GrabCAD
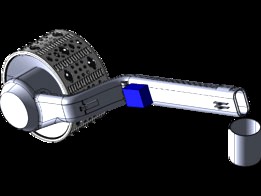
Lunar Wheel Regolith Sampling System
by GrabCAD
Last crawled date: 1 year, 10 months ago
Lunar Wheel Regolith Sampling System
Lunar Wheel Regolith Sampling System is a system is an integrated system and not an entirely and exclusively designed new system dedicated to the sampling of the regolith though it is a dedicated sampling system which is a result of the innovation/ slight modification of the present/current landers or rovers landing or wheels technology.
Landers or rovers use certain kind of technology to explore its surrounding (arms in case of landers and rovers itself are dedicated robots for exploration and have robotic arms for certain functional operations).
The proposed design/idea takes the advantage of this feature of the landers or rovers and this makes it valuable sampling system which is not an entirely new sampling system which is mounted/employed on its parent rover or lander. Rather than employing an entire new system this system demands slight modification in the current design of the presently used mars or moon rovers or landers which are in operation right now and this makes it useful and can be used by both landers and rovers for the sampling of the regolith.
This system consists of a wheel system (which is similar to front landing wheel system of the airplanes) which is mounted either separately on rovers or landers or with minor adjustments can be integrated with the present system and thus saves the total weight and power of the system.
In this system, modification begins with the tyre of the wheels (which is of similar type as is being used in the rovers at present). this proposed tyre design consist of no of through holes of various sizes on its surface, which allows the wire rang of regolith to being sampled inside out. holes are of particular size are in particular number, in particular pattern and in particular order are stamped which allows the regolith of wide variety (under the limits of the sample sizes) are collected and sampled simultaneously as due to mechanical properties of the rubber tyre it will compresses while in contact the ground and this will expands the hole which allows the regolith to move inside the wheel, and when the wheel leaves the ground its holes get contracted due to removal of compression load on that part of the tyre and thus the regolith get trapped for ages inside the wheel till it get recovered in the sampling container/cylinder. and due to sizes and arrangement of holes and limit to expansion and contraction of holes (which depends upon the mechanical and chemical properties of the rubber tyre) the regolith also get sampled while getting collected by the wheel. thus, the first sampling is performed along with the depositing/collecting operation of the regolith.
More the wheel will roll on the surface, more the chances to collect the regolith and this may vary according to the sampling site, chosen, the side of the wheel is sufficiently chosen, that it will be able to collect the regolith even at the extreme locations where regolith of desired size, quantity and quality are limited.
A natural rubber padding is provided which is the second layer after the rubber tyre have a small hole punched all over its circumference and has longitudinal cuts which samples the regolith again and allows regolith only of desired quality and its main task is to control the quantity of the regolith entering the wheel. it also acts like a valve for the finer regolith’s which may easily wash out through bigger holes from the wheel tyre if padding is absent.
After two samplings, the regolith moves towards the core of the wheel, the axle. before passing on to the axle, regolith must have to pass through wheel alloy or supporting frame which holds tyre and the axle together. this allow is of frustum type from outside and acts as a sliding pass/or a funnel from inside which collects the regolith from the wheels outer layer and transport it to the axle of the wheel. the frustum type outer layer of the wheel checks the loss of the regolith while transferring/transportation of regolith through the funnel type sliding alloys which has teflon coating on its inside surface.
Axle of the wheel is a hollow conical funnel which allows the flow of regolith from number of passing holes through which the alloy rims are joined. the axle is the integral part of the wheel rim/alloy. the conical shape of the axle guides the regolith in one direction, in the direction of the hub and other side is closed, which is the narrow side and has one mini-spy camera for the monitoring purposes of the regolith.
Now when the regolith has been passed to the axle, it is now free to move to the wheel's arm which is a hollow body, through the hub which joins/supports and derives the wheel by transmitting the power from the deriving motor (which is mounted on the base/board of the rover or lander, and thus therefore there is no requirement of a separate command module as rover/lander can directly control the sampling operations) to the wheel through the wheel arm and this hub is the integral part of the arm which on one side takes the regolith from axle, and form other side transfer it to the hollow arm channel. the hub of the wheel has more than sufficient space to store the regolith till the desired quantity and quality of regolith is being collected.
