GrabCAD
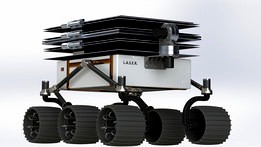
L.A.S.E.R. - Lunar Automotive Sun Energy Redirector
by GrabCAD
Last crawled date: 1 year, 11 months ago
Characteristics
Meet the “Lunar Automotive Sun Energy Redirector”!
L.A.S.E.R. is a tele-operated heliostat system attached to a Rocker-Bogie that is designated for concentrating/redirecting sunlight, illuminating of shadowed areas and thermal management.
Heliostat dimensions: while packed: 1.62 m x 1.2 m x 0.36 m
while deployed: 8.28 m x 1.7 m x 0.13 m
Overall dimensions: while packed: 1.5 m x 1.36 m x 1.99 m
while deployed (standard position): 8.28 m x 3.04 m x 1.99 m
Weight: Heliostat system: 115 kg
Total weight: 475 kg
Reflective area: 1.7 m^2 x 6 = 10.2 m^2
Heliostat system
The architecture chosen for the system design is curtain folding type. 6 mirror panels are folded around a central photovoltaic panel (used while the system is deployed). To reduce the weight, the 4 mm thick reflective plastic sheet was chosen because they are thick enough to support their own weight. The system is operated by motorized hinges (6 pieces) that handle a set of metal sleepers on which the mirrors are installed.
Solar array
The heliostat include a large solar panel (1.32 m^2) that is used while the system is closed. While when deployed, a second photovoltaic is revealed in the center that take the role of the first. This array allows that, when it’s needed or in extreme cases, both can be used to convert energy at the price of two unused mirror panel.
Guidance system
The guide system is composed of 2 axes of rotation perpendicular to each other that allow the orientation of the heliostat system. Taking into account the mass of the system, it was opted for the variant of servomotors that operate a cycloidal reducer, thus offering a benefit regarding the exact accuracy of the system positioning (considered necessary for precise illumination of targets or areas at a greater distance).
Sun tracking
Sun tracking is made via 4 individually encapsulated photoresistors. By regional stimulating of light, the sensor has the ability to locate the direction of origin of the light rays. The sensor is also equipped with its own pitch-rotation axis that allows its perpendicular positioning in the direction of the light source, while the heliostat system can individually change its angle of attack.
External power connector
The system allows continuous charging at the dock station through the 2 embossed strips arranged horizontally on the back of the rover. The docking station is also provided with 2 such horizontal contacts arranged at the same height as the others, so the rover can come into contact with them and thus the power supply can be achieved while it is not deployed. It should be mentioned that the contacts from the docking station are provided with springs that allow a state of continuous pressure exerted towards the supply contacts, eliminating the risk of unwanted interruption of the charging process.
Disclaimer
Even if the theme of the contest was not focused on making the rover model, I took the liberty of designing my own system. It is worth mentioning that the model belongs entirely to me and is made by me. If I had more time I could have prepared a fully functional model with the entire internal organological structure.
Recap
Each actuator and gear is provided with its own insulation jacket with a thickness of 10 mm, the material used being the aerogel (given its own density). This is easily seen in cutaway renderings highlighted with a blue stripe.
In order to reflect as much light as possible to an area as far away as possible, it was decided to choose a rigid reflection surface. A flexible surface requires high tension and even with this, it will not be possible to rise to the quality and quantity of reflection of a rigid planar surface.
Given the large reflective surface and the not so great storage space (taking into account the fact that that volume must be shared with the displacement system) it was considered the best mirror storage system as folding curtains.
In order to keep the assembly of mirrors as simple as possible, a system has been designed to fold as few times as possible (to reduce the increase in the number of actuators and implicitly to reduce the complexity of the model).
The ability of individual focusing of the mirrors in a concave type assembly, in combination with the high precision of the orientation of the system allows a much greater distance of action compared to any other system.
Additionally, the centers of mass of the system were calculated in the most unfavorable conditions: the heliostat system extended horizontally, in front and side of the rover (particular case, that has no application in normal use) and the results are satisfactory: The rover can operate the heliostat system complete safety located on an inclination of 32 °. Obviously, this value increases in regular use.
Also, the height at which the system is positioned while it is open, provides enough ground clearance for the deployment and use of the heliostat system, leaving enough room to terrain unevenness (1.3 m)
In order to prevent the interference of the lunar dust with the mechanical systems, it was avoided the use of any translation systems (telescopic rods, ball screw guidance system, linear roller bearings, linear motors, etc.). Thus, all the operating methods used are exclusively rotational axes (which allows a better sealing against external dust)
