GrabCAD
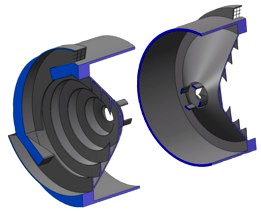
MERLIN Scoop Design
by GrabCAD
Last crawled date: 1 year, 10 months ago
In the design of an extraterrestrial sampling system, it is critical that the following two items are specifically addressed.
1. The geophysical properties of the regolith targeted for collection
2. The environmental properties of the planet for collection
In the case of lunar sample collection targeted by RASSOR, two problems need to be addressed that will otherwise render a successful terrestrial design insufficient and/or incapable of collection on the moon.
1. Testing with properly baked out KSC-1 Lunar Regolith reveal higher values of cohesion (exacerbated by the triboelectric charging from particle agitation) and internal friction (likely due to particle topology). Said plainly: particles will stick and clump together inside the collection drum. Additionally, with a cohesion over 1.0 kPA (KCS-1), particles will not necessarily flow like dry sand, instead behaving like fully saturated wet sand. “After the first Surveyor landing, it was said that “the lunar soil behaves like damp beach sand”, even though everyone knew full well there was no water on the Moon. “ [1]
2. Due to the reduced lunar gravitational field (compared to earth), the centripetal forces present in the drum cannot be ignored. At the design specification of 20 rpm, the force of gravity is only 1.6 times the centripetal force present in the drum. When accounting for the significant electrostatics that will be present with fine particles in zero atmosphere, the centripetal force can overwhelm gravitational forces. Particles will adhere to the outside wall of the collection drum, even at TDC of a drums rotation.
When considering the above two points, many designs that have sample storage in the same internal cavity as sample collection will not be able to reach maximum fill ratios. Once you reach a minimum level of sample collected, that sample will clump to the outside walls of the drum preventing additional sample from being collected.
In addition to the special requirements of a lunar collection system, there are general guidelines than all extraterrestrial collection devices should implement to maximize sample flow and minimize clogging.
1. Maximum particle size able to be collected must be strictly controlled in two dimensions (length & width). If a particle/sample/rock is collected that is too large, it can become permanently jammed inside the device. By controlling length and width, the only rogue sample possible can be a cigar shaped sample. If only one dimension is controlled, disks are able to enter the system easily which quickly can lead to jamming and device failure.
2. Once maximum collection size (length and width) are controlled, internal cavities must be 3x that size in cross section. This prevents three particle bridge clogging in internal passageways.
3. No converging or diverging internal cavities and/or passageways. This minimizes particle clogging/clumping that can then be packed in with a Morse taper effect.
4. No relative internal sliding surface, moving parts, or mechanisms within the sample flow. These will ALWAYS jam.
Proposed Design Solution
The design outlined in the attached PDF and part files proposes a solution that addresses the above concerns. As each batch of sample is collected, sample is immediately diverted through an Archimedes screw to a central holding chamber. The motion to this chamber is helped by both gravitational and centripetal forces. The metering effect of the screw reduces the opportunity for sample charging and clumping as well as removing it from preventing additional sample from being collected.
Sample collection and handling is done passively through geometry with no jammable sliding surfaces or mechanisms. Maximum particle size of 10x10mm is controlled at the inlet to each scoop by steel wire. Between 13-16.6 liters of regolith is held within the central holding chamber with an additional 4.6-5.8 liters held in the Archimedes screw as overflow after the central chamber has filled. Total sample captured is 19.6-22.4 liters. Design can be further optimized to increase this range.
No attempt at mass optimization or DFM has been made, however the design is straightforward and would be easily to manufacture from anodized 6061 or tiodized 6AL-4V and be less than 5kg.
[1] https://www.lpi.usra.edu/lunar/surface/carrier_lunar_soils.pdf
1. The geophysical properties of the regolith targeted for collection
2. The environmental properties of the planet for collection
In the case of lunar sample collection targeted by RASSOR, two problems need to be addressed that will otherwise render a successful terrestrial design insufficient and/or incapable of collection on the moon.
1. Testing with properly baked out KSC-1 Lunar Regolith reveal higher values of cohesion (exacerbated by the triboelectric charging from particle agitation) and internal friction (likely due to particle topology). Said plainly: particles will stick and clump together inside the collection drum. Additionally, with a cohesion over 1.0 kPA (KCS-1), particles will not necessarily flow like dry sand, instead behaving like fully saturated wet sand. “After the first Surveyor landing, it was said that “the lunar soil behaves like damp beach sand”, even though everyone knew full well there was no water on the Moon. “ [1]
2. Due to the reduced lunar gravitational field (compared to earth), the centripetal forces present in the drum cannot be ignored. At the design specification of 20 rpm, the force of gravity is only 1.6 times the centripetal force present in the drum. When accounting for the significant electrostatics that will be present with fine particles in zero atmosphere, the centripetal force can overwhelm gravitational forces. Particles will adhere to the outside wall of the collection drum, even at TDC of a drums rotation.
When considering the above two points, many designs that have sample storage in the same internal cavity as sample collection will not be able to reach maximum fill ratios. Once you reach a minimum level of sample collected, that sample will clump to the outside walls of the drum preventing additional sample from being collected.
In addition to the special requirements of a lunar collection system, there are general guidelines than all extraterrestrial collection devices should implement to maximize sample flow and minimize clogging.
1. Maximum particle size able to be collected must be strictly controlled in two dimensions (length & width). If a particle/sample/rock is collected that is too large, it can become permanently jammed inside the device. By controlling length and width, the only rogue sample possible can be a cigar shaped sample. If only one dimension is controlled, disks are able to enter the system easily which quickly can lead to jamming and device failure.
2. Once maximum collection size (length and width) are controlled, internal cavities must be 3x that size in cross section. This prevents three particle bridge clogging in internal passageways.
3. No converging or diverging internal cavities and/or passageways. This minimizes particle clogging/clumping that can then be packed in with a Morse taper effect.
4. No relative internal sliding surface, moving parts, or mechanisms within the sample flow. These will ALWAYS jam.
Proposed Design Solution
The design outlined in the attached PDF and part files proposes a solution that addresses the above concerns. As each batch of sample is collected, sample is immediately diverted through an Archimedes screw to a central holding chamber. The motion to this chamber is helped by both gravitational and centripetal forces. The metering effect of the screw reduces the opportunity for sample charging and clumping as well as removing it from preventing additional sample from being collected.
Sample collection and handling is done passively through geometry with no jammable sliding surfaces or mechanisms. Maximum particle size of 10x10mm is controlled at the inlet to each scoop by steel wire. Between 13-16.6 liters of regolith is held within the central holding chamber with an additional 4.6-5.8 liters held in the Archimedes screw as overflow after the central chamber has filled. Total sample captured is 19.6-22.4 liters. Design can be further optimized to increase this range.
No attempt at mass optimization or DFM has been made, however the design is straightforward and would be easily to manufacture from anodized 6061 or tiodized 6AL-4V and be less than 5kg.
[1] https://www.lpi.usra.edu/lunar/surface/carrier_lunar_soils.pdf
Similar models
grabcad
free