When the regolith collecting operation is completed (the camera tells the command module about the desired quantity and quality has been achieved or not), the wheel arm is lifted about the roll axes by a rotary motor (through the motor coupling provided, which is directly coupled to the motor and is tightly fixed on the arm frame with the help of tightening bolts), which is the same motor which is used to derive the wheel (a separate motor can be employed as per requirement) and the arm/lunar wheel will rise about the roll axis (which lies on the floor of the rover/lander) and thus the regolith under the influence of the planetary gravity rushes against the rise of the wheel (in the opposite direction). this motion is similar to the recoiling or rewinding of the front landing wheel system of the airplane. this motion is similar to the motion which is followed by the robotic arms of the landers and the rovers which usually do this to keep the mechanism safe form the radiation by winding up/closing their mechanism and storing in the rover's or lander's body. and in addition to it, the pace of this winding/stowing operation is very low due to limited power supply. this proposed idea/system will take advantage of both the motion and its pace and uses it to transfer the regolith to the sampling cylinder from through the wheel arm.
During the lifting/stowing operation of the wheel, the regolith are forced to move against, in the direction opposite to the rising direction and at the entry of the hollow arm channel, there is a sampling tray which separates the rogolithic rocks (of size greater than 1 cm) from the regolithic dust (of size smaller than 1 cm) before the third stage of sampling, where the regolithic rocks are sampled for the maximum numbers allowed in the final sample.
After the regolith passed through the entry of the arm channel and over the sampling tray, it is now exposed to a couple of sudden bends which will force the regolith to change its direction and this bend has major impact on regolithic rocks as due to its higher relative mass with respect to regolithic dust, it will possess higher velocity and the bend has a chance to sample the rocks on the basis of the maximum quantity allowed. the number of regolithic rocks arriving and departing the first bend is monitored by the mini-spy cameras mounted on the hub and on the second bend. Due to the combined analyses and monitoring of both the cameras, the door at the first bend will open/or we can say it get closed (as it opens the passage for the regolithic rocks to get moved out of the arm's channel (into the space again) by moving in and closing the passage, which continues to the arm's channel and to the sampling cylinder) after 20 regolithic rocks passes through the bend and moves forward towards the second bend. the door is mounted such that it will act like a single door for two passes/routes, when the door closes one route, the other gets open automatically.
During in this mean time, when the third sampling operation is being carried in, the regolithic dust will safely and securely get deposited in the arm channel after being sampled by the sampling plate. the geometrical design of the arm and bends are such that regolithic dust will continue to move in the channel without getting involved in the third sampling operation.
When the first camera (which is mounted in the axle) and the second camera (which is mounted on the hub) gives the clearance about the execution of the regolithic rock in the system before the third sampling stage, the third sampling will be halted.
In the meantime, the regolithic rock which is allowed to pass through the third sampling stage and the regolithic dust which passes without being involved in the third sampling stage are free to move through the second bend and into the arm's femur (longest straight channel which joins the wheel to the main frame of the rover or the lander through the deriving motor) under the precise monitoring of the third camera (which is mounted at the second bend) and the weight or density sensing device. when the camera and sensors at the second bend tells that the amount of regolith needed/desired are collected and have passes through the second bend, the rotary motor will operate and the fourth sampling beings with the open of the regolith sampling door. the excess amount, (other than the desired/required regolith sample) is dumped through the door under the influence of the stowing motion of the wheel's arm.
The sampled regolith sample which has passed the fourth stage of sampling, in the meantime is being transported to the sampling cylinder through the arm femur/arm channel ,which is placed just next to the arm (which is placed firmly at its position on the base/floor of the rover/lander), when arm is in a position where whole regolith sample can move/wash out off from the wheel's arm, while rotating along its roll axis.