Meet the “Lunar Automotive Sun Energy Redirector”!
L.A.S.E.R. is a tele-operated heliostat system attached to a Rocker-Bogie that is designated for concentrating/redirecting sunlight, illuminating of shadowed areas and thermal management.
Heliostat dimensions: while packed: 1.62 m x 1.2 m x 0.36 m
while deployed: 8.28 m x 1.7 m x 0.13 m
Overall dimensions: while packed: 1.5 m x 1.36 m x 1.99 m
while deployed (standard position): 8.28 m x 3.04 m x 1.99 m
Weight: Heliostat system: 115 kg
Total weight: 475 kg
Reflective area: 1.7 m^2 x 6 = 10.2 m^2
Heliostat system
The architecture chosen for the system design is curtain folding type. 6 mirror panels are folded around a central photovoltaic panel (used while the system is deployed). To reduce the weight, the 4 mm thick reflective plastic sheet was chosen because they are thick enough to support their own weight. The system is operated by motorized hinges (6 pieces) that handle a set of metal sleepers on which the mirrors are installed.
Solar array
The heliostat include a large solar panel (1.32 m^2) that is used while the system is closed. While when deployed, a second photovoltaic is revealed in the center that take the role of the first. This array allows that, when it’s needed or in extreme cases, both can be used to convert energy at the price of two unused mirror panel.
Guidance system
The guide system is composed of 2 axes of rotation perpendicular to each other that allow the orientation of the heliostat system. Taking into account the mass of the system, it was opted for the variant of servomotors that operate a cycloidal reducer, thus offering a benefit regarding the exact accuracy of the system positioning (considered necessary for precise illumination of targets or areas at a greater distance).
Sun tracking
Sun tracking is made via 4 individually encapsulated photoresistors. By regional stimulating of light, the sensor has the ability to locate the direction of origin of the light rays. The sensor is also equipped with its own pitch-rotation axis that allows its perpendicular positioning in the direction of the light source, while the heliostat system can individually change its angle of attack.
External power connector
The system allows continuous charging at the dock station through the 2 embossed strips arranged horizontally on the back of the rover. The docking station is also provided with 2 such horizontal contacts arranged at the same height as the others, so the rover can come into contact with them and thus the power supply can be achieved while it is not deployed. It should be mentioned that the contacts from the docking station are provided with springs that allow a state of continuous pressure exerted towards the supply contacts, eliminating the risk of unwanted interruption of the charging process.
Disclaimer
Even if the theme of the contest was not focused on making the rover model, I took the liberty of designing my own system. It is worth mentioning that the model belongs entirely to me and is made by me. If I had more time I could have prepared a fully functional model with the entire internal organological structure.
Recap
Each actuator and gear is provided with its own insulation jacket with a thickness of 10 mm, the material used being the aerogel (given its own density). This is easily seen in cutaway renderings highlighted with a blue stripe.
In order to reflect as much light as possible to an area as far away as possible, it was decided to choose a rigid reflection surface. A flexible surface requires high tension and even with this, it will not be possible to rise to the quality and quantity of reflection of a rigid planar surface.
Given the large reflective surface and the not so great storage space (taking into account the fact that that volume must be shared with the displacement system) it was considered the best mirror storage system as folding curtains.
In order to keep the assembly of mirrors as simple as possible, a system has been designed to fold as few times as possible (to reduce the increase in the number of actuators and implicitly to reduce the complexity of the model).
The ability of individual focusing of the mirrors in a concave type assembly, in combination with the high precision of the orientation of the system allows a much greater distance of action compared to any other system.
Additionally, the centers of mass of the system were calculated in the most unfavorable conditions: the heliostat system extended horizontally, in front and side of the rover (particular case, that has no application in normal use) and the results are satisfactory: The rover can operate the heliostat system complete safety located on an inclination of 32 °. Obviously, this value increases in regular use.
Also, the height at which the system is positioned while it is open, provides enough ground clearance for the deployment and use of the heliostat system, leaving enough room to terrain unevenness (1.3 m)
In order to prevent the interference of the lunar dust with the mechanical systems, it was avoided the use of any translation systems (telescopic rods, ball screw guidance system, linear roller bearings, linear motors, etc.). Thus, all the operating methods used are exclusively rotational axes (which allows a better sealing against external dust)
Similar models
grabcad
free

