GrabCAD
![[FreeCAD] Vacuum Lifting System - Venturi Type - Final Year Project](/previews/6148979.jpg)
[FreeCAD] Vacuum Lifting System - Venturi Type - Final Year Project
by GrabCAD
Last crawled date: 1 year, 11 months ago
PROJECT REPORT : https://mega.nz/file/7E5CxCiL#JFj6YiENNaBOzImBemI9ndOQH7nCULL36oFwGbRnMRU
This is my Final Year Project at the university. The objective is to lift a 30kg Class D Gypsum Block, and this end-effector can be used by a robotic arm to build a partition wall.
The design was carried out almost entirely in FreeCAD. A2Plus workbench was used to create the assemblies.
The following parts were used for this project:
LIFTING FUNCTIONALITY:
1. Vacuum Ejector : CV-25HS (1 Piece)
2. Suction Cups: Flat, 125mm - SMC ZPT 125-H (3 Pieces)
3. Filter: SMC ZFC-200 (3 Pieces)
SAFETY FEATURE:
1. Ropes: 4mm thick, 0.9m long, terminated at both ends.
2. 40mm long Aluminum Profile to guide screw
-Function: Locks and releases the rope of the safety feature
3. Solenoid Actuator: 10mm stroke, 12V DC
-Function: Electrically-operated Lock and Unlock mechanism for the removable end of the rope
4. Arduino: Controls the Solenoid Actuators by buttons and separately by magnetic reed switches
5. Magnetic Reed Switch: 10mm x 1.8mm.
-Function: Magnet attached to rope termination. Used by Arduino to semi-automate the locking process. The rope can be locked by the operator with just one hand.
6. Relay Module: 8-channel, used to operate the 12V solenoid actuators.
END EFFECTOR FRAME:
1. 2020 Aluminium Profiles : 55cm, 65cm, 38cm, 16cm, 4cm
2. Aluminium Plate: Custom-ordered, fits SMC ZPT direct-mount fittings. Through holes without threading.
CREDITS:
Two parts were not designed by me
1. Zachary Nash designed the 8-channel Relay Module drawing I used
2. Sedanur Kirci designed the Arduino Uno drawing I used.
This is my Final Year Project at the university. The objective is to lift a 30kg Class D Gypsum Block, and this end-effector can be used by a robotic arm to build a partition wall.
The design was carried out almost entirely in FreeCAD. A2Plus workbench was used to create the assemblies.
The following parts were used for this project:
LIFTING FUNCTIONALITY:
1. Vacuum Ejector : CV-25HS (1 Piece)
2. Suction Cups: Flat, 125mm - SMC ZPT 125-H (3 Pieces)
3. Filter: SMC ZFC-200 (3 Pieces)
SAFETY FEATURE:
1. Ropes: 4mm thick, 0.9m long, terminated at both ends.
2. 40mm long Aluminum Profile to guide screw
-Function: Locks and releases the rope of the safety feature
3. Solenoid Actuator: 10mm stroke, 12V DC
-Function: Electrically-operated Lock and Unlock mechanism for the removable end of the rope
4. Arduino: Controls the Solenoid Actuators by buttons and separately by magnetic reed switches
5. Magnetic Reed Switch: 10mm x 1.8mm.
-Function: Magnet attached to rope termination. Used by Arduino to semi-automate the locking process. The rope can be locked by the operator with just one hand.
6. Relay Module: 8-channel, used to operate the 12V solenoid actuators.
END EFFECTOR FRAME:
1. 2020 Aluminium Profiles : 55cm, 65cm, 38cm, 16cm, 4cm
2. Aluminium Plate: Custom-ordered, fits SMC ZPT direct-mount fittings. Through holes without threading.
CREDITS:
Two parts were not designed by me
1. Zachary Nash designed the 8-channel Relay Module drawing I used
2. Sedanur Kirci designed the Arduino Uno drawing I used.
Similar models
grabcad
free
![[FreeCAD] 100mm Vacuum Suction Cup - Nitrile](/t/5619798.jpg)
[FreeCAD] 100mm Vacuum Suction Cup - Nitrile
...but decent for illustration.
i have based it on an smc-branded suction cup, i believe it is from the smc zpt suction cup series.
3d_export
$10
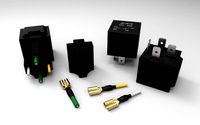
relay jd1912 12v 40a with connector
...and a standard connector with terminals for this and similar relays. using this model in the layout of the...
grabcad
free

door lock solenoid driver
...door lock solenoid driver
grabcad
door lock solenoid driver using relays
grabcad
free