All the operations like third and fourth sampling is carried out simultaneously with the rotation/stowing operation of the wheel's arm.
Weight and Power:
This proposed sampling system is an integral part of the presently used system which is achieved by the slight modification and whole sampling operation is being carried out under the motion of the presently used system and thus taking advantage of the designed motion and design (structure) of the current system, this system will work with very low power requirement or the whole modified system may use some additional power (which is very less) to overcome the frictional losses or to move the additional mass (which is also very less).
In case of rovers, this system need power to lift the wheel to deposit regolith in the sampling cylinder and in case of landers, it will need power to perform rolling operation on the surface of the planet to collect the regolith. in both cases all other operational requirements are successfully fulfilled by the motion of the existing system, thus this system, uses very less power exclusively for sampling operation.
In terms of weight, this system is just a slight modification of the existing system which when innovated can either needs a little modification which will add some mass or need a replacement with the exiting parts/components (as likely to be in the case of wheel rim/axle) which will again add no to very less mass to the entire system.
Thus, the overall power consumption is very less and weight of the sampling system (exclusive) is very low. moreover, when considered the case where both present systems are operating with the additional sampling system which possess and impose entire new mass and power requirements to the whole system, this proposed system is very good in both ways relatively.
Reliability and Effectiveness.
This proposed system uses very common things which are happening in daily life without any connections in-between them. using an air-less, rubber tyre with holes and slots to collect and sample the regolith is a tested and verified idea which is noble in this field, as this particular, collecting and sampling solution by a rubber material with hole has been tested by millions who have a hole in the sole of their shoes/boot/sleepers or any other foot wears.
Rest of the mechanism is very common one and is operating successfully in daily life.
Therefore, this is the mechanism which is 100% reliable and effective and has the potential to solve and crack this lunar regolith sampling challenge.
At the end, thank you for giving me a platform to showcase my skills and do something constructive in the greatest human expedition of exploring the universe.
Thank You.
Diwakar
Lunar Wheel Regolith Sampling System is a system is an integrated system and not an entirely and exclusively designed new system dedicated to the sampling of the regolith though it is a dedicated sampling system which is a result of the innovation/ slight modification of the present/current landers or rovers landing or wheels technology.
Landers or rovers use certain kind of technology to explore its surrounding (arms in case of landers and rovers itself are dedicated robots for exploration and have robotic arms for certain functional operations).
The proposed design/idea takes the advantage of this feature of the landers or rovers and this makes it valuable sampling system which is not an entirely new sampling system which is mounted/employed on its parent rover or lander. Rather than employing an entire new system this system demands slight modification in the current design of the presently used mars or moon rovers or landers which are in operation right now and this makes it useful and can be used by both landers and rovers for the sampling of the regolith.
This system consists of a wheel system (which is similar to front landing wheel system of the airplanes) which is mounted either separately on rovers or landers or with minor adjustments can be integrated with the present system and thus saves the total weight and power of the system.
In this system, modification begins with the tyre of the wheels (which is of similar type as is being used in the rovers at present). this proposed tyre design consist of no of through holes of various sizes on its surface, which allows the wire rang of regolith to being sampled inside out. holes are of particular size are in particular number, in particular pattern and in particular order are stamped which allows the regolith of wide variety (under the limits of the sample sizes) are collected and sampled simultaneously as due to mechanical properties of the rubber tyre it will compresses while in contact the ground and this will expands the hole which allows the regolith to move inside the wheel, and when the wheel leaves the ground its holes get contracted due to removal of compression load on that part of the tyre and thus the regolith get trapped for ages inside the wheel till it get recovered in the sampling container/cylinder. and due to sizes and arrangement of holes and limit to expansion and contraction of holes (which depends upon the mechanical and chemical properties of the rubber tyre) the regolith also get sampled while getting collected by the wheel. thus, the first sampling is performed along with the depositing/collecting operation of the regolith.