Lunar Torch
...that provides power for onboard electronics. heliostat is folded similar to simple hand fan and deployed using spring loaded...
grabcad
free

TORCH - Modular Heliostat Array
...flecting area : 21,264 m^2
power estimate from reflecting area : 27,643 kw
solar panel area : 1,772 m^2
weight estimate : 2334 kg
grabcad
free

NASALunarTorch
...tness, requires very less actuators and overall reduces complexity, thus cost too.
kindly see the design report for more details.
grabcad
free

Lunar Sailor (NCKU ISP)
...xsq6wb5ro
https://youtu.be/28gxmpzqx2y
designed by team ncku isp (national cheng kung university, institute of space propulsion)
grabcad
free

Non-Motorized-Deployment Heliostat
... entire package can be scaled down to fit into or onto a rover. more mirrors can be added to make up for reduced reflecting area.
grabcad
free

Lunar Torch with inflatable structure
...in opposition at the mirror film there is a similar system of tie rods. with the inflatable chambers deflated...
grabcad
free

Lunar Torch with inflatable structure
...in opposition at the mirror film there is a similar system of tie rods. with the inflatable chambers deflated...
grabcad
free

Heliostat rover (Ijele)
...ith the necessary dimensions of about 2m by 1.5m an it is then stowed using the harness at the bottom of the primary lunar rover.
grabcad
free

Lunar TORCH Design
...nshots of some of the phases of the heliostat, an stl file of the dormant heliostat, and a video of the heliostat being deployed.
grabcad
free

PenTRAY
...m proximity.
the model has greater flexibility and solar panels which will give the heliostat to work under difficult conditions.
Redirector
thingiverse
free
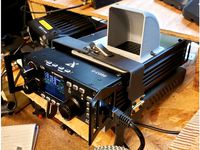
Xiegu G90 Speaker Redirector by tdeagan
...or for the xiegu g90. it was designed to be held in place by the g90-h1 bracket, but tape would also work.
print needs supports.
thingiverse
free
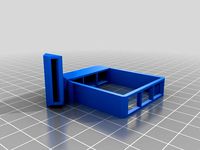
Ormerod 2 fan duct redirector by offbow
...ool the print, i will try and update if i have any problems.
v6:fixed end piece so it doesn't hit the hot end
v5:first upload
thingiverse
free

High-Velocity Air Conditioning Vent Redirector by fejikso
... so it is annoying to feel the high-speed air during the night. i created this redirector that plugs snuggly into the 2in outlet.
thingiverse
free