LED and REED console on the handlebar
...bcad
led and reed console on the handlebar
3 leds for 3 different functions control
2 reed for 2 functions to switch with magnet
grabcad
free

ROBOT END EFFECTOR
.... pneumatic actuators were replaced with electric actuators. this allowed multiple sizes of bottles to be ran during operations.
grabcad
free

Pneumatic folding table on 2 sides.
...near solenoid actuators.
2 linear solenoid actuator, 10mm stroke, 12v dc 1a, pull type
1 compact cylinder stroke 50mm metal work
thingiverse
free

Case for Arduino Uno and 1 or 2 Relays by kabeza
...abeza
thingiverse
this case is designed to contain an arduino one and a standard relay
now also with the freecad source files!!!
grabcad
free

Linear Solenoid Actuator
...linear solenoid actuator
grabcad
linear solenoid actuator, 10mm stroke, 12v dc 1a, pull type
grabcad
free

Vacuum Lifter
...vacuum lifter
grabcad
vacuum operator hoist end effector. cad files are property of my client, and not available.
grabcad
free

Solenoid Lock
...omation in security systems. the model consists of a dynamic spring, and is 1:1 full scale model of those commercially available.
Venturi
3d_ocean
$2
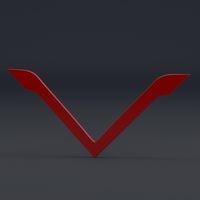
Venturi Logo
...s) .images previews were rendered with blender internal render(cycles). format:(.3ds)/(.obj)/(.blend) .blender:face(6432)/vert...
turbosquid
$179
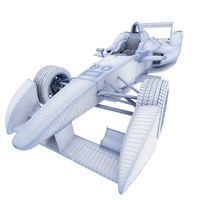
Formula E Venturi
... available on turbo squid, the world's leading provider of digital 3d models for visualization, films, television, and games.
turbosquid
$18
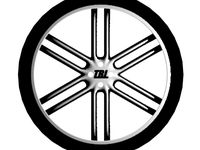
TBL Venturi rim
... available on turbo squid, the world's leading provider of digital 3d models for visualization, films, television, and games.
3d_export
$9

Venturi Logo 3D Model
...e part of avto transport 3d model logo emblem detailed high quality c4d obj lwo 3ds
venturi logo 3d model rmodeler 58786 3dexport
turbosquid
$175

Venturi Formula E 2020
...ormula e 2020 for download as ma, 3ds, obj, c4d, fbx, and dae on turbosquid: 3d models for games, architecture, videos. (1490412)
turbosquid
$179

Formula E Season 3 Venturi
... free 3d model formula e season 3 venturi for download as max on turbosquid: 3d models for games, architecture, videos. (1244991)
turbosquid
$179
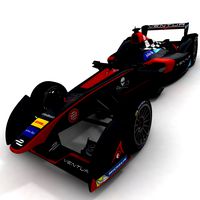
Formula E Season 2 Venturi
... available on turbo squid, the world's leading provider of digital 3d models for visualization, films, television, and games.
humster3d
$75

3D model of Venturi 260 LM 1994
...detailed 3d model of venturi 260 lm 1994 in various file formats. all our 3d models were created maximally close to the original.
3d_export
$6

venturi pfister valves-02
...imension: 26 cm x 26cm x 41cm<br>version vray: 3.6 corona: 4.1<br>unwrap: yes<br>formats: 3ds max 2012, fbx,obj
3d_export
$8

venturi pfister valves-01
...sion: 140 cm x 60 cm x 60 cm<br>version vray: 3.6 corona: 4.1<br>unwrap: yes<br>formats: 3ds max 2012, fbx, obj
Freecad
3d_export
$160
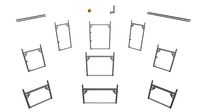
speedyscaf assembly frames
...for example guardrail hook travel. they were designed with freecad and the item textures svg contains all fcstd files...
3d_export
$5