More the wheel will roll on the surface, more the chances to collect the regolith and this may vary according to the sampling site, chosen, the side of the wheel is sufficiently chosen, that it will be able to collect the regolith even at the extreme locations where regolith of desired size, quantity and quality are limited.
A natural rubber padding is provided which is the second layer after the rubber tyre have a small hole punched all over its circumference and has longitudinal cuts which samples the regolith again and allows regolith only of desired quality and its main task is to control the quantity of the regolith entering the wheel. it also acts like a valve for the finer regolith’s which may easily wash out through bigger holes from the wheel tyre if padding is absent.
After two samplings, the regolith moves towards the core of the wheel, the axle. before passing on to the axle, regolith must have to pass through wheel alloy or supporting frame which holds tyre and the axle together. this allow is of frustum type from outside and acts as a sliding pass/or a funnel from inside which collects the regolith from the wheels outer layer and transport it to the axle of the wheel. the frustum type outer layer of the wheel checks the loss of the regolith while transferring/transportation of regolith through the funnel type sliding alloys which has teflon coating on its inside surface.
Axle of the wheel is a hollow conical funnel which allows the flow of regolith from number of passing holes through which the alloy rims are joined. the axle is the integral part of the wheel rim/alloy. the conical shape of the axle guides the regolith in one direction, in the direction of the hub and other side is closed, which is the narrow side and has one mini-spy camera for the monitoring purposes of the regolith.
Now when the regolith has been passed to the axle, it is now free to move to the wheel's arm which is a hollow body, through the hub which joins/supports and derives the wheel by transmitting the power from the deriving motor (which is mounted on the base/board of the rover or lander, and thus therefore there is no requirement of a separate command module as rover/lander can directly control the sampling operations) to the wheel through the wheel arm and this hub is the integral part of the arm which on one side takes the regolith from axle, and form other side transfer it to the hollow arm channel. the hub of the wheel has more than sufficient space to store the regolith till the desired quantity and quality of regolith is being collected.
When the regolith collecting operation is completed (the camera tells the command module about the desired quantity and quality has been achieved or not), the wheel arm is lifted about the roll axes by a rotary motor (through the motor coupling provided, which is directly coupled to the motor and is tightly fixed on the arm frame with the help of tightening bolts), which is the same motor which is used to derive the wheel (a separate motor can be employed as per requirement) and the arm/lunar wheel will rise about the roll axis (which lies on the floor of the rover/lander) and thus the regolith under the influence of the planetary gravity rushes against the rise of the wheel (in the opposite direction). this motion is similar to the recoiling or rewinding of the front landing wheel system of the airplane. this motion is similar to the motion which is followed by the robotic arms of the landers and the rovers which usually do this to keep the mechanism safe form the radiation by winding up/closing their mechanism and storing in the rover's or lander's body. and in addition to it, the pace of this winding/stowing operation is very low due to limited power supply. this proposed idea/system will take advantage of both the motion and its pace and uses it to transfer the regolith to the sampling cylinder from through the wheel arm.
During the lifting/stowing operation of the wheel, the regolith are forced to move against, in the direction opposite to the rising direction and at the entry of the hollow arm channel, there is a sampling tray which separates the rogolithic rocks (of size greater than 1 cm) from the regolithic dust (of size smaller than 1 cm) before the third stage of sampling, where the regolithic rocks are sampled for the maximum numbers allowed in the final sample.
After the regolith passed through the entry of the arm channel and over the sampling tray, it is now exposed to a couple of sudden bends which will force the regolith to change its direction and this bend has major impact on regolithic rocks as due to its higher relative mass with respect to regolithic dust, it will possess higher velocity and the bend has a chance to sample the rocks on the basis of the maximum quantity allowed. the number of regolithic rocks arriving and departing the first bend is monitored by the mini-spy cameras mounted on the hub and on the second bend. Due to the combined analyses and monitoring of both the cameras, the door at the first bend will open/or we can say it get closed (as it opens the passage for the regolithic rocks to get moved out of the arm's channel (into the space again) by moving in and closing the passage, which continues to the arm's channel and to the sampling cylinder) after 20 regolithic rocks passes through the bend and moves forward towards the second bend. the door is mounted such that it will act like a single door for two passes/routes, when the door closes one route, the other gets open automatically.
