Thingiverse
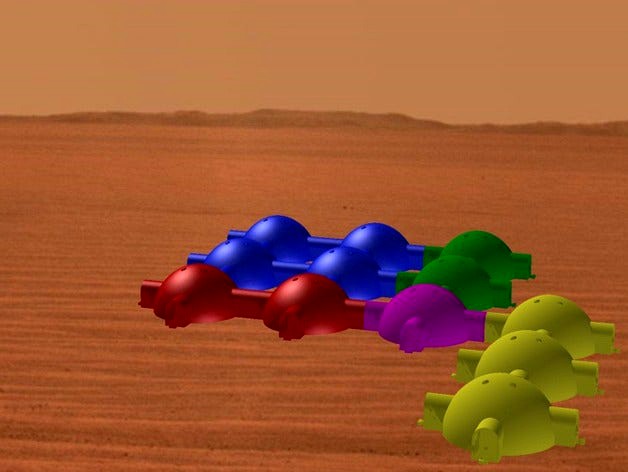
Mars base designed by UND Mars In Situ Resource Utilization Design Group by UNDMarsResourceGroup
by Thingiverse
Last crawled date: 3 years ago
A 3D Printed Mars Base Built from In Situ Resources*
By UND Mars In Situ Resource Utilization Mission Design Group
Mars has excited humanity for quite a while. This submission presents one such concept which is based on reducing mission launch and deep space transfer mass and volume requirements via the fabrication of most of the base structures from in-situ resources. This mission concept requires technical advancement in several areas beyond those typically required for Martian missions. Specifically, this work requires advancement in the development of basalt additive manufacturing (also known as 3D printing) technology and analysis of the produced basalt structuresâ permeability and ability to maintain a pressurized environment suitable for human habitation.
Kelso, in [1], suggested the 3D printing of basalt, but provided an insufficient explanation of the operations of a basalt 3D printer. The basic concept of 3D printing is well known. In the recent past, the basic Fused Deposition Modeling (FDM) technique has been augmented through an increase in the materials that can be printed. An overview of a basalt 3D printing approach for use on Mars is presented in [2].
Maintaining a pressurized living and working environment within the structures is critical. Prior work [3-5] has characterized the permeability of basalt; however, this work did not consider the specific compositions of basalt found on Mars. In [2], multiple considerations regarding and solutions to the challenge of sealing the 3D printed basalt are presented. A worst-case scenario would be to utilize a bladder such as Bigelow Aerospace has demonstrated [6] in space.
The base would be comprised of multiple modular structures. The largest, the agriculture / construction dome, would be built from materials carried onboard the interplanetary spacecraft as well as 2.4 m tall basalt panels fabricated from local materials onboard the landed spacecraft. When this structure is done, the basalt 3D printer will then be moved from its location in the spacecraft to the agriculture / construction dome, where it will be attached to longer rails, allowing it to print the smaller-sized structures. When construction is done, this structure is used as an agricultural growing facility (a set of translucent panels for parts of the dome are carried onboard the spacecraft for this use).
The other structures, which are printed whole in the construction dome, include the housing / laboratory / multi-purpose unit, which, as the name suggests, can be configured with equipment and furniture to suite mission needs (and prospectively re-configured multiple times during the mission). Two versions of this structure (the dome shown and a cylindrical underground version) exist. A version of this module is also used as a command (central control area) unit and as a services (water / air / waste / etc. processing) unit. These modules are connected by interlocking tunnels (both above and below ground) which also house the data/power/water/sewage/etc. piping/cabling for the units.
Construction is designed to be performed primarily by robots sent on an unmanned construction mission. These robots will, upon landing, produce initial pieces of the agriculture / construction dome within the spacecraft and setup supporting truss and install them. These will them be robotically moved to their final location and attached to adjacent structures, as per the base design.
Robotic construction of the base will take two forms: the 3D printer, housed in the agriculture / construction dome, will be a stationary robot, which will print ready-to-use smaller structures. These will be moved (and the agriculture / construction dome initially constructed) by construction robots.
Power to these units is supplied via very high frequency wireless power transfer from the orbiting craft (which carried the lander to Mars) so as to not increase mission risk and increase landing fuel costs by landing the limited nuclear power reactors. The high frequency transmissions reduce free space loss considerably, making this a viable power system in this instance.
This description is abstracted from [2] (we are happy to provide a copy of this paper to the contest reviewers upon request to benjamin.kading@my.und.edu)
Some images also sourced from [2]; use of NASA imagery for the background of one image is gratefully acknowledged. NASA imagery is not subject to US copyright.
References:
References
[1] R. Kelso. Expanding the planetary analog test sites in hawaii-planetary basalt manipulation. Presented at AGU Fall Meeting Abstracts. 2013, .
[2] B. Kading and J. Straub, "Design of a Manned Mars Mission Utilizing In-Situ Resources for Structure Fabrication," Acta Astronautica, Prepared for Submission to.
[3] N. I. Christensen and R. Ramananantoandro. Permeability of the oceanic crust based on experimental studies of basalt permeability at elevated pressures. Tectonophysics 149(1), pp. 181-186. 1988.
[4] A. T. Fisher. Permeability within basaltic oceanic crust. Rev. Geophys. 36(2), pp. 143-182. 1998.
[5] M. O. Saar and M. Manga. PermeabilityâÂÂporosity relationship in vesicular basalts. Geophys. Res. Lett. 26(1), pp. 111-114. 1999.
[6] Air barrier for use with an expandable structure, R. T. Bigelow. Feb 5, 2013). US 8366051 B2 , 2013.