Sampling System for a Lunar Rover
...sampling system for a lunar rover
grabcad
collection and separation of lunar dust and regoliths by use of centrifugal force.
grabcad
free

NASA_DRUM_Challenge_MRin
... aluminum 6061. it has a maximum fill volume of 31.5 liters. the design of this bucket drum was inspired by the fibonacci series.
grabcad
free

Archimedes Screw Lunar Sampling
... motor that will change the angle of the collection tube to lower it into the soil and raise it once finished collecting samples.
grabcad
free

sedimentation chamber
...ticles with size greater than 50 μm.o velocity of flue gas reduced in large chamber.o particles settle under gravitational force.
grabcad
free

93% Fill Bucket Drum
...achieve the desired 17.6 liter capacity. this bucket drum design can be scaled to fit other robotic regolith collecting vehicles.
grabcad
free

Ultimate Excavation Drum Redesign
...vironment. when gravity is present, regolith will settle down at the bottom and this will not be an issue for the design as well.
grabcad
free

bucket drum NASA challenge
...ter: 450 mm
the average captured volume of regolith: 20 liters
materials used:
scoop blades: titanium
rest of the drum: aluminum
grabcad
free

Lunar Sampling System Design Challenge
...ampling system design challenge
grabcad
the system for collecting and sorting regolith.
description of the system in a pdf file.
grabcad
free

NASA Lunar Sampling System
...nasa lunar sampling system
grabcad
sample separation system is capable to collect, separate and layer regolith.
grabcad
free

NASA Lunar Sampling System
...mbly can collect and store samples. it has compact design and smaller footprint. with telescopic expandable arm it can be shrink.
Merlin
turbosquid
$40

Merlin
... available on turbo squid, the world's leading provider of digital 3d models for visualization, films, television, and games.
turbosquid
$9
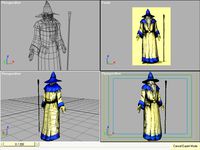
merlin sorcerer
... available on turbo squid, the world's leading provider of digital 3d models for visualization, films, television, and games.
turbosquid
$5

Leroy Merlin Phuket
...royalty free 3d model leroy merlin phuket for download as max on turbosquid: 3d models for games, architecture, videos. (1288437)
turbosquid
$112
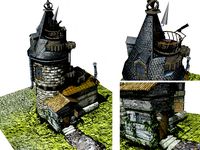
Merlin`s tower
... available on turbo squid, the world's leading provider of digital 3d models for visualization, films, television, and games.
turbosquid
$14