During in this mean time, when the third sampling operation is being carried in, the regolithic dust will safely and securely get deposited in the arm channel after being sampled by the sampling plate. the geometrical design of the arm and bends are such that regolithic dust will continue to move in the channel without getting involved in the third sampling operation.
When the first camera (which is mounted in the axle) and the second camera (which is mounted on the hub) gives the clearance about the execution of the regolithic rock in the system before the third sampling stage, the third sampling will be halted.
In the meantime, the regolithic rock which is allowed to pass through the third sampling stage and the regolithic dust which passes without being involved in the third sampling stage are free to move through the second bend and into the arm's femur (longest straight channel which joins the wheel to the main frame of the rover or the lander through the deriving motor) under the precise monitoring of the third camera (which is mounted at the second bend) and the weight or density sensing device. when the camera and sensors at the second bend tells that the amount of regolith needed/desired are collected and have passes through the second bend, the rotary motor will operate and the fourth sampling beings with the open of the regolith sampling door. the excess amount, (other than the desired/required regolith sample) is dumped through the door under the influence of the stowing motion of the wheel's arm.
The sampled regolith sample which has passed the fourth stage of sampling, in the meantime is being transported to the sampling cylinder through the arm femur/arm channel ,which is placed just next to the arm (which is placed firmly at its position on the base/floor of the rover/lander), when arm is in a position where whole regolith sample can move/wash out off from the wheel's arm, while rotating along its roll axis.
All the operations like third and fourth sampling is carried out simultaneously with the rotation/stowing operation of the wheel's arm.
Weight and Power:
This proposed sampling system is an integral part of the presently used system which is achieved by the slight modification and whole sampling operation is being carried out under the motion of the presently used system and thus taking advantage of the designed motion and design (structure) of the current system, this system will work with very low power requirement or the whole modified system may use some additional power (which is very less) to overcome the frictional losses or to move the additional mass (which is also very less).
In case of rovers, this system need power to lift the wheel to deposit regolith in the sampling cylinder and in case of landers, it will need power to perform rolling operation on the surface of the planet to collect the regolith. in both cases all other operational requirements are successfully fulfilled by the motion of the existing system, thus this system, uses very less power exclusively for sampling operation.
In terms of weight, this system is just a slight modification of the existing system which when innovated can either needs a little modification which will add some mass or need a replacement with the exiting parts/components (as likely to be in the case of wheel rim/axle) which will again add no to very less mass to the entire system.
Thus, the overall power consumption is very less and weight of the sampling system (exclusive) is very low. moreover, when considered the case where both present systems are operating with the additional sampling system which possess and impose entire new mass and power requirements to the whole system, this proposed system is very good in both ways relatively.
Reliability and Effectiveness.
This proposed system uses very common things which are happening in daily life without any connections in-between them. using an air-less, rubber tyre with holes and slots to collect and sample the regolith is a tested and verified idea which is noble in this field, as this particular, collecting and sampling solution by a rubber material with hole has been tested by millions who have a hole in the sole of their shoes/boot/sleepers or any other foot wears.
Rest of the mechanism is very common one and is operating successfully in daily life.
Therefore, this is the mechanism which is 100% reliable and effective and has the potential to solve and crack this lunar regolith sampling challenge.
At the end, thank you for giving me a platform to showcase my skills and do something constructive in the greatest human expedition of exploring the universe.
Thank You.
Diwakar
Similar models
grabcad
free