By UND Mars In Situ Resource Utilization Mission Design Group
Mars has excited humanity for quite a while. This submission presents one such concept which is based on reducing mission launch and deep space transfer mass and volume requirements via the fabrication of most of the base structures from in-situ resources. This mission concept requires technical advancement in several areas beyond those typically required for Martian missions. Specifically, this work requires advancement in the development of basalt additive manufacturing (also known as 3D printing) technology and analysis of the produced basalt structuresâ permeability and ability to maintain a pressurized environment suitable for human habitation.
Kelso, in [1], suggested the 3D printing of basalt, but provided an insufficient explanation of the operations of a basalt 3D printer. The basic concept of 3D printing is well known. In the recent past, the basic Fused Deposition Modeling (FDM) technique has been augmented through an increase in the materials that can be printed. An overview of a basalt 3D printing approach for use on Mars is presented in [2].
Maintaining a pressurized living and working environment within the structures is critical. Prior work [3-5] has characterized the permeability of basalt; however, this work did not consider the specific compositions of basalt found on Mars. In [2], multiple considerations regarding and solutions to the challenge of sealing the 3D printed basalt are presented. A worst-case scenario would be to utilize a bladder such as Bigelow Aerospace has demonstrated [6] in space.
The base would be comprised of multiple modular structures. The largest, the agriculture / construction dome, would be built from materials carried onboard the interplanetary spacecraft as well as 2.4 m tall basalt panels fabricated from local materials onboard the landed spacecraft. When this structure is done, the basalt 3D printer will then be moved from its location in the spacecraft to the agriculture / construction dome, where it will be attached to longer rails, allowing it to print the smaller-sized structures. When construction is done, this structure is used as an agricultural growing facility (a set of translucent panels for parts of the dome are carried onboard the spacecraft for this use).
The other structures, which are printed whole in the construction dome, include the housing / laboratory / multi-purpose unit, which, as the name suggests, can be configured with equipment and furniture to suite mission needs (and prospectively re-configured multiple times during the mission). Two versions of this structure (the dome shown and a cylindrical underground version) exist. A version of this module is also used as a command (central control area) unit and as a services (water / air / waste / etc. processing) unit. These modules are connected by interlocking tunnels (both above and below ground) which also house the data/power/water/sewage/etc. piping/cabling for the units.
Construction is designed to be performed primarily by robots sent on an unmanned construction mission. These robots will, upon landing, produce initial pieces of the agriculture / construction dome within the spacecraft and setup supporting truss and install them. These will them be robotically moved to their final location and attached to adjacent structures, as per the base design.
Robotic construction of the base will take two forms: the 3D printer, housed in the agriculture / construction dome, will be a stationary robot, which will print ready-to-use smaller structures. These will be moved (and the agriculture / construction dome initially constructed) by construction robots.
Power to these units is supplied via very high frequency wireless power transfer from the orbiting craft (which carried the lander to Mars) so as to not increase mission risk and increase landing fuel costs by landing the limited nuclear power reactors. The high frequency transmissions reduce free space loss considerably, making this a viable power system in this instance.
This description is abstracted from [2] (we are happy to provide a copy of this paper to the contest reviewers upon request to benjamin.kading@my.und.edu)
Some images also sourced from [2]; use of NASA imagery for the background of one image is gratefully acknowledged. NASA imagery is not subject to US copyright.
References:
References
[1] R. Kelso. Expanding the planetary analog test sites in hawaii-planetary basalt manipulation. Presented at AGU Fall Meeting Abstracts. 2013, .
[2] B. Kading and J. Straub, "Design of a Manned Mars Mission Utilizing In-Situ Resources for Structure Fabrication," Acta Astronautica, Prepared for Submission to.
[3] N. I. Christensen and R. Ramananantoandro. Permeability of the oceanic crust based on experimental studies of basalt permeability at elevated pressures. Tectonophysics 149(1), pp. 181-186. 1988.
[4] A. T. Fisher. Permeability within basaltic oceanic crust. Rev. Geophys. 36(2), pp. 143-182. 1998.
[5] M. O. Saar and M. Manga. PermeabilityâÂÂporosity relationship in vesicular basalts. Geophys. Res. Lett. 26(1), pp. 111-114. 1999.
[6] Air barrier for use with an expandable structure, R. T. Bigelow. Feb 5, 2013). US 8366051 B2 , 2013.
Similar models
thingiverse
free
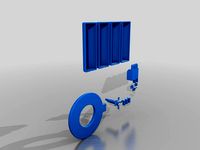
Nuclear Mars Base by Lepidopteranodon
...ng transported materials. the plants themselves are grown using growlights, also powered by electricity from the central reactor.
thingiverse
free