Fan 40 x 40 mm redirector (cooling Hot-End insulator) by ChaosModder
...ey guys,
i built a redirector for 40 x 40 mm fan. this is because for it to cool the insulator at the hot end.
i hope you like it
thingiverse
free
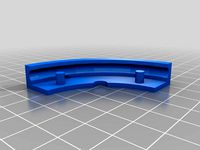
Pull Chain Redirector by TheAndyman
...chain to keep the chain in tension.
the chain guide screws into a wall, and the sleeve captures the chain in the curved groove.
thingiverse
free

servo push rod redirector by cgapeart
...ll be used to accomplish that.
it looks like i probably designed this a bit too small. recommend scaling it up to at least 150%.
thingiverse
free
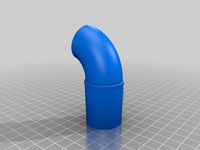
Vacuum cleaner exhaust redirector
...hing, so this gadget redirects the blast upward.
two versions, thin-walled (redirector.stl) and thick-walled (redirector2.stl).
thingiverse
free

Auggie's iPhone 7, 6 and 6S cradle with sound redirector amplifier Landscape and Portrait Modes by Auggie
...d.
it also works as a night table cradle to recharge overnight and to use alarm clock apps in either landscape or portrait modes.
thingiverse
free
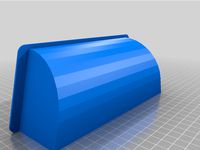
tv sound redirector thing by laserkittydesigns
... tcl tv. should be sizeable in slicer to fit your needs. also i stuck them on with hot glue
printed on prusa mini draft settings.
thingiverse
free

Water Redirector for Waterfall Wall by infinityis
...wall-with-led-illumination.
the opposite orientation can be generated by negatively scaling an axis in the 3d printer software.
Lunar
3ddd
free
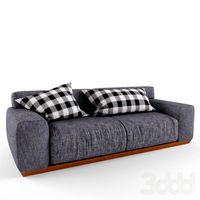
erba lunare
...erba lunare
3ddd
erba
erba lunare
turbosquid
$10
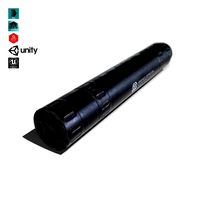
Suppressor Lunar
...quid
royalty free 3d model suppressor lunar for download as on turbosquid: 3d models for games, architecture, videos. (1380407)
3ddd
$1

Lunar lounge
...ounge
3ddd
stellarworks
модель кресла lunar lounge от производителя stellar works. габаритные размеры 850x710x800. 23k полигонов.
turbosquid
$62

Lunar Lander
... free 3d model lunar lander for download as obj, fbx, and lxo on turbosquid: 3d models for games, architecture, videos. (1185844)
turbosquid
$10
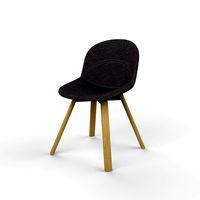
Lunar Chair
...y free 3d model lunar chair for download as 3ds, obj, and dae on turbosquid: 3d models for games, architecture, videos. (1219708)
3ddd
free
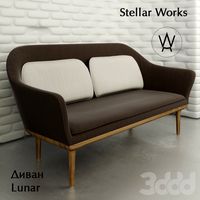
Диван Lunar
...d710xh800mm. в архиве есть текстуры, файлы в 2011 и 2014 версиях и obj-файл. 8,5k полигонов. turbo-/meshsmooth при необходимости.
turbosquid
$39

Lunar Sword
...e 3d model lunar sword for download as max, obj, fbx, and dae on turbosquid: 3d models for games, architecture, videos. (1440758)
turbosquid
$10
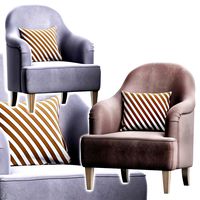
Lunar Armchair
...del lunar armchair by jamni for download as max, fbx, and obj on turbosquid: 3d models for games, architecture, videos. (1566066)
turbosquid
$1

Lunar car
...e 3d model lunar car for download as 3ds, obj, md3, and blend on turbosquid: 3d models for games, architecture, videos. (1209060)
turbosquid
$99