MERLIN MODERN LUX
... available on turbo squid, the world's leading provider of digital 3d models for visualization, films, television, and games.
3d_export
$20

rigged swordfish merlin sword fish
...rigged swordfish merlin sword fish
3dexport
rigged swordfish merlin sword fish
3d_export
$60

agustawestland eh-101 merlin
...d at factories in yeovil, england and vergiate, italy; licensed assembly work has also taken place in japan and the united states
cg_studio
$59
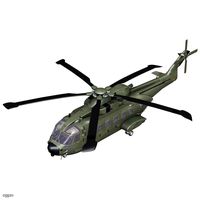
Augusta Westland EH101 Merlin HC3A Transport Helicopter3d model
...ugusta westland eh101 merlin hc3a transport helicopter 3d model, royalty free license available, instant download after purchase.
3ddd
$1

Nomon Merlin 12 N орех
...
настенные часы в современном стиле. материал - древесина (орех), нержавеющая сталь. офисные часы, большие часы, часы из металла.
3ddd
$1

Nomon Merlin 4 N wenge
...настенные часы в современном стиле. материал - древесина (венге), нержавеющая сталь. офисные часы, большие часы, часы из металла.
Scoop
archibase_planet
free

Scoop
...scoop
archibase planet
spade scoop shovel
scoop n250608 - 3d model (*.gsm+*.3ds) for interior 3d visualization.
archibase_planet
free

Scoop
...scoop
archibase planet
scoop dipper ladle
kitchen accessories n141107 - 3d model (*.gsm+*.3ds) for interior 3d visualization.
3d_export
free

scoop
...scoop
3dexport
3ddd
$1
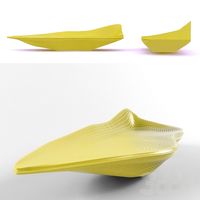
Scoop
...scoop
3ddd
дизайн захи хадид.
turbosquid
$39

Scoop
... available on turbo squid, the world's leading provider of digital 3d models for visualization, films, television, and games.
turbosquid
$3
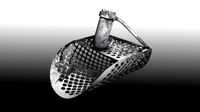
Scoop
... available on turbo squid, the world's leading provider of digital 3d models for visualization, films, television, and games.
3d_export
$10
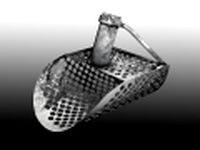
SCOOP 3D Model
...scoop 3d model
3dexport
scoop beach dig mole delve
scoop 3d model lllarapov 96017 3dexport
archive3d
free
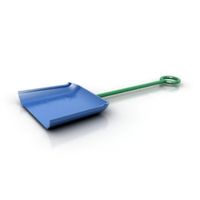
Scoop 3D Model
...hive3d
spade scoop shovel
scoop n250608 - 3d model (*.gsm+*.3ds) for interior 3d visualization.
turbosquid
$4

Antique Scoop
...oyalty free 3d model antique scoop for download as ma and obj on turbosquid: 3d models for games, architecture, videos. (1460892)
turbosquid
$49

Scoop Stretcher
... available on turbo squid, the world's leading provider of digital 3d models for visualization, films, television, and games.
Design
3ddd
$1
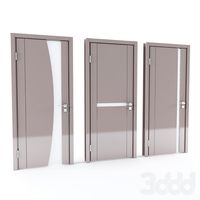
LINE DESIGN (Doors Design)
...line design (doors design)
3ddd
дверь
modern doors design - line design concept
turbosquid
$5

designer
...alty free 3d model designer for download as max, obj, and fbx on turbosquid: 3d models for games, architecture, videos. (1422665)
3ddd
$1
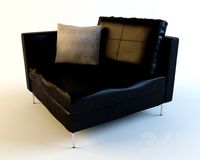
VER DESIGN
...ver design
3ddd
ver design
кресло ver design
3ddd
$1
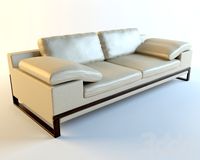
VER DESIGN
...ver design
3ddd
ver design
диван ver design
3ddd
$1
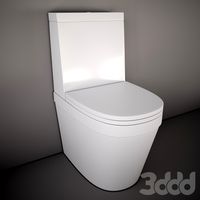
Bagno design
...bagno design
3ddd
bagno design , унитаз
санитария bagno design
3ddd
free
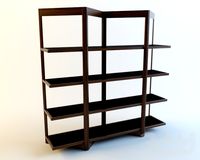
VER DESIGN
...ver design
3ddd
ver design , стеллаж
полка ver design
3ddd
$1
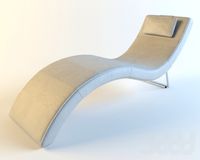
VER DESIGN
...ver design , лежак , шезлонг
шезлонг ver design
3d_export
free
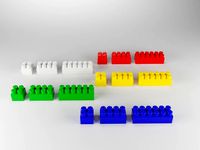
designer
..., trees and much more. the model has 3 types of parts: - 4 cells - 6 cells - 8 cells the *.max file contains 5 colored materials.
3d_export
$19
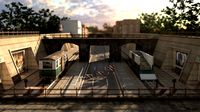
level design
...level design
3dexport
you can use this design (level design) in your own game.
3d_export
$7
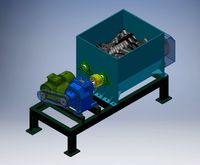
Crusher design
...crusher design
3dexport
crusher design