Astrobiobound Spacecraft by mfritz
...ue to thin parts (communication dishes, robot arms) and need support. the year ended before we could optimize these for printing.
thingiverse
free
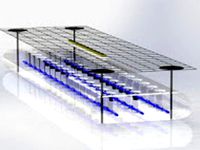
Mars Deployable Greenhouse Project by Damiana
...ned for multi-habitat. they both are deployable. the main structure is the central one. when it lands on mars surface it deploys.
thingiverse
free

Mars Atmosphere Mine by NathansMind
...ter planet. i have also really enjoyed seeing the solutions other people have come up with. let me know if you have any feedback.
thingiverse
free
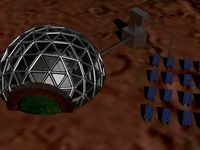
Ico-Dome Mars Base by TIMISH
...h minimal upkeep, it is the ideal living solution for anyone willing to live on mars.
diametre is subject to buyers preference.
thingiverse
free

pascee's Mars base by skelman8
...s beneath the crust. the space ship will have retractable solar panels for in-space flight and a liquid fuel booster for takeoff.
thingiverse
free
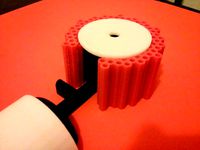
Mars Research Station Two by xmbrst
... in the photos.)
scale
--
the connector tunnels that link the inflatable habs are just big enough for a person to walk through.
thingiverse
free

MakerBot Mars Base Challenge - Early Mars Base Station by HAitCH_
...samples)
new vehicles:
heavy lift platform
explorer-excavator
and some cool add ons to the mars base:
containers and drill bits
thingiverse
free
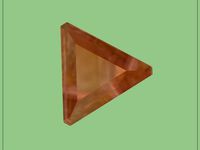
Bentonite Crystal by wslab
...l as a sealant, since it provides a self-sealing, low permeability barrier. it is used to line the base of landfills for example.
thingiverse
free

Mars Rover Raspberry Pi Arduino Robot Platform by paulcox
...www.mathworks.com/matlabcentral/fileexchange/46441-mars-rover-robot-2014-competitionhttp://makerzone.mathworks.com/tag/mars-rover
Situ
thingiverse
free
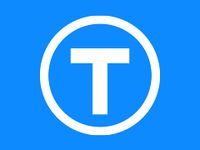
Microscope tray for in situ studies by wRm_
... epifluorescence for in situ studies on the host rock.
tray should fit any microscope that can handle standard 76 x 26 mm slides.
thingiverse
free