Ornament Element Molding 06
...and vertexs: polys:2 378 verts:2 664 formats: 3ds max 2015,blender,cinema4d,obj,fbx,stl,freecadrhino enjoy 3d modeling good...
3d_export
$90
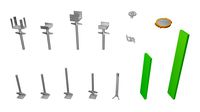
allround scaffolding base plates
...travel of base plate 60. they were designed with freecad and the item svg textures contains all fcstd files...
3d_export
$60
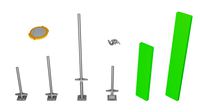
speedyscaf base plates
...travel of base plate 60. they were designed with freecad and the item svg textures contains all fcstd files...
3d_export
$15

Furniture Collection
...and vertexs: polys:89 794 verts:102 149 formats: 3ds max 2015,blender,cinema4d,obj,fbx,stl,freecadrhino warning:dont forget to active turbosmooth after final modeling. enjoy...
3d_export
$15
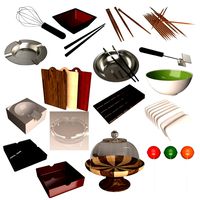
Food and Tableware Collection
...and vertexs: polys:209 451 verts:206 977 formats: 3ds max 2015,blender,cinema4d,obj,fbx,stl,freecadrhino warning:dont forget to active turbosmooth after final modeling. enjoy...
3d_export
$49
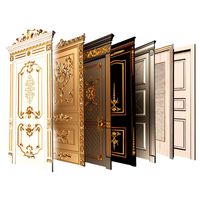
Door and Accessories Collection
...polys:3 633 242 verts:3 746 968 formats: 3ds max 2015,blender,cinema4d,obj,fbx,stl,freecadrhino warning:dont forget to active turbosmooth after final modeling. enjoy...
3d_export
$39

Classic Frame and Mirror Collection
...324 698 verts: 2 392 831 formats: 3ds max 2015,blender,cinema4d,obj,fbx,stl,freecadrhino warning:dont forget to active turbosmooth after final modeling. enjoy...
3d_export
$29
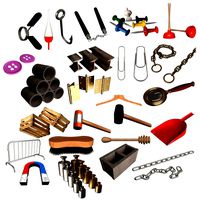
Houseware and Industrial Objects Collection
...polys:1 036 349 verts:1 076 683 formats: 3ds max 2015,blender,cinema4d,obj,fbx,stl,freecadrhino warning:dont forget to active turbosmooth after final modeling. enjoy...
3d_export
$19
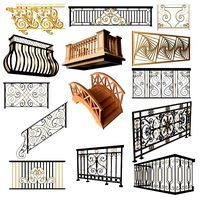
Railing Balcony and Footbridge Collection
...polys:2 739 216 verts:2 753 693 formats: 3ds max 2015,blender,cinema4d,obj,fbx,stl,freecadrhino warning:dont forget to active turbosmooth after final modeling. enjoy...
Vacuum
archibase_planet
free

Vacuum cleaner
...cuum cleaner vacuum hoover exhauster
vacuum cleaner stefano galli n250213 - 3d model (*.gsm+*.3ds) for interior 3d visualization.
3d_export
$12

vacuum cleaner
...vacuum cleaner
3dexport
vacuum cleaner fo houses
3ddd
$1

Vacuum Cleaner
...vacuum cleaner
3ddd
пылесос
vacuum cleaner + obj + textures
3d_export
$170
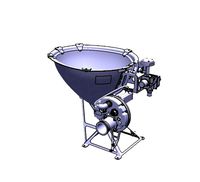
VACUUM BOWL
...vacuum bowl
3dexport
3d_export
$5
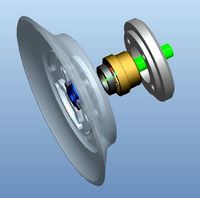
Bracket vacuum 3D Model
...bracket vacuum 3d model
3dexport
vacuum
bracket vacuum 3d model bkl1989 63086 3dexport
3d_export
$50