Lunar Plow
... available on turbo squid, the world's leading provider of digital 3d models for visualization, films, television, and games.
Energy
3ddd
free
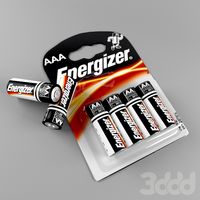
battery energier
...battery energier
3ddd
battery energier , батарейка
battery energier
3ddd
$1
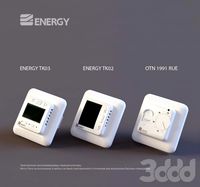
Термостаты ENERGY
... терморегулятор , термостат
термостаты фирмы energy
3d_export
$10
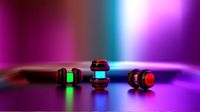
energy capsule
...energy capsule
3dexport
energy capsule
3d_export
$5

energy annon
...energy annon
3dexport
energy cannon
3d_ocean
$6
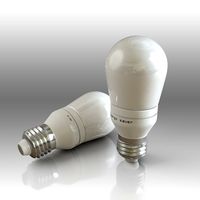
Energy bulb
...energy bulb
3docean
bulb eco ecological energy bulb lamp light lighting
energy bulb.
3d_ocean
$5
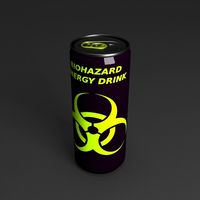
Energy Drink
...energy drink
3docean
biohazard cool drink energy drink fresh ice power soda can
an energy drink can
3d_export
$5
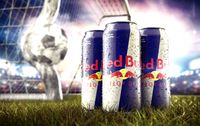
energy drink
...energy drink
3dexport
high poly model of energy drink....
3d_export
$18
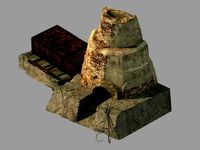
boiler-chemical energy-electricity-thermal energy
...iler-chemical energy-electricity-thermal energy
3dexport
boiler-chemical energy-electricity-thermal energy<br>3ds max 2015
3d_export
$6
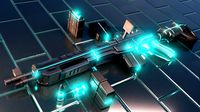
energy - m14
...rom m14, powered by energy that shoots 10 powerful energy away<br>"take it easy, this will kill you without pain"
3ddd
$1

Jacuzzi Energy
...jacuzzi energy
3ddd
джакузи
белая, прямоугольная акриловая ванна jacuzzi energy 180
Sun
3d_export
$5
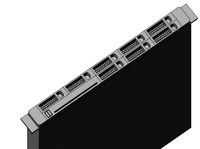
sun oracle sun fire x4170
...sun oracle sun fire x4170
3dexport
sun oracle sun fire x4170
3d_export
$5

sun
...sun
3dexport
3d_export
$20
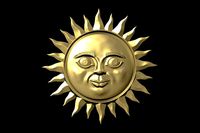
sun
...beautifully. ~ 100,000 for the sun ring ~ 100,000 for the sun face everything in a convenient obj format. dragonwahlnus*gmail*com
turbosquid
free

Sun
...sun
turbosquid
free 3d model sun for download as max on turbosquid: 3d models for games, architecture, videos. (1482222)
3d_ocean
$3

Sun
...ine. .blend end .obj files included. uv unwrapped and material, texture is applied. texture size is 1024×512. sun glow effects...
turbosquid
$25

Sun
...sun
turbosquid
royalty free 3d model sun for download as fbx on turbosquid: 3d models for games, architecture, videos. (1635393)
turbosquid
$3

Sun
...n
turbosquid
royalty free 3d model sun for download as blend on turbosquid: 3d models for games, architecture, videos. (1484318)
3d_export
$12
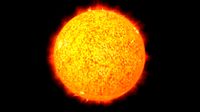
sun model
...sun model
3dexport
3d model sun prop.
turbosquid
free

The Sun
... available on turbo squid, the world's leading provider of digital 3d models for visualization, films, television, and games.
3d_export
$5
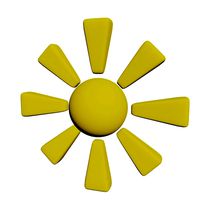
symbol sun
...symbol sun
3dexport
3 d model symbol sun
Automotive
turbosquid
$49