Digital Caliper Extensions. by mohojo
...calipers and they will measure double glazing units in situ ...
thingiverse
free

Tevo Tarantula Stock X-Carriage by bitbrain
...stock x-carriage for the tevo tarantula. measurements done in situ so may not be perfect but should be pretty...
thingiverse
free
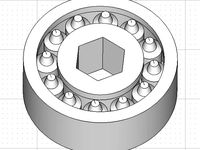
Wheel with Cylinder Bearings by Thex1138
...a work in progress wheel with bearings printed in situ dimensions are now sweet! i hope you guys like...
thingiverse
free

LightwaveRF JSJSLWL100WH Wall Mount by canidorichard
...wall and can be easily removed or used in situ ...
thingiverse
free

coude 90° culbuteur R5 gt turbo by SINGULARITE
...coude de 90° pour vapeur d huile qui ce situ sur le...
thingiverse
free
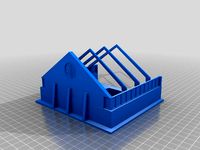
Eglise de Veneux-Les Sablons pour l'expo in situ Art & Spirituel by cva
... d’arts, laure-marie meyer, elsa rousselle, kate kaiser
contacts : anne biró biroanne@free.fr, dominique jacquot dojacquot@gmx.fr
thingiverse
free
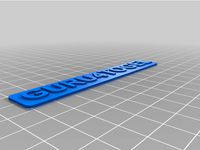
Guru4Togel
...guru4togel thingiverse situ data pengeluaran togel pasaran singapura hongkong dan sidney serta...
thingiverse
free
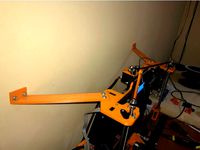
tiranta soporte pared by brus10000
...para la parte derecha. hacer perforaciones donde mejor se situ. ...
Resource
thingiverse
free
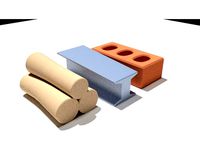
Fortnite resources by Maxirush
...fortnite resources by maxirush
thingiverse
fortnite resources
made with blender
thingiverse
free

Kingsburg Resource Tray by Sembiance
...kingsburg resource tray by sembiance
thingiverse
resource try to hold resources for the kingsburg board game.
thingiverse
free

Catan Resource Tiles by SupermanPrime
...rce tiles by supermanprime
thingiverse
these are resource tiles that i've created to replace the resource cards in the game.
thingiverse
free

Resource Card Holder by greenearwax
...resource card holder by greenearwax
thingiverse
a holder for resource and development cards for catan.
thingiverse
free

Stone Age Resources by romroig
...stone age resources by romroig
thingiverse
stone age resources (if you need more)
thingiverse
free

Wood Resource Token by Smashed_Pumpkin
...wood resource token by smashed_pumpkin
thingiverse
wood resource token i made for the boardgame scythe.
thingiverse
free

Oil Resource Token by Smashed_Pumpkin
...oil resource token by smashed_pumpkin
thingiverse
oil resource token i made for the boardgame scythe
thingiverse
free
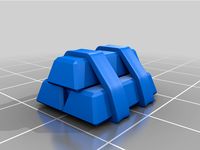
Metal Resource Token by Smashed_Pumpkin
...metal resource token by smashed_pumpkin
thingiverse
metal resource token i made for the boardgame scythe
thingiverse
free

Oil Resource Token by Smashed_Pumpkin
...oil resource token by smashed_pumpkin
thingiverse
oil resource token i made for the boardgame scythe
thingiverse
free

Harbour - Resource Board by DasMatze
...harbour - resource board by dasmatze
thingiverse
a little board for easier resource-tracking for the boardgame harbour.
Mars
thingiverse
free

mars
...mars
thingiverse
mars fait avec topographie de mars
thingiverse
free
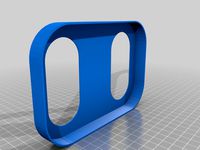
Terraforming Mars
...terraforming mars
thingiverse
rangement pour terraforming mars
thingiverse
free
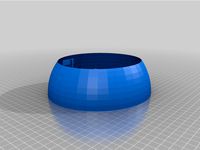
Mars dome
...mars dome
thingiverse
a mars dome that has a flag and rooms
thingiverse
free
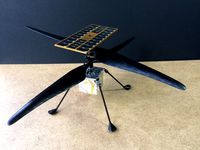
Mars helicopter
...copter
thingiverse
this is a 1/5th scale replica of the jpl mars scout helicopter which will accompany the nasa 2020 mars rover.
thingiverse
free

handle for MARS
...handle for mars
thingiverse
i wanted to install a handle to my elegoo mars.
thingiverse
free

