GrabCAD
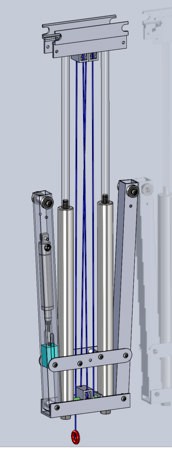
Gas Winch
by GrabCAD
Last crawled date: 1 year, 11 months ago
UPDATE 2016-12-19:
Built this and a compression mechanism using a 20" travel bottle jack from Harbor Freight.
Good and bad.
Good.
The force is there if everything is straight and true and lined up well.
Everything is strong enough to take the loads (a non-trivial task, let me tell you).
Bad.
It is a beast to compress safely or otherwise. Required a mechanism to do safely -- probably not something you can just put into your arbor press and load.
We have not tuned to latch but I can see that there is going to be too much friction left over even with tuning. The latch release machanism is probably not up to the task.
Twisting is the death of this design. The two gas springs are only kept parallel by a single bracket at the bottom. This is not enough to keep the two gas springs from twisting with respect to each other.
Bottom line: these gas springs can store a lot of energy, easily enough to lift a robot at the end of a match, but this mechanism is not the mechanism we are looking for.
New direction needed: one that does not have two struts working in parallel (independent motion allowed, do not require synchronization between the two -- will probably require 2 independent latches, one per spring). One that is more compact.
Goals: fit inside a 2"X2" square tube, robust latch & release, servo activated release (will probably require a latch that is sprung toward unlatch, restrained by a second latch also sprung toward unlatch with THAT latch held in place by a mini-servo Hitec 65 series).
Stay tuned...
Suppose you need to pull a string with ~275lbs over a distance of ~4ft (1100 ft-lbs of work = 1500 N-m = 1500J of work) and suppose you needed it to be released by a pneumatic actuator with 60psi of pressure (max). Well my friend, you've come to the right place. Here is a design that can latch two (yes 2!) 550lbs gas springs and release that force with a small air piston.
Thanks to great input from my friend Artur (and some FEA's Artur is the best), I discovered that the design had some problems. Also, McMaster's CAD for their small air cylinder did not match the real part so it would not fit inside the 3/4" square tube.
Long story short, upped the arms to 1" tube and added a stronger bracket to the top (and better aluminum 2X the yeild).
Will need to design a loading mechanism because it takes over 1600lbs to load. Lots of force, More then the bearings will be happy with...
Stay tuned.
Also, latest ZIP file is a pack and go of the solidworks files and they include drawings (very simple ones).
Built this and a compression mechanism using a 20" travel bottle jack from Harbor Freight.
Good and bad.
Good.
The force is there if everything is straight and true and lined up well.
Everything is strong enough to take the loads (a non-trivial task, let me tell you).
Bad.
It is a beast to compress safely or otherwise. Required a mechanism to do safely -- probably not something you can just put into your arbor press and load.
We have not tuned to latch but I can see that there is going to be too much friction left over even with tuning. The latch release machanism is probably not up to the task.
Twisting is the death of this design. The two gas springs are only kept parallel by a single bracket at the bottom. This is not enough to keep the two gas springs from twisting with respect to each other.
Bottom line: these gas springs can store a lot of energy, easily enough to lift a robot at the end of a match, but this mechanism is not the mechanism we are looking for.
New direction needed: one that does not have two struts working in parallel (independent motion allowed, do not require synchronization between the two -- will probably require 2 independent latches, one per spring). One that is more compact.
Goals: fit inside a 2"X2" square tube, robust latch & release, servo activated release (will probably require a latch that is sprung toward unlatch, restrained by a second latch also sprung toward unlatch with THAT latch held in place by a mini-servo Hitec 65 series).
Stay tuned...
Suppose you need to pull a string with ~275lbs over a distance of ~4ft (1100 ft-lbs of work = 1500 N-m = 1500J of work) and suppose you needed it to be released by a pneumatic actuator with 60psi of pressure (max). Well my friend, you've come to the right place. Here is a design that can latch two (yes 2!) 550lbs gas springs and release that force with a small air piston.
Thanks to great input from my friend Artur (and some FEA's Artur is the best), I discovered that the design had some problems. Also, McMaster's CAD for their small air cylinder did not match the real part so it would not fit inside the 3/4" square tube.
Long story short, upped the arms to 1" tube and added a stronger bracket to the top (and better aluminum 2X the yeild).
Will need to design a loading mechanism because it takes over 1600lbs to load. Lots of force, More then the bearings will be happy with...
Stay tuned.
Also, latest ZIP file is a pack and go of the solidworks files and they include drawings (very simple ones).
Similar models
thingiverse
free
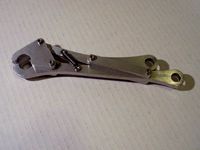
Four Bar Mechanism Release Latch by LucidOne
...m load. always design with a reasonable factor of safety. don't be dumb, be safe.
http://www.youtube.com/watch?v=oqeoplosnlg
grabcad
free