Vacuum Cleaner 3D Model
...vacuum cleaner 3d model
3dexport
vacuum cleaner
vacuum cleaner 3d model kaxa3d 12593 3dexport
3d_export
$5

vacuum cleaner
...vacuum cleaner
3dexport
diameter 32 mm
archive3d
free
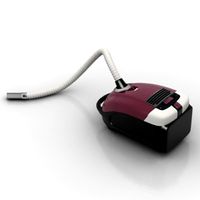
Vacuum cleaner 3D Model
...er
vacuum cleaner stefano galli n250213 - 3d model (*.gsm+*.3ds) for interior 3d visualization.
turbosquid
$69

vacuum furnaces
... available on turbo squid, the world's leading provider of digital 3d models for visualization, films, television, and games.
turbosquid
$59
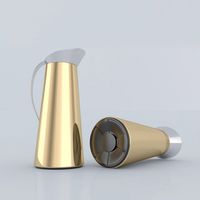
Vacuum Italian
... available on turbo squid, the world's leading provider of digital 3d models for visualization, films, television, and games.
Lifting
archibase_planet
free
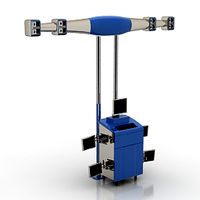
Lift
...lift
archibase planet
lift hoist car lift
lift 1 - 3d model (*.3ds) for interior 3d visualization.
archibase_planet
free
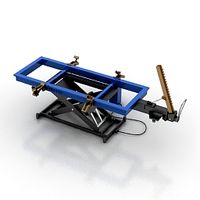
Lift
...lift archibase planet lift lifting jack autohoist lift 2 - 3d model (*.gsm+*.3ds) for...
archibase_planet
free

Lift
...lift
archibase planet
lift autohoist car lift hoist
lift 3 - 3d model (*.gsm+*.3ds) for interior 3d visualization.
3d_ocean
$21
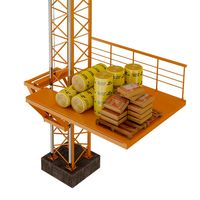
Lift
...lift
3docean
crane industrial lift loader machine outdoor work
lifts with building materials
archibase_planet
free
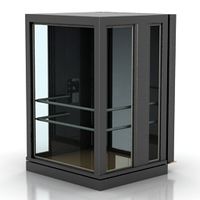
Lift
...lift
archibase planet
lift elevator
lift n050713 - 3d model (*.gsm+*.3ds) for interior 3d visualization.
archibase_planet
free
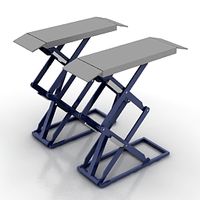
Lift
...lift
archibase planet
lift autohoist hoist
lift for car n240611 - 3d model (*.3ds) for interior 3d visualization.
archibase_planet
free
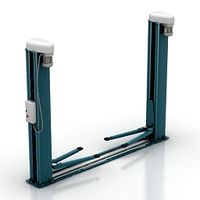
Lift
...lift
archibase planet
lift autohoist hoist
lift for car n020711 - 3d model (*.gsm+*.3ds) for interior 3d visualization.
archibase_planet
free
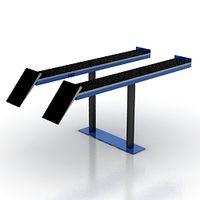
Lift
...lift
archibase planet
autohoist lift hoist
lift car 2 n150111 - 3d model (*.gsm+*.3ds) for interior 3d visualization.
archibase_planet
free
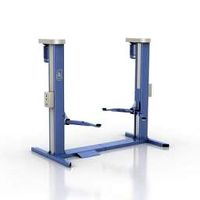
Lift
...lift
archibase planet
car lift car elevator hoist