MARS ROVER by leonk
...mars rover by leonk
thingiverse
mars rover
thingiverse
free

Mars Meteorite by Casbarox
...mars meteorite by casbarox
thingiverse
mars meteorite
thingiverse
free

ROVER MARS by leonk
...rover mars by leonk
thingiverse
rover mars
thingiverse
free

Mars spaceship by 5665
...mars spaceship by 5665
thingiverse
mars not included
thingiverse
free

Mars Lander by cerberus333
...mars lander by cerberus333
thingiverse
mars lander
Utilization
thingiverse
free
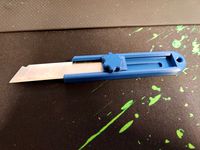
Utility Knife
...utility knife
thingiverse
easy to print utility knife.
inspired by dhp73`s design thing:3775612
thingiverse
free
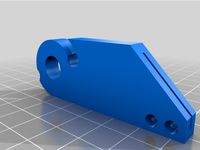
Utility Knife by cheftuecke
...utility knife by cheftuecke
thingiverse
simple utility knife
thingiverse
free
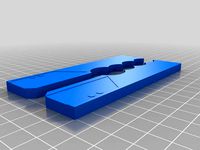
Utility Knife by EvilTeach
...utility knife by evilteach
thingiverse
this is a plastic handle for a utility knife blade.
thingiverse
free
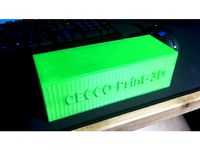
Box Utility by Sirassassin
...box utility by sirassassin
thingiverse
box utility
x - 200mm
y - 70mm
z - 65mm
thingiverse
free

Utility Hook by Matsugawa
...utility hook by matsugawa
thingiverse
wall-mounted utility hook with four flush points for wood screws.
thingiverse
free
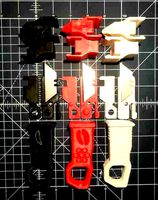
Utility Knife by Vandelayandco
...ty knife by vandelayandco
thingiverse
made a utility knife handle that snaps into either a keychain blade guard or a wall mount.
thingiverse
free

Micro servo Utilities by thomasgobert
...micro servo utilities by thomasgobert
thingiverse
utilities for micro servo
thingiverse
free

Bathroom Utility Holder by nerdmakerengineer
... drain holes
bathroom utility holder with screw holes
bathroom utility holder no holes
data
width: 105mm
hight: 100mm
depth: 43mm
thingiverse
free

Basic Utility Tripod by joshgoreworks
...basic utility tripod by joshgoreworks
thingiverse
utility tripod designed by joshgoreworks.com
thingiverse
free
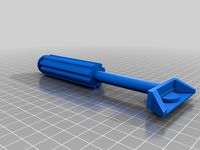
utility razor blade scraper
...utility razor blade scraper
thingiverse
utility razor blade scraper
Group
thingiverse
free

group by amarjeetkapoor
...group by amarjeetkapoor
thingiverse
checking the groups
thingiverse
free

Building Group by ethanahlberg
...building group by ethanahlberg
thingiverse
borr group
thingiverse
free

group of items by Legatusarch
...group of items by legatusarch
thingiverse
here is a group of house hold items that should print fantastically.
thingiverse
free
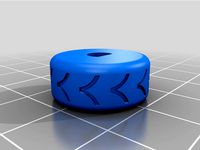
model group by leetony
...model group by leetony
thingiverse
thingiverse
free

desks group right by DoESLiverpool
...desks group right by doesliverpool
thingiverse
desks group right
thingiverse
free
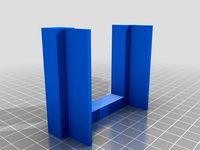
grouped clip by 24smithq
...grouped clip by 24smithq
thingiverse
this is for my project
thingiverse
free
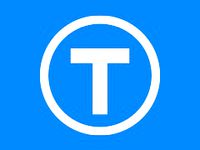
Group 1 by David14john
...group 1 by david14john
thingiverse
assignment 1
thingiverse
free