Automotive
... available on turbo squid, the world's leading provider of digital 3d models for visualization, films, television, and games.
3d_export
$6

Automotive test equipment
...automotive test equipment
3dexport
automotive test equipment
turbosquid
$9
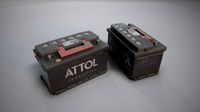
Automotive battery
... 3d model automotive battery for download as ma, obj, and fbx on turbosquid: 3d models for games, architecture, videos. (1407180)
turbosquid
free
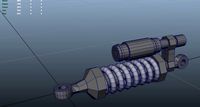
Automotive Suspension
... available on turbo squid, the world's leading provider of digital 3d models for visualization, films, television, and games.
turbosquid
free
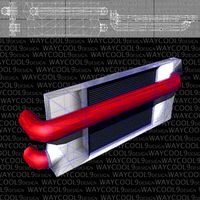
An Automotive Intercooler
... available on turbo squid, the world's leading provider of digital 3d models for visualization, films, television, and games.
turbosquid
free
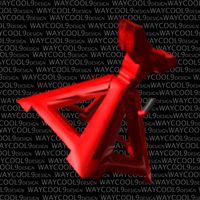
An Automotive Jackstand
... available on turbo squid, the world's leading provider of digital 3d models for visualization, films, television, and games.
turbosquid
free

