABS. In case of the load exceeding 300 lbf it will still stay assemble as the side pattern will keep it safe.
Other features provide high strenght and low weight or are design acordingly to the design spec.
This part requires minimal amount of material to print and requires just one print process to have fully usable product, without the need to assembly, separate parts. Functionality is simple and based on very old and commonly used principles (lever, support and spring effect of material in certain geometry).
It could be designed in more thoughtful way but 1.5 day is a very limited time to do it according to specification in not native language, I believe that optimising this approach is the best way of implementing a good product to NASA employees in such demanding conditions as space is.
1. My design consist of just one printed part without any additional features
2. My HCA proposal is snap on type feature with auto locking mechanism
3. Way of assembling and disassembling the clamp. PLease have a look at some renderings for reference.
Four teeth are supported by lever sliding above them, with rectangular feature at the end, and of a support rib above. This creates locked and tightly fitted clamp as teeth can't travel up or down as they are beein locked by the lever supported by the rib above and any movement downwards is locked by the rail. If one wants to disassemble the clamp, then only finger pressing the four levers towards middle rib is required (square ends of the levers will reveal the beam of the teeth and will allow them to travel upwards) and slight pull the clamp to bend four teeth support. At this point teeth beams will lock the lever against springing back, so user will be able tu pull the clamp in most convenient way, with just friction reaction of the clamp.
The clamp is very well locked when assembled and the teeth being locked against outside movement, create very good locking feature. In case of pulling load exceeding maximum values, the beam has got side pattern of protrusions, which will keep the clamp still assembled even if the beam of the teeth connection will be broken.
I have started designing the clamp on 15th of February so I haven't rigorously checked it's structural capabilities but quick calculations show that Z Tensile (build direction): 50 lbf will create just 6MPa on the teeth beam , which is 6 times less than Re of ABS. In case of the load exceeding 300 lbf it will still stay assemble as the side pattern will keep it safe.
Other features provide high strenght and low weight or are design acordingly to the design spec.
This part requires minimal amount of material to print and requires just one print process to have fully usable product, without the need to assembly, separate parts. Functionality is simple and based on very old and commonly used principles (lever, support and spring effect of material in certain geometry).
It could be designed in more thoughtful way but 1.5 day is a very limited time to do it according to specification in not native language, I believe that optimising this approach is the best way of implementing a good product to NASA employees in such demanding conditions as space is.
Similar models
grabcad
free

Nasa hand rail clamp assembly
...sed by astronauts on iss to provide rigid mounting locations required in a microgravity environment for normal daily operations.
grabcad
free

NASA CHALLENGE - HANDRAIL CLAMP ASSEMBLY
...next to the rail than further away from it. similary, the clamp widens away from the rail. this results...
grabcad
free

NASA Handrail Clamp Assembly (CHAMP)
...asa
update:- this version has a provision to unhook the upper clamp by simply pressing the handles. now its more simpler to use.
grabcad
free

NASA CHAMP - Ratchet Clamp
... turn disengages the "teeth".
clamp is printed in one piece therefore no need for printing multiple parts or assembly.
grabcad
free

CHAMP QR
.... measures 73420.47 cubic millimeters in volume.
6. self driving locating and locking mechanism, just push and lock in position.
grabcad
free

Nasa HCA -1
...nasa hca -1
grabcad
still looking for clamping methods.
grabcad
free

NASA Handrail Clamp Assembly Challenge
...asa handrail clamp assembly challenge
grabcad
low material costing hand rail assembly with two way adjustable locking mechanism.
grabcad
free

NASA CHAMP with Fast Twist & Lock
...with the nut without tools. it is very easy printable and only chunky parts good for handling with them in stressfull situations.
grabcad
free

3FPD-NASA CHAMP Handrail Clamp - Design 1
...king if moved along handrail
-entire design is printed, including the hinge pins (which have a flat surface for ease of printing)
grabcad
free

GE Quick Connect V2
...parts.
manual operation, no tools needed for assembly or disassembly.
quick connect! it can be assembled in less than one minute.
Hca
3dfindit
free
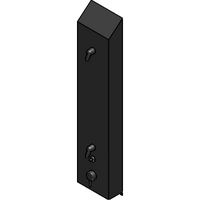
CWSMS-HCA
...cwsms-hca
3dfind.it
catalog: willoughby industries
3dfindit
free