Foundry Group Coin by bfeld
...foundry group coin by bfeld
thingiverse
a coin with the foundry group logo on one side. the usd exchange rate is unknown.
thingiverse
free

Piston Rod group by poetryinmotion
...oup by poetryinmotion
thingiverse
all the parts required to build as pictured fits with the cross block and cylinder group parts
thingiverse
free
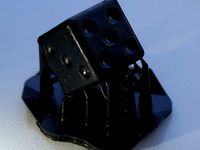
Dice by Ameloot-Group
...dice by ameloot-group
thingiverse
this a standard 16mm dice, for regular gaming purposes.
Und
thingiverse
free
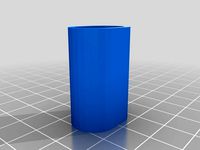
Zahnbürstenhalter und Staubschutz by tauchpiranha
...zahnbürstenhalter und staubschutz by tauchpiranha
thingiverse
zahnbürstenhalter und staubschutz
thingiverse
free

Nicht trinken und drucken
...nicht trinken und drucken
thingiverse
nicht trinken und drucken
thingiverse
free
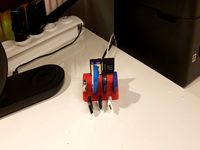
USB UND KABELHALTER
...usb und kabelhalter
thingiverse
ich habe das gemach weil ich immer so viele kabel usb stick und sd karten herumligen hate. :-)
thingiverse
free
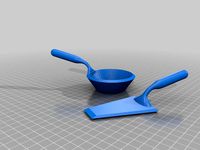
Maurer Kelle und Pfandl by Syzguru11
...maurer kelle und pfandl by syzguru11
thingiverse
maurer kelle und pfandl
thingiverse
free

Laptop und Tablet Wandhalterung by Jaegerdrucker
...laptop und tablet wandhalterung by jaegerdrucker
thingiverse
laptop und tablet wandhalterung
thingiverse
free

Schubladen und Box by manfred3010
...laden und box by manfred3010
thingiverse
die anderen schubladen und boxen gibt es hier
https://www.thingiverse.com/thing:4790559
thingiverse
free
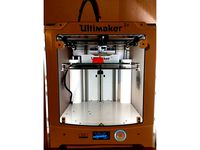
Halter und Verschlüsse by niederhauser83
...se by niederhauser83
thingiverse
halter und verschlüsse für die frontscheibe.
benötigt wird zusätzlich eine plexiglasscheibe 3mm
thingiverse
free

Yin und Yang Schale
...yin und yang schale
thingiverse
ich hatte mal etwas lange weile und ich habe mich da mal probiert
thingiverse
free

Stifte und zettelbox by GottderDrachen
...stifte und zettelbox by gottderdrachen
thingiverse
das sind boxen für den gürtel um stifte und zettel dabei zu haben
thingiverse
free
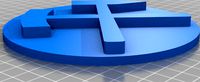
Schlägel und Eisen by subprint
...schlägel und eisen by subprint
thingiverse
Base
thingiverse
free
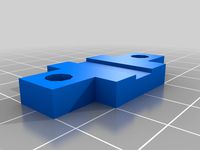
Base
...base
thingiverse
this base helps wedge the end of the tape measure to the floor
thingiverse
free
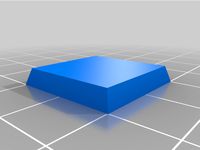
Kings of War Bases / Scenic Bases
... 80mm 3.2mm base with lp
kow 250mm 100mm 3.2mm base with lp
kow 250mm 150mm 3.2mm base with lp
kow 300mm 100mm 3.2mm base with lp
thingiverse
free

base by savethemonsters
...base by savethemonsters
thingiverse
base
thingiverse
free
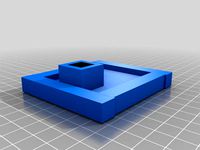
base by jesse53
...base by jesse53
thingiverse
base
thingiverse
free
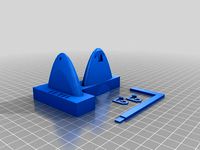
base by m2kalista
...base by m2kalista
thingiverse
base
thingiverse
free