NASA Portable Conveyor Sampling Tool
...will be made out of pinned sections (not shown in model), and aluminium for the axles. total mass of sampling system = 0.4-0.5kg.
grabcad
free

ARES Lunar Sampler
...e telescoping scoop arm is used to gently brush regolith over the gradient so that the samples are not damaged before collection.
grabcad
free

Lunar Regolith Collector
...uces the operating cost, power & weight by utilizing the conventional pick and place method being used for sample collection.
grabcad
free

NASA Lunar Sampling System Design Challenge- Option 2
... that arm would handle.
this concept is an extension of my earlier submitted option 1. please review and let me know your views.
grabcad
free

Regolith Scoop Filter
... power. lastly, to manage the temperature of the electronics, the system will use reflective shielding to maintain internal heat.
grabcad
free

INDIE - a self-deploying lunar sampling system
...er 10 watts of power (bucket only). but then... it would need a different name.
more details are available in readme - indie.pdf
grabcad
free

Sampling System for a Lunar Rover
...sampling system for a lunar rover
grabcad
collection and separation of lunar dust and regoliths by use of centrifugal force.
grabcad
free

Simple Sampling system
...le sampling system
grabcad
a simple and effective sampling system which can easily filtre the desired rocks sizes and regolith.
grabcad
free

nasa sample system
..., where sample is delivered through desired path naturally following configured groove with height difference to collection rail.
grabcad
free

Wheel and Tire for robotics wheel
...asses through the centre of the wheel. the engine spins the axle round and round, turning the wheel and moving the vehicle along.
Regolith
3d_sky
free
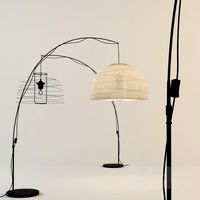
Ikea regolith
...ikea regolith
3dsky
ikea
floor lamp, curvedhttp://www.ikea.com/ru/ru/catalog/products/50103406/
thingiverse
free
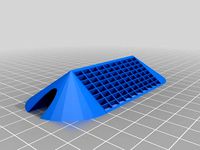
Customizable struts for regolith-shielded dugout houses by drxenocide
...golith.
*edit (2014jun01) added support for model making and sheet building. because if i win, makerbot will want to print one.
thingiverse
free
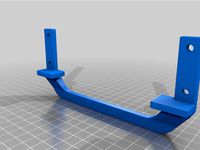
HP V1910-24G Tabletop Stand by Regolith
...006a) switch on my desk and be able to organize patch cables below. foot uses the mounting locations for rack ears. requires two.
thingiverse
free

Replacement knob for Harbor Freight ladder by Regolith
...nob for the folding hinge. printed this in pla and it's held up fine. maybe abs or petg if you want it to be super bombproof.
thingiverse
free
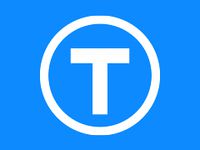
Headrest Maglite Mount by Regolith
...10mm rods). the clip installs by twisting onto the headrest rods, and the maglite adds a rigid connection between the two mounts.
thingiverse
free
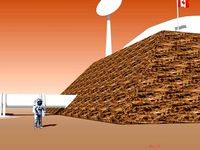
Mars complex: Regolith construction by smichel
...cal factories wii extract oxygen and chlorates from the abundant minerals to fuel the trip back and forth between earth and mars.
3d_sky
free
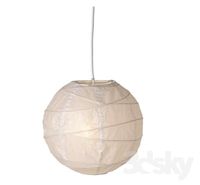
Ikea01
...ikea01 3dsky regolith lamp from ikea...
3d_sky
$8

IKEA / REGOLIT
...ikea / regolit 3dsky lampshade ikea regolith regolit shade diameter: 45...
thingiverse
free
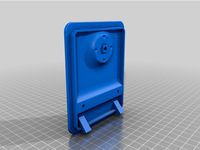
Tekonsha P3 Mount (Toyota Tacoma Gen1) by Regolith
...l using an earlier revision (this version has the mounting screws moved outboard to hold the hoop a little tighter to the panel).
thingiverse
free
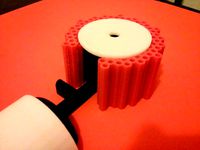
Mars Research Station Two by xmbrst
...habs are printed in black in the photos.) 3d-printed regolith structures -- to provide better radiation and structural protection,...
Lunar
3ddd
free
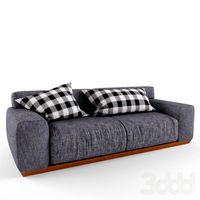
erba lunare
...erba lunare
3ddd
erba
erba lunare
turbosquid
$10
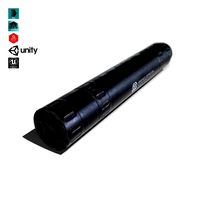
Suppressor Lunar
...quid
royalty free 3d model suppressor lunar for download as on turbosquid: 3d models for games, architecture, videos. (1380407)
3ddd
$1

Lunar lounge
...ounge
3ddd
stellarworks
модель кресла lunar lounge от производителя stellar works. габаритные размеры 850x710x800. 23k полигонов.
turbosquid
$62