lift n090709 - 3d model (*.gsm+*.3ds) for interior 3d visualization.
archibase_planet
free
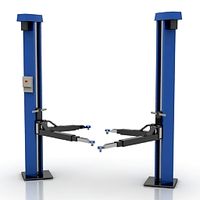
Lift
...lift
archibase planet
lift hoist elevator
lift car 1 n150111 - 3d model (*.gsm+*.3ds) for interior 3d visualization.
Final
3ddd
$1
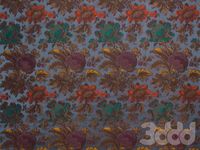
Ardecora-Finale
...ardecora-finale
3ddd
ardecora
ткань итальянского производителя ardecora, артикул finale. в архиве 7 цветов. ткань портьерная.
turbosquid
$3
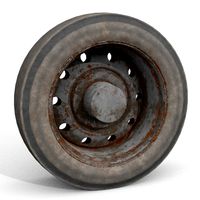
Wheel Final
...osquid
royalty free 3d model wheel final for download as fbx on turbosquid: 3d models for games, architecture, videos. (1364402)
turbosquid
free
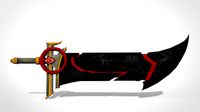
Final Sword
...osquid
royalty free 3d model final sword for download as max on turbosquid: 3d models for games, architecture, videos. (1428573)
turbosquid
$16
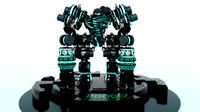
Yeti final
...lty free 3d model yeti final for download as ma, obj, and fbx on turbosquid: 3d models for games, architecture, videos. (1374065)
turbosquid
$180
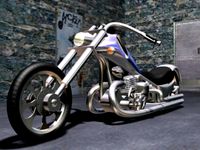
moto final
... available on turbo squid, the world's leading provider of digital 3d models for visualization, films, television, and games.
turbosquid
$80
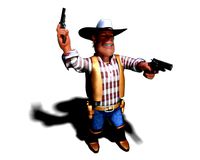
final cowboy.max
... available on turbo squid, the world's leading provider of digital 3d models for visualization, films, television, and games.
turbosquid
$36
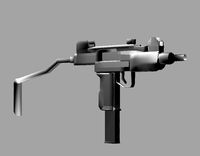
Final UZI
... available on turbo squid, the world's leading provider of digital 3d models for visualization, films, television, and games.
turbosquid
$25
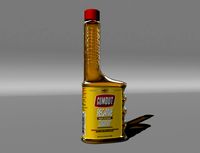
Gumout Final
... available on turbo squid, the world's leading provider of digital 3d models for visualization, films, television, and games.
turbosquid
$15
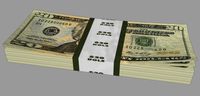
money finals
... available on turbo squid, the world's leading provider of digital 3d models for visualization, films, television, and games.
turbosquid
$15
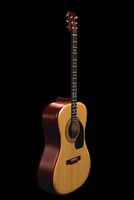
guitar final
... available on turbo squid, the world's leading provider of digital 3d models for visualization, films, television, and games.
Year
turbosquid
$29