Spring-loaded latch of movable mechanisms
...spring-loaded latch of movable mechanisms
grabcad
spring-loaded latch of movable mechanisms
grabcad
free

Spring-loaded latches
...ixed by toothed spring-loaded latches. the advantages of this design are the simplicity, reliability and safety of the mechanism.
grabcad
free

Bolt and Latch Mechanism with Nichrome Burn-Wire Release
...ch provides preload to the two interfacing satellite segments.
please see our attached pdf for further explanation and analysis.
grabcad
free

Better Gas Winch
...stall torque at 6v. there are other servos in similar sizes that have 2-4x the torque. will investigate these...
grabcad
free

Latch , shock , tight
...to the lock direction ¼ second apart and the
amount of force can be set easily using a screw and lock nut to pressure the
springs
grabcad
free

LATCH ASSEMBLY
...d consumer goods. they are used in doors, cabinets, windows, and other enclosures where a secure fastening mechanism is required.
grabcad
free

Spring Mechanism
...ng the application of the required 200 n maximum clamping force between the plates. four springs are used throughout the closure.
thingiverse
free
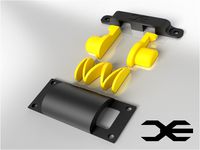
Spring-loaded latching mechanism
....com/thing:3969571
designed with freecad, quickly rendered with cadrays.
conceivably engineering - little competence, big smiles.
thingiverse
free
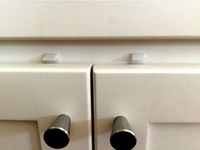
Pushbutton Child Safety Latch for Cabinets by jbramel
... if you use a more brittle plastic like pla, be careful not to break the parts when assembling the sliding mechanism (see below).
Winch
3d_export
$10
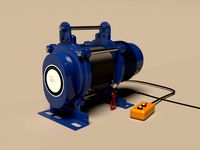
winch
...winch
3dexport
turbosquid
$15
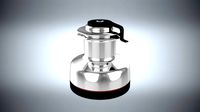
winch
...ty free 3d model winch for download as 3ds, ige, obj, and 3dm on turbosquid: 3d models for games, architecture, videos. (1355394)
3ddd
$1
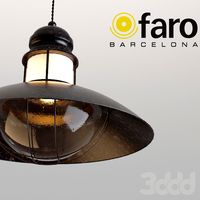
Faro Winch
...t lamphttp://www.faro.es/es/productos/winch-lampara-colgante-marron/
polyrate: 23679
в архиве присутствуют fbx и obj.
turbosquid
$30

Winch
...ree 3d model winch for download as ma, max, obj, fbx, and stl on turbosquid: 3d models for games, architecture, videos. (1368556)
3ddd
$1
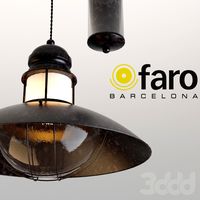
Faro Winch
...://www.faro.es/es/productos/winch-lampara-colgante-con-peso-marron/
polyrate: 238187
в архиве присутствуют fbx и obj.
3ddd
$1