Base by danielolivier
...base by danielolivier
thingiverse
base
thingiverse
free
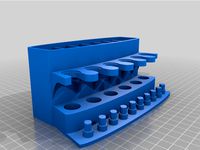
base by savethemonsters
...base by savethemonsters
thingiverse
base part
thingiverse
free
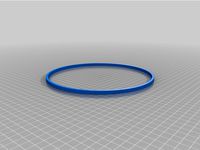
Lamp Base
...lamp base
thingiverse
lamp base
thingiverse
free

The lamp base
...the lamp base
thingiverse
the lamp base
thingiverse
free

20x20 Base
...20x20 base
thingiverse
20x20 base
Design
thingiverse
free

2D Design
...2d design
thingiverse
2d design
thingiverse
free
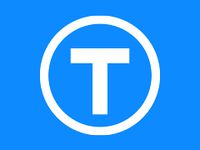
2D DESIGN
...2d design
thingiverse
2d design
thingiverse
free

Lego design
...lego design
thingiverse
lego design
thingiverse
free
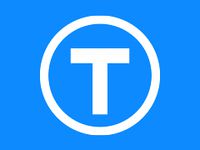
Eggbot designs
...eggbot designs
thingiverse
a bunch of eggbot designs
thingiverse
free
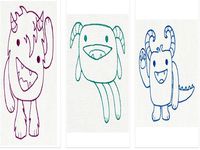
Eggbot Designs
...eggbot designs
thingiverse
a bunch of eggbot designs
thingiverse
free
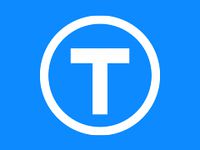
2D Design
...2d design
thingiverse
the 2d design of the laptop stand.
thingiverse
free
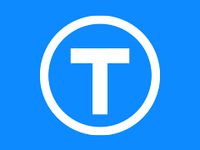
2D Design
...2d design
thingiverse
2d design on adobe illustrator
thingiverse
free
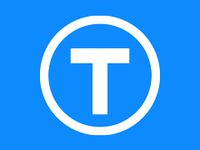
2D design
...2d design
thingiverse
please find attached the ud design
thingiverse
free
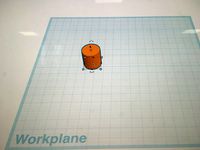
3D Design
...3d design
thingiverse
the greatest 3d design in my life.
thingiverse
free

2D Design
...2d design
thingiverse
2d design made with adobe illustrator
Designed
thingiverse
free

2D Design
...2d design
thingiverse
2d design
thingiverse
free
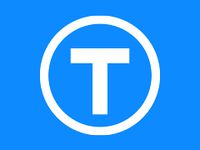
2D DESIGN
...2d design
thingiverse
2d design
thingiverse
free

Lego design
...lego design
thingiverse
lego design
thingiverse
free
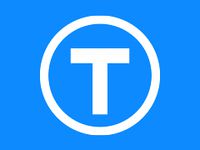
Eggbot designs
...eggbot designs
thingiverse
a bunch of eggbot designs
thingiverse
free
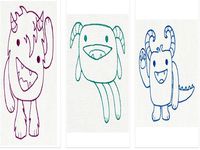
Eggbot Designs
...eggbot designs
thingiverse
a bunch of eggbot designs
thingiverse
free
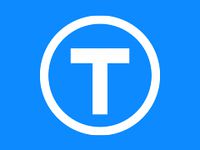
2D Design
...2d design
thingiverse
the 2d design of the laptop stand.
thingiverse
free
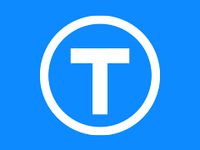
2D Design
...2d design
thingiverse
2d design on adobe illustrator
thingiverse
free
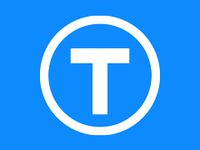
2D design
...2d design
thingiverse
please find attached the ud design
thingiverse
free
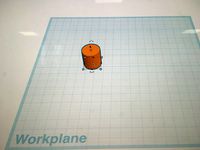
3D Design
...3d design
thingiverse
the greatest 3d design in my life.
thingiverse
free

2D Design
...2d design
thingiverse
2d design made with adobe illustrator