New Year
...urbosquid
royalty free 3d model new year for download as max on turbosquid: 3d models for games, architecture, videos. (1483853)
3ddd
$1
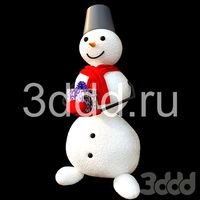
DDD NEW YEAR
...ddd new year
3ddd
3ddd new year
3ddd
$1
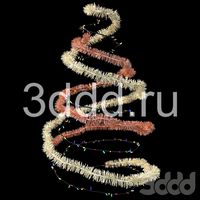
DDD NEW YEAR
...ddd new year
3ddd
3ddd new year
3d_export
$5

new year
...new year
3dexport
3d_export
$5
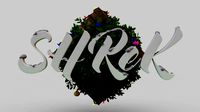
new year
...new year
3dexport
3d_ocean
$4
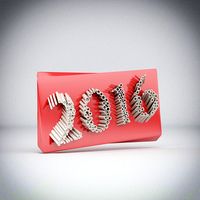
New Year
...vray it come with these file 3dsmax 2016 2015 2014 2013 maya 2016 obj blender c4d stl for 3d print 3ds fbx keyshot happy new year
3d_ocean
$4
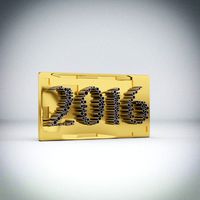
New Year
...vray it come with these file 3dsmax 2016 2015 2014 2013 maya 2016 obj blender c4d stl for 3d print 3ds fbx keyshot happy new year
3d_ocean
$4
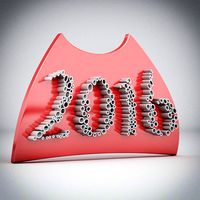
New Year
...vray it come with these file 3dsmax 2016 2015 2014 2013 maya 2016 obj blender c4d stl for 3d print 3ds fbx keyshot happy new year
3d_ocean
$4
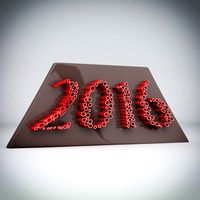
New Year
...vray it come with these file 3dsmax 2016 2015 2014 2013 maya 2016 obj blender c4d stl for 3d print 3ds fbx keyshot happy new year
3d_ocean
$4
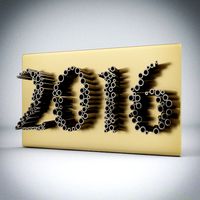
New Year
...vray it come with these file 3dsmax 2016 2015 2014 2013 maya 2016 obj blender c4d stl for 3d print 3ds fbx keyshot happy new year
System
archibase_planet
free
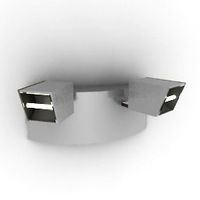
System
...m
archibase planet
fire alarm system fire alarm box
security light system - 3d model (*.gsm+*.3ds) for interior 3d visualization.
archibase_planet
free
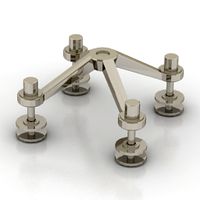
Spider system
...stem spider glass system
spider system to fix glass stefano galli n050912 - 3d model (*.gsm+*.3ds) for interior 3d visualization.
3ddd
$1
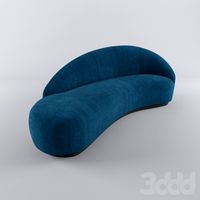
Euforia System
...euforia system
3ddd
euforia
euforia system
3d_export
$50
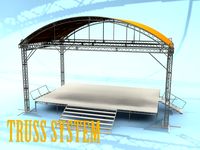
Roof system Truss system 3D Model
...oof system truss system 3d model
3dexport
roof system truss truss stage
roof system truss system 3d model aleksbel 38970 3dexport
3ddd
$1
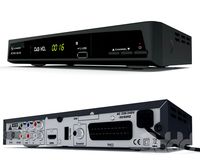
DVD System
...dvd system
3ddd
dvd , schneider
dvd system
design_connected
free
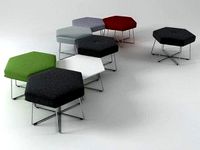
Seating system
...seating system
designconnected
free 3d model of seating system
3d_export
$5
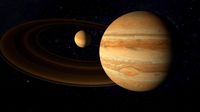
solar system
...solar system
3dexport
solar system in c4d, with 8k nasa textures
3ddd
$1
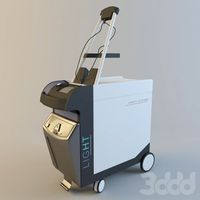
Quanta System
...quanta system
3ddd
медицина
quanta system.
лазерное оборудование для медицинских центров
3d_export
$15
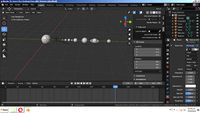
solar system
...nd the other the sun, the earth and the moon, the latter has an animation with camera movement included, the files are in spanish
3d_export
$14
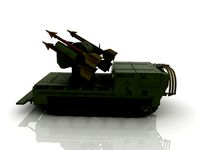
missile system
...missile system
3dexport
Type
3d_export
$5
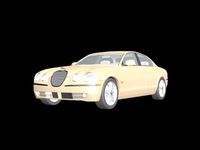
s type
...s type
3dexport
s type formats max 3ds obj stl
3d_export
$5
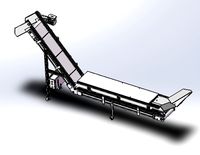
l-type conveyor
...l-type conveyor
3dexport
l-type conveyor
3d_export
$5