Lunar Lander
... free 3d model lunar lander for download as obj, fbx, and lxo on turbosquid: 3d models for games, architecture, videos. (1185844)
turbosquid
$10
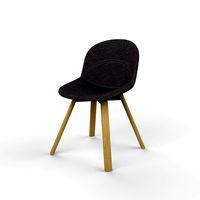
Lunar Chair
...y free 3d model lunar chair for download as 3ds, obj, and dae on turbosquid: 3d models for games, architecture, videos. (1219708)
3ddd
free
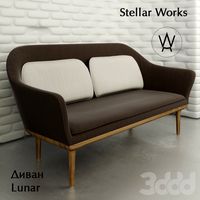
Диван Lunar
...d710xh800mm. в архиве есть текстуры, файлы в 2011 и 2014 версиях и obj-файл. 8,5k полигонов. turbo-/meshsmooth при необходимости.
turbosquid
$39

Lunar Sword
...e 3d model lunar sword for download as max, obj, fbx, and dae on turbosquid: 3d models for games, architecture, videos. (1440758)
turbosquid
$10
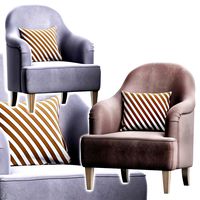
Lunar Armchair
...del lunar armchair by jamni for download as max, fbx, and obj on turbosquid: 3d models for games, architecture, videos. (1566066)
turbosquid
$1

Lunar car
...e 3d model lunar car for download as 3ds, obj, md3, and blend on turbosquid: 3d models for games, architecture, videos. (1209060)
turbosquid
$99

Lunar Plow
... available on turbo squid, the world's leading provider of digital 3d models for visualization, films, television, and games.
Sampling
turbosquid
$15
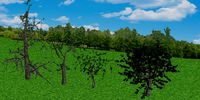
Tree Sample
...royalty free 3d model tree sample for download as max and fbx on turbosquid: 3d models for games, architecture, videos. (1238276)
turbosquid
$9

Blood Sample
... free 3d model blood sample for download as max, obj, and fbx on turbosquid: 3d models for games, architecture, videos. (1305026)
turbosquid
$2

Face Sample
...free 3d model face sample for download as blend, fbx, and obj on turbosquid: 3d models for games, architecture, videos. (1586198)
turbosquid
$3
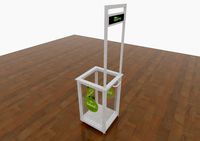
Sampling Bin
... 3d model sampling bin for download as max, fbx, 3ds, and obj on turbosquid: 3d models for games, architecture, videos. (1596035)
turbosquid
$39
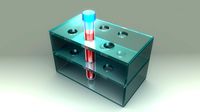
Blood sample
... available on turbo squid, the world's leading provider of digital 3d models for visualization, films, television, and games.
turbosquid
free

monkey sample
... available on turbo squid, the world's leading provider of digital 3d models for visualization, films, television, and games.
3d_export
$5
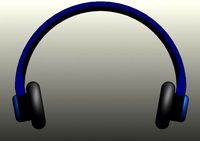
Headphone Sample
...created as a sample using solidworks. the rar file contains .sldprt file and .stl file. the 3d model can be used for 3d printing.
turbosquid
$30
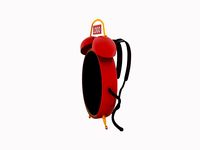
coffee Sampling Bag
...royalty free 3d model coffee sampling bag for download as 3ds on turbosquid: 3d models for games, architecture, videos. (1697356)
turbosquid
$7

Medicine Bottle Sample
...e 3d model medicine bottle sample for download as obj and fbx on turbosquid: 3d models for games, architecture, videos. (1332437)
turbosquid
$10
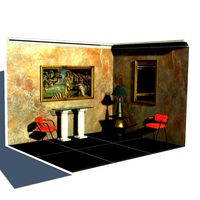
Living Room Sample
...living room sample for download as unitypackage, max, and fbx on turbosquid: 3d models for games, architecture, videos. (1705843)
Wheel
archibase_planet
free
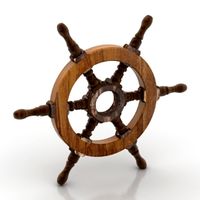
Wheel
...l steering control steering wheel
wheel ship steering wheel n060215 - 3d model (*.gsm+*.3ds+*.max) for exterior 3d visualization.
3d_ocean
$14
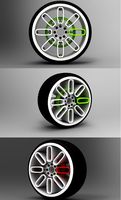
Wheel
...wheel
3docean
car rim car wheel rim wheel
high poly car wheel design. 16,840 polys
3d_export
free