An Automotive Shock
... available on turbo squid, the world's leading provider of digital 3d models for visualization, films, television, and games.
turbosquid
$99
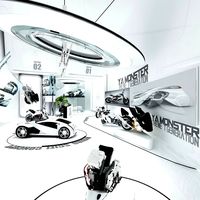
Futuristic Automotive Showroom
...e 3d model futuristic automotive showroom for download as max on turbosquid: 3d models for games, architecture, videos. (1563687)
turbosquid
$49
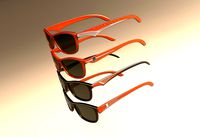
sunglasses automotive style
...sunglasses automotive style for download as max, fbx, and obj on turbosquid: 3d models for games, architecture, videos. (1672628)
turbosquid
$80
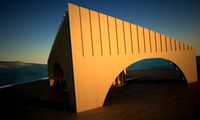
AUTOMOTIVE STUDIO 2011
... available on turbo squid, the world's leading provider of digital 3d models for visualization, films, television, and games.
R
3ddd
$1
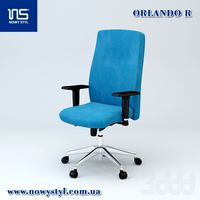
ORLANDO R
...orlando r
3ddd
новый стиль
новый стиль - orlando r
design_connected
$11
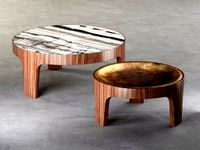
R-Table
...r-table
designconnected
henge r-table computer generated 3d model. designed by castagna, massimo.
design_connected
$7
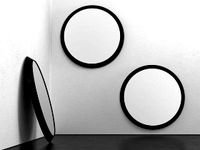
Cone R
...cone r
designconnected
bonaldo cone r computer generated 3d model. designed by pasini, ennio.
3ddd
$1
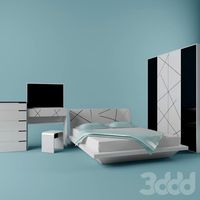
R&B
...r&b
3ddd
r&b
спальный гарнитур r&b;
3d_export
$5
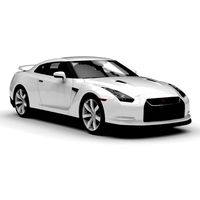
nissan gt-r
...nissan gt-r
3dexport
this is nissan gt-r
turbosquid
$10
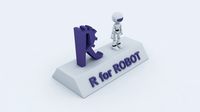
R for ROBOT
...osquid
royalty free 3d model r for robot for download as max on turbosquid: 3d models for games, architecture, videos. (1694233)
turbosquid
$5
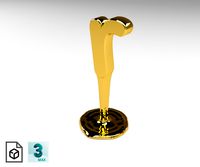
Letter r
...urbosquid
royalty free 3d model letter r for download as max on turbosquid: 3d models for games, architecture, videos. (1408525)
turbosquid
$5
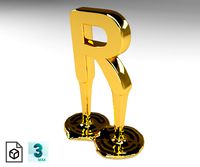
Letter R
...urbosquid
royalty free 3d model letter r for download as max on turbosquid: 3d models for games, architecture, videos. (1408526)
3d_export
$5
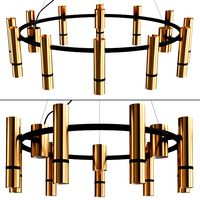
react r
...r 9 lamps (6+3) ø 60 × 21 cm 12 lamps (9+3) ø 80 × 21 cm polys: 208 539 verts: 213 675 https://ru.lampachn.com/react-r-p0551.html
turbosquid
$40
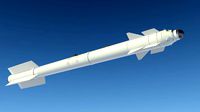
R-73
...uid
royalty free 3d model r-73 for download as blend and fbx on turbosquid: 3d models for games, architecture, videos. (1620664)
E
3ddd
$1
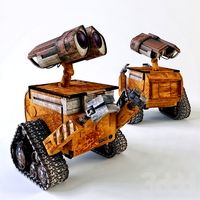
WALL-E
...wall-e
3ddd
wall-e , робот
wall-e
3d_export
$100
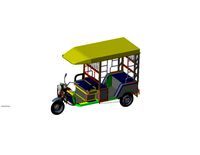
e-rickshaw
...e-rickshaw
3dexport
e-rickshaw- it have 3d model of passenger e-rickshaw
3d_ocean
$12
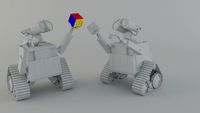
Wall E
...wall e
3docean
character robot wall e
its a 3d model of wall e….
turbosquid
$68
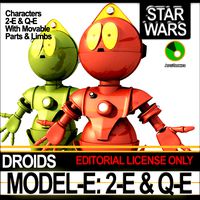
Model-E Droids 2-E Q-E Star Wars
... available on turbo squid, the world's leading provider of digital 3d models for visualization, films, television, and games.
cg_studio
$45
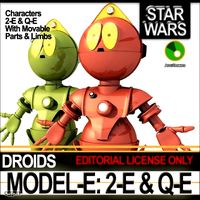
Model-E Droids 2-E Q-E Star Wars3d model
....3ds .c4d .obj .vue - model-e droids 2-e q-e star wars 3d model, royalty free license available, instant download after purchase.
3d_export
$100
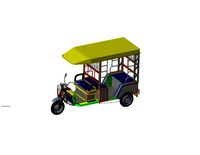
e-rickshaw
...e-rickshaw
3dexport
e-rickshaw design for passenger it have all mechanical component
design_connected
$7
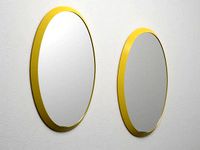
Cone E
...cone e
designconnected
bonaldo cone e computer generated 3d model. designed by pasini, ennio.
3ddd
$1
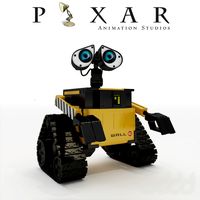
Wall-E NEW
...wall-e new
3ddd
wall-e , робот
wall-e
design_connected
$29
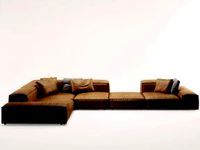
Extrasoft E
...extrasoft e
designconnected
living divani extrasoft e computer generated 3d model. designed by lissoni, piero.
3ddd
$1

E-Turn
... скамейка
современная скамейка фирмы kundalini.
модель e-turn.
дизайнер brodie neil.
размеры: h 42 cm l 185 cm w 54 cm