CWTS-HCA
...cwts-hca
3dfind.it
catalog: willoughby industries
3dfindit
free
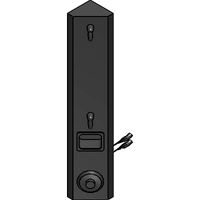
CWKS-HCA
...cwks-hca
3dfind.it
catalog: willoughby industries
3dfindit
free

CWDS-HCA
...cwds-hca
3dfind.it
catalog: willoughby industries
3dfindit
free
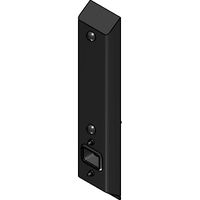
WBS-HCA-2HD
...wbs-hca-2hd
3dfind.it
catalog: willoughby industries
thingiverse
free
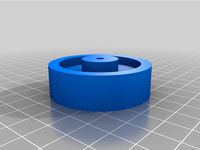
Parasound HCA-1206 Amplifier Foot
...ing feet.
there is a cutout on the base of the foot to place a circular felt furniture pad that are about 18mm-20mm in diameter.
renderosity
$18
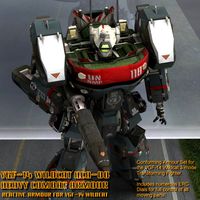
VGF-14 Wildcat HCA-00 Reactive Armour - for Poser
... fitted (this pose can be found in your "poses" library in the folder labelled "mecha mode poses").</p>
grabcad
free

Nasa HCA -1
...nasa hca -1
grabcad
still looking for clamping methods.
grabcad
free

NASA HCA - 2
...inking of clamping method which should be used. this is another clamp that i came up with. please send your comments and critics.
Nasa
turbosquid
$49
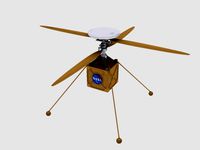
Nasa Marscopter
...id
royalty free 3d model nasa marscopter for download as max on turbosquid: 3d models for games, architecture, videos. (1323349)
turbosquid
$500

NASA Crawler
... available on turbo squid, the world's leading provider of digital 3d models for visualization, films, television, and games.
turbosquid
$5
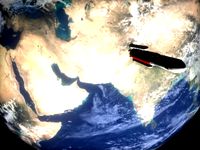
Nasa Rocket
... available on turbo squid, the world's leading provider of digital 3d models for visualization, films, television, and games.
turbosquid
$1

NASA Spool.max
... available on turbo squid, the world's leading provider of digital 3d models for visualization, films, television, and games.
3d_export
$15
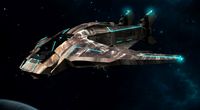
US NASA 3D Model
...us nasa 3d model
3dexport
spaceship ship nasa battle blender
us nasa 3d model antonielfelain 96625 3dexport
turbosquid
$99
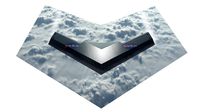
NASA MIT Wing
...oyalty free 3d model nasa mit wing for download as ma and max on turbosquid: 3d models for games, architecture, videos. (1510099)
turbosquid
$29
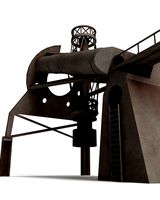
NASA Electronic Telescope
... available on turbo squid, the world's leading provider of digital 3d models for visualization, films, television, and games.
turbosquid
$6
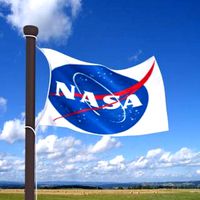
Real flag NASA
... available on turbo squid, the world's leading provider of digital 3d models for visualization, films, television, and games.
3d_export
$41
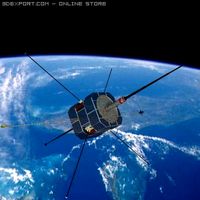
NASA FAST Satellite 3D Model
...odel
3dexport
nasa space satellite earth aurora sensor panel solar orbit
nasa fast satellite 3d model visualmotion 20244 3dexport
3d_export
$20
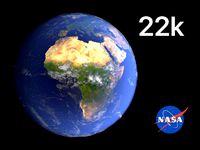
22k photorealistic earth - nasa
...tures directly from nasa.<br>nasa solar system bundle coming soon!<br>contact info@teichmanmedia.eu for all iquiries.