volkswagen type 2
...volkswagen type 2
3dexport
volkswagen type 2
turbosquid
$150
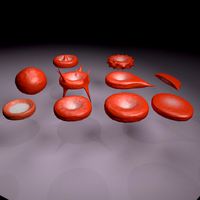
RBC types
...osquid
royalty free 3d model rbc types for download as blend on turbosquid: 3d models for games, architecture, videos. (1343563)
turbosquid
$1
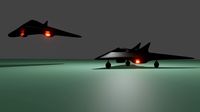
B-Type
...urbosquid
royalty free 3d model b-type for download as blend on turbosquid: 3d models for games, architecture, videos. (1609608)
3ddd
$1
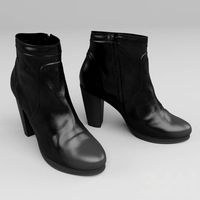
shoes type A
...shoes type a
3ddd
туфли
shoes
turbosquid
$39
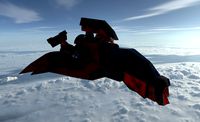
R-type
...oyalty free 3d model r-type for download as max, obj, and fbx on turbosquid: 3d models for games, architecture, videos. (1303675)
turbosquid
$5
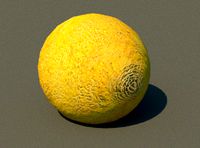
melon type
...ee 3d model melon galia type for download as ma, fbx, and obj on turbosquid: 3d models for games, architecture, videos. (1557188)
3d_export
free
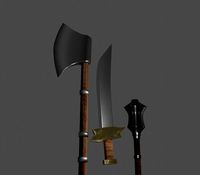
three different type
...three different type
3dexport
three different type: mace, axe, sword
turbosquid
$49
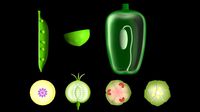
Types of Placentation
... available on turbo squid, the world's leading provider of digital 3d models for visualization, films, television, and games.
Project
3d_export
$7
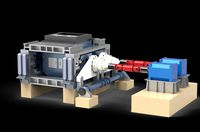
project
...project
3dexport
project
3d_export
$20
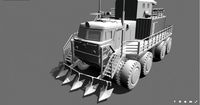
Project
...project
3dexport
design_connected
$16
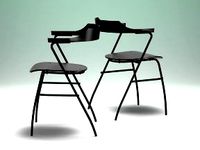
Project Chair
...project chair
designconnected
rex kralj project chair computer generated 3d model. designed by žitnik, marjan.
3ddd
$1
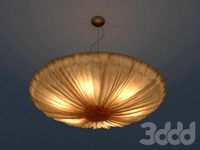
lectric Project
...настроены. сетка очень плотная.
доступно только для группы "profi"
про группу "profi" можно прочитать в чаво
3d_ocean
$19
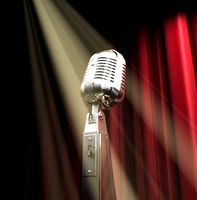
Soon project
...kup. made in 3ds max 2013 1- 3dsmax with vray render included material and light 2- obj file 3- fbx file hope you like it plea...
turbosquid
$49
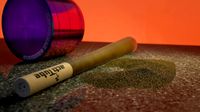
Joint | Project
...squid
royalty free 3d model joint | project for download as on turbosquid: 3d models for games, architecture, videos. (1297983)
turbosquid
$11
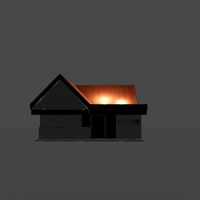
house project
...bosquid
royalty free 3d model house project for download as on turbosquid: 3d models for games, architecture, videos. (1672482)
turbosquid
$450
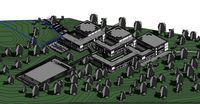
University project
...
royalty free 3d model university project for download as rvt on turbosquid: 3d models for games, architecture, videos. (1463354)
turbosquid
$30
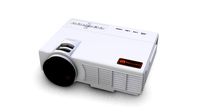
smart projecter
...lty free 3d model smart projecter for download as max and obj on turbosquid: 3d models for games, architecture, videos. (1236214)
3d_export
$5
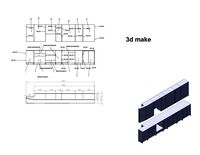
project drawing
...project drawing
3dexport
project drawing and 3d model<br>format jpg sldprt dwg<br>by 3d make