Faro Winch
...ttp://www.faro.es/es/productos/winch-lampara-aplique-marron-h-350mm/
polyrate: 13307
в архиве присутствуют fbx и obj.
3ddd
$1
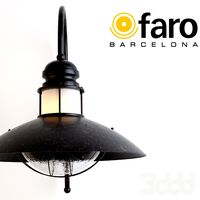
Faro Winch
...ttp://www.faro.es/es/productos/winch-lampara-aplique-marron-h-460mm/
polyrate: 13687
в архиве присутствуют fbx и obj.
turbosquid
$15
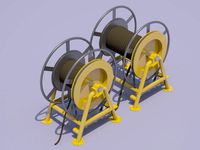
Rope Winches
...squid
royalty free 3d model rope winches for download as max on turbosquid: 3d models for games, architecture, videos. (1415993)
turbosquid
$10
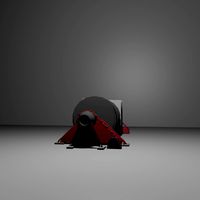
Winche(cabrestante)
...ee 3d model winche(cabrestante) for download as fbx and blend on turbosquid: 3d models for games, architecture, videos. (1376679)
turbosquid
$12
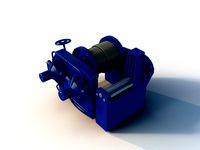
Stern Winch
...y free 3d model stern winch for download as max, fbx, and obj on turbosquid: 3d models for games, architecture, videos. (1591899)
Gas
archibase_planet
free
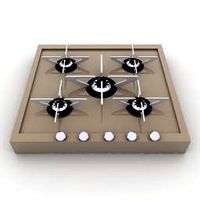
Gas
...gas
archibase planet
kitchen range gas stove cooker
gas - 3d model (*.gsm+*.3ds) for interior 3d visualization.
archibase_planet
free
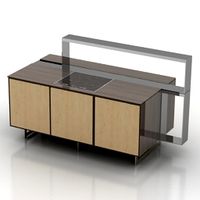
Gas-stove
...e
archibase planet
gas-stove gas cooker kitchen-range gas stove
gas-stove - 3d model (*.gsm+*.3ds) for interior 3d visualization.
archibase_planet
free
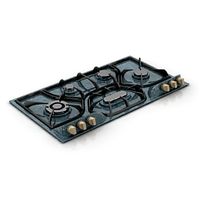
Gas stove
...ase planet
gas stove kitchen-range gas-stove gas cooker
gas stove n280711 - 3d model (*.gsm+*.3ds) for interior 3d visualization.
archibase_planet
free
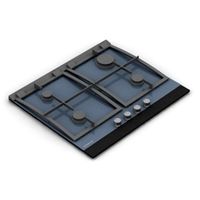
Gas stove
...e planet
gas stove gas cooker kitchen-range gas-stove
gas stove siemens n230912 - 3d model (*.3ds) for interior 3d visualization.
archibase_planet
free
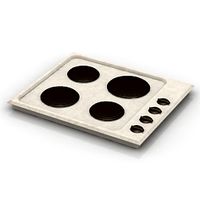
Gas stove
...ase planet
gas stove kitchen-range gas-stove gas cooker
gas stove n201211 - 3d model (*.gsm+*.3ds) for interior 3d visualization.
archibase_planet
free
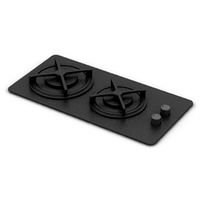
Gas stove
...ase planet
gas stove kitchen-range gas-stove gas cooker
gas stove n210512 - 3d model (*.gsm+*.3ds) for interior 3d visualization.
archibase_planet
free
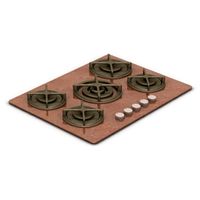
Gas stove
...ase planet
gas stove gas cooker kitchen-range gas-stove
gas stove n170912 - 3d model (*.gsm+*.3ds) for interior 3d visualization.
archibase_planet
free

Gas stove
...ase planet
gas stove gas cooker kitchen-range gas-stove
gas stove n310313 - 3d model (*.gsm+*.3ds) for interior 3d visualization.
archibase_planet
free
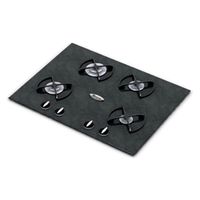
Gas stove
...ase planet
gas stove gas cooker kitchen-range gas-stove
gas stove n110814 - 3d model (*.gsm+*.3ds) for interior 3d visualization.
archibase_planet
free
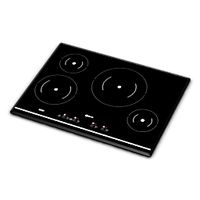
Gas stove
...ase planet
gas stove gas cooker kitchen-range gas-stove
gas stove n111014 - 3d model (*.gsm+*.3ds) for interior 3d visualization.