wheel
...wheel
3dexport
wheel
3d_export
free
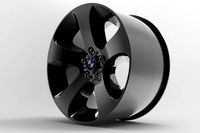
wheel
...wheel
3dexport
wheel
3d_export
free
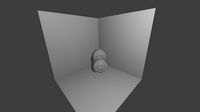
Wheel
...wheel
3dexport
wheel
3d_export
$5

wheel
...wheel
3dexport
wheel for car.
3d_export
$5
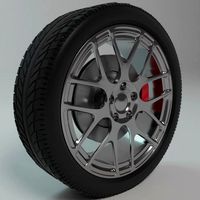
wheel
...wheel
3dexport
car wheel
3d_export
$5

wheel
...wheel
3dexport
car wheel
3d_export
$5
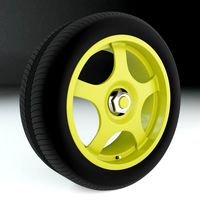
wheel
...wheel
3dexport
car wheel
3d_export
$5
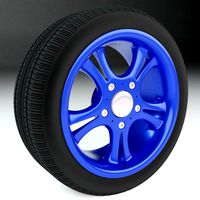
wheel
...wheel
3dexport
car wheel
System
archibase_planet
free
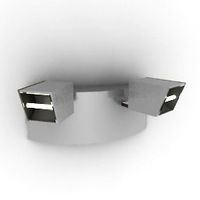
System
...m
archibase planet
fire alarm system fire alarm box
security light system - 3d model (*.gsm+*.3ds) for interior 3d visualization.
archibase_planet
free
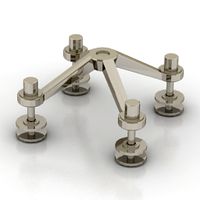
Spider system
...stem spider glass system
spider system to fix glass stefano galli n050912 - 3d model (*.gsm+*.3ds) for interior 3d visualization.
3ddd
$1
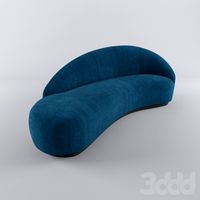
Euforia System
...euforia system
3ddd
euforia
euforia system
3d_export
$50
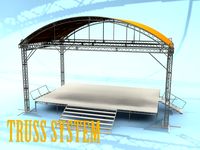
Roof system Truss system 3D Model
...oof system truss system 3d model
3dexport
roof system truss truss stage
roof system truss system 3d model aleksbel 38970 3dexport
3ddd
$1
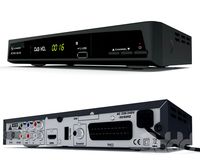
DVD System
...dvd system
3ddd
dvd , schneider
dvd system
design_connected
free
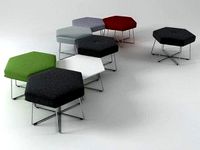
Seating system
...seating system
designconnected
free 3d model of seating system
3d_export
$5
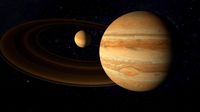
solar system
...solar system
3dexport
solar system in c4d, with 8k nasa textures
3ddd
$1
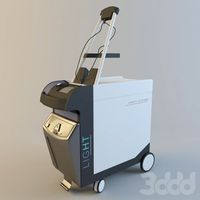
Quanta System
...quanta system
3ddd
медицина
quanta system.
лазерное оборудование для медицинских центров
3d_export
$15
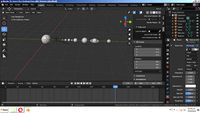
solar system
...nd the other the sun, the earth and the moon, the latter has an animation with camera movement included, the files are in spanish
3d_export
$14
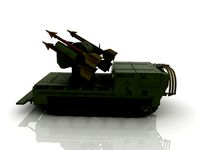
missile system
...missile